Surface Finishes
Orbital Sander
The most common surface finish for sheet metal parts, orbital sanding uses a random orbital device to remove dross and surface debris from the cutting process. It is ideal for internal components or applications where form, fit, and function are the priorities, but not recommended for cosmetic use.
Straight Grain/Brushed
This surface finish uses a sanding belt to apply a uniform directional pattern on the sheet metal surface, often for cosmetic or end-user-facing purposes. The straight grain can be applied in three ways:
Welded parts often have raised surfaces where the weld beads form. We carefully smooth and blend these weld areas into the surrounding material to ensure a seamless and uniform finish.
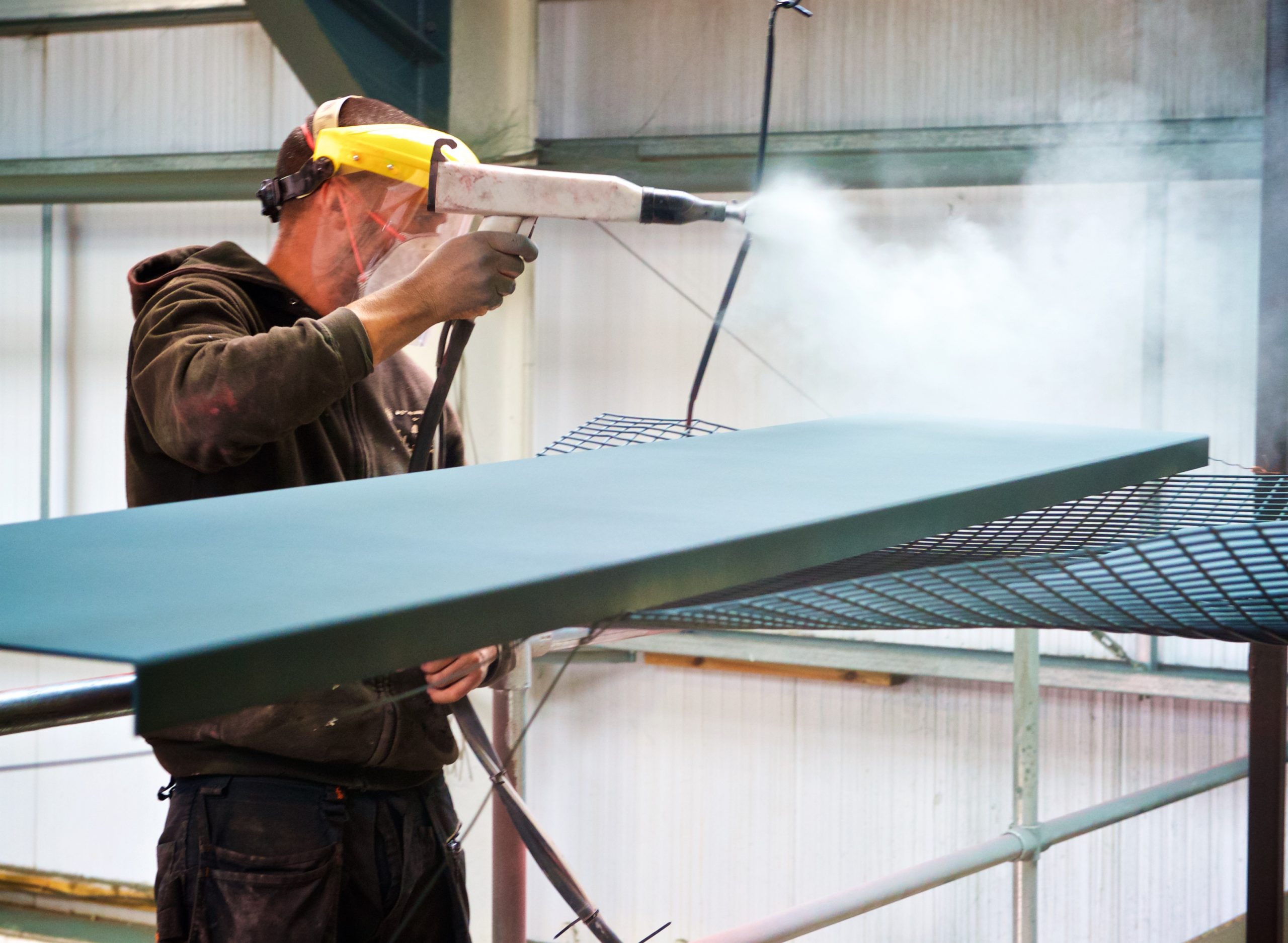
Powder Coating
Plating and Coatings
Finish | Descriptive Name | Compatible Material Types | Specification | Additional Information |
---|---|---|---|---|
Anodizing | Clear Anodizing | Aluminum | Type II, MIL-A-8625, Class 1 | |
Color Anodizing | Type II, MIL-A-8625, Class 2, "Color" | Request your color choice in the "custom option" selection of your online quote. You can request any color. | ||
Black Anodizing | Type II, MIL-A-8625, Class 2, Black | |||
Hardcoat Anodizing | Clear Hardcoat Anodizing | Aluminum | Type III, MIL-A-8625, Class 1 | Minimum coating thickness 0.020in. (0.508mm) |
Hardcoat Anodizing with Teflon | Type I, MIL-A-63576 | |||
Black Hardcoat Anodizing | Type III, MIL-A-8625, Class 2, Black | |||
Chromate | Clear Chromate (Chem-Film) | Aluminum | Type II, MIL-BTL-5541, Class 3 | RoHS, non-hexavalent chromate |
Yellow Chromate (Chem-Film) | Type I, MIL-DTL-5541, Class 3 | Hexavalent chromate | ||
Electroless Nickel | Electroless Nickel, EN | Aluminum | Type IV, ASTM-B733, SC1, Class 1 | Minimum coating thickness 0.0002 in. (0.005mm). **ASTM specifications for these materials are not listed on this table, but you can find them in your online quote. |
Stainless Steel** | ||||
Steel** | ||||
Passivation | Nitric Passivation | Stainless Steel | Nitric 2, ASTM-A967, Practice D | |
Citric Passivation | Citric 3, ASTM-A967, Practice D | |||
Tin | Tin | Copper | Class A, ASTM-B545 | |
Zinc | Zinc(with no supplementary treatment) | Steel | Type I, ASTM-B633, FE/ZN 5 SC1 | minimum coating thickness 0.0002 in. (0.005mm) |
Clear Zinc(with colorless chromate) | Type III, ASTM-B633, FE/ZN 5 SC1, Clear | minimum coating thickness 0.0002 in. (0.005mm) | ||
