When choosing the right cooler, it’s not just about the size or color. You’ve probably heard brands and manufacturers mention terms like “rotomolded” and “injection molded,” and you might be wondering what exactly they mean in terms of the cooler’s construction and performance.
As a leading hard cooler manufacturer in China, we break down the differences between rotomolded and injection molded coolers in this post. We’ll explain how each is made, what that means for durability and performance, and which option might best suit your needs, whether you’re outfitting an adventure or sourcing for business purposes.
- 1. Understanding the Manufacturing Processes
- 2. Structural Differences
- 3. Insulation & Ice Retention
- 4. Durability in Real-World Use
- 5. Weight & Portability
- 6. Design & Aesthetics
- 7. Production Cost & Retail Price
- 8. Environmental Impact
- 9. Which Cooler Is Right for You?
- 10. Why KingStar Mold Rotomolded Coolers Stand Out
- Conclusion
1. Understanding the Manufacturing Processes
Before we can compare performance, let’s start at the beginning—how these coolers are made. The manufacturing process plays a direct role in how durable, insulated, and reliable a cooler will be in the wild (or in your backyard).
Rotational Molding (Rotomolding)
Rotomolding, short for rotational molding, is a slow but precise method used to produce rugged, high-performance coolers.
In rotomolding, powdered polyethylene resin is added to a hollow mold, which is then heated and slowly rotated on two axes. As the mold rotates, the softened resin evenly coats the interior walls, building up thickness with every turn. Once cooled, the result is a single seamless piece with consistent wall thickness throughout.
This method creates coolers with extra-thick walls and no weak points—no seams, no glue, and no fusing required. It’s also ideal for reinforcing corners and stress points, making the cooler incredibly impact-resistant. That’s why most premium outdoor coolers use this method.
Injection Molding
Injection molding, on the other hand, is a faster and more cost-efficient method typically used for producing lightweight, consumer-grade coolers.
In this method, melted plastic is injected into a steel mold under high pressure. The mold is usually in two parts—one for the top shell and one for the bottom. After cooling, the two pieces are joined together with insulation filled in between. It allows for quick production and detailed exterior shapes. However, the process introduces seams and thinner walls compared to rotomolding. These coolers are lighter and less expensive to produce, but also generally less rugged and insulating.
2. Structural Differences
Now that we understand how each cooler is made, let’s look at how the structure of these coolers affects their durability and performance in the real world.
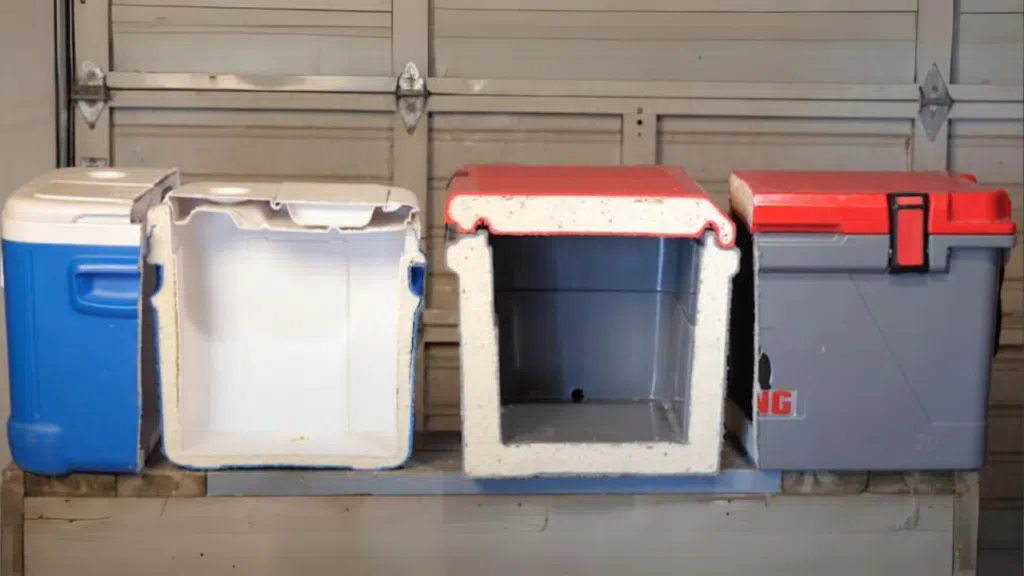
Rotomolded
- Seamless, One-Piece Shell with Thick Walls and Reinforced Corners: Rotomolded coolers are built as a single, continuous piece, meaning there are no seams that could separate or crack over time. The thick, uniform walls provide excellent insulation and strength. This one-piece design ensures that even the corners, often the most vulnerable part of a cooler, are reinforced for extra durability.
- Uniform Insulation with Fewer Weak Points: The process of slow rotation during manufacturing allows for consistent thickness of insulation all around the cooler. This eliminates weak points that could affect temperature retention, keeping your ice and drinks colder for longer.
