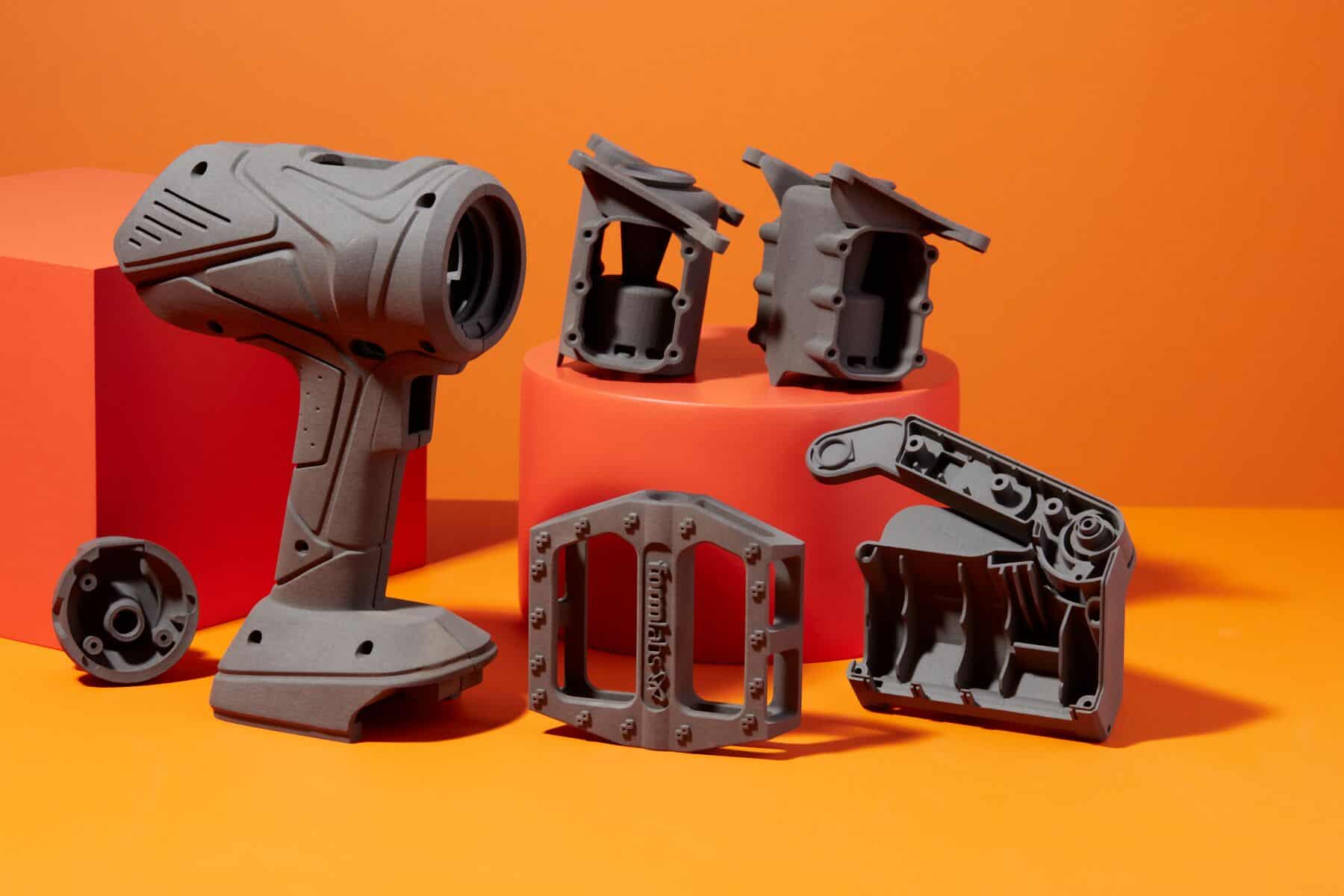
SLS 3D Printing Overview
Selective Laser Sintering (SLS) is a versatile industrial 3D printing technology that produces precise, high-performance prototypes and end-use parts, with production times as fast as just one day. By utilizing a range of materials, including nylon-based resins and thermoplastic polyurethane (TPU), SLS creates robust, durable parts that excel in heat resistance, chemical stability, flexibility, and dimensional accuracy. Unlike other 3D printing methods, SLS doesn’t require support structures, allowing for more efficient builds where multiple parts can be nested together in a single print. This makes it an economical choice for producing larger quantities of functional components or complex geometries.
