Injection molding is one of the most widely used manufacturing processes in producing plastic parts across various industries, including automotive, electronics, and consumer goods. Its efficiency, precision, and ability to produce complex shapes make it a preferred choice for large-scale production. However, the success of the injection molding process depends on several factors, and one of the most significant challenges that manufacturers face is ensuring that the final products meet the desired quality standards.
Among the various defects that can occur during injection molding, flow marks (or flow lines) are a critical concern. These visible imperfections typically appear on the surface of molded parts, often in the form of wavy lines or concentric circles. While flow marks may not always affect the functionality of a part, they can significantly impact its aesthetic appeal and, in some cases, its structural integrity. Since consumers and industries prioritize both functionality and appearance, even minor defects can lead to part rejection or costly rework, making it essential to understand their causes and take preventive measures.
In this article, we will explore two common types of flow marks in injection molding, their causes, and how to prevent them. As a leading injection molding company with extensive experience, we have compiled this guide to help fellow manufacturers and design engineers. Understanding and addressing these imperfections is essential for producing high-quality, visually appealing products. We’ll discuss practical solutions and design modifications to eliminate flow marks, ensuring both functionality and aesthetics are met, ultimately leading to better production outcomes.
- 1. What Are Flow Marks?
- 2. Type 1: Flow Marks from Uneven Melt Flow
- 3. How Exactly Uneven Melt Flow Leads to Flow Marks
- 4. How to Prevent Flow Marks from Uneven Melt Flow
- 5. Type 2: Flow Marks Caused by Temperature Gradient Issues
- 6. The Role of Temperature in Flow Marks
- 7. How to Avoid Flow Marks from Temperature Gradient Issues
- 8. Best Practices for Preventing Both Types of Flow Marks
- 9. Conclusion
1. What Are Flow Marks?
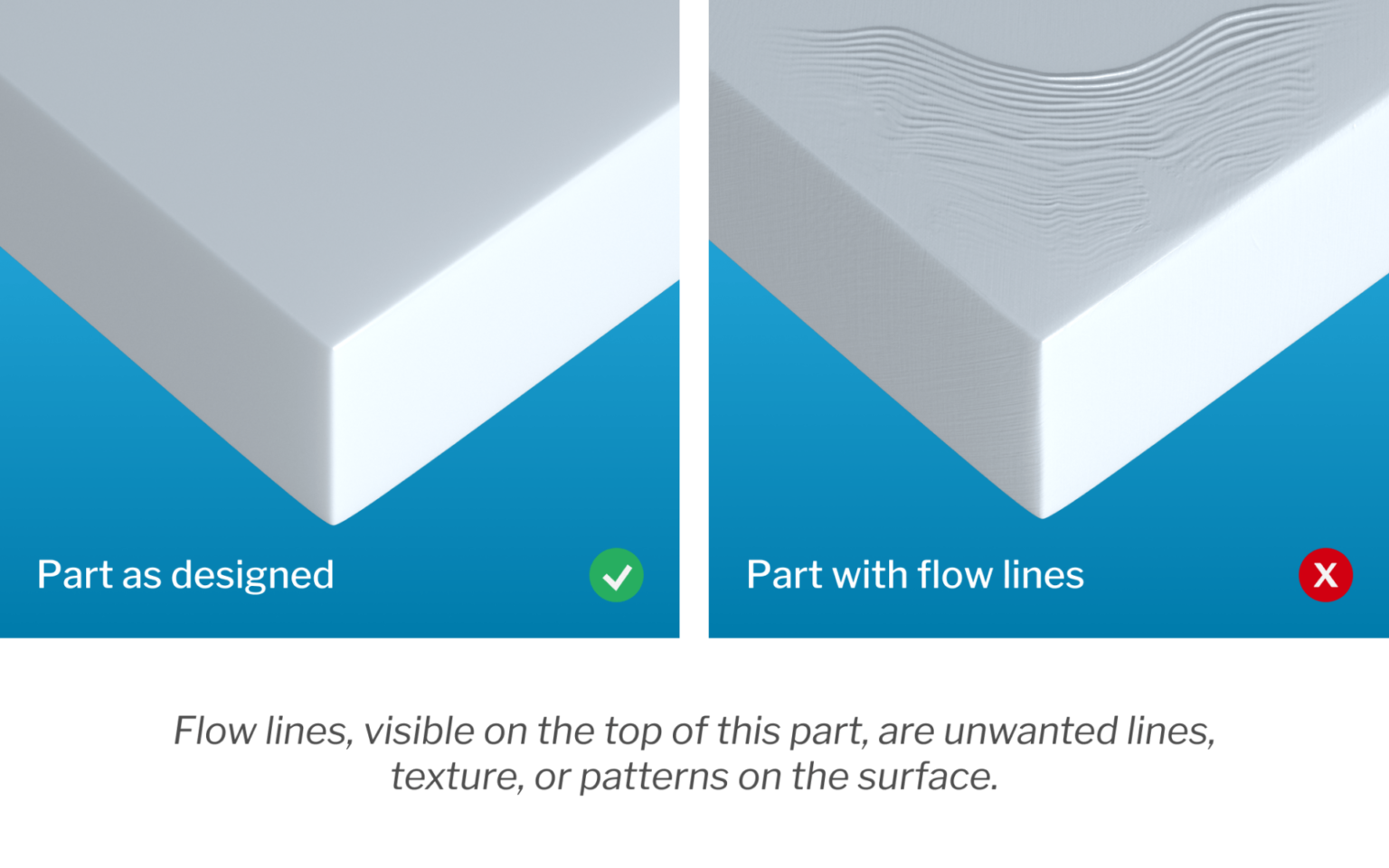
Flow marks, also known as flow lines, are visible surface imperfections that appear on molded parts as wavy lines or patterns. These marks are a result of the non-uniform flow of molten plastic as it enters the mold cavity during the injection molding process. Flow marks typically form as concentric circles or linear patterns, which can be noticeable after the part cools and solidifies.
