Fused Deposition Modelling (FDM) 3D Printing Service
Our FDM Printing Capabilities
Item | Details |
---|---|
General Tolerance | ± Single build layer thickness for the first inch; ±0.002" per subsequent inch. |
Maximum Single Build Size | Up to 24" x 36" x 36" (609.6mm × 914.4mm × 914.4mm) |
Lead Time | Standard: 2–3 days for prototypes; 5–7 days for small batches (10–50 units) |
Layer Resolution | 0.007"–0.020" (adjustable by part complexity; 0.007" for fine details, 0.020" for fast functional parts) |
Layer Height Accuracy | ≤0.010" for parts <16"; ≤0.013" for parts 16"–36" |
Minimum Wall Thickness | 0.047" for parts <16"; 0.060" for parts 16"–36" (tested for structural integrity in repeated use) |
Maximum Print Speed | Up to 150 mm/s (varies by layer height; 80–100 mm/s for precision parts) |
Minimum Feature Size | 0.020" (for small details like holes, tabs, or textured surfaces) |
Repeatability | ±0.001" across 50+ consecutive prints of the same design |
FDM Materials
Explore a full range of high-performance FDM materials designed to meet diverse application requirements across industries.
Note: The main properties and data of each material are included. Please click to expand.
Explore our full 3D printing material selection at: 3D Printing Materials
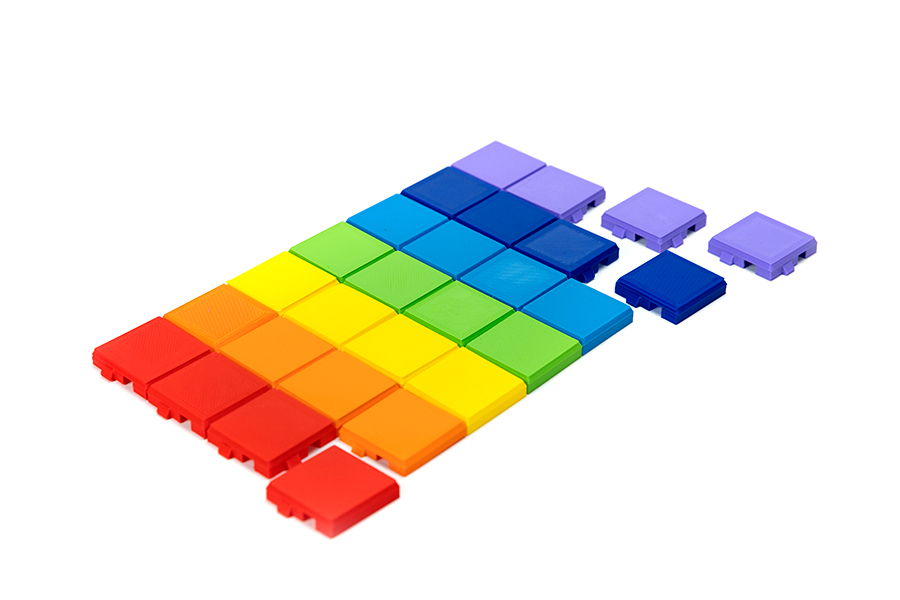
FDM Infill Options
Rectangular
Standard infill pattern, strong in all directions, fast to print, with minimal bridging.
This is our go-to for high-volume, straightforward parts—think small brackets or enclosures. We’ve found it shines in batch production because its consistent print speed (20-30% faster than triangular patterns) keeps lead times tight, and its minimal bridging reduces post-processing (no extra support cleanup). Pro tip: Pair it with 30-50% density for most functional parts—strikes the sweet spot between strength and material use.
Triangular/diagonal
Enhances strength along wall directions; slightly longer print time.
We rely on this for parts with clear “load paths,” like long, thin structural beams or lever arms. In practice, tweaking the angle (we often use 45° vs. 30°) boosts wall-adjacent strength by ~15% in tests—critical for parts that bear weight along their edges. Just note: The extra print time (5-10% longer than rectangular) is worth it for stress-heavy applications.
