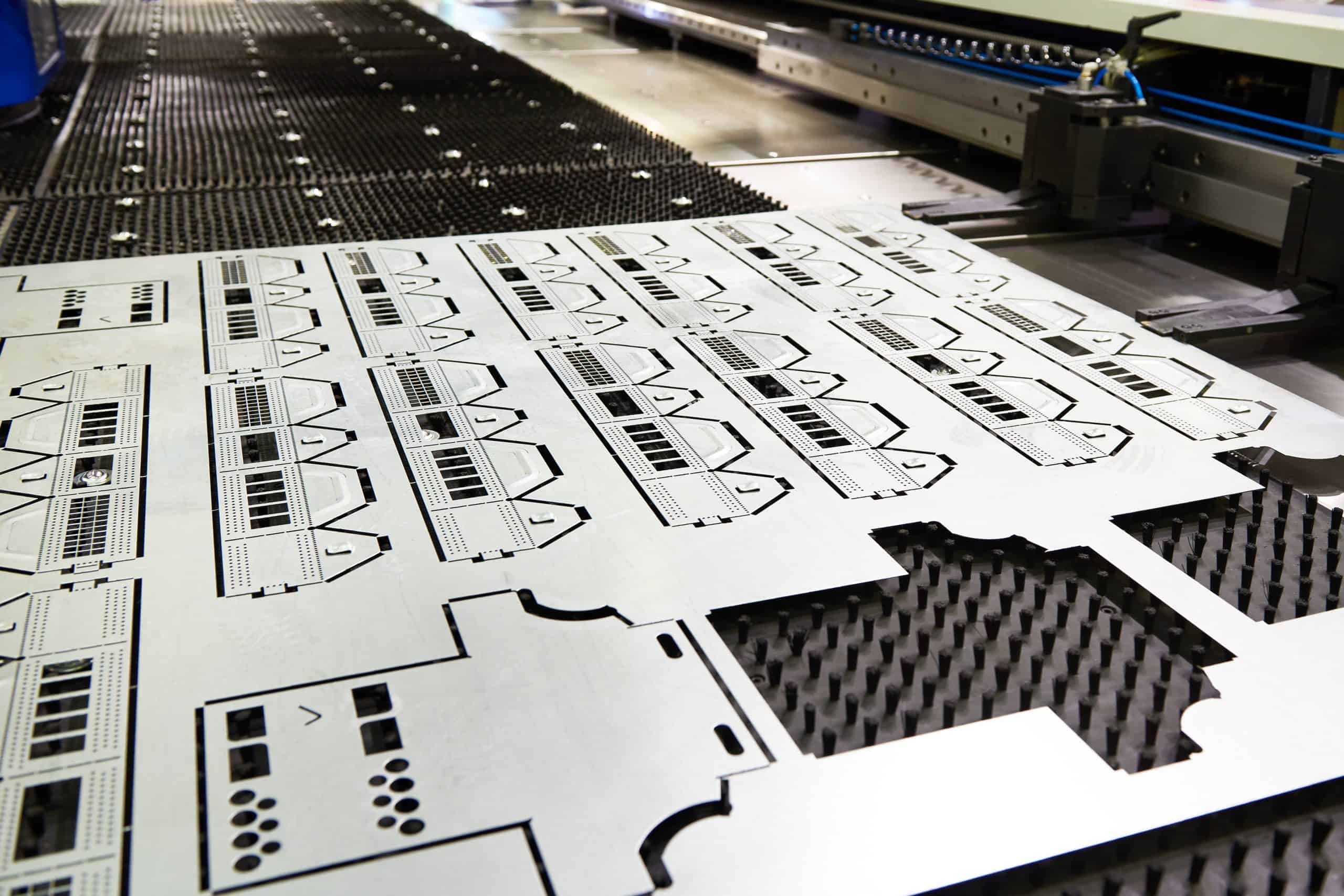
Overview of Sheet Metal Fabrication
Sheet metal fabrication is a manufacturing process that involves shaping and assembling metal sheets into specific parts or products. This process includes techniques such as cutting, bending, punching, and welding to create components used in a wide range of industries, including automotive, aerospace, construction, and electronics. Sheet metal fabrication offers high durability, precision, and versatility, allowing manufacturers to produce complex and customized designs with ease.
Our sheet metal fabrication process begins with selecting the appropriate type of metal, typically steel, aluminum, or stainless steel, depending on the desired properties of the final product. The metal sheets are then cut into the required shapes using tools such as laser cutters, shears, or water jets. Following this, the sheets are bent or stamped into specific forms using press brakes or stamping presses. Depending on the complexity of the design, additional processes like welding or assembly may be performed to complete the product. The result is a finished, precision-crafted component ready for use in its intended application.
Advantages of Sheet Metal Fabrication
Cost-Effective Manufacturing
Sheet metal fabrication is a cost-efficient method for producing high-quality components, especially in large volumes. It minimizes material waste and production time, reducing overall manufacturing costs.
Versatility in Design
Sheet metal can be easily shaped, cut, and assembled into a wide range of designs and structures. This flexibility allows for the production of everything from simple parts to complex, custom configurations.
High Strength-to-Weight Ratio
Sheet metal offers an excellent strength-to-weight ratio, making it ideal for industries like aerospace and automotive. It provides durability and robustness while maintaining a lightweight profile, crucial for many engineering applications.
Precision and Consistency
Free Design Review for Sheet Metal Fabrication
Take advantage of a 30-minute virtual meeting with our sheet metal applications engineer to refine your project. This session is perfect for addressing questions and ensuring your design meets production requirements.
Assessing material suitability for your application
Optimizing design for cost-effectiveness
Enhancing strength and durability
Choosing the best fabrication techniques for accuracy and minimal waste
KingStar Mold, Your Trusted Partner
At KingStar Mold, we prioritize quality at every stage of the process to deliver precise sheet metal parts, from initial design through to production. We adhere to Design for Manufacturability (DFM) principles, taking the time to fully understand your requirements and offer optimal solutions for your project.
Our capabilities include advanced manufacturing techniques such as laser cutting, bending, punching, welding, stamping, and riveting. Using state-of-the-art inspection tools—such as CMM, 2D measuring instruments, XRF analyzers, gauges, micrometers, and calipers—we ensure all parts meet stringent standards.
With years of experience and ISO-certified fabrication facilities, we guarantee that each project meets the highest quality standards. Trust KingStar Mold for accurate, custom sheet metal parts tailored to your specifications.
