- Overview of cost-effective injection molding
- Importance of choosing the right factory for your needs
- Key Factors Affecting Injection Molding Costs
- Comparing Injection Molding Costs Globally
- China: The Global Leader in Injection Molding
- Mexico: A Viable Alternative for North American Businesses
- India: Low Labor Costs and Growing Manufacturing Capabilities
- Southeast Asia: A Rising Hub for Injection Molding
- Key Benefits of Choosing Cost-Effective Factories
- Challenges to Consider When Choosing Cost-Effective Factories
- Conclusion
Overview of cost-effective injection molding
Plastic injection molding is one of the most widely used manufacturing processes for producing high-precision plastic parts, especially in industries such as automotive, electronics, and consumer goods. Typically, the cost of injection molding varies from a small-scale 3D printing for 100$ to a high-volume complex multi-cavity steel molding for 100,000$+.
Cost-effective injection molding refers to the ability to produce these parts at a competitive price while maintaining high quality and efficiency. Achieving cost-effectiveness in injection molding involves optimizing various aspects, such as material selection, mold design, production processes and so on.
For businesses looking to scale production, choosing the right injection molding factory can make a significant difference in both cost and the quality of the final product.
Importance of choosing the right factory for your needs
Selecting the right factory for your injection molding needs is crucial for long-term success. A factory like us that understands your unique requirements can offer customized solutions, ensuring that production costs are kept under control without compromising on quality. Additionally, a reliable and cost-efficient partner can provide timely delivery, consistent results, and the flexibility to adjust to changing market demands, making them an indispensable part of your manufacturing strategy.
Key Factors Affecting Injection Molding Costs
Injection molding involves multiple cost factors, each of which significantly impacts the final price of production. These factors include material costs, machine efficiency, mold design, labor costs, and the geographical location of manufacturing. Understanding each of these elements can help businesses make more informed decisions and optimize their overall production expenses.
1. Material Costs
Material costs are one of the most significant contributors to the total expense of injection molding. These costs consist of both metal costs for mold manufacturing and plastic resin costs for injection molding. Both the availability and quality of raw materials influence these costs.

Plastic Resin Prices: Recycled vs. Virgin Materials
Plastic resin prices vary greatly depending on whether the material is recycled (reprocessed plastic) or virgin (new) plastic. The price fluctuations are influenced by multiple factors such as the material type, quality, market demand, and regional supply conditions. Below is an overview of the prices for recycled plastic pellets and virgin plastic pellets.
-
Recycled Plastic Pellet Prices
Recycled plastic pellets, also known as regrind or reprocessed material, have prices that are heavily influenced by the recycling market, and can vary significantly over time. For example, in Guangdong province (as of September 23, 2024), the approximate prices of various recycled plastic pellets were as follows (excluding tax):
ABS White Pellets: $1.00 – $1.03 USD per kg
PE High-Density White, Grade 1: $0.94 – $0.96 USD per kg
PET Blue-White Clean Flakes (3D): $0.73 – $0.74 USD per kg
PET Clean Bottles (White, De-labeled, De-capped): $0.68 – $0.74 USD per kg
PVC Pure White Pipe (Shredded): $0.37 – $0.38 USD per kg
EPS White High-Quality Material (Cold-pressed Blocks): $0.58 – $0.59 USD per kg
PP White Pellets: $0.81 – $0.82 USD per kg
Note: The prices above are based on the market at a specific point in time, and are subject to fluctuation due to factors like market supply and demand, raw material prices, and quality variation.
-
Virgin Plastic Pellet Prices
Virgin plastic pellets are made from newly produced plastic resin and generally come with a more stable pricing structure than recycled materials. However, prices can still vary significantly based on resin type, quality, and market conditions. Below are some examples of virgin plastic pellet approximate prices (range estimates):
Polypropylene (PP): Price can range from $1 USD to up to $10 USD per kg, depending on factors such as market conditions, product specifications, and quality.
Polycarbonate (PC): PC is an engineering plastic and tends to have a higher price compared to general-purpose plastics. The price is generally above $10 USD per kg.
Polyethylene (PE): PE prices vary depending on the type and intended use. High-Density Polyethylene (HDPE) and Low-Density Polyethylene (LDPE) have different price ranges.
HDPE: $0.96 – $1.24 USD per kg
LDPE: $1.10 – $1.37 USD per kg
Plastic pellet prices are subject to constant fluctuation and depend on several market factors including material type, quality, region, and the supply-demand balance. Understanding these factors can help businesses plan their material procurement strategies more effectively. If you need up-to-date pricing, it’s recommended to consult suppliers directly or monitor industry news and reports for real-time data.
Impact of High-Volume Production:
High-volume production enables manufacturers to negotiate discounts with material suppliers. For example, bulk purchasing of resin or mold steel might allow for a 5%-10% discount, significantly reducing material costs in the long run.
2. Tooling Costs
As mentioned in the introduction, tooling costs are often one of the largest cost drivers in the injection molding process. The cost of creating and maintaining molds can vary significantly based on the method used for mold production and the materials selected.
Methods of Tooling Production
Injection molds are typically created using one of three main methods: CNC machining, Electrical Discharge Machining (EDM), and 3D printing. Each method has its advantages and cost implications depending on the complexity of the mold design, material choice, and production volume.
CNC (Computer Numerical Control) machining is the most common method used to create high-precision aluminum and steel molds. CNC machines remove material from a workpiece through rotating tools, allowing for the production of complex cavity designs. However, the process may require multiple tool changes, which can slow down the production time and increase costs, especially as the mold complexity rises. CNC machines require skilled labor and dedicated space, which means many companies opt to outsource mold production to specialized service providers.
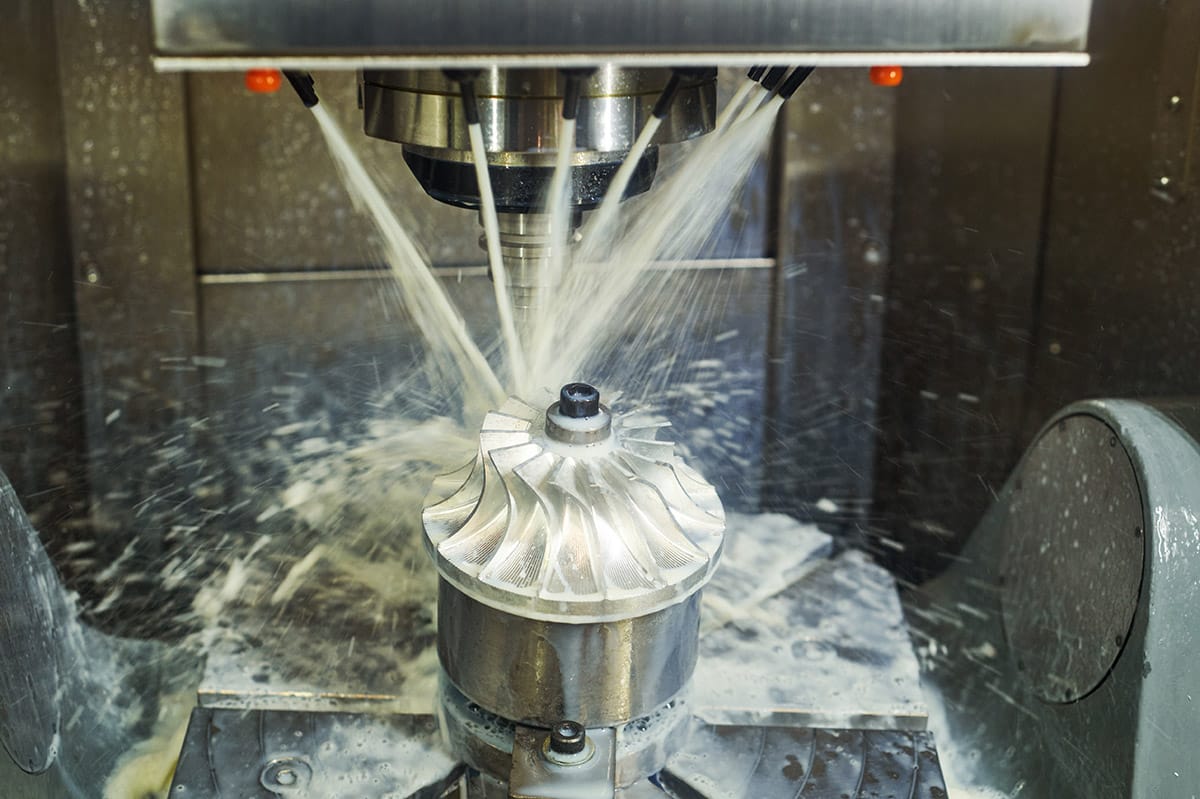
Material Costs: The material used in CNC machining molds is typically high-quality tool steel, such as P20, H13, or S7, which is durable and able to withstand high pressure during the injection molding process. The cost of tool steel can vary, but in general, prices range from $4 – $10 USD per kilogram depending on the type and quality of the steel.
