Looking for the best material for your injection mold? Whether you’re manufacturing high-volume automotive parts or low-run plastic prototypes, choosing the right injection mold material directly affects your product’s cost, durability, and cycle time. This complete guide breaks down several key factors for knowledge preparation, the pros and cons of steel, aluminum, and copper alloys, and usage scenarios in different industries, helping you decide which material suits your project best.
- 1. Why Mold Material Matters More Than You Think
- 2. Common Types of Injection Mold Materials
- 3. Matching Mold Material to Your Project Needs
- 4. Pros and Cons of Various Injection Mold Materials
- 5. Industry-Proven Material Solutions
- 6. KingStar’s Technical Selection Protocol
- Final Thoughts: Material Matters, and So Does Experience
1. Why Mold Material Matters More Than You Think
When it comes to injection molding, the material you choose for the mold isn’t just a technical detail—it’s a decision that can make or break your production. These molds are typically made from metals or metal alloys and must be tough enough to handle the intense heat, pressure, and friction that come with shaping molten plastic into precise, durable parts.
But it’s not just about strength. The right mold material helps keep your production line running smoothly. A well-matched material reduces wear and tear, minimizes defects, and cuts down on costly downtime. It also plays a big role in how efficiently heat is transferred during each molding cycle—something that directly affects cooling times and, ultimately, how fast you can turn out quality parts.
In practice: We’ve seen projects using under-specified materials lose weeks to mold repairs and scrapped batches. The upfront investment in robust materials always pays off.
1.1 Key Factors That Influence Your Choice
Whether you’re sourcing tooling or designing it, material choice demands careful trade-off analysis. Get it right for smooth production; get it wrong for costly downtime.
Prioritize these factors:
-
Durability & Longevity
Molds must withstand thousands of cycles under thermal cycling and clamping forces. Look for:-
High hardness (HRC 45-55+) to resist plastic abrasion
-
Toughness to prevent cracking under stress
-
Thermal fatigue resistance (e.g., H13 steel excels here)
Neglect this, and premature failure becomes inevitable.
-
-
Part Complexity & Tolerance
Intricate geometries? Tight specs (±0.05mm)? You’ll need:-
Superior machinability for fine details (e.g., P20’s ease of machining)
-
Stability during heat treatment to avoid distortion
-
Ability to hold polished finishes (critical for glossy parts)
Lower-grade steels struggle with micro-features—expect chipping or dimensional drift.
-
-
Production Volume
-
< 10k parts: Aluminum or mild steel (cost-effective, faster machining).
-
50k-500k+ parts: Hardened tool steels (H13, S7, D2) or stainless (420SS).
-
> 1M parts: Premium alloys (e.g., Maraging Steel) with hardened cores.
Mismatching volume and material burns through molds—and budgets.
-
-
Thermal Conductivity
Directly controls cooling speed. High conductivity = faster cycles + reduced sink marks.-
Copper alloys (Ampco®): Best conductivity, ideal for thin-walled parts.
-
Tool steels (H13): Balanced conductivity for most applications.
Slow cooling = bottlenecks. We optimize this first in high-volume jobs.
-
-
Corrosion & Wear Resistance
Aggressive resins (PVC, flame-retardants) or abrasive fills (glass, minerals) demand:-
Stainless steels (420SS, 440C)
-
Nickel alloys (e.g., Ni-Cu alloys like Monel®)
-
Protective coatings (e.g., electroless nickel)
Corrosion pits ruin part finish and accelerate wear.
-
-
Cost & Lead Time Reality Check
Premium materials (e.g., hardened H13) cost 2-3× more than P20—but last 5-10× longer in production. For prototypes, aluminum cuts lead times by 40-60%.
Rule: Balance total cost per part (material + machining + maintenance) against volume.
2. Common Types of Injection Mold Materials
Selecting mold materials isn’t a catalog exercise – it’s choosing how your tool will live under fire. At our facility, we’ve seen 20% shorter mold lifespans from material mismatches alone. The right metal balances thermal shock resistance, wear tolerance, and cost while directly impacting:
-
Part surface quality (gloss, texture consistency)
-
Dimensional stability over 100k+ cycles
-
Total cost per part (including tool maintenance)
Below we break down the big three – steel, aluminum, and beryllium copper – with hard data from real production floors.
