Vapor Smoothing for 3D Printing
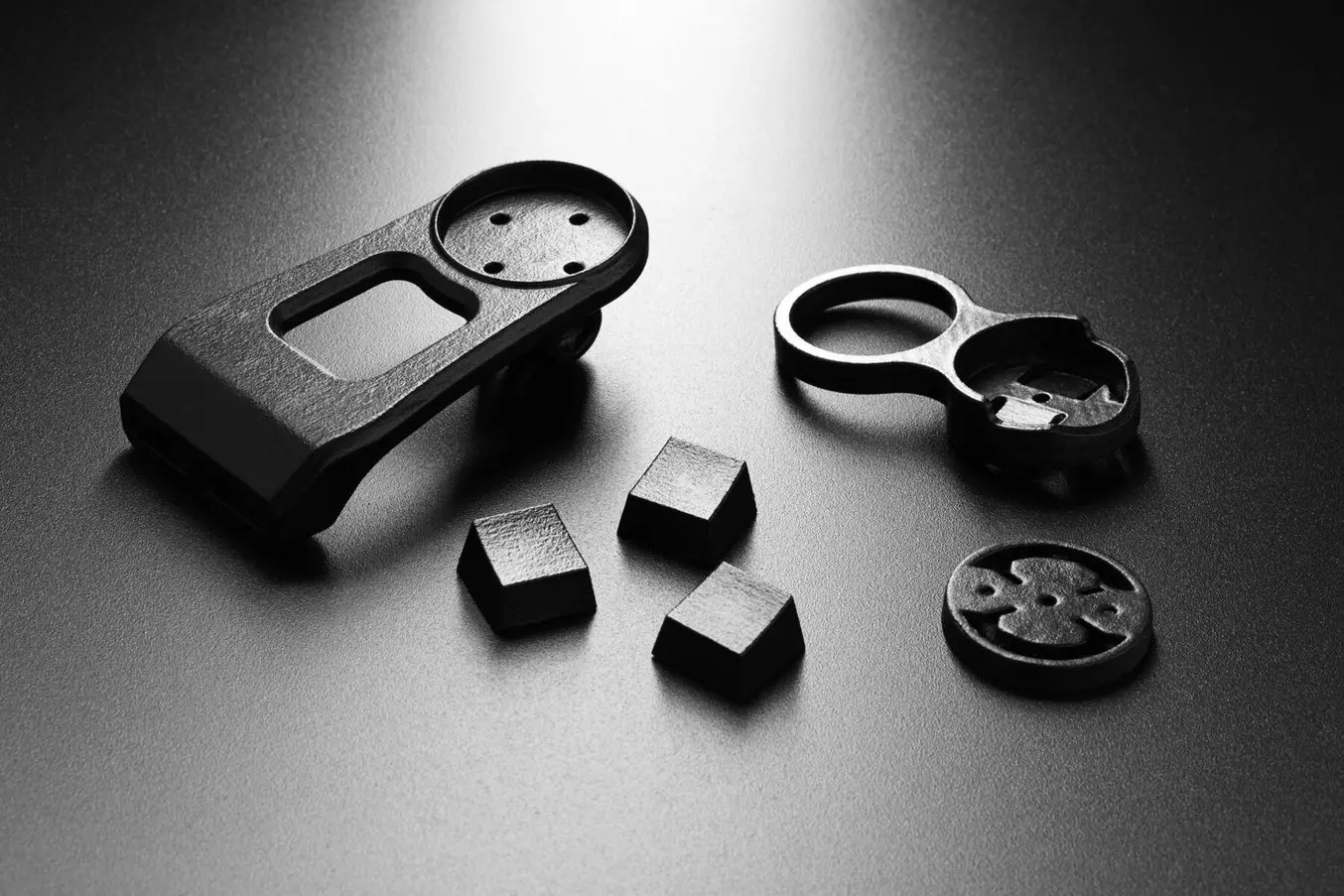
Vapour Smoothing Overview
Vapor smoothing is an advanced post-processing technique designed to enhance the surface quality of 3D printed parts. By applying vapor to the part’s surface, this process effectively smooths out rough textures and visible layer lines, resulting in a polished and professional finish. It is particularly beneficial for parts that require an aesthetically pleasing appearance or improved surface performance, such as those used in consumer goods or high-end prototypes. In addition to its visual benefits, vapor smoothing can also increase the part’s durability by improving surface strength and wear resistance.
