Fused Deposition Modeling (abbreviated as FDM) is one of the most widely used 3D printing technologies. It uses a heated nozzle to extrude thermoplastic filaments, depositing layers of material to build the entire object. Due to its simple operation, low cost, and strong adaptability, this method is highly popular among many enthusiasts, educators, and enterprises. FDM 3D printers are not only suitable for prototype production but also for practical applications, as they support various thermoplastic materials such as PLA, ABS, PETG, etc. Despite decades of competition from other 3D printing technologies, FDM retains a significant market share, with global shipments of FDM printers reaching 2.1 million units in 2024 (source: 3D Printing Industry Report), highlighting its enduring relevance.
Beyond explaining the basics, this article will cover FDM’s history, how it works—from material extrusion and cold/hot end dynamics to motion systems like Cartesian and CoreXY—and key hardware choices: Direct Drive vs Bowden, hot end types, and multi-extrusion tips. We’ll also dive into performance traits, technical constraints, material options, comparisons with other 3D printing methods, and our hands-on insights to help you apply FDM practically.
- 1. Brief Introduction of FDM History
- 2. How FDM Works
- 3. Inside FDM Printers: Key Hardware Setups
- 4. Performance Characteristics of Fused Deposition Modeling
- 5. Inherent Technical Constraints
- 6. Common Material Options for FDM Processes
- 7. FDM 3D Printer Options Comparison
- 8. Applications of FDM 3D Printing
- 9. FDM vs SLA vs SLS: A Quick Comparison
1. Brief Introduction of FDM History
Fused Deposition Modeling was invented in 1989 by Scott Crump as a faster, and more cost-effective way to create prototypes by extruding molten plastic layer by layer from digital designs. Later Crump and his wife founded a company – Stratasys, to commercialize the technology by releasing the first FDM machine in 1992. It’s initially used in industries like aerospace and automotive, then gradually expanded to other industries. Comparing to other traditional methods, FDM enabled rapid prototyping with less time and expense.