These imperfections can significantly affect the visual quality of the molded parts. In some cases, they may not impair the part’s functionality, but they can make the product look less professional or lower its aesthetic value, which is crucial for products that require a flawless finish, such as consumer goods and automotive parts. Additionally, flow marks may indicate issues with the molding process, such as improper temperature, pressure, or gate design, which can also impact the overall quality and performance of the part.
2. Type 1: Flow Marks from Uneven Melt Flow
Flow marks from uneven melt flow often manifest as wavy or concentric patterns around the gate area where the molten plastic first enters the mold. These marks are a direct result of inconsistent flow caused by temperature differences and poor melt uniformity.
Flow marks can degrade the visual quality of the molded product, which can impact its market appeal. While these marks may not affect the product’s functionality, they can make the product less desirable, especially in applications where appearance is critical.
Inconsistent Flow Patterns and Cooling Rates Cause Defects
Flow marks are a direct result of uneven flow during the injection molding process. When molten plastic is injected into the mold cavity, it should ideally fill the mold evenly. However, if the flow is not uniform, some parts of the cavity may receive molten plastic earlier than others, while others might take longer. This difference in timing causes uneven cooling as well.
- How it happens:
If some areas of the mold cool prematurely, the molten plastic will harden in those spots while other areas remain liquid. As the plastic continues to fill the mold, the flow pattern will be disrupted, resulting in visible lines, waves, or concentric patterns on the surface of the molded part. - Effect:
The cooling rate is crucial because premature cooling not only creates flow marks but also affects the final strength and dimensional accuracy of the part. The uneven cooling can lead to warping, sink marks, or internal stresses in addition to surface defects.
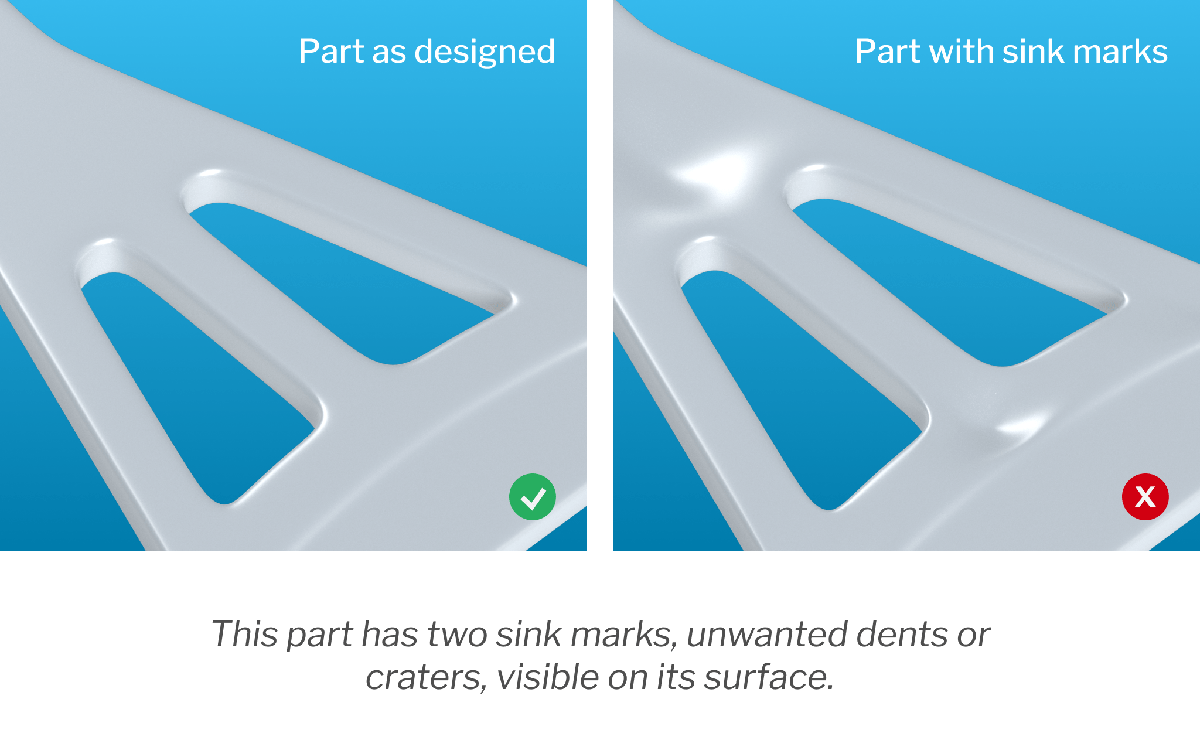
The Role of Temperature Gradients in Melt Flow
Temperature gradients play a significant role in the formation of flow marks. When molten plastic enters a cooler mold, the outer layers of the plastic start to cool and solidify quickly, while the inner layers of the molten plastic remain hotter and more fluid. This creates a temperature gradient, which impacts the uniformity of the flow.
