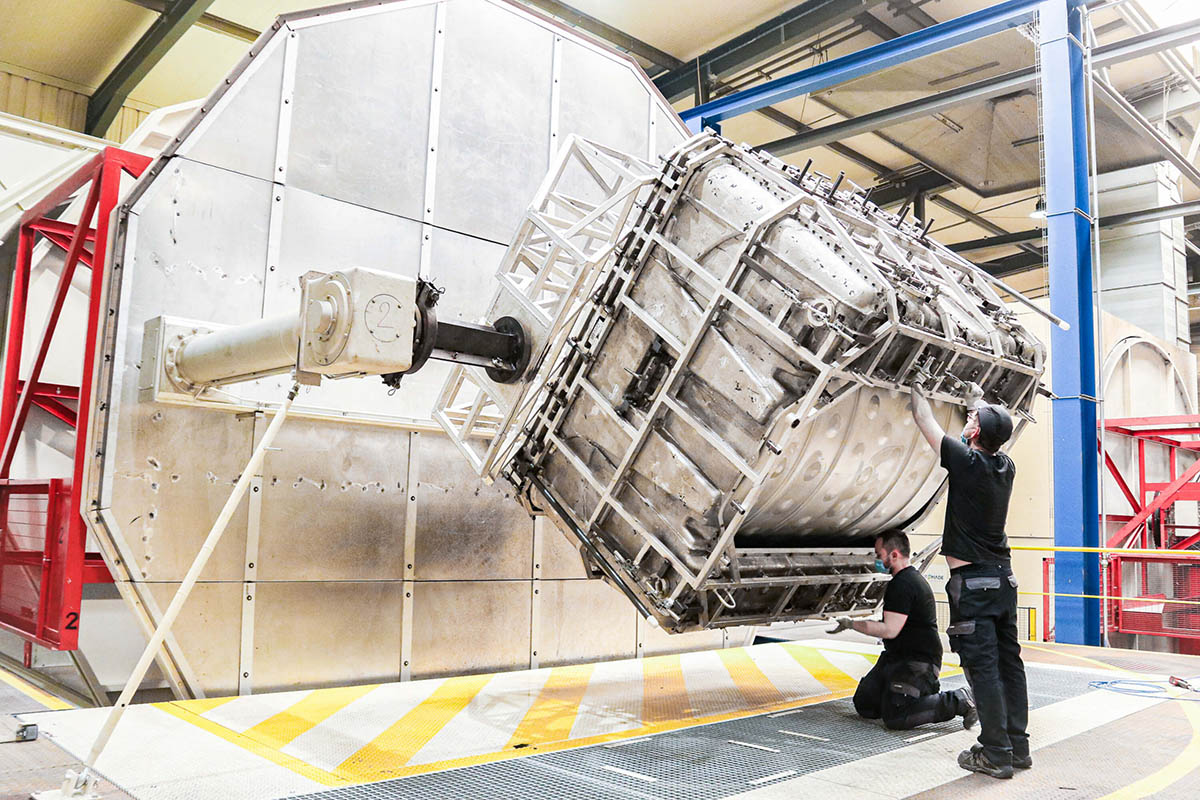
What is rotomolding?
Rotomolding, or rotational molding, is a unique plastic manufacturing process designed to create seamless, hollow parts with exceptional durability and design flexibility. Unlike other molding methods, it uses slow, biaxial rotation and low-pressure heat to evenly distribute powdered resin along the interior of a mold. This produces stress-free components with uniform wall thickness—ideal for everything from industrial tanks and insulated containers to playground equipment and automotive parts.
What sets rotomolding apart is its ability to handle complex shapes, molded-in inserts, and even foam filling for added strength or insulation. The tooling is cost-effective and easy to modify, making it a smart solution for low to medium production volumes, prototyping, or specialty designs. With broad material compatibility and support for custom colors and textures, rotomolding offers manufacturers a powerful combination of versatility, efficiency, and aesthetic freedom.
