Metal 3D Printing Overview
Metal 3D Printing, also known as Direct Metal Laser Sintering (DMLS) or Selective Laser Melting (SLM), is an advanced additive manufacturing process that produces high-precision metal parts by fusing fine layers of metal powder using a powerful laser. This technology enables the creation of complex geometries, intricate internal structures, and lightweight designs that are difficult or impossible to achieve with traditional manufacturing methods. DMLS and SLM are ideal for producing durable, functional components with excellent mechanical properties, making them preferred solutions for industries requiring exceptional precision and performance.
Common applications of DMLS include:
Our DMLS/SLM Capabilities
Metric | US | |
---|---|---|
High Resolution | 20 microns | 0.00079 in. |
Normal Resolution | 30 microns | 0.0012 in. |
Normal Resolution (X Line*) | Aluminum: 40 microns Inconel: 60 microns | Aluminum: 0.00157 in. Inconel: 0.00236 in. |
Metric | US | |
---|---|---|
High Resolution | Al: 94mm x 98mm x 98mm 70mm x 88mm x 88mm | Al: 3.7 in. x 3.8 in. x 3.8 in. 2.7 in. x 3.5 in. x 3.5 in. |
Normal Resolution | 330mm x 245mm x 245mm | 13.0 in. x 9.6 in. x 9.6 in. |
Normal Resolution (X Line*) | 500mm x 800mm x 400mm | 19.7 in. x 15.7 in. x 31.5 in. |
Metric | US | |
---|---|---|
High Resolution | 0.153mm Aluminum: 0.381mm | 0.006 in. Aluminum: 0.015 in. |
Normal Resolution | 0.381mm (0.762mm for Aluminum) | 0.015 in (0.030 in. for Aluminum) |
Normal Resolution (X Line*) | 0.381mm (0.762mm for Aluminum) | 0.015 in. (0.030 in. for Aluminum) |
For well-designed parts, tolerances of ±0.003 in. (0.075mm) in the X/Y dimensions for the first inch, plus 0.1% of the nominal length (0.001mm/mm), are typically achievable. In the Z dimension, tolerances of ±0.006 in. for the first inch, plus 0.1% of the nominal length, can be expected. However, tolerances may vary based on part geometry.