- How temperature gradients affect flow:
As the molten plastic flows into the mold cavity, the cooler mold areas cause the outer layers of the melt to solidify faster, while the inner melt maintains its fluidity. This creates an uneven flow pattern, with the flow of the molten plastic not being consistent. These variations in the flow and cooling rates result in flow marks on the surface of the molded part. - Effect on the product:
Temperature gradients lead to the formation of visible surface defects. The faster-cooled regions near the mold surface restrict the flow of the melt, causing the slower-moving material to form wavy patterns. The result is a surface that looks uneven or streaked, with flow lines that can diminish the aesthetic quality of the product.
3. How Exactly Uneven Melt Flow Leads to Flow Marks
In the previous section, we discussed the theoretical causes of flow marks, and for this section we will show some specific problems that may occur in practice and visual effect of each misoperation.
Cause 1: Slow Injection Speed
A slow injection speed occurs when the molten plastic is injected into the mold at too low a velocity, causing the melt to cool before it fully fills the mold cavity. This results in uneven flow patterns, as some areas of the molten plastic cool prematurely.
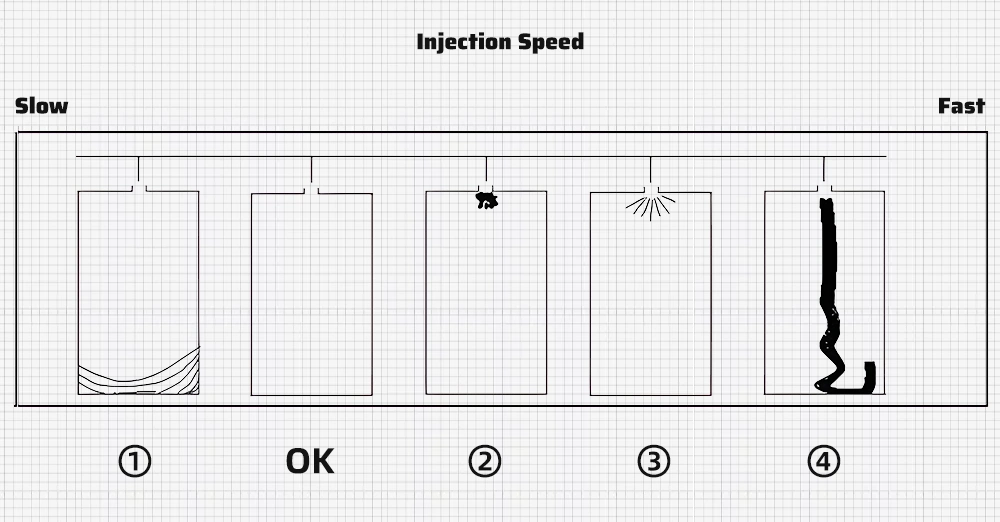
- Effect:
Flow marks typically appear as wavy or concentric patterns around the gate area. As the melt cools too quickly in some areas, the flow becomes uneven, leading to visible flow lines on the molded part’s surface.
Cause 2: Low Injection Pressure
Low injection pressure means there isn’t enough force to push the molten plastic into the mold evenly. This can prevent the mold from filling properly and lead to inconsistent flow.
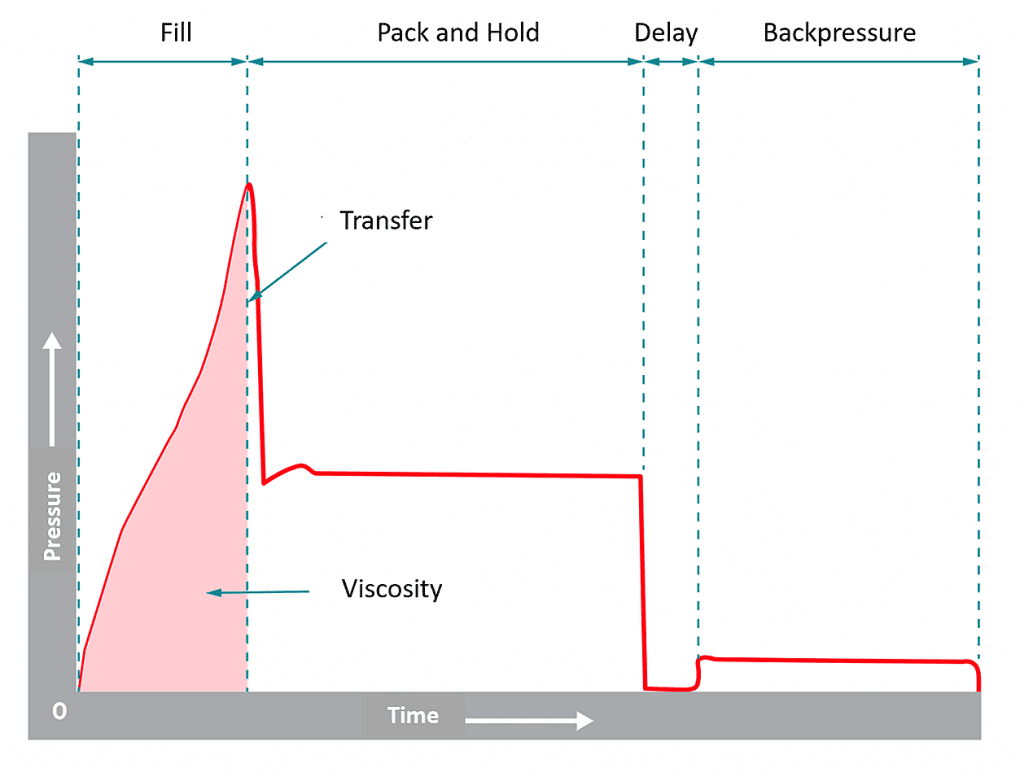
- Effect:
Flow marks usually form as irregular patterns, especially near the injection point. Since the pressure is insufficient, the molten plastic doesn’t fill the mold completely, and the flow becomes uneven, creating noticeable surface defects.