KingStar Mold’s Rotomolding Services
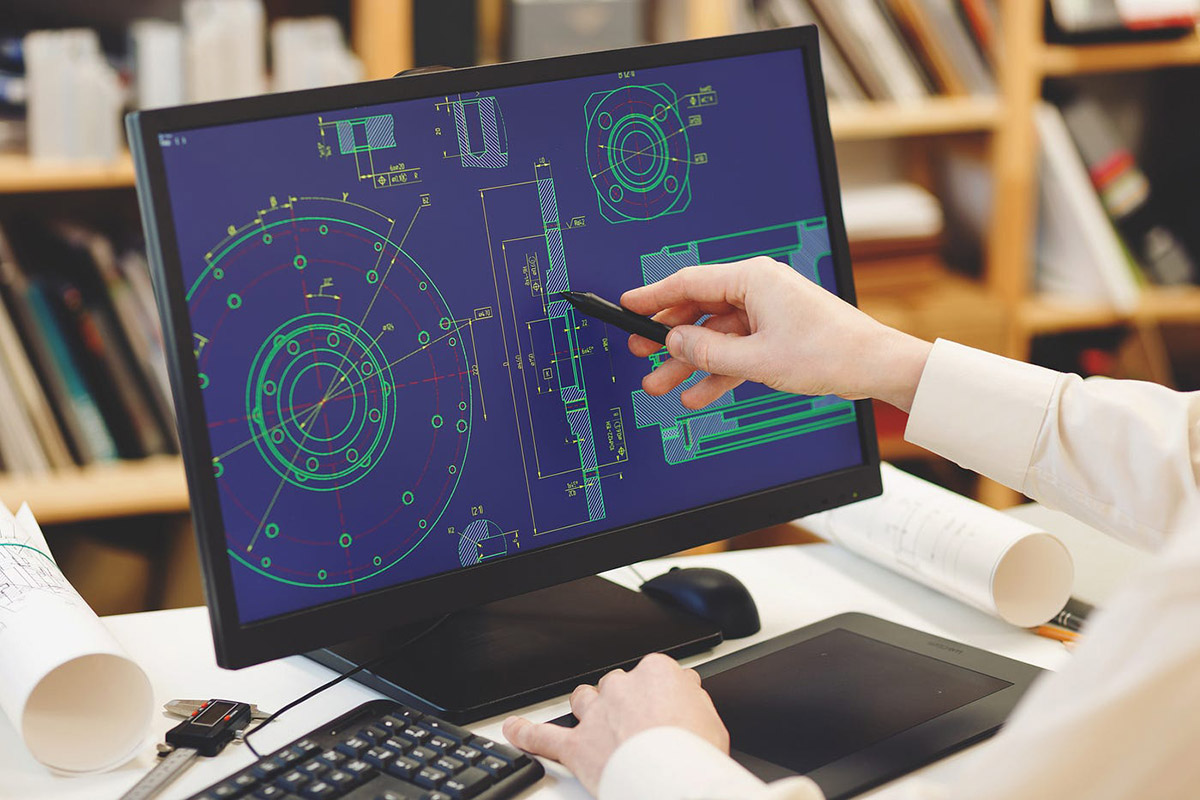
Product Development
Finding the right partner for your rotomolding project is critical. At KingStar Mold, our experienced team supports you from initial concept through 3D design and prototyping. We work closely with you to ensure your product is optimized for the rotational molding process—minimizing risk and maximizing manufacturability at every stage.