Injection Molded
- Two Shells Joined with Insulation in Between: Unlike rotomolded coolers, injection-molded coolers are made of two separate pieces—the top shell and bottom shell—that are joined together with insulation in between. While this can provide decent insulation, the seams where the two shells are fused are potential weak spots where the cooler could crack or break, especially under stress.
- Visible Seams and Potential Stress Points: These seams not only affect the structural integrity of the cooler but can also compromise its ability to retain cold over long periods. For example, over time, the edges where the two parts meet may loosen, allowing warm air to seep in or cool air to escape.
3. Insulation & Ice Retention
One of the most important factors when choosing a cooler is how well it can retain ice and keep your drinks cold. Let’s break down how the two manufacturing methods compare in terms of insulation and ice retention.
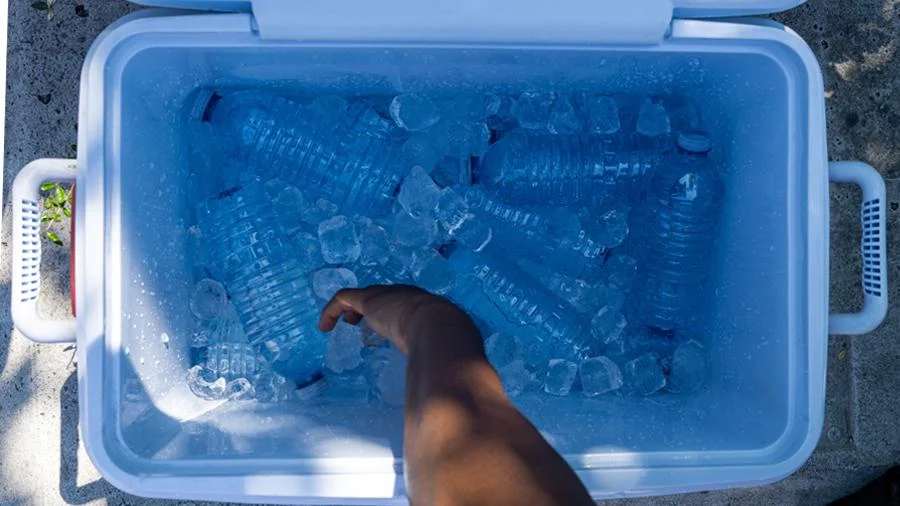
Rotomolded Coolers
- Thicker Walls (Often 2–3 Inches): Rotomolded coolers are typically designed with thicker insulation walls, often ranging from 2 to 3 inches. This extra thickness provides superior temperature retention, ensuring that your ice stays frozen for days.
- Better Ice Retention (7–10 Days): Due to the thicker walls and seamless construction, rotomolded coolers are built for long-term ice retention. In fact, many high-quality rotomolded coolers can keep ice intact for up to 7 to 10 days, making them ideal for long trips, outdoor adventures, and weekend getaways.
Injection Molded Coolers
- Thinner Insulation: On the other hand, injection molded coolers typically have thinner insulation. While this can still provide some cooling power, it often doesn’t compare to the thickness and consistency of rotomolded insulation.
- Shorter Ice Retention (1–3 Days): Because of the thinner walls and the dual-shell design, ice retention in injection molded coolers tends to be less impressive. Most injection molded coolers can keep ice for about 1 to 3 days, which is suitable for short day trips but not for extended camping or fishing adventures.
4. Durability in Real-World Use
Durability is a key factor when choosing a cooler, especially if you plan on using it in rough environments. Whether you’re hiking, tailgating, or embarking on a week-long camping trip, the durability of your cooler matters. Let’s compare the toughness of rotomolded vs injection molded coolers.
