At KingStar Mold, as a leading custom plastic molding service provider in China, we understand that selecting the right plastic molding process is critical to delivering high-quality, cost-effective parts. Plastic molding is essential for producing a vast array of products across industries—from automotive to consumer goods. Each molding technique offers unique advantages depending on design complexity, material, and production volume.
This post explores six common types of plastic molding processes we specialize in, helping you better understand which method fits your project needs.
Injection molding is the most widely used plastic molding process, prized for its versatility and ability to produce complex parts with high precision. In this method, plastic resin pellets are melted and injected under high pressure into a steel mold cavity. Once the molten plastic cools and solidifies, the mold opens to eject the finished part. Injection molding excels in producing large volumes of consistent parts, from automotive components and medical devices to consumer electronics housings. Although initial tooling costs can be high, the cost per part drops significantly with volume, making it ideal for mass production.
There are several specialized types of injection molding that extend its capabilities:
• Overmolding: This involves molding one material over another, allowing multi-material parts with enhanced functionality or aesthetics.
• Insert Molding: In this process, pre-formed components such as metal inserts are placed into the mold before injection, encapsulating them with plastic to create integrated assemblies.
• Gas-Assisted Injection Molding: Uses gas to create hollow sections inside the part, reducing weight and material usage while maintaining strength.
• Micro Injection Molding: Designed for producing extremely small, precise parts often used in medical or electronic applications.
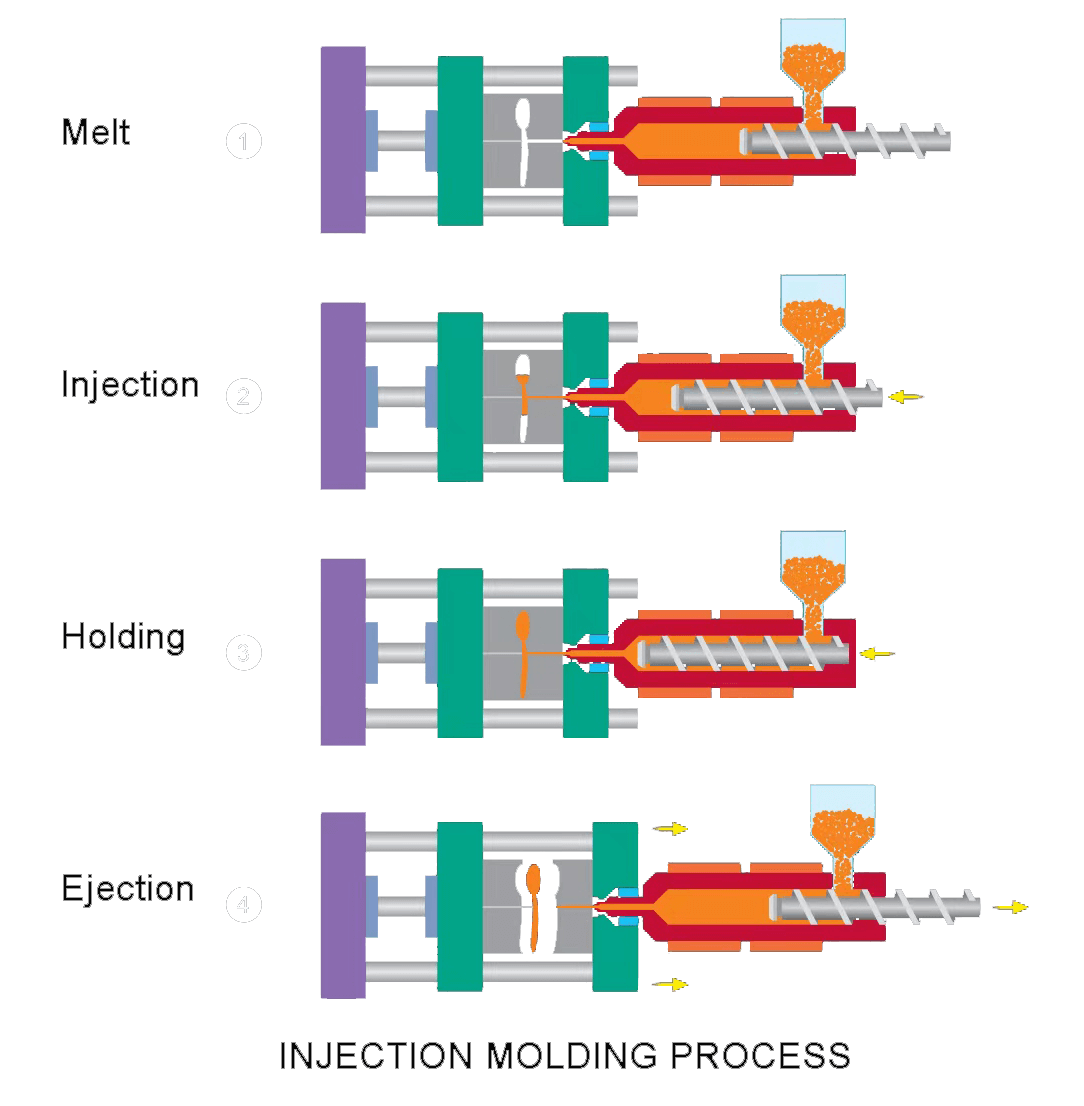
2. Blow Molding
Blow molding is primarily used to create hollow plastic objects, such as bottles, containers, and drums. The process begins with a heated plastic tube called a parison, which is clamped inside a mold. Compressed air is then blown into the parison, inflating it to conform to the mold’s shape. After cooling, the mold opens and the hollow part is ejected. Blow molding offers an efficient way to produce thin-walled, hollow products in high volumes and is compatible with various thermoplastics like polyethylene and polypropylene.