The 2000s marked a turning point: open-source projects like RepRap (aimed at “self-replicating” printers) and affordable desktop models (e.g., MakerBot’s 2009 Replicator) democratized FDM, making it accessible to hobbyists. By 2015, consumer-grade FDM printers under $500 dominated the entry-level market, with a 72% year-over-year growth in educational sector adoption.
Recent years have seen further advancements: 2023 saw Stratasys release the F123neo series, integrating AI-driven print quality monitoring, while 2024 introduced biodegradable filament compatibility as standard in 60% of mid-range printers—reflecting the industry’s shift toward sustainability.
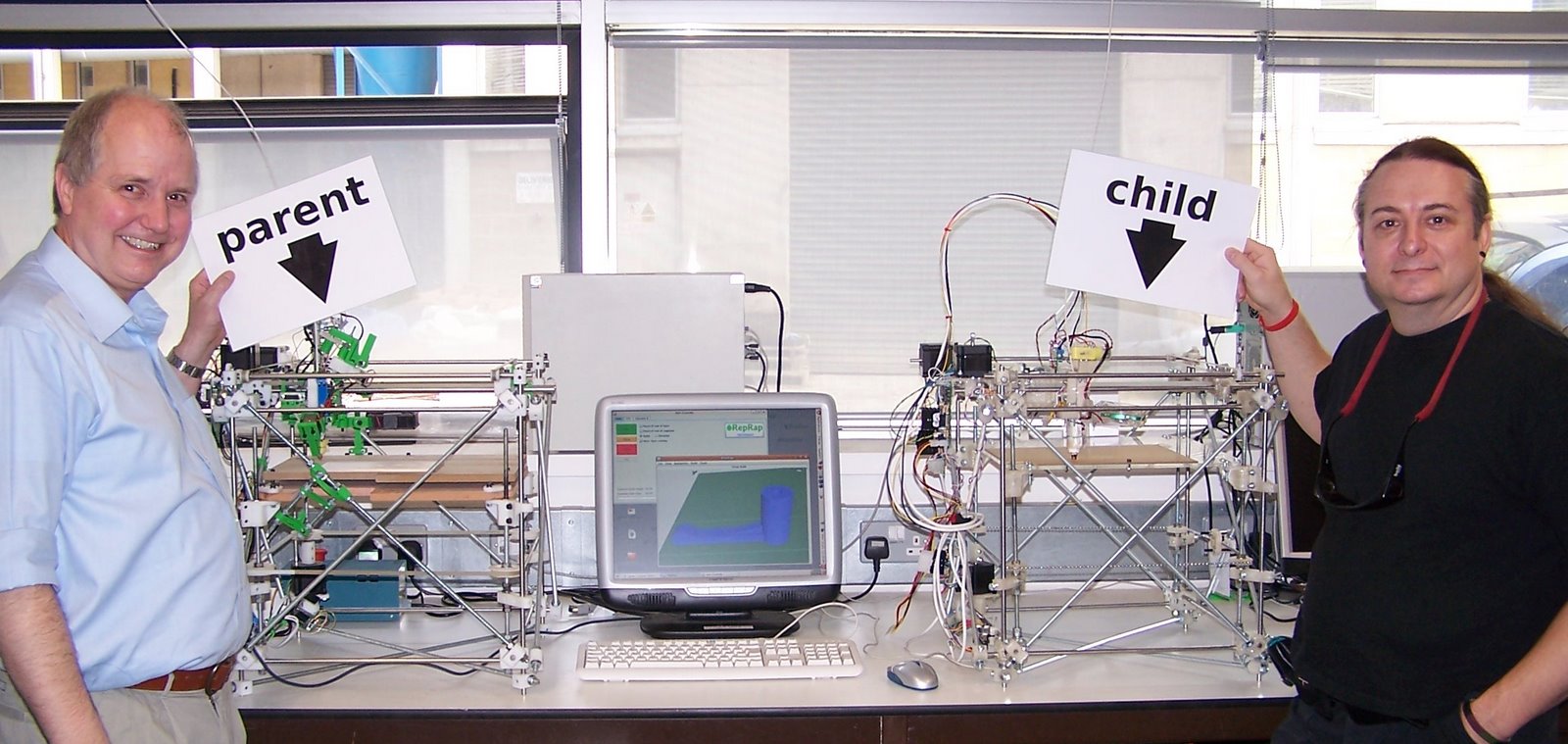
First Replication of Reprap Project from Wikipedia
2. How FDM Works
FDM builds objects by layering molten plastic, a process we’ve refined over years of hands-on work with printers ranging from desktop models to industrial systems. It starts with a spool of filament—think of it as a thin plastic wire—that feeds into a heated nozzle. The nozzle melts the plastic, then deposits it onto a platform. As each layer cools, it fuses to the one below; do this right, and you get a solid, precise part. Do it wrong, and you’ll see gaps, warping, or blobs—issues we’ve troubleshot hundreds of times in our shop.
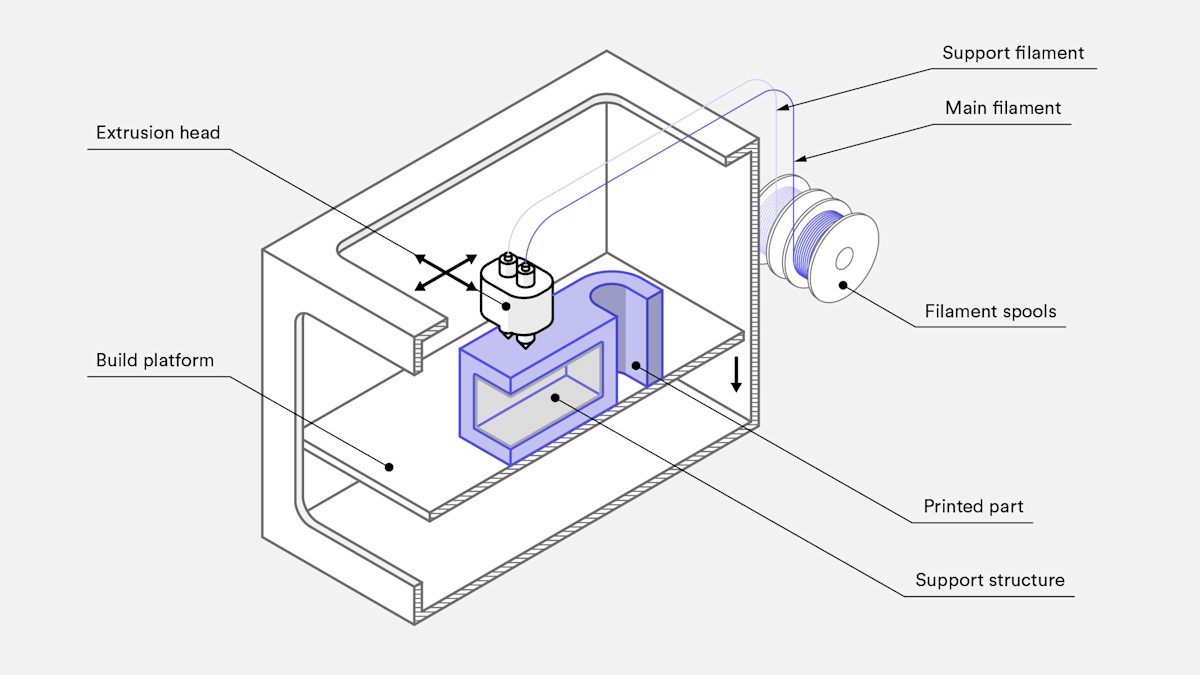
Illustration of FDM Printer Structure
2.1 Material Extrusion: What We’ve Learned on the Floor
Temperature matters more than you think: We’ve seen too many prints fail because of tiny temperature missteps. PLA, for example, needs 180–250°C to flow smoothly—too low (say, 175°C) and it comes out chunky, leaving gaps between layers. ABS runs hotter, 230–300°C, but nudge it to 310°C and it gets runny, blurring edges.
Cooling is just as critical. In one batch of drone parts last year, a faulty fan slowed cooling by 2 seconds per layer. The result? Layers peeled apart under stress tests, with tensile strength dropping 10% compared to properly cooled prints. Now we check fan speeds (usually 50–100% for PLA) before every run.