Common applications of SLS include:
Our SLS 3D Printing Design Guidelines & Capabilities
Metric | US | |
---|---|---|
Layer Thickness | 0.1016mm | 0.004 in. |
Metric | US | |
---|---|---|
PA12 | 482mm x 482mm x 431mm | 19 in. x 19 in. x 17 in. |
PP (Polypropylene) | 304mm x 269mm x 269mm | 12.6 in. x 10.6 in. x 10.6 in. |
Nylon and TPU Materials | 304mm x 269mm x 406mm | 12.6 in. x 10.6 in. x 16 in. |
Metric | US | |
---|---|---|
Minimum Wall Thickness | 0.762mm | 0.030 in. |
For well-optimized designs, SLS typically achieves tolerances of ±0.010 in. (0.25mm) plus 0.1% of the nominal length. However, tolerance accuracy may vary depending on the geometry of the part.
Metric | US | |
---|---|---|
PP and TPU | 1.01mm | 0.04 in. |
Nylons | 0.762mm | 0.03 in. |
Parts with larger dimensions (>7 in.) or thin features are more prone to warping during the SLS process. To minimize this risk, we recommend maintaining a consistent thickness of 0.125 in. (3.175mm) across the part for better structural stability.
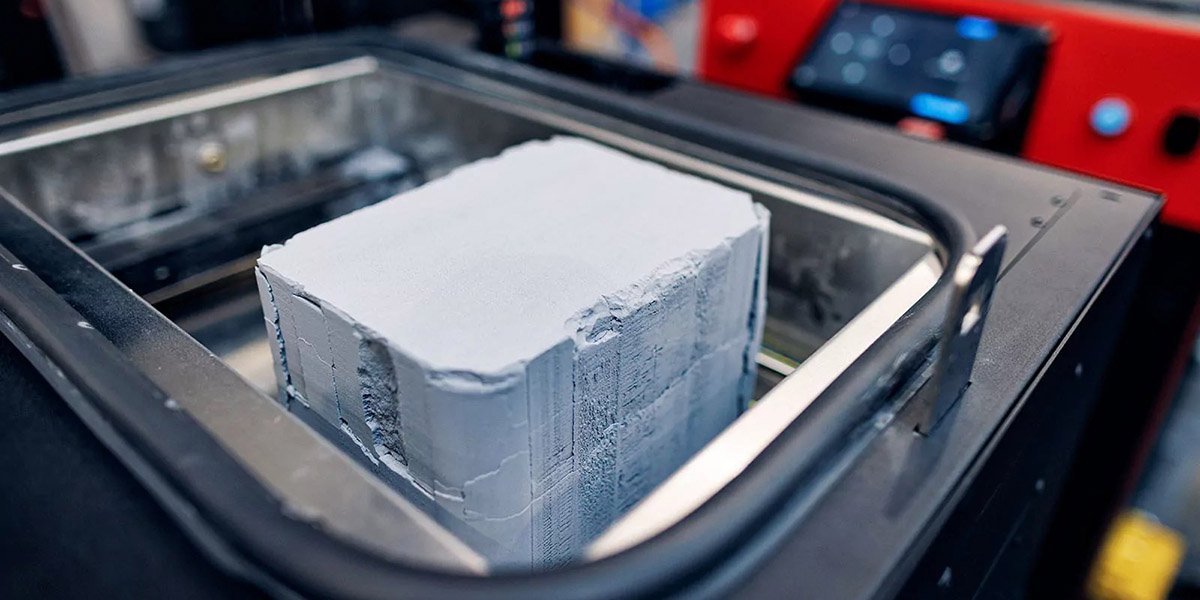
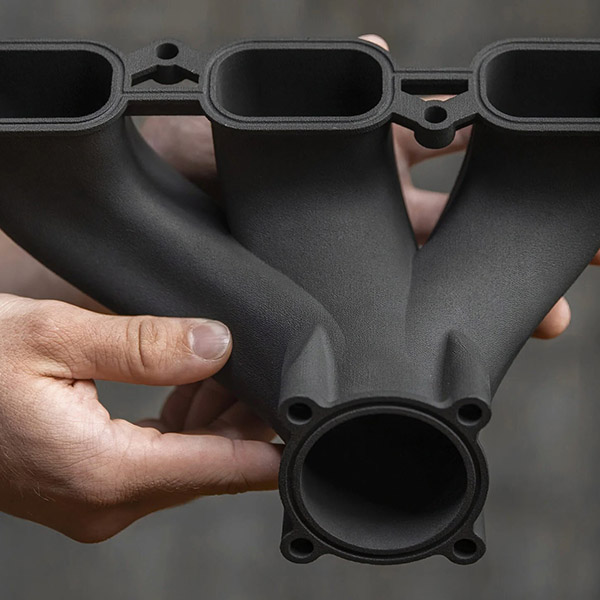
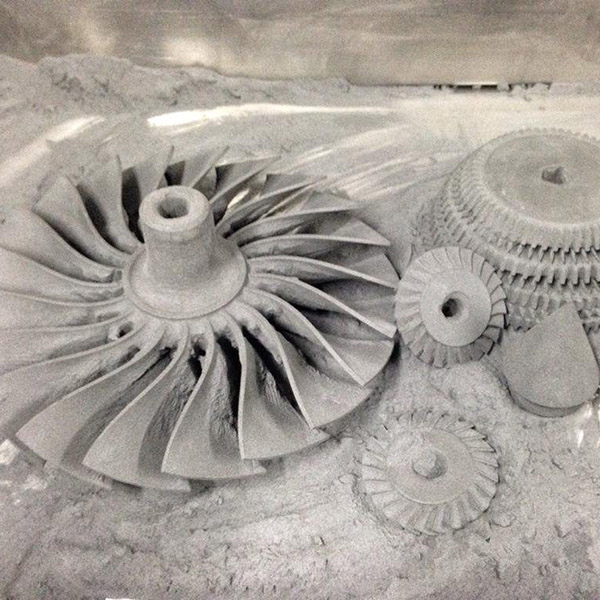