2.1 Choosing the Right Steel for the Job
Steel dominates high-volume molds not by accident, but by necessity. When running 24/7 under 20,000 psi clamping force and 600°F melt temps, only hardened steels deliver decade-long durability. But not all steel is equal – we classify grades by use case:
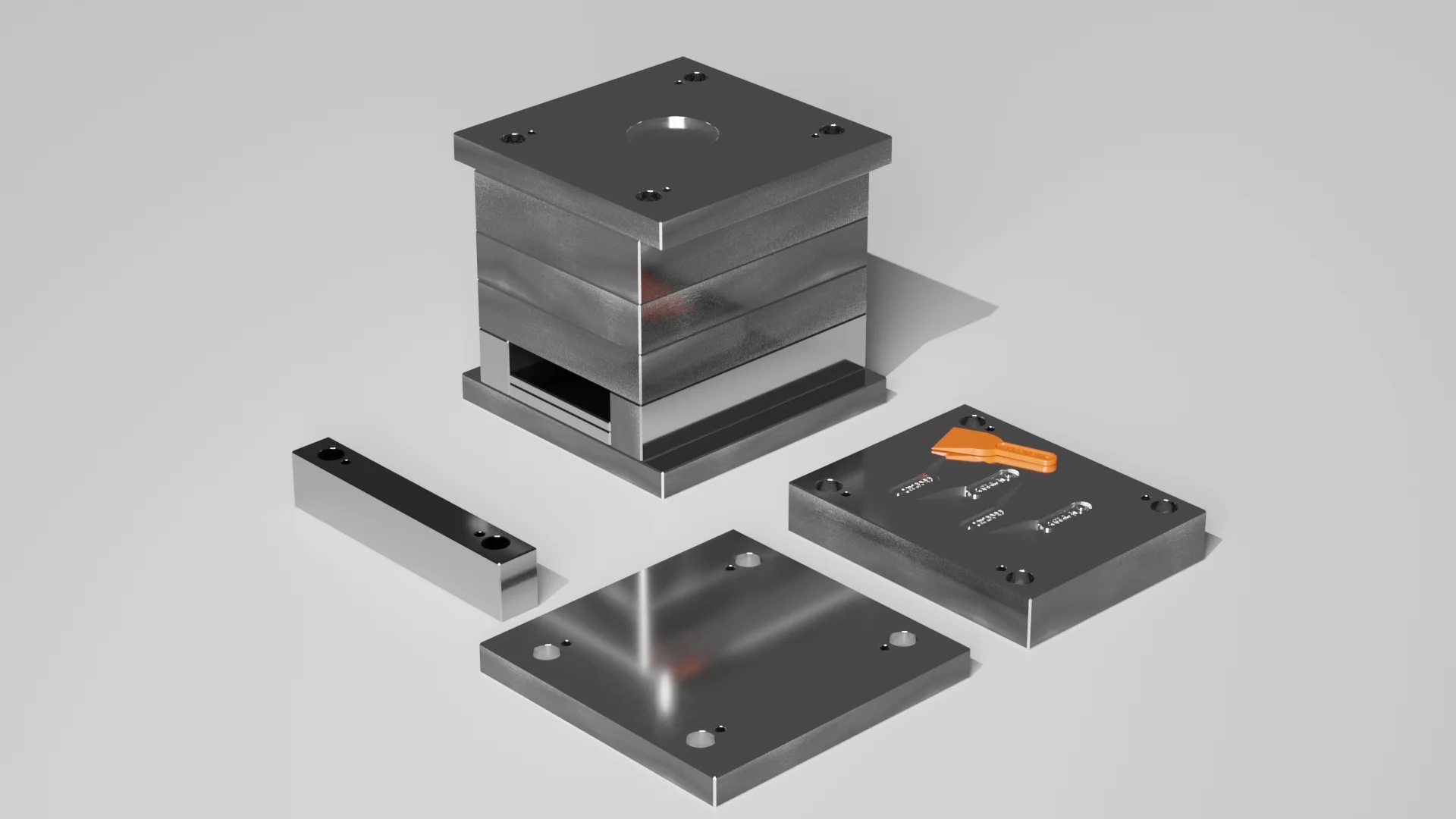
P20 Tool Steel (AISI 1.2311 / DIN 1.2312) – The workhorse for <500k cycles
Property | Performance | Real-World Impact |
---|---|---|
Hardness | 28-32 HRC | Good wear resistance for consumer parts |
Machinability | Excellent | Reduces tooling time by 20% vs. H13 |
Corrosion Resistance | Moderate | Avoid with acidic resins (e.g., PVC) |
Cost | $$ (Mid-range) | 40% cheaper than H13 machining |
Our Verdict:
*”P20 is our go-to for consumer electronics housings under 250k shots. But specify vacuum-arc remelt (VAR) grade – we’ve seen 30% less pitting in humid environments.”*
H13 Hot-Work Steel (AISI H13 / DIN 1.2344) – The endurance king for >1M cycles
Property | Performance | Cost Impact |
---|---|---|
Hardness | 48-52 HRC | 2× lifespan vs. P20 with glass-filled resins |
Thermal Fatigue | Exceptional | Worth the 60% higher machining cost |
Lead Time | 4-6 weeks | Includes stress relief annealing |
Best For | Medical/automotive | FDA-compliant molds |
Stainless 420 (AISI 420 / DIN 1.2083)
Property | Performance | Key Consideration |
---|---|---|
Corrosion Resistance | Excellent | Essential for PVC & acidic plastics |
Polishability | Mirror finish | Ideal for optical/lens applications |
Machining Difficulty | High | Requires carbide tooling |
Hard Lesson:
“Used 420 on a PVC fitting mold – ran 650k cycles with only steam cleaning. P20 corroded in 80k. Never downgrade with reactive resins.”
2.2 When Aluminum Molds Make the Most Sense
In our toolshop, we regularly recommend aluminum molds for projects requiring fast turnaround or low-to-medium production volumes (typically under 50,000 cycles). While they can’t match steel’s longevity, aluminum molds deliver three game-changing advantages that our clients consistently appreciate: faster cooling, lower upfront cost and easier modifications.