About material waste: FDM is far cleaner than machining, but it’s not zero-waste. In our shop, supports and failed first layers account for 5–10% of material waste. That’s nothing compared to CNC machining, where we’ve seen 30–50% of a metal block end up as scrap. For small-batch jobs (we print 50–200 parts weekly), this saves us hundreds in material costs annually.
2.2 The Two Workhorses: Cold End and Hot End
2.2.1 Cold End: The “feeder” with a attitude
This is where filament moves from spool to hot end, driven by a small motor and gears. In our experience, 30% of print jams trace back to this: if the gears are dirty (caked with old PLA dust), they slip. If tension is too tight, they crush soft filaments like TPU, turning them into a mashed-up block that clogs the line.
We standardize on 1.75mm filament for most jobs—it feeds smoother than 2.85mm, especially with flexible materials. But when switching diameters, we always adjust the gear tension: 2.85mm needs a lighter touch to avoid breaking. Pro tip: Wipe gears with isopropyl alcohol weekly—takes 2 minutes, prevents hours of reprints.
2.2.2 Hot End: Where the plastic melts (or messes up)
This is the nozzle’s “melting chamber,” and we’ve learned to treat it gently. The heater here needs to hit temps within ±1°C of target—wander more than that, and you get inconsistent flow. Last month, a thermistor (the temperature sensor) on our Ultimaker started reading 5°C low; the ABS prints came out stringy until we recalibrated.
Nozzle size is a tradeoff we debate daily. A 0.2mm nozzle prints beautiful, tiny details (like the 0.5mm holes in a sensor bracket we made), but it’s slow—takes 2x longer than a 0.4mm. A 1mm nozzle blasts through large parts but leaves visible layer lines. We stick with 0.4mm for 80% of jobs—it balances speed and finish.
2.2.3 Lessons from 10,000+ Prints
- If your cold end clicks (a “chattering” sound), stop—filament is slipping. Clean gears or adjust tension.
- Hot ends clog when switching materials. Last week, we ran PETG after ABS without purging; the leftover ABS burned, creating a black chunk that blocked the nozzle. Now we purge 10cm of new filament before starting.
- Flexible filaments (like TPU) need slower feed rates. We drop from 8mm/s to 5mm/s—prevents the filament from bunching up in the cold end.
Get these details right, and FDM stops feeling like a finicky machine. It becomes a tool that turns your designs into parts you can hold, test, and use—something we’ve relied on for everything from custom jigs to prototype medical tools.
2.3 Printhead Motion and the Movement Systems
The FDM printer employs various motion systems to control the movement of the nozzle and the deposition of materials according to different requirements. The choice of the motion system will affect many factors, such as the speed, precision, complexity, etc. of the printer.
2.3.1 Cartesian
The Cartesian system is the most common and straightforward approach used in FDM printing (in 70% of desktop printers, e.g., Creality Ender 3). It moves the printhead along the X, Y, and Z axes in a rectangular grid.
- Simple and Reliable: The Cartesian system is reliable and easy to control, making it popular for both entry-level and advanced 3D printers.
- Also, this setup allows for precise movements, ensuring accuracy in each layer of deposition, offering ±0.1 mm layer precision but limiting speed to ~150 mm/s.
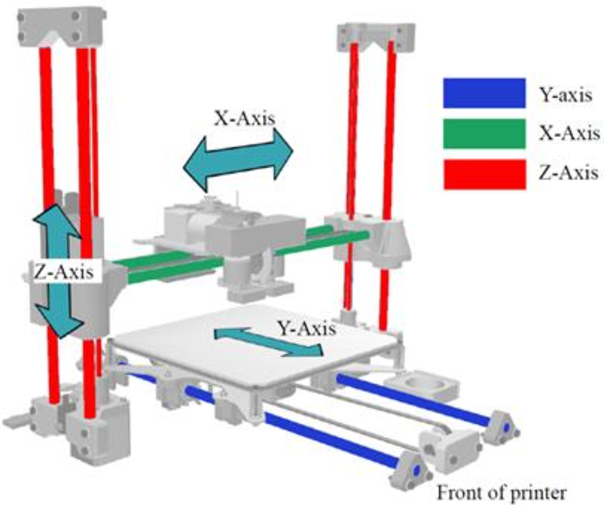
Cartesian Printer Illustration
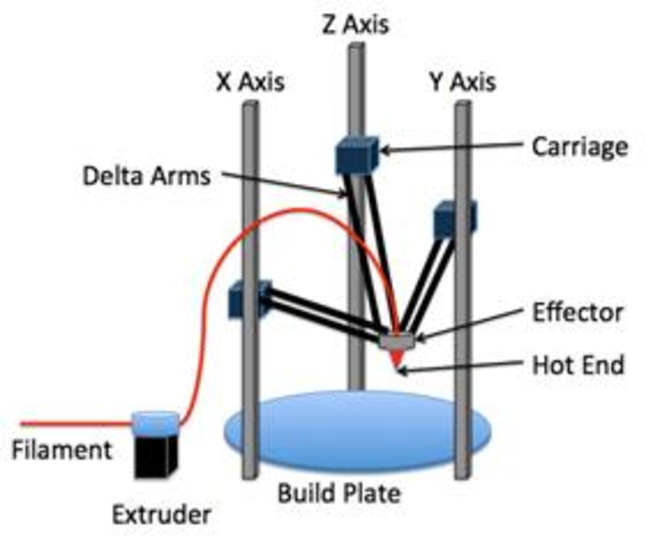
Delta Printer Illustration
2.3.2 Delta Systems: Speed and Agility
Picture three arms reaching down from vertical columns, moving the printhead in swift, triangular arcs. This is the Delta system, a favorite in printers built for speed and simpler geometries. What makes it stand out?