eBook of Definitive Guide for SLS 3D Printing
We complied comprehensive insights and best practices for optimizing part design, material selection, and post-processing to achieve the highest quality and performance to be an eBook. Complete the form below to get the eBook.
Surface Finishing Options for SLS Parts
Options | Description | Colors |
---|---|---|
Dyeing | Reaches all surfaces of a part, including the most inaccessible recesses, resulting in a very uniform finish. | Black, RAL/Pantone colors |
Painting | A well-known way to add colors and hide print lines. | Black, RAL/Pantone colors |
Polishing | It is commonly used to improve the appearance of a part, prevent contamination, eliminate oxidation, create a smooth surface, or protect against corrosion. | - |
Spray Painting | A quick way to color parts, reaching areas that cannot be reached with a brush. | Black, RAL/Pantone colors |
Vapour Smoothing | See Details from Below | - |
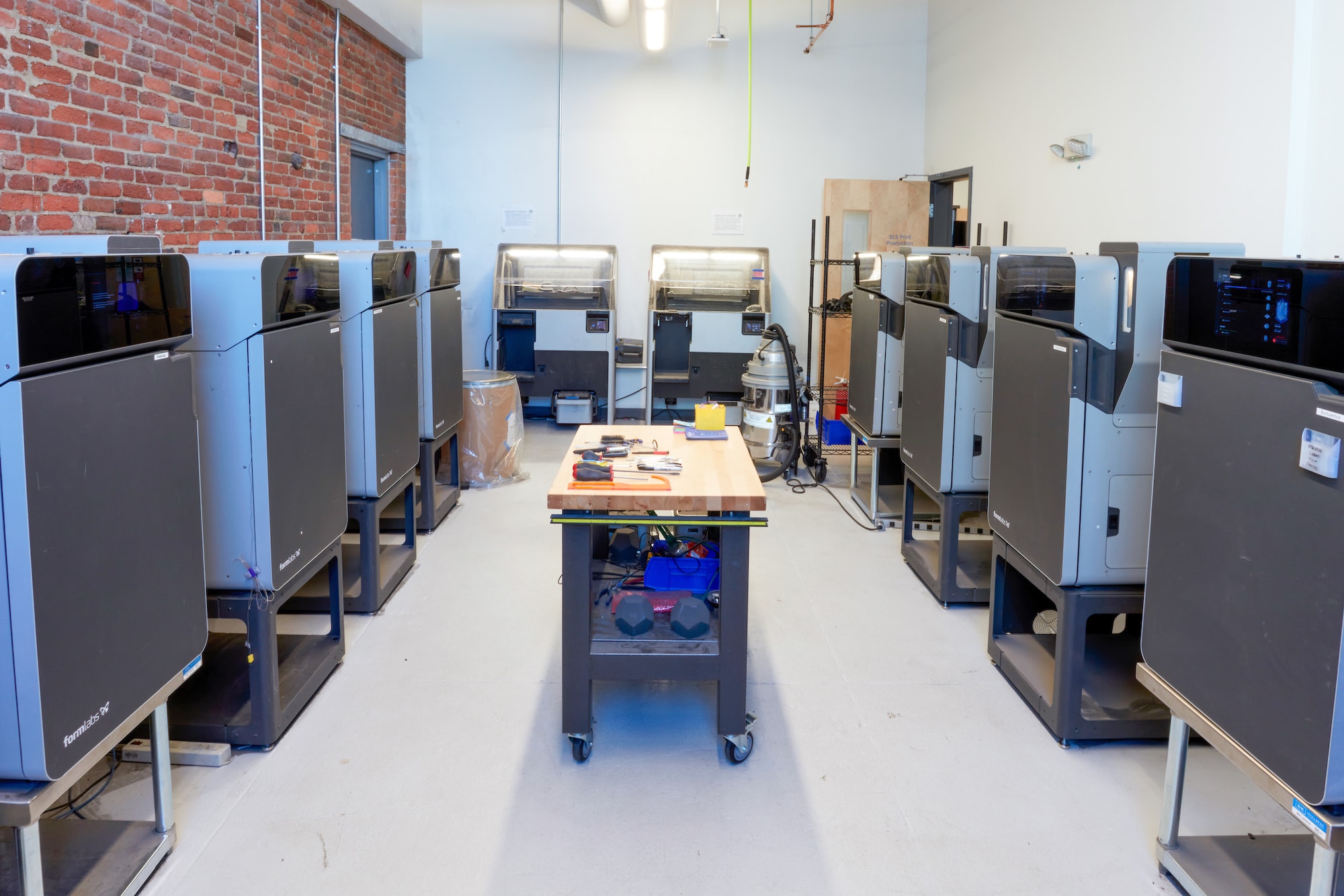
Our SLS Printers
At KingStar Mold, we are committed to delivering the highest quality parts through cutting-edge technology. To ensure precision, durability, and exceptional results, we utilize top-tier SLS 3D printers from Formlabs and 3D Systems.
The Formlabs Fuse 1 provides an accessible yet powerful solution for creating high-performance parts with its reliable powder handling and seamless print capabilities, perfect for both prototyping and low-volume production. Meanwhile, 3D Systems’ ProX 500 offers industrial-grade performance with its advanced materials and high-resolution prints, making it the ideal choice for demanding applications requiring exceptional detail and accuracy.
With these state-of-the-art machines, we can produce intricate, durable, and functional parts tailored to your needs, all while maintaining the highest standards of quality and efficiency.
Design For SLS 3D Printing
When designing for SLS 3D printing, it’s crucial to account for material properties and part orientation to ensure optimal strength and functionality. Aim for uniform wall thickness (around 1-3 mm) to avoid weak spots and ensure even sintering. Additionally, incorporate design features like rounded corners and chamfers to improve the printability and reduce stress concentration during the sintering process. See more Details from below.