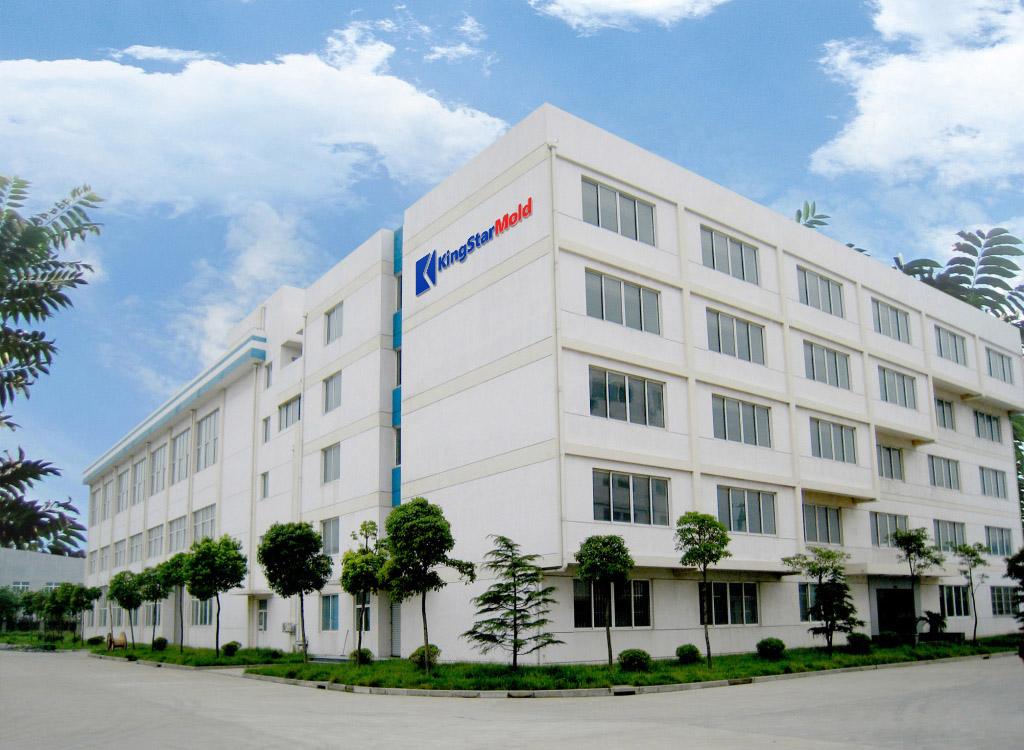
Our Factory In China
KingStar Mold is a leading manufacturer based in China, specializing in custom injection molds and the production of plastic and silicone components. With over ten years of experience, we offer comprehensive solutions from mold design to production, ensuring the highest standards of quality and precision.
Our factory is equipped with advanced machinery and staffed by skilled professionals, dedicated to delivering tailored, high-performance parts for a variety of industries. Whether it’s plastic, silicone, or a combination of materials, KingStar Mold provides reliable, cost-effective solutions for every project.
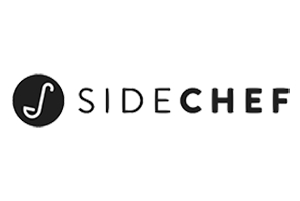
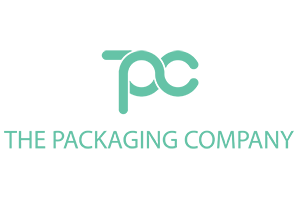
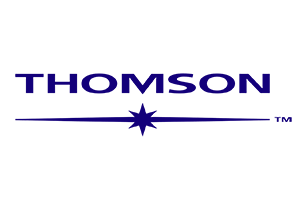
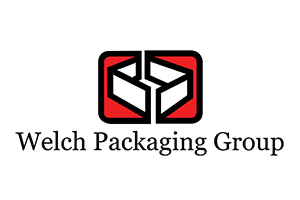
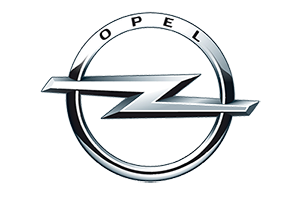
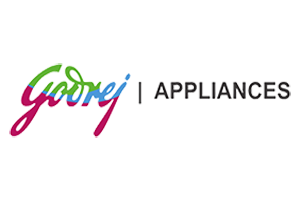
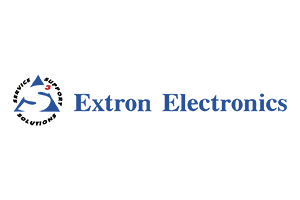
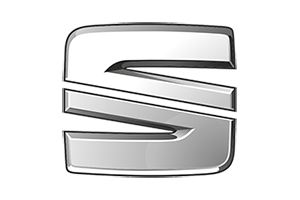
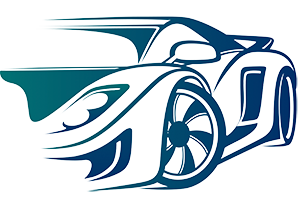
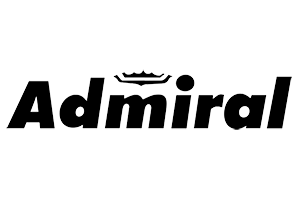
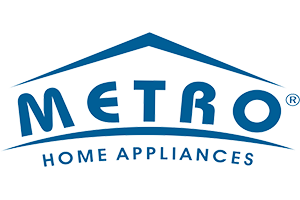
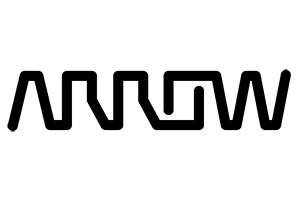
Sheet Metal Materials
Aluminum is a highly durable and lightweight metal, prized for its ability to resist corrosion. Its versatility and ease of manipulation make it suitable for diverse industries, such as automotive, aerospace, and construction, where strength and weight efficiency are critical.
Color: Silvery-white, often with a shiny or matte finish.
Cost: Generally affordable, with prices fluctuating based on alloy type and market conditions. Aluminum is cost-effective for large-scale projects.
Subtypes: 5052, 5083, 6061
Copper is a reddish-brown metal known for its excellent conductivity, making it ideal for electrical and thermal applications. It is highly malleable and resistant to corrosion, though it can tarnish over time.
Color: Reddish-brown that gradually turns greenish with oxidation.
Cost: Copper tends to be more expensive than aluminum, especially when used for high-performance applications like electrical wiring or heat exchangers.
Subtypes: C101(T2), C103(T1), C103(TU2), C110(TU0)
Brass is an alloy of copper and zinc, offering good strength, corrosion resistance, and an attractive gold-like appearance. It is commonly used for decorative purposes, plumbing, and electrical fittings.
Color: Yellow to reddish-gold depending on the zinc content.
Cost: More expensive than aluminum and steel, but relatively affordable compared to other high-end metals like bronze.
Subtypes: C27400, C28000, C36000
Steel is an alloy of iron and carbon, known for its strength, durability, and versatility. It is commonly used in construction, automotive, and machinery applications. Steel can be further alloyed to improve its properties.
Color: Typically silvery-gray, though it can vary depending on the alloy and surface treatment.
Cost: Generally affordable, with prices varying depending on the grade and specific steel alloy. Mild steel is one of the most cost-effective materials.
Subtypes: Galvanized Steel (SGCC / SECC), SPCC, Q235, 1020
Stainless steel is an alloy of iron, chromium, and sometimes nickel, known for its excellent corrosion resistance and strength. It is commonly used in food processing, medical equipment, and architectural applications due to its durability and resistance to rust.
Color: Silvery-gray with a shiny, reflective surface.