EDM is used to create highly intricate mold designs that cannot be easily replicated by standard machining methods. The process involves using electrical discharges between an electrode and the workpiece to erode material, gradually forming the desired mold shape. EDM is known for its precision and often doesn’t require additional post-processing. Similar to CNC machining, EDM is an industrial process commonly outsourced by many companies to specialized workshops.
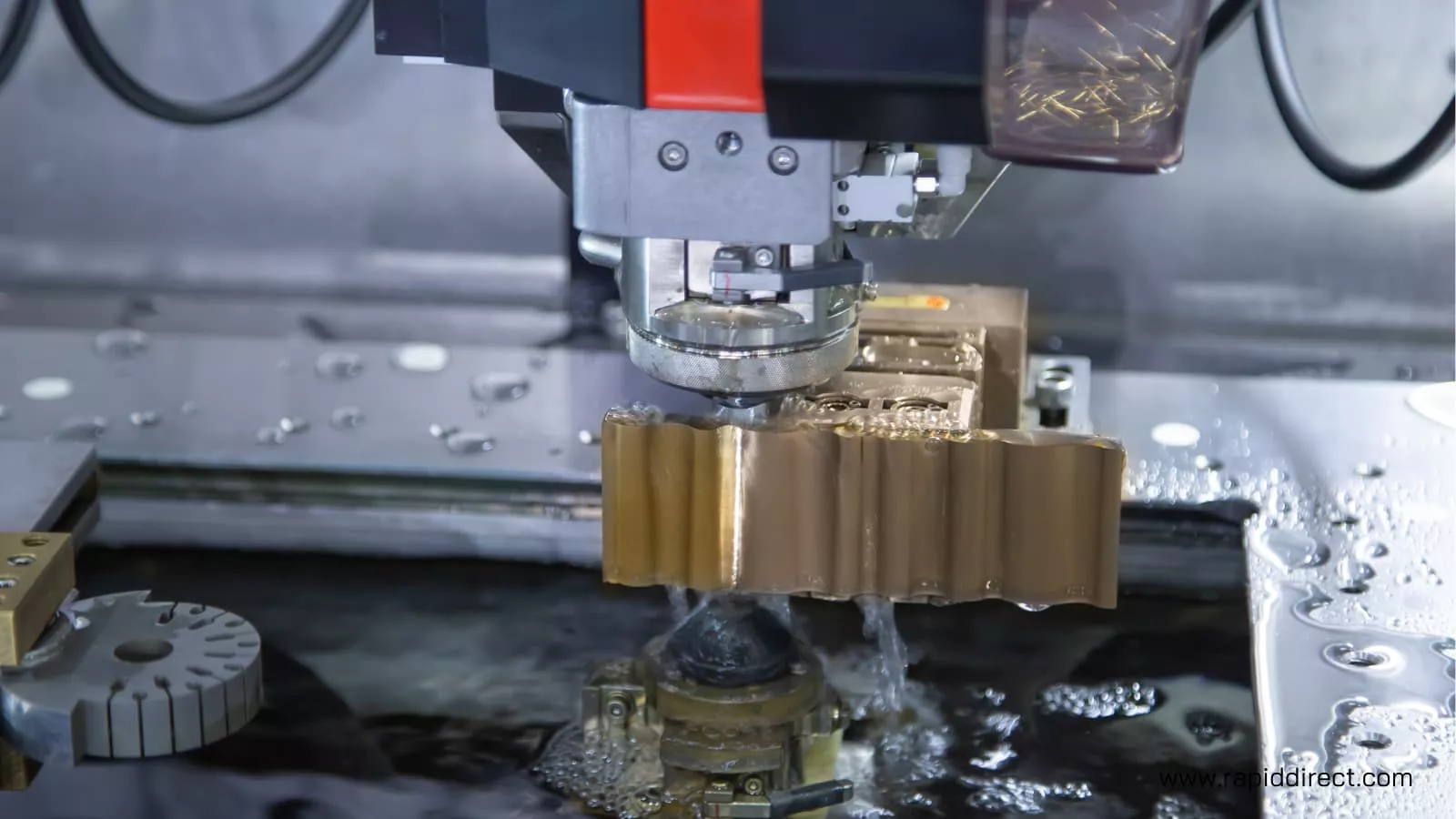
Material Costs: For EDM, the electrodes are often made from copper or graphite, which have their own associated costs. Copper electrodes, for example, can cost around $10 – $15 USD per kilogram, depending on market conditions.
3D printing has emerged as an efficient and cost-effective solution for producing injection molds, especially for low to medium volume production runs. 3D printed molds can be created quickly with minimal equipment, saving both CNC machining time and labor costs. The flexibility of 3D printing allows manufacturers to test and iterate designs before committing to expensive traditional tooling. One of the most popular 3D printing technologies for injection molding is Stereolithography (SLA), known for its smooth surface finish and high accuracy, which is critical for mold transfer and ejection.