Improved Surface Finish
Vapor smoothing significantly reduces surface roughness, resulting in a much smoother, more polished appearance. This process enhances the overall aesthetics of 3D printed parts by minimizing visible layer lines and imperfections. The smoother surface is ideal for applications requiring high-quality visuals, such as consumer products or prototypes.
Enhanced Hygiene and Moisture Resistance
Vapor smoothing helps to reduce bacterial growth and moisture absorption, making it beneficial for parts used in sensitive environments. Studies have shown a 60% reduction in MRSA bacteria growth on Nylon 12 parts after vapor smoothing. This makes it an excellent choice for medical or food-related applications, where hygiene is crucial.
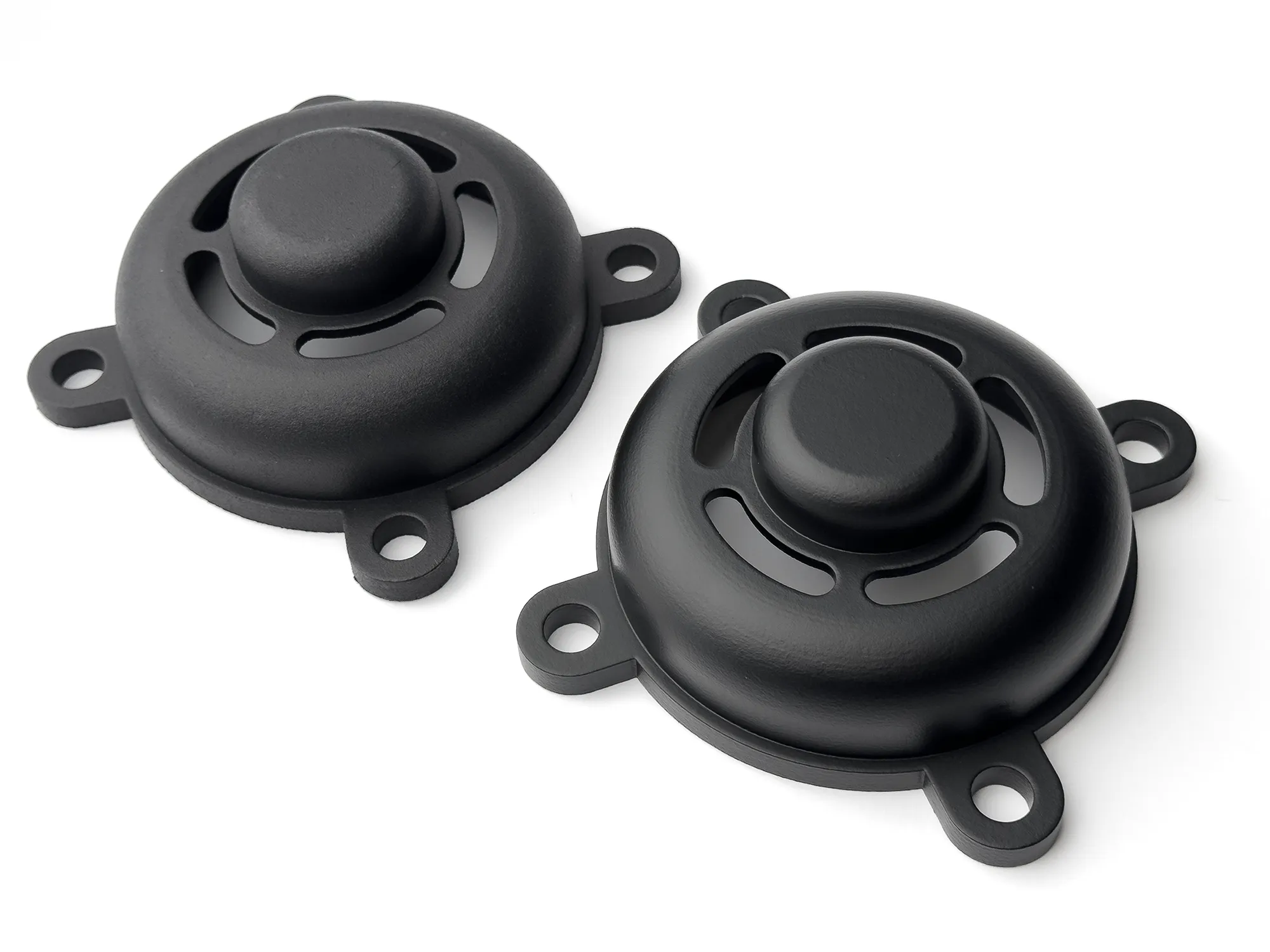
Standard Finished | Vapour Smoothed
Uniform Coverage for Complex Geometries
Unlike other coating methods, vapor smoothing can reach all surfaces of a part, including areas that are difficult to access or out of direct sight. This ensures consistent smoothness across the entire part, improving the finish even in intricate designs with complex geometries. This capability is a significant advantage for parts with internal features or tight spaces.