*Currently, only Inconel 718 and Aluminum are available for our large-format X Line machine.
Parts with larger dimensions (>7 in.) or thin features are more prone to warping during the SLS process. To minimize this risk, we recommend maintaining a consistent thickness of 0.125 in. (3.175mm) across the part for better structural stability.
Finishing Option | Description |
---|---|
Polished | Surfaces are sanded to the desired grit level, resulting in a somewhat reflective and bright finish, though some sanding lines or marks may still be visible. |
Brushed | Surfaces are directionally sanded to the desired grit level. |
Satin | Surfaces are sanded to the desired grit level, then grit blasted and bead blasted for a smooth finish. |
Standard | Support structures are removed, and layer lines remain visible. |
1 mm
5 Days
± 0.3mm
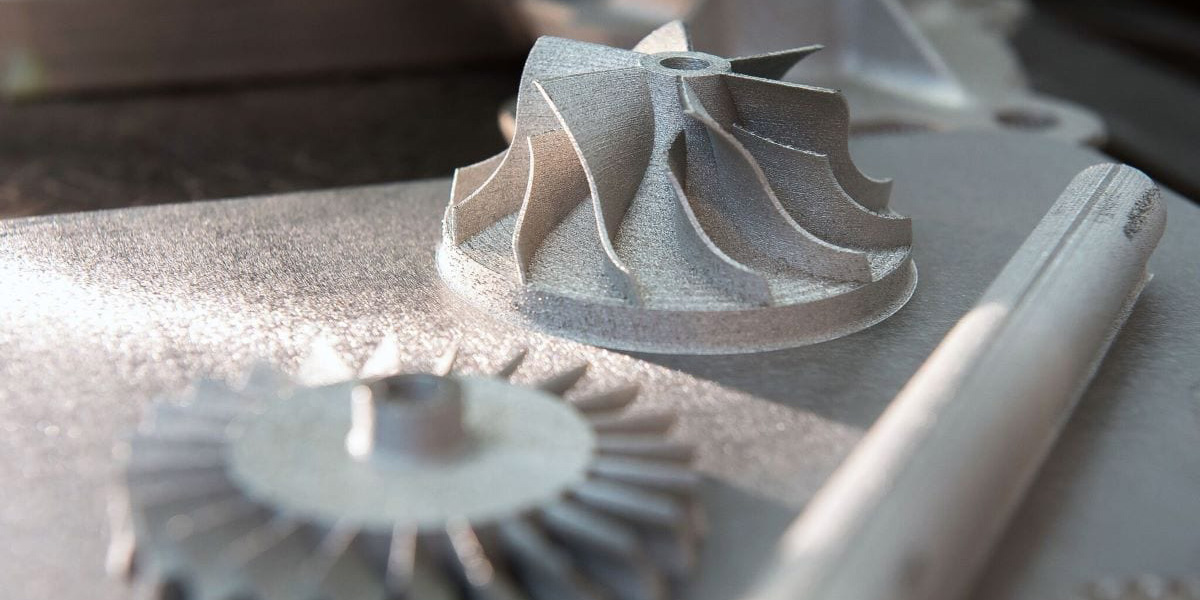
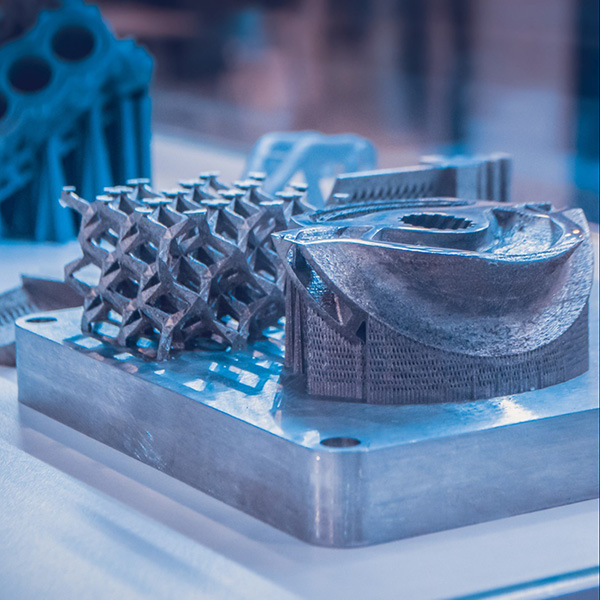
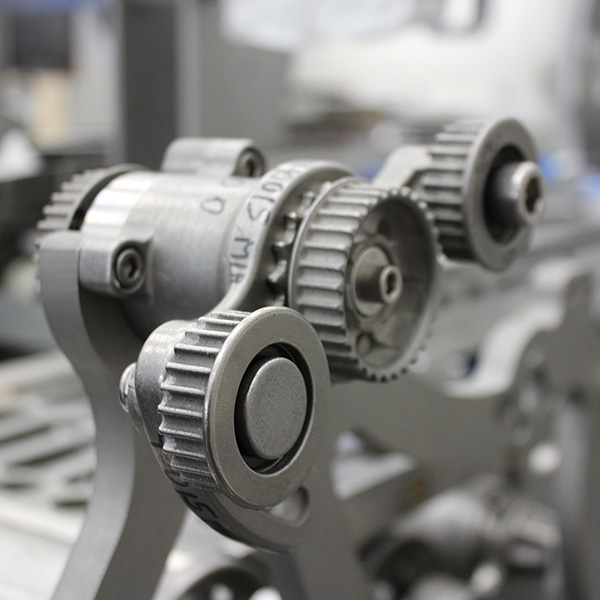
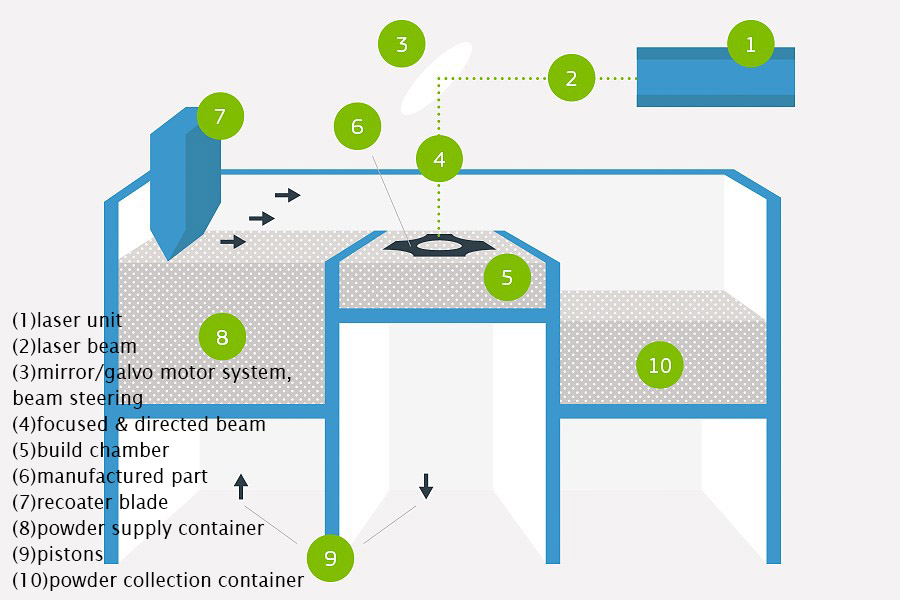
How Does Metal 3D Printing Work?
The Direct Metal Laser Sintering (DMLS) 3D printing process begins with the laser unit (1) generating a high-powered laser beam (2), which is directed by the mirror/galvo motor system (3) and beam steering (3) to precisely melt and fuse metallic powder on the build platform (5). Initially, the laser sinters support structures to the base plate, followed by the part itself. As each cross-section layer of powder is micro-welded, the build platform (5) shifts down, and the recoater blade (7) moves across to deposit the next layer of powder from the powder supply container (8). Layer by layer, this process is repeated until the part is complete. Once the build is finished, parts undergo manual brushing to remove loose powder, followed by heat treatments to relieve stress. Afterward, parts are removed from the platform, and support structures are detached. Final finishing steps such as bead blasting and deburring are done, ensuring the part is nearly 100% dense. Throughout the process, pistons (9) and the powder collection container (10) manage powder distribution and collection, ensuring smooth operation and efficient material handling.
Material Properties
Material | Resolution | Condition | Ultimate Tensile Strength (MPa) | Yield Stress (MPa) | Elongation (%) | Hardness | Datasheet |
---|---|---|---|---|---|---|---|
Aluminum (AlSi10Mg) | 20 μm | Stress Relieved | 268 | 180 | 15 | 46 HRB | |
30 μm | Stress Relieved | 345 | 228 | 8 | 59 HRB | ||
40 μm | Stress Relieved | 296 | 186 | 10 | 50 HRB | ||
Stainless Steel (316L) | 20 μm | Stress Relieved | 565 | 386 | 78 | 90 HRB | View |
Stainless Steel (17-4 PH) | 20 μm | Solution & Aged (H900) | 1,190-1,310 | 1,050-1,170 | 6-13 | 38-40 HRC | View |
30 μm | Stress Relieved | 586 | 379 | 75 | 88 HRB | ||
Cobalt Chrome (Co28Cr6Mo) | 20 μm | As Built | 1,255 | 772 | 17 | 39 HRC | |
30 μm | As Built | 1,213 | 820 | 14 | 38 HRC | ||
Copper (CuNi2SiCr) | 20 μm | Precipitation Hardened | 496 | 434 | 23 | 87 HRB | View |
Inconel 718 | 20 μm | Stress Relieved | 986 | 676 | 36 | 33 HRC | |
30 μm | Stress Relieved | 993 | 627 | 39 | 30 HRC | ||
30 μm | Solution & Aged per AMS 5663 | 1,434 | 1,207 | 18 | 46 HRC | ||
60 μm | Stress Relieved | 958 | 572 | 40 | 27 HRC | ||
60 μm | Solution & Aged per AMS 5663 | 1,386 | 1,200 | 19 | 45 HRC | ||
Inconel 625 | 20 μm | As Built | 765 | 334 | 42 | 7 HRC | View |
