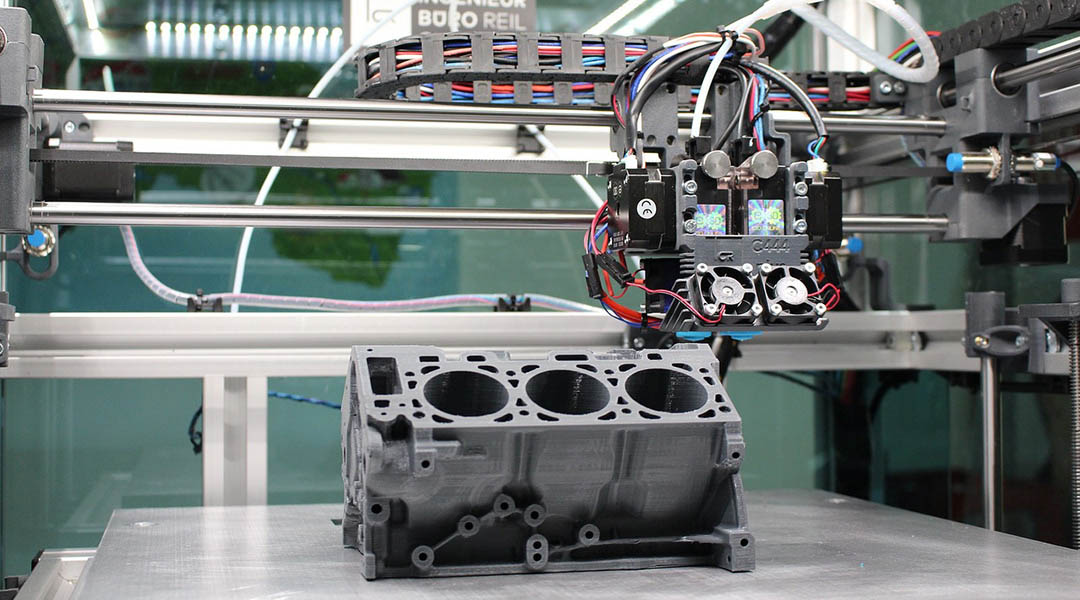
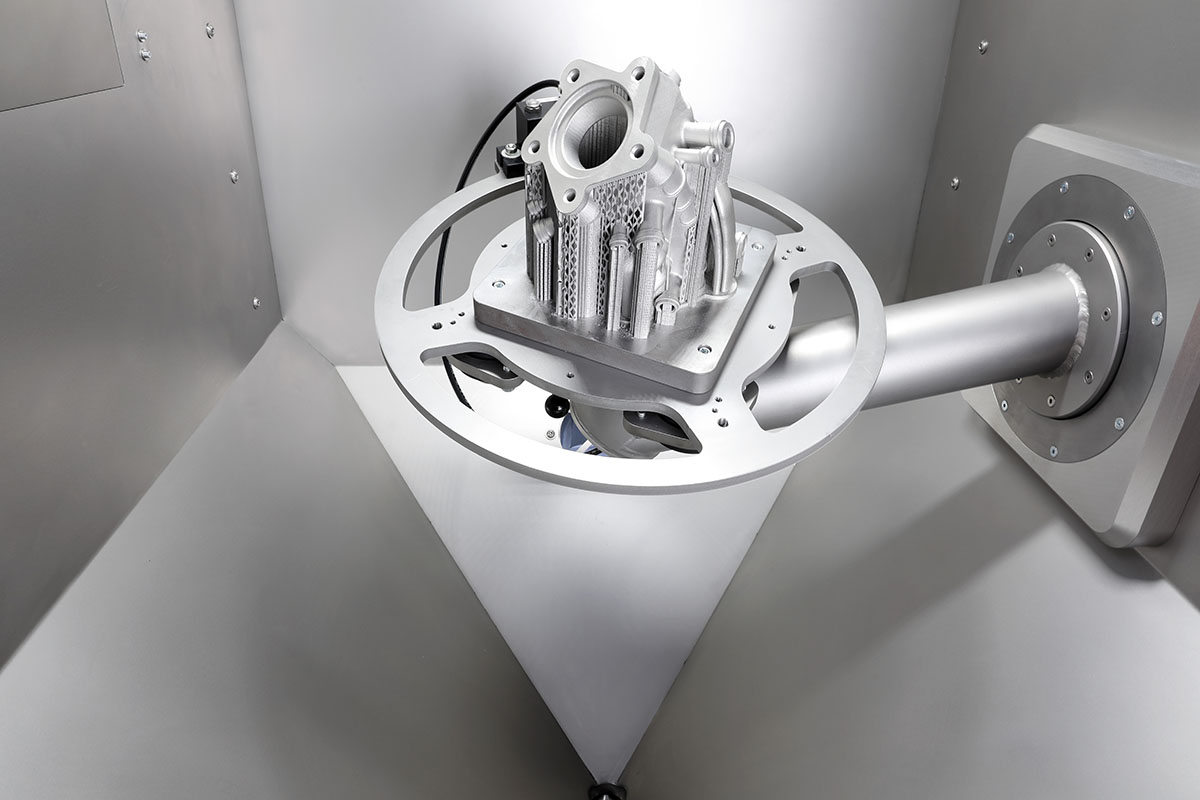
Design Guidelines for Titanium (Ti6Al4V) Parts
Normal Resolution | High Resolution | |
---|---|---|
Max Part Size | 13.0 in. x 9.6 in. x 9.6 in. / 330mm x 245mm x 245mm | 2.7 in. x 3.5 in. x 3.5 in. / 70mm x 88mm x 88mm |
Layer Thickness | 0.0012 in. / 30 microns | 0.00079 in. / 20 microns |
Minimum Feature Size | 0.015 in. / 0.381mm | 0.006 in. / 0.153mm |
Automotive
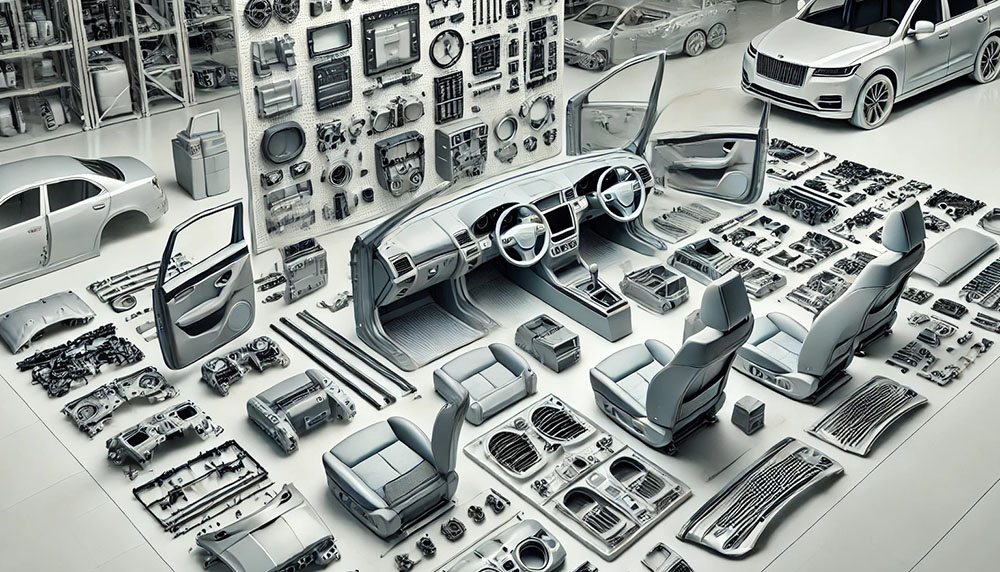
Aerospace
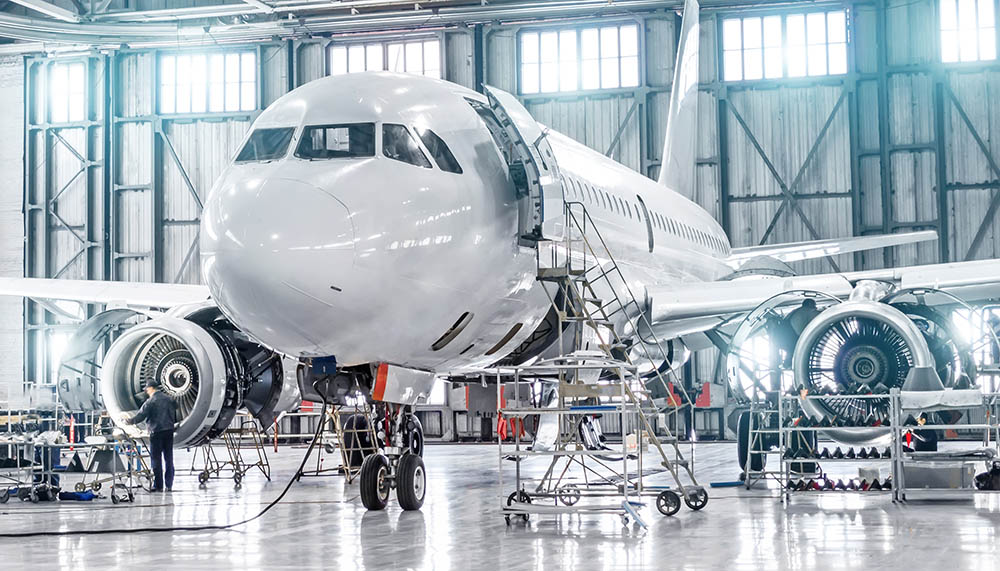
Medical

Industrial Equipment
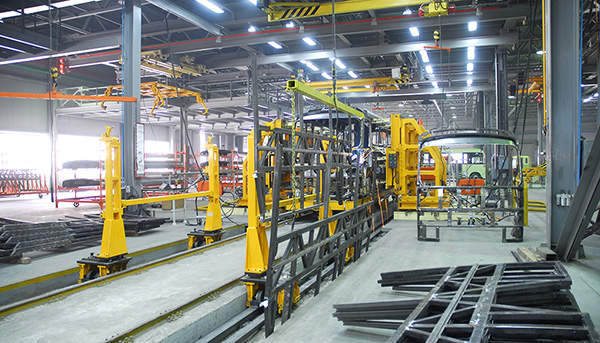
Properties of Titanium (Ti6Al4V)