Cost: Stainless steel is more expensive than regular steel due to its corrosion-resistant properties and the cost of alloying elements, such as chromium and nickel.
Subtypes: SUS 304
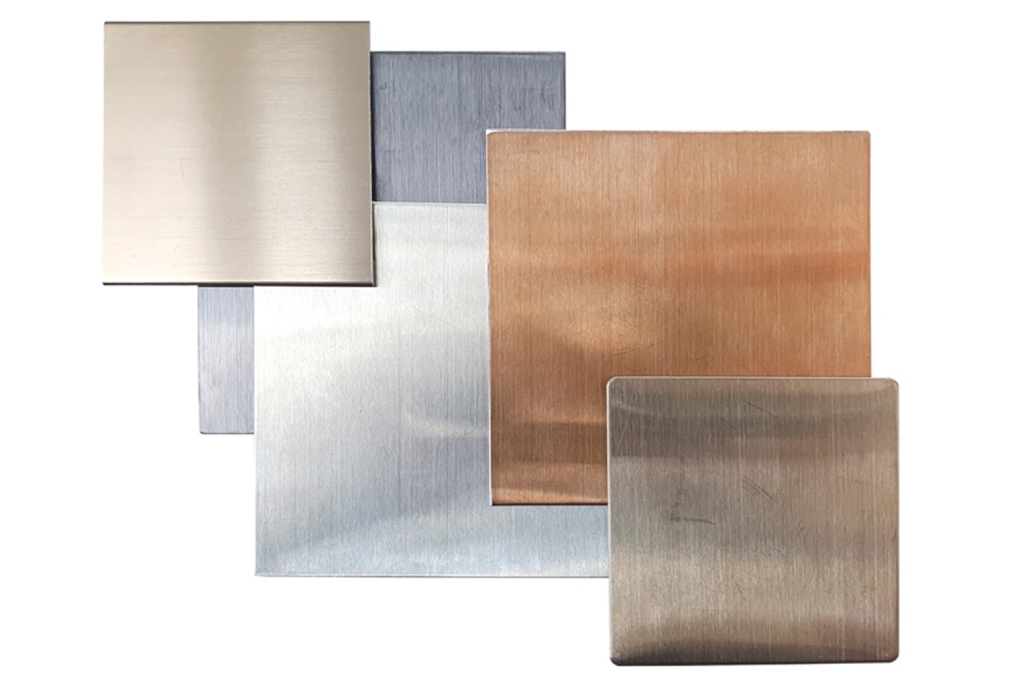
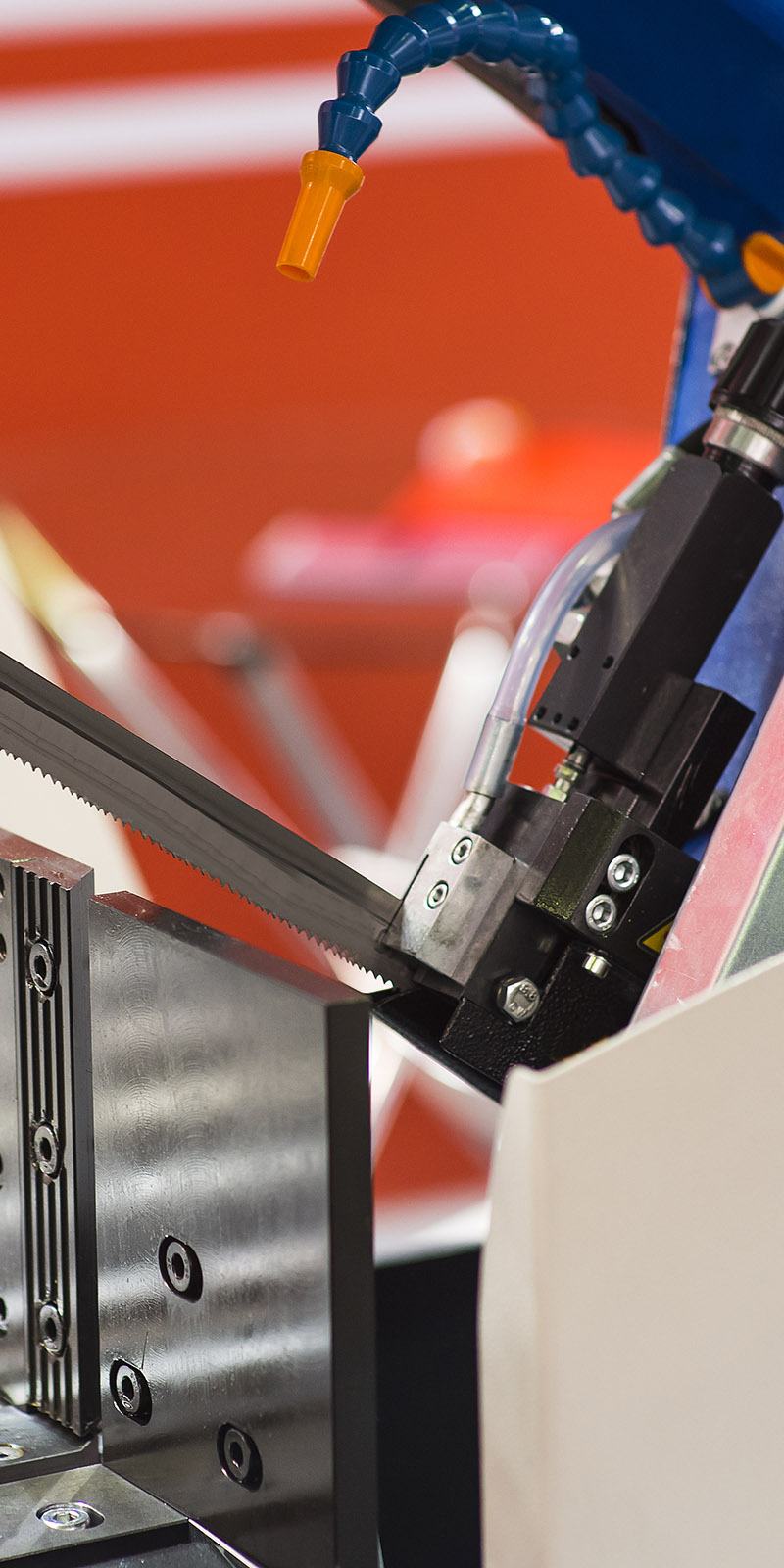
Why Choose Us
We Believe You Will Choose Us Again
Only companies with extensive market experience and a deep understanding of customer needs can offer the best service.
Skilled
High-precision production equipment, skilled production staff, and guaranteed delivery times.
Experienced
Over ten years of industry experience, with a mature quotation system and technical support.
Thoughtful
Customized processing options that save time and effort, with active support throughout pre-sales and post-sales.
Equipped
Engineers review designs to identify and resolve potential issues, backed by advanced testing equipment.
