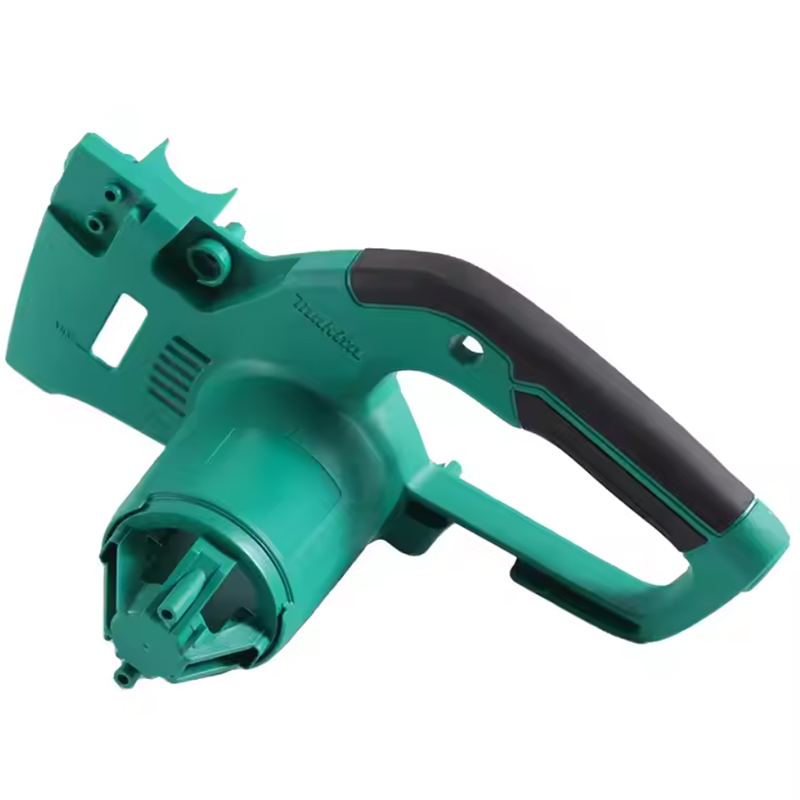
Two-Color or Materials Plastic Parts Solution
Orders Workflow
Initial Consultation & Design Review
We begin by discussing your project’s goals and reviewing the design to ensure it’s optimized for the specific manufacturing process. At this stage, we suggest improvements or adjustments to enhance efficiency, functionality, and manufacturability.
Material Selection
Our experts assist in selecting the right materials for your product based on performance requirements and compatibility with the manufacturing process. The correct material choice ensures durability, cost-effectiveness, and the desired product functionality.
Design & Engineering
Using advanced CAD and simulation tools, we develop a custom design for your project. This step ensures precise details and identifies potential challenges early in the process, optimizing the design for efficient manufacturing.
Prototyping & Sample Testing
A prototype or sample is created to verify design accuracy, functionality, and performance. Rigorous testing is conducted to ensure the product meets your specifications before moving into full-scale production.
Production Setup & Initial Production
We set up the required machines, molds, or tools for the manufacturing process. The initial production run is performed to confirm the setup, assess quality, and fine-tune settings for optimal results.
Final Production & Quality Control
After final approval, we proceed with full-scale production, ensuring continuous quality checks. Comprehensive inspections at each stage ensure that every part meets the highest standards before delivery.
Why Choose KingStar Mold for Two-Shot Molding?
The Benefits of Partnering with KingStar Mold
Advanced Two-Shot Machines
Our two-shot injection molding workshop is equipped with multiple high-efficiency machines, enabling rapid mass production at a lower cost.
Two-Shot Mold Development
We have the capability to design and manufacture high-precision two-color molds in our dedicated mold fabrication workshop, ensuring exceptional quality and accuracy.