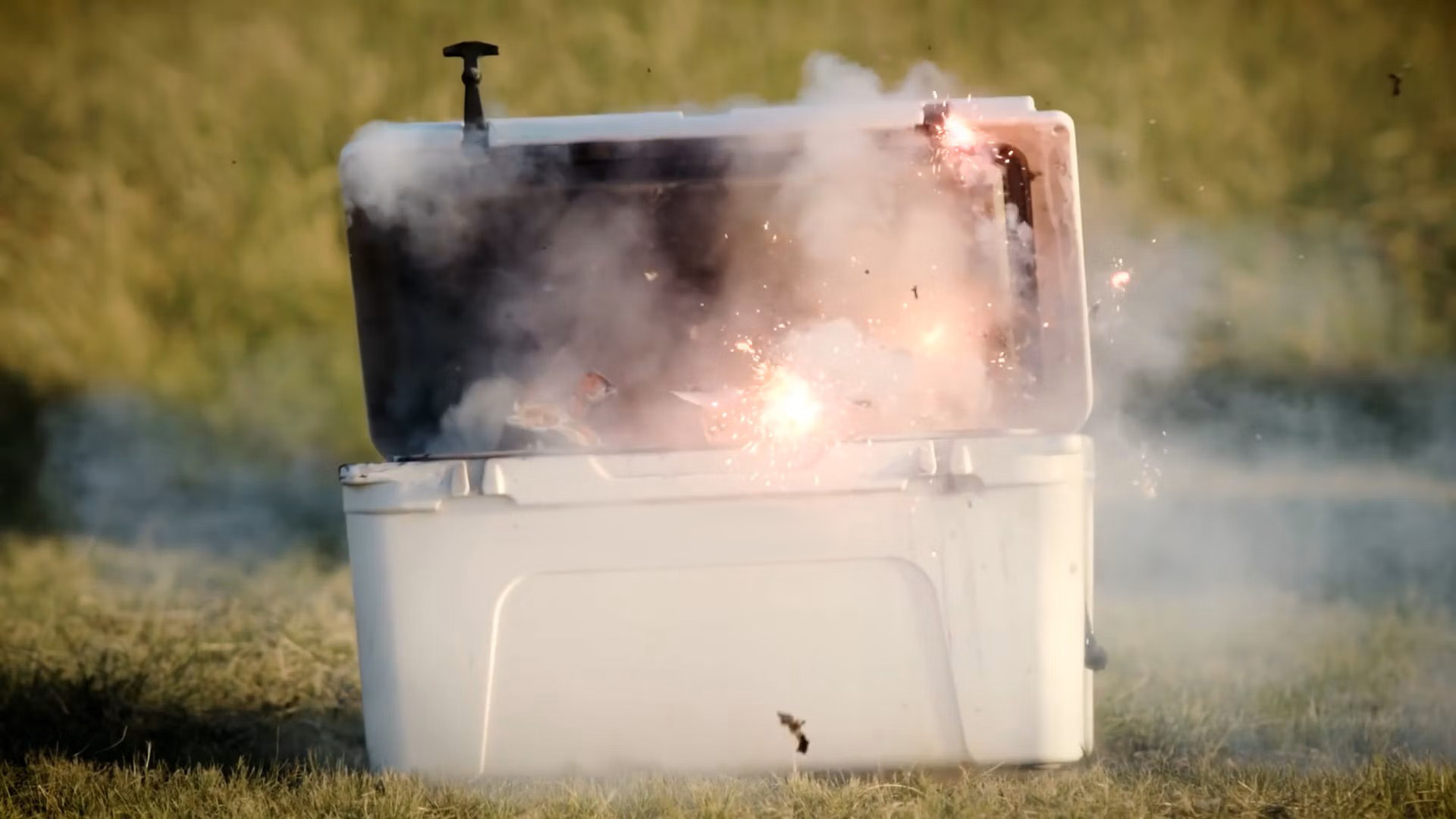
Rotomolded Coolers
- Impact-Resistant: Rotomolded coolers are highly impact-resistant due to their single-piece, seamless construction. Whether dropped or knocked around, these coolers can withstand rugged environments without significant damage.
- Less Prone to Cracking: Thanks to the thicker walls and reinforced corners, rotomolded coolers are less prone to cracking under heavy loads or stress. They’re built to last, even when exposed to extreme conditions.
Injection Molded Coolers
- Adequate for Casual Use: Injection molded coolers are adequate for everyday, casual use, such as picnics, short trips, or sporting events. However, they are more susceptible to breakage over time when subjected to heavy impacts or harsh environments.
- Handles & Hinges May Loosen: Over time, the handles and hinges of injection molded coolers may start to loosen. This is because of their two-piece construction, which can create weak points where stress is applied, making them more prone to wear and tear.
5. Weight & Portability
When choosing a cooler, weight and portability are critical factors, especially if you plan on carrying it for long distances or through rugged terrain. Let’s break down how rotomolded and injection molded coolers differ in this area.
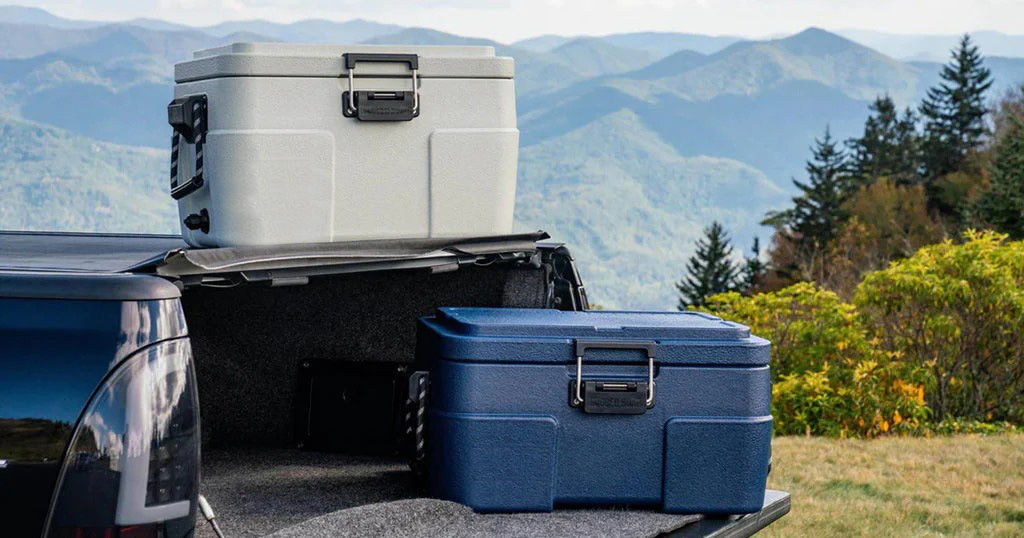
5.1 Injection Molded vs. Rotomolded Coolers
Injection molded coolers are generally lighter because of their thinner walls and dual-shell construction. This makes them easier to carry, particularly for solo adventures or quick trips where weight is a concern. If you’re looking for something to take on a short hike or day trip, an injection molded cooler is a great choice.
