Plastic injection molding is a transformative manufacturing process that injects melted plastic into precisely designed molds. Through centuries, this technique has revolutionized the production of everyday items, from simple products like bottles to automotive parts with complex design. As more and more industries seek efficient, cost-effective solutions, plastic injection molding is standing out for its ability to produce high-quality components with high speed and precision.
Originating in the mid-19th century, this method has evolved with advanced technologies and sustainable practices, while addressing environmental concerns. In this post, we’ll explore the principles, processes, history and future trends of plastic injection molding, stating its importance in modern manufacturing.
Injection Molding Machine: Producer Of Plastic Molds
As implied in its name, plastic injection molding is a manufacturing process used to create parts by injecting molten plastic into a mold. This method is particularly favored by product developers or managers for producing large quantities of perfectly identical items within a fast turnaround time. Whether it’s the casing for a smartphone or components for a medical device, plastic injection molding is integral to modern manufacturing.
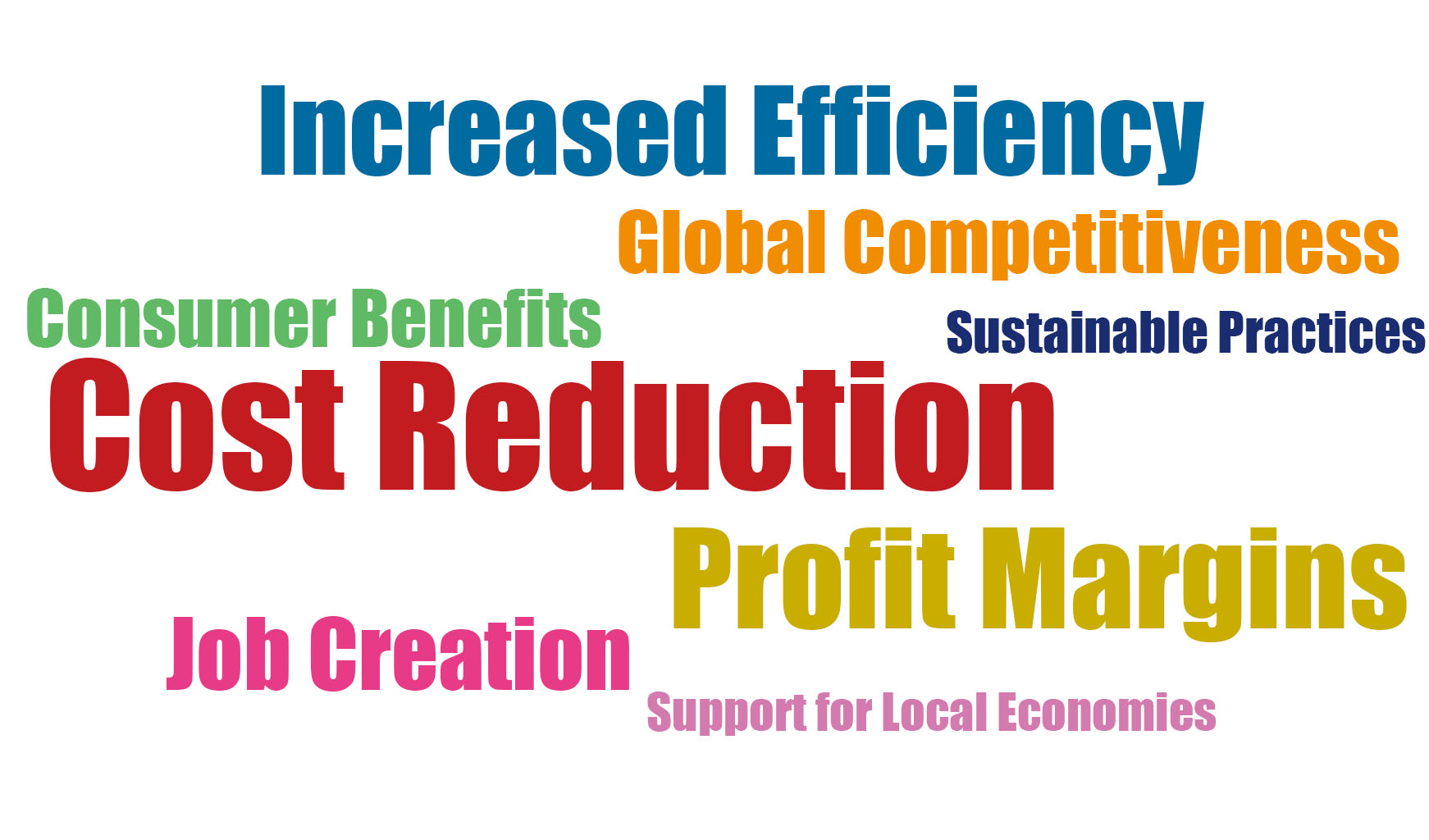
First of all, many beginners who have just entered the industry may mistakenly think that injection molding machines are molds, because most of the time people call them both by “molds” in casual conversation. But actually, molds are metal (usually) containers where plastic pellets are injected into, while injection molding machines are used to provide thrust for the injection molding process after assembling the mold. Below is a more detailed and professional description.
Injection Molding Machine: The machinery used to heat and inject the plastic into the mold. It consists of several components as listed below.
Barrel: Plastic pellets undergo plasticization within this cylindrical chamber. A rotating screw homogenizes the melt while advancing it toward the injection zone.
Mold: The product’s birth chamber – a custom-made steel/aluminum cavity that shapes molten plastic into final forms.