Cause 3: Low Mold Temperature
When the mold temperature is too low, the molten plastic cools too quickly as it enters the mold. This premature cooling results in areas of the mold solidifying too early, hindering the flow of the remaining molten plastic.
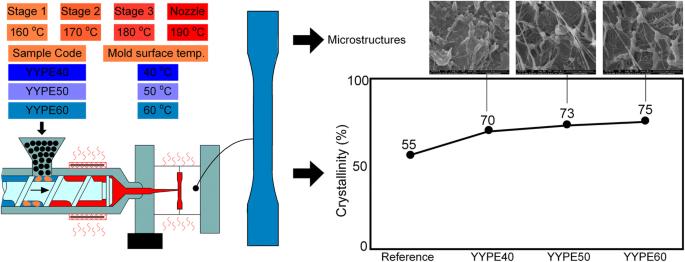
- Effect:
The resulting flow marks appear as uneven color patches or lines on the molded part. The temperature difference between the solidified and the still-flowing plastic leads to irregular surface patterns, especially near the mold’s gate area.
Cause 4: Incorrect Gate or Runner Design
Improper gate or runner design, such as narrow runners or small gates, can restrict the flow of the molten plastic. This limited flow causes some areas of the mold to fill inadequately, leading to uneven pressure and cooling.
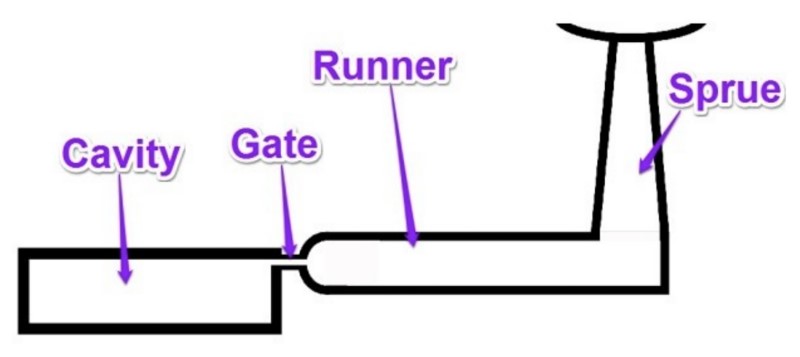
- Effect:
Flow marks arise as the molten plastic is forced to travel through narrow channels, causing it to cool unevenly. This results in inconsistent filling and surface defects, particularly in areas of the molded part close to the gate or where the flow is restricted.
Cause 5: Low Melt Temperature
If the melt temperature is too low, the plastic’s viscosity increases, reducing its flowability. A lower melt temperature makes it harder for the plastic to fill the mold completely, often leaving parts of the cavity underfilled.
- Effect:
Low melt temperatures can cause poor flowability, leading to visible flow marks. These marks occur because the molten plastic doesn’t flow smoothly into the mold, resulting in uneven filling and surface defects.
4. How to Prevent Flow Marks from Uneven Melt Flow
Now that we know how the flow marks occur, the types of misoperation, and corresponding visual effects, we are now sharing some ways to improve the process.
Optimizing Injection Speed and Pressure
To prevent flow marks caused by uneven melt flow, optimizing injection speed and pressure is crucial.
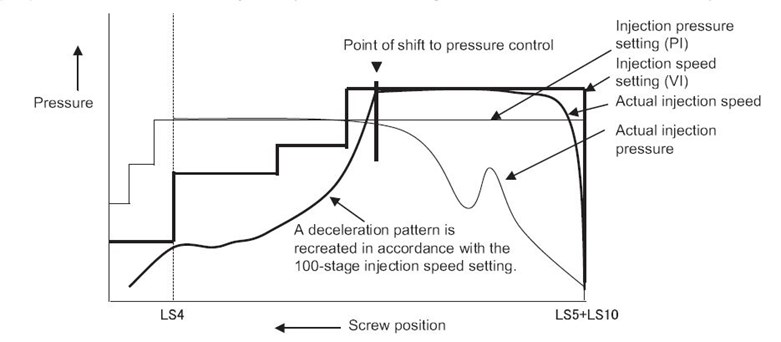
- Injection Speed:
Increasing the injection speed ensures that the molten plastic reaches the mold quickly, minimizing the chances of premature cooling. Faster injection reduces the time for the plastic to cool before it fills the mold completely, helping to maintain a consistent flow pattern. - Injection Pressure:
Similarly, adequate injection pressure is essential to maintain uniformity in the melt. Low pressure may not adequately pack the mold, leading to incomplete filling and uneven flow, which creates flow marks. By increasing the pressure, the molten plastic is injected more uniformly into the mold, ensuring consistent filling and reducing the risk of surface defects.
Both injection speed and pressure must be balanced to ensure the melt is injected smoothly, without rushing the process or causing turbulence that could lead to other issues like jetting or air traps.
Adjusting Mold Temperature
Maintaining the correct mold temperature is essential in preventing flow marks.