Our Solutions for Sheet Metal Fabrication
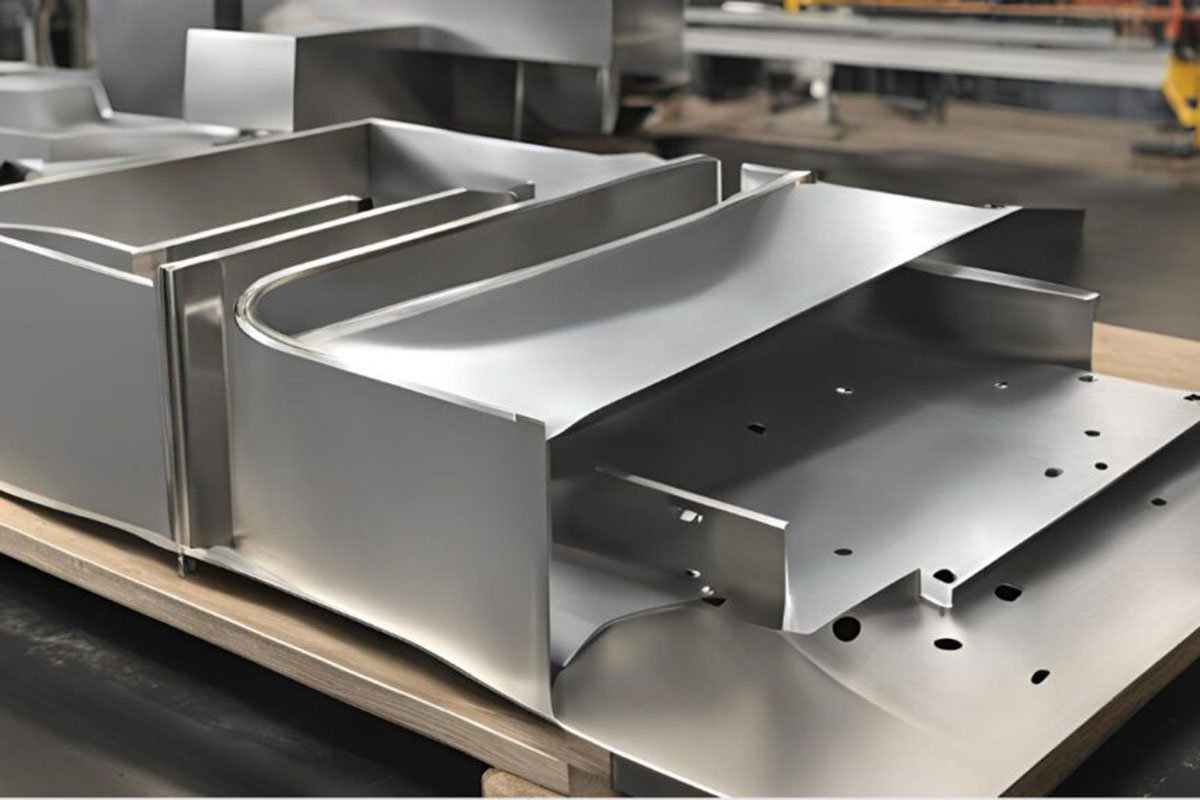
Rapid Prototyping
KingStar Mold’s rapid prototyping service allows for the quick development of functional sheet metal prototypes, enabling designers to test and refine their concepts before full-scale production. Using advanced techniques like laser cutting and precision bending, we accelerate the product development process while ensuring high accuracy and quality.
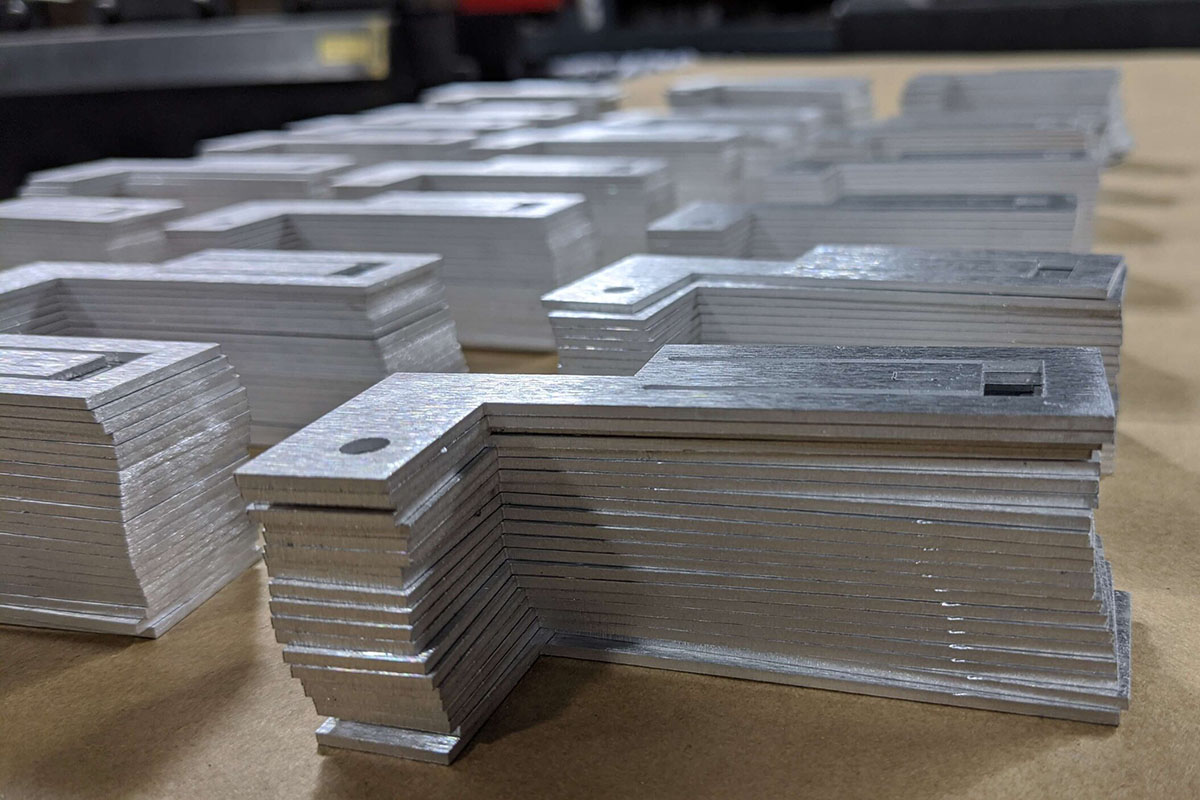
Low Volume Fabrication
At KingStar Mold, our low volume fabrication service is tailored for producing small quantities of custom sheet metal parts, ideal for prototypes, pilot runs, or specialized applications. We offer flexibility and precision, ensuring high-quality results without the need for large-scale production.