On the flip side, rotomolded coolers tend to be heavier due to their thicker walls and single-piece construction. While the weight can be a drawback for portability, they often come equipped with stronger handles and better grips, making them easier to carry despite the added weight. This durability makes them a solid choice for group camping or extended trips where the cooler needs to endure a lot of handling.
5.2 Use-Case Tradeoffs
Solo Adventures vs Group Camping: If you’re traveling solo or with a small group, weight might be a major consideration. For these trips, injection molded coolers could be ideal because of their lighter weight. However, if you’re going on a group camping trip and need a cooler that can handle more rigorous conditions while carrying more gear, rotomolded coolers provide the durability you’ll need, despite their heavier build.
6. Design & Aesthetics
When it comes to choosing a cooler, design and aesthetics can play a big role in your decision-making process. Do you prefer a sleek, modern cooler that blends into your gear, or do you want something that looks tough and ready for any challenge? Here’s how the designs of rotomolded and injection molded coolers stack up.
Injection Molded Coolers: Varied Colors & Sleek Design
Injection molded coolers are known for their variety in color options and often have a sleeker, more streamlined design. This makes them a popular choice for those who want a cooler that not only performs well but also looks aesthetically pleasing. These coolers are often available in a range of colors and designs, catering to different styles and preferences.
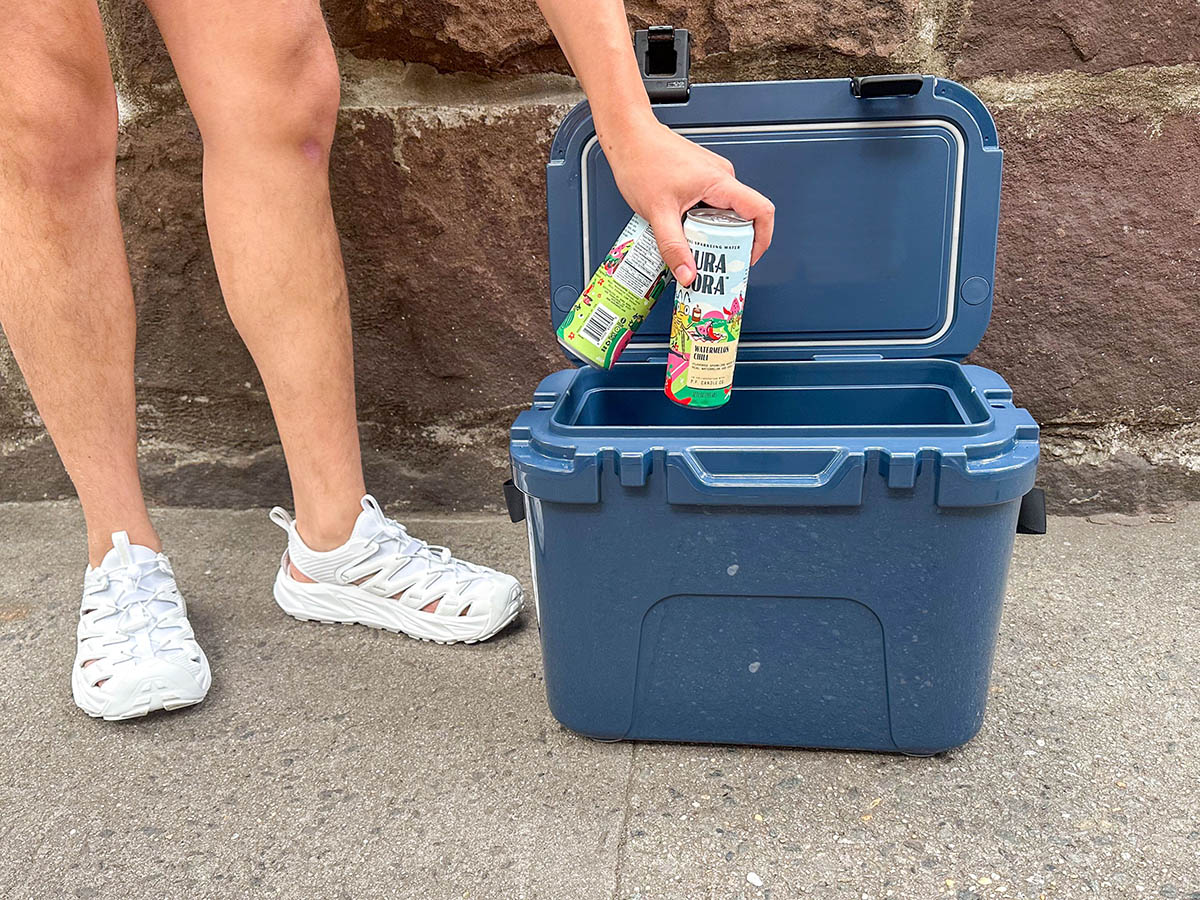
Rotomolded Coolers: Rugged and Industrial
In contrast, rotomolded coolers tend to have a rugged, industrial look. Their design is all about function over form, and they usually feature a more purpose-driven aesthetic. These coolers are often bulkier and have a more “workhorse” appearance, which suits their durability-focused nature. Think outdoor adventures and heavy-duty use—rotomolded coolers are built to look the part.