Feed Hopper: Gravity-fed reservoir supplying raw pellets to the barrel’s feed throat continuously.
Nozzle: Terminal orifice regulating material transfer from barrel to mold, maintaining laminar flow through precise temperature control.
Heaters: Devices surrounding the barrel that maintain the necessary temperature to melt the plastic pellets, allowing them to flow easily for injection.
Reciprocating Screw: This helical rotor achieves three critical functions: Shearing pellets to generate frictional heat; Homogenizing melt composition; Functioning as a volumetric injection piston
Injection Unit: The integrated melting-delivery system comprising barrel, reciprocating screw, and nozzle assembly.
Stationary Platen: Hydraulic-actuated plate executing mold opening/closing cycles via toggle or direct-pressure systems.
Movable Platen: Hydraulically-driven plate that opens/closes the mold for part ejection.
Ejector Plate: A component that holds ejector pins, which push the molded part out of the mold once it has cooled and solidified.
Clamping Unit: It’s very much like a hydraulic fortress – generating 50-6,000+ tons of compressive force to counteract injection pressure and prevent flash.
Tie Rods: Four steel columns maintaining structural alignment between platens during clamping cycles.
So there we have it. If you go to an engineer about the whole process, you’ll probably hear:
“First things first: we pick the right plastic pellets for the job. These get dumped into the hopper up top, where they tumble down into the barrel. As they’re pushed along by the screw, heaters cook them until they turn completely gooey.
Now here’s where the action happens – that molten plastic gets squirted through the nozzle into the chilled mold cavity at crazy high pressure. The cold mold basically flash-freezes the plastic into whatever shape we designed into it. After the cooling timer dings, the mold halves split open. That’s when ejector pins kick the finished part out, ready for trimming or assembly.”
This workhorse process lets manufacturers produce parts with complex design with razor-sharp precision, making it the MVP of modern manufacturing.