Retention of Mechanical Properties
Vapor smoothing improves the visual appeal and surface quality without compromising the part’s mechanical strength or functionality. Tests have shown minimal changes in the mechanical properties of parts after smoothing. This means that parts can achieve better aesthetics while maintaining their structural integrity and performance.
Considerations Before Vapor Smoothing
Vapor Smoothing Settings
Different vapor smoothing systems and manufacturers utilize unique parameters and solvents for the smoothing process. Key variables that are often adjusted include temperature and pressure settings, with each SLS material requiring a distinct profile to ensure optimal results. In collaboration with Formlabs, AMT has created specific profiles for all Formlabs SLS materials, which can be accessed by contacting AMT directly for specialized machine settings.
Impact of Part Geometry
The geometry of the part, such as wall thickness and overall size, can influence the vapor smoothing process and should be considered when configuring the smoothing profile. For example, AMT has different machine profiles for thin Nylon 12 Powder parts (with walls under 2 mm thick) and thicker parts (over 3 mm thick), ensuring the settings are tailored for each design’s specific requirements.
Racking and Attachment Marks
Parts are typically suspended from metal wire racks during the vapor smoothing process, which requires areas to attach wires or clips. Though the marks left by these attachments are minimal, it’s possible to eliminate them by adding a connection point to the design or, for large production runs, linking multiple parts together during the design phase.
Solvent Pooling Management
To prevent the accumulation of vapor solvent in concave areas, parts with cup-like features should be positioned facing downwards to promote runoff. In cases where design flexibility allows, it may be beneficial to avoid including such features altogether to optimize the vapor smoothing process.
Safety and Installation Considerations
AMT provides a detailed guide for preparing facilities to safely install and operate PostPro SF machines, ensuring compliance with safety standards. This guide also includes operator safety training, which is critical for reducing risks associated with the process. For a deeper understanding of the results from collaborative testing on surface properties, antimicrobial benefits, and moisture absorption, refer to AMT and Formlabs’ white paper for detailed insights.
