In today’s competitive manufacturing landscape, producing high-quality products isn’t just a goal—it’s a measurable discipline. At the heart of this discipline lies CTQ, or Critical to Quality, a framework that translates customer expectations into specific, actionable, and measurable product or process characteristics. In the field of injection molding, where precision, consistency, and repeatability are vital, CTQ reporting is not merely beneficial—it’s essential.
CTQs help bridge the gap between what a customer wants and how a product is made. For manufacturers like KingStar Mold, where we produce custom injection molds and molded plastic parts for automotive, household, and industrial applications, CTQ reporting ensures that quality isn’t left to interpretation. Instead, it is quantified, monitored, and continuously improved throughout every stage—from mold design and tooling to production and final inspection.
At KingStar Mold, our commitment to measurable quality control is reflected in how we approach every project. We use CTQ principles to guide decisions, validate processes, and demonstrate accountability to our clients. By clearly defining and tracking critical parameters such as dimensional accuracy, surface finish, material performance, and process stability, we guarantee not just compliance with specifications but consistency across production runs.
This article explores how CTQ reporting works in practice, how it integrates with KingStar Mold’s operations, and why it plays a pivotal role in driving reliable outcomes for our global customers.
- 1. What Is CTQ Reporting in Manufacturing?
- 2. Why CTQ Matters at KingStar Mold
- 3. Voice of the Customer (VOC): The Starting Point
- 4. Creating a CTQ Tree for Mold Manufacturing
- 5. Key CTQ Elements in Injection Molding
- 6. CTQ in the Tooling Process
- 7. Monitoring and Reporting CTQs in Production
- 8. Using CTQ Data to Drive Continuous Improvement
- 9. When VOC Becomes a CTQ: Practical Scenarios
- 10. Challenges and Best Practices in CTQ Implementation
- Conclusion
1. What Is CTQ Reporting in Manufacturing?
CTQ reporting, short for Critical to Quality reporting, is a quality management tool used to define and monitor the key attributes that directly impact a product’s performance and customer satisfaction. It focuses on identifying the specific, measurable characteristics that must be met to ensure that the end product aligns with customer requirements.
1.1 Definition and Core Purpose of CTQ Reporting
CTQ reporting establishes a set of quantifiable standards that reflect the essential quality attributes a product or process must achieve. These are not general indicators—they are tightly linked to what the customer values most. In manufacturing, CTQs are embedded into quality plans, inspection protocols, and process controls, forming the backbone of a proactive quality assurance strategy.
1.2 Role in Translating Customer Expectations into Measurable Parameters
Customer expectations often begin as broad goals—strength, durability, appearance, or precision. CTQ reporting converts these abstract requirements into clear, trackable metrics such as ±0.02 mm dimensional tolerance, specific surface roughness levels, or minimum tensile strength thresholds. This conversion ensures that both engineering and production teams understand and consistently meet the customer’s true priorities.
1.3 Examples of CTQs in Mold Manufacturing
At KingStar Mold, we apply CTQ reporting to define and control critical variables throughout the tooling and molding lifecycle. Some common examples of CTQs in our processes include:
- Dimensional Tolerance: Precise measurements within a tight tolerance range (e.g., ±0.01 mm) to ensure proper part fit and function.
- Surface Finish: Specific Ra values for cosmetic or functional surfaces, depending on the application (e.g., automotive interior vs. technical parts).
- Material Strength: Verification of material performance metrics such as impact resistance, tensile strength, or thermal stability, especially important for end-use components in demanding environments.
By defining these parameters early and monitoring them throughout production, CTQ reporting helps us eliminate variability, reduce defects, and maintain high levels of customer satisfaction.
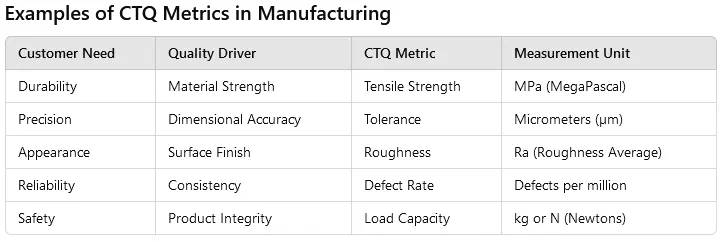
2. Why CTQ Matters at KingStar Mold
At KingStar Mold, delivering high-quality injection molds and plastic parts is not just about meeting expectations; it’s about exceeding them. CTQ (Critical to Quality) reporting plays a crucial role in this process by ensuring that customer requirements are not only understood but also precisely translated into measurable standards.
2.1 Customer-Driven Requirements
In the world of mold manufacturing, the customer’s needs and expectations drive every decision. Each project begins with a detailed analysis of these requirements, focusing on key factors such as part functionality, durability, and aesthetic qualities. For KingStar Mold, this means that CTQs are tailored specifically to meet customer demands. Whether it’s a tight dimensional tolerance or a specific surface finish requirement, our team ensures that these critical attributes are identified from the very start, so they can be consistently met throughout the production process.
2.2 A Foundation for Process Standardization
CTQ reporting is not just about fulfilling immediate customer requirements; it’s also about creating a foundation for process standardization and repeatability. By defining clear CTQs early in the project, KingStar Mold can standardize production processes across various molds and plastic parts. This minimizes variation and ensures that each mold meets the same high-quality standards, regardless of the scale of production. With the ability to track and measure CTQs, we can continuously refine our processes, eliminating inefficiencies and ensuring that every part produced is identical in quality.
2.3 Aligning with Quality Assurance Goals
At KingStar Mold, our commitment to excellence is reflected in our rigorous quality assurance (QA) protocols. CTQ reporting aligns seamlessly with these goals by providing a structured, data-driven approach to quality management. Each critical factor—whether it’s dimensional accuracy, material strength, or surface finish—is tracked and reported to ensure that we meet the highest standards of quality. This approach not only guarantees that our products meet customer specifications but also provides the transparency and traceability necessary for continuous improvement.
By prioritizing CTQs in every stage of production, KingStar Mold upholds its reputation for delivering precision-engineered molds and plastic parts that meet or exceed industry standards.
3. Voice of the Customer (VOC): The Starting Point
At KingStar Mold, the journey to delivering high-quality molds and plastic parts begins with a deep understanding of the Voice of the Customer (VOC). Gathering customer requirements is a critical first step in ensuring that the final product aligns perfectly with their needs and expectations. CTQ reporting hinges on this foundational step, turning customer insights into actionable, measurable standards.