Wiggle
Allows twisting/compression, softer; ideal for flexible rubber or soft nylon materials.
This is a hidden gem for “give” in parts—we use it for TPU gaskets or nylon shock absorbers. But here’s the catch: It works best with low density (10-20%)—higher density makes it stiff, defeating the purpose. We also adjust print speed (slower by 10%) to prevent the nozzle from “skipping” over the wavy paths, ensuring smooth, consistent flexibility.
Honeycomb
Popular, fast-printing, high-strength, with robust all-directional strength.
This is our top pick for large, flat parts (e.g., equipment panels) where weight matters. In real-world runs, a 60% density honeycomb is 30% lighter than a 60% rectangular infill but with similar impact resistance. We’ve also noticed it’s less prone to warping on big prints—those hexagonal cells distribute heat more evenly, cutting down on post-print warpage by ~25% in our workshop tests.
Infill Density Reference Chart
Infill Density (%) | Characteristics | Typical Applications |
---|---|---|
0% | Extremely lightweight with minimal material usage; prints very quickly. However, it lacks structural strength entirely, as the part is mostly hollow. | Decorative prototypes, non-functional display models, or parts where weight reduction is critical (e.g., props). |
20% | Lightweight with basic rigidity; uses moderate material and prints relatively fast. It offers limited load-bearing capacity and may flex under moderate stress. | Simple low-stress parts (e.g., small casings for lightweight electronics, basic snap-fit components with minimal force). |
50% | Balances strength and weight effectively; provides decent rigidity and impact resistance. Prints in reasonable time with moderate material consumption, though it is heavier and slower than lower densities. | General-purpose functional parts (e.g., jigs, fixtures, medium-load brackets, tool handles). |
80% | High structural strength with dense internal patterns; withstands significant pressure and repeated stress. However, it is heavier, takes longer to print, and consumes more material than lower densities. | Heavy-duty parts (e.g., high-load brackets, structural components in machinery, gears with regular stress). |
100% | Solid structure with maximum strength and rigidity; offers excellent durability and tight tolerances. It is the heaviest option, requires the longest print time, and uses the most material. | Critical load-bearing parts (e.g., mechanical connectors, high-pressure components, parts needing hermetic sealing). |
Notes:
Typical Applications
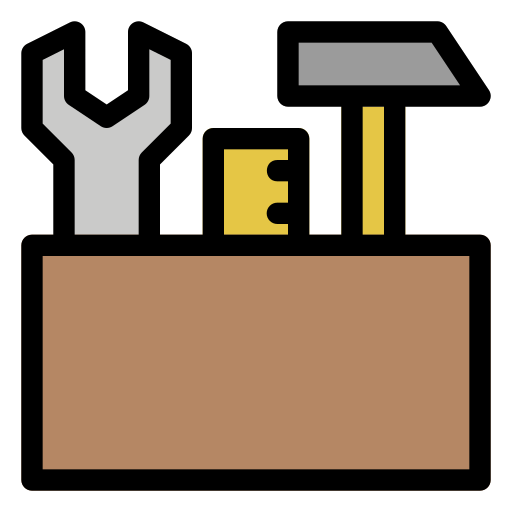
Workholding Tools
FDM offers a fast and cost-effective solution for producing custom jigs, fixtures, and tooling aids used across manufacturing lines.
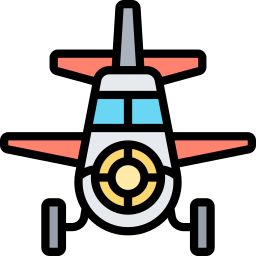
Aviation and Aerospace
Lightweight, strong FDM parts are increasingly replacing traditional metal components, with common applications including cabin interior parts and under-the-hood engine elements.