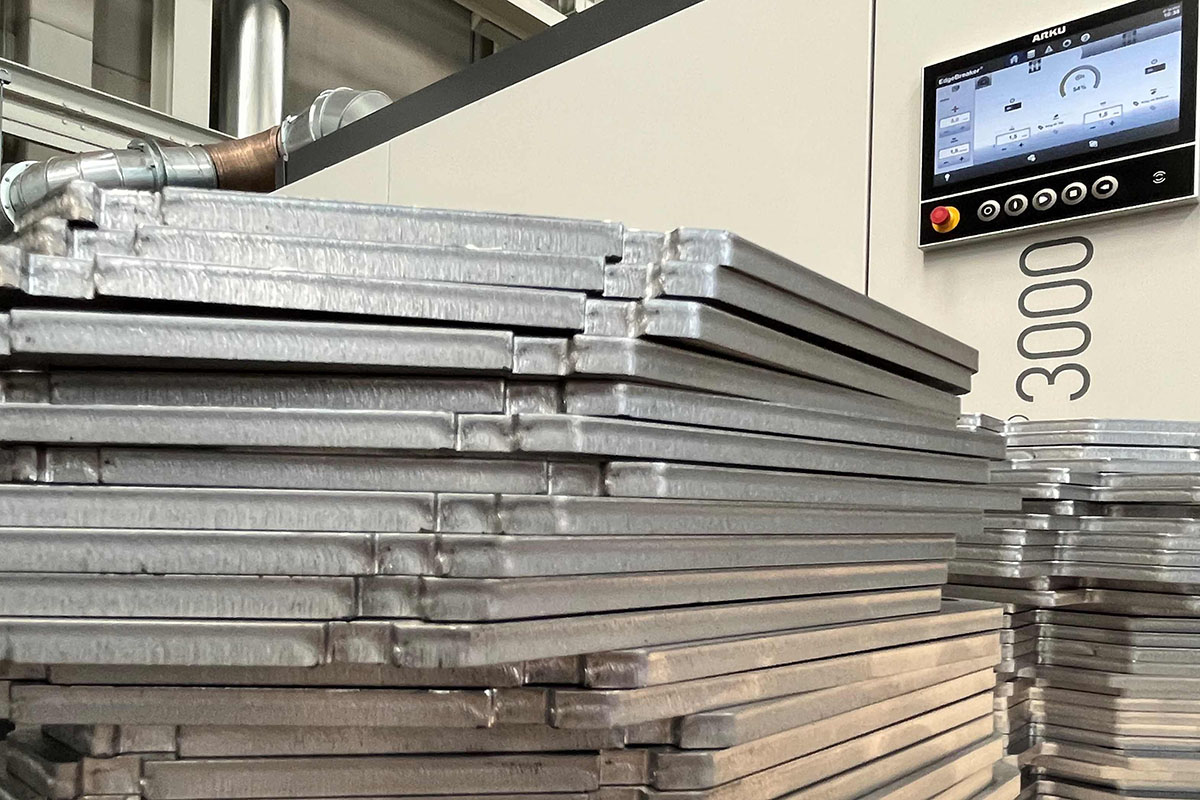
High-volume Production
KingStar Mold’s high volume fabrication service is optimized to deliver large quantities of custom sheet metal parts with consistent quality and efficiency. Our advanced production techniques and streamlined workflows ensure cost-effective solutions for high-demand production runs.
Our Customizable Services for Sheet Metal Fabrication
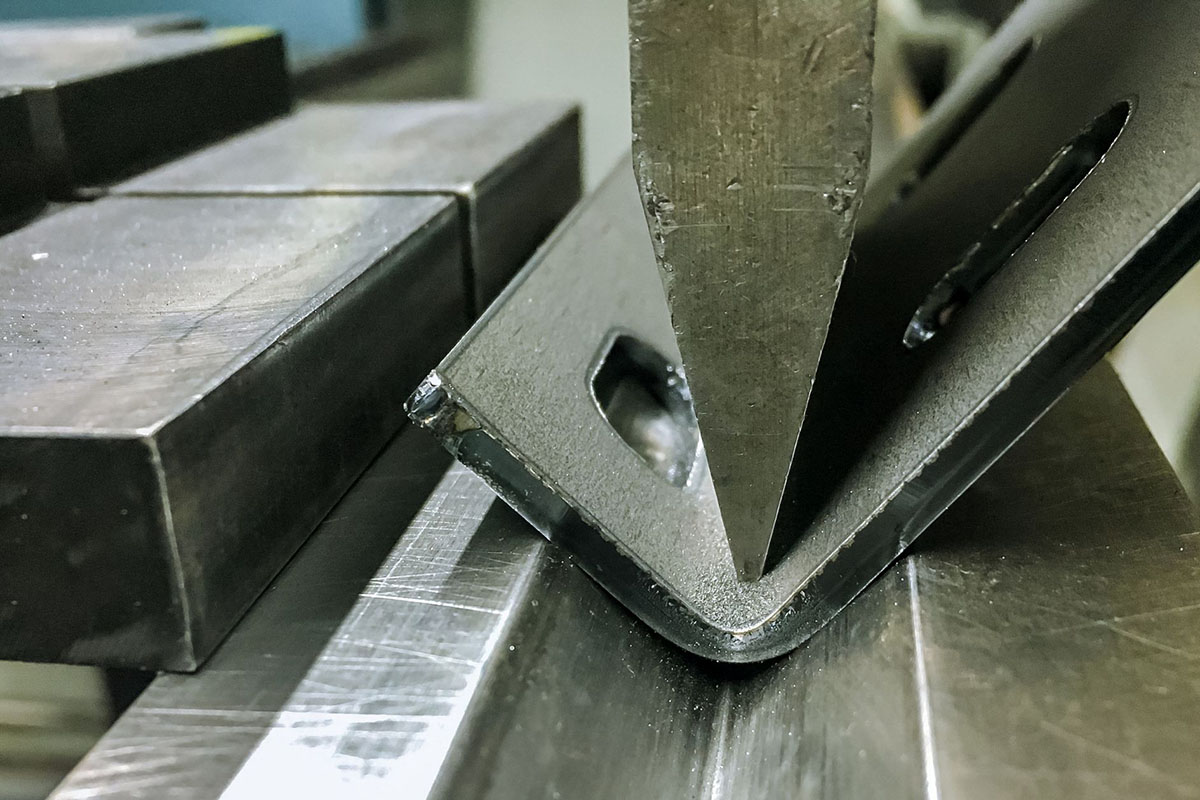
Forming & Bending
Forming and bending are metalworking processes where controlled force is applied to sheet metal to shape it into specific angles, curves, or complex forms, ensuring precision and durability for a variety of industrial applications.