Both types of coolers have incorporated innovative features, but rotomolded coolers often come with extra built-in functionalities like molded cup holders, tie-down slots, and non-slip feet. These added features enhance usability, particularly in outdoor and rugged environments where you need your cooler to be as functional as it is durable. Injection molded coolers may have these features too but tend to focus more on compactness and convenience.
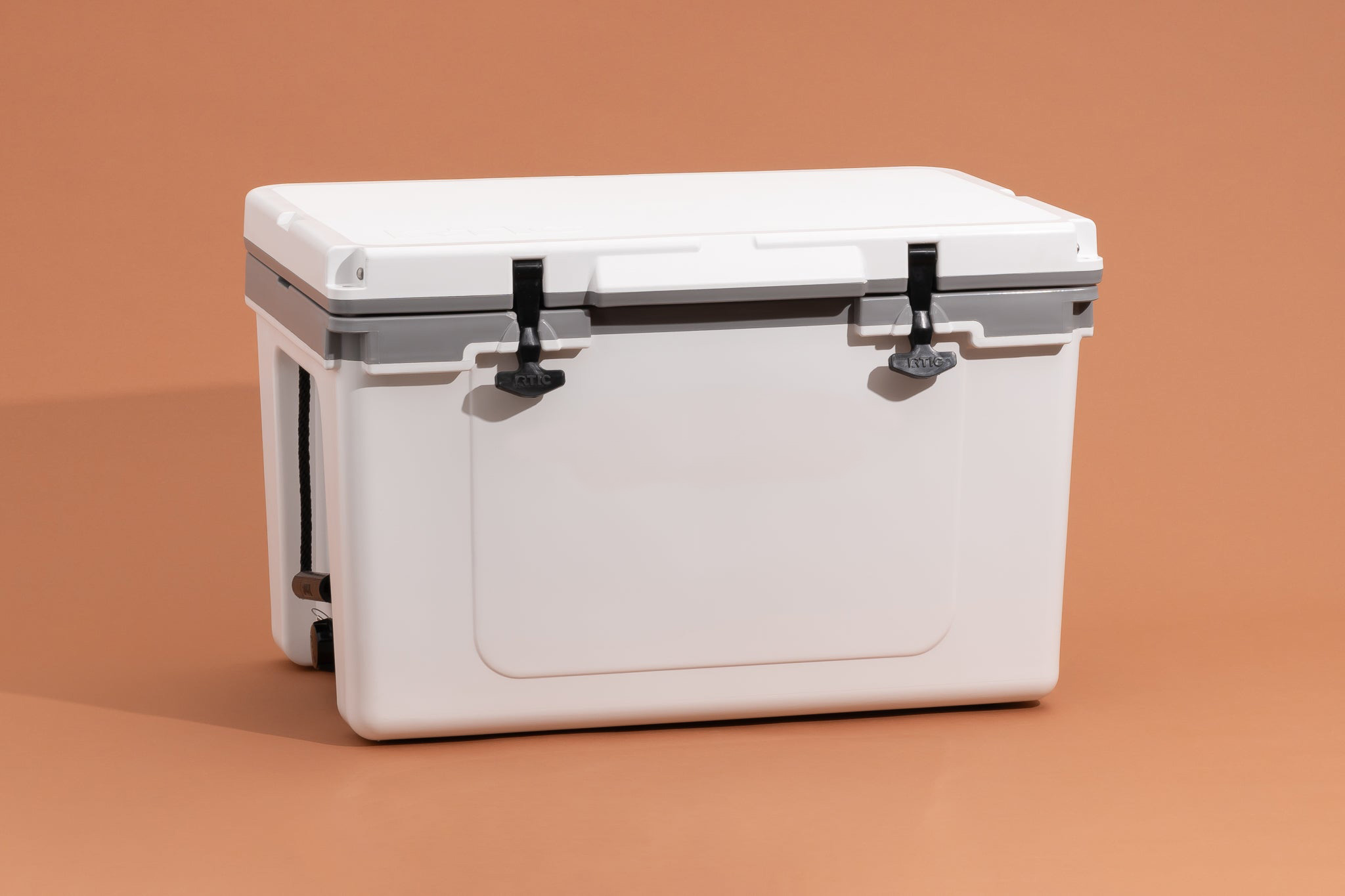
7. Production Cost & Retail Price
When it comes to rotomolded and injection molded coolers, the production cost is a crucial factor to consider. It influences not only the price of the cooler but also the overall value you get from the product. Understanding the manufacturing processes behind each cooler type helps explain their cost differences and why you might choose one over the other.