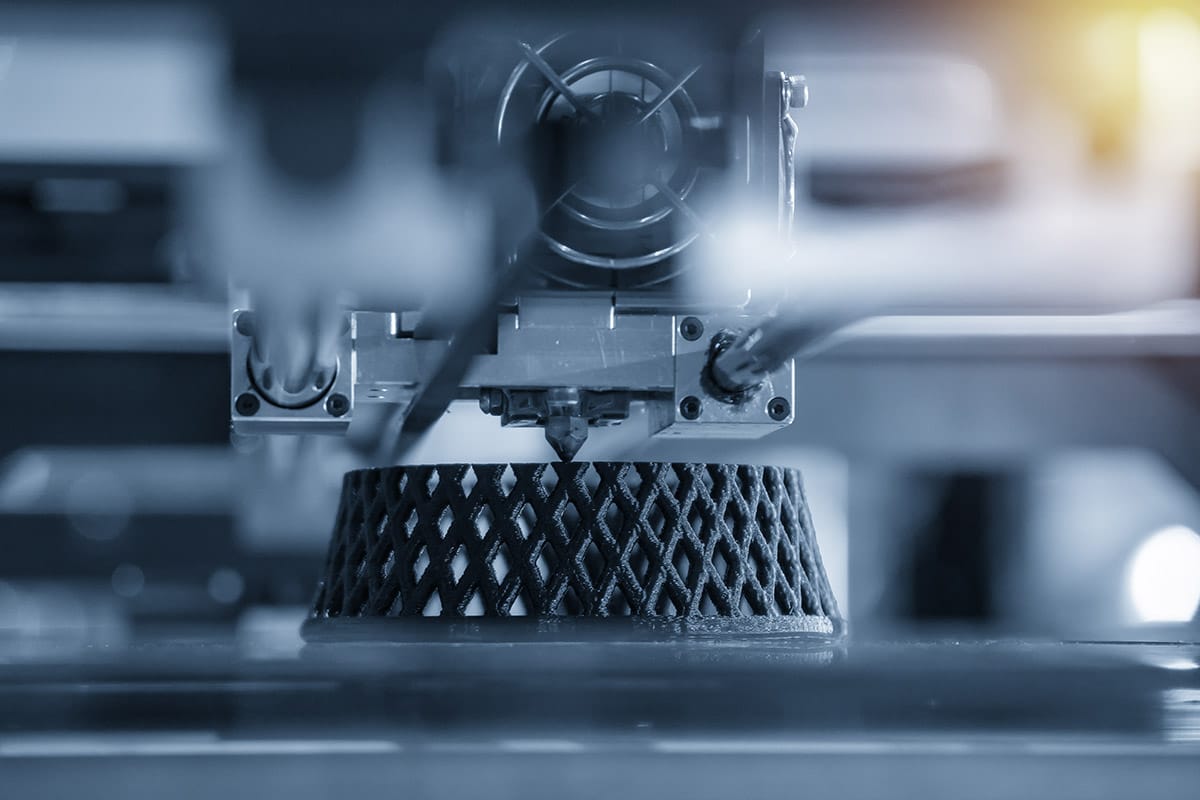
Material Costs: The cost of 3D printing materials varies depending on the resin used. High-performance resins for SLA printing, which offer durable and accurate results, can range from $100 – $400 USD per kilogram. The price will depend on the resin’s performance properties, such as heat resistance and tensile strength.
Choosing the Right Tooling Method
When deciding on the tooling method, manufacturers need to weigh several factors:
- Complexity of the Mold Design: Highly intricate designs may require EDM or CNC machining, as 3D printing may not always provide the required precision and durability for certain molds.
- Production Volume: CNC and EDM are better suited for high-volume production, where mold durability and longevity are critical. However, for small or prototype runs, 3D printing provides flexibility and a lower upfront cost.
- Material Selection: The choice of materials for mold production can impact both tooling costs and production efficiency. Tool steels like H13 are commonly used in CNC and EDM methods due to their excellent wear resistance, whereas 3D printed molds are often made from specialized resins or metal-filled filaments.
3. Machine Power and Efficiency
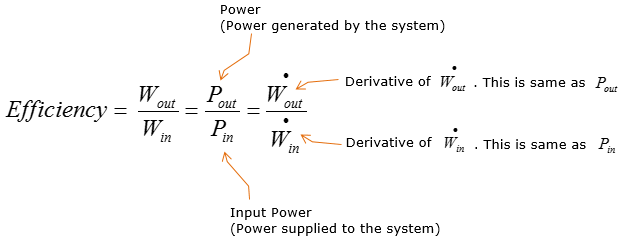
The power and efficiency of machines used in injection molding directly affect both production time and energy consumption, which in turn impacts the overall cost of manufacturing.
-
Energy Consumption:
Machines with servo-electric drives tend to consume 30%-40% less energy compared to traditional hydraulic machines.
For example, a typical hydraulic injection molding machine may use 15 kWh for every 1,000 units produced. In comparison, a servo-driven machine would use only 9 kWh for the same batch.
-
Energy Cost Calculation:
If the electricity rate is $0.1 per kWh, the energy cost for 1,000 units would be:
Hydraulic Machine:
15kWh×0.1USD/kWh=1.5USD
Servo-Driven Machine:
9kWh×0.1USD/kWh=0.9USD
By using more efficient machines, energy consumption is reduced, saving 40% in energy costs.
-
Production Time:
The larger the production volume, the lower the unit cost. Optimizing the production process to reduce cycle times increases efficiency and reduces costs. For example, a 20% reduction in cycle time can lower the overall cost per unit by the same percentage, leading to substantial savings in high-volume production.
4. Mold Design and Complexity
The complexity of a part’s design and size significantly affects the overall cost of injection molding. Larger parts, intricate designs, and additional mold features all contribute to higher tooling costs.
-
Part Size
The size of the part being molded directly impacts the size of the required mold. Larger parts require bigger molds to accommodate them, leading to increased material usage and longer production cycles. Compared to producing the same design but at a smaller scale, larger molds generally result in higher costs. This increase is due to the larger amount of material needed and the longer processing time required to complete each production cycle.
-
Part Design Complexity
Parts with complex geometries require more intricate mold designs to accurately form the part. Mold designs typically consist of two main sides: the A-side and the B-side.
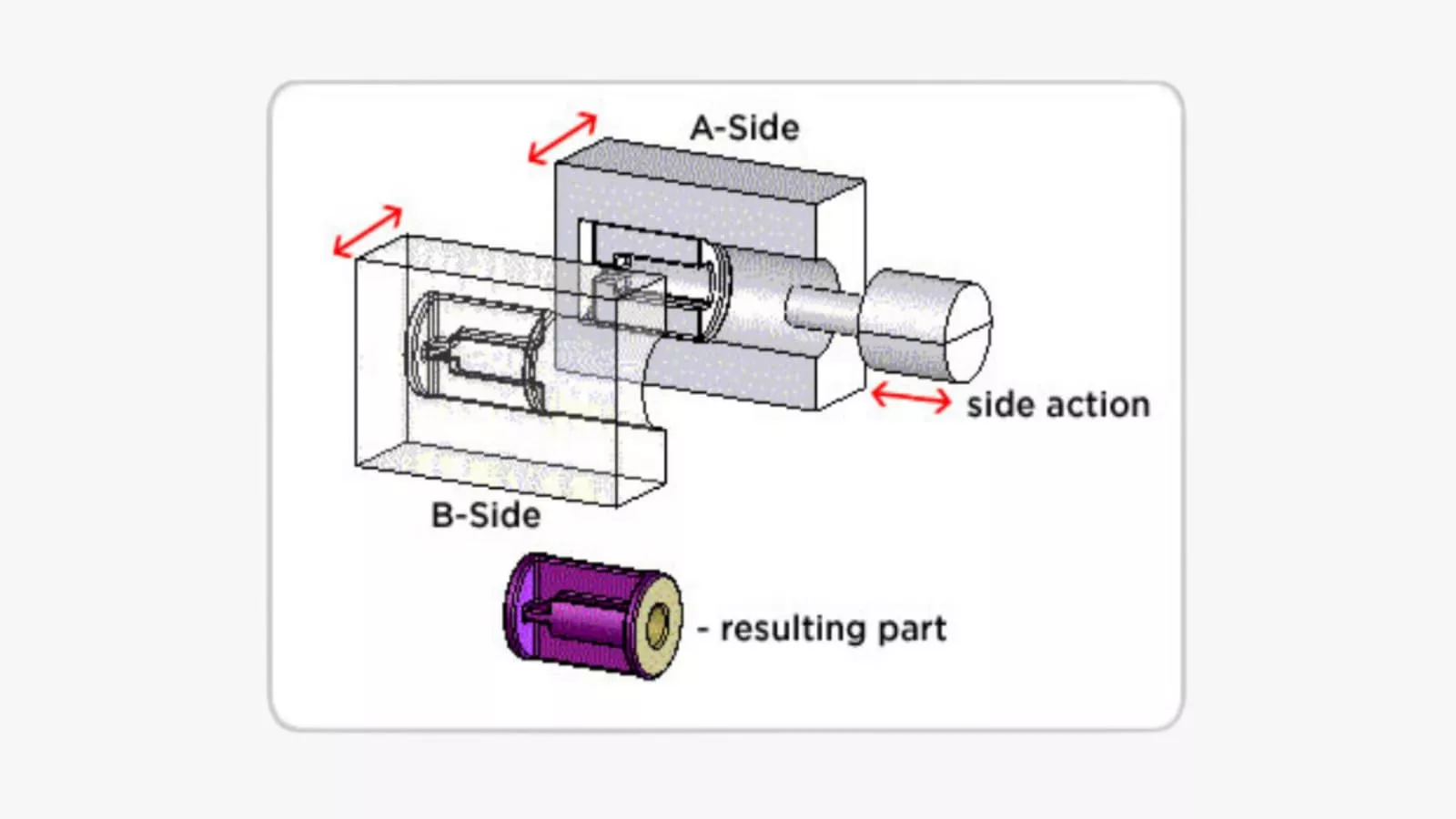
A-side: This is the decorative side that the user sees. It needs to be smooth and aesthetically pleasing, often requiring additional precision in the molding process.