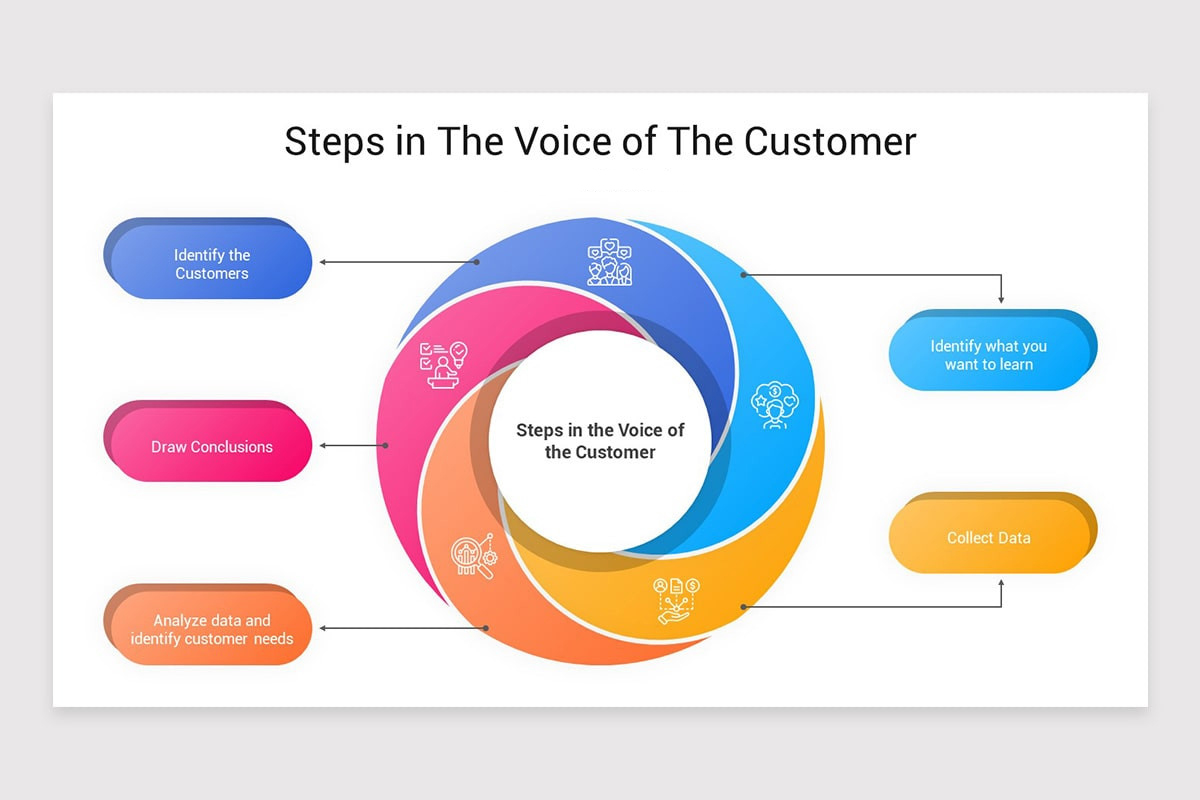
3.1 Gathering Customer Requirements
The process starts with the collection of customer inputs, typically through Request for Quotations (RFQs), design specifications, and direct consultations. These documents serve as the initial touchpoint, providing valuable details about the customer’s vision for the product. At KingStar Mold, we place a strong emphasis on open communication with our clients. Whether it’s understanding the specific requirements for a mold or gaining insights into the intended use of the plastic part, we ensure that every expectation is clearly captured.
3.2 Turning Vague Expectations into Actionable CTQs
Often, the customer’s initial requirements may be vague or broad—terms like “strong,” “durable,” or “precise” can be subjective and open to interpretation. The key to effective CTQ reporting is the ability to turn these general expectations into actionable, measurable parameters. This is where our expertise comes into play.
We work closely with our clients to break down these general expectations into specific, quantifiable CTQs such as dimensional tolerances, material specifications, and surface finishes. For instance, a “strong” part might be translated into a specific tensile strength value, and “precise” might correspond to a particular range of allowable deviations in part dimensions. By refining these expectations, we create a clear roadmap for production.
3.3 Real-World Example: VOC for an Automotive Interior Component
Let’s consider a real-world example where VOC played a pivotal role in the development of an automotive interior component. A client requested an injection-molded part for a car’s dashboard, specifying the need for high-quality aesthetics and durability under extreme temperature conditions. Initially, these requirements were broad, but by collaborating with the client and conducting in-depth consultations, we distilled these needs into clear CTQs:
- Dimensional Tolerances: Tight tolerances for fitting the part into other dashboard components.
- Surface Finish: A smooth, glossy surface finish to meet aesthetic standards.
- Material Strength: The part needed to withstand high temperatures without warping or degrading, so specific material strength and thermal resistance properties were specified.
- Impact Resistance: Ensuring that the part could survive minor impacts without cracking or losing integrity.
This process of translating the VOC into measurable CTQs ensured that our team had a clear direction and could maintain the high standards of quality required for the automotive industry.
By starting with a deep understanding of the VOC, KingStar Mold is able to set the stage for precise, quality-driven manufacturing processes. This helps us to ensure that we meet—and often exceed—our clients’ expectations, delivering products that truly reflect their needs.
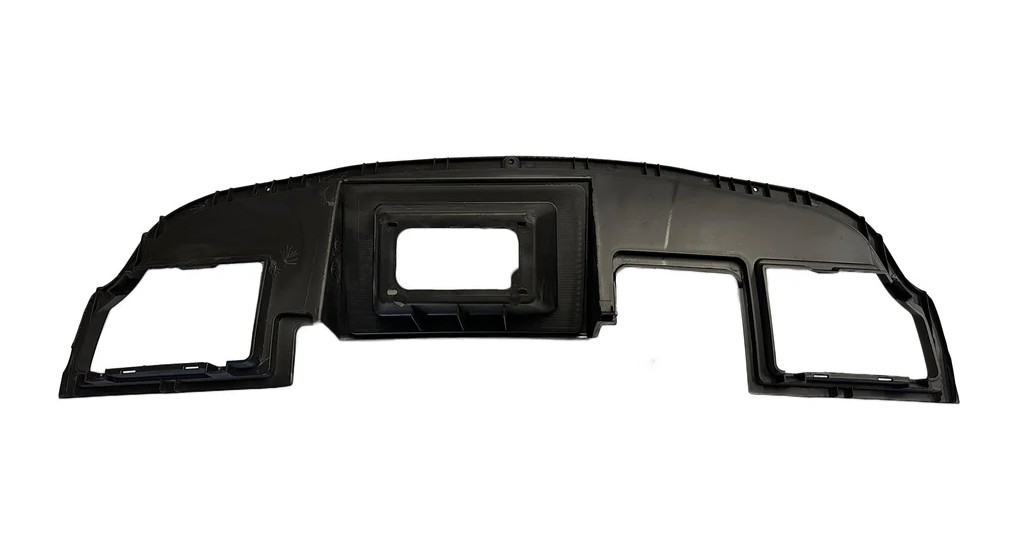
4. Creating a CTQ Tree for Mold Manufacturing
Creating a CTQ tree is an essential part of translating customer requirements into measurable standards in mold manufacturing. At KingStar Mold, we use the CTQ tree to ensure that we are precisely aligned with customer expectations while maintaining the highest quality standards. This structured approach breaks down complex customer needs into clear, actionable, and measurable parameters.
4.1 Overview of the CTQ Tree Structure
The CTQ tree is essentially a hierarchical diagram that visually represents how customer requirements translate into specific, measurable attributes that are critical to the quality of the final product. It starts with broad customer needs and gradually breaks them down into more detailed, technical requirements. Each branch of the tree represents a different aspect of the product or process, such as material properties, dimensional tolerances, or process capabilities. By the time you reach the leaf nodes of the tree, you have specific, quantifiable CTQs that guide manufacturing efforts.
The structure of the CTQ tree typically involves several levels:
- Customer Requirements (Top Level): The general needs and expectations as expressed by the customer.
- Critical Categories (Second Level): These are the key quality attributes that are essential to meet customer expectations (e.g., dimensional accuracy, surface finish, material strength).
- Measurable Technical Requirements (Third Level): The precise, quantifiable specifications for each critical category (e.g., ±0.05 mm tolerance, surface roughness of 1.6 µm, tensile strength of 200 MPa).
