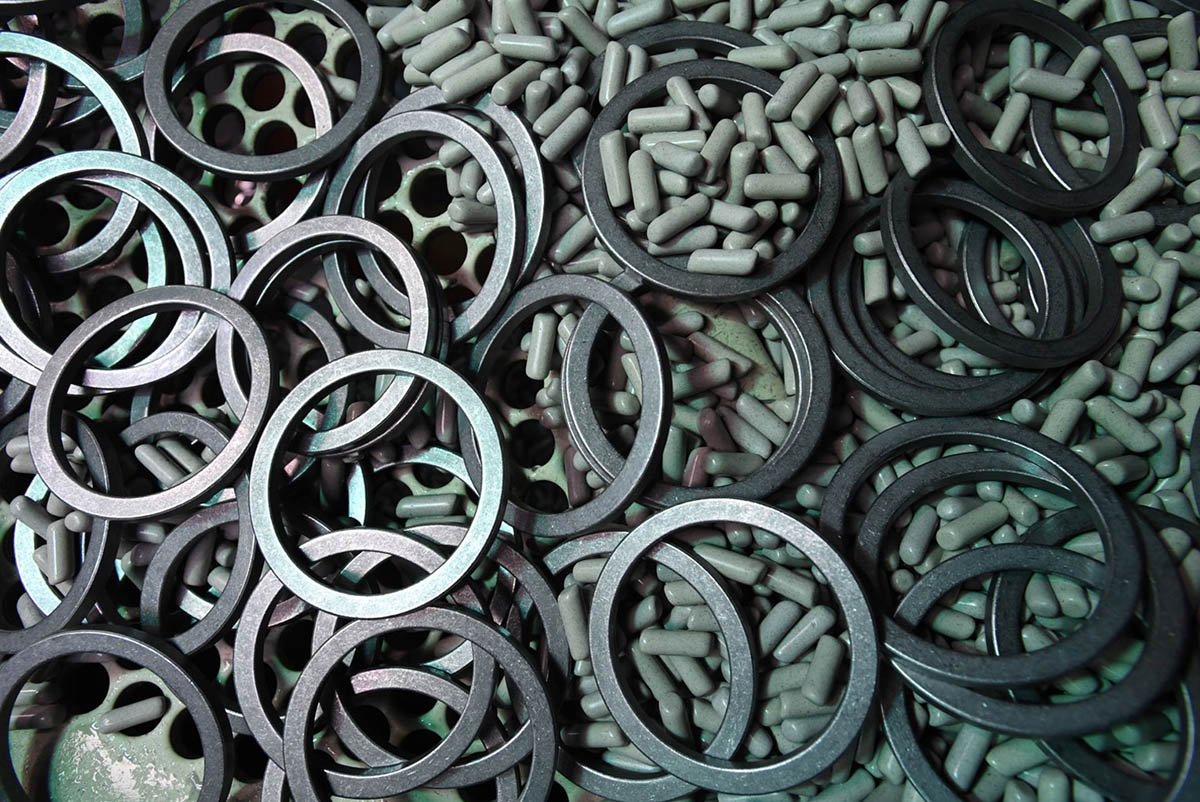
What is Tumbling & How Does It Work?
Tumbling, also known as mass finishing or harperizing, is a highly effective process used to smooth and polish manufactured parts by removing surface defects, burrs, and rough edges. Compared to other surface treatment processes, tumbling can process a large number of parts at once, thus saving both time and cost.
It works by placing parts, abrasive media, and a compound into a rotating or vibrating chamber. As the machine moves, friction between the parts and media gently grinds down surface imperfections, smooths edges, and polishes the material. In high-energy tumbling, like centrifugal barrel finishing (CBF), the barrels spin on a turret, generating intense forces that accelerate the process and deliver consistent, high-quality finishes—even on hard metals or complex geometries.