3. Extrusion Molding
Extrusion molding differs from other processes by continuously forcing molten plastic through a shaped die, producing long, continuous profiles with uniform cross-sections. Common extrusion products include pipes, tubing, weatherstripping, and plastic sheets. The extruded material is cooled and cut to length. This process is especially suitable for manufacturing parts requiring consistent thickness and length. Extrusion molding provides a cost-effective solution for producing high volumes of these types of profiles.
4. Compression Molding
In compression molding, a pre-measured amount of plastic material (often a thermosetting resin or composite) is placed into a heated mold cavity. The mold halves close, applying heat and pressure to shape and cure the material into its final form. This process is well-suited for producing strong, durable parts with variable thickness and size, such as automotive panels, electrical components, and industrial parts. Compression molding is cost-effective for medium to large parts and offers excellent mechanical properties due to the curing step.
As a variant of compression molding, transfer molding is designed for intricate parts and those with inserts or detailed features. In this process, plastic material is heated in a chamber and then forced into the mold cavity through a narrow channel called a sprue. This allows for better control over material flow and reduces waste. Transfer molding is often used to produce small, precise components like electrical insulators, seals, and gaskets, especially when thermosetting plastics are involved.
Rotational molding, or rotomolding, is a unique process used to manufacture large, hollow, seamless plastic parts. A powdered resin is placed inside a mold that rotates slowly on two perpendicular axes inside a heated chamber. The resin melts and coats the mold’s interior evenly. After sufficient heating, the mold cools while continuing to rotate, solidifying the part with uniform wall thickness. Rotational molding is ideal for producing tanks, containers, kayaks, and playground equipment.
At KingStar Mold, most of our hard coolers are produced using this rotomolding process. This technique enables us to create durable, seamless coolers with excellent insulation and consistent wall thickness, ensuring high quality and long-lasting performance. Rotational molding also offers low tooling costs and minimal material waste, although cycle times tend to be longer compared to other molding methods.