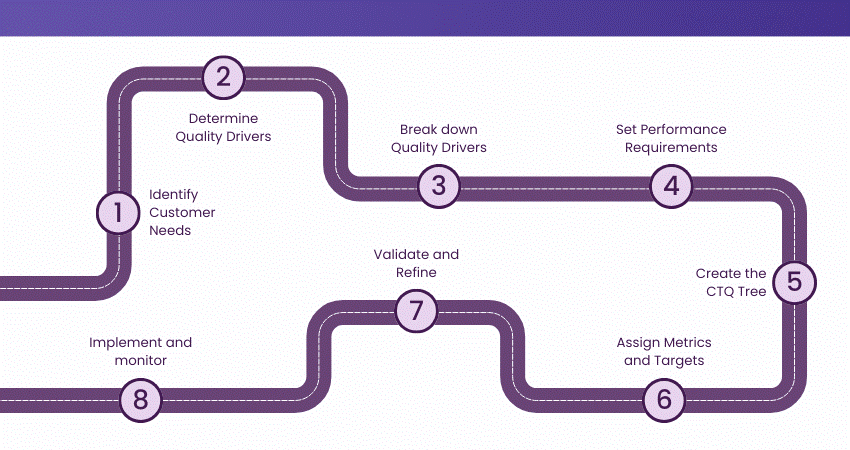
4.2 Steps to Break Down Customer Needs into Measurable Technical Requirements
- Identify Customer Requirements: Begin by gathering customer inputs through RFQs, design specifications, or direct consultations. These will provide you with broad, high-level requirements.
- Translate Broad Requirements into Critical Categories: Identify the key attributes that affect the product’s performance. For example, if a customer requires a part with high precision, dimensional accuracy becomes a critical category.
- Decompose into Measurable Technical Requirements: For each critical category, break it down into specific, quantifiable CTQs. This step might involve working with engineers, designers, and material specialists to ensure that the criteria can be measured accurately.
- Validate with the Customer: Once the CTQ tree has been built, it’s important to review it with the customer to ensure that their needs have been accurately captured and translated into measurable standards.
4.3 Sample CTQ Tree for a Two-Shot Mold
Let’s walk through an example of a CTQ tree for a two-shot injection molding project. A two-shot mold is designed to create two different materials in a single, complex part, often used for components that require different colors or material properties in one piece.
1. Customer Requirement: The customer needs a two-shot molded part that meets specific color, durability, and functionality standards.

2. Critical Categories:
-
- Dimensional Accuracy: The part must fit into the larger assembly with precise tolerances.
- Surface Finish: The surface must be smooth and free of defects.
- Material Performance: The materials used must meet specific thermal, tensile, and impact resistance requirements.
3. Measurable Technical Requirements:
-
- Dimensional Accuracy: Tolerance of ±0.1 mm on critical dimensions.
- Surface Finish: A smooth surface with a roughness of Ra ≤ 1.6 µm.
- Material Performance:
- Tensile Strength: Minimum of 150 MPa for the primary material.
- Impact Resistance: Minimum of 5 J for the secondary material at -20°C.
- Thermal Stability: Must withstand temperatures of up to 150°C without degradation.
In this example, each category and requirement in the CTQ tree directly correlates with the customer’s needs, ensuring that every aspect of the mold manufacturing process is optimized for quality.
By using a CTQ tree in mold manufacturing, KingStar Mold ensures that all customer expectations are met precisely and consistently. This method not only improves product quality but also enhances communication and transparency between the customer and the production team, resulting in a more efficient and reliable manufacturing process.
5. Key CTQ Elements in Injection Molding
In the field of injection molding, CTQ (Critical to Quality) elements refer to the characteristics that have the most direct impact on the function, performance, and appearance of the molded parts. At KingStar Mold, we believe in tailoring our quality standards to suit the specific needs of the project. While some elements are rigidly controlled due to their direct impact on customer satisfaction or functionality, others are more flexible. Let’s explore the key CTQ factors in our process:
5.1 Dimensional Accuracy: Precision Where It Counts
For KingStar Mold, dimensional accuracy is the cornerstone of many high-quality projects, especially those where parts need to fit together perfectly in an assembly or endure mechanical stress. When precision is a critical requirement, such as with parts used in automotive applications, we achieve tight tolerances of ±0.05 mm to ensure that every component is exact.
- Why it matters: Ensuring perfect dimensional accuracy prevents issues like misalignment, which can lead to performance failure or assembly challenges.
- Relaxed tolerances for non-critical areas: For non-critical components, such as internal features that do not directly impact the part’s function or assembly, we allow slightly wider tolerance ranges to optimize production efficiency and cost.
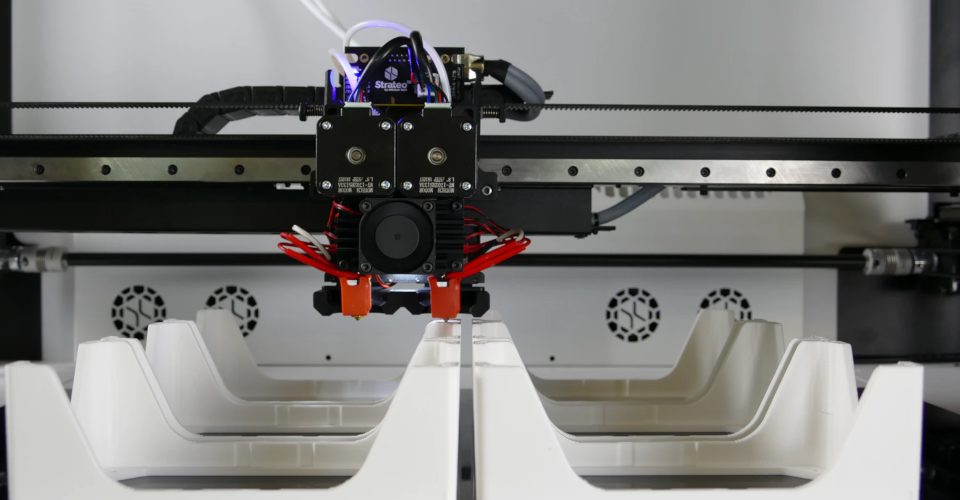
5.2 Surface Finish: The Balance Between Function and Aesthetics
The quality of a part’s surface finish plays a significant role in both its aesthetic appeal and durability. For products with visible surfaces, such as consumer electronics enclosures or automotive interior components, a smooth, flawless finish is non-negotiable. For these parts, we meet high SPI (Society of Plastics Industry) finish standards, often going as high as SPI A or SPI B. A smooth surface improves part durability and visual appeal, crucial for end-user satisfaction.
For internal components: Parts that are not exposed to the end user, such as those used in industrial machinery, can have a lower SPI rating, reducing production time and costs without sacrificing functionality.