Black Zinc(with colored (black) chromate) | Type II, ASTM-B633, FE/ZN 5 SC1, Black | minimum coating thickness 0.0002 in. (0.005mm) | ||
Yellow Zinc(with colored (yellow) chromate) | Type II, ASTM-B633, FE/ZN 5 SC1, Yellow | minimum coating thickness 0.0002 in. (0.005mm) |
Wet Paint
With wet paint, a liquid coating is applied to your part to deliver an aesthetically appealing finish. Available in virtually any color, this process is often paired with a primer layer to enhance paint adhesion and durability.
Wet paint is ideal when visual consistency across parts is a key consideration, which is why it’s commonly used in automotive and consumer electronics.
Our wet paint options are available with or without primer.
To ensure your specifications are met precisely, please provide the full paint specification (including color and texture). You can send these details to us via email, or communicate them during a phone call or online meeting. You may also submit a 2D drawing with the paint specifications included.
Special Considerations for Wet Paint:
- Quotes with wet paint service may take slightly longer than 24 hours.
- If masking is required as part of your finished product, please submit a 2D drawing.
Silk Screening
Silk screening on sheet metal involves forcing ink through a fine mesh screen with a stencil to create the desired design, transferring ink onto the exposed areas of the metal surface. This process is commonly used to add labels, instructions, or decorative patterns to fabricated metal products.
Requesting silk screening for your project is simple. Just submit the following information:
Please keep in mind the following silk screening considerations:
Masking
Available Tape And Rounds (Discs) For Masking
Tape | Rounds/Discs | ||
---|---|---|---|
Standard | Metric | Standard | Metric |
0.250 in. | 6.35mm | 0.3125 in. | 7.938mm |
0.500 in. | 12.7mm | 0.375 in. | 9.525mm |
0.675 in. | 17.145mm | 0.500 in. | 12.7mm |
0.750 in. | 19.05mm | 0.625 in. | 15.875mm |
1.000 in. | 25.4mm | 0.750 in. | 19.05mm |
2.000 in. | 50.8mm | 1.000 in. | 25.4mm |
Part Marking
Our part marking service provides clear and durable identification on sheet metal components, ensuring traceability and consistency across your production process. Whether for serial numbers, logos, or part numbers, we offer precise marking solutions that enhance both function and branding.