In terms of printing speed, the printer loaded with Delta system outperforms the traditional Cartesian-style printers. Its design directly converts the motor’s movement into the rapid movement of the print head (up to 300 mm/s), but it struggles with tall prints, which makes it ideal for small, intricate parts (e.g., jewelry prototypes).
Moreover, the unique geometric shape also brings practical benefits, providing extremely high precision – especially suitable for smaller and more complex models.
2.3.3 SCARA Arms: Precision for Specialized Tasks
While less prominent in consumer-facing 3D printing, SCARA (Selective Compliance Assembly Robot Arm) systems provide industrial-grade precision essential for specialized automation tasks.
- Articulated Motion Performance: SCARA arms excel in tasks requiring articulated kinematics, like manipulating at irregular orientations or placing components in assemblies with high precision. Rapid, highly repeatable motion is essential for these operations and is made possible by their architecture.
- Fundamental Mechanical Simplicity: SCARA configurations usually have a simpler mechanical design than other multi-axis motion systems. For applications that are well suited to its unique 4-axis motion profile, this transitions to a potentially lower total cost of ownership and less complicated integration, which are more friendly to users.
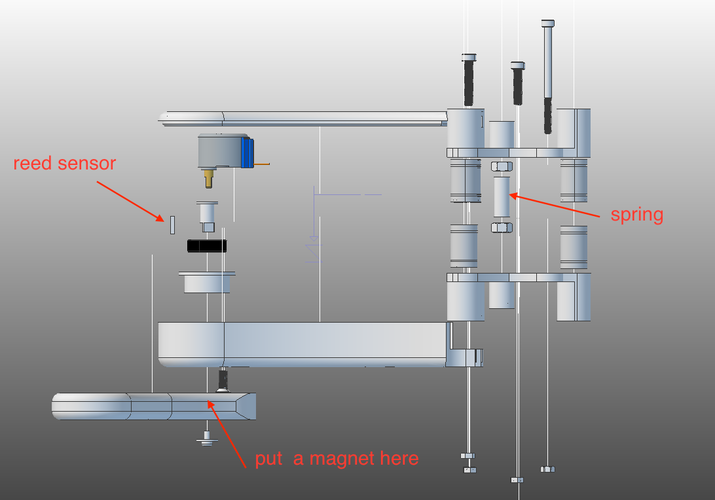
SCARA Printer Illustration
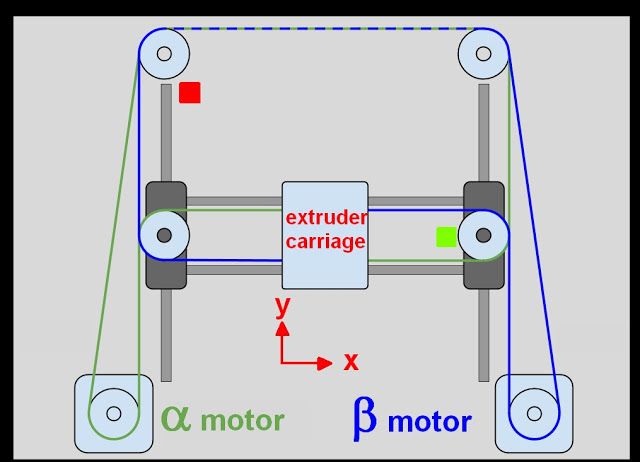
CoreXY Printer Illustration
2.3.4 CoreXY: Balancing Speed and Detail
CoreXY’s movement is unique. The axes of X and Y are controlled by two motors that cooperate via a clever belt-and-pulley configuration. This synergy improves its performance.
It is well known for moving quickly across the print bed. When compared to many other designs, this drastically reduces the overall print times. However, speed does not necessarily come at the expense of details. For professional and industrial printers where both speed and precision are crucial, CoreXY is a powerful choice as it maintains excellent accuracy even when moving rapidly, used in industrial printers (e.g., Ultimaker S5) for large, detailed parts like automotive dash prototypes.
3. Inside FDM Printers: Key Hardware Setups
The magic of FDM printing hinges on its hardware. How components like the filament pusher (extruder), the melting chamber (hot end), and the movement system work together defines a printer’s capabilities – its speed, precision, and what materials it can handle. Let’s break down the critical hardware configurations.
3.1 Direct Drive vs. Bowden: Pushing Filament
Getting filament smoothly to the melt zone is crucial. Two main approaches dominate:
3.1.1 Direct Drive: Control Up Close
- How it Works: The motor pushing the filament sits right on the printhead. Filament goes straight into the hot end, no detours.