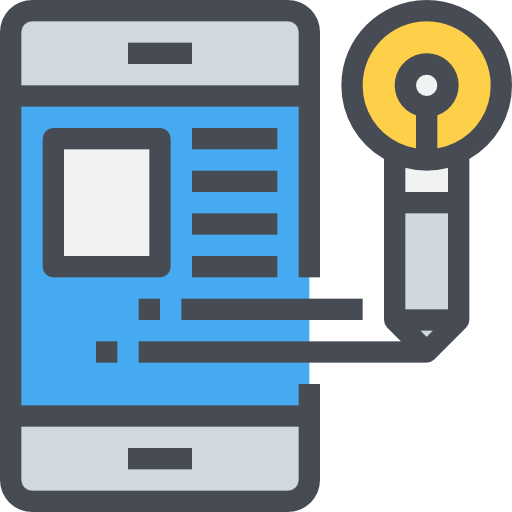
Rapid Prototyping
Thanks to the strength and durability of FDM materials, prototypes can be tested for fit, finish, and performance, helping refine designs before committing to production tooling.
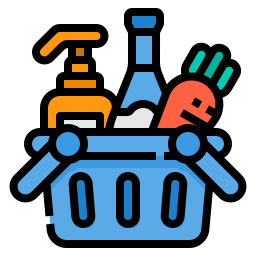
Consumer Goods
The chemical and impact resistance of FDM-printed parts makes them well-suited for a wide range of consumer products that require everyday durability.
FDM Finishing Options
Surface Finish | Most Common Materials | Colors | Description | Examples (Commonly Processed Parts) |
---|---|---|---|---|
Sanded | PLA, ABS, PETG | – | Manual or machine sanding to smooth surfaces and reduce visible layer lines | Prototypes needing smooth edges (e.g., consumer product handles, toy parts) |
Media Blasted | PLA, ABS, Nylon | – | Matte finish achieved by blasting parts with fine media for consistent texture | Tooling fixtures, industrial brackets (requires uniform low-gloss texture) |
Vapor Smoothed | ABS, ASA | – | Chemical vapor treatment melts outer layer for glossy, sealed surfaces | Consumer electronics casings, visible prototypes (needs sleek, polished look) |