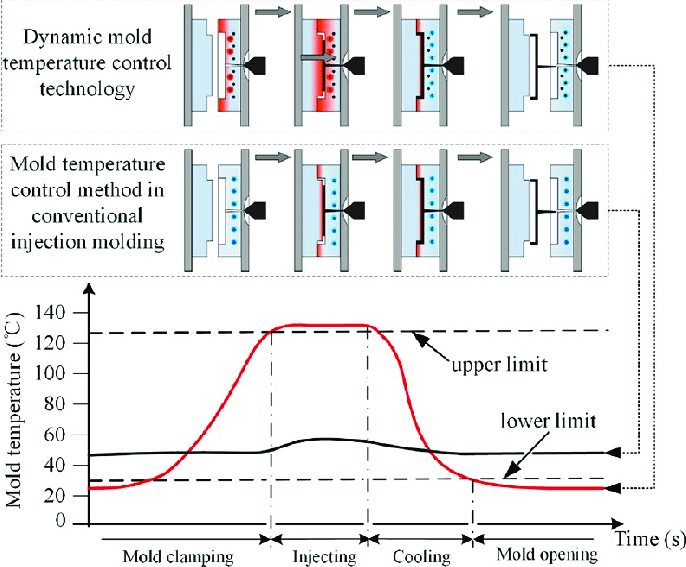
- Preventing Premature Cooling:
If the mold temperature is too low, parts of the molten plastic will cool and solidify before filling the cavity. This premature cooling can cause flow marks as the material cools unevenly across the mold surface. By raising the mold temperature to an optimal level, the flow of the molten plastic becomes more uniform, reducing the risk of flow marks and improving the part’s overall surface quality. - Consistent Temperature Control:
Consistent control of mold temperature throughout the process helps prevent temperature gradients that cause uneven flow. Cooling channels in the mold should be adjusted to ensure even heat dissipation, allowing for more uniform melt flow and cooling. A stable temperature also helps to reduce stresses that could affect the structural integrity of the molded part.
Improving Gate and Runner Design
The design of the gates and runners plays a significant role in preventing flow marks caused by uneven flow patterns.
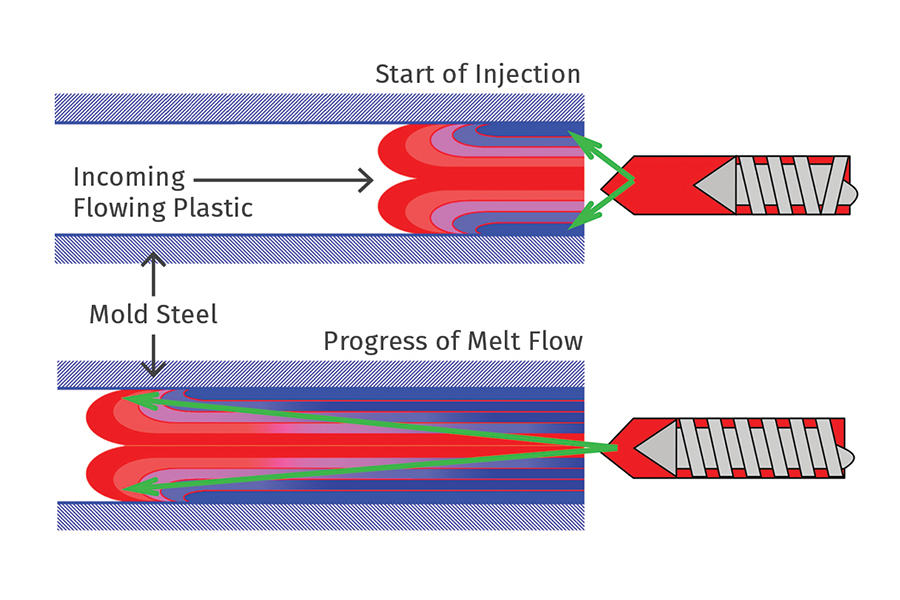
- Correct Gate and Runner Size:
Gates and runners that are too small restrict the flow of molten plastic, leading to higher chances of uneven flow. Small gates cause the melt to slow down, cool prematurely, and form inconsistent patterns. By ensuring the gates and runners are appropriately sized, you can prevent bottlenecks in the flow path, allowing for a smoother, more even injection process. - Optimized Flow Paths:
A well-designed gate and runner system ensures that the molten plastic flows evenly into all parts of the mold. Properly designed gates (e.g., fan gates or edge gates) and well-calculated runner systems help distribute the melt more evenly across the mold cavity, reducing the likelihood of flow marks and improving part quality.
5. Type 2: Flow Marks Caused by Temperature Gradient Issues
Flow marks caused by temperature gradient issues are another common defect in injection molding. These marks typically appear as circular or linear patterns on the surface of the molded part, often surrounding thicker or hotter sections of the part.
Cause: Inconsistent Mold or Melt Temperatures
Temperature gradients are caused when there are differences in the temperatures between the mold, the molten plastic, and sometimes even the mold’s cooling system. These temperature differences can lead to uneven cooling and flow behavior, which results in flow marks on the surface of the part.

- Mold Temperature Variations:
If the mold temperature is not consistent across the entire mold, some areas may cool faster than others, causing the melt to solidify unevenly. This results in visible flow marks as the plastic fills areas that have different cooling rates. - Melt Temperature Differences:
When the molten plastic enters the mold, it may have varying temperatures due to inconsistent heating or improper material preparation. These differences in temperature affect the viscosity and flowability of the plastic, contributing to uneven flow and surface defects.