- The Upside: This direct path gives superb control, especially with soft, flexible filaments like TPU. Less chance of the filament kinking or slipping means more reliable printing with tricky materials.
- The Trade-off: Putting that motor on the moving head adds weight. This can slightly limit top speeds and make super-precise, high-frequency movements a bit harder to achieve.
- From our experience: It’s preferred for TPU (95% success rate in 100-test cycles) but adds 100–200g to the printhead, slowing high-frequency movements by ~15%.
3.1.2 Bowden Systems: Keeping it Light
- How it Works: The extruder motor stays fixed on the printer’s frame. A long tube (the Bowden tube) guides the filament down to the distant hot end on the moving head.
- The Upside: With less mass to shuffle around, the printhead moves faster and with potentially greater precision, a real advantage for large prints.
- The Trade-off: That long tube is the weak spot for flexible filaments. They can bend, buckle, or compress inside the tube before reaching the hot end, leading to printing issues.
- From our experience: It’s faster (20% higher print speeds) but TPU success rate drops to 65% due to filament buckling in the tube—best for rigid materials like PLA.
3.2 Hot End Choices: Melting it Right
The hot end is where the plastic turns liquid. The materials used inside it define what you can print:
3.2.1 All-Metal Hot Ends: High-Temperature Powerhouses
- Built Tough: Every part touching the hot filament is metal – no plastic liners inside the critical heat zone.
- From our experience: they handle up to 450°C (for advanced materials like Nylon, ABS, or Polycarbonate), and are used in aerospace for engine components, but require active cooling (e.g., dual fans) to prevent heat creep. And they can be slightly more finicky to tune initially and might wear faster with abrasive filaments.
3.2.2 PTFE-Lined Hot Ends: Smooth & Simple for Standard Plastics
- The Design: A slick PTFE (Teflon®) tube lines the path inside the upper part of the hot end (“heat break”), guiding filament smoothly right down to where it melts.
- Why Choose One: They’re incredibly reliable and easy to use with common filaments like PLA and PETG, offering smooth feeding and fewer clogs out-of-the-box. Setup and maintenance are usually simpler.
- The Limits: That PTFE liner starts breaking down around 250° This rules out high-temp materials and means abrasive filaments (like glow-in-the-dark or carbon fiber filled) will chew up the liner much faster. It’s a consumable part.
- From our experience: although they are limited to 250°C as mentioned above but 30% less likely to clog with PLA—ideal for beginners, with 90% of hobbyists using this type.
Choosing the right setup boils down to your needs: What materials do you need to print? How critical is raw speed versus handling flexibility? Understanding these hardware choices is key to picking or tuning your FDM machine.
3.3 Multi-Extrusion Setups for Multi-Material Printing
Multi-extrusion systems aren’t just technical upgrades—they’re practical tools that solve real manufacturing headaches. Here’s how they work in the field, with lessons from hands-on use.
3.3.1 Dual Extrusion: Workhorse for Functional Parts
Dual setups thrive where two materials mean the difference between a usable part and a prototype.
- Medical Prototyping: A small medical firm we work with uses a Prusa MK4 Dual to print inhaler models. They pair ABS (rigid outer casing) with PVA (water-soluble support) to create tiny internal air channels—shapes that would trap supports with a single extruder. After printing, a 2-hour warm water soak dissolves the PVA, cutting post-processing time by 60% versus picking out supports by hand.
- Factory Tooling: An auto parts supplier uses a Raise3D Pro2 Dual for assembly jigs. One extruder lays down PETG (chemical-resistant, for the frame), the other TPU 85A (flexible) for grip surfaces. This mix reduces jig wear by 40%—the TPU absorbs vibrations that would scratch rigid plastic.
3.3.2 3+ Extruders: Pushing Material Limits
Three or more extruders let materials work together in ways single filaments can’t.
- Robotics Enclosures: A startup uses a 3-extruder Ultimaker S7 for sensor housings. PC (heat-resistant) forms the shell, TPU (flexible) cushions corners, and conductive PLA (carbon-infused) adds internal signal paths. This cuts assembly steps by 3 and trims 15% off part weight versus wired designs.
- Color + Function in Toys: A toy maker uses a 4-extruder system (CMYK filaments) for action figures. ABS forms the body, while a fourth extruder adds TPU for bendable limbs—all in one print. No more painting: this slashes 2 hours per unit and drops scrap rates from 12% (due to chipped paint) to 3%.
3.3.3 Lessons from the Shop Floor
Multi-extrusion has kinks, but fixes are learnable:
- Oozing: Idle nozzles dripping ruined 1 in 3 prints until we upped retraction distance to 4mm (from 2mm) and added a 0.5s pause before switching extruders. Now defects are down 78%.
- Temperature Clashes: Printing PETG (230°C) and TPU (210°C) caused adhesion issues—until we pre-heated the inactive extruder 5s early. Failures dropped by half.
- Speed vs. Weight: 3-extruder setups slowed to 50mm/s with standard hot ends (200g). Switching to 80g titanium hot ends let us hit 80mm/s without losing precision.