Painted (Non-Cosmetic) | PLA, ABS, PETG | Black, Gray | Basic sanding and painting focused on functionality over perfect appearance | Utility jigs, internal machine components (needs protection, not visibility) |
Painted (Cosmetic) | PLA, ABS, PC-ABS | Pantone/RAL colors | High-quality sanding and painting for visible, aesthetic parts | Retail product prototypes (e.g., small appliance panels, cosmetic tool housings) |
Customer Spec Paint | PLA, ABS, PETG | Custom Colors | Painting per specific customer color/finish requirements | Branded parts (e.g., company-logoed device casings, color-matched components) |
Specialty Coated | PLA, ABS, TPU | Varies | Coatings for UV resistance, anti-scratch, or soft touch | Outdoor-use parts (UV coating), grip handles (soft-touch coating) |
Pad Printed | PLA, ABS, PETG | Pantone Colors | Precise transfer of small logos, icons, or texts | Control knobs (small labels), medical device components (tiny instructions) |
Screen Printed | PLA, ABS, Nylon | Pantone Colors | Printing larger graphics or labels directly on parts | Toy surfaces (large graphics), equipment panels (instruction labels) |
Inserts | ABS, Nylon, PETG | – | Installation of metal inserts for threads, fasteners, or structural reinforcement | Brackets (threaded inserts for screws), handles (reinforced fastener points) |