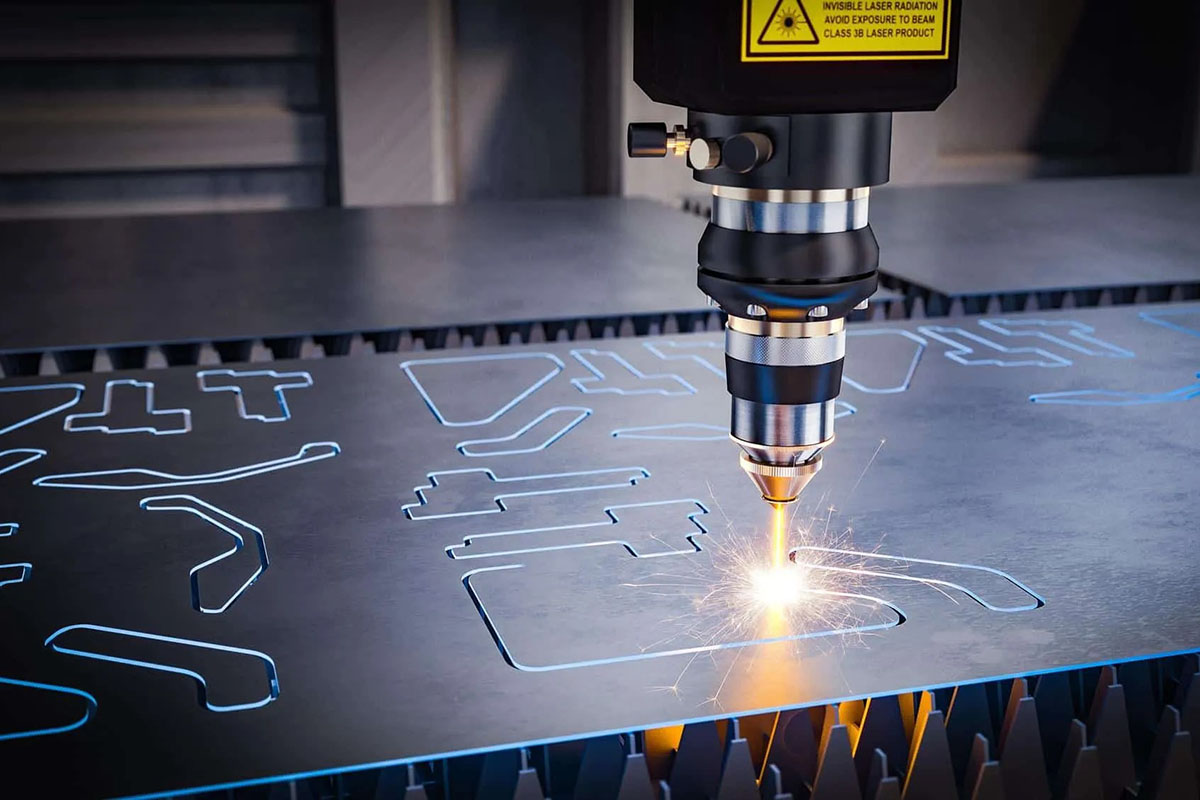
Laser Cutting
Laser cutting utilizes a high-powered laser beam to precisely cut through sheet metal, offering exceptional accuracy, clean edges, and the ability to handle intricate designs with minimal material waste.
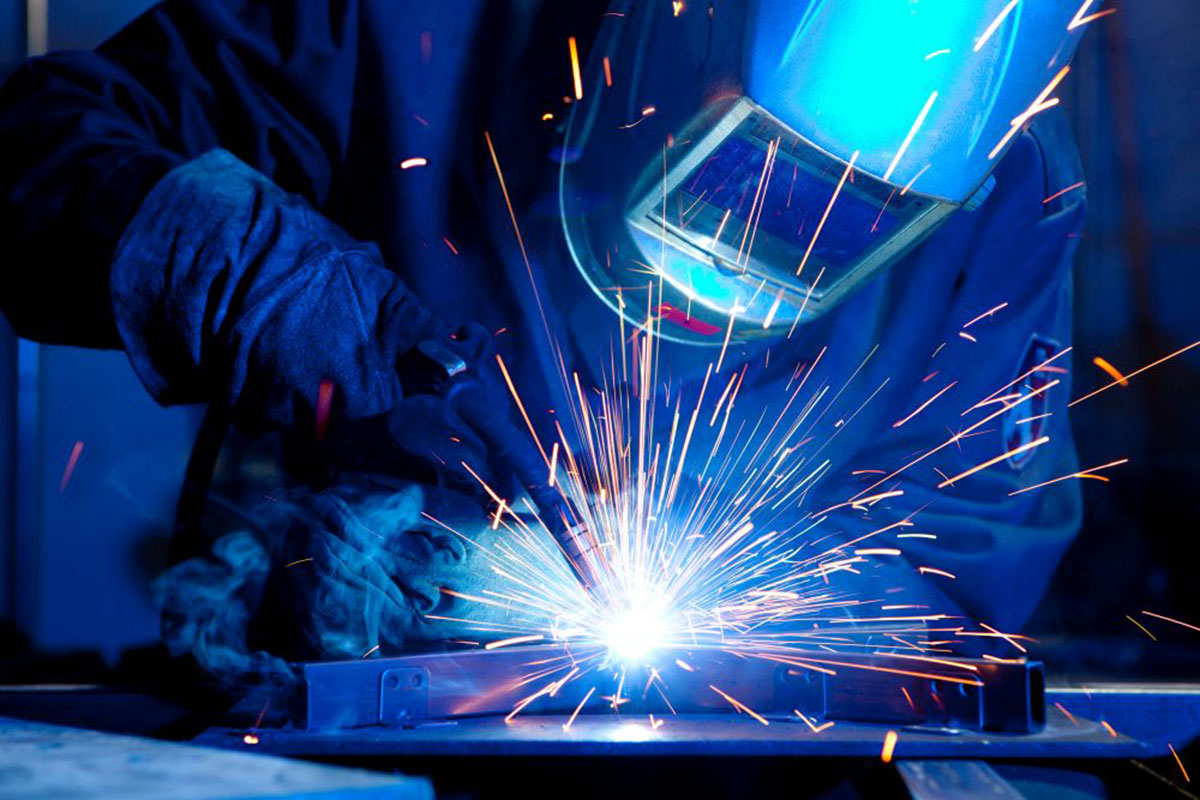
Welding
Welding is a critical joining process where heat and pressure are applied to fuse metal components together, ensuring strong, durable bonds that are essential for structural integrity.
