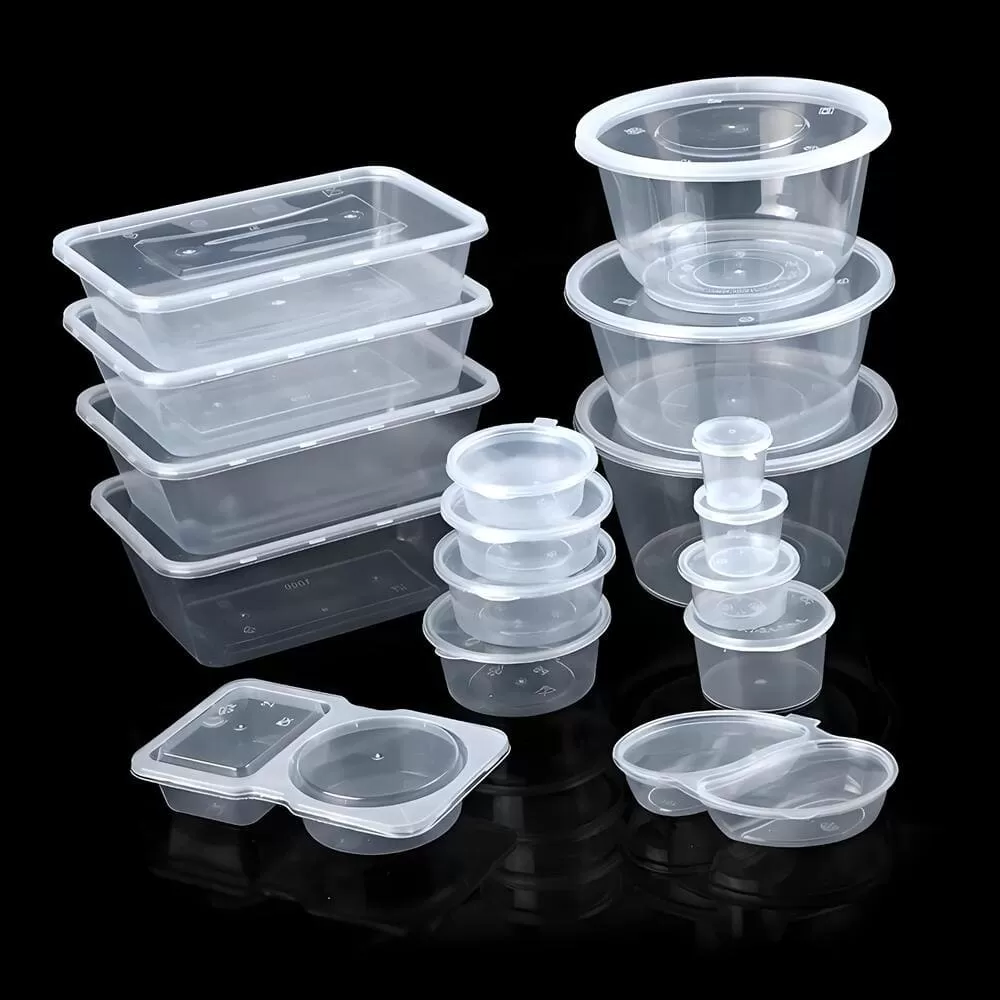
-
Resources for The Complete Guide to Thin Wall Injection Molding
What is thin wall injection molding?