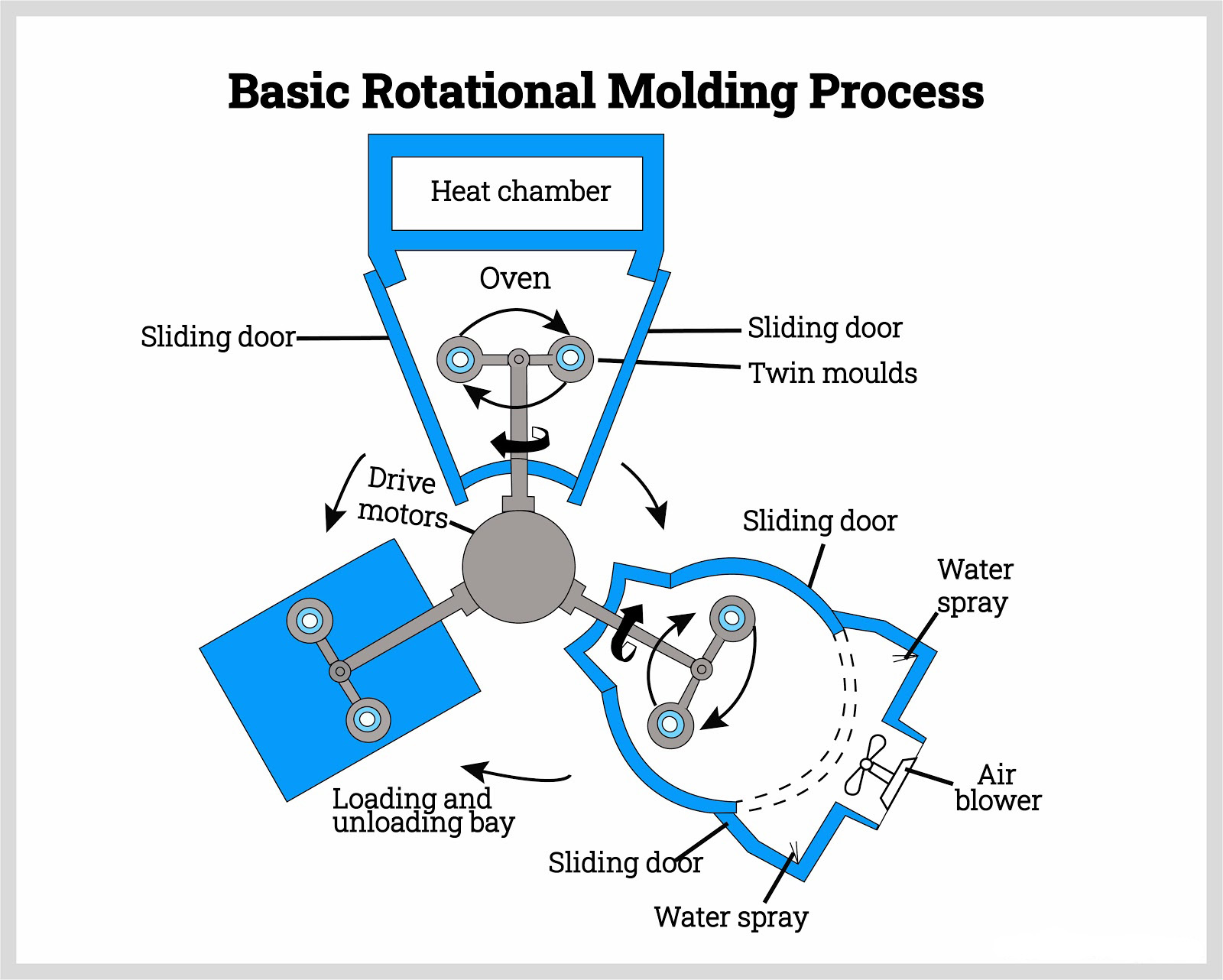
6. Thermoforming
Thermoforming involves heating a plastic sheet until it becomes pliable, then shaping it over a mold by applying vacuum or pressure. Once cooled, the plastic retains the mold’s shape and is trimmed to create the final product. This process is commonly used for packaging, trays, disposable cups, and large panels. Thermoforming is advantageous due to its lower tooling costs and fast turnaround, though it is generally best suited for simpler shapes and thinner materials compared to injection molding.
Conclusion
Choosing the right plastic molding process can significantly impact your product’s quality, cost, and production timeline. At KingStar Mold, our experienced team offers tailored solutions in custom plastic mold building and precision plastic part molding production to meet diverse industry requirements. Whether you need prototypes or high-volume production, our advanced technology and expert know-how ensure reliable, efficient results.
Send email to sales@kingstarmol.com or leave online message today to learn how we can support your project with top-tier plastic molding services and help bring your designs to life.