B-side: This side includes the hidden structural components, such as ribs or bosses, that support the functionality of the part. The B-side is typically rougher in surface finish compared to the A-side.
Parts with complex A-side and B-side designs usually increase mold costs due to the additional materials and labor required. For example, designs with undercuts or complex geometries may require sliding actions or core pulls in the mold, which adds further complexity and cost.
-
Part Volume and Mold Cavity
The volume of the part affects the mold cavity size, and thus, the total tooling cost. A larger part volume requires a larger cavity, which in turn increases the pressing time. The more cavities needed for multi-cavity molds, the longer the mold filling and curing time, ultimately extending the production cycle. This additional time increases overall costs, as slower production means higher labor and machine time costs.
By considering these factors—part size, design complexity, and cavity volume—manufacturers can better understand the cost drivers for mold creation. These elements directly impact the tooling and production costs and should be carefully considered during the design phase to optimize manufacturing efficiency and cost-effectiveness.
5. Labor Costs
Labor costs are an important factor in mold manufacturing and injection molding. Skilled workers are needed to operate machines, supervise production, and ensure quality control. Labor costs vary depending on location.
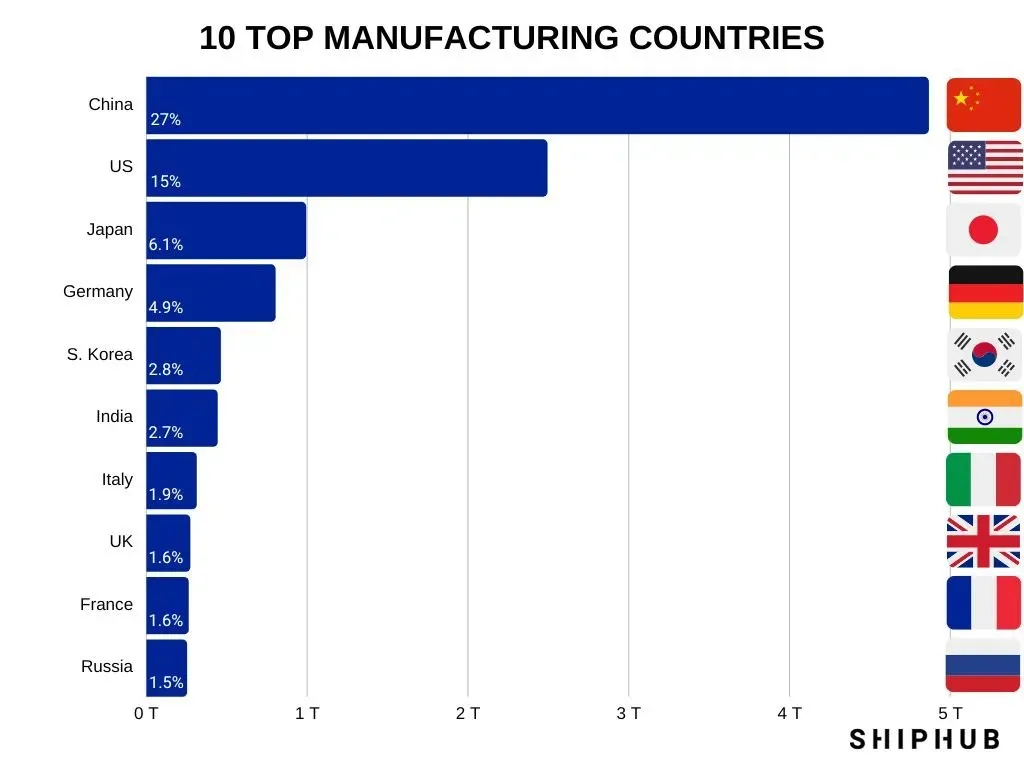
-
Cost Differences by Region:
- Southeast Asia: Labor costs are relatively low, with workers earning between $200 and $500 per month. Countries like Vietnam, Thailand, and Indonesia have become attractive manufacturing hubs due to their competitive labor rates.
- Eastern Europe: Labor costs are higher than in Southeast Asia but still lower than in Western Europe or the U.S., ranging from $700 to $1,500 per month. Countries like Poland, Hungary, and Romania offer competitive prices while maintaining a skilled workforce.
- North America/Europe: Labor costs in countries like the U.S. or Germany can range from $3,000 to $5,000 per month, making it a more expensive option for manufacturers compared to regions like Southeast Asia and Eastern Europe.
- Mexico: Labor costs in Mexico are more affordable than in the U.S. or Canada, typically ranging from $500 to $1,000 per month. The proximity to North America and favorable trade agreements, such as the USMCA, make it an attractive option for North American businesses.
- China: China remains one of the world’s leading manufacturing hubs, with labor costs typically ranging from $600 to $1,500 per month. While costs have been rising in recent years, the country’s well-established infrastructure, skilled workforce, and manufacturing expertise make it a highly competitive option for a wide range of industries.
- India: Labor costs in India are very low, with workers typically earning between $150 and $400 per month. India’s growing manufacturing capabilities, along with government incentives and industrial zones, make it an increasingly popular choice for cost-effective production.
Outsourcing production to a region with lower labor costs (e.g., Southeast Asia) could reduce labor costs by as much as 60%.
6. Manufacturing Location
The geographical location of the manufacturing facility has a direct impact on the overall costs due to transportation, logistics, and proximity to suppliers.