Evolution of Plastic Injection Molding
Foundational Era (1860s-1930s)
- Material Genesis: Bakelite (Leo Baekeland, 1907) established the first viable synthetic polymer platform
- John Wesley Hyatt’s 1872 plunger-based injector enabled early mass production of celluloid items (machine prototype)
- But at that time, manual operation and material constraints restricted complexity and throughput
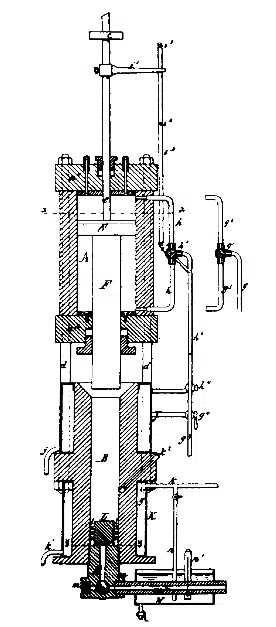
Industrialization Leap (1940s-1960s)
“The reciprocating screw didn’t just improve molding—it redefined material behavior during processing.”
— James Watson Hendry, 1946 (Inventor of the screw injection machine )
Critical Innovation: Hendry’s screw system revolutionized plastication homogeneity and injection control
At the same time, hydraulic clamping (1950s) enabled high-volume production for automotive/consumer sectors, and engineering thermoplastics (e.g., ABS, nylon) was put into use, expanding functional applications.
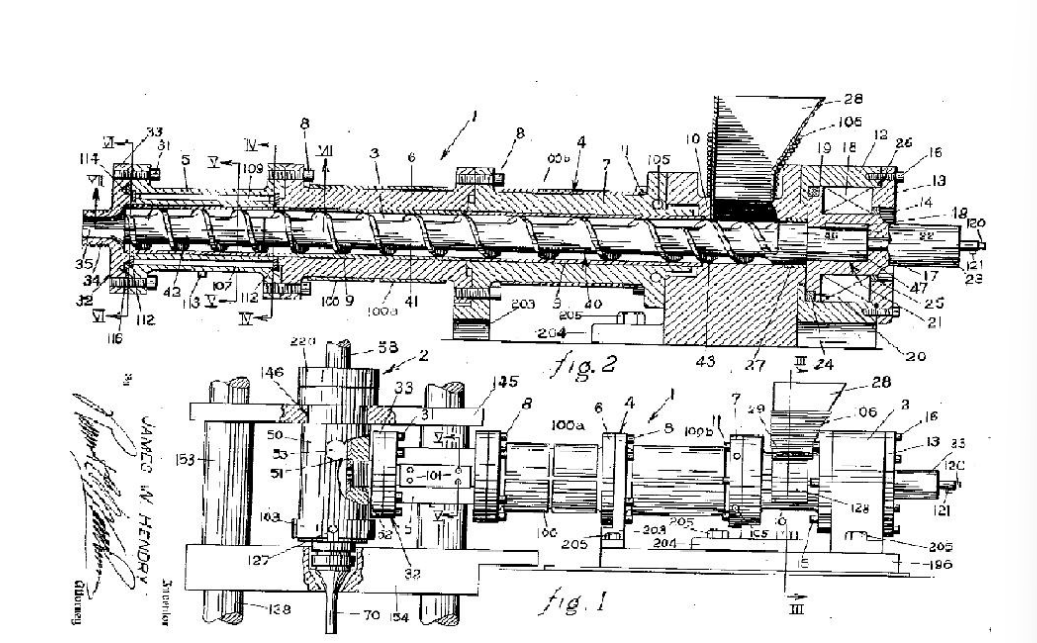
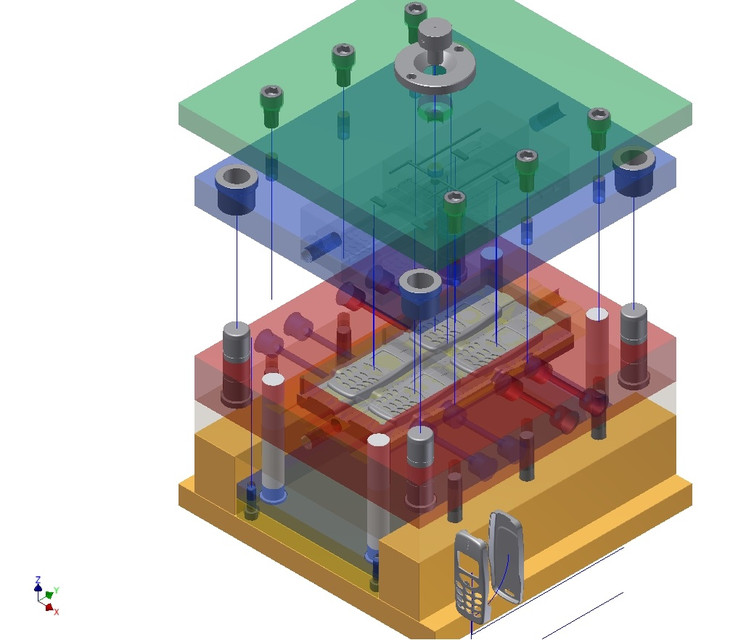
Digital Transformation (1970s-1990s)
- Precision Engineering: CAD/CAE enabled first-principles mold design; CNC machining ensured micron-level accuracy
- Glass-filled polymers and high-temperature resins met demanding mechanical specifications