20 μm | Solution & Aged (H900) | 1,372 | 1,227 | 10 | 42 HRC | ||
30 μm | Wrought AMS 5599 | 827 | 414 | 30 | 0-19 HRC | ||
40 μm | Stress Relieved | 43 | 27 | 10 | 50 HRC | ||
60 μm | Stress Relieved | 139 | 83 | 40 | 27 HRC | ||
Titanium (Ti6Al4V) | 20 μm | Stress Relieved | 1,055 | 951 | 15 | 35 HRC | View |
30 μm | Stress Relieved | 993 | 855 | 18 | 33 HRC | ||
H13 Tool Steel | 20 μm | Annealed | 620 | 345 | 22 | 40 HRC | View |
20 μm | As Built | 1,540 | 960 | 4 | 40 HRC | ||
30 μm | Heat-Treated | 1,580-1,680 | 1,250-1,360 | 4.7-14 | 45-46 HRC | ||
D2 Tool Steel | 20 μm | Heat-Treated | 3,841 | 1,714-2,200 | N/A | 55-62 HRC | View |
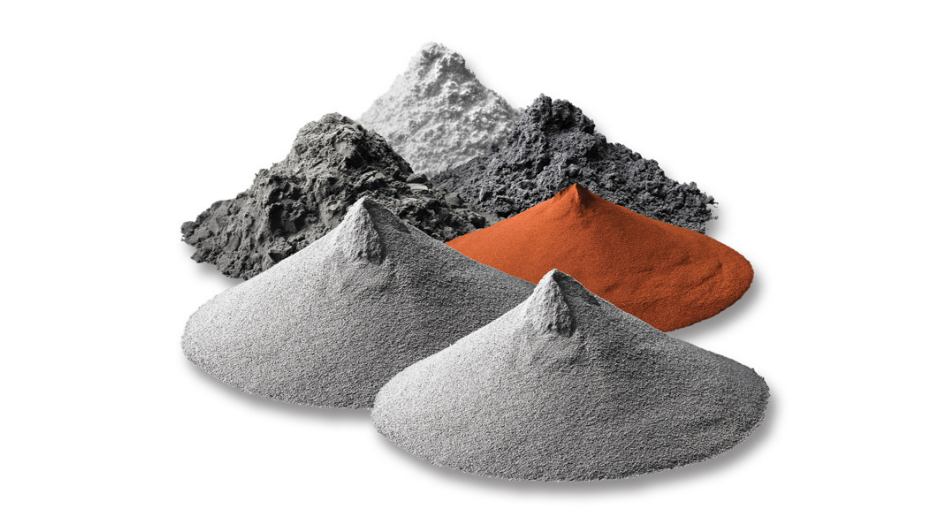
Key Notes:
20 μm = High Resolution (HR)
30, 40, and 60 μm = Normal Resolution (NR)
These values are approximate and may vary based on machine settings and process parameters. Independent lab testing is recommended for critical applications.
Material and Surface Finishing Options
Aluminum (AlSi10Mg)
Aluminum AlSi10Mg is similar to a 3000 series alloy commonly used in casting and die-casting processes. It offers a strong strength-to-weight ratio, along with high temperature and corrosion resistance. The material also provides good fatigue, creep, and rupture strength, making it suitable for demanding applications. Final parts made from AlSi10Mg undergo stress relief treatment to enhance stability and durability.
Custom Finishing Options
Stainless Steel (316L)
Choose 316L when stainless steel flexibility is required, as it is more malleable than 17-4 PH. This makes it ideal for applications needing greater ductility and deformation resistance. Final parts made from 316L undergo stress relief treatment to enhance stability and performance.