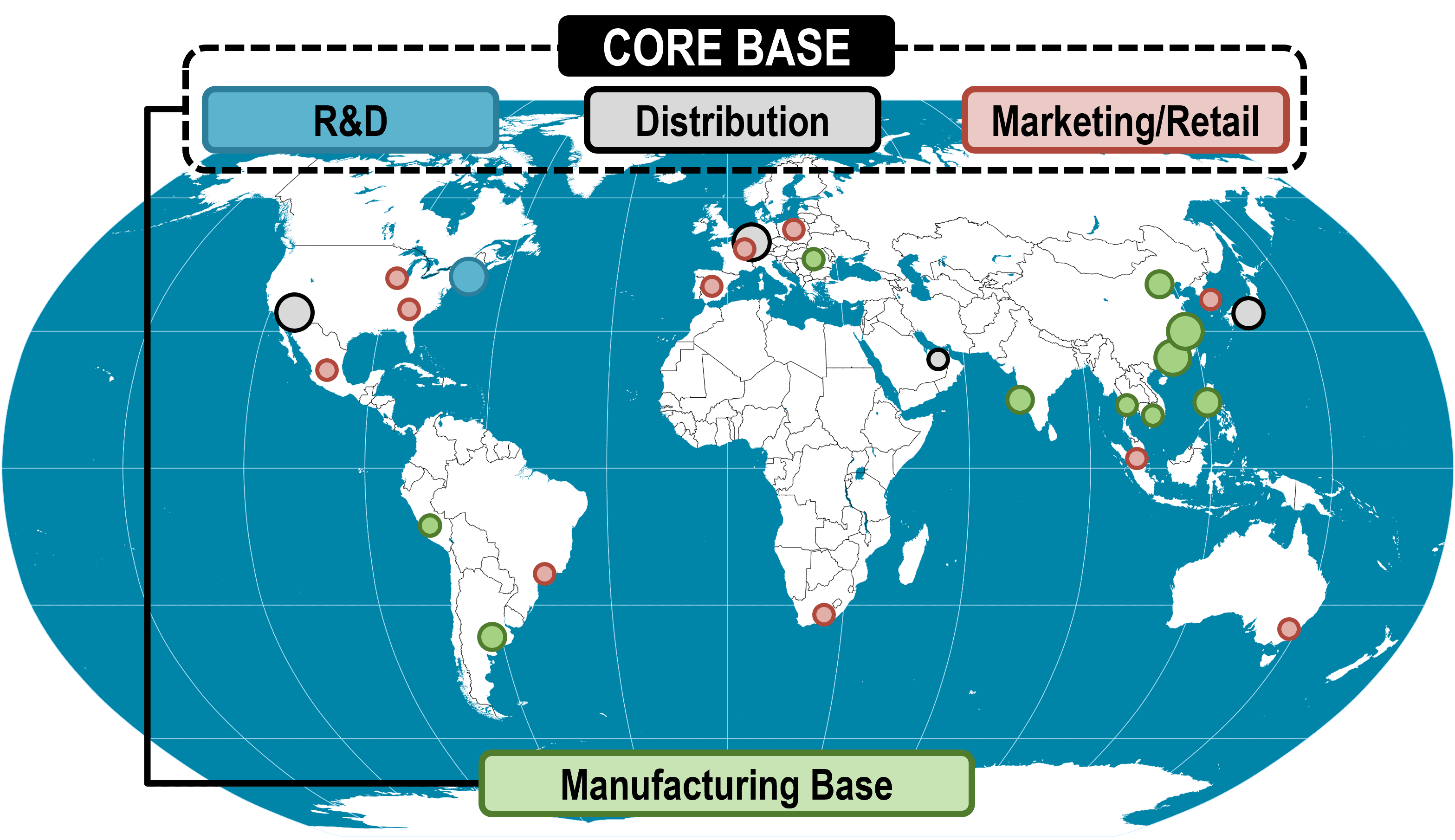
-
Transportation and Logistics:
Shipping costs can account for a significant portion of the total cost, especially for international shipments. For example, shipping a 500 kg pallet of plastic resin from the U.S. to Europe might cost $300 – $500.
Proximity to suppliers can reduce lead times and costs. For example, a U.S. company manufacturing in Mexico benefits from lower shipping costs and faster delivery times.
Example: A U.S.-based company manufacturing in Mexico might save 30%-40% on logistics costs compared to sourcing from a supplier in Asia, due to the proximity of the two countries.
Comparing Injection Molding Costs Globally
When evaluating the costs of injection molding, it’s important to understand how regional differences can impact overall expenses. Factors such as labor rates, material availability, technology access, and economic conditions vary widely between developed and developing countries, influencing the cost structure for manufacturers.
Differences Between Developed and Developing Countries
In developed countries, labor costs are typically higher due to more stringent regulations, skilled labor requirements, and higher standards of living. These costs are reflected in the price of injection molding services. However, such countries often benefit from advanced technologies, higher precision, and faster delivery times, which can justify the premium cost for certain industries requiring high-quality standards.
In contrast, developing countries often have lower labor costs, which can significantly reduce the overall production cost. This makes them appealing for companies seeking cost-effective manufacturing options. However, challenges like access to high-quality materials, longer shipping times, and less advanced manufacturing technology may offset some of the savings. Despite these factors, many developing countries are still able to offer competitive pricing, particularly for larger production runs.
Cost Comparison Overview: China vs. Mexico vs. India vs. Southeast Asia
The cost of injection molding varies significantly between regions due to different economic conditions, labor costs, and access to resources. Below is an overview of the cost comparison between China, Mexico, India, and Southeast Asia, which will be explored in more detail in the following sections.
- China: Known for its advanced manufacturing infrastructure and cost-effective production capabilities, China remains a global leader in injection molding services. While labor costs have been rising in recent years, China’s scale of operations and mature supply chains help keep overall production costs competitive.
- Mexico: Proximity to the United States, lower shipping costs, and competitive labor rates make Mexico an attractive choice for North American companies. While labor is cheaper than in the U.S., it is generally higher than in China, but its strategic location provides faster lead times and reduced logistics costs.
- India: India offers lower labor costs compared to China and Mexico, but challenges such as inconsistent quality, longer lead times, and limited access to advanced molding technologies can sometimes increase the total cost of production.
- Southeast Asia: Countries like Vietnam, Thailand, and Indonesia provide low labor costs and can be cost-effective for high-volume manufacturing. However, the availability of raw materials and shipping times may impact overall cost savings, especially for regions further from key global markets.
In the next section, we will delve deeper into the specific cost comparison factors for each of these regions, highlighting key differences in material costs, labor, technology, and infrastructure.
China: The Global Leader in Injection Molding
China continues to be a global leader in injection molding, offering cost-effective solutions with significant advantages for high-volume production. While there are many benefits, companies must also navigate challenges when outsourcing to Chinese manufacturers.
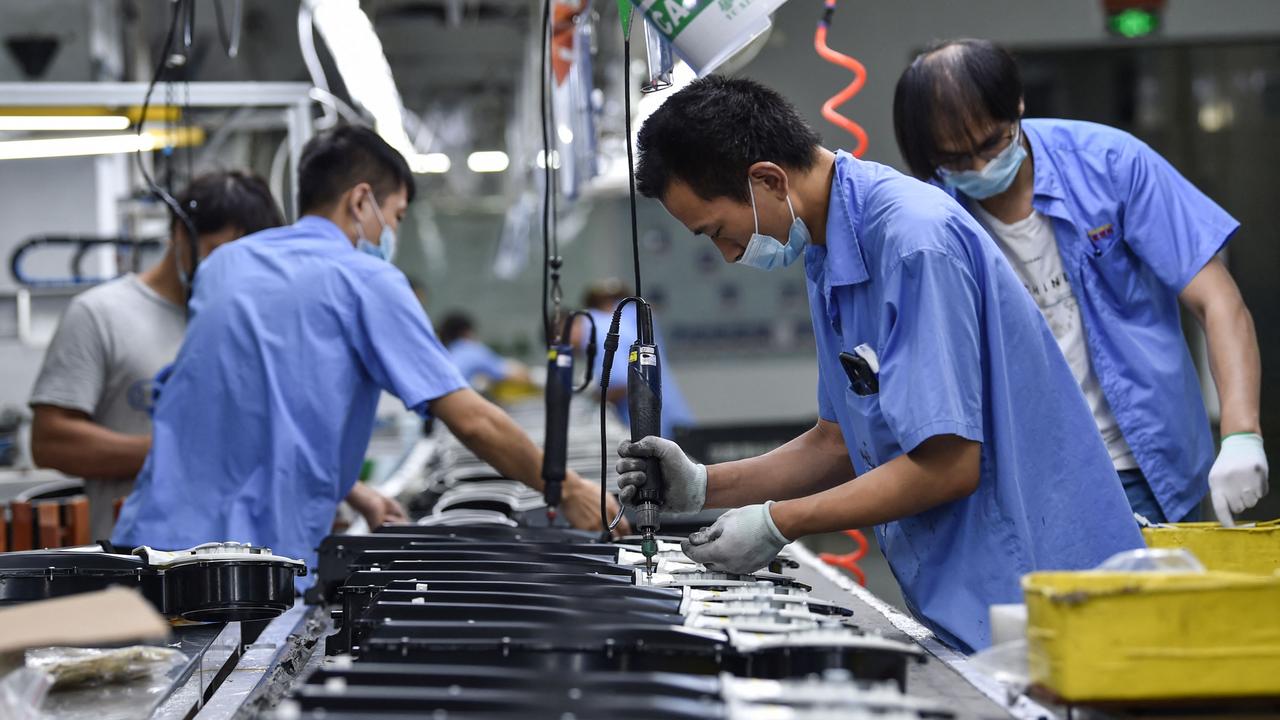
Cost Advantages of Chinese Factories
- Lower Labor Costs: China’s labor rates are still lower than in developed nations, making it a more affordable option for mass production.