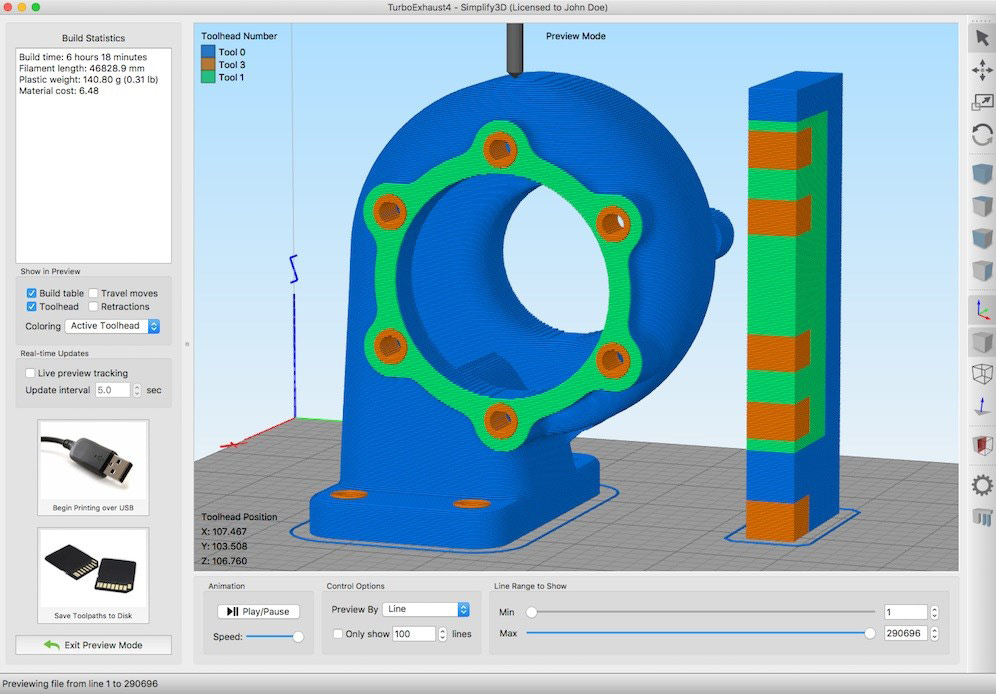
Advantages of Choosing SLA 3D Printing
High Precision and Detail
SLS 3D printing produces highly accurate parts with fine details and complex geometries that are difficult to achieve with traditional manufacturing methods. It’s ideal for prototyping and low-volume production of parts with intricate designs. The precision allows for functional prototypes that closely resemble the final product.
Strong and Durable Materials
SLS offers a wide range of robust materials like nylon and glass-filled nylons, which provide excellent mechanical properties and wear resistance. These materials are ideal for parts that require high strength, flexibility, and heat resistance. SLS-printed parts are well-suited for demanding industries like automotive, aerospace, and medical.
Rapid Turnaround and Prototyping
SLS is well-known for its speed, offering quick turnaround times for prototypes and low-volume production parts. The technology enables fast iterations of designs, helping engineers and designers test and refine parts in a fraction of the time compared to traditional methods. This makes it an efficient solution for accelerating product development.
No Support Structures Required
SLS 3D printing stands out by eliminating the need for traditional support structures, as the surrounding powder provides natural support during the printing process. This advantage opens up greater design possibilities, enabling the creation of intricate shapes, hollow sections, and internal features that would be challenging with other methods. Additionally, it streamlines production by reducing the need for extra post-processing steps, saving both time and costs.