Custom Finishing Options
Stainless Steel (17-4 PH)
Stainless steel 17-4 PH is a precipitation-hardened alloy known for its exceptional hardness and corrosion resistance. It offers significantly higher tensile and yield strength compared to 316L stainless steel but has lower elongation at break, making it ideal for applications requiring strength over flexibility. Final parts made from 17-4 PH undergo vacuum solution heat treatment followed by H900 aging to achieve full hardness and durability.
Custom Finishing Options
Cobalt Chrome (Co28Cr6Mo)
Cobalt Chrome (Co28Cr6Mo) is a superalloy primarily composed of cobalt and chromium, known for its high tensile strength and excellent resistance to creep and corrosion. These properties make it a reliable material for aerospace components and medical instrumentation that require durability and performance under stress.
Custom Finishing Options
Inconel 718/625
Inconel 718 and Inconel 625 are nickel-based superalloys widely used in metal 3D printing for high-performance applications. Inconel 718 offers excellent strength, corrosion resistance, and durability under extreme temperatures and mechanical stress, making it ideal for aerospace and industrial parts. Printed components typically undergo stress relief, with optional solution and aging per AMS 5663 for higher strength and hardness. In contrast, Inconel 625 provides outstanding corrosion resistance and good strength without requiring precipitation hardening. It’s well-suited for applications in chemical processing, marine, and aerospace environments where resistance to aggressive media and thermal fatigue is critical.
Custom Finishing Options
Titanium (Ti6Al4V)
Titanium (Ti6Al4V) is a versatile, high-performance alloy known for its exceptional strength-to-weight ratio. Its mechanical properties, including tensile strength, elongation, and hardness, are comparable to wrought titanium when measured against Ti grade 23 annealed, making it ideal for demanding applications.
Custom Finishing Options
H13 Tool Steel
H13 tool steel is a chromium-molybdenum hot work steel recognized for its toughness and thermal fatigue resistance. It offers a good balance of strength, hardness, and ductility, making it ideal for high-temperature tooling and die-casting applications. Properties are similar to wrought H13 when heat-treated after 3D printing.
Primary Benefits
D2 Tool Steel
D2 tool steel is a high-carbon, high-chromium alloy known for its excellent wear resistance and edge retention. It delivers high hardness and compressive strength, making it suitable for tooling, dies, and applications requiring long-lasting cutting edges. Mechanical properties are comparable to conventionally produced D2 when properly heat-treated.
Primary Benefits
Post-Processing Options for Metal 3D-Printed Parts
Method | Applicable Materials | Color | Description |
---|---|---|---|
Sanding | All | – | Smooths edges, reduces visible layers, and removes support marks. |
Spray Painting | All | Black, Pantone/RAL colors | Quick coloring method that reaches difficult areas. |
Plating | All | – | Enhances appearance, creates a reflective surface, or prevents corrosion. |
3- and 5-Axis Milling | All | – | Improves dimensional accuracy and surface finish through precision milling. |
Turning | All | – | Rotates parts for symmetrical shaping and accurate machining. |
Custom Finishing | All | – | Tailored surface treatments to meet specific requirements. |
Brushed (150, 220, 400) | All | – | Creates a uniform, directional texture with different grit levels. |
Satin | All | – | Produces a smooth, non-reflective surface with a soft sheen. |
Polished | All | – | Achieves a high-gloss, reflective finish. |
Passivation | Stainless Steel | – | Enhances corrosion resistance by removing free iron from the surface. |
Wire EDM | All | – | Uses electrical discharges for precise cutting of metal parts. |
Tapping and Reaming | All | – | Creates precise threads and smooth, accurate holes. |
Method | Applicable Materials | Description |
---|---|---|
Stress Relief | All | Reduces internal stresses caused by the 3D printing process, improving dimensional stability and mechanical performance. |
NADCAP Heat Treatment | Nickel Alloys, Titanium | Certified heat treatment process for aerospace-grade parts, ensuring compliance with industry standards. |
Hot Isostatic Pressing (HIP) | Titanium, Inconel, Steel | Applies high pressure and temperature to eliminate internal voids, enhance density, and improve mechanical properties. |
Solution Annealing | Stainless Steel, Inconel | Improves corrosion resistance and refines grain structure by dissolving precipitates. |
Aging | Nickel Alloys, Titanium | Enhances mechanical properties by hardening the material through controlled heating. |
Method | Applicable Materials | Description |
---|---|---|
Traceability | All | Ensures full traceability of material sources and processing history, ensuring quality and compliance. |
Chemistry | All | Analyzes the chemical composition of the material to verify conformity to specifications and performance requirements. |
Particle Size and Distribution Analysis | All | Measures the size distribution of powder particles, ensuring uniformity for optimal flowability and part quality in 3D printing. |
Method | Applicable Materials | Description |
---|---|---|
Tensile Testing | All | Measures a material's tensile strength, yield strength, and elongation by applying uniaxial force until failure. |
Rockwell Hardness | All | Evaluates the surface hardness of a part by measuring the depth of penetration under a specific load. |
DMLS and SLM can create parts with an accuracy of up to 0.1mm. For even tighter tolerances, our in-house CNC machining services can refine your parts, offering the precision you need while maintaining the design flexibility provided by additive manufacturing.