Why Choose Our Two-Shot Molding Service
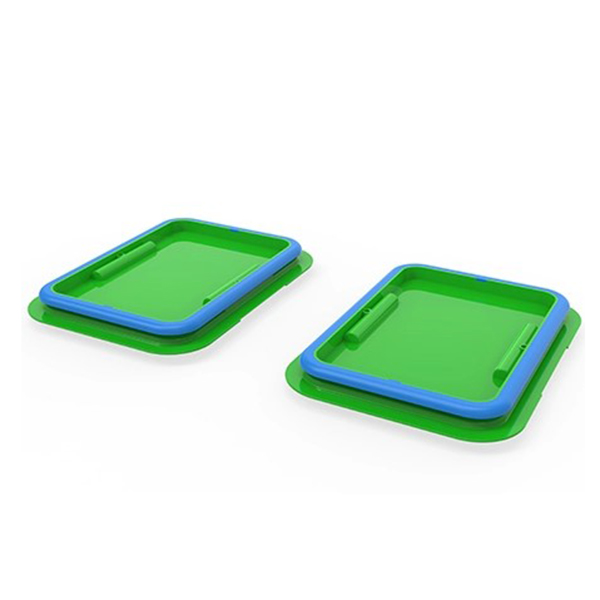
Fast Turnaround Times
We prioritize efficiency at every stage, ensuring quick prototyping and fast production without compromising on quality. Our streamlined process helps you meet tight deadlines with ease.
Cost-Effective Solutions
By optimizing production methods and material usage, we offer competitive pricing while maintaining the highest standards of quality. Our goal is to provide you with exceptional value for your investment.

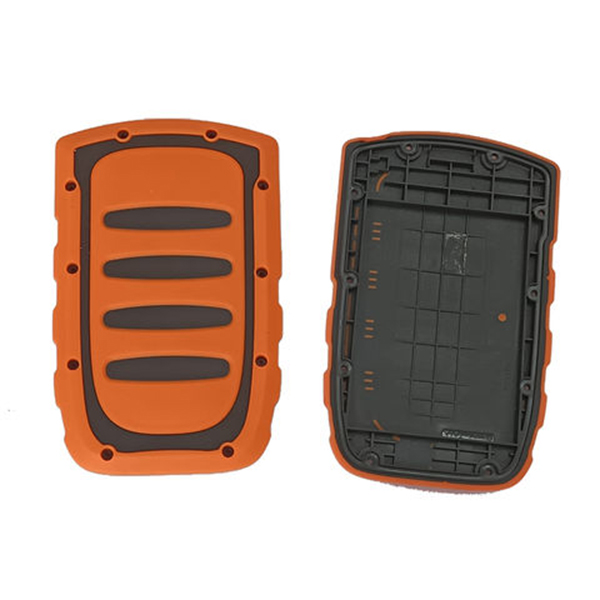
High-Quality, Durable Parts
With our expertise and advanced technology, we produce parts that are not only visually appealing but also built to last. Our focus on durability ensures long-lasting performance in every product we create.
End-to-End Support
From initial consultation to final production, we provide comprehensive support throughout the entire project. Our team is dedicated to guiding you every step of the way to ensure successful outcomes.
