Sheet Metal Materials
- Lightweight yet strong for structural reliability
- Corrosion-resistant options for long-term performance
- Versatile selection for diverse fabrication needs
Aluminum 5052 is a highly versatile alloy commonly used for sheet metal components. Its exceptional resistance to corrosion makes it well-suited for applications in demanding environments. With excellent formability and weldability, this alloy allows for complex shapes to be efficiently fabricated from flat sheets. Known for its strength, lightweight properties, and smooth finish, 5052 aluminum is a preferred material across various industries.
Tensile Strength | Elongation | Hardness | Max. Part Size | Thickness Range | Characteristics | |
---|---|---|---|---|---|---|
Metric | 227.527 MPa | 12% | 60 HRB | 990.6mm x 1193.8mm | 0.635mm to 6.35mm | Formability, Corrosion Resistance, Weldability |
US | 33 kpsi | 12% | 60 HRB | 39 in. x 47 in. | 0.025 in. to 0.250 in. | As above |
Aluminium 5754 (3.3535 / AlMg3) is known for its superior mechanical strength when compared to other non-heat-treatable aluminium alloys. This alloy provides excellent resistance to both atmospheric conditions and seawater, making it ideal for marine and outdoor applications. Its high strength-to-weight ratio and corrosion resistance make it a reliable choice in industries that require durability and longevity. Whether used in structural components or protective sheeting, Aluminium 5754 ensures both performance and protection in demanding environments.
Tensile Strength | Elongation | Hardness | Max. Part Size | Thickness Range | Characteristics | |
---|---|---|---|---|---|---|
Metric | 180 – 250 MPa | 14% – 16% | 45 HRB | 990.6mm x 1193.8mm | 0.635mm to 6.35mm | Formability, Weldability, Corrosion Resistance, Strength, Durability |
US | 26.11 – 36.26 kpsi | 14% – 16% | 45 HRB | 39 in. x 47 in. | 0.025 in. to 0.250 in. | As above |
This alloy is medium-strength with exceptional corrosion resistance and is the strongest among non-heat-treatable alloys. However, it is not suitable for applications above 65°C. It offers excellent machinability and corrosion resistance, making it ideal for many environments. While it can be welded using standard methods, it is not recommended for welding in the heat-affected zones of high-strength alloys.
Tensile Strength | Elongation | Hardness | Max. Part Size | Thickness Range | Characteristics | |
---|---|---|---|---|---|---|
Metric | 270 – 345 MPa | 16% | 81.5 HRB | 990.6mm x 1193.8mm | 0.635mm to 6.35mm | Formability, Weldability, Corrosion Resistance, Strength, Durability |
US | 39.15 – 50.04 kpsi | 16% | 81.5 HRB | 39 in. x 47 in. | 0.025 in. to 0.250 in. | As above |
Aluminum 6061, often called structural aluminum, is a high-strength alloy enhanced with silicon. It offers greater strength than 5052 but has reduced formability and weldability due to its lower modulus of elasticity. Despite this, it retains a lightweight profile, making it ideal for applications where strength is a priority. Unlike some alloys, 6061 is designed with performance in mind rather than aesthetics.
Tensile Strength | Elongation | Hardness | Max. Part Size | Thickness Range | Characteristics | |
---|---|---|---|---|---|---|
Metric | 310.264 MPa | 12% | 95 HRB | 990.6mm x 1193.8mm | 0.635mm to 6.35mm | Strength Corrosion, Resistance |
US | 45 kpsi | 12% | 95 HRB | 39 in. x 47 in. | 0.025 in. to 0.250 in. | As above |
Tensile Strength | Elongation | Hardness | Max. Part Size | Thickness Range | Characteristics | |
---|---|---|---|---|---|---|
Metric | 110 – 260 MPa | 6% – 15% | 65 – 95 HRB | 990.6mm x 1193.8mm | 0.635mm to 6.35mm | Formability, Weldability, Corrosion Resistance, Strength, Durability |
US | 15.95 – 37.71 kpsi | 6% – 15% | 65 – 95 HRB | 39 in. x 47 in. | 0.025 in. to 0.250 in. | As above |
Tensile Strength | Elongation | Hardness | Max. Part Size | Thickness Range | Characteristics | |
---|---|---|---|---|---|---|
Metric | 275 – 540 MPa | 2 - 10% | 55 – 163 HRB | 990.6mm x 1193.8mm | 0.635mm to 6.35mm | Formability, Weldability, Corrosion Resistance, Strength, Durability |
US | 39.89 – 78.32 kpsi | 2 - 10% | 55 – 163 HRB | 39 in. x 47 in. | 0.025 in. to 0.250 in. | As above |
Brass C260, a copper-zinc alloy, is distinguished by its signature golden-yellow appearance. It shares corrosion resistance and formability with Aluminum 5052, making it a durable choice. Heavier than aluminum, Brass C260 excels in applications where aesthetics and visual appeal are key. Its strength and malleability also allow for intricate designs and decorative uses.