Design Guide for Vapour Smoothing
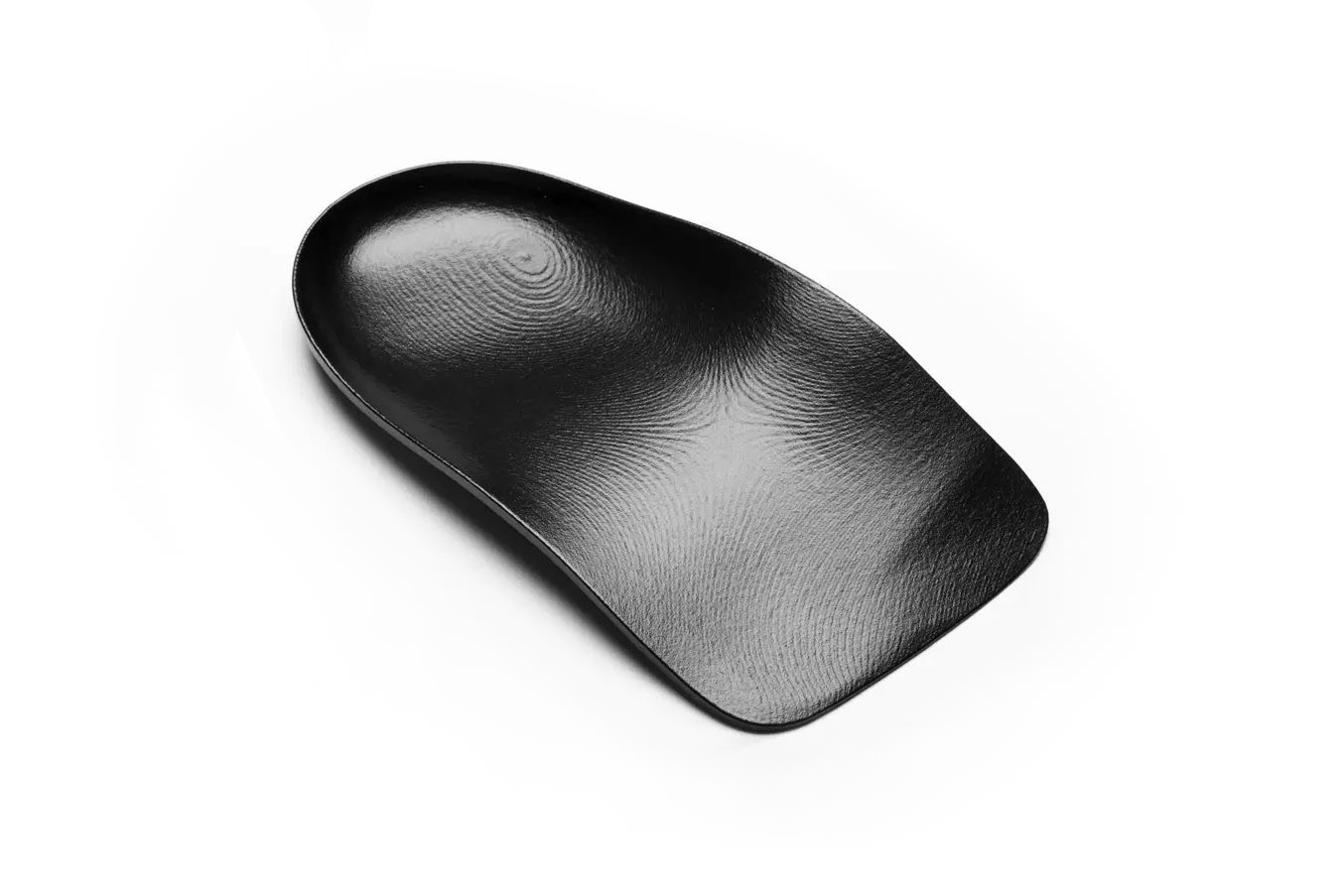
Automotive Components
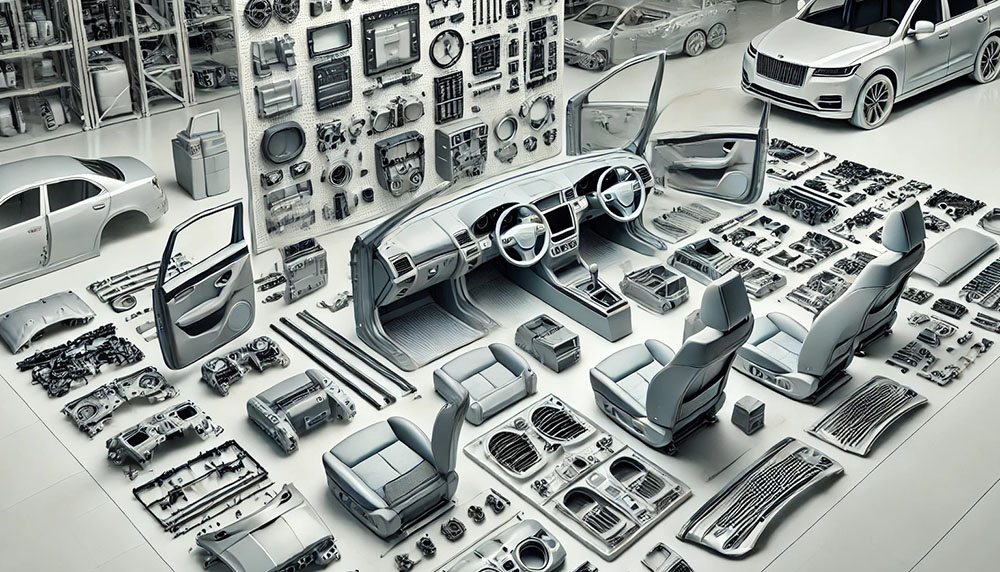
Consumer Goods
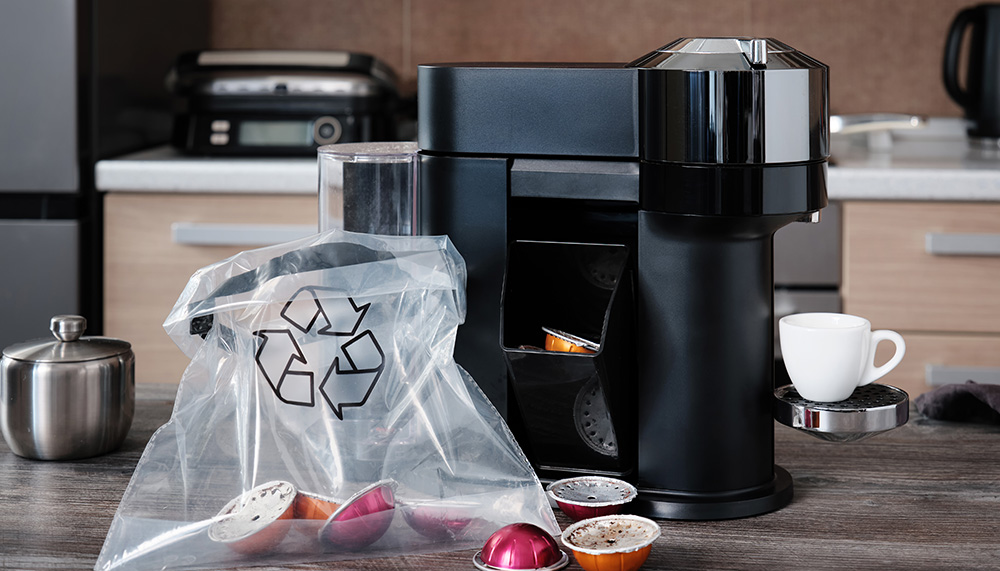
Industrial Equipment
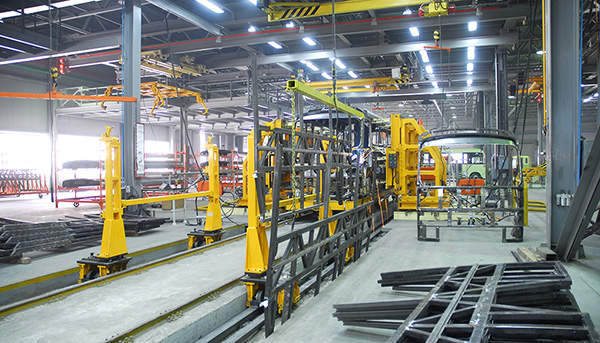
Medical Devices

Cost Example of Vapor Smoothing
The cost of vapor smoothing depends on several variables, including part size, material type, surface complexity, and order quantity. Typically, the cost correlates with the part’s dimensions and quantity, with larger or more intricate parts requiring more processing time and resources. Below is an pricing example for your reference.