Effect on Product: Circular or Linear Flow Marks
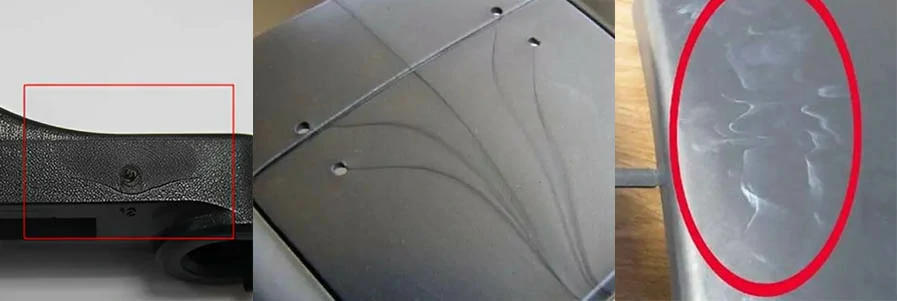
- Flow marks caused by temperature gradients typically appear as circular or linear patterns around areas of the molded part that are either thicker or have more heat retention. These marks may surround thicker sections of the part that have more mass and take longer to cool.
- Areas with inconsistent temperature may show distinct marks, which could be circular in shape around thicker areas, or linear around parts where cooling was uneven, such as the edge of a thick section of plastic.
6. The Role of Temperature in Flow Marks
Temperature plays a crucial role in the formation of flow marks during the injection molding process. The way temperature variations are managed can significantly impact the flow pattern and surface finish of the molded parts.
How Different Temperatures in the Mold and Melt Contribute to Non-Uniform Flow
The temperature differences between the molten plastic and the mold itself directly affect the flow of plastic as it fills the mold cavity. When the temperature of the mold is too low or inconsistent, it causes parts of the molten plastic to cool and solidify prematurely.
- Premature Cooling:
Premature cooling occurs when areas of the mold cool faster than others, causing parts of the molten plastic to harden before the cavity is fully filled. This leads to uneven filling and flow marks on the surface. - Inconsistent Melt Temperature:
If the melt temperature is not uniform across the mold cavity, the plastic may flow unevenly into the mold, leading to non-uniform cooling and the formation of visible surface defects.
The Effects of Premature Cooling and Rapid Solidification
- Premature Cooling:
When molten plastic cools too quickly due to low mold temperatures or fast solidification, flow marks are formed. These marks can be circular or linear and will appear as uneven areas where the plastic hardened faster than in other parts of the mold. - Rapid Solidification:
Rapid solidification of the plastic in some areas causes shrinkage, which can lead to internal stresses, warping, and visible flow marks on the surface. The result is an inconsistent texture and appearance that degrades the overall aesthetic quality of the molded part.
7. How to Avoid Flow Marks from Temperature Gradient Issues
Now that we’ve explored the causes of flow marks due to temperature gradients, let’s look at some methods to prevent these issues in the injection molding process.
Increasing Melt and Mold Temperature: Balancing Heat for Uniform Flow
Maintaining consistent and balanced temperatures throughout the molding process is critical to avoiding temperature gradient issues.
- Melt Temperature:
Increasing the melt temperature ensures that the plastic is more fluid, allowing it to flow evenly into the mold cavity. Higher melt temperatures also reduce the risk of premature cooling, which can lead to flow marks. - Mold Temperature:
Similarly, adjusting the mold temperature to a consistent and optimal level helps ensure that the plastic flows evenly. If the mold temperature is too low, the plastic will cool too quickly and lead to surface defects. Higher mold temperatures promote even cooling, which helps to reduce temperature gradients and the formation of flow marks.