- Large-scale Production: Chinese factories benefit from economies of scale, which help reduce costs for large volume orders.
- Efficient Supply Chains: The well-developed infrastructure in China ensures quick access to raw materials and reduces shipping costs for bulk orders.
Leading Companies in Injection Molding Industry
Several prominent companies in China are leading the injection molding industry with their expertise and competitive pricing:
- KingStar Mold: Like many top on-demand high precision part manufacturers, KingStar Mold leverages China’s cost advantages to offer precision injection molding services for industries such as automotive, household products, and more.
- TK Group: Specializing in automotive and household components, they offer high precision and efficient production.
- Siler Basis: Known for their ability to handle complex designs, they serve industries ranging from electronics to consumer goods.
KingStar Mold’s ability to deliver high-quality, cost-effective solutions makes it competitive with other leading companies in the region.
Challenges Faced by Companies Outsourcing to China
Despite China’s competitive advantages, there are a few challenges when outsourcing production:
- Quality Control: Companies like Huangyan Zhongtai Mould have developed strong quality assurance processes to minimize defects, while KingStar Mold also offers rigorous quality control to ensure products meet international standards.
- Longer Lead Times: With shipping delays and customs clearance, companies can experience longer delivery times. However, some companies, including Xiamen L&L Mould, have optimized their supply chains to minimize these delays, and KingStar Mold follows similar practices to keep production on schedule.
- Communication Barriers: The language gap can sometimes create misunderstandings, but leading companies, including KingStar Mold, prioritize seamless communication to avoid such issues.
By partnering with experienced and reliable manufacturers in China, companies can overcome these challenges and benefit from the country’s cost-effective injection molding capabilities.
Mexico: A Viable Alternative for North American Businesses
Mexico has become an increasingly attractive destination for North American businesses looking for cost-effective injection molding solutions. Its proximity to the U.S. offers distinct advantages in terms of logistics and transportation costs, making it an ideal location for companies aiming to streamline their manufacturing and reduce shipping times.
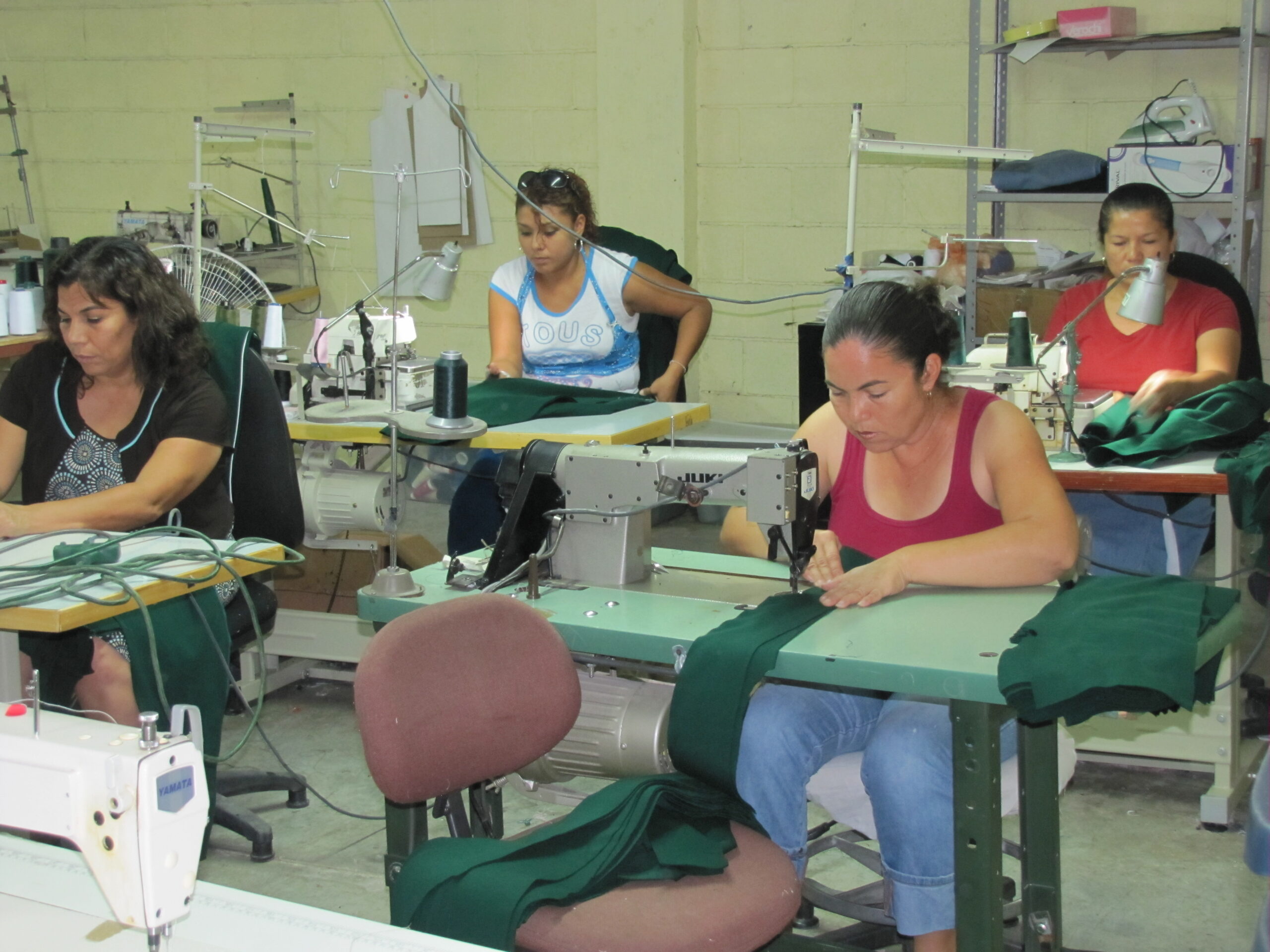
Lower Transportation Costs and Proximity to the U.S.
- Geographical Advantage: Mexico’s proximity to the United States allows companies to significantly reduce transportation costs and delivery times compared to Asian alternatives. This makes it an excellent choice for businesses in the U.S. and Canada looking to shorten their supply chain.
- Faster Turnaround: With direct land transportation routes between Mexico and the U.S., businesses can reduce lead times, which is crucial for companies operating on tight schedules.
Reduced Shipping Costs: For North American companies, manufacturing in Mexico eliminates the long-distance shipping costs associated with outsourcing to Asia, providing a more affordable and time-efficient option.
Competitive Labor Costs and Quality Standards in Mexico
- Affordable Labor: Mexico’s labor costs are lower than those in the U.S., but workers are highly skilled in injection molding and other manufacturing processes, making it a competitive alternative to more expensive regions.