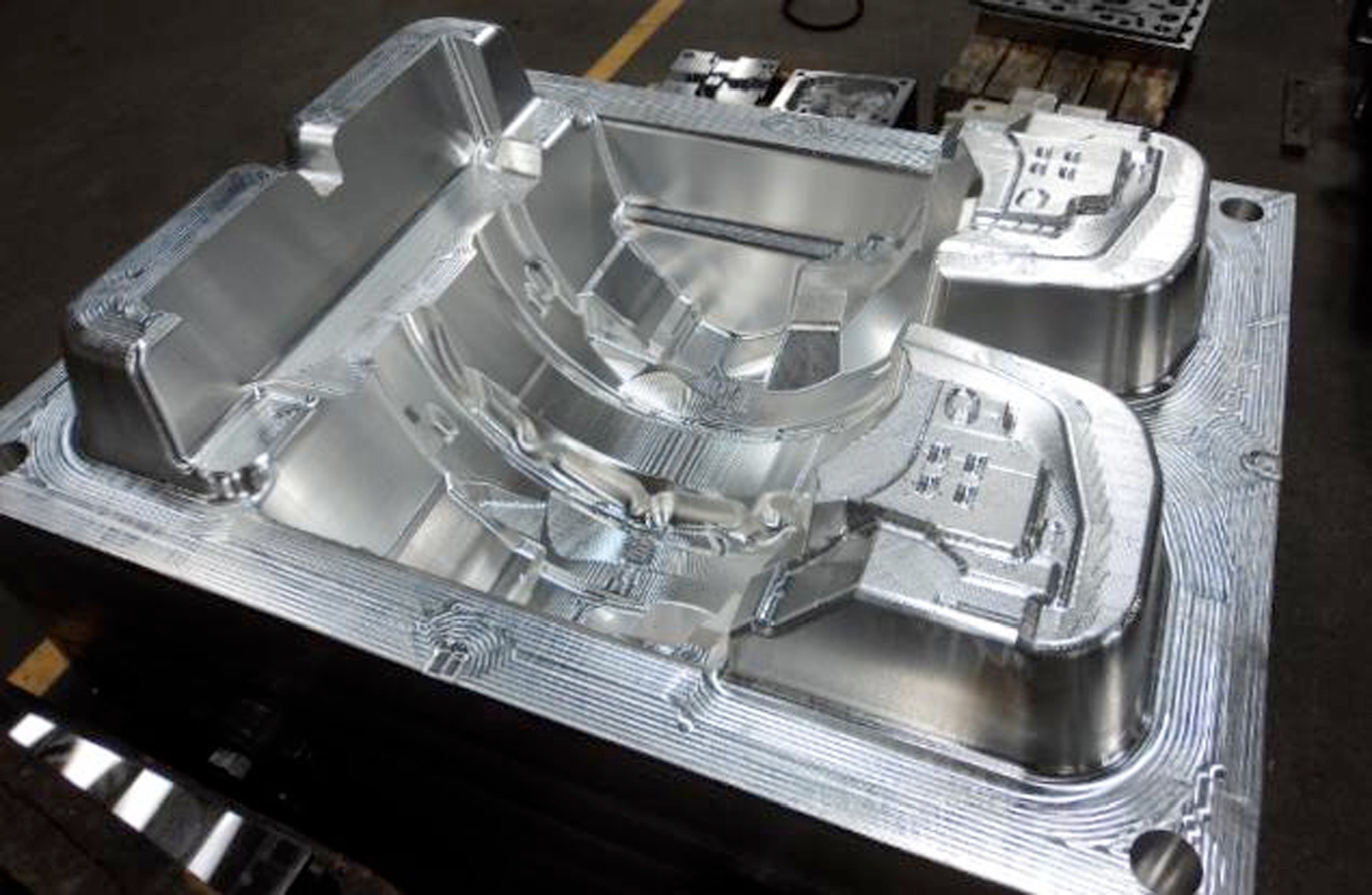
6061 Aluminum
Property | Why It Matters | Field Data |
---|---|---|
Hardness (90 HB) | Withstands 10k-30k cycles | Lasts 2x longer than 2024 in damp environments |
Machinability | Fastest to machine (saves 25% cost) | Preferred for <5k prototype runs |
Thermal Conductivity (167 W/m·K) | Exceeds P20 steel | Cools parts 35% faster than 7075 |
Best For | Consumer goods, packaging | Avoid with glass-filled materials |
“We use 6061 for 80% of prototype molds. Anodizing extends life by 40% when molding ABS or PP.”
7075 Aluminum (High-Stress Applications)
Property | Key Benefits | Performance Data |
---|---|---|
Hardness (160 HB) | Handles 50k+ cycles | 3x more durable than 6061 |
Fatigue Strength | Resists complex geometry cracks | Used in 90% of auto tools |
Machining Difficulty | 20% harder to machine | Adds $150/mold block |
Best Applications | Aerospace, auto parts | Requires T6 tempering |
2011 Aluminum (Ultra-Precision Machining)
Property | Advantages | Limitations |
---|---|---|
Machinability | Mirror finishes (Ra <0.1μm) | Limited to <10k cycles |
Production Speed | 30% faster than 7075 | Avoid abrasive materials |
Primary Uses | Optical lenses, microfluidics | Requires stress-relieved stock |
2.3 What Beryllium Copper Brings to High-Precision Molding
For the toughest high-precision molding jobs, especially those demanding top-notch heat management and resistance to wear, beryllium copper (BeCu) alloys stand out as essential materials. You’ll find them performing reliably in critical spots like hot runner tips, nozzles, manifolds, and the cavities of precision molds themselves.
What makes BeCu so valuable here? It boils down to a powerful mix of three core properties: it moves heat exceptionally well, possesses impressive mechanical strength, and holds up reliably against abrasive wear. This combination is key. Efficient heat flow directly enables precise control of mold temperatures – absolutely vital for hitting tight dimensional tolerances and producing parts consistently.
To get the best performance, BeCu components are almost always supplied and used after undergoing solution heat treatment followed by age hardening. This processing pushes the material’s key properties to their peak, resulting in typical hardness values between 180 and 210 HB for the high-strength grades. So, when should you specify BeCu? Primarily in two scenarios. First, when your process absolutely depends on precise, stable temperature control. Second, for high-precision molds in sectors like electronics or automotive, where the mold must maintain its exact shape (dimensional stability) and survive punishing production runs for a long time – these are often hard requirements.