Tensile Strength | Elongation | Hardness | Max. Part Size | Thickness Range | Characteristics | |
---|---|---|---|---|---|---|
Metric | 427.475 MPa | 25% | 70 HRB | 457.2mm x 609.6mm | 0.635mm to 3.175mm | Aesthetics, Formability, Corrosion Resistance |
US | 62 kpsi | 25% | 70 HRB | 18 in. x 24 in. | 0.025 in. to .125 in. | As above |
Copper 101 (C101), also called oxygen-free electronic (OFE) copper, is valued for its high purity and exceptional electrical conductivity. It resists corrosion and is highly formable, making it suitable for precision applications. Compared to oxygenated Copper 110, C101 is more expensive but preferred when minimizing impurities is critical. Its primary use is in industries where superior conductivity outweighs cost considerations.
Tensile Strength | Elongation | Hardness | Max. Part Size | Thickness Range | Characteristics | |
---|---|---|---|---|---|---|
Metric | 282.685 MPa | 14% | 40 HRB | 457.2mm x 609.6mm | 0.813mm to 3.175mm | Electrical Conductivity, Thermal Conductivity, Formability |
US | 41 kpsi | 14% | 40 HRB | 18 in. x 24 in. | 0.032 in. to .125 in. | As above |
Copper 110 (C110) is an oxygenated variant of Copper 101, offering strong electrical conductivity and corrosion resistance at a lower cost. It is widely used in practical applications such as wiring, heat exchangers, and plumbing components. C110 retains the formability of C101 while being more readily available. However, its small oxygen content introduces impurities, making it less pure than C101 for high-precision needs.
Tensile Strength | Elongation | Hardness | Max. Part Size | Thickness Range | Characteristics | |
---|---|---|---|---|---|---|
Metric | 282.685 MPa | 14% | 40 HRB | 457.2mm x 609.6mm | 0.635mm to 3.175mm | Cost Effectiveness, Corrosion Resistance, Thermal Conductivity, Formability |
US | 41 kpsi | 14% | 40 HRB | 18 in. x 24 in. | 0.025 in. to .125 in. | As above |
Low Carbon Steel 1008 is a staple in sheet metal fabrication, offering excellent formability and resistance to cracking due to its low carbon content (under 0.30%). Its weldability is superior to high-carbon steels, making it a versatile choice for various applications. While 1008 is susceptible to corrosion in its raw state, it easily accepts coatings such as zinc plating or powder coating for enhanced protection.
Tensile Strength | Elongation | Hardness | Max. Part Size | Thickness Range | Characteristics | |
---|---|---|---|---|---|---|
Metric | 344.738/448.159 MPa | 20/30% | 63-80 HRB | 990.6mm x 1193.8mm | 0.609mm to 6.35mm | Formability, Weldability, Cost Effectiveness, Strength, Durability |
US | 50/65 kpsi | 20/30% | 63-80 HRB | 39 in. x 47 in. | 0.024 in. to .250 in. | As above |
Cold-rolled galvanized steel features a factory-applied zinc coating that protects against corrosion while giving it a characteristic spangled finish. This coating makes it less compatible with secondary finishes like powder coating unless properly prepped. Though not ideal for welding due to zinc fume emissions, it offers excellent formability, making it well-suited for press brake operations.
Tensile Strength | Elongation | Hardness | Max. Part Size | Thickness Range | Characteristics | |
---|---|---|---|---|---|---|
Metric | 365.422 MPa | 36% | 50-65 HRB | 990.6mm x 1193.8mm | 0.609mm to 3.403mm | Formability, Pre-Plated, Cost Effectiveness, Strength, Durability |
US | 53 kpsi | 36% | 50-65 HRB | 39 in. x 47 in. | 0.024 in. to 0.134 in. | As above |
Cold-rolled galvannealed steel undergoes heat treatment and annealing after zinc coating, forming a zinc-iron alloy for enhanced corrosion resistance and a matte finish. This surface improves paint adhesion compared to galvanized steel but still presents welding challenges. Both materials maintain excellent formability, making them versatile for various applications.