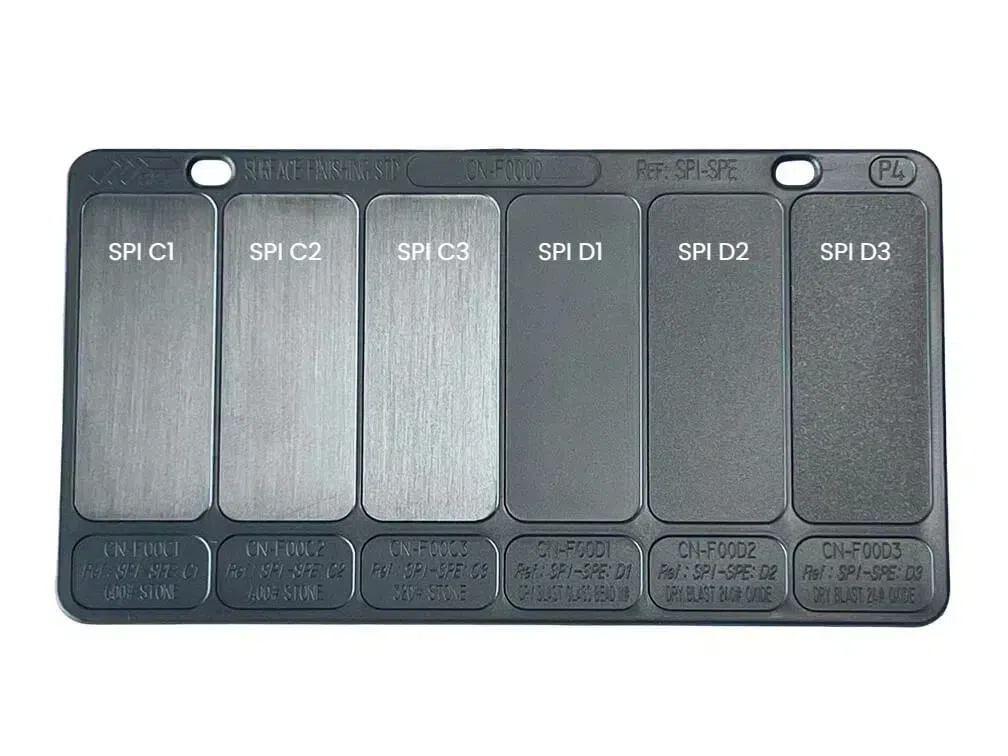
5.3 Material Flow: Ensuring Uniformity
In injection molding, consistent material flow is essential to producing parts that meet the strength and consistency standards. Flow consistency ensures that the plastic fills the mold evenly, which is crucial for parts that require a high level of strength and durability. At KingStar Mold, we use advanced simulation software to optimize the flow in critical areas.
Variations in material flow can lead to defects like short shots or incomplete filling, affecting both the appearance and strength of parts, but for non-critical parts, where material flow does not impact structural integrity, we allow for flexible flow control such as slight variations, saving time and resources.
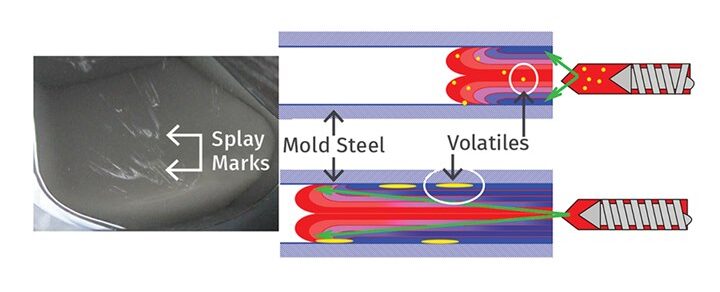
5.4 Parting Line Precision: Aesthetic and Functional Harmony
Parting lines, the line where two halves of the mold meet, are another critical element for parts requiring high precision. When manufacturing consumer products such as appliances or automotive components, parting line precision directly influences the overall appearance of the product. However, for non-visible parts, such as machine components, we allow parting lines to be less precise without compromising the part’s function.
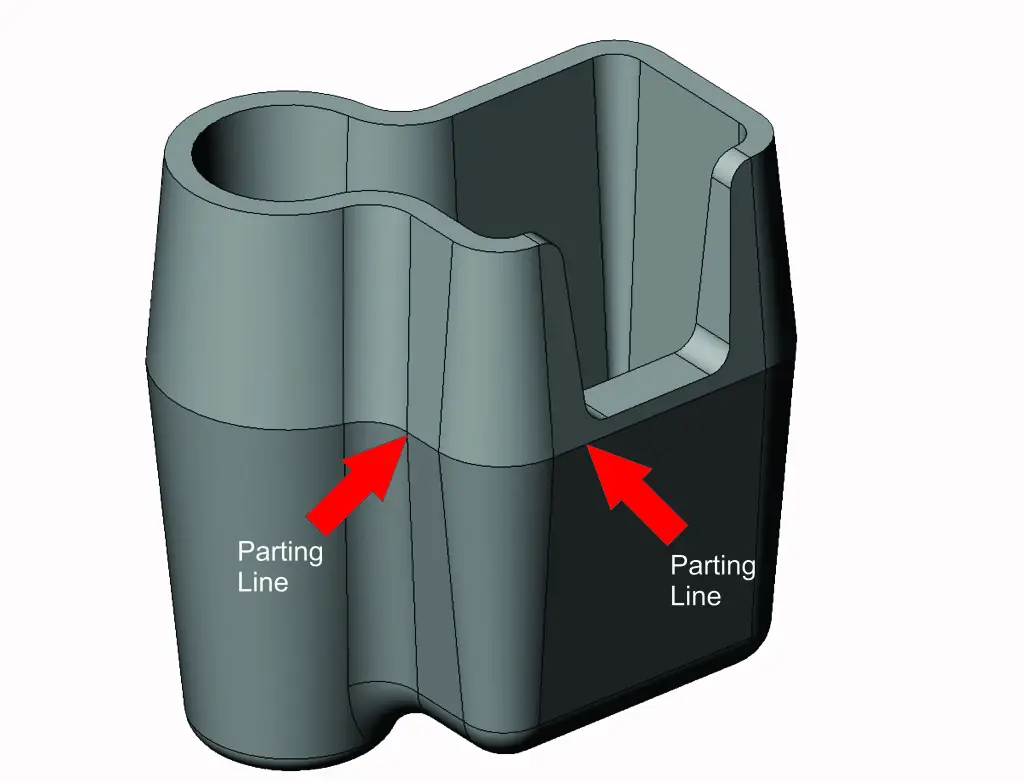
5.5 Cycle Time: Maximizing Efficiency
Cycle time is a critical consideration in optimizing production rates while maintaining high-quality standards. At KingStar Mold, we maintain a balance between production speed and quality. For critical components that require detailed attention to dimensions, filling, or surface finish, we optimize the cycle time to ensure no compromise on quality. However, for parts with fewer performance requirements, we aim to reduce cycle time without affecting their functional attributes. Faster cycle times improve throughput, making the process more cost-effective while meeting demand.
- Adjusting cycle time for non-critical parts: Parts that are functionally less demanding can have a shortened cycle time, allowing us to maintain a high production rate without affecting the overall performance of the part.
At KingStar Mold, we understand that not all parts are created equal. While we ensure that CTQ elements like dimensional accuracy, surface finish, and material flow are strictly controlled for mission-critical components, we also recognize when it is appropriate to relax certain standards in less critical areas. This flexibility allows us to optimize production costs and lead times, ensuring that every project meets customer expectations without compromising on the core elements that matter most.
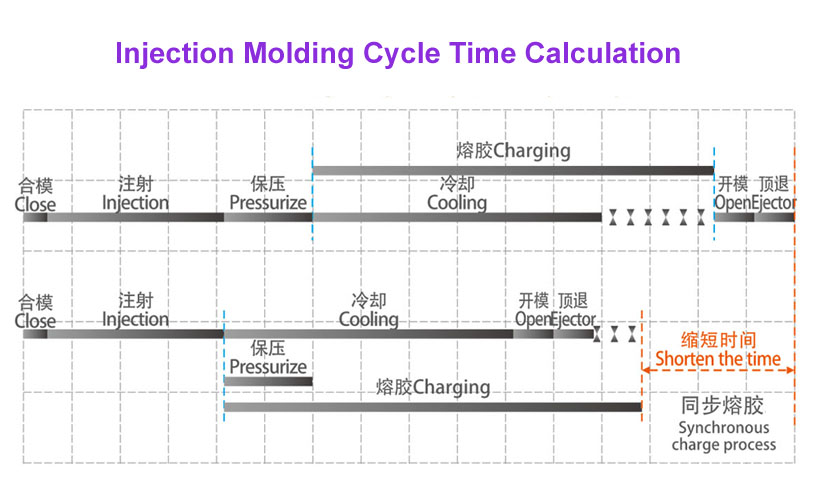
6. CTQ in the Tooling Process
The tooling process plays a fundamental role in the production of high-quality injection molds. At KingStar Mold, Critical to Quality (CTQ) elements in the tooling process are closely monitored to ensure that molds are both durable and efficient in producing parts that meet stringent customer requirements. These CTQs focus on the integrity of the mold itself, which impacts part quality, production efficiency, and tooling longevity.