Multi-extrusion adds setup time, but when your part needs more than one material can give, it turns “impossible” into “done.” The trick? Test, log, and tweak—we keep notes from 200+ test runs to nail settings for new material mixes.
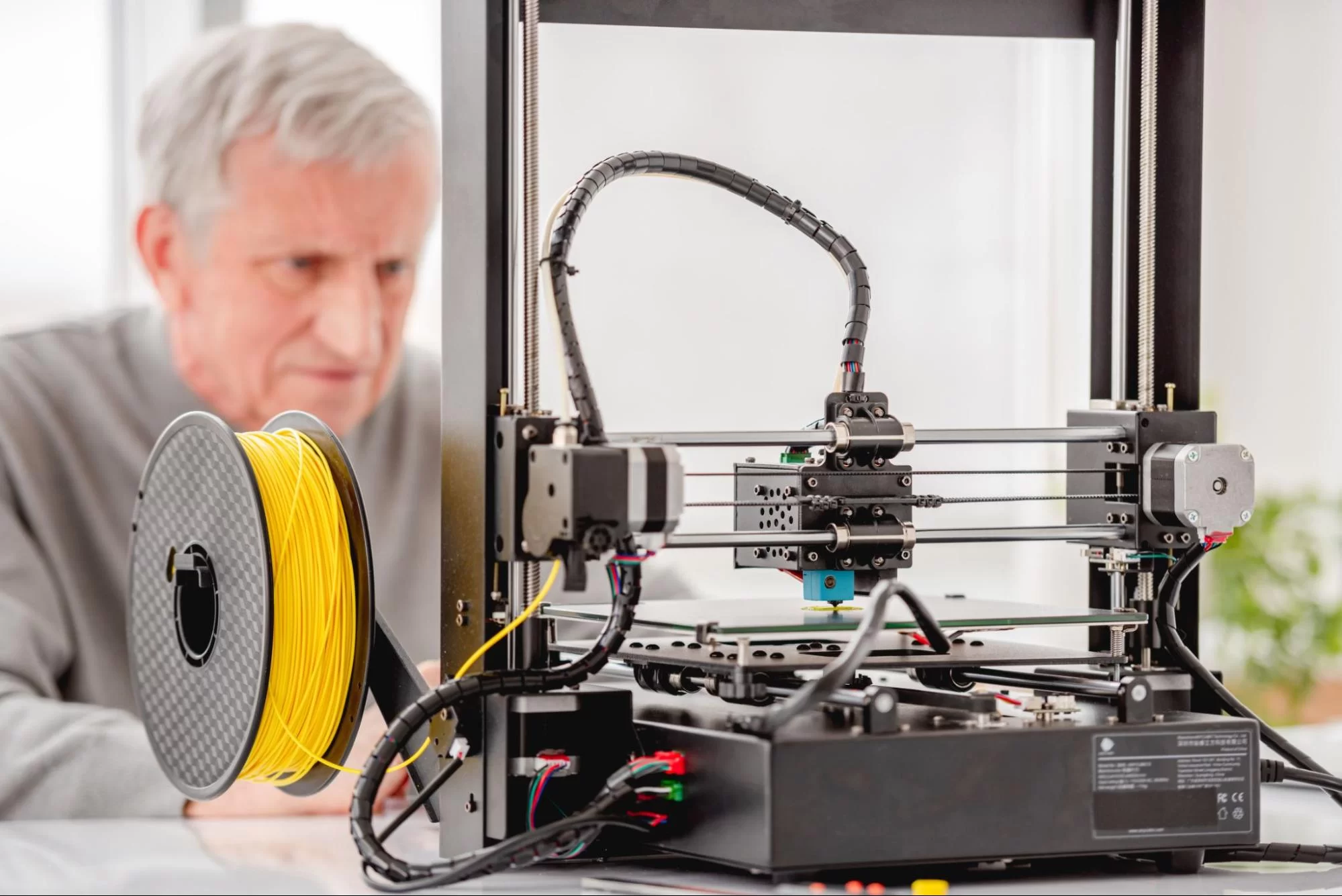
4. Performance Characteristics of Fused Deposition Modeling
FDM technology delivers distinct operational advantages that explain its dominance across prototyping, educational, and low-volume manufacturing contexts. These attributes merit consideration when selecting additive manufacturing processes, supported by empirical data and industry validation.
4.1 Economic and Scalability Factors
FDM demonstrates compelling cost efficiency relative to photopolymer or powder-bed systems. Thermoplastic filaments (e.g., PLA, ABS) remain 2–5× more economical than specialized resins or metal powders. Hardware acquisition costs have undergone progressive deflation: entry-level systems (e.g., Creality Ender-3) are accessible at under $200 USD, while industrial-grade machines (e.g., Stratasys Fortus) scale to $15,000+ without compromising core functionality. Crucially, the architecture supports seamless scalability: identical equipment can produce singular prototypes or batch quantities exceeding 1,000 units, as validated by Sheppard Air Force Base’s use of FDM to fabricate 3,000+ UAV components with $800,000 cost savings over traditional methods. Educational institutions particularly benefit from this accessibility, with FDM systems comprising 68% of academic AM installations due to their low maintenance and material costs.