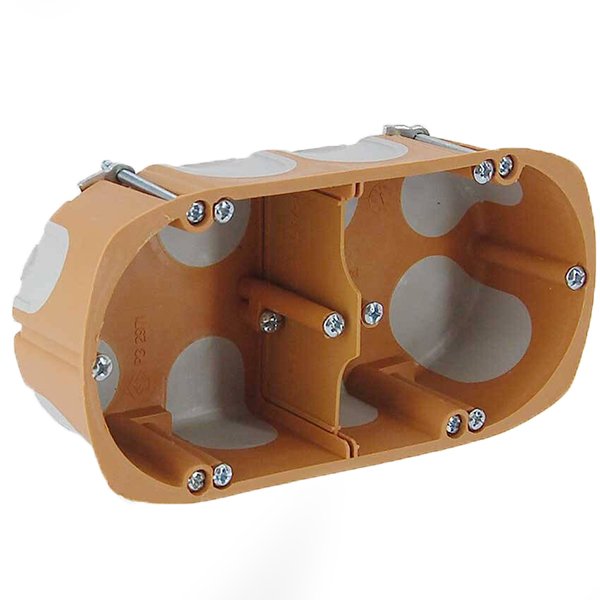
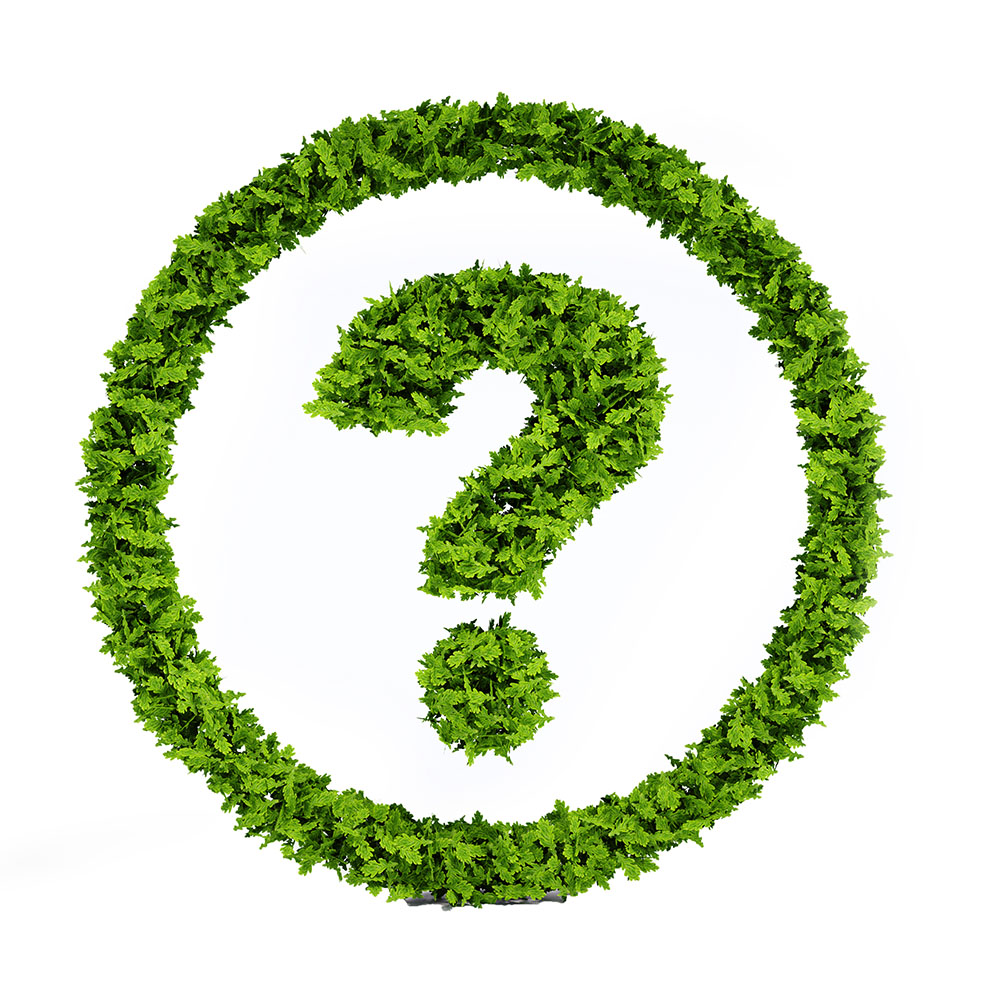
Yes, KingStar Mold offers comprehensive material selection guidance for two-shot molding projects. Our technical experts and materials engineers evaluate a variety of factors, including material properties such as dynamic characteristics, chemical resistance, heat stability, and appearance. Based on this analysis, we recommend materials that are compatible with the two-shot molding process and meet the required performance standards.