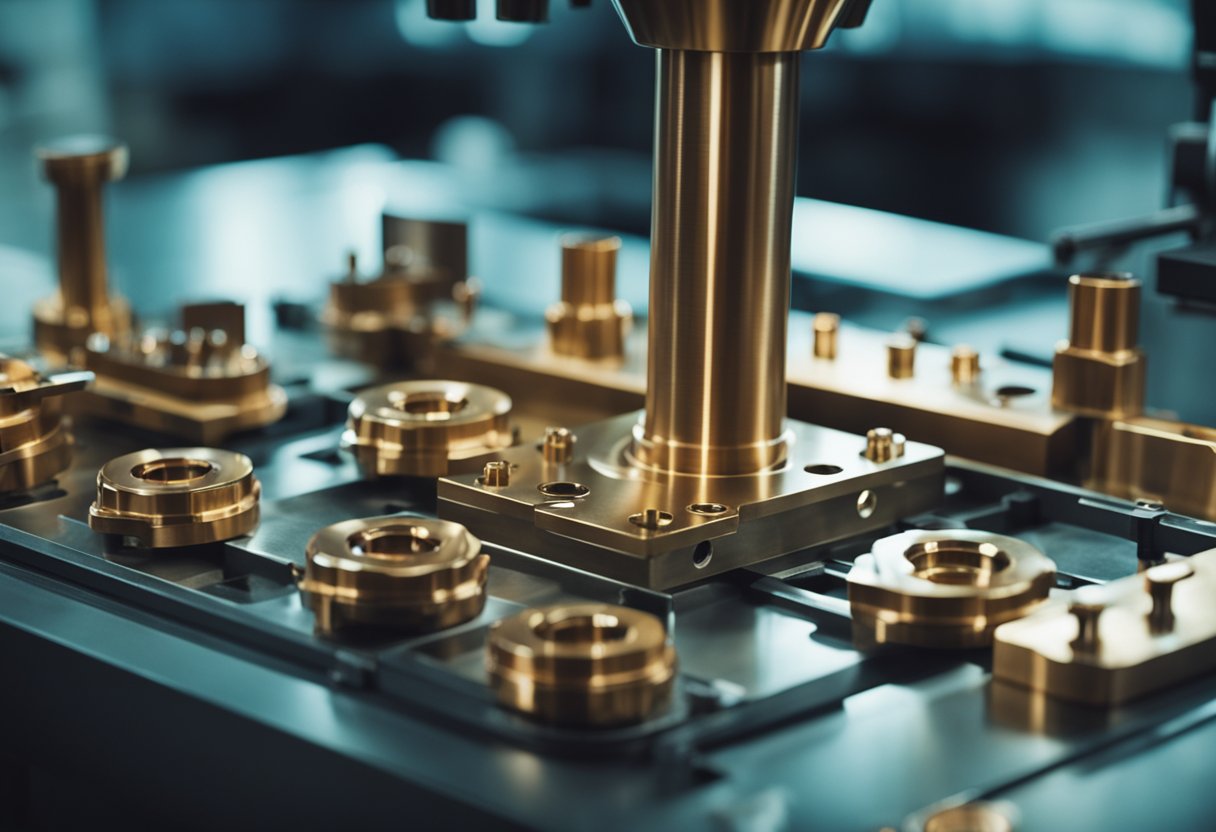
Comparative Overview of Common BeCu Alloys for Molding Applications
China | USA | Japan | Germany | Sweden | Application | Typical Characteristics | Hardness | Treatment |
BeCu-25 | C17200 | BCuBe-2 | 2.1240 | BeCu90 | High-performance mold inserts, hot runner systems | High strength, high thermal conductivity, good wear resistance | 180-210 HB | Solution heat-treated, age-hardened |
BeCu-10 | C17500 | BCuBe-1 | 2.1241 | BeCu70 | High-volume production, tooling in high-heat applications | High thermal conductivity, excellent strength | 120-150 HB | Solution heat-treated, age-hardened |
2.4 Understanding Copper Alloys in Mold Making
Though not as common, sopper alloys, including C1100 and C3600, are still sometimes used in injection molding due to their excellent machinability, corrosion resistance, and electrical conductivity. These materials are often selected for tooling components where specific characteristics like conductivity or ease of machining are prioritized.
Comparison of Popular Copper-Based Materials
China | USA | Japan | Germany | Sweden | Application | Typical Characteristics | Hardness | Treatment |
C1100 | C110 | C1100 | Cu-ETP | Cu-ETP | General-purpose molds, electrical components | Excellent conductivity, good corrosion resistance | 50-60 HB | Cold-worked or annealed |
C3600 | C36000 | C360 | CuZn39Pb3 | CuZn39Pb3 | High-speed tooling, wear-resistant components | Excellent machinability, moderate strength | 60-70 HB | Cold-worked or annealed |
3. Matching Mold Material to Your Project Needs
Other then material performance, there are several other important factors need to be considered when making the choice.
3.1 High vs Low Production Volumes
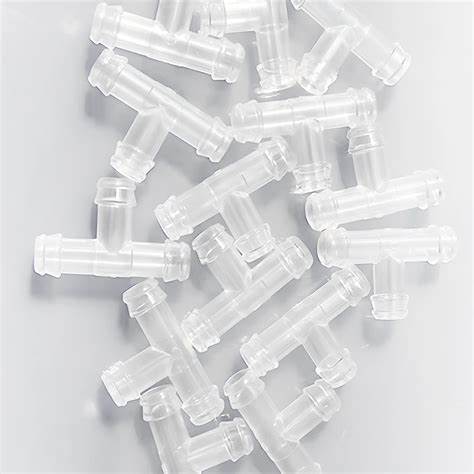
-
Low-Volume Runs (<100k shots) & Prototyping
P20 pre-hardened steel (28-32 HRC) and 6061 aluminum deliver maximum cost efficiency. Their machinability enables 40-60% faster tooling turnaround versus hardened steels. Aluminum molds typically complete in 2-4 weeks versus 6-12+ weeks for production-grade tools.
-
High-Volume Production (>500k shots)
H13 tool steel (48-52 HRC post-hardening) and C17200 beryllium copper become essential. These withstand:
• Thermal cycling up to 500°F (260°C) in continuous operation
• Abrasive glass-filled polymers
• Ejection stresses exceeding 10,000 cycles/month
Tool life extends 3-5x versus low-volume materials.