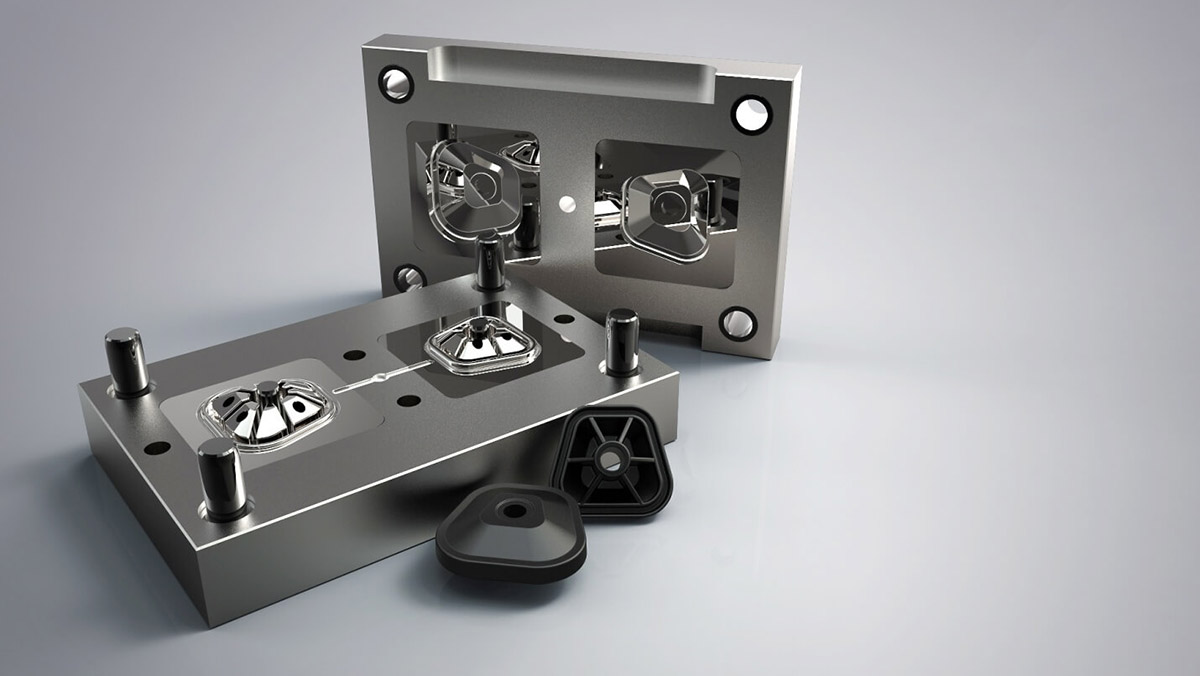
6.1 Mold Base Hardness: The Foundation of Tool Durability
One of the CTQ factors that directly influences the lifespan of a mold is the hardness of the mold base material. Hardness ensures that the mold can withstand repeated cycles of injection molding without suffering wear and tear that could impact part quality.
Since a high-quality, durable mold base prevents deformation, misalignment, or surface damage, which could affect the dimensional accuracy of the molded parts, we use high-hardness tool steels and perform hardness testing to ensure that each mold base can withstand extensive use without losing structural integrity.
6.2 Cooling Efficiency: Managing Temperature Variations
Efficient cooling is another CTQ factor in the tooling process that directly affects cycle times and the quality of molded parts. Poor cooling efficiency can lead to inconsistent material cooling, resulting in warping or dimensional inaccuracies in parts.
- Why it matters: Adequate cooling ensures uniform part quality by minimizing material shrinkage and maintaining precise dimensions.
- KingStar Mold’s approach: We use advanced cooling channel designs and thermal analysis software to optimize mold cooling, reducing cycle times while maintaining the necessary quality.
6.3 Ejection Reliability: Ensuring Smooth Part Release
The ejection process is vital to the smooth functioning of injection molds, ensuring that parts are removed without defects such as scratches or distortion. Ejection reliability is critical, especially for delicate or complex parts.
- Why it matters: Reliable ejection minimizes the risk of damaging the part during removal and prevents issues like stuck parts or excessive wear on the mold.
- KingStar Mold’s ejection systems: We implement advanced ejection systems, such as automated ejector pins and air-assisted ejection mechanisms, to ensure that every part is removed cleanly and efficiently.
6.4 Inspection Methods: Ensuring Accuracy at Every Stage
To ensure that tooling meets the required CTQ parameters, KingStar Mold employs a variety of inspection methods throughout the tooling process. These methods are essential to identify any issues early on, minimizing costly repairs and ensuring that the tooling meets the necessary specifications.
- Coordinate Measuring Machine (CMM): The CMM is used to precisely measure the dimensions of mold components, checking for any deviations from the required specifications.
- Optical Measuring: For detailed features, we use optical measurement systems to assess fine tolerances and surface finishes that may not be easily measurable with traditional tools.
- Pressure Monitoring: Throughout the molding process, we monitor injection pressure to ensure that the material is flowing into the mold as designed, detecting any potential blockages or variations that could impact part quality.
6.5 KPIs Tied to Tooling CTQs
Key Performance Indicators (KPIs) are used to evaluate the effectiveness of the tooling process. These KPIs are tied to specific CTQs and offer measurable ways to track performance.
- Tool Wear Rate: This measures the rate at which the mold base experiences wear, ensuring that molds maintain their integrity over time.
- Cycle Time Reduction: By measuring cycle time improvements, we can assess the efficiency of cooling and ejection systems, directly linking this KPI to our tooling CTQs.
- Ejection Success Rate: This tracks the number of parts successfully ejected without issues, such as defects or part sticking. A high ejection success rate directly correlates to mold reliability and ejection system effectiveness.
At KingStar Mold, we understand that the quality of our tooling process directly impacts the overall success of our injection molding operations. Through rigorous monitoring and precision control of CTQ elements like mold base hardness, cooling efficiency, and ejection reliability, we ensure that each mold is optimized for performance and longevity. Using advanced inspection methods and focusing on KPIs tied to tooling CTQs, we consistently meet customer expectations while driving continuous improvement in our processes.
7. Monitoring and Reporting CTQs in Production
Effective monitoring and reporting of Critical to Quality (CTQ) parameters during production is essential for maintaining consistent part quality and meeting customer expectations.
At KingStar Mold, we employ advanced quality control techniques throughout the manufacturing process to ensure that every part adheres to the required specifications. Real-time tracking, quality checks, and data documentation play a critical role in ensuring that our injection molding operations are both efficient and reliable.
7.1 In-Line and Post-Process Quality Checks
Continuous quality checks, both in-line during production and post-process, are vital to ensuring that any potential issues are identified and addressed quickly.
- In-line checks: These are performed during the production process to assess parts as they are being molded. For example, dimensional measurements are taken as parts exit the mold, and checks are performed to ensure that the parts meet CTQ specifications, such as wall thickness, parting line precision, and surface finish.