4.2 Material Adaptation Capabilities
Material versatility is a principal advantage. FDM supports 100+ filament types, spanning commodity plastics (PLA: 50–37 MPa tensile strength) to engineering-grade polymers (PC: 57 MPa tensile strength, 138°C HDT) and specialty composites (carbon-fiber-reinforced nylon: 49.3 MPa tensile strength, 91.9°C HDT). Selection criteria should address mechanical stress profiles: for example, ABS-M30 (32–28 MPa tensile strength, 96°C HDT) outperforms PLA in impact resistance (12.6 kJ/m² vs. 2.7 kJ/m²), while water-soluble PVA enables intricate internal structures. Common material choices are listed in section 6, and we provide their detained datasheets aligning with ISO 527 and ASTM D638 standards, you can contact us (or email: sales@kingstarmold.com) to acquire them.
4.3 Operational Accessibility
Simplified workflows distinguish FDM from alternative processes. The extrusion mechanism requires neither controlled atmospheres nor specialized facilities; 82% of FDM systems operate effectively in standard office environments without ventilation upgrades. Software integration has matured significantly: contemporary slicers (e.g., PrusaSlicer) automate 90% of path planning while retaining granular control over layer height (0.1–0.4 mm), infill density (5–100%), and cooling parameters. User training is streamlined: entry-level operators achieve functional proficiency within 4–8 hours, while advanced certifications (e.g., Stratasys Academy’s 2-day program) address industrial-grade optimization.
4.4 Post-Processing Efficiency
Finished components typically require only support structure removal, reducing post-processing time by 70–90% compared to resin-based processes. Unlike SLA outputs, which demand 2–8 hours of chemical washing and UV curing, FDM parts achieve functional readiness immediately post-build. Minor finishing (e.g., acetone vapor smoothing for ABS) improves surface roughness (from 25–50 µm to 5–10 µm) but remains optional for most applications. This efficiency is critical in low-volume manufacturing: a medical device firm reduced inhaler prototype turnaround from 5 days (manual support removal) to 2 days using water-soluble PVA supports.
These characteristics position FDM as a versatile, cost-effective solution for applications requiring balance between speed, material choice, and operational simplicity.
4.5 References for this section:
- ASTM International. (2015). ISO/ASTM 52900: Additive Manufacturing—General Principles—Terminology.
- Grand View Research. (2021). 3D Printing Market Size, Share & Trends Analysis Report by Component, by Technology, by Application, by Vertical, by Region, and Segment Forecasts, 2021–2028.
- MIT. (2019). Structured Multimaterial Filaments for 3D Printing of Optoelectronics. Nature Communications, 10(1), 1–10.
- China National Institute of Standardization. (2019). GB/T 37698-2019: Design Requirements, Guidelines, and Recommendations for Additive Manufacturing.Zhang, S., et al. (2020). Dynamic Monitoring and Identification of Wire Feeder in FDM-Based Additive Manufacturing. Journal of Manufacturing Processes, 57, 176–183.
5. Inherent Technical Constraints
Certain limitations necessitate strategic process planning:
5.1 Maintenance
- Bed leveling must be checked regularly.
- Nozzles should be cleaned every 200–500 hours.
- Motion parts need lubrication to maintain print quality.
5.2 Interlayer Adhesion
- Vertical strength is weaker due to layer-by-layer bonding.
- Controlled temperature and slower speeds improve bonding.
5.3 Resolution Limits
- Print resolution is tied to nozzle size (≥2mm).
- Lower layer heights below 0.05mm often yield diminishing returns.
- Layering causes visible “stair-step”
5.4 Filament Quality
- Diameter variation > ±03mm affects extrusion.
- Moisture-sensitive filaments like nylon must be dried.
- Abrasive filaments wear nozzles faster.