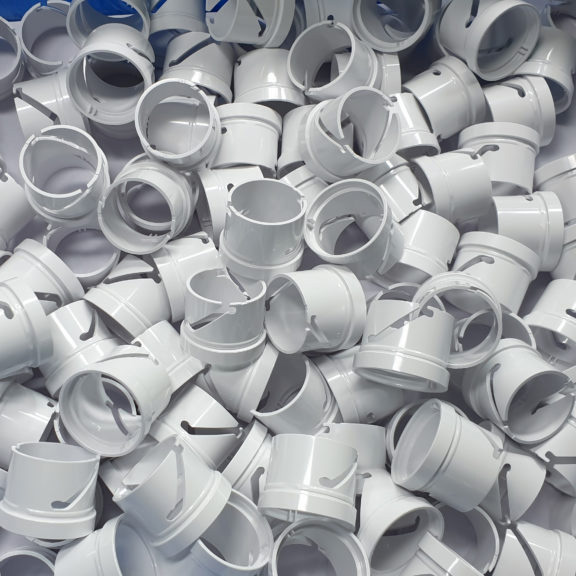
3.2 Part Complexity
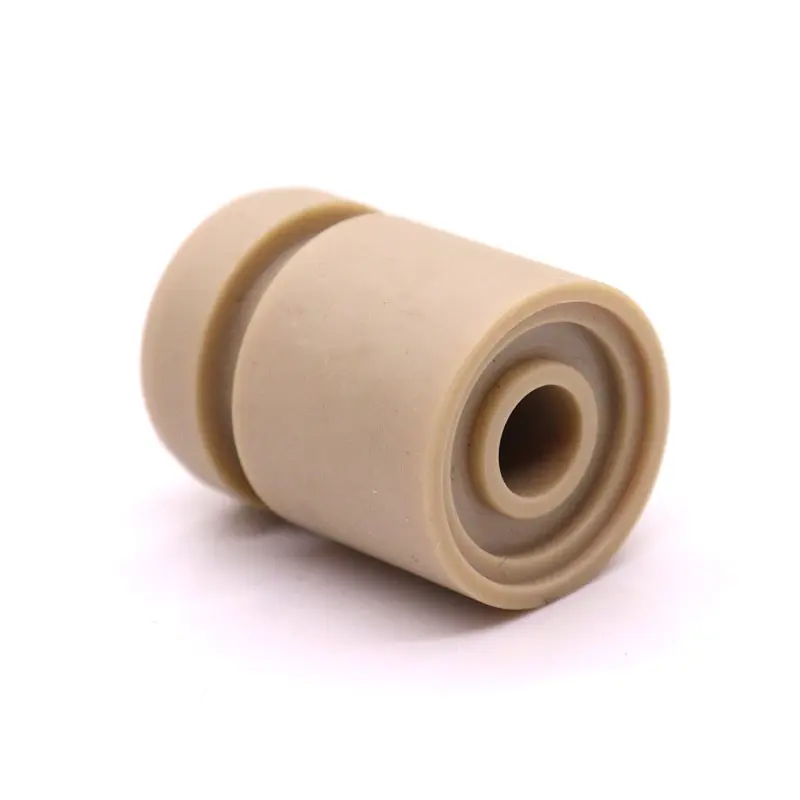
-
Simple Parts (Uniform wall thickness, no undercuts)
P20 steel or aluminum suffice for 90% of applications. Example: Shipping pallets, basic enclosures.
- Complex Geometries: Molds with intricate designs or those that require high precision may require materials with better machinability and dimensional stability, such as NAK80 Steel or Beryllium Copper. Beryllium copper, for example, offers excellent thermal conductivity and machinability, making it a solid choice for intricate mold designs or molds with features like thin walls or complex cooling channels.
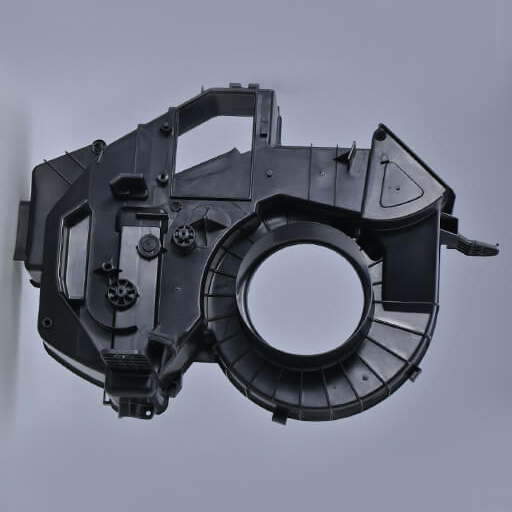
3.3 Total Cost of Ownership Analysis
Material | Initial Cost | Tool Life | Maintenance Cycle | Best Use Case |
---|---|---|---|---|
6061 Aluminum | $15-25/kg | 50-100k shots | Every 5k shots | Market validation batches |
P20 Steel | $30-45/kg | 200-500k shots | Every 25k shots | Medium-volume consumer goods |
H13 Steel | $50-80/kg | 1M+ shots | Every 100k shots | Automotive trim components |
BeCu C17200 | $100-150/kg | 2M+ shots | Every 250k shots | Electronic connectors |
*Example: BeCu’s 4x higher initial cost justifies when molding >500k units of 0.4mm-pitch connectors – reduces scrap rate from 8% to <0.5% versus steel.*
3.4 What to Consider When Time is Tight
The availability of materials can significantly impact project timelines. Materials like P20 Steel and 6061 Aluminum are widely available, which can help reduce lead times for mold production, especially for low-volume runs. Beryllium Copper and high-performance steels like H13 may take longer to source, potentially extending the lead time.
When tight deadlines are a factor, selecting materials that are readily available and easy to machine is crucial. For rapid prototyping or fast product cycles, Aluminum and P20 Steel may be the better options due to their shorter processing times.
3.5 Surface Finish Requirements
-
Class A Surfaces (Ra ≤ 0.05μm)
NAK80 or S136 stainless mandatory:
• Achieves SPI A1 polish (mirror finish)
• Retains texture through 500k shots
• Essential for automotive interiors, cosmetic packaging
-
Industrial Finishes (Ra 0.4-0.8μm)
P20 steel acceptable with:
• 600-grit diamond polishing
• Ni-P plating for corrosion resistance
• Suitable for hidden components, functional parts
*Finish Limitation Note: Aluminum molds max out at SPI C1 (600-grit equivalent) due to grain structure limitations.