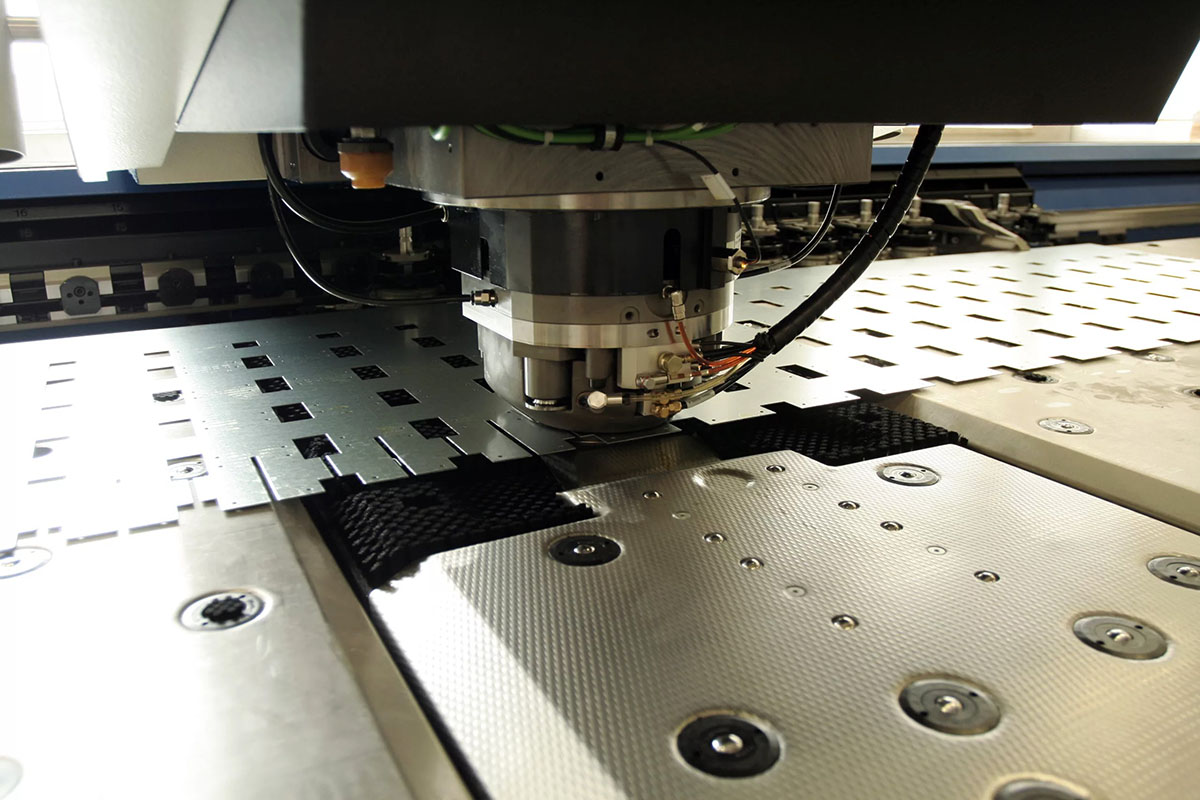
Punching
Punching is a sheet metal fabrication process in which a punch press creates holes or shapes by applying force to a die, providing efficient, high-volume production for precise and repeatable results.
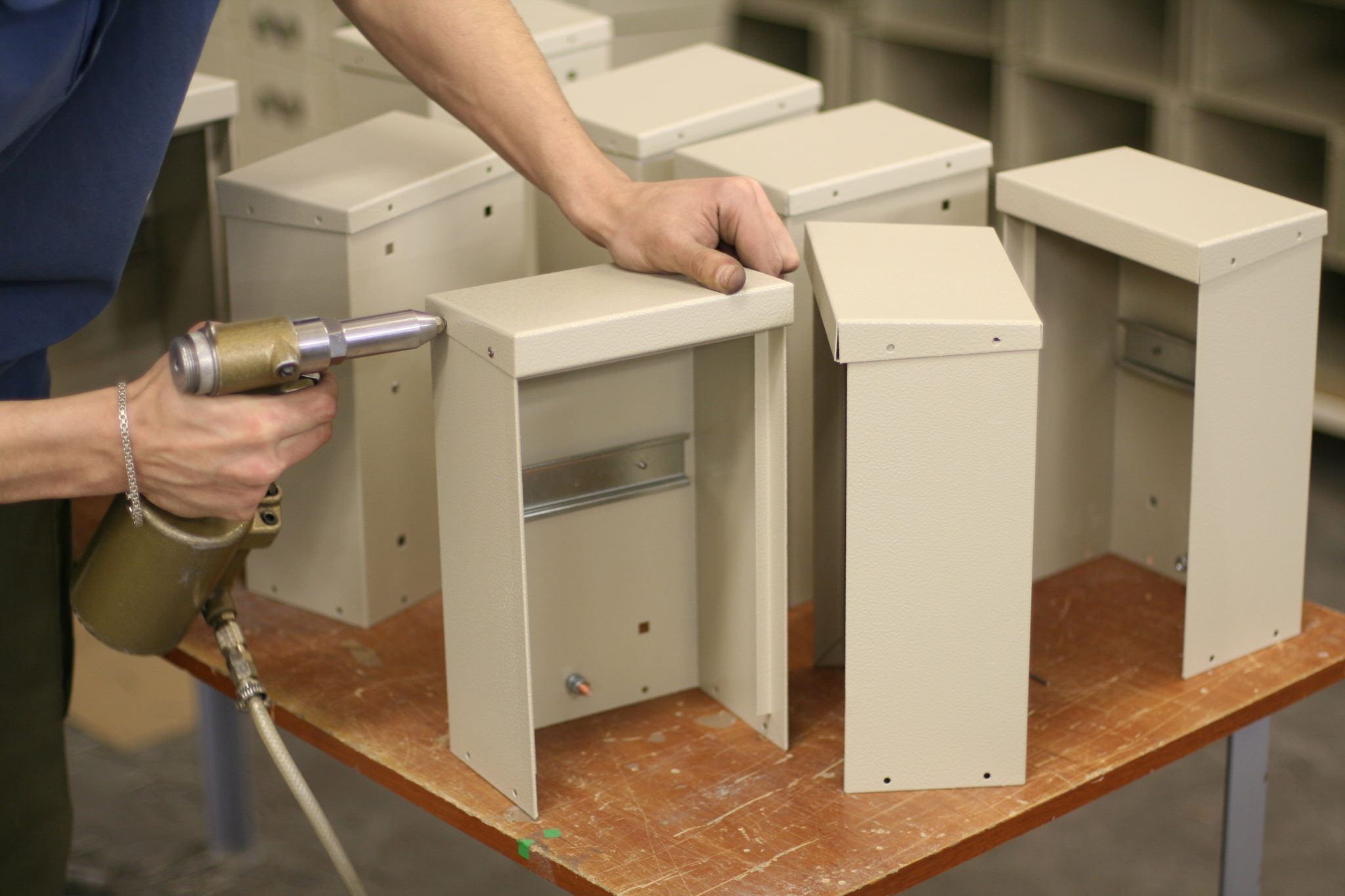
Fabricated Assemblies
It involve the process of combining multiple metal components, including those from welding, bending, punching, and other techniques, to create a complete, functional unit. This ensures high-quality, durable, and precise final products tailored to specific application needs.