Method | Applicable Materials | Description |
---|---|---|
3, 4, and 5 Axis CNC Machining | All | Utilizes multiple axes for precise and complex part geometries, offering high accuracy and flexibility in machining. |
CNC Turning | All | Rotates parts to create symmetrical shapes, improving dimensional accuracy and surface finish. |
Wire EDM | All | Uses electrical discharges to cut through metals with high precision, ideal for intricate and detailed cuts. |
CNC Tapping | All | Creates accurate threaded holes in parts, ensuring consistent and reliable threading quality. |
Design For DMLS 3D Printing
When designing for DMLS 3D printing, it’s essential to consider material properties and part orientation to maximize strength and functionality. Ensure uniform wall thickness (around 1-3 mm) to prevent weak points and promote even sintering. Design features such as rounded corners and chamfers help enhance printability and reduce stress concentrations during the sintering process. For more detailed guidance, see below.
Case Study: Aluminum Gripper Redesign with Metal 3D Printing
A robotics manufacturer sought to improve an aluminum gripper used in high-speed automated assembly. Traditionally CNC-machined, the original design was limited by subtractive manufacturing constraints and involved high machining costs for complex geometries.
By switching to metal 3D printing, the team achieved significant design freedom, enabling lightweight lattice structures and integrated features previously impossible to machine. The redesigned gripper reduced part weight by 30%, lowered manufacturing costs through less material waste and simplified assembly, and maintained the required strength and performance under operational loads.
Key Benefits:
Case Study: Rocket Engine Cooling Component in Inconel 718
A space propulsion company needed a high-performance component for the cooling system of a liquid-fueled rocket engine. Traditional manufacturing struggled to produce complex internal channels essential for precise coolant flow, while also withstanding extreme thermal stress during engine operation.
Metal 3D printing with Inconel 718 provided the perfect solution, thanks to its exceptional thermal resistance and mechanical strength at elevated temperatures. Engineers were able to design intricate internal geometries, improving heat transfer efficiency and reducing weight. The printed component performed reliably under severe thermal cycling, contributing to safer, more efficient rocket launches.
Key Benefits:
Case Study: Production Line Components Redesign with Metal 3D Printing
A well-known global lighting manufacturer sought to improve efficiency and reduce operational costs on one of its high-volume production lines. Two critical machine components, traditionally machined and assembled from multiple parts, suffered from frequent wear and complex maintenance, leading to downtime and significant expenses.
Engineers turned to metal 3D printing to redesign these components as consolidated, single-piece parts with optimized geometries. The new designs not only increased durability and simplified installation but also reduced material waste and eliminated several manufacturing steps. As a result, the company achieved nearly €90,000 in annual savings while improving production line reliability and efficiency.
Key Benefits:
Case Study: Lightweight Titanium Bracket for Electric Aircraft
An innovative electric aircraft company was striving to reduce weight in its airframe without sacrificing structural integrity. One critical component, the ENDY bracket, was originally machined and contributed significant mass to the overall design.