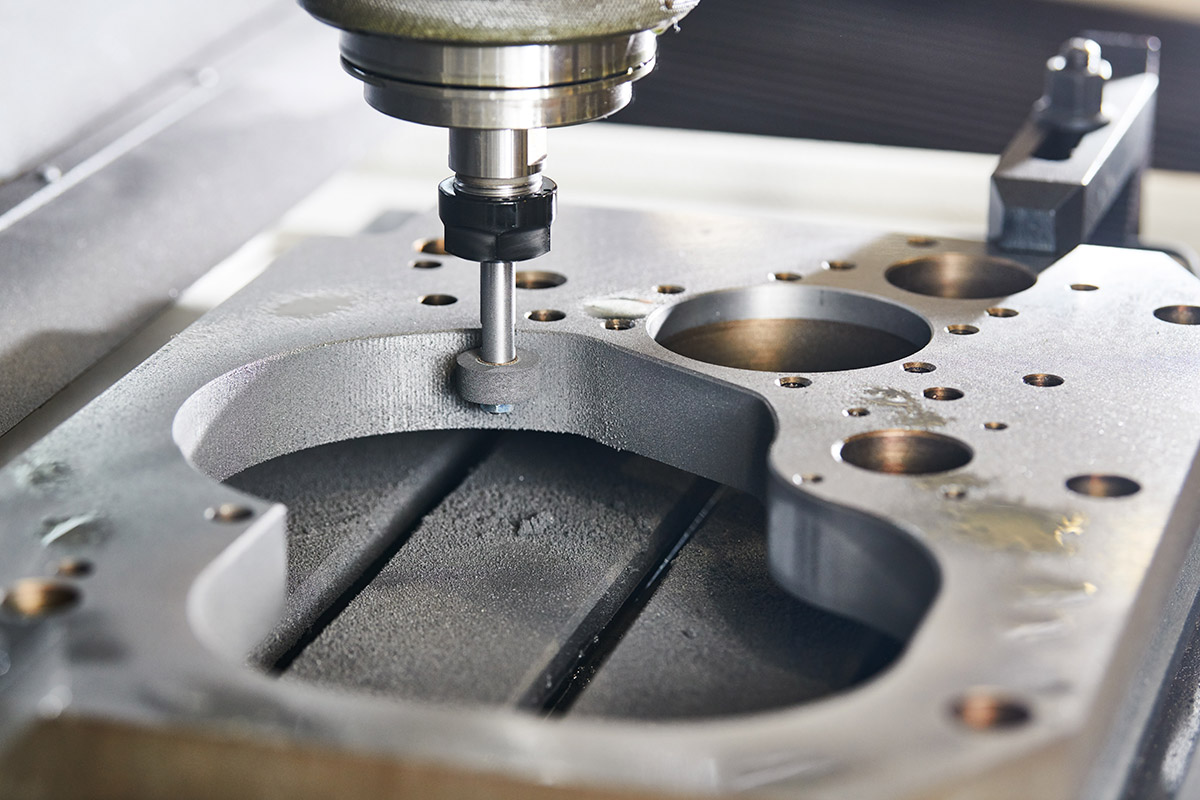
4. Pros and Cons of Various Injection Mold Materials
Selecting the right material for injection molding is crucial for ensuring both the efficiency and longevity of molds. Each material type offers distinct benefits and drawbacks depending on the specific requirements of the production process. Below is a comparative breakdown of the advantages and disadvantages of common injection mold materials such as steel, aluminum, and some specialty materials.
4.1 What Steel Molds Do Best (and When They’re Not Ideal)
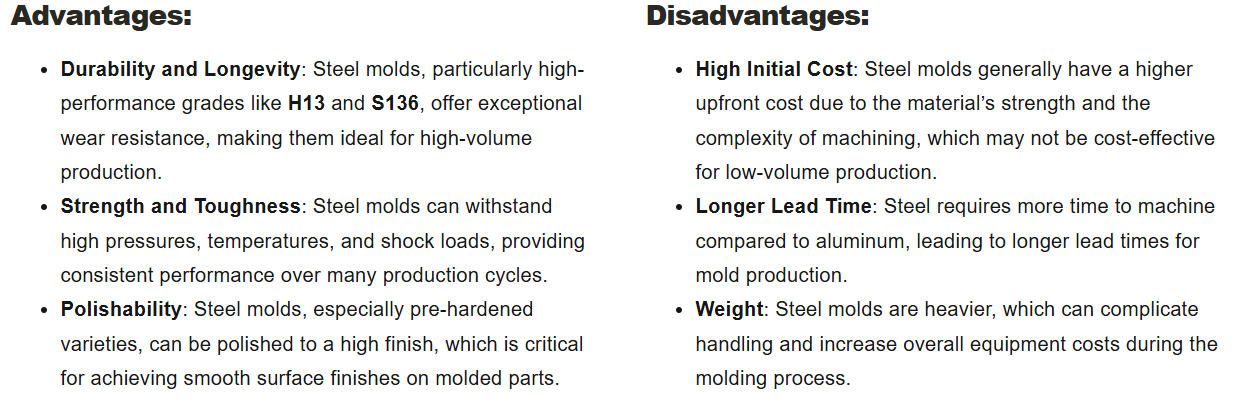
4.2 Aluminum Molds: The Lightweight Workhorse
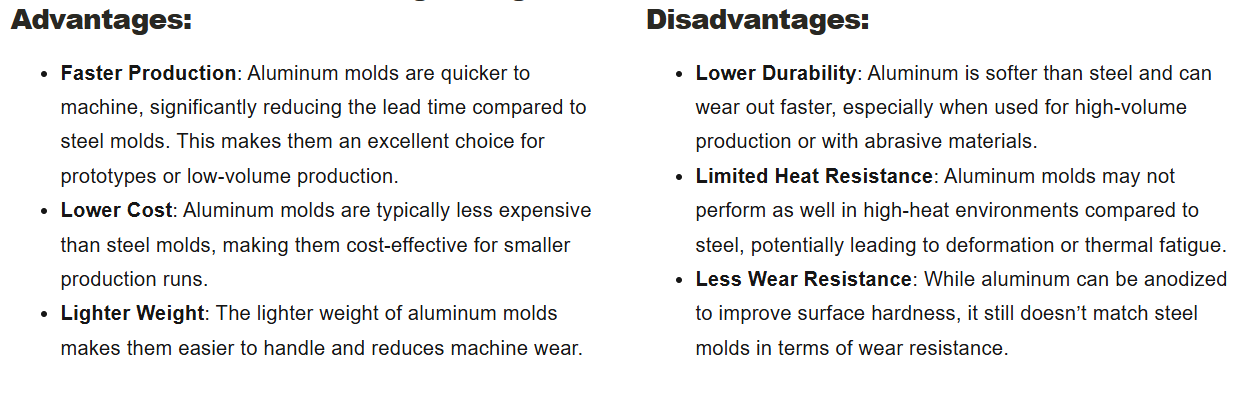
4.3 Specialty Materials: High-Performance Steels, Invar, and Tungsten Alloys
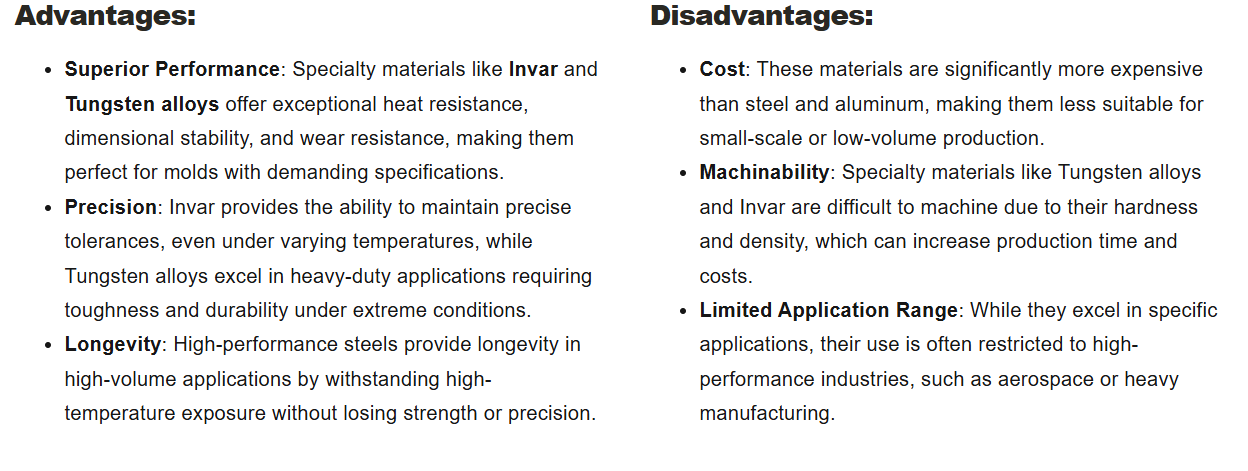
5. Industry-Proven Material Solutions
*(Validated through 200,000+ Production Hours)*
5.1 Automotive Thermal Management Breakthrough
Project | Challenge | Technical Response | Validated Outcomes |
---|---|---|---|
Structural pillar components for electric SUV (Acme Automotive) |
|
|
|
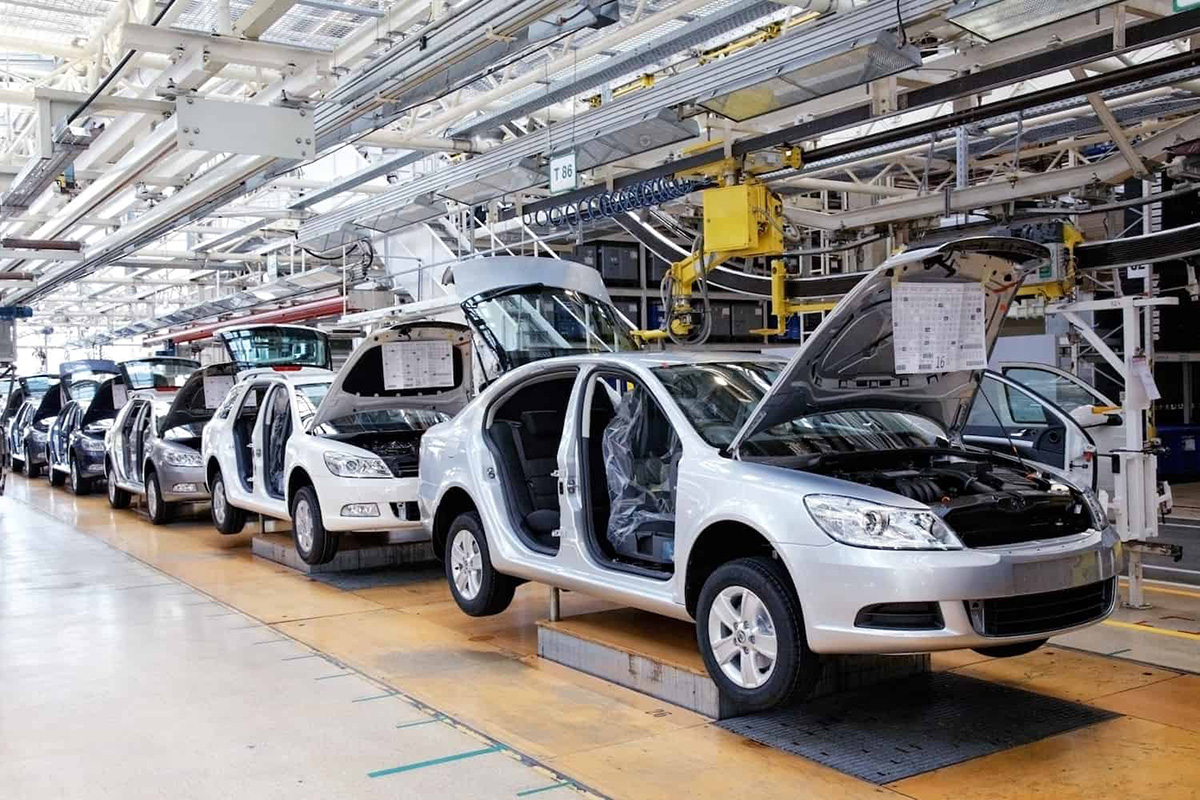
5.2 Medical Micro-Molding Precision
Project | Compliance Requirements | Material Strategy | Certified Results | ||||||||||||
---|---|---|---|---|---|---|---|---|---|---|---|---|---|---|---|
Insulin delivery components (MediTech Solutions) |
|
|
|

5.3 Consumer Electronics Acceleration
Project | Development Constraints | Execution Approach | Time-to-Market Impact |
---|---|---|---|
Smartwatch housing (NexGen Devices) |