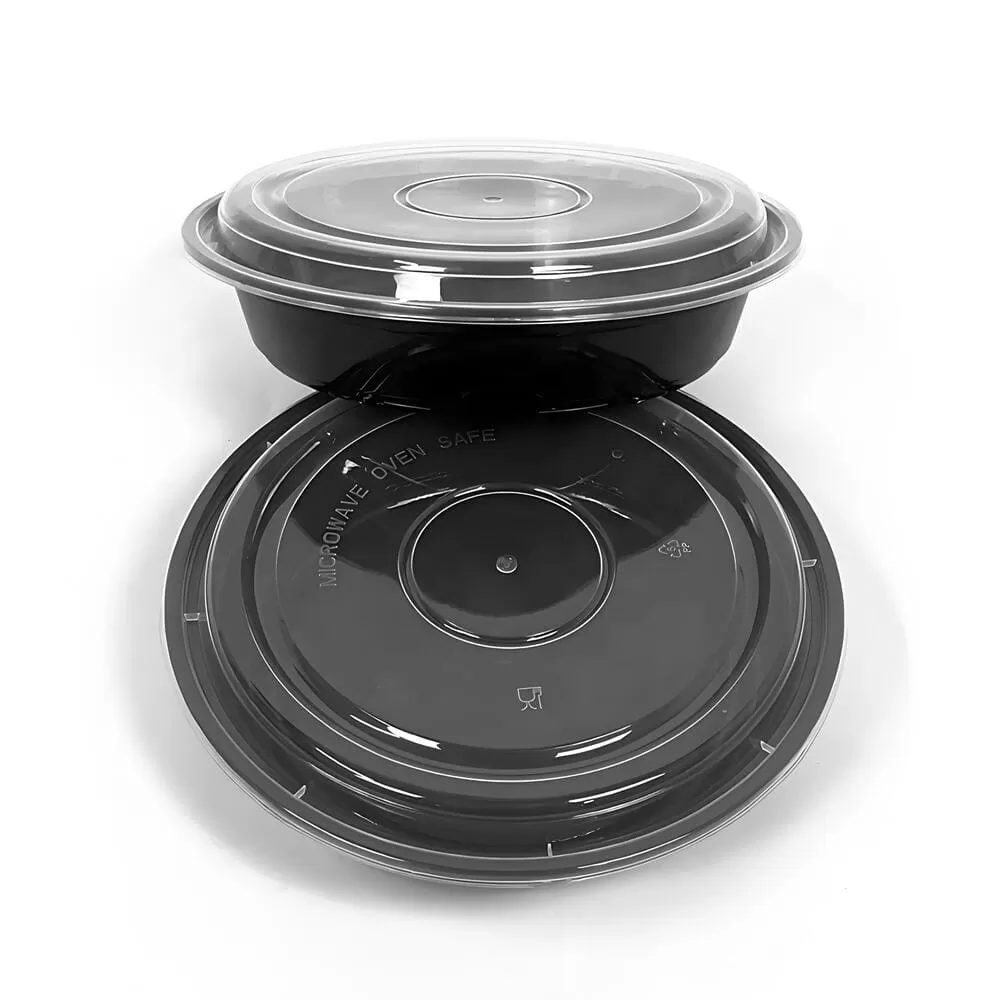
Thin-wall injection molding is a specialized injection molding process used to manufacture parts with thin walls.
This technology is often referred to as thin-wall plastic injection molding, and it can be defined in three ways:
- The molded product has a wall thickness of less than 1 mm, with a projected area of the plastic part exceeding 50 cm².
- The wall thickness of the molded product is below 1 mm (or 1.5 mm), or the ratio of thickness (t) to diameter (d) of disc-shaped plastic parts is under 0.05. This is considered thin-wall injection molding.
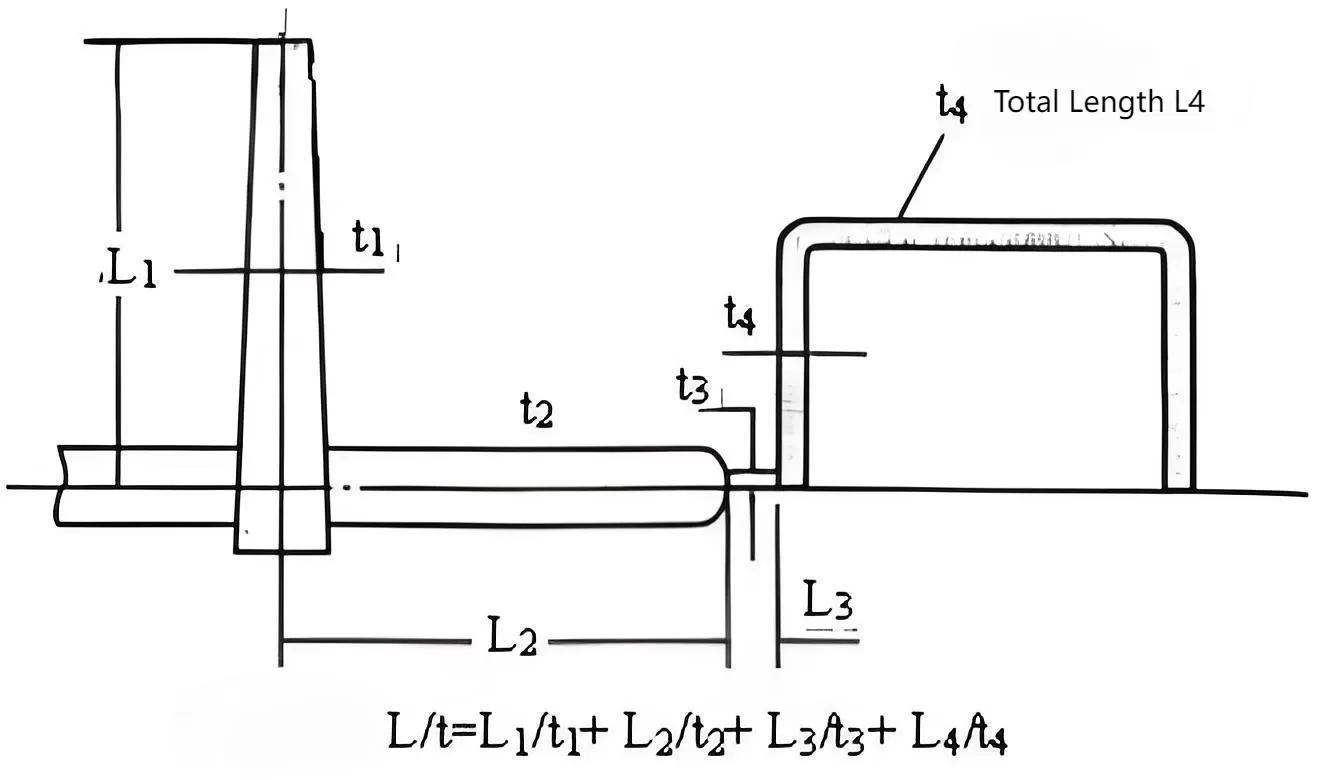
- The flow length (L) from the mold’s main channel to the furthest point of the finished product, divided by the wall thickness (t) of the product, is referred to as the flow length/wall thickness ratio. When this ratio exceeds 150 (L/t > 150), the process is categorized as thin-wall injection molding. If the thickness is not uniform, the ratio can be calculated in sections.
For example:
- For a disposable lunch box made from PP (with a viscosity factor of 1), the flow length is 135 mm and the wall thickness is 0.45 mm. The flow length/wall thickness ratio is 300 (135/0.45), which is greater than 150, qualifying it as thin-wall injection molding.