- Process Control: Closed-loop hydraulic systems and statistical process monitoring reduced defects by more than 60%
Modern Frontiers (2000s-Present)
Domain | Innovation | Industry Impact |
Industry 4.0 | IoT-enabled real-time viscosity control | ±0.15% dimensional consistency |
Sustainability | Bio-polymers & in-line regrind systems | 30-50% carbon footprint reduction |
Micro-molding | Sub-gram shot capabilities | Medical device miniaturization |
Manufacturing Criticality & Ubiquitous Applications
Plastic injection molding constitutes the backbone of industrial mass production, delivering unmatched freedom for part design, material efficiency (±2% scrap rates according to our past 2 years’ manufacturing reports), and per-part economics (70%-90% cost cut down comparing with 3d printing or cnc machining).
- Packaging Innovations
- Primary Containment: FDA-compliant PP/PE containers (e.g., pharmaceutical bottles, food-grade tubs)
- Closure Systems: Precision-molded tamper-evident caps with <0.15mm sealing tolerances
- Material Advantage: Thin-wall molding (0.2-0.5mm) reducing material consumption by 25%
- Automotive Engineering
- Structural Components: Glass-filled PA66 intake manifolds, impact-modified PC/ABS instrument panels
- Safety Systems: Airbag housings with UL 94 V-0 flammability ratings
- Economic Impact: 60-70% of non-metallic auto parts produced via injection molding
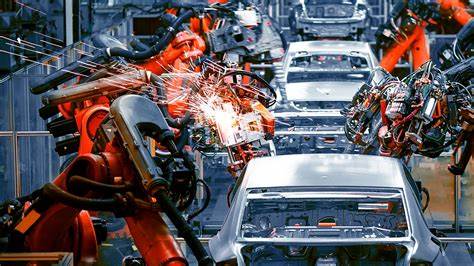
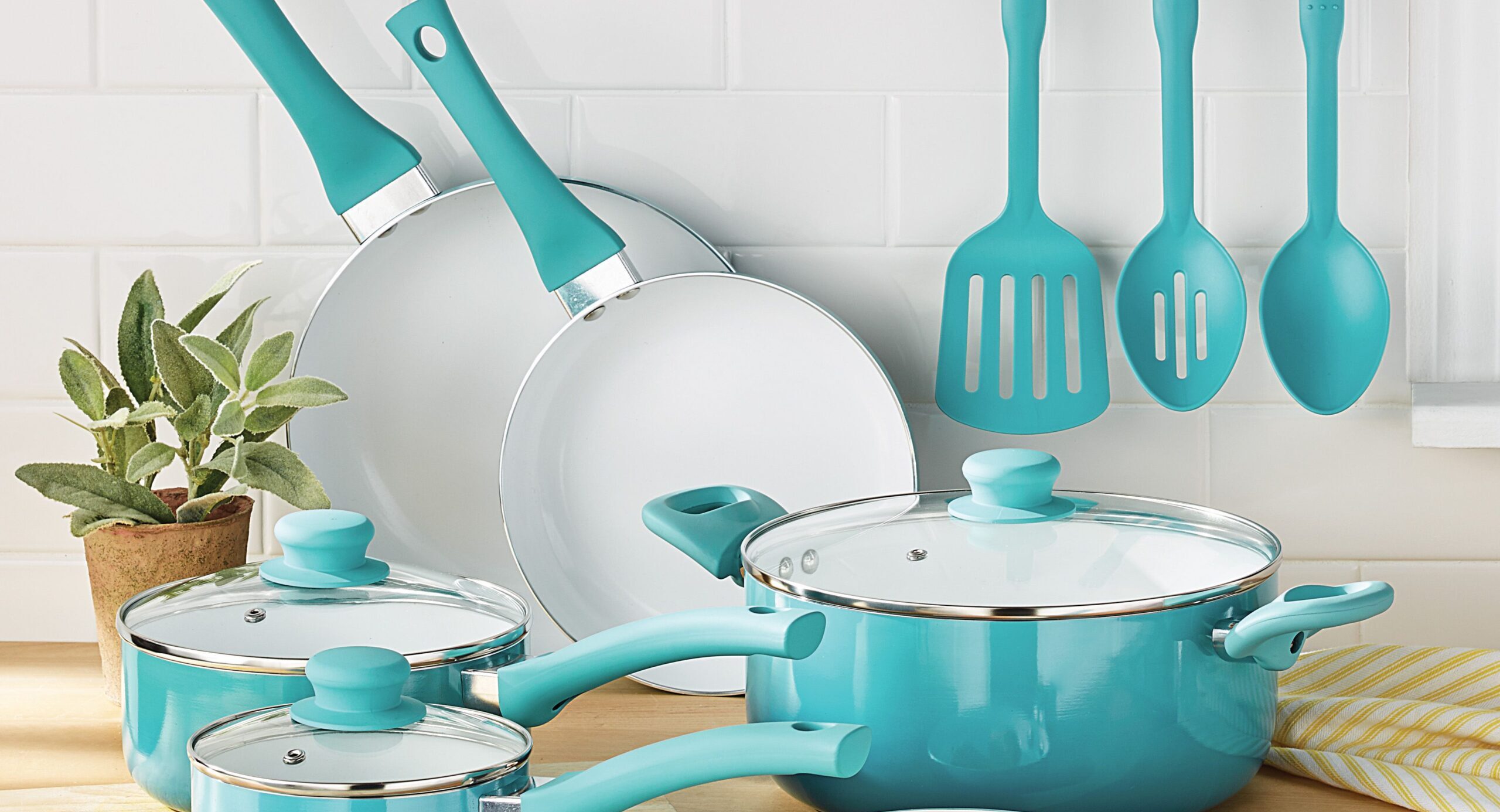
- Consumer & Medical Goods
Sector | Components | Material Innovation |
Electronics | Snap-fit housings, connector bodies | Flame-retardant ABS, EMI-shielding compounds |
Healthcare | Sterile syringe barrels, inhaler components | USP Class VI medical-grade COC |
Durables | Ergonomic tool grips, appliance gears | Fiber-reinforced POM for <0.01% creep deformation |
“No other process delivers such geometric freedom at automotive production volumes. It’s the silent enabler of product innovation.”
— Dr. Maureen Steinwall, ASM Fellow & 40-year molding industry authority
What are the steps of plastic mold injection?
- Feed Pellets:Plastic pellets are loaded into the machine’s hopper.
- Melt Plastic:The pellets move into a heated barrel. A rotating screw pushes them forward while heaters melt them into liquid plastic.
- Inject into Mold:The screw pushes forward like a plunger, forcing the molten plastic under high pressure through a nozzle into a closed, cooled mold cavity.
- Cool & Solidify:The plastic inside the mold cools down and hardens into the shape of the cavity.