Part | Automotive Hose | Eyewear Frames | Rigid Orthotic Insole |
---|---|---|---|
Model Dimensions (mm) | 180 x 25 x 70 | 144 x 36 x 47 | 157 x 23 x 80 |
Material | TPU 92A Powder | Nylon 12 Powder | Nylon 11 Powder |
Quantity | 40 | 80 | 50 |
Cost of Vapor Smoothing (per part) | $1.10 | $0.49 | $0.98 |
Cost of Sintered Powder (per part) | $4.50 | $0.62 | $3.98 |
Total Cost Per Part | $5.60 | $1.11 | $4.96 |
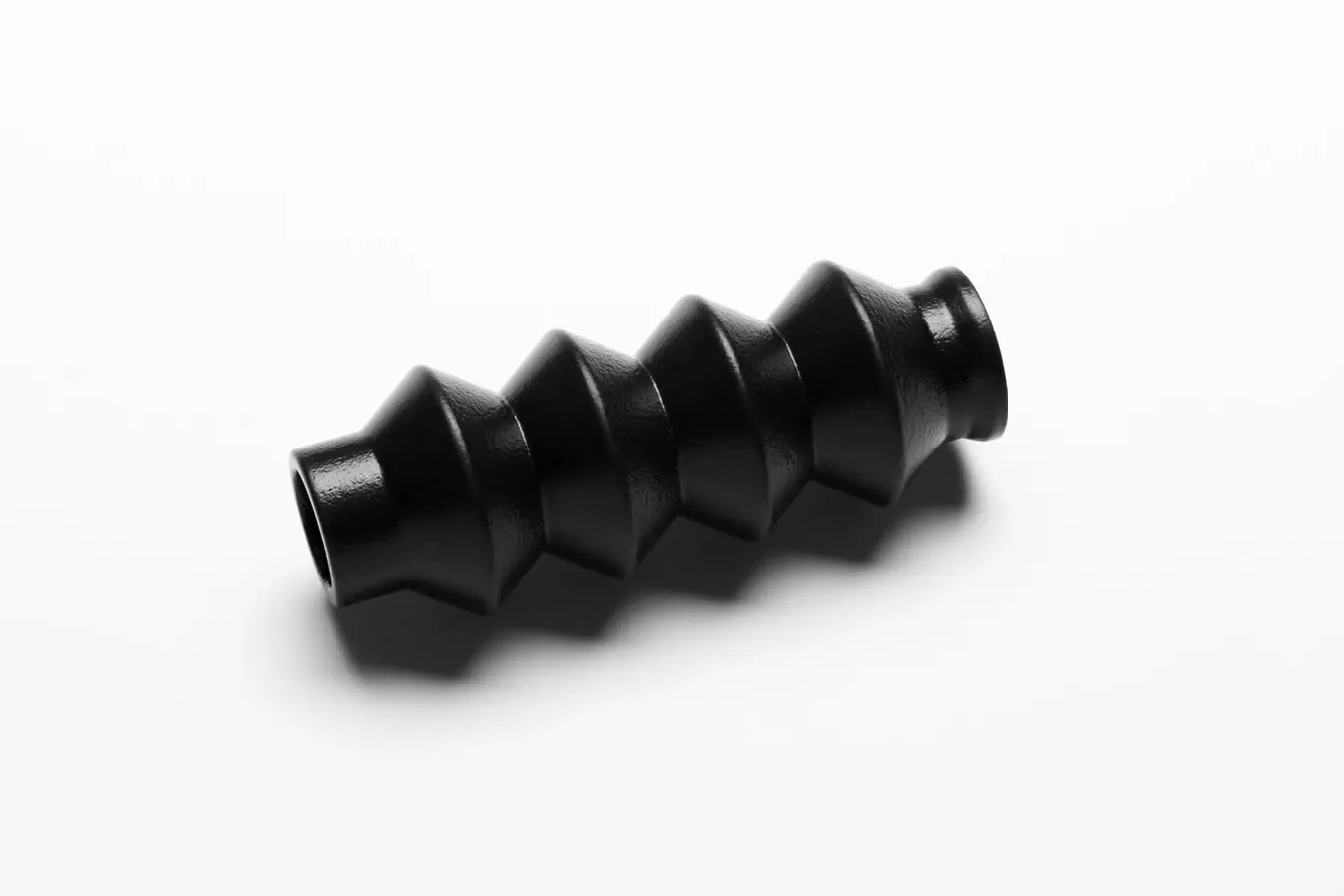

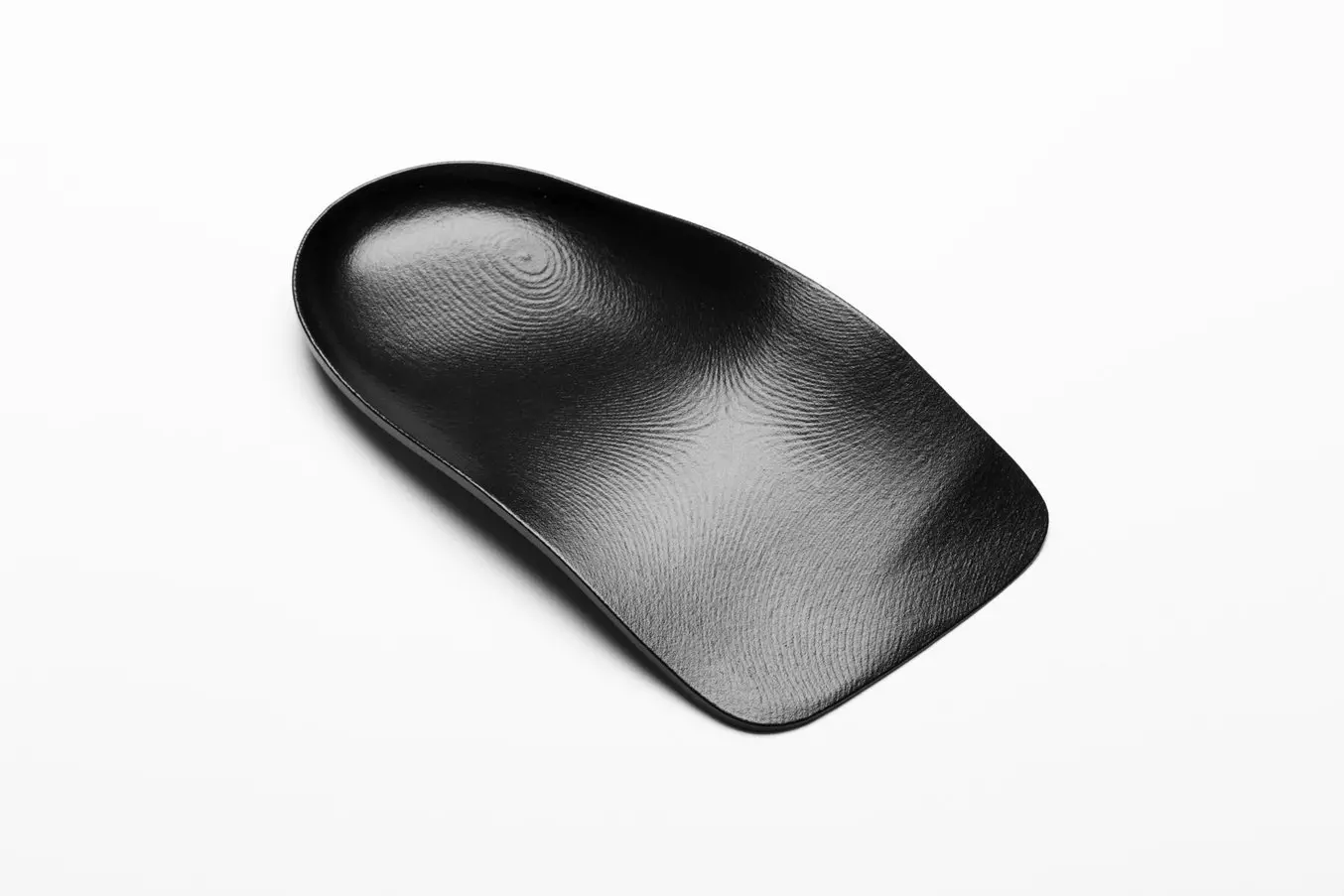
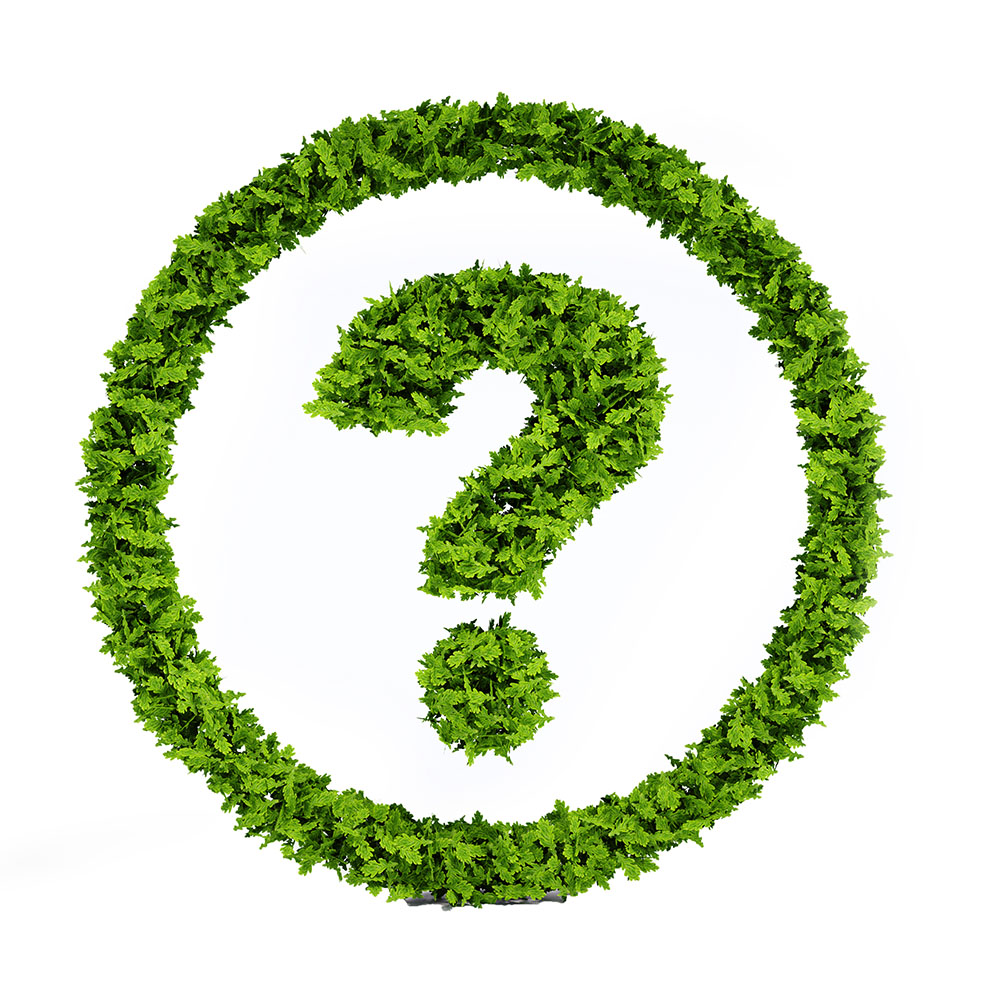
Vapor smoothing works well with materials like nylon, TPU, and other thermoplastic powders commonly used in SLS 3D printing.
Yes, KingStar Mold provides vapor smoothing services to enhance the surface quality of 3D printed parts, offering a smooth, consistent finish without compromising part integrity.
Vapor smoothing has minimal impact on the mechanical properties of most parts, preserving their strength while improving aesthetics and surface finish.
Vapor smoothing is a process that improves the surface finish of 3D printed parts by exposing them to a vaporized solvent, which smooths out the roughness, enhancing both appearance and performance.
KingStar Mold offers professional vapor smoothing services with the expertise to deliver consistent, high-quality results, making it an ideal choice for companies looking to enhance the appearance and performance of their 3D printed components.
The time required for vapor smoothing depends on the size and complexity of the part, but typically it takes a few hours per part, with additional time for post-processing steps.
While vapor smoothing is effective for many parts, its success depends on part geometry, size, and material type. Parts with complex internal features or small dimensions may require special consideration.
Vapor smoothing provides a more uniform finish across the entire part, including difficult-to-reach areas, unlike other techniques like bead blasting or sanding, which may leave inconsistencies.