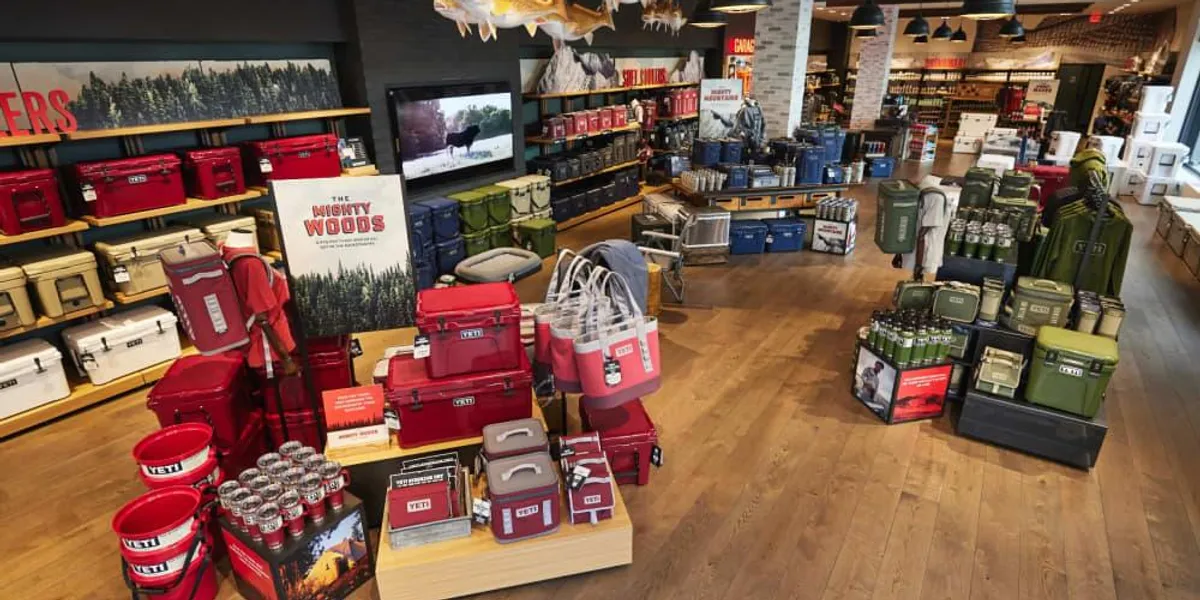
7.1 Injection Molding vs. Rotational Molding
Injection Molding
- Cheaper to Produce: Injection molding is typically a more affordable process compared to rotomolding, largely because of the faster cycle times and lower material waste. In this process, plastic is melted and injected into a mold at high pressure, forming the cooler’s shape. This repetitive process allows manufacturers to create large quantities of coolers quickly, reducing the cost per unit.
- Mass Production Efficiency: The molds used in injection molding are made from durable materials, and they can be reused many times without significant degradation. This scalability means that manufacturers can produce a large volume of coolers without significant increases in cost, making them ideal for mass production. The relatively low per-unit cost of these coolers enables companies to sell them at lower retail prices, catering to a larger market.
- Economic for Lightweight Coolers: Injection molding is best suited for producing lightweight coolers, which require less material and less labor-intensive molding. Since the focus is often on creating budget-friendly, mass-market coolers, the price to the consumer tends to be lower. However, this comes with trade-offs in terms of durability, insulation, and performance, as thinner walls are used to save on material costs.
Rotomolding
- Higher Upfront Cost: The rotational molding (rotomolding) process involves a different set of challenges that increase production costs. First, rotomolding requires heavier, more specialized molds, which are more expensive to manufacture than the molds used in injection molding. The molds also need to be large and capable of withstanding high temperatures. Additionally, the molding process itself is slower—plastic resin is added to the mold, which then rotates on two axes to evenly distribute the material. The slow rotation ensures that the resin adheres to the mold evenly, but this takes more time than the fast injection process.