Using Hot Runner Systems: Maintaining Consistent Temperature Throughout the Part
Hot runner systems help prevent temperature fluctuations in the mold by keeping the molten plastic at a consistent temperature as it travels through the runner system.
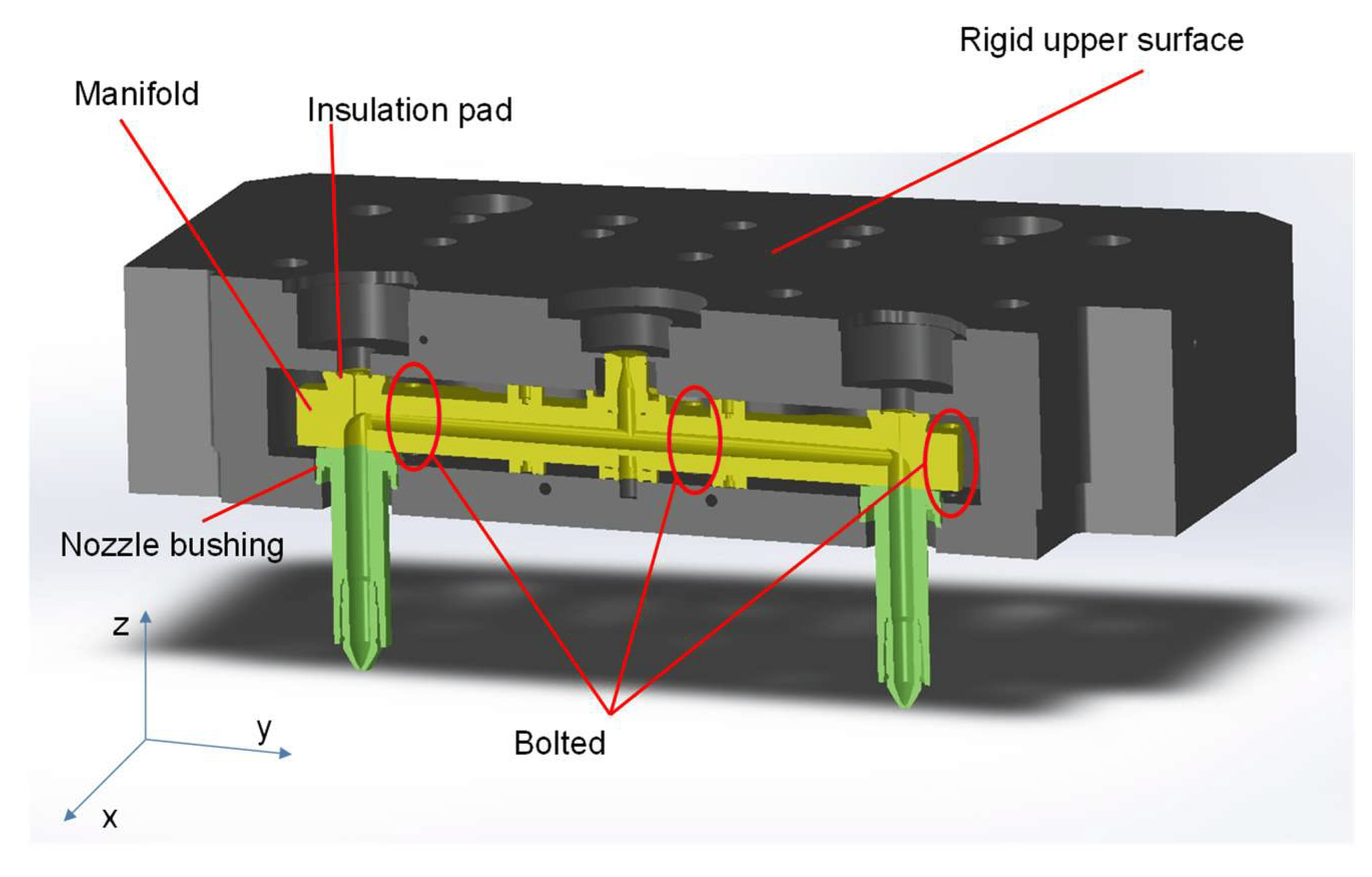
- Consistent Heat Distribution:
A hot runner system maintains the temperature of the melt throughout the molding process, preventing the plastic from cooling too quickly or unevenly. By ensuring that the molten plastic is kept at an optimal temperature, hot runner systems help minimize the formation of flow marks caused by temperature gradients. - Improved Flow Control:
Hot runners allow for better control of the flow of the molten plastic into the mold, which helps ensure that the material fills the cavity evenly and avoids the formation of visible flow lines.
Optimizing Cooling Time and Uniformity: Preventing Thermal Gradients
Optimizing the cooling time and uniformity is key to minimizing thermal gradients in the mold.

- Cooling Channel Design:
Ensuring that the cooling channels in the mold are evenly distributed and optimized allows for uniform cooling across the entire part. This prevents areas of the part from cooling too quickly, which would otherwise lead to flow marks. - Cooling Time Adjustment:
Adjusting the cooling time to allow for a more gradual solidification of the plastic helps to maintain a uniform temperature distribution, reducing the risk of thermal gradients and the resulting surface defects.
8. Best Practices for Preventing Both Types of Flow Marks
Preventing flow marks in injection molding requires a combination of optimized injection parameters, improved mold design, and the use of advanced mold technologies. By following these best practices, manufacturers can minimize the risk of both types of flow marks—those caused by uneven melt flow and temperature gradient issues.
Balanced Injection Parameters: Managing Speed, Pressure, and Temperature
Properly balancing the injection parameters is crucial to ensuring uniform melt flow and preventing flow marks.
- Injection Speed:
Increasing the injection speed ensures that the molten plastic reaches the mold quickly, reducing the risk of premature cooling and promoting a more uniform flow. However, the speed should be controlled to avoid turbulence or issues like jetting. - Injection Pressure:
Adequate injection pressure is essential for pushing the molten plastic into the mold evenly. Too low a pressure will result in incomplete filling and inconsistent flow, leading to visible flow marks. Ensuring sufficient pressure throughout the process helps maintain consistent flow and reduces defects. - Melt and Mold Temperature:
As discussed, the correct temperature settings are critical for smooth, uniform flow. Maintaining optimal melt and mold temperatures ensures that the plastic fills the cavity properly and cools evenly, reducing the likelihood of flow marks due to temperature gradients or uneven melt flow.
Mold Design Improvements: Rounding Sharp Corners and Adjusting Gate Placement
The design of the mold itself plays a significant role in preventing flow marks. Several design improvements can help optimize flow and reduce defects.