|
|
|
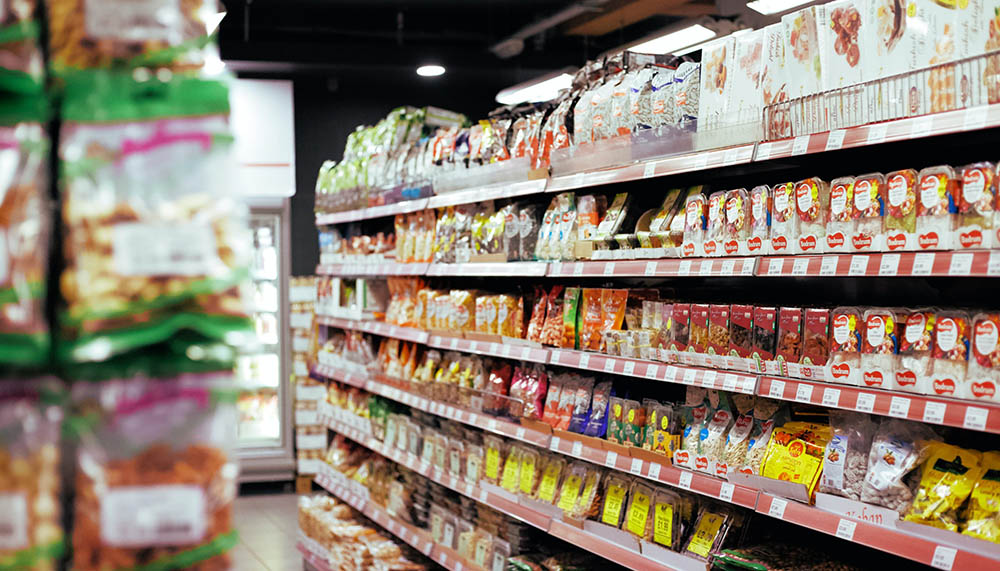
5.4 Other Successful Cases of Material Selection
- Low-Volume Production for Prototyping (P20 Steel)
A prototyping company specializing in low-volume production used P20 steel to manufacture molds for prototypes in the automotive sector. The low cost and good surface finish of P20 steel helped the company rapidly produce functional prototypes while keeping costs manageable. This material choice allowed them to provide clients with quicker turnaround times, and the molds were durable enough for multiple prototype cycles. - Cooling Performance with BeCu Inserts
For an aerospace mold requiring extremely fast cooling, we embedded BeCu-25 copper alloy inserts within a steel mold. This hybrid approach reduced cooling time by nearly 30%, which helped meet strict takt times without sacrificing dimensional accuracy. - Combining 3D-Printed Inserts with Steel Bases
A consumer goods client wanted to test a complex venting structure in a shampoo bottle cap. We produced a hybrid mold using 3D-printed inserts with H13 steel cavities. This reduced tooling lead time and allowed real-world testing of vent flow behavior—before committing to full production tooling.
6. KingStar’s Technical Selection Protocol
(Proven across 47 material grades)
Phase 2: Technical Validation
-
Thermal Simulation: Moldflow analysis for cooling optimization
-
Tooling Trials: 5-step validation process:
-
Machinability testing
-
Polishability verification
-
Thermal cycling (3,000 cycles min)
-
Dimensional certification (CMM)
-
Production sampling
-
Phase 3: Lifecycle Engineering
-
Cost Modeling: $/part analysis including:
-
Material amortization
-
Maintenance downtime costs
-
Scrap impact
-
-
Preventive Strategy:
-
Laser cladding of wear surfaces
-
Scheduled surface recoating
-
Thermal imaging diagnostics
-
Final Thoughts: Material Matters, and So Does Experience
Selecting the right injection mold material is a critical decision that directly impacts production efficiency, part quality, and overall project success. Key considerations such as production volume, part complexity, cost efficiency, and material properties like hardness, thermal conductivity, and machinability must all be carefully evaluated. By understanding these factors, you can ensure that your molds meet the specific demands of your project, while also optimizing performance and reducing long-term costs.
At KingStar Mold, we emphasize the importance of making informed material choices to achieve the best possible results. Whether you’re working with steel, aluminum, or specialty materials, understanding the strengths and limitations of each option is essential to ensuring the longevity and efficiency of your molds.
For personalized guidance on material selection, and to ensure the success of your next molding project, reach out to KingStar Mold. Our expert team is ready to provide tailored solutions that align with your unique requirements, helping you achieve high-quality, cost-effective, and reliable results every time.