Tensile Strength | Elongation | Hardness | Max. Part Size | Thickness Range | Characteristics | |
---|---|---|---|---|---|---|
Metric | 344.738 MPa | 37% | 50-65 HRB | 990.6mm x 1193.8mm | 0.609mm to 3.403mm | Formability, Pre-Plated, Cost Effectiveness, Strength, Durability |
US | 50 kpsi | 37% | 50-65 HRB | 39 in. x 47 in. | 0.024 in. to 0.134 in. | As above |
Tensile Strength | Elongation | Hardness | Max. Part Size | Thickness Range | Characteristics | |
---|---|---|---|---|---|---|
Metric | 586.054/551.581 MPa | 55%/55% | 70 HRB | 990.6mm x 1193.8mm | 0.609mm to 6.35mm | Formability, Weldability, Corrosion Resistance, Strength, Durability |
US | 85/80 kpsi | 55%/55% | 70 HRB | 39 in. x 47 in. | 0.024 in. to 0.250 in. | As above |
Tensile Strength | Elongation | Hardness | Max. Part Size | Thickness Range | Characteristics | |
---|---|---|---|---|---|---|
Metric | 579.16/537.791 MPa | 60%/55% | 79 HRB | 990.6mm x 1193.8mm | 0.609mm to 3.403mm | Formability, Weldability, Corrosion Resistance, Strength, Durability |
US | 84/78 kpsi | 60%/55% | 79 HRB | 39 in. x 47 in. | 0.024 in. to 0.134 in. | As above |
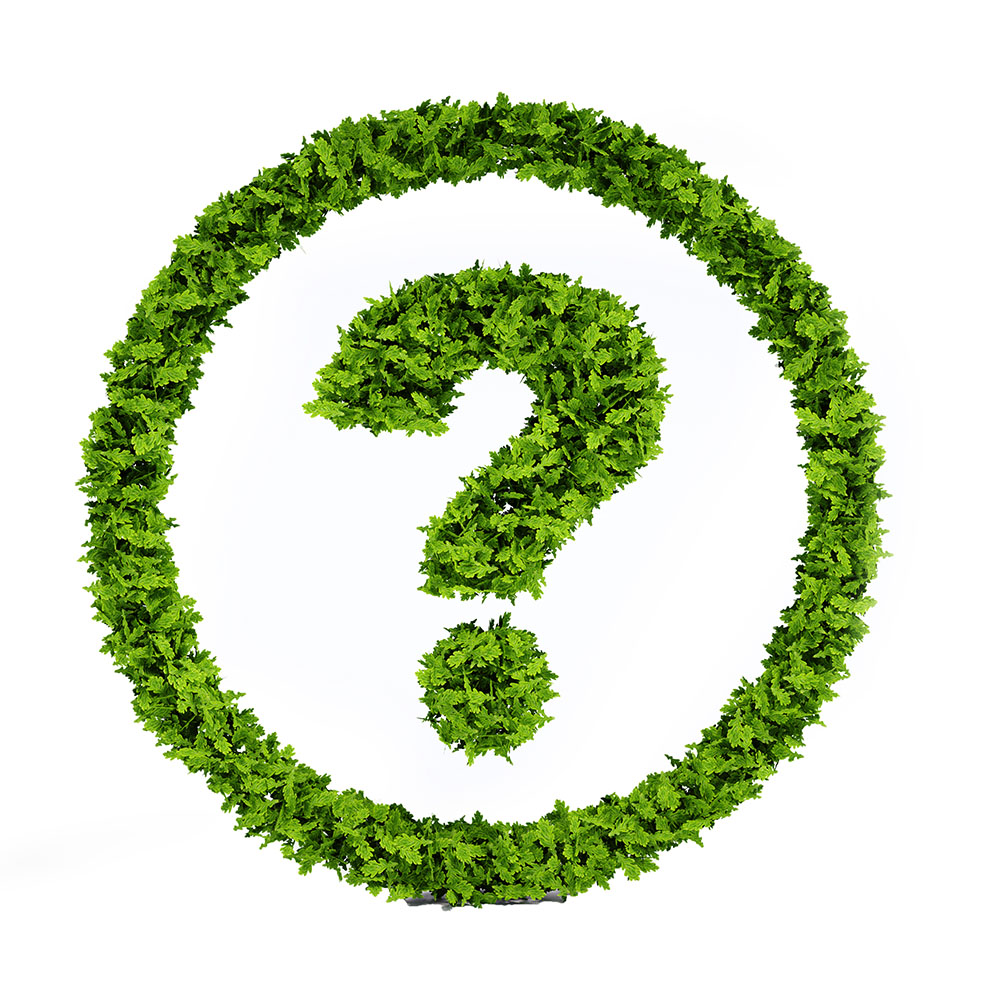
Yes, at KingStar Mold, we work with a variety of high-performance sheet metal materials such as aluminum, steel, and brass, customized to meet the specific needs of our clients.
Cold-rolled steel is processed at room temperature, offering smoother finishes and better precision, while hot-rolled steel is made at higher temperatures, making it easier to form but less precise.
The choice of material depends on factors such as strength, corrosion resistance, weight, and the required finish for your part.
Materials like aluminum, steel, copper, and brass are widely used in sheet metal fabrication due to their strength, durability, and formability.
The maximum thickness depends on the specific equipment and material type but typically ranges from 0.1mm to several millimeters for most processes.
Coatings such as galvanization, powder coating, or anodizing can enhance the corrosion resistance of sheet metal materials.
Industries such as automotive, aerospace, and electronics can benefit from our precise sheet metal manufacturing services, providing strong, lightweight components for various applications.
Absolutely! We utilize advanced technologies and precision manufacturing processes to create complex, high-quality sheet metal parts.