- Material Usage and Waste: Rotomolding also involves using more material per unit than injection molding, as the process requires thicker walls to ensure strength, insulation, and durability. While this improves the quality of the cooler, it also increases material costs. Additionally, rotomolding can lead to more material waste since it uses larger amounts of plastic compared to injection molding, where more precise amounts can be injected into the mold.
- Long-Term Durability Justifies the Price: The higher material costs and slower production cycle of rotomolding translate to a higher initial cost for rotomolded coolers. However, the superior insulation, durability, and strength of rotomolded coolers make them a long-term investment. Unlike injection molded coolers, which may be prone to cracking or damage from rough handling, rotomolded coolers are known for their resilience and extended ice retention.
7.2 Greater Longevity = Better Value
While rotomolded coolers are typically more expensive upfront, their long-term value makes them an appealing choice for those who prioritize durability and performance. These coolers can last for years and are often used for rugged outdoor activities like camping, fishing, or hunting. In comparison, injection molded coolers, which are cheaper initially, may break down faster under tough conditions, requiring replacement more frequently. Therefore, the higher initial cost of a rotomolded cooler is often justified by its long lifespan and better performance over time.
7.3 Reducing the Cost Gap with Direct-from-Factory Options
One way to bridge the cost gap between rotomolded and injection molded coolers is to purchase from a direct-from-factory supplier like KingStar Mold. By eliminating middlemen, such as wholesalers and retailers, manufacturers can offer premium rotomolded coolers at significantly lower prices. This direct supply model helps reduce the price markup typically added by distributors and resellers, allowing customers to access high-quality coolers without paying the full retail price.
With direct-from-factory options, you can enjoy the durability, superior insulation, and rugged build of a rotomolded cooler, while benefiting from the cost savings that come from bypassing traditional retail markup. This makes KingStar Mold’s coolers an attractive option for those seeking high-performance products at competitive prices.
8. Environmental Impact
Rotomolding
- Lower Environmental Footprint: Rotomolding generally involves fewer volatile chemicals and uses lower-pressure production, making it more environmentally friendly during the manufacturing process. The slow rotation process reduces the likelihood of material waste, contributing to a more sustainable production cycle.
- Health Considerations: Since rotomolding often involves fewer toxic substances, it may also have a lower impact on human health compared to injection molding, which sometimes uses more harmful chemicals in the production of certain plastics.
Injection Molding
- Increased Waste: While injection molding features faster production cycles, it tends to produce more scrap material, which can increase its environmental footprint. The high-precision required for creating intricate parts also leads to more plastic waste compared to the more forgiving rotomolding process.
- Chemical Use: The injection molding process can sometimes involve more harmful chemicals in the plastic melting process, potentially affecting both environmental sustainability and human health over time.
When considering lifecycles, rotomolded coolers tend to have a longer lifespan, which reduces their need for replacement, ultimately contributing to less waste and better overall sustainability. In contrast, injection molded coolers, due to their lighter materials and lower durability, may need replacing more frequently.
9. Which Cooler Is Right for You?
Choosing between a rotomolded and injection molded cooler ultimately depends on your needs—both from a consumer and supplier perspective. Here’s a breakdown to help both buyers and suppliers understand which cooler type best suits their requirements.
9.1 Ideal Consumer User Profiles:
- Choose Rotomolded for:
- Hunting: Rugged, long-lasting, and excellent ice retention for extended trips.
- Boating: Impact-resistant, perfect for rough waters and unpredictable conditions.
- Camping: Extended ice retention and durability for multi-day trips in the wilderness.
- Multi-day Trips: Keep your food and beverages chilled for days without worrying about ice melting.
- Choose Injection Molded for:
- Daily Picnics: Lightweight and easy to carry, great for short trips and casual outings.
- Sports Days: Compact and easy to transport for quick access to refreshments during outdoor games.
- Office Use: Portable and budget-friendly for keeping drinks cold during office hours.
9.2 Supplier Perspective: Considerations for Manufacturers and Wholesalers
When choosing between rotomolded and injection molded coolers, suppliers will need to factor in production efficiency, cost-effectiveness, and customer demand.
Rotomolded Coolers:
- Production Cost: Higher upfront costs due to longer production cycles and more specialized equipment. However, rotomolding offers significant long-term value as it reduces the frequency of replacement or repairs.
- Order Volume: Best suited for larger or bulk orders as it’s a more labor-intensive process.
- Customization: Rotomolding allows for customized designs with fewer limitations on shape and structure, which is ideal for suppliers offering specialized, high-performance products.
- Durability: The durability of rotomolded coolers makes them a favorite for high-end market segments. Suppliers can justify the higher price with long-lasting products.
Injection Molded Coolers:
- Production Cost: Injection molding is cost-effective for mass production with a quick turnaround. This method allows for efficient production of coolers at lower per-unit costs.