- High-Quality Manufacturing: Mexico has invested in its manufacturing capabilities, with many factories meeting international quality standards such as ISO certifications. This allows businesses to ensure that their products are of high quality while benefiting from lower production costs.
- Skilled Workforce: Mexico has a growing workforce of skilled technicians and engineers, which contributes to the high standards of manufacturing in the country.
Leading Companies in Injection Molding Industry
Several Mexican companies have made a name for themselves in the injection molding industry, offering cost-effective solutions for various industries:
- Rosti Mexico: Known for its work in the automotive and electronics industries, Rosti Mexico specializes in high-quality, precision molding at competitive prices.
- Protolabs Mexico: A leading name in the rapid prototyping and injection molding industry, offering fast and efficient solutions for custom parts and low-volume production.
By choosing Mexico, North American businesses can tap into competitive labor costs, faster shipping times, and a high level of manufacturing expertise, making it a compelling alternative to overseas production.
India: Low Labor Costs and Growing Manufacturing Capabilities
India has emerged as a key player in the global manufacturing landscape, particularly for industries seeking cost-effective injection molding solutions. With its competitive labor costs and a growing base of advanced manufacturing capabilities, India is a viable option for businesses aiming to balance affordability with quality.
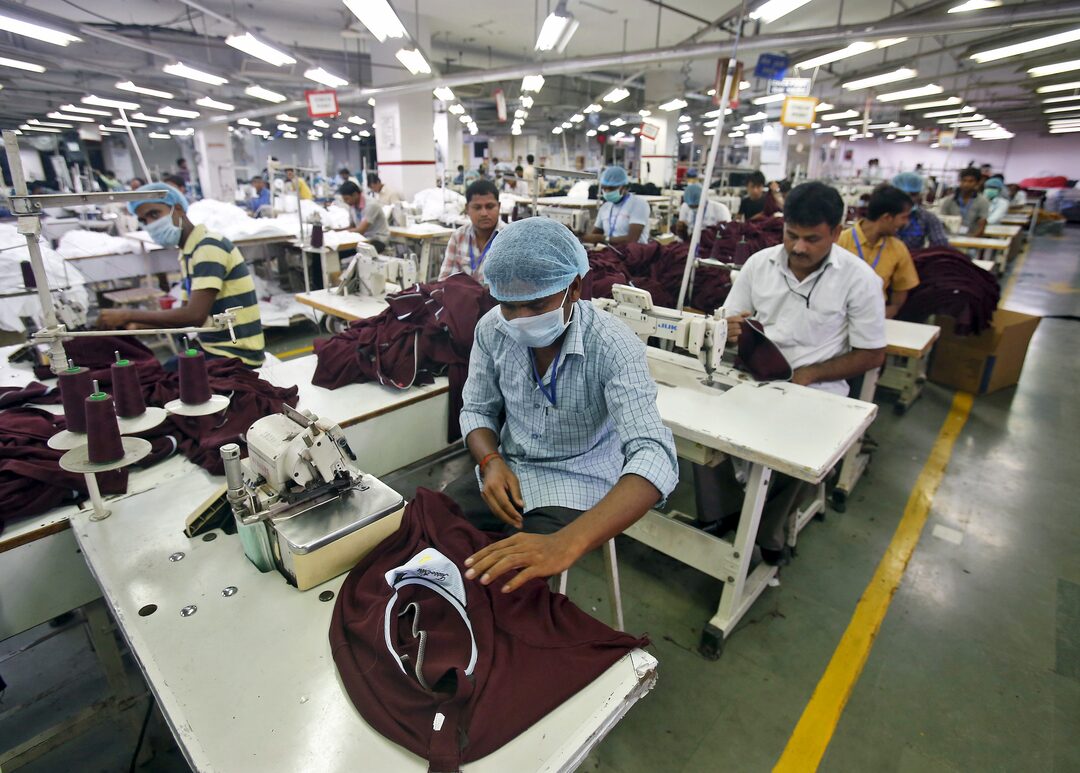
Benefits of Outsourcing to India
- Cost-Effective Labor: India is well-known for its low labor costs, making it an attractive option for businesses looking to reduce production expenses. Compared to Western countries, India offers significant savings, especially in industries such as injection molding, where skilled labor is required for precise manufacturing.
- Skilled Workforce: India has a large, young, and educated workforce. Many engineers and technicians are trained in advanced manufacturing techniques, ensuring that quality is not compromised despite the lower labor costs.
- Rapid Scaling: India’s vast labor pool and increasing industrialization allow businesses to scale their production quickly, meeting rising demand without sacrificing cost efficiency.
Government Incentives and Industrial Zones
- Make in India Initiative: The Indian government has actively encouraged foreign investment through its “Make in India” initiative, which offers a range of incentives for manufacturers. These include tax exemptions, duty cuts on imported machinery, and subsidies for certain industries.
- Special Economic Zones (SEZs): India has established numerous SEZs that provide favorable conditions for manufacturing companies. These zones offer tax holidays, streamlined customs processes, and a stable regulatory environment, which significantly lowers operational costs.
- Policy Support: The government’s push towards digitization, ease of doing business reforms, and infrastructure improvements make India a growing manufacturing hub for injection molding companies.
Leading Companies in Injection Molding Industry
India boasts a number of leading companies in the injection molding sector, including:
- Bharat Group: Known for its high-precision injection molding solutions, Bharat Group has established itself as a key player in sectors like automotive, electronics, and consumer goods.
- Rajoo Engineers: Specializing in a wide range of injection molding and plastic processing machinery, Rajoo Engineers offers comprehensive solutions for manufacturers across various industries.
- Laxmi Industries: Focused on the production of high-quality plastic products, Laxmi Industries uses state-of-the-art injection molding techniques to serve industries like automotive and medical.
India is increasingly recognized as a cost-effective, high-quality manufacturing destination for injection molding, thanks to its combination of low labor costs, government incentives, and growing industrial infrastructure. For businesses seeking a balance between cost savings and high manufacturing standards, India offers significant advantages.