Post-Machined | ABS, Nylon, PC | – | Machining processes like drilling, milling, or reaming to achieve fine tolerances | Precision parts (e.g., holes for bearings, threaded bores needing tight fit) |
Assembly | PLA, ABS, PETG | – | Final assembly combining multiple printed and non-printed parts | Robotics kits, small machinery subassemblies (e.g., gear + bracket + housing) |
Case Studies of FDM 3D Printing
Advantages of FDM 3D Printing
Comparison Table of 3D Printing Technologies
Technology | Maximum Build Volume | Typical Lead Time | Dimensional Accuracy | Best for Prototyping | Suitable for End-Use |
---|---|---|---|---|---|
SLA | 533mm x 635mm x 736mm | 2 days | ± 0.2% with a minimum of ± 0.13 mm | High-detail visual models | Small, non-functional parts with aesthetic needs |
SLS | 482mm x 482mm x 431mm | 3 days | ± 0.3% with a minimum of ± 0.3 mm | Durable plastic prototypes for testing | Functional low-volume plastic components |
DMLS | 500mm x 800mm x 400mm | 3 days | ±0.3 mm | Metal parts with complex features | Strong, functional metal components in limited runs |
MJP | 294 x 211 x 144 mm | 2 days | ±0.1 mm | Highly detailed small-scale prototypes | Small batches of high-resolution parts |