Resolution | Condition | Ultimate Tensile Strength | Yield Stress | Elongation | Hardness |
---|---|---|---|---|---|
20 μm | Stress Relieved | 153 ksi / 1055 Mpa | 138 ksi / 951 Mpa | 15% | 35 HRC |
30 μm | Stress Relieved | 144 ksi / 993 Mpa | 124 ksi / 855 Mpa | 18% | 33 HRC |
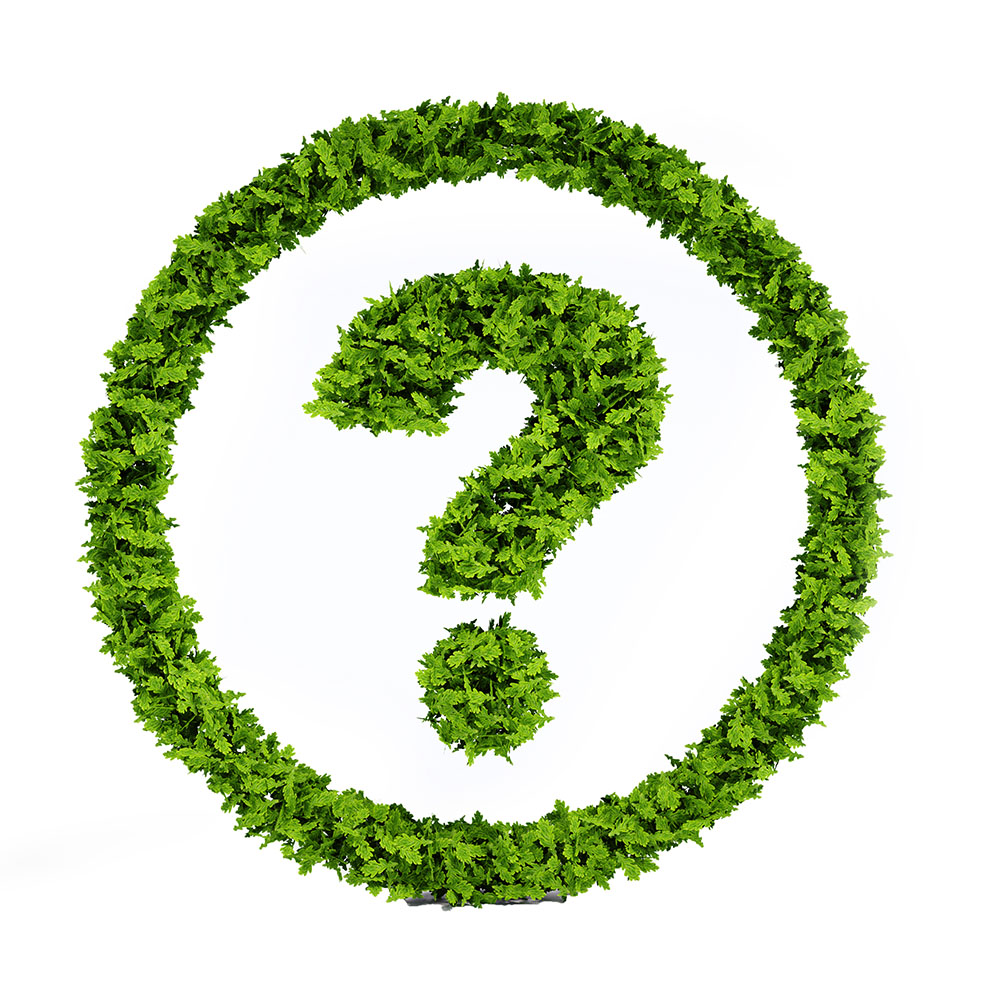
Yes, titanium parts undergo vacuum stress relief treatment to enhance mechanical properties and reduce internal stresses.
Yes, Ti6Al4V is biocompatible and widely used for medical implants, including orthopedic and dental applications.
Most titanium 3D printing applications use Ti6Al4V, a strong and lightweight alloy known for its high mechanical performance and resistance to extreme environments.
Titanium 3D printing offers high strength-to-weight ratio, excellent corrosion resistance, and biocompatibility, making it ideal for aerospace, medical, and industrial applications.
Yes, KingStar Mold offers post-processing services, including stress relief, machining, surface finishing, and quality inspection.
KingStar Mold ensures high precision in titanium 3D-printed parts with fine feature resolution and tight tolerances for demanding applications.
Titanium 3D printing is widely used in aerospace, automotive, medical, and high-performance industrial sectors.
Yes, KingStar Mold provides large-format titanium 3D printing with build sizes up to 31.5” x 15.7” x 19.7” (800mm x 400mm x 500mm).