- Open Mold & Eject:The mold opens. Pins push the solidified plastic part out of the mold.
- Repeat:The mold closes, and the cycle starts again.
Plastic Injection Molding or 3D Printing: Which To Choose
Deciding between plastic injection molding and 3D printing depends heavily on your project’s needs. Here’s a clear comparison:
Aspect | Plastic Injection Molding | 3D Printing |
Best For: | Mass Production | Prototyping & Low Volumes |
Speed (High Vol. per Part): | Very Fast | Slow |
Setup Cost: | High (mold design & manufacturing) | Low (no physical tooling needed) |
Cost Per Part: | Low | High |
Design Freedom: | Limited (must allow mold release & filling) | High (complex geometries easily built) |
Part Strength: | High & Consistent | Variable |
Surface Finish: | Smooth and Precise | Layered Texture |
Material Choice: | Primarily Thermoplastics/Thermosets | Wider range |
Lead Time: | Longer upfront (slow mold creation) | Very Short |
Design Changes: | Costly and Slow | Easy & Fast (only need to modify digital file) |
Material Waste: | Higher | Lower |
When to Choose Which:
- Choose 3D Printing if:
- You need prototypes in a short time.
- Your Production runs are small(e.g., 1-100 parts).
- Part design is highly complex or custom.
- You need to change design rather frequently.
- You prefer low upfront cost.
- Choose Injection Molding if:
- You need large quantities (thousands or millions).
- Low cost per partis essential (at volume).
- You require high strength, durability, and precision.
The Bottom Line:
There’s no single “best” technology. Match the process to your project’s priorities: volume, cost, speed, complexity, and material needs. Often, 3D printing is ideal for prototyping and initial design, while injection molding takes over for cost-effective mass production.
What Is The Future of Plastic Injection Molding?
Just like any other technologies, plastic injection molding is always developing. Based on decades of industry evolution and current engineering advances, here’s what we’re realistically seeing shape its future – making factories more efficient, products more innovative, and processes more sustainable:
- Factories with Instant Feedback
Forget guesswork. Modern workshops are wiring up machines with sensors that constantly monitor every little detail during production – just like a fitness tracker for your press. In practice, this means:
- Predicting hiccups before they halt production:Spotting a pump vibration trend that signals wear, allowing maintenance before a breakdown happens or defected products produce.
- Auto-tuning for peak performance:Machines subtly adjusting settings in real-time to maintain perfect part quality, even as material batches vary slightly.
Last but not least, one of the greatest things about smart-manufacturing is taht it provides instant dashboards showing exactly how each machine and mold is performing, leading to smarter decisions and surely, and (maybe) more importantly, making the bosses more at ease.
- Materials Revolution: Beyond Just Plastic
Advanced bioplastics that break down responsibly and high-performance recycled resins meeting tough specs are moving beyond prototypes into real production.
And moreover, these materials deliver tangible performance and environmental benefits, meeting both stricter regulations and conscious consumer demand.
- Robots: Your New (and Highly Skilled) Co-Workers
Automation is moving far beyond simple part removal. Picture this:
Lined-up cobots are now handling hot parts, delicate insert loading, or precise quality checks with vision systems far sharper than the human eye.
And let’s don’t forget that robots don’t tire, which ensure the 10,000th part matches the 1st perfectly – and this is especially critical for medical or automotive components.
Put simply, plastic injection molding remains a vital, efficient way to produce high-quality plastic parts at scale. Whether you’re perfecting a prototype or ramping up full production, understanding how this process works helps you make smarter choices for your project. At KingStar Mold, we use this deep process knowledge every day. We focus on finding practical, cost-effective molding solutions tailored to your specific part and volume needs. If you’re still weighing your options, learn more about why manufacture with an on-demand maker—and discover the flexibility and responsiveness it brings to your production timeline. Ready to see how proven injection molding can bring your design to life efficiently? Let’s talk about making it happen.