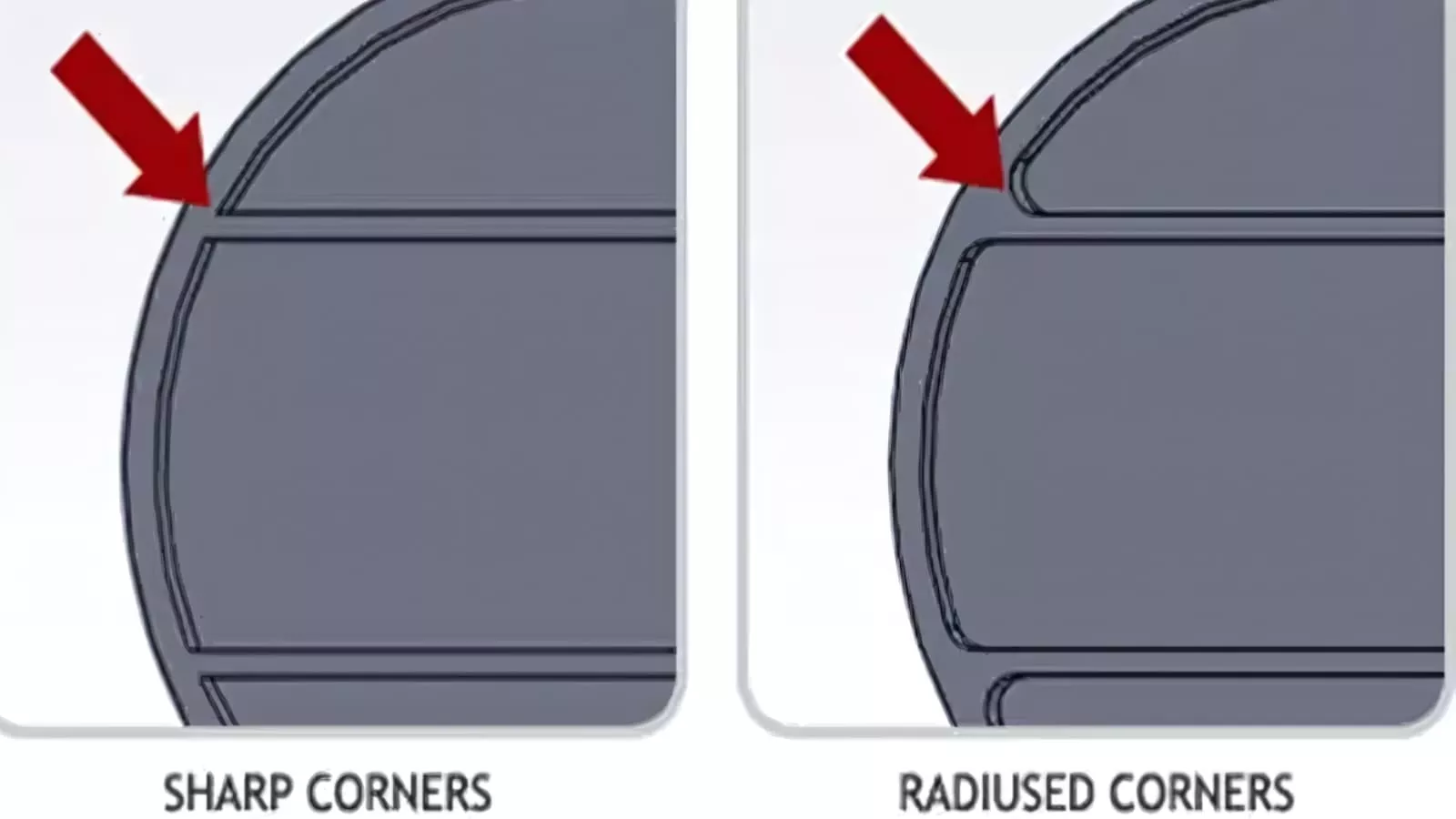
- Rounding Sharp Corners:
Sharp corners in the mold can cause flow disruptions, leading to uneven filling and the formation of flow marks. By rounding sharp corners and edges, the molten plastic flows more smoothly, reducing the likelihood of uneven cooling or flow patterns. - Adjusting Gate Placement:
Proper gate placement ensures that the molten plastic flows evenly into the cavity. Gates placed in areas with thinner sections help ensure even distribution of the melt. Conversely, poorly placed gates can cause uneven filling and premature cooling, which leads to flow marks. A well-designed gate system reduces the risk of localized cooling differences, which is crucial for maintaining part quality.
Advanced Mold Technologies: Utilizing Hot Runner Systems and Optimizing Mold Cooling
Advanced mold technologies can significantly enhance the molding process and help prevent flow marks.
- Hot Runner Systems:
Hot runner systems maintain a consistent temperature for the molten plastic as it travels through the runner and into the mold cavity. This reduces the risk of temperature gradients and helps ensure uniform flow. By keeping the melt at an optimal temperature, hot runner systems minimize surface defects like flow marks caused by uneven cooling. - Optimizing Mold Cooling:
Proper cooling is key to achieving uniform solidification of the molded part. Optimizing the cooling channels and controlling cooling time ensures that the mold temperature remains consistent throughout the process. This prevents temperature gradients and allows for even cooling, reducing the risk of flow marks and improving the overall quality of the part.
By adopting these best practices—managing injection parameters carefully, improving mold design, and utilizing advanced technologies—manufacturers can significantly reduce the occurrence of flow marks, ensuring high-quality molded parts with optimal aesthetics and functionality.
9. Conclusion
Flow marks are a common issue in injection molding, affecting both the aesthetic and functional quality of molded parts. Understanding the two primary types of flow marks—those caused by uneven melt flow and temperature gradient issues—allows manufacturers to pinpoint the root causes and take corrective actions.
To mitigate flow marks, it is essential to fine-tune injection molding parameters such as injection speed, pressure, and temperature. By carefully controlling these variables, manufacturers can achieve a consistent flow pattern, prevent premature cooling, and avoid temperature gradients. Small adjustments can make a significant difference in reducing surface defects and improving overall product quality.
Working with experienced and reliable injection mold providers, like KingStar Mold, ensures that your parts are produced to the highest standards. KingStar Mold specializes in precise injection molding, offering advanced technologies, custom mold designs, and in-depth knowledge of the industry. Their expertise in optimizing molding parameters and preventing flow marks results in high-quality, aesthetically pleasing, and functional molded parts.
Leave online message or send email to sales@kingstarmold.com to ensure your products meet both visual and performance standards, enhancing customer satisfaction and market competitiveness.