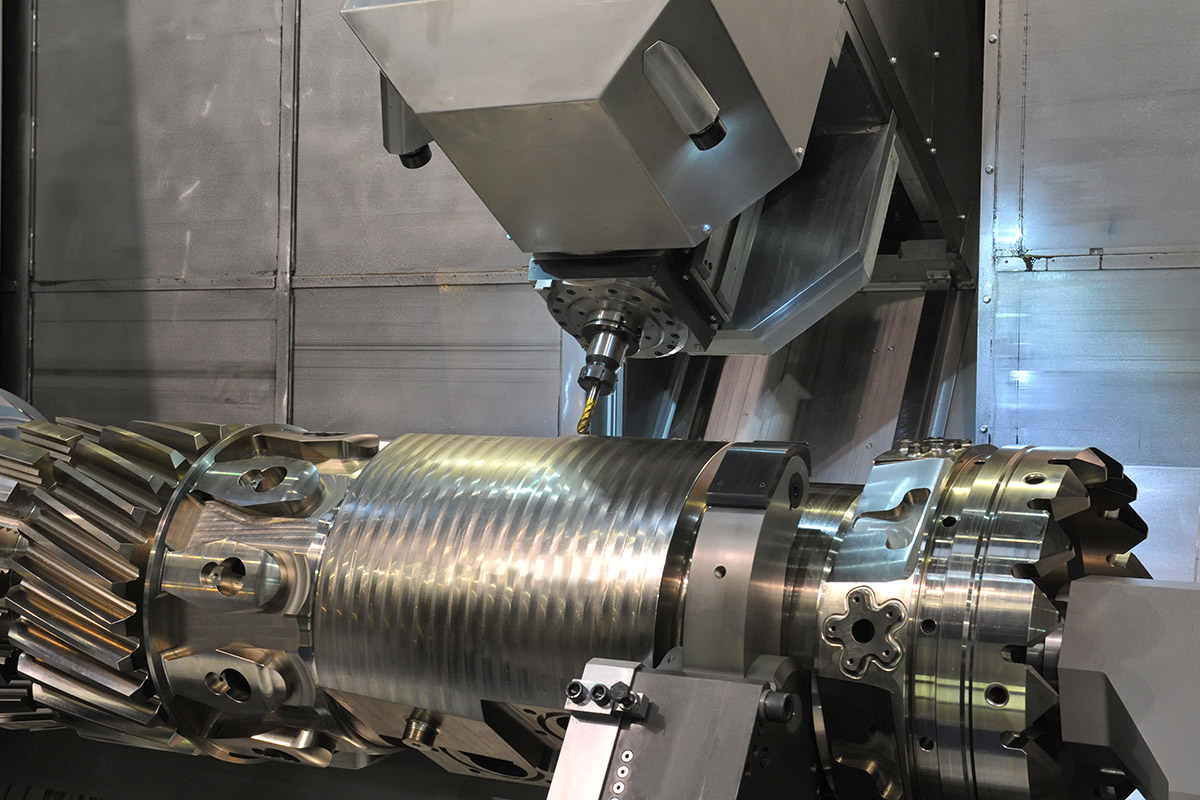
Mold Making
We offer a full range of mold making solutions tailored to your project’s needs. From cost-effective fabricated steel tools to high-precision CNC-machined aluminum molds, our experts help you select the best option based on your production volume, part complexity, and budget—ensuring durability and consistent performance.
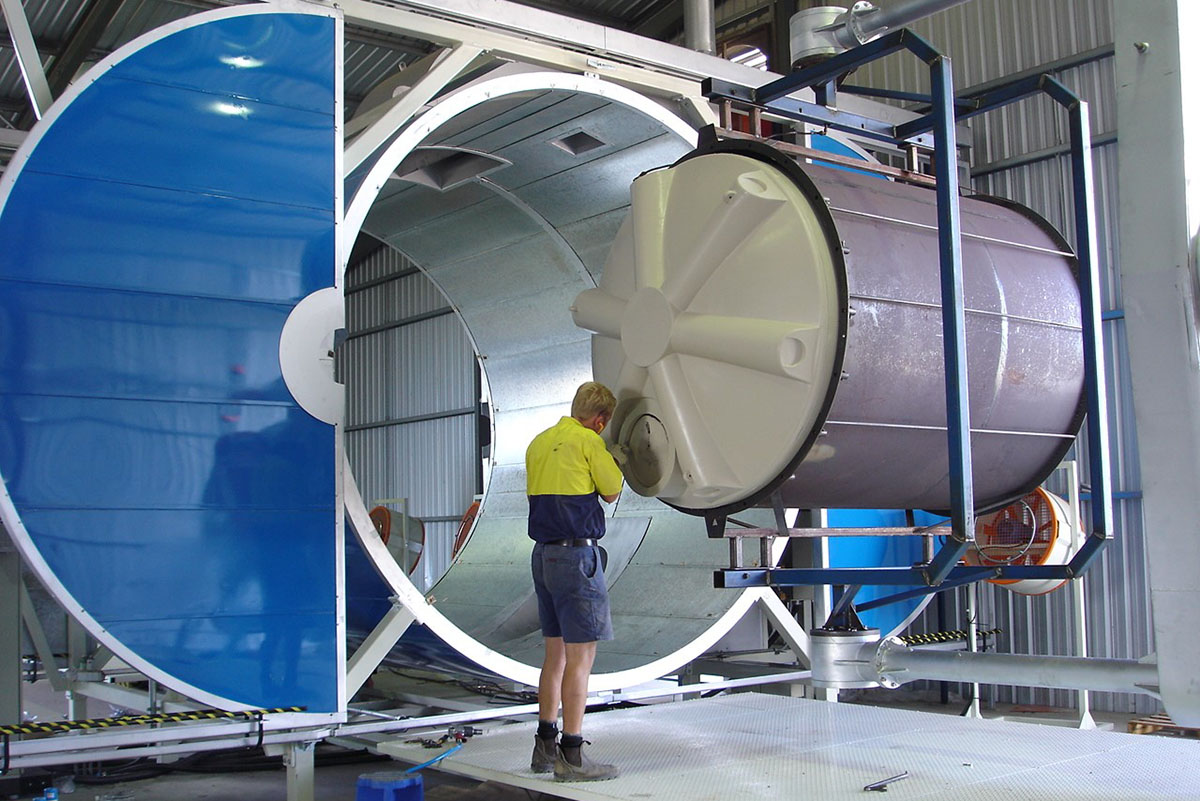
Rotational Molding
KingStar Mold is equipped to handle production runs from 50 to 20,000 units annually. Utilizing lean manufacturing techniques, we deliver high-quality molded parts efficiently while meeting your specific assembly and post-production requirements. Our process supports a wide variety of shapes, sizes, and material specifications.
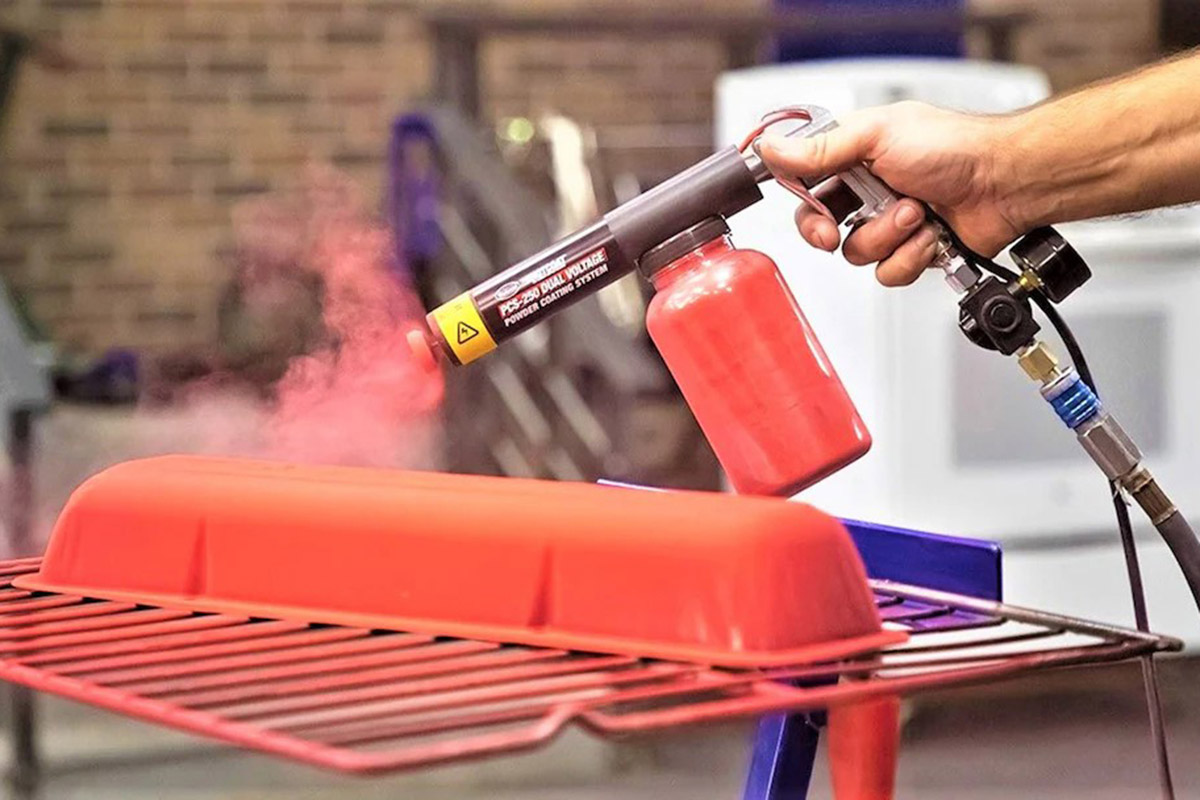
Post-Processing Services
Beyond molding, we provide a full suite of post-processing capabilities, including trimming, CNC finishing, insertion of hardware, assembly, and custom labeling. These value-added services allow you to receive fully finished parts ready for market or further integration.
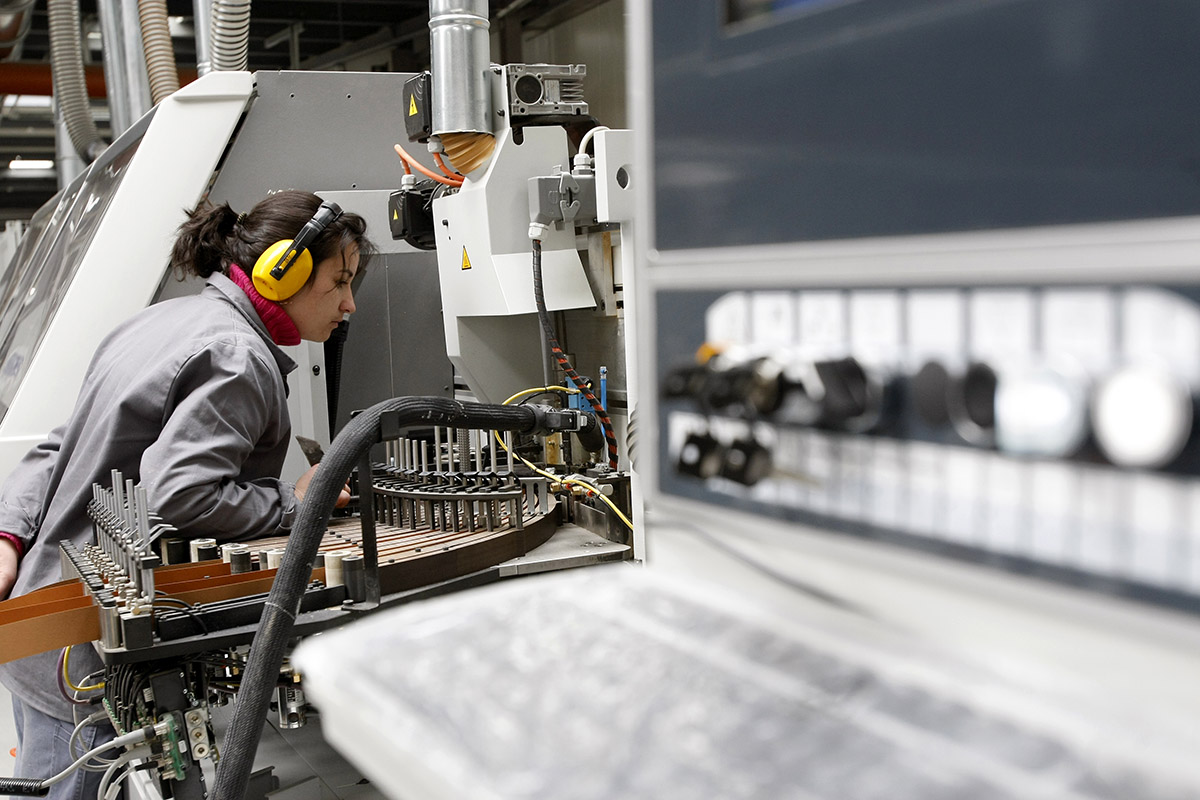
Quality Management
Quality is central to every step of our process. Our quality control system includes material verification, in-process inspections, and final dimensional checks to ensure each part meets your exact specifications. From prototype to full production, we are committed to delivering dependable, high-quality results.
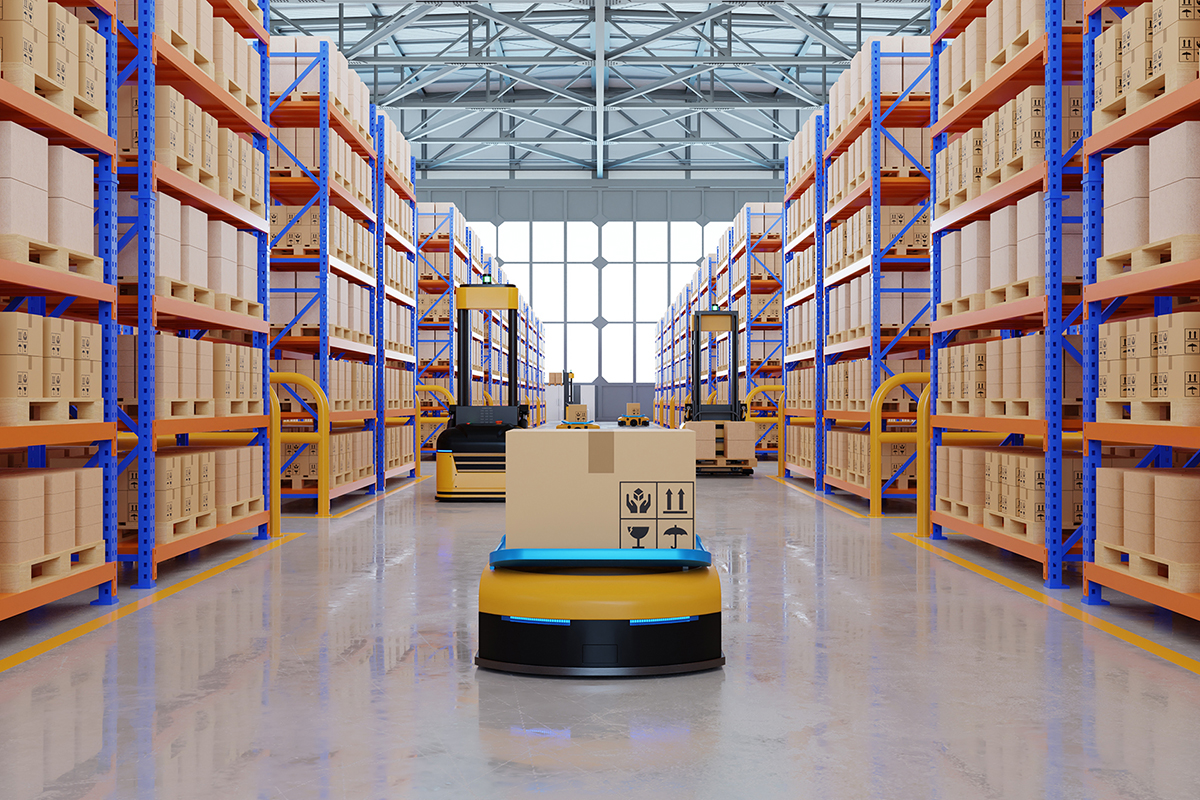
Warehousing & Logistics
With a 30,000 sq. ft. facility and covered outdoor storage, KingStar Mold offers secure warehousing for tools, components, and finished goods. We also support blanket order fulfillment and sub-assembly storage. Our logistics network—backed by in-house transportation and trusted 3PL partners—ensures on-time delivery at competitive rates.
Benefits of Rotomolding
Commonly Used Materials in Rotomolding