- For a mobile phone battery shell made from PC (with a viscosity factor of 2), the flow length is 38 mm and the wall thickness is 0.25 mm. The flow length/wall thickness ratio is 152 (38/0.25), and when multiplied by the viscosity factor (2), the ratio becomes 304, which is also greater than 150, thus also classified as thin-wall injection molding.
What is the principle of thin-wall injection molding?
The key principles of thin-wall injection molding include the following aspects:
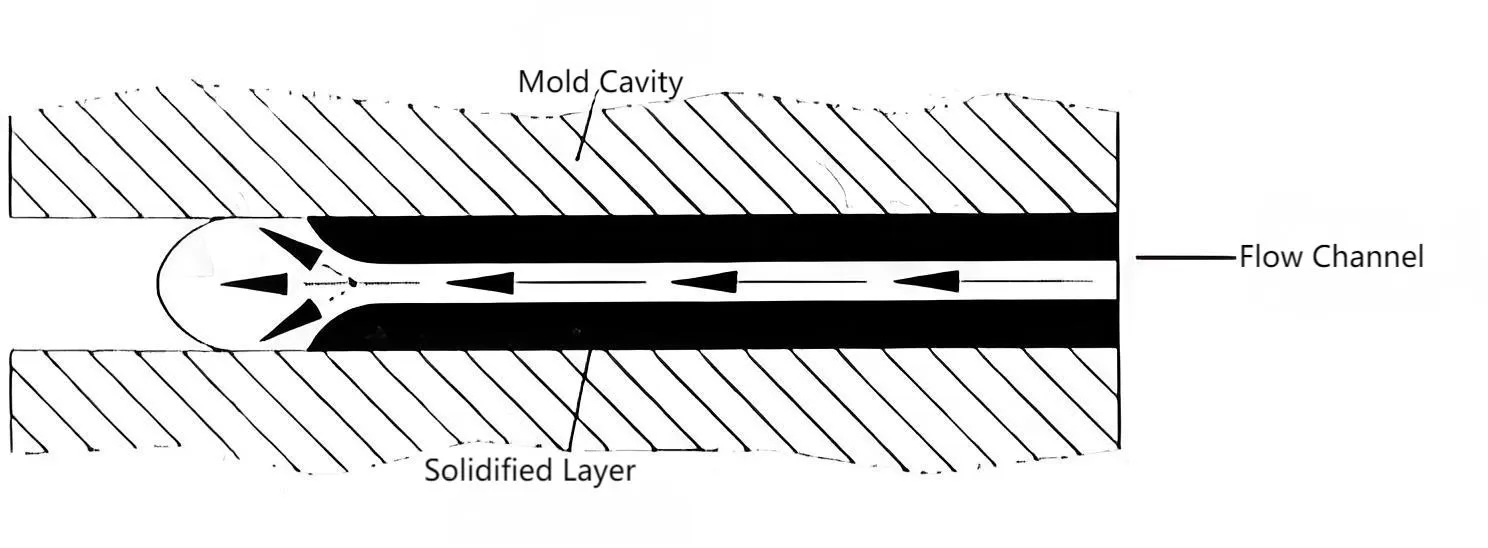
Injection Flow Process
Guide to Selecting Raw Materials for Thin-Wall Injection Molding
When selecting materials for thin-wall injection molding, key principles to consider include excellent fluidity, high impact resistance, superior thermal stability, low orientation, and excellent dimensional stability.
Commonly used materials for thin-wall injection molding include polypropylene (PP), polycarbonate (PC), acrylonitrile-butadiene-styrene (ABS), PC/ABS blends, and PA6, among others.
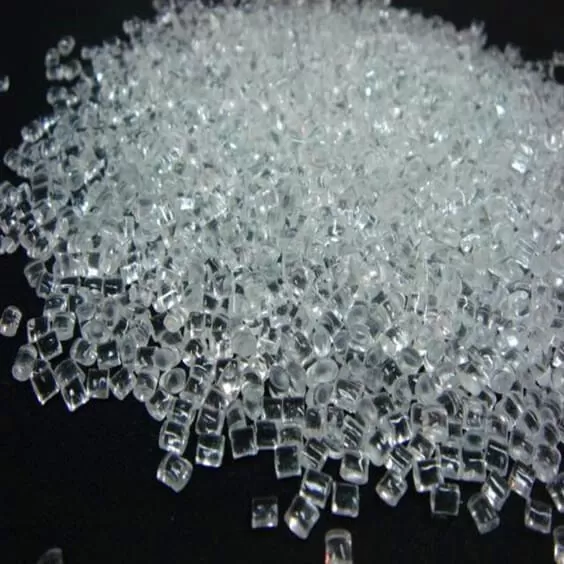
Excellent Dimensional Stability:
The raw materials used in thin-wall injection molding should offer excellent dimensional stability. This ensures that the molded parts experience minimal dimensional changes during both processing and usage, meeting the required precision standards.
Flowability:
Good flowability is essential in thin-wall injection molding to ensure that the molten material can fill the thin walls of the mold. Materials with high flowability ensure that thin-walled parts are completely filled during the injection process, preventing voids or incomplete filling. For example, PP plastics with a high melt index, such as Basell’s Moplen RP1086, are favored. PS/ABS blends are also commonly used for their combination of toughness and flowability, making them ideal for thin-wall applications.
High Impact Resistance:
Thin-walled plastic parts often need to withstand higher impact forces, so choosing materials with high impact resistance is crucial. This ensures that the parts can resist external impacts without breaking or getting damaged during regular use. As wall thickness decreases in thin-wall injection molding, materials with better physical properties are needed to maintain the strength and durability of the product.
What’s the reason of choosing thin-wall injection molding?
The cost of plastics typically represents a significant portion of the finished product cost, often ranging from 50% to 80%. By reducing wall thickness, this proportion can be lowered. As consumer electronic devices like mobile phones, digital cameras, and handheld computers continue to become smaller and lighter, the design of plastic parts is increasingly shifting towards thinner walls.