Common Material Choice
Applications Comparison Table
Application Category | Process Objectives | Applicable Materials | Technical Parameters & Media | Industry Use Cases |
---|---|---|---|---|
Surface Finishing | Polishing, Brightening, Burnishing, Smoothing | Steel, Stainless Steel, Aluminum, Brass, Copper, Titanium, Cobalt-Chromium Alloys | Media: Ceramic (aggressive cut), Plastic (soft polish), Carbon Steel (high-gloss finish) Roughness (Ra): 0.1–1.25 μm |
Jewelry, Watch Components, Decorative Hardware |
Deburring & Edge Conditioning | Burr Removal, Flash Removal, Edge Rounding (Radius ≤0.2 mm) | Die-cast Aluminum/Zinc, Machined Steel, Titanium Fasteners | Media: Plastic Cones/Stars (internal edges), Ceramic Triangles (external edges) Cycle Time: 15–120 mins |
Automotive Parts, Aerospace Fasteners, Medical Implants |
Cleaning & Pretreatment | Rust/Scale Removal, Degreasing, Oxide Stripping | Carbon Steel, Stainless Steel, Copper Alloys | Compound: Alkaline/Chelating Agents + Water Process: Wet Tumbling (pH 8–10) |
Metal Recycling, Electroplating/Anodizing Prep |
Surface Hardening | Work Hardening, Densification | Tool Steel, Bearing Alloys (e.g., SAE 52100), Cobalt-Chromium | Media: Carbon Steel Shot (G50–G120) Pressure: 5–20 G-force Hardness Increase: 10–15% |
Cutting Tools, Wear-Resistant Components |
Contaminant Removal | Slag/Shot Blast Residue Elimination, Particulate Extraction | Investment Castings, Forged Components | Media: Synthetic Abrasives (Non-embedding) Filtration: <50-μm Particles |
Foundry Outputs, Forging Shops |
Edge Radiusing | Precision Edge Rounding (Radius 0.1–0.5 mm) | Titanium Sheets, Aluminum Extrusions, Magnesium Alloys | Media: Ceramic Obloids, Preformed Resin Media Tolerance: ±0.05 mm |
Aircraft Skin Panels, Electronics Enclosures |
Stress Relieving | Micro-Crack Closure, Residual Stress Reduction | Ground Gears, Laser-Cut Parts, Heat-Treated Components | Media: Non-abrasive Ceramic Media Cycle: Low-Speed Tumbling (2–8 hrs) |
Precision Gears (pre-grinding), Engine Components |
Surface Texturing | Matte Finishing (Ra >2.5 μm), Satin Finish | Brass Fittings, Architectural Bronze, Medical Devices | Media: Walnut Shells, Organic Grits Process: Dry Tumbling |
Consumer Electronics, Surgical Instruments |
*Resources:
1. Pre-shaving Gear Hobs. General Administration of Quality Supervision, Inspection and Quarantine of the People’s Republic of China / Standardization Administration of China. [2012-03-09]
2. Guidelines for the Technical Examination of Bronze Sculpture. David Bourgarit et al. [2025]
Benefits of Tumbling
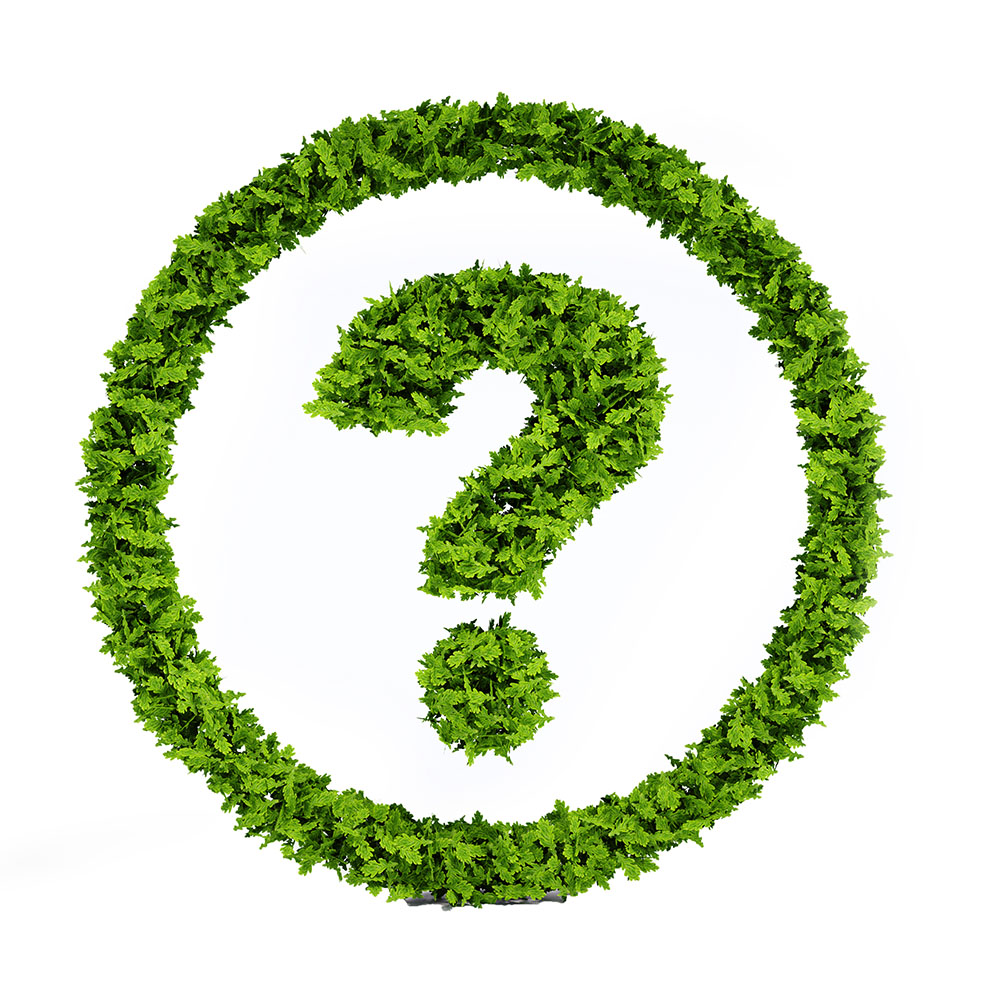
Frequently Asked Questions