- Post-process checks: After molding, parts undergo a second round of quality inspections. These may include visual inspections, CMM (Coordinate Measuring Machine) testing, and tensile strength evaluations to ensure that the final product meets customer requirements and adheres to established CTQs.
At KingStar Mold, our commitment to quality ensures that any deviations from the CTQ parameters are immediately addressed, minimizing the risk of defective parts reaching our customers.
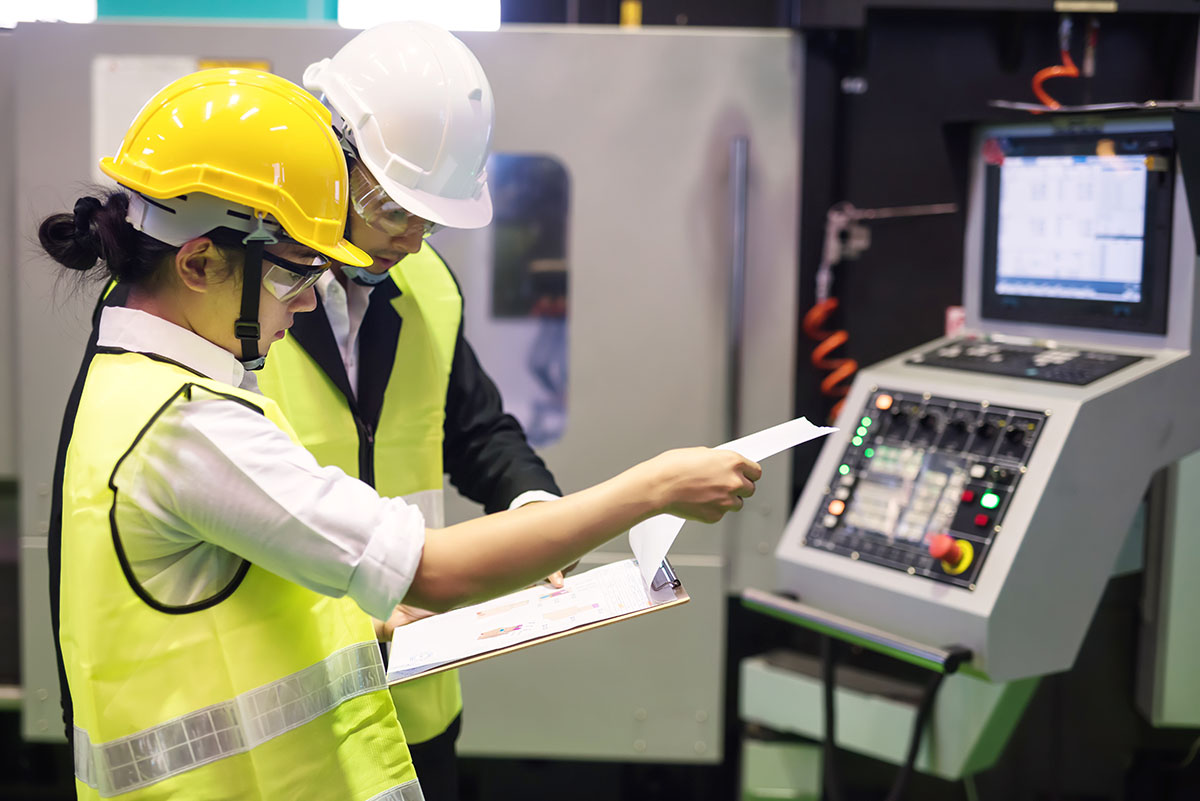
7.2 Real-Time Tracking Tools and SPC (Statistical Process Control)
To stay ahead of any potential issues, we use real-time tracking tools that allow us to continuously monitor key variables and adjust production parameters on-the-fly. These tools provide immediate feedback, enabling us to maintain consistent part quality throughout production.
- Real-time tracking tools: We use specialized software to track parameters such as temperature, pressure, and cycle time during the molding process. This data is continuously monitored to detect variations that could indicate a potential quality issue.
- Statistical Process Control (SPC): SPC is used to analyze production data and ensure that the process remains stable and within acceptable limits. By applying statistical methods to process data, we can identify trends and take corrective action before a deviation becomes a defect. This proactive approach ensures that CTQs are consistently met across all production runs.
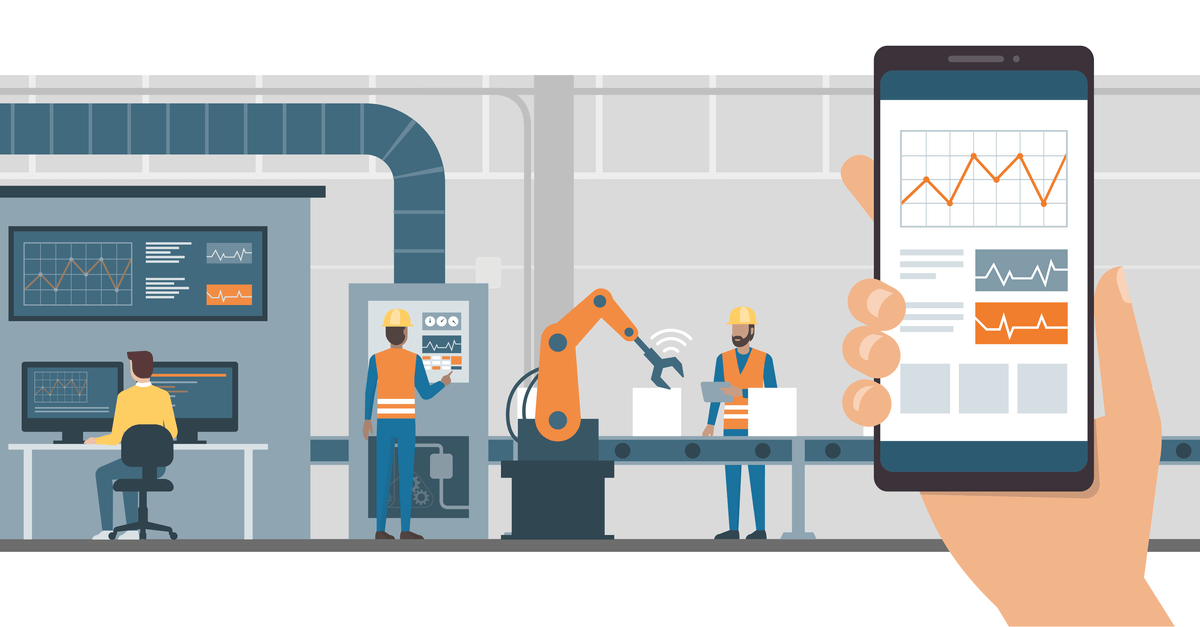
7.3 How KingStar Mold Documents and Reports CTQ Data to Clients
KingStar Mold places a high priority on transparency and communication with our clients. To keep customers informed of the CTQ performance and quality metrics, we provide detailed reports that document every stage of the manufacturing process.
- CTQ Data Documentation: We maintain detailed records of all CTQ data, including inspection results, SPC charts, and real-time tracking metrics. These records are systematically organized and can be reviewed at any time, ensuring that clients have full access to quality data.
- Client Reports: Upon request, we provide CTQ reports to clients, detailing the quality checks performed during the production process, the results of those checks, and any corrective actions taken. These reports not only confirm the adherence to agreed-upon quality standards but also serve as a valuable tool for continuous improvement and collaboration between KingStar Mold and our clients.
At KingStar Mold, we understand the importance of clear communication when it comes to quality assurance. Our real-time tracking tools, SPC methods, and thorough documentation ensure that our clients are always informed and confident that their molds are produced to the highest standards of quality.