FDM | 609.6mm × 914.4mm × 914.4mm | 2 days | ± 0.3% with a minimum of ± 0.3 mm | Proof-of-concept and utility prototypes | Non-aesthetic functional parts like fixtures and jigs |
MJF | 294 x 144 x 211 mm | 4 days | ±0.3 mm | Functional and accurate prototypes | Short-run plastic parts needing strength and precision |
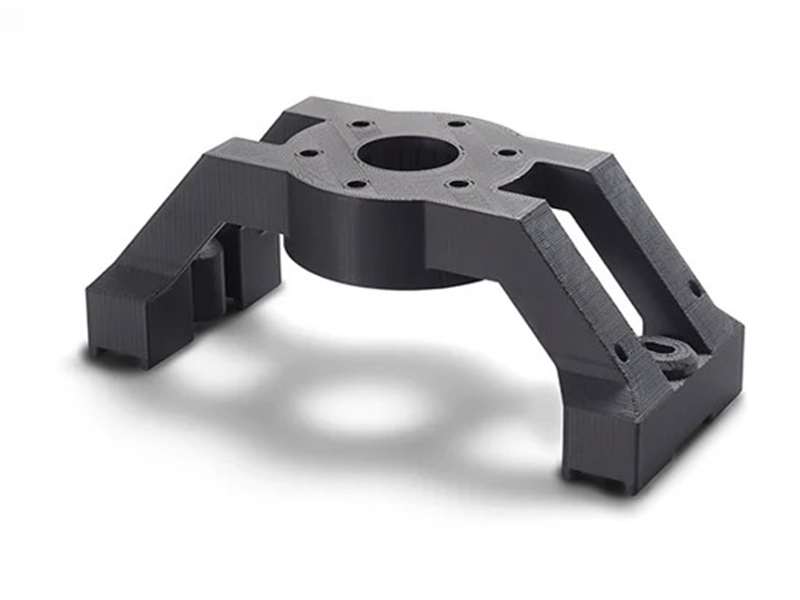
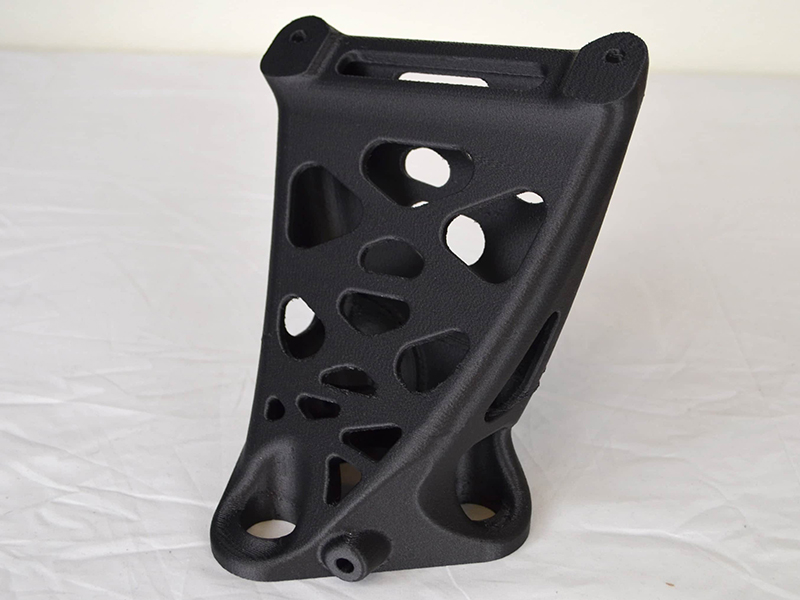
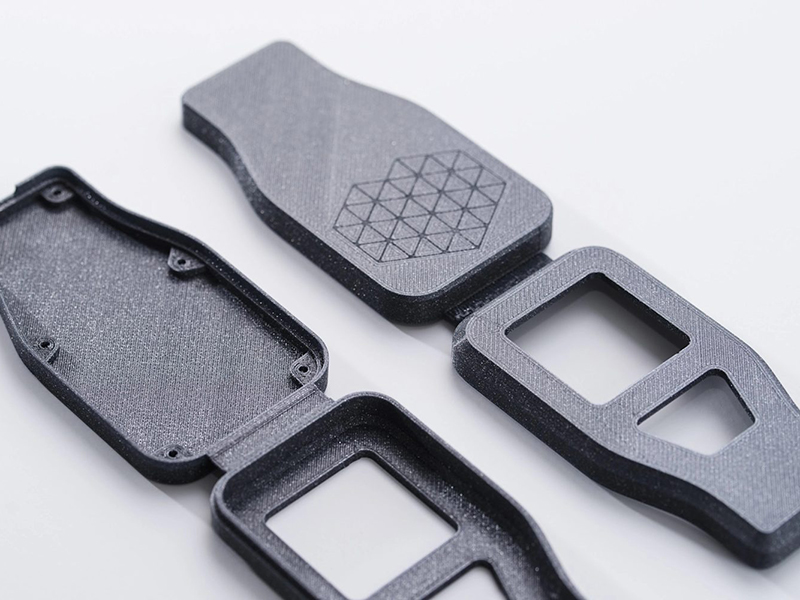
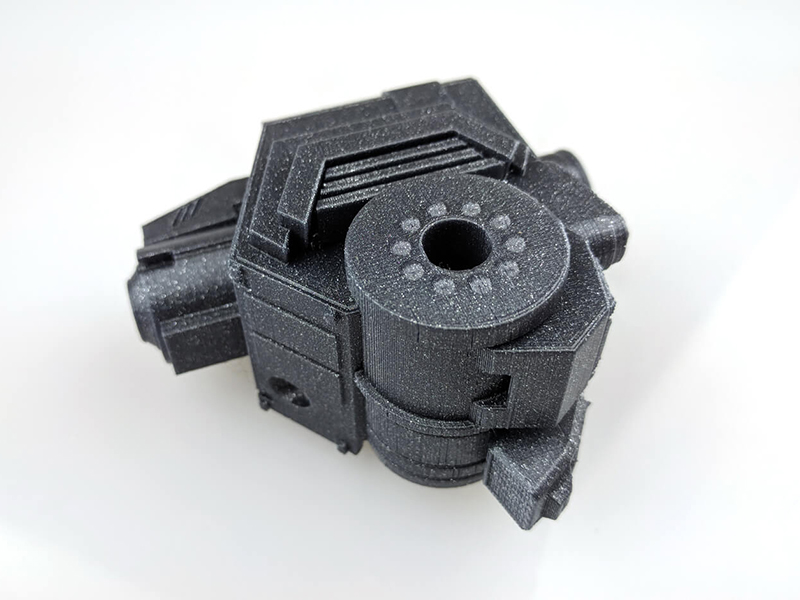
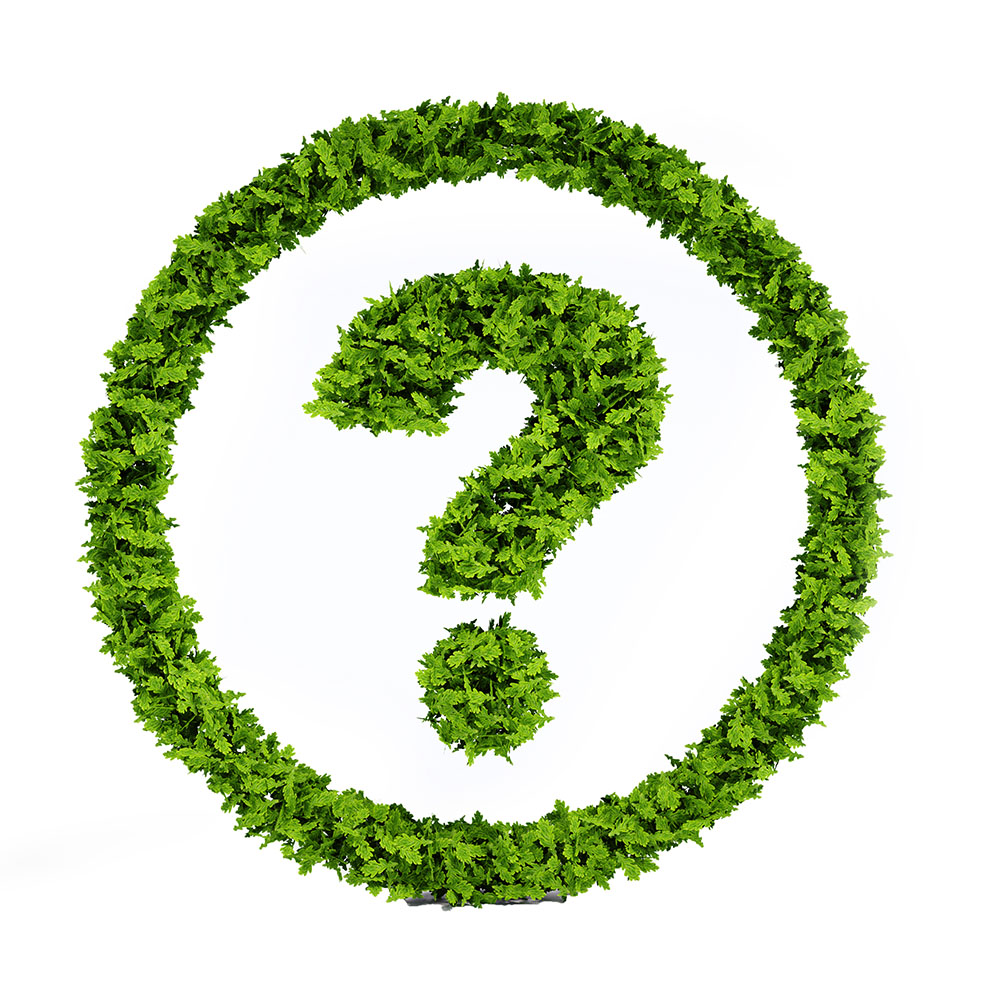
Frequently Asked Questions
While FDM 3D printing is highly effective for prototyping and low-volume production, it is typically not used for large-scale mass production due to speed limitations compared to traditional manufacturing methods. However, it is ideal for producing customized parts or small batches.
The print duration varies by part size and complexity: smaller, simpler parts can finish in a few hours, while larger or intricate designs may take 1–3 days. At our service, the total lead time (encompassing printing, post-processing, and preparation) typically falls within 2–3 days for most projects. This lead time does not include shipping or delivery time.