① Weight Reduction: Thin-wall injection molding enables the production of lightweight parts with reduced material usage, making it ideal for industries like aerospace, automotive, and medical, where weight is a critical factor.
② Cost Savings: By minimizing material usage, thin-wall injection molding helps lower production costs, particularly for high-volume production runs.
③ Increased Production Speed: Thin-wall injection machines are capable of producing parts faster than traditional molding machines, making them highly efficient for large-scale manufacturing.
④ Improved Part Consistency: Thin-wall injection molding ensures uniform part quality, minimizing shrinkage and ensuring consistency, which is crucial for applications requiring precise, reliable components.
What are the applications of thin-wall injection molding?
Thin-wall injection molding technology is widely used in various industries. Some common applications include:
① Food Packaging
Thin-wall injection molding is extensively used in food packaging, allowing the production of containers with excellent sealing and preservation properties, such as plastic bowls and boxes. The technology’s fast production speed and high efficiency make it suitable for large-scale production, meeting the food packaging industry’s demand for both production efficiency and high-quality products.
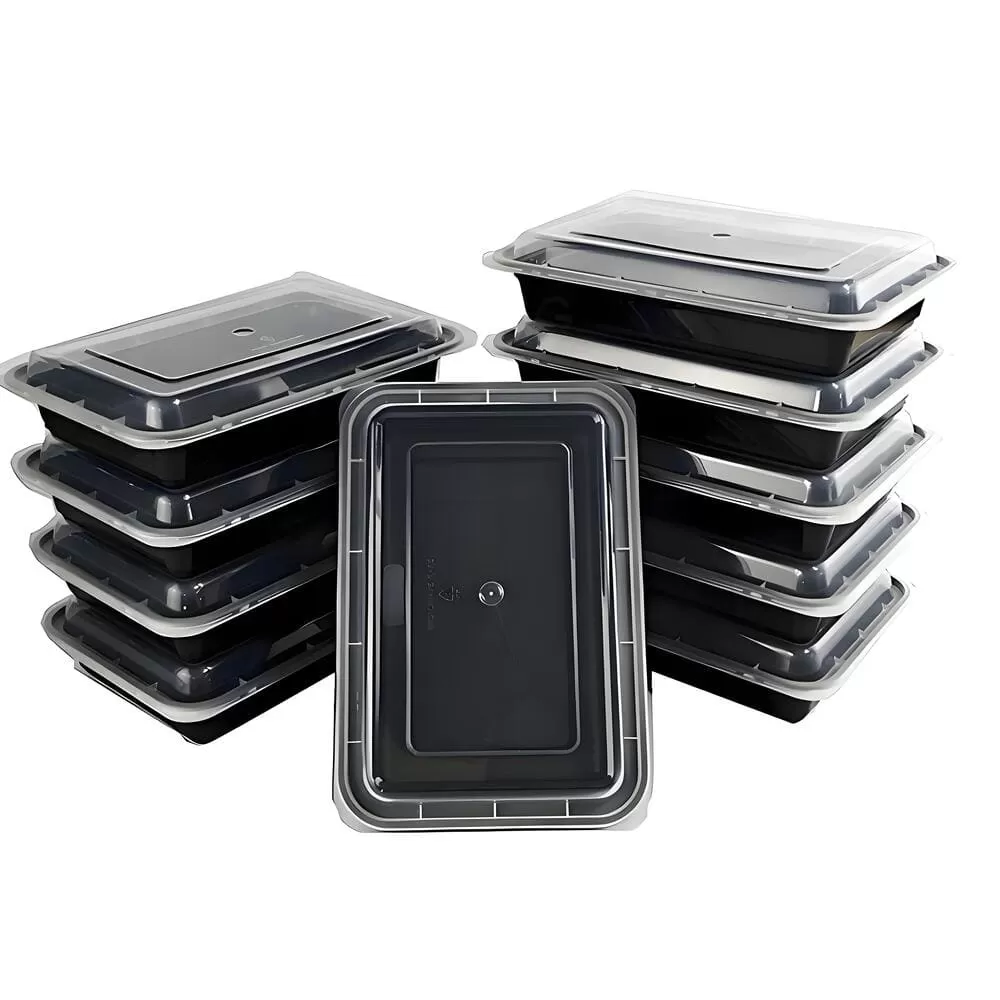