To include part marking in your project, please submit a 2D drawing that specifies:
Standard and Cosmetic Parts
Standard | Cosmetic | |
---|---|---|
Description | When lower cost is a greater priority than appearance | Functionally cosmetic parts that make you and your parts look good to stakeholders |
Quantity | 1-100+ parts | Best for 1-25 parts |
Surface Finish | Protolabs' discretion | Customer specified(grain direction, orbital sanded) |
Safe Handling | Yes | Yes |
Cost | $ | $$ |
Use Cases | Form, fit, function prototyping; internal components | Testing or demonstration units, trade show parts, external components |
Part Applications | Internal brackets and mounts, heat shields, support structures, washers, spacers, electrical components | Housings, covers, face plates, external brackets and mounts |
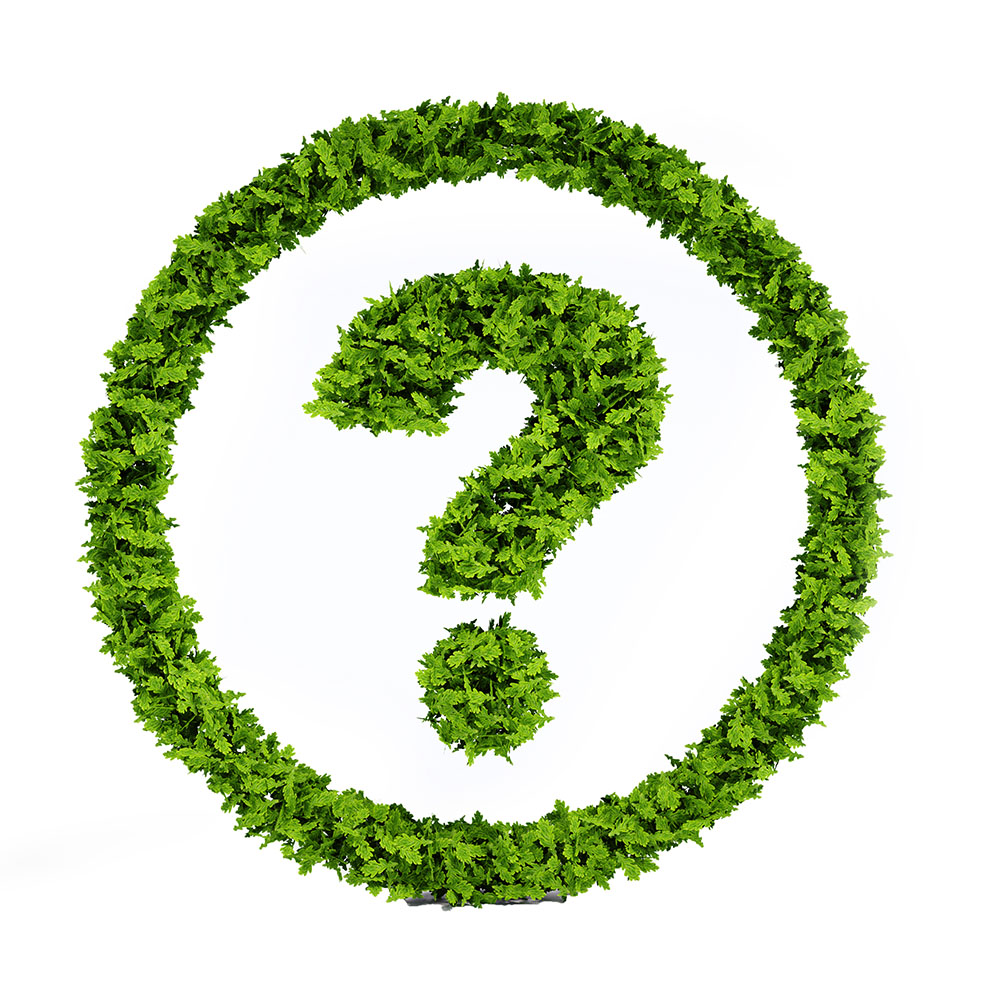