Tumbling provides highly consistent surface finishes across batches, especially when media type, part load, and cycle time are carefully controlled. At KingStar Mold, our vibratory and centrifugal systems maintain uniform motion and part exposure. We routinely achieve surface roughness (Ra) values within ±5% of target across batches, and dimensional changes from edge rounding or surface removal typically remain under ±0.001″ (±0.025 mm), depending on the part geometry and media type. Our in-process checks ensure every part meets the required surface spec and aesthetic uniformity.
Yes, but it requires careful media selection and process control. Softer media like plastic or corn cob is used to avoid deformation or surface damage. Low-energy tumbling or shorter cycle times are also recommended for fragile parts. At KingStar Mold, we fine-tune parameters to protect precision and cosmetic components.
Absolutely. KingStar Mold tailors the tumbling process based on your material, geometry, and finish requirements. Whether it’s a delicate medical component or rugged industrial hardware, we deliver optimized results every time.
The number of parts that can be processed at once during tumbling depends on the machine type, part size, and media-to-part ratio. For example:
-
Vibratory tumblers (1–100 cu ft capacity) can handle anywhere from 500 to over 10,000 small parts per cycle, depending on part size and batch configuration.
-
Centrifugal barrel finishers can process hundreds to a few thousand precision parts in one run, with cycle times as short as 10–30 minutes.
-
Rotary barrel tumblers can hold 50–300 lbs of combined parts and media, ideal for medium to large part volumes.
At KingStar Mold, we tailor each batch size based on part geometry, finish requirements, and material sensitivity—ensuring efficient, high-throughput finishing without compromising quality.
Yes, when properly configured, tumbling is highly suitable for both precision and cosmetic parts. By selecting the appropriate media type, size, and compound, along with fine-tuning the machine speed and cycle duration, tumbling can produce smooth, uniform surfaces with minimal dimensional change. This makes it ideal for applications where aesthetics and performance are equally important—such as aerospace components that require tight tolerances, medical devices that demand a clean, burr-free surface, or consumer products that need a polished, appealing finish. At KingStar Mold, we customize the tumbling process to meet the specific quality requirements of each part, ensuring that precision is preserved while achieving the desired visual and tactile appearance.