At KingStar Mold, we excel at meeting quality standards and optimizing mold creation and assembly processes. We use advanced CAD/CAM software, cutting-edge measurement tools, and precise machining techniques to ensure proper alignment, even material distribution, and strict dimensional control throughout production. We employ various quality checks, including measurement, functionality testing, and performance evaluations, to ensure that every part meets the highest standards of consistency and quality.
The processing time for two-shot molding can vary depending on factors such as the complexity of the part, production volume, material availability, and tool requirements. At KingStar Mold, we prioritize our clients’ time and work closely with them to create customized schedules. With our skilled team, advanced equipment, and efficient production methods, we are able to minimize lead times while maintaining high-quality standards and meeting agreed-upon deadlines.
Two-shot molding is particularly valuable in industries that require complex, multi-material parts with enhanced functionality, aesthetics, and durability. Fields such as consumer goods, automotive, aerospace, and medical products heavily rely on this technique. The process is ideal for creating a variety of products, from ergonomic handles for medical devices to soft-touch grips for portable electronics. Two-shot molding is an excellent way to innovate and differentiate your products in today’s competitive market.
Several important factors must be considered when designing parts for two-shot molding to ensure optimal results:
– Material Compatibility: Choose materials with properties that complement each other and work well together to achieve the desired outcome.
– Part Design: Consider factors like wall thickness, draft angles, and undercuts to ensure the parts are easy to fill and eject from the mold.
– Gate and Runner Design: Plan for efficient material flow and mixing by designing gates and runners that allow for easy access and optimal material distribution.
– Mold Design Features: Incorporate mold features such as cores, holes, and shut-off surfaces that are properly polished to ensure proper material separation and accurate component registration.
– Process Optimization: Adjust factors such as temperature, cycle time, and injection pressure to consistently produce high-quality, precise parts.
Warping can occur in ABS parts due to uneven cooling or inconsistent wall thickness. To reduce warping, we recommend designing parts with uniform wall thickness and incorporating rib structures where possible. Additionally, precise control over the cooling rate and mold temperature during the molding process helps maintain part integrity, resulting in a more stable, warp-free product.
At KingStar Mold, our commitment to excellence distinguishes us from other two-shot molding companies. We bring expertise, state-of-the-art equipment, and innovative solutions, all while prioritizing quality and customer satisfaction. Our goal is to deliver reliable, high-quality results that meet and exceed our customers’ expectations.
The suitability of two-shot molding for mass production depends on the specific project requirements; however, it is capable of handling both small and large-scale orders. With our cutting-edge two-shot molding equipment, advanced process optimization, and streamlined production methods, we can efficiently manage a wide range of production volumes while maintaining consistent quality and efficiency.
At KingStar Mold, we leverage our extensive expertise in material compatibility testing to handle all of your two-shot molding requirements. Before production, we conduct thorough tests to ensure the selected materials are suitable and will bond effectively throughout the molding process. Using advanced molding techniques, precise process control, and rigorous quality assurance, we maintain optimal conditions for material compatibility in every project.
Two-shot molding provides several advantages over traditional manufacturing methods, including:
– Improved Durability: This process allows for combining multiple materials or colors in a single cycle, resulting in stronger, more durable components with fewer weak spots. It also eliminates the need for additional assembly steps, enhancing overall product integrity.
While the initial cost of two-shot molding may be higher, it can save money over time by reducing material waste, streamlining the manufacturing process, and shortening assembly times.
– Faster Production: By creating complex parts in a single mold cycle, two-shot molding can significantly reduce lead times, speeding up delivery.
Two-shot molding utilizes a specialized mold designed to handle two injection cycles. This mold and its supporting systems are engineered to complete both shots without needing to remove the partially molded product between stages.