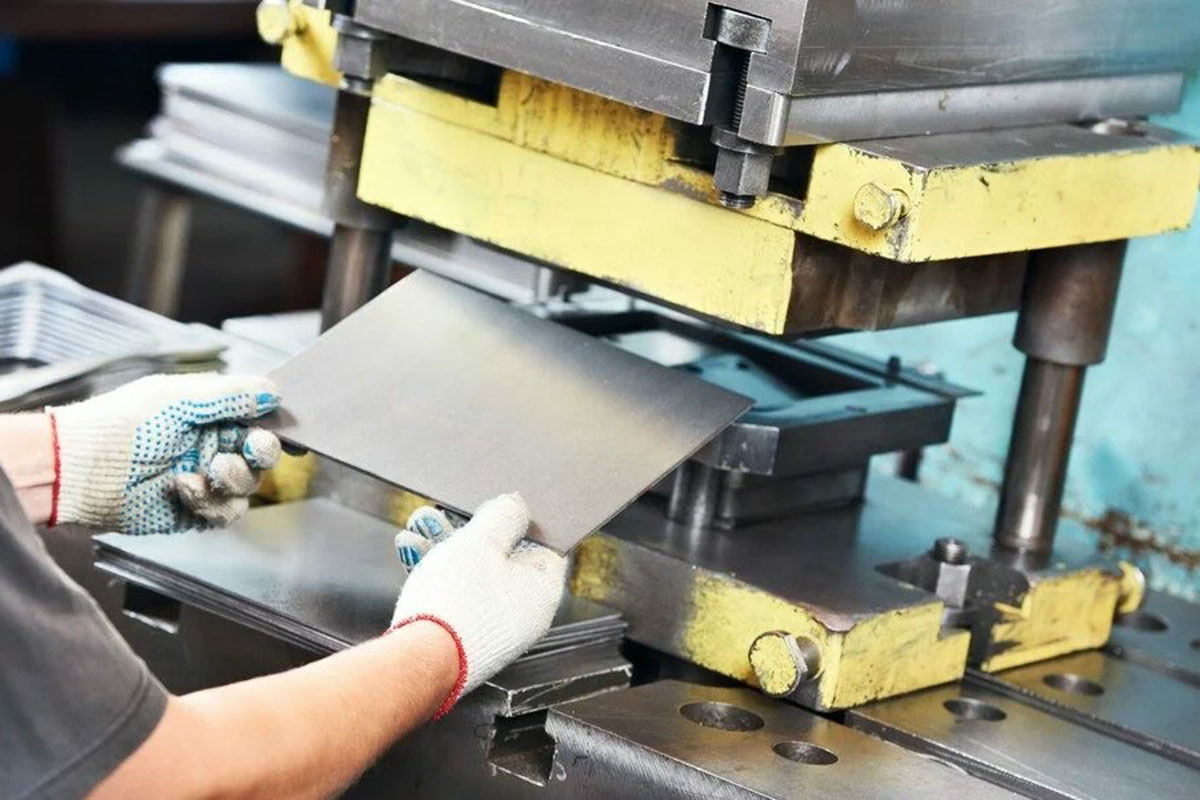
Stamping
Stamping is a manufacturing process that uses a die to press sheet metal into specific shapes or patterns, delivering high-volume production with precision and consistency for a wide range of applications.
Capabilities & Lead Time
Fabrication Capabilities | Eligibility | Applications |
---|---|---|
Cutting (laser or punch) Deburring Forming/bending (≤12 bends) Hardware insertion (extensive PEM® library) Tapping/countersinks | Material thicknesses: ≤0.125 in. (≤3.175mm) | Brackets, Covers, Panels, Flat geometries, Mounts |
Fabrication Capabilities | Eligibility | Applications |
---|---|---|
Include all 3-day processing options plus CNC-machined features (flanges, pockets, and other features) Additional forming options (complex setups or sequencing, >12 bends) Intricately formed features (hems, jogs/offsets) Punch-formed features | All material thicknesses: 0.024 in. - 0.250 in. (0.61mm-6.35mm) | Complex internal componentry Parts with features critical to quality or functionality Enclosure or chassis housings |
Fabrication Capabilities | Finishing Options | Applications |
---|---|---|
Welding (add 1 day) Assembly (add 1-3 days) | Powder Coating (add 2 days) Plating/coating (add 2 days) Masking (add 1-2 days) Silk screening (add 1 day) Part marking (add 1 day) | Weldments Multi-component assemblies End-user-facing projects |
Accepted File Format and Configuration
File Format | Configuration Requirements |
---|---|
.DXF | 2D vector files for laser cutting, punching, and routing |
.DWG | AutoCAD drawings for precise fabrication design |
.STEP | 3D CAD files for assemblies and complex geometry |
.IGES | For 3D geometry exchange in CAD software |
.STL | Used for 3D printing or rapid prototyping |
For reference drawings, but not for direct fabrication | |
.Parasolid | 3D CAD format for accurate part design and tooling |
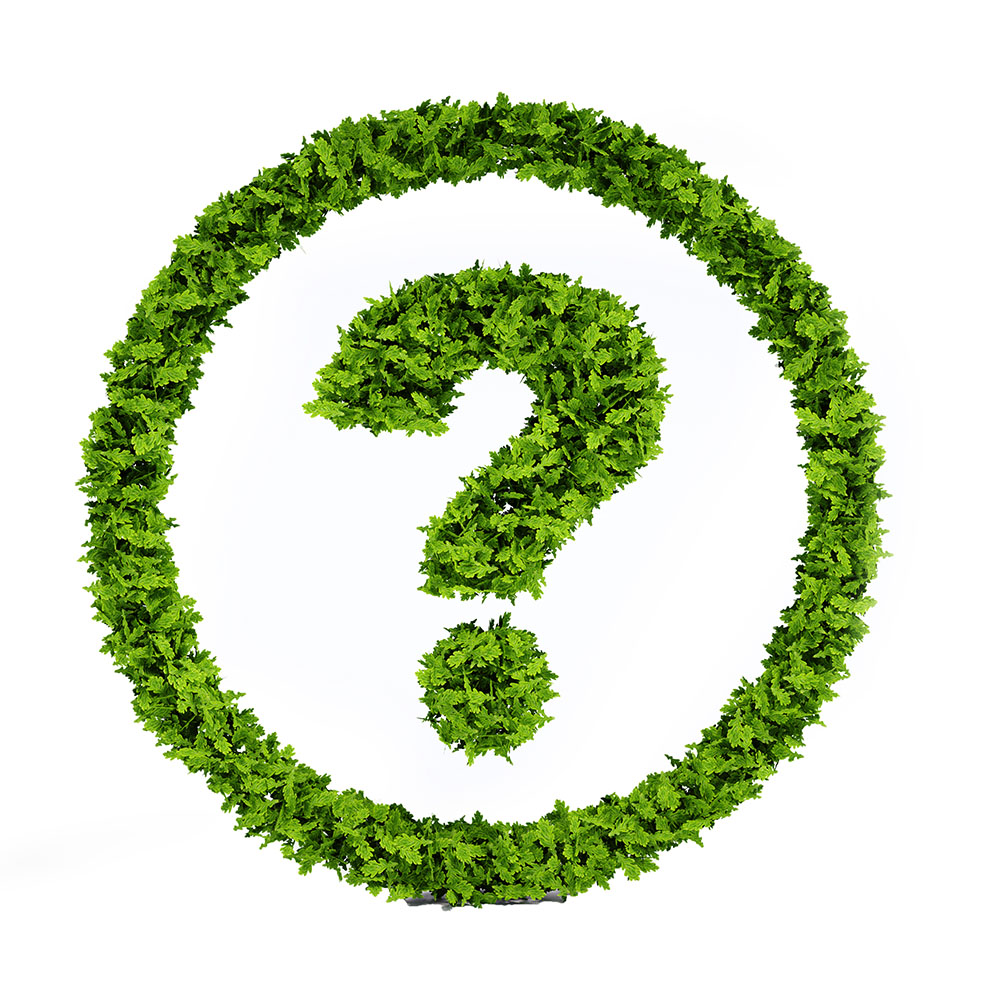