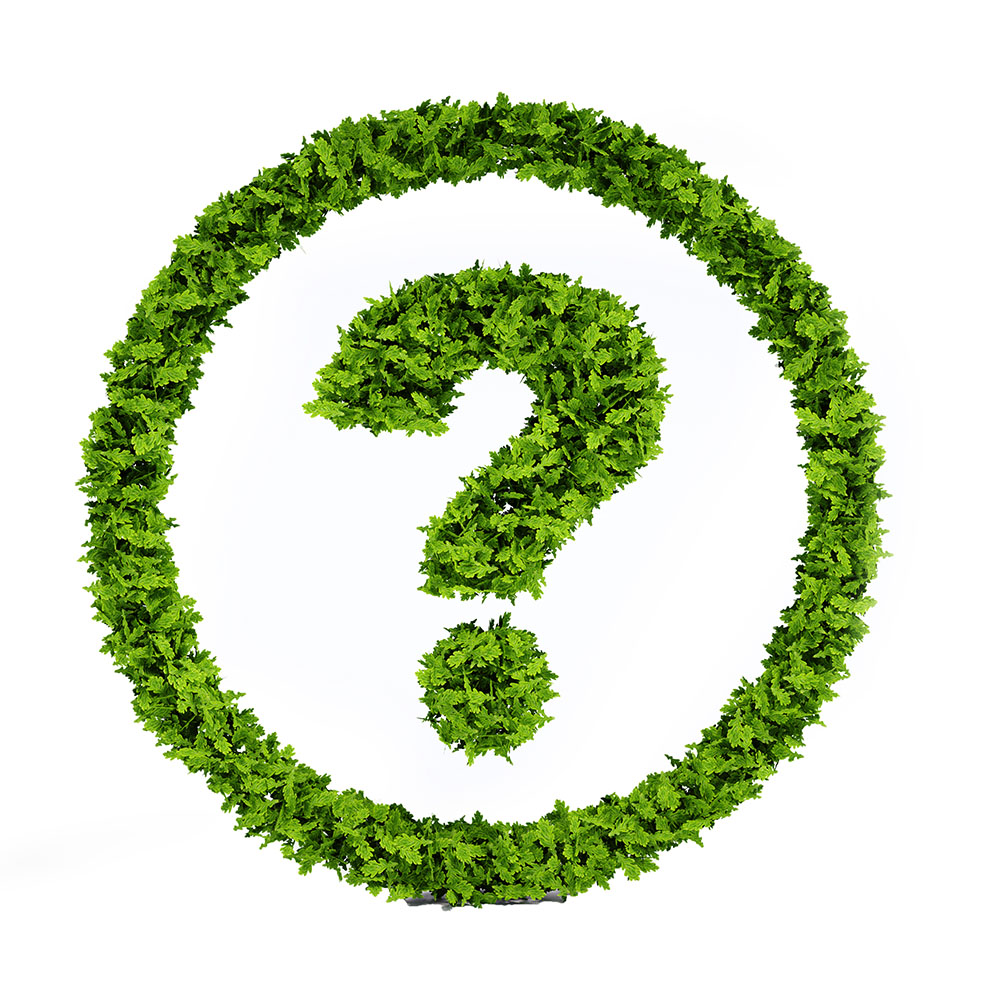
SLS 3D printing offers high accuracy, with tolerances typically ranging from ±0.10 mm for larger parts to ±0.02 mm for small, intricate features. KingStar Mold ensures precise prints with advanced equipment and expert technicians to deliver parts that meet tight specifications.
SLS 3D printing commonly uses nylon-based powders, glass-filled nylons, and thermoplastic materials like TPU. These materials are chosen for their strength, durability, and flexibility. KingStar Mold offers a variety of materials to meet specific project requirements, ensuring the right material for your application.
SLS offers high precision, the ability to create complex geometries, and the use of durable materials. The process eliminates the need for support structures and allows for faster prototyping, making it an ideal choice for engineers looking for detailed, functional parts. KingStar Mold specializes in delivering these benefits efficiently for our customers.
Selective Laser Sintering (SLS) is an additive manufacturing process that uses a laser to sinter powdered material, layer by layer, to create durable and detailed parts. At KingStar Mold, we use this technology to produce high-performance parts suitable for various industries, from automotive to medical.
Getting started with SLS 3D printing at KingStar Mold is easy. Simply contact us with your part specifications, and our team will guide you through the design and production process. Whether you need a prototype or low-volume production, we’ll provide the best solution to meet your needs.
Yes, SLS parts often require some post-processing, such as cleaning the powder and smoothing surfaces. However, since SLS does not require support structures, the process is generally quicker and more cost-effective than other 3D printing methods. KingStar Mold offers comprehensive post-processing services to ensure your parts are finished to perfection.
SLS 3D printing can produce parts quickly, with lead times as short as 1 to 3 days, depending on the complexity of the design. This makes it an efficient choice for rapid prototyping and short-run production. KingStar Mold ensures timely delivery without compromising on quality.
SLS is ideal for producing functional prototypes, complex geometries, and low-volume production parts. It excels at creating strong, durable parts for industries like aerospace, automotive, and medical. At KingStar Mold, we provide tailored SLS solutions to meet diverse customer needs.