By focusing on in-line and post-process checks, leveraging real-time tracking and SPC tools, and maintaining clear and comprehensive CTQ data documentation, KingStar Mold ensures that quality control remains at the core of our operations. Our commitment to accurate reporting and transparency with clients reinforces our dedication to producing high-quality molds that meet the most stringent requirements.
8. Using CTQ Data to Drive Continuous Improvement
At KingStar Mold, Critical to Quality (CTQ) data is not only a tool for ensuring current production standards but also a driving force behind continuous improvement. By analyzing CTQ deviations and implementing effective feedback loops, we can make informed adjustments to our processes, improving overall efficiency, reducing defects, and ensuring that our molds meet or exceed customer expectations consistently.
8.1 Identifying Trends and Root Causes Through CTQ Deviations
A crucial part of the continuous improvement process is identifying trends and root causes when CTQ parameters deviate from the target.
- CTQ Deviations: When a deviation occurs in one or more CTQs (such as dimensional accuracy, parting line precision, or material flow), it’s an early warning sign that something in the process needs attention. Monitoring and analyzing CTQ data allows our team to spot these deviations quickly.
- Trend Analysis: By reviewing historical CTQ data, we can identify patterns and recurring issues that may indicate systemic problems. For instance, if a dimensional tolerance is consistently off on certain parts or molds, we can determine whether the issue lies in the mold design, tooling, or machine calibration.
- Root Cause Analysis: Once a trend is identified, a detailed root cause analysis is conducted. This might involve investigating tooling wear, material inconsistencies, or machine calibration issues that could be causing the CTQ deviations. Addressing these root causes enables us to fix the underlying problems rather than just the symptoms, resulting in long-term improvements in product quality.
8.2 Feedback Loops to Design, Tooling, and Production Teams
At KingStar Mold, we use the insights gained from CTQ data analysis to create feedback loops that involve cross-functional teams from design, tooling, and production.
- Design Feedback: If CTQ data shows that certain features or tolerances are difficult to achieve, the design team can adjust the part design to make it more manufacturable. For example, if undercuts or excessive wall thicknesses are leading to frequent defects, the design team can modify the part to improve its moldability without compromising the product’s functionality.
- Tooling Feedback: Tooling issues are a common source of CTQ deviations, so feedback from CTQ analysis is critical for the tooling team. If deviations are linked to cooling efficiency, ejection reliability, or mold wear, the tooling team can refine mold design or repair worn-out tooling to maintain tight tolerances.
- Production Feedback: Real-time CTQ tracking helps production teams identify issues as they occur, allowing them to make immediate adjustments. For example, if temperature control or pressure settings are affecting material flow, operators can tweak parameters in real time to bring production back within CTQ limits.
By continuously cycling this feedback between teams, KingStar Mold fosters a collaborative environment where all teams are aligned in the pursuit of high-quality, defect-free production.
8.3 Case Study: Solving a Short Shot Issue by Analyzing CTQ Data
One real-world example of how CTQ data drives continuous improvement at KingStar Mold involved solving a recurring short shot issue in a customer’s automotive component.
- The Problem: A short shot occurs when the mold cavity is not completely filled with material, leading to incomplete parts. For a specific automotive component, we noticed that some parts were frequently showing signs of short shots, leading to delays and customer complaints.
- CTQ Data Analysis: Upon reviewing the CTQ data, we noticed that the material flow and filling consistency were often out of specification, especially during specific times in the molding cycle. This pointed to an issue with the injection pressure and mold temperature.
- Root Cause: By working closely with the tooling and production teams, we determined that the mold cooling system was uneven, leading to inconsistent material flow during the injection process. Additionally, the injection pressure was insufficient for filling the mold entirely.
- Solution: The tooling team made adjustments to the cooling system to ensure more even temperature distribution across the mold, and the production team recalibrated the injection pressure settings. We also fine-tuned the material flow rate to ensure a smooth and consistent filling of the mold cavity.
- Results: After implementing these changes, the number of short shots decreased dramatically, and the production line ran smoothly. Continuous monitoring of the CTQ data confirmed that the issue had been resolved, and quality improved.
This case study illustrates the power of CTQ data analysis in identifying and addressing issues, driving improvements that enhance both part quality and operational efficiency.

9. When VOC Becomes a CTQ: Practical Scenarios
In mold manufacturing, the transition from Voice of the Customer (VOC) to Critical to Quality (CTQ) is a crucial step in ensuring that customer needs are translated into precise, measurable specifications. This process helps prioritize the most important elements of a product, ensuring both functionality and quality. Below, we explore two practical scenarios that showcase how VOC becomes CTQ at KingStar Mold.
9.1 Example 1: High-Gloss Surface Requirement in Consumer Products
One of the most common VOCs in consumer products is the high-gloss surface finish. Customers often request a mirror-like finish for their products, especially in items like cosmetic packaging, luxury appliances, and consumer electronics.
- VOC to CTQ: To meet this requirement, we translate the high-gloss finish into specific CTQs, such as achieving a SPI A1 surface finish (the highest quality standard for mold surfaces). This translates to very tight specifications regarding mold surface smoothness, material consistency, and injection speed.
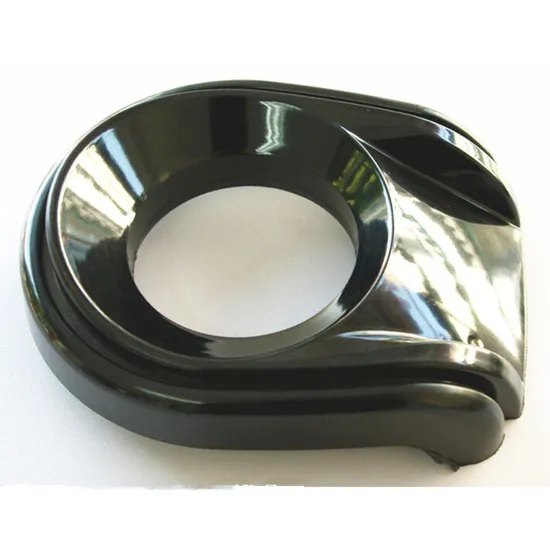
- Prioritizing Quality: The surface finish is prioritized as a high-priority CTQ because it directly impacts the product’s aesthetic appeal and marketability. Any deviation from this standard could result in a product that fails to meet consumer expectations, leading to dissatisfaction and potential loss of market share.
- Process Control: To achieve the desired high-gloss finish, the tooling process involves polishing mold surfaces to a mirror-like sheen, and we use high-precision injection molding techniques to control material flow and cooling rates. Continuous inspection and monitoring ensure that the CTQ for surface finish is consistently met throughout production.
9.2 Example 2: Pressure Resistance in Industrial Plastic Housings
For industrial applications, such as plastic housings for electrical components, the VOC often focuses on pressure resistance and structural integrity. In these scenarios, the customer needs the product to withstand high pressure without cracking or deforming.
- VOC to CTQ: The customer specifies a certain pressure resistance (e.g., a part must endure up to 500 psi without failure). This VOC is translated into a CTQ that outlines the necessary material strength, wall thickness, and design features (such as ribbed structures or reinforced sections) to achieve the required performance under pressure.
- Prioritizing Durability: The pressure resistance becomes a critical CTQ because failure in these parts could lead to device malfunctions or even safety hazards, especially in sectors like automotive or electronics. Ensuring the durability of these parts is therefore non-negotiable.
- Design and Testing: We utilize high-strength thermoplastic materials and perform extensive pressure testing during production. The mold design is specifically optimized to ensure the structural integrity of the part. Additionally, advanced techniques like finite element analysis (FEA) are used in the design phase to simulate pressure conditions and identify potential failure points before production begins.