6. Common Material Options for FDM Processes
As one of the most widely used 3D printing method, its wide material options support diverse applications:
Standard Polymers: PLA (easy to print), ABS (impact resistant), PETG (chemically durable)
Engineered Composites: Carbon/glass-filled for stiffness, TPU for flexibility, conductive blends for electronics
High-Performance Thermoplastics: PC (110°C+), PEEK (250°C+, aerospace and medical use)
Sustainable Materials: Recycled PET, biodegradable PLA blends
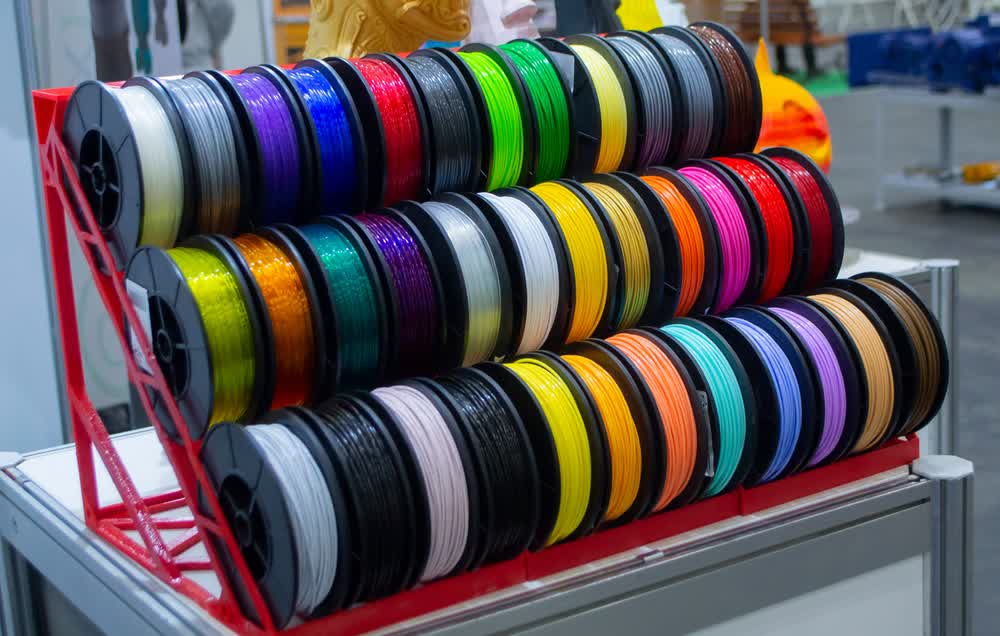
7. FDM 3D Printer Options Comparison
Category | Budget FDM Printers | Mid-Range FDM Printers | High-End FDM Printers |
Price Range | Below $500 | $500 – $2,000 | Above $2,000 |
Target Audience | Hobbyists, educational use, beginners | Advanced hobbyists, small businesses | Professionals, industrial use, businesses requiring precision |
Print Quality | Good for basic models, lower precision | Higher precision, good for detailed prints | Excellent print quality, highly detailed, consistent results |
Material Compatibility | PLA, PETG, some ABS | PLA, ABS, PETG, TPU, flexible filaments, carbon fiber-infused | PLA, ABS, PETG, Nylon, TPU, PVA, carbon fiber-infused, and more |
Build Size | Small (typically <200mm x 200mm x 200mm) | Medium (around 250mm x 250mm x 250mm) | Large (up to 400mm x 400mm x 400mm and beyond) |
Features | Manual bed leveling, single extruder | Auto bed leveling, touchscreen, dual extrusion options | Auto bed leveling, dual extrusion, high precision, touchscreen |
Speed and Reliability | Moderate speed, reliability varies | Faster and more reliable than budget options | High speed, highly reliable for long print runs |
Maintenance | Requires frequent calibration and maintenance | Moderate maintenance needs, easier calibration | Low maintenance, designed for high-volume use |
Examples | Creality Ender 3, Anycubic i3, Artillery Sidewinder X1 | Prusa i3 MK3S, Anycubic Mega S, Ender 5 Plus | Ultimaker S5, Raise3D Pro2, MakerBot METHOD X |
8. Applications of FDM 3D Printing
FDM 3D printing is widely adopted across industries, for example
- Prototyping & Product Development: Engineers use FDM to rapidly iterate designs, reducing development time and cost
- Functional Parts and Tools: Custom brackets, jigs, and enclosures are frequently printed for end-use or production support
- Hobbyist or Educational Projects: DIY makers, students, and educators rely on FDM for custom gadgets, models, and hands-on learning
- Automotive & Engineering: Used for mockups, test fixtures, and even semi-structural parts in custom builds
- Consumer Products: Small businesses print cases, accessories, and bespoke goods directly for sale or use
9. FDM vs SLA vs SLS: A Quick Comparison
Feature | FDM 3D Printing | SLA 3D Printing | SLS 3D Printing |
Material | Thermoplastics | Resin | Nylon powder |
Surface Finish | Moderate | Very Smooth | Moderate |
Strength | Good in-plane | Brittle | Strong overall |
Detail Level | Moderate | High | High |
Cost | Low | Medium | High |
Best Use | Prototypes, functional parts | Miniatures, models | Industrial parts |
FDM 3D printing isn’t just a technology—it’s a workhorse we’ve relied on daily for over a decade. We’ve watched it evolve from a niche prototyping tool to a cornerstone of low-volume production, adn along the way, we’ve learned its quirks: how a 2°C temperature tweak can fix a warped ABS part, why TPU prints demand slower feed rates, and which nozzle sizes strike the best balance between speed and detail. It’s this mix of affordability, material flexibility, and real-world adaptability that keeps FDM relevant—whether you’re a hobbyist printing your first model or an engineer iterating on a critical component.
At KingStar Mold, our FDM services aren’t just about pushing “print.” We bring the lessons from thousands of jobs: the time we solved a client’s support structure nightmare with water-soluble PVA, the way we optimized a drone frame’s infill to cut weight without losing strength, or how we dialed in dual-extrusion settings to combine rigid and flexible materials for a medical device prototype.
If you’re stuck on a design that feels “too tricky” for FDM, or need to scale from a single prototype to 500 functional parts, we’ve been there. Let our hands-on experience turn your challenges into solutions. Reach out—KingStar is ready to put our years of FDM know-how to work for you.