By adopting metal 3D printing in titanium and applying a topology-optimized design, engineers successfully reimagined the bracket’s geometry. The result was a 40% weight reduction compared to the original part, while maintaining the required mechanical performance and safety standards. This advancement supports longer flight times and improved efficiency in next-generation electric aviation.
Key Benefits:
Case Study: Lightweight Titanium Wishbone for Automotive Applications
An automotive engineering team set out to reduce weight in a high-performance vehicle’s suspension system without compromising durability. Traditionally machined wishbones were heavy and limited in geometry, restricting possibilities for weight savings and performance improvements.
By leveraging metal 3D printing in titanium, the team created a wishbone featuring an internal honeycomb structure. This innovative design reduced material usage and overall part weight while preserving the required stiffness and load-bearing capacity. The result was a lighter, high-strength component that enhances vehicle agility and fuel efficiency.
Key Benefits:
Why Use 3D Printing for Metal Parts?
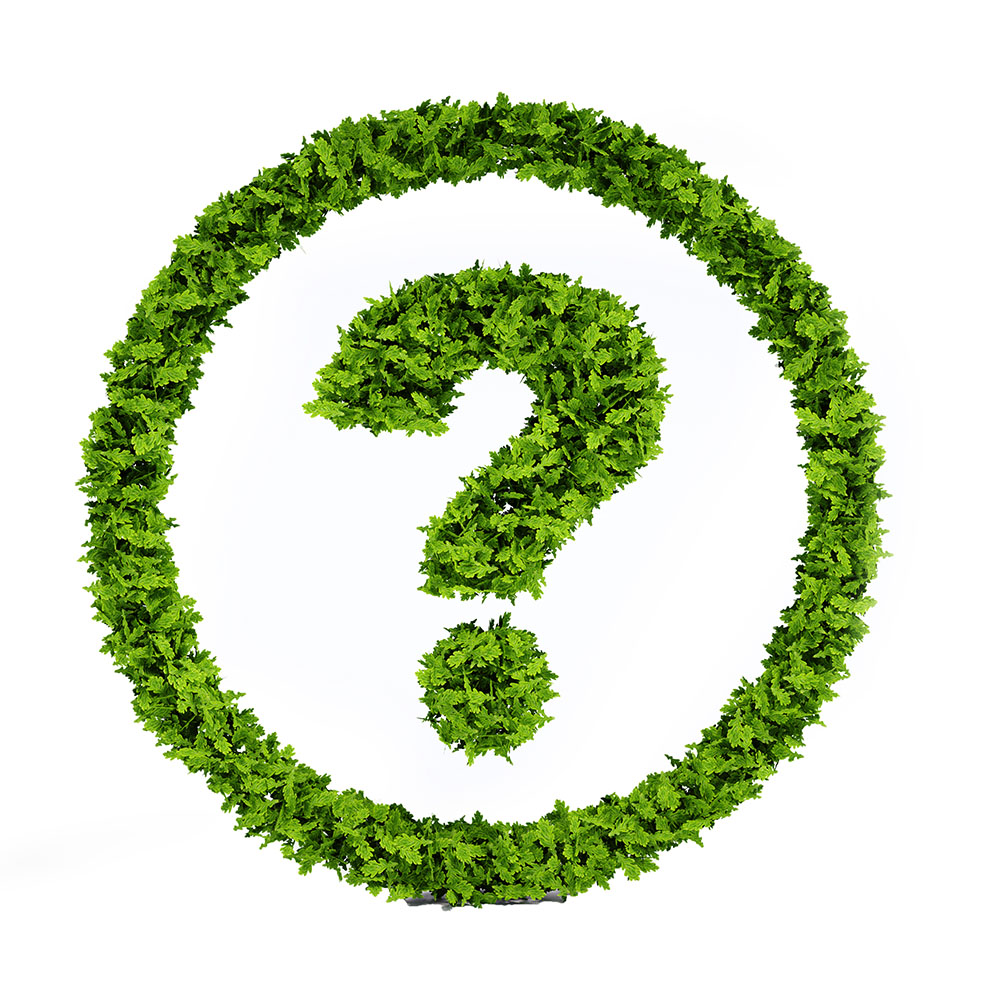