Southeast Asia: A Rising Hub for Injection Molding
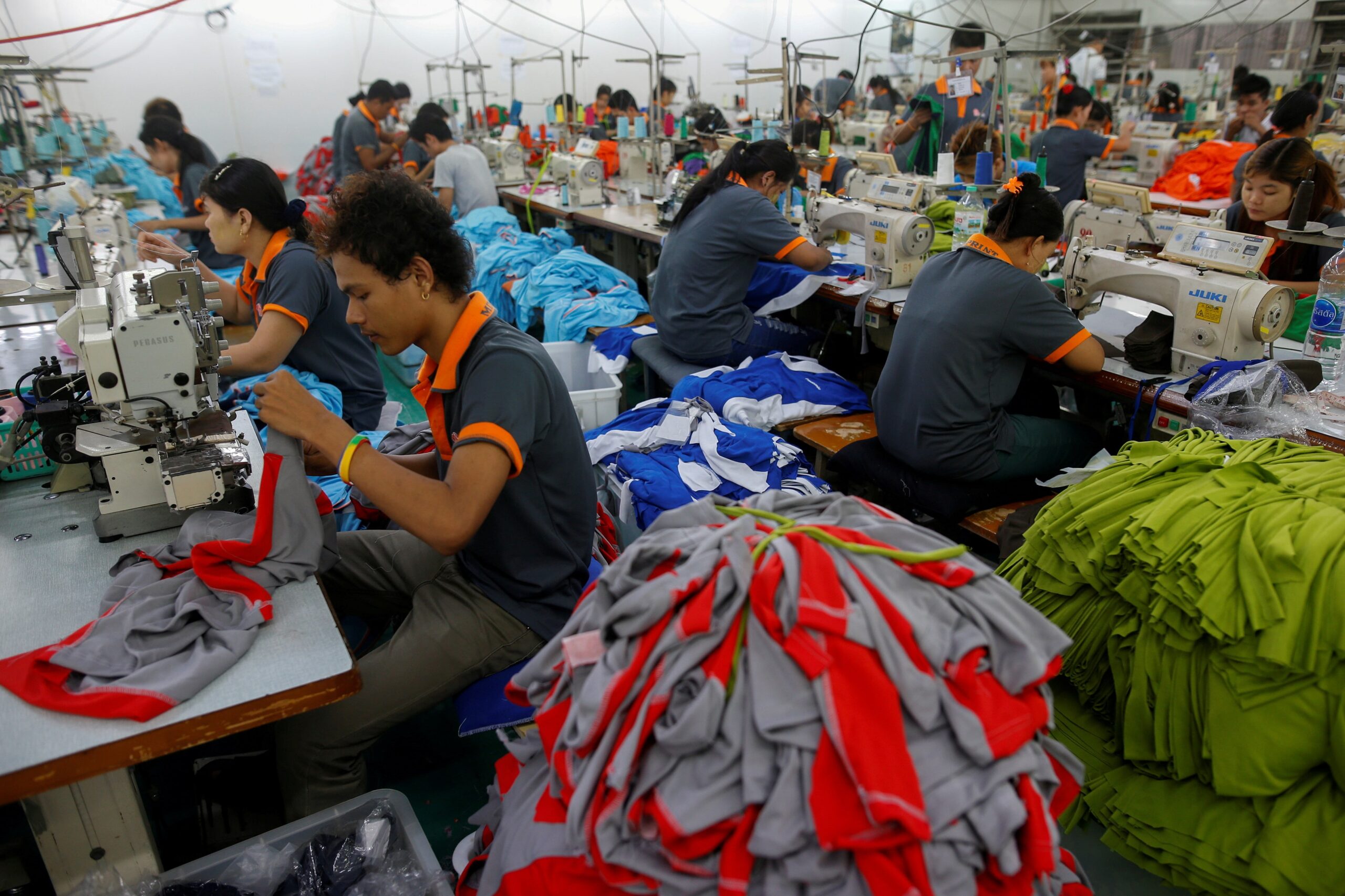
The Role of Vietnam, Thailand, and Indonesia
Southeast Asia, particularly countries like Vietnam, Thailand, and Indonesia, has become an increasingly important hub for injection molding due to their cost-effective manufacturing environments and improving industrial capabilities. These countries benefit from a combination of low labor costs, favorable geographic locations, and a growing infrastructure for international trade.
- Vietnam has established itself as a rising star in the injection molding industry, with a competitive labor force and growing expertise in manufacturing sectors like electronics, automotive, and consumer goods.
- Thailand offers a well-developed industrial base, particularly in automotive and electronics components, benefiting from its extensive experience in high-precision manufacturing.
Indonesia is expanding its capacity in injection molding, focusing on consumer goods, packaging, and automotive parts, driven by an increasing demand for these products.
Trade Agreements and Their Impact on Manufacturing
Southeast Asian countries are taking advantage of regional trade agreements to enhance their global competitiveness in the injection molding industry. For example:
- The ASEAN Free Trade Area (AFTA) enables tariff reductions between member countries, fostering a more seamless trade environment and reducing overall manufacturing costs.
- Bilateral agreements between Southeast Asian countries and major markets such as the U.S. and the EU have also facilitated growth in the injection molding sector by reducing tariffs and simplifying export processes.
Leading Company in Injection Molding Industry
Several companies in Southeast Asia are becoming leaders in the injection molding industry, providing high-quality services and products. Notable companies include:
- Siam Polymers Co., Ltd. in Thailand, which specializes in automotive and consumer goods production through advanced injection molding processes.
- Vina Plastic Co., Ltd. in Vietnam, known for its work in manufacturing parts for the electronics and automotive industries, delivering both cost efficiency and quality.
- Daya Plast Indonesia in Indonesia, which has grown rapidly in recent years, providing injection molding services to the automotive, household, and packaging sectors.
As the Southeast Asian injection molding industry continues to grow, it presents an attractive alternative for companies seeking a balance between cost efficiency, quality, and a diverse range of products.
Key Benefits of Choosing Cost-Effective Factories
When selecting a manufacturing partner, the goal is to find a factory that offers high-quality products at competitive prices. Cost-effective factories not only help reduce expenses but also provide additional advantages that enhance overall business performance. Here are three key benefits to consider:
- Lower Production Costs
Cost-effective factories help reduce the overall expenses of manufacturing by offering lower labor and material costs. These savings are passed on to businesses, allowing them to lower their product prices or improve profit margins. - Increased Production Efficiency
Many cost-effective factories focus on optimizing production processes. Streamlined operations and use of modern technologies can result in quicker turnaround times and fewer errors, leading to faster deliveries and consistent product quality. - Flexibility and Scalability
Cost-effective factories often have the ability to scale production quickly to meet demand. They can easily adjust their output, which is particularly beneficial for businesses that experience fluctuating market needs or seasonal spikes in production.
By understanding these benefits, businesses can make more informed decisions when choosing a manufacturing partner. Opting for cost-effective factories not only cuts down on operational expenses but also ensures improved efficiency and the ability to respond swiftly to changing market conditions.
Challenges to Consider When Choosing Cost-Effective Factories
While cost-effective factories offer significant advantages, there are a few challenges that businesses must consider to avoid potential risks. Two common concerns are intellectual property (IP) protection and ensuring quality control and consistency.
Intellectual Property Concerns
Outsourcing to cost-effective factories, especially in regions with less stringent IP regulations, can pose risks related to the protection of proprietary designs and technologies. Businesses must take extra precautions, such as drafting clear contracts, conducting regular audits, and establishing secure communication channels.
KingStar Mold’s Approach:
At KingStar Mold, we prioritize the protection of our clients’ intellectual property. We enforce rigorous confidentiality contracts and employ secure communication channels to guarantee the protection of sensitive information throughout the entire manufacturing process. Additionally, our team is well-versed in international IP laws, ensuring compliance with global standards.
Quality Control and Consistency Issues
Maintaining consistent quality across all units is crucial, particularly when working with factories that operate at lower costs. Variations in materials, equipment, and processes can lead to inconsistent product quality.
KingStar Mold’s Approach:
KingStar Mold implements robust quality control systems to monitor every stage of production. We use advanced technologies such as real-time quality tracking and automated inspection tools to ensure high standards are maintained. Our experienced quality control team conducts thorough checks, from material sourcing to final product delivery, ensuring that each batch meets or exceeds client expectations.
By addressing these challenges proactively, businesses can benefit from cost-effective manufacturing without compromising on intellectual property protection or product quality.
Conclusion
In summary, choosing cost-effective factories for injection molding offers several key advantages, including long-term cost savings, faster production lead times, and access to advanced manufacturing capabilities. However, businesses must be mindful of challenges such as intellectual property concerns and quality control issues. By carefully selecting a factory with a strong focus on security and consistency, these challenges can be effectively managed.
At KingStar Mold, we address these concerns by ensuring strict IP protection and implementing comprehensive quality control systems, enabling our clients to reap the benefits of cost-effective manufacturing without compromising on quality.
Selecting the right factory is essential for optimizing production costs while maintaining high standards. By carefully evaluating factors such as location, expertise, and the factory’s commitment to quality and IP protection, businesses can make informed decisions that drive success in the competitive world of injection molding.
If you’re looking for a reliable and cost-effective injection molding partner, KingStar Mold is here to help. Contact us today to discuss your needs and how we can support your manufacturing goals.