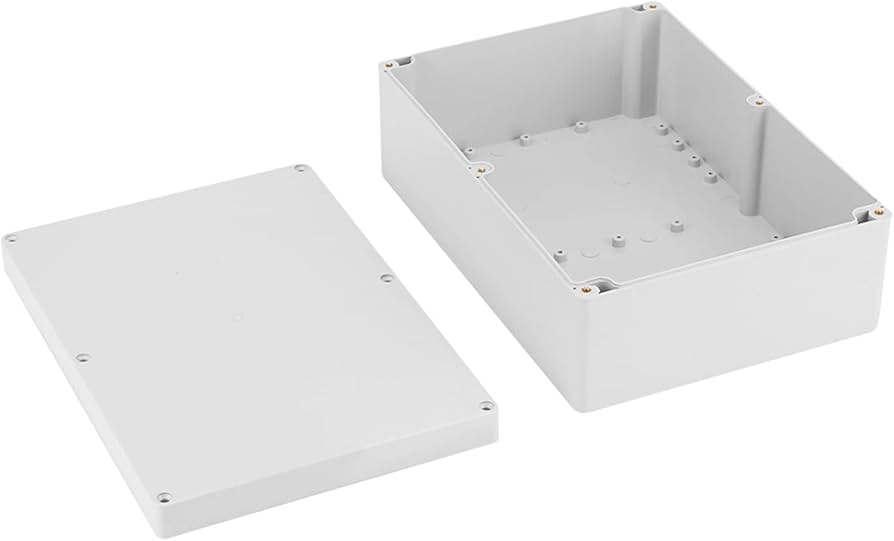
9.3 How CTQs Are Prioritized Based on Risk, Cost, and Customer Impact
At KingStar Mold, prioritizing CTQs is not a one-size-fits-all process. We take a strategic approach by considering the risk, cost, and customer impact of each CTQ. Here’s how we decide which CTQs take precedence:
- Risk Assessment: Critical CTQs that could lead to safety issues, product failure, or regulatory non-compliance are given top priority. For example, in automotive or medical applications, dimensional accuracy and material strength might be prioritized over aesthetic factors like surface finish, due to the direct impact on product functionality and safety.
- Cost Considerations: While customer needs must always be met, cost optimization is also important. Some CTQs, like surface finish or decorative coatings, may require additional resources (e.g., polishing or painting). These are balanced against the production cost to ensure that meeting customer requirements doesn’t become prohibitively expensive.
- Customer Impact: The importance of each CTQ is heavily influenced by how it affects the customer’s end product. For example, aesthetic factors such as surface finish or color might be crucial in consumer-facing products but less important in industrial applications where performance is the primary concern.
To ensure that we meet all customer expectations while balancing these factors, we conduct regular customer consultations and employ risk-based prioritization in our production planning. This ensures that high-priority CTQs are always given the focus they deserve, while lower-priority CTQs are handled efficiently without compromising the overall product quality.
10. Challenges and Best Practices in CTQ Implementation
Implementing Critical to Quality (CTQ) metrics in mold manufacturing is essential for ensuring that customer expectations are consistently met. However, this process is not without its challenges. From vague customer specifications to managing CTQ overload, manufacturing teams need to navigate these obstacles effectively. Below, we explore common challenges faced during CTQ implementation and share best practices for overcoming them.
10.1 Overcoming Vague Customer Specs
One of the most common challenges in CTQ implementation is dealing with vague or unclear customer specifications. Customers may provide general descriptions of their needs without detailing measurable requirements. For example, a customer may request a “smooth surface finish” without specifying an exact level of smoothness, or they may say a part “should be durable” without defining the specific material properties.
- Challenge: This lack of clarity can result in misaligned expectations between the customer and manufacturer, potentially leading to quality issues or rework.
- Best Practice: It’s essential to engage in thorough consultations with the customer to clarify their expectations. This can include asking for detailed design specifications, reviewing similar products in the market, and conducting engineering reviews. At KingStar Mold, we also provide design for manufacturability (DFM) guidance to ensure that customer needs are feasible within our production capabilities.
- Proactive Communication: At KingStar Mold, we strive to eliminate ambiguity early on in the project by having detailed conversations and following up with written specifications. By establishing clear expectations, we avoid later-stage corrections and ensure both the customer and our team are aligned on the CTQ requirements.
10.2 Avoiding CTQ Overload: Selecting the Right Metrics
Another challenge in CTQ implementation is CTQ overload, which occurs when too many metrics are chosen, overwhelming the manufacturing process and complicating decision-making. Customers may try to specify every minor detail, leading to a large number of CTQs that might not all be critical to the product’s overall success.
- Challenge: While every CTQ is important, having too many can dilute focus, increase the complexity of quality control processes, and inflate production costs unnecessarily.
- Best Practice: Prioritize CTQs based on customer impact, risk, and cost. Not every specification needs to be treated with equal importance. At KingStar Mold, we use risk-based assessments to determine which CTQs truly matter. For instance, dimensional accuracy and material strength are high-priority CTQs in industries like automotive, while surface finish might be a lower priority in less aesthetic-sensitive parts.
- Streamlining the Process: By focusing on critical performance metrics, we ensure that the manufacturing process stays efficient. For example, we may streamline certain tolerances in non-critical areas to allocate resources to more pressing CTQs, like part strength or dimensional consistency. This targeted approach helps us meet customer needs while maintaining cost-effectiveness.
10.3 Tips for Team Alignment on CTQ Goals
CTQ implementation involves coordination across multiple teams, from design and engineering to tooling and production. Achieving alignment among teams on CTQ goals is crucial for ensuring that everyone is working toward the same objectives.
- Challenge: Miscommunication or lack of understanding between departments can lead to discrepancies in how CTQs are interpreted and implemented. For example, the engineering team may focus on dimensional accuracy, while the tooling team may prioritize cooling efficiency, causing a disconnect in achieving the final product’s quality.
- Best Practice: Clear communication and collaboration are key. At KingStar Mold, we ensure that all departments are involved in the early stages of CTQ planning. During initial design reviews and project kickoff meetings, we share the CTQ tree and discuss the relative importance of each CTQ across teams. This approach helps establish a unified vision for the product and ensures that all parties understand the critical goals.
- Cross-Functional Training: Providing training for team members across different departments can also help. When design engineers understand the tooling constraints and production staff understand the importance of certain design features, they are better equipped to work together toward achieving the CTQs.
- Regular Check-ins: We conduct regular project reviews at KingStar Mold, where progress toward CTQ goals is tracked and any discrepancies are addressed. This keeps teams on the same page throughout the manufacturing process and allows for quick adjustments when necessary.
Conclusion
Critical to Quality (CTQ) reporting is an indispensable component in ensuring high-quality mold production. It transforms customer expectations into measurable, actionable parameters that can be systematically tracked and optimized throughout the manufacturing process. By focusing on the most crucial aspects of the product’s design and functionality, CTQs help manufacturers like KingStar Mold maintain precision and consistency while aligning with customer needs.
At KingStar Mold, we take a proactive approach to managing CTQs, ensuring that all aspects of mold production—from design to tooling and final inspection—are aligned with customer specifications. Through careful monitoring and continuous improvement, we not only meet the required quality standards but also push for innovation and efficiency, resulting in superior products with minimized waste and maximum performance.
We encourage our clients to collaborate closely with us from the outset to clearly define their CTQs. The more detailed and specific the CTQs are, the more effectively we can deliver results that exceed expectations. Working together ensures a smooth workflow, faster time-to-market, and the assurance that the final product aligns with the highest industry standards.