- Order Volume: Ideal for smaller orders or large-scale production runs of standard designs. It’s faster and more economical when producing high volumes of simpler designs.
- Customization: While there is some room for customization, injection molding is limited by the need for separate pieces and internal insulation, which may not offer the same level of customization that rotomolding provides.
- Durability: While injection molded coolers can be durable, they are more prone to cracking and breaking over time. This may influence suppliers looking to position their products in value-driven markets.
9.3 Quick Checklist for Buyers
Criteria | Rotomolded Coolers | Injection Molded Coolers |
Insulation | Thick walls (2–3 inches), great for long ice retention | Thinner walls, good for shorter cooling periods |
Size | Larger capacity, ideal for group use or extended trips | More compact, great for personal or small group use |
Weight | Heavier, harder to carry | Lighter, easier to transport |
Budget | Higher upfront cost, better long-term value | Lower cost, more affordable |
Use Frequency | Best for frequent use in rugged conditions | Best for occasional or casual use |
9.4 Pros & Cons for Business Owners
Production Factor | Rotomolded Coolers | Injection Molded Coolers |
Manufacturing Process | Slow rotation in a single mold, uniform resin distribution | Injection into two molds, faster cycle time |
Production Efficiency | Longer cycle time, suitable for low to medium production | Faster production cycle, suitable for large-scale production |
Material Usage | High-quality materials, suited for high-performance coolers | Lighter materials, suited for lightweight coolers |
Production Cost | Higher upfront cost, but better long-term value due to durability | Lower production cost, more suited for mass-market sales |
Product Consistency | Single-piece construction ensures uniform wall thickness and stable structure | Two-part assembly can lead to visible seams and potential inconsistencies over time |
Waste & Environmental Impact | Less waste, low-pressure process, more energy-efficient and environmentally friendly | Potentially more waste, faster cycles, higher environmental impact |
Mold Complexity | More complex mold design, suited for custom, small-batch production | Simpler molds, suited for standardized mass production |
Health & Safety Risks | Fewer harmful substances released, safer for long-term use | More harmful substances may be released, especially during high-temperature injection |
Market Applicability | High-end market, long-term investment, ideal for customers needing durability and specialized products | Low to mid-range market, suited for everyday casual use |
Whether you are a consumer looking for a cooler that can withstand extended trips or a supplier aiming for mass production at competitive prices, the decision between rotomolded and injection molded coolers ultimately boils down to your specific needs. For those who value durability, ice retention, and rugged performance, rotomolded coolers offer significant long-term value. However, for those prioritizing cost-effectiveness and lighter, portable coolers, injection molded coolers make a great choice.
10. Why KingStar Mold Rotomolded Coolers Stand Out
Factory-Direct Excellence
At KingStar Mold, we pride ourselves on offering factory-direct products, cutting out unnecessary middlemen and ensuring that you get the best prices possible without compromising on quality. As a direct manufacturer based in China, we specialize in providing bulk availability of rotomolded coolers, allowing us to handle large orders with fast turnaround times.
Quality Materials & Long-Lasting Insulation
We use only the finest materials and cutting-edge technology in the production of our rotomolded coolers. Our coolers feature thick, durable walls and premium insulation, ensuring they keep your contents chilled for days. This quality craftsmanship makes our coolers perfect for everything from rugged outdoor adventures to long-term storage. You can count on KingStar Mold to provide products that are built to last, making them a reliable choice for both wholesalers and end customers.
Customization & Branding Opportunities
At KingStar Mold, we understand the importance of custom branding in today’s competitive market. That’s why we offer customization options for rotomolded coolers, allowing you to add your logo, color schemes, and unique designs to your products. Whether you’re looking to wholesale coolers with your brand or create OEM options for a specific clientele, we provide flexible solutions tailored to your needs.
By choosing KingStar Mold as your source for rotomolded coolers, you’re not only getting a product of exceptional quality but also the ability to leverage our expertise in customization and bulk production capabilities. Cost-effective, durable, and highly customizable, our coolers are the perfect solution for businesses looking to offer top-tier products with a competitive edge.
Conclusion
When choosing between rotomolded and injection molded coolers, it’s crucial to remember that function dictates form. As a wholesaler, you’re looking for products that meet the needs of a diverse customer base — from outdoor enthusiasts needing rugged durability to those seeking lightweight, cost-effective options for everyday use. Your focus should be on ensuring that the coolers you supply not only align with these varying demands but also offer durability, performance, and long-term value.
Investing in coolers isn’t just about price; it’s about offering products that perform well, have lasting value, and are reliable in real-world use. By considering factors like insulation, durability, and weight, you can provide your customers with the right choice for their needs, enhancing their satisfaction and loyalty.
At KingStar Mold, we specialize in providing premium rotomolded coolers and injection molded options that meet the highest standards of quality and performance. With factory-direct pricing and customizable solutions, we offer the best products for wholesale and OEM purposes, ensuring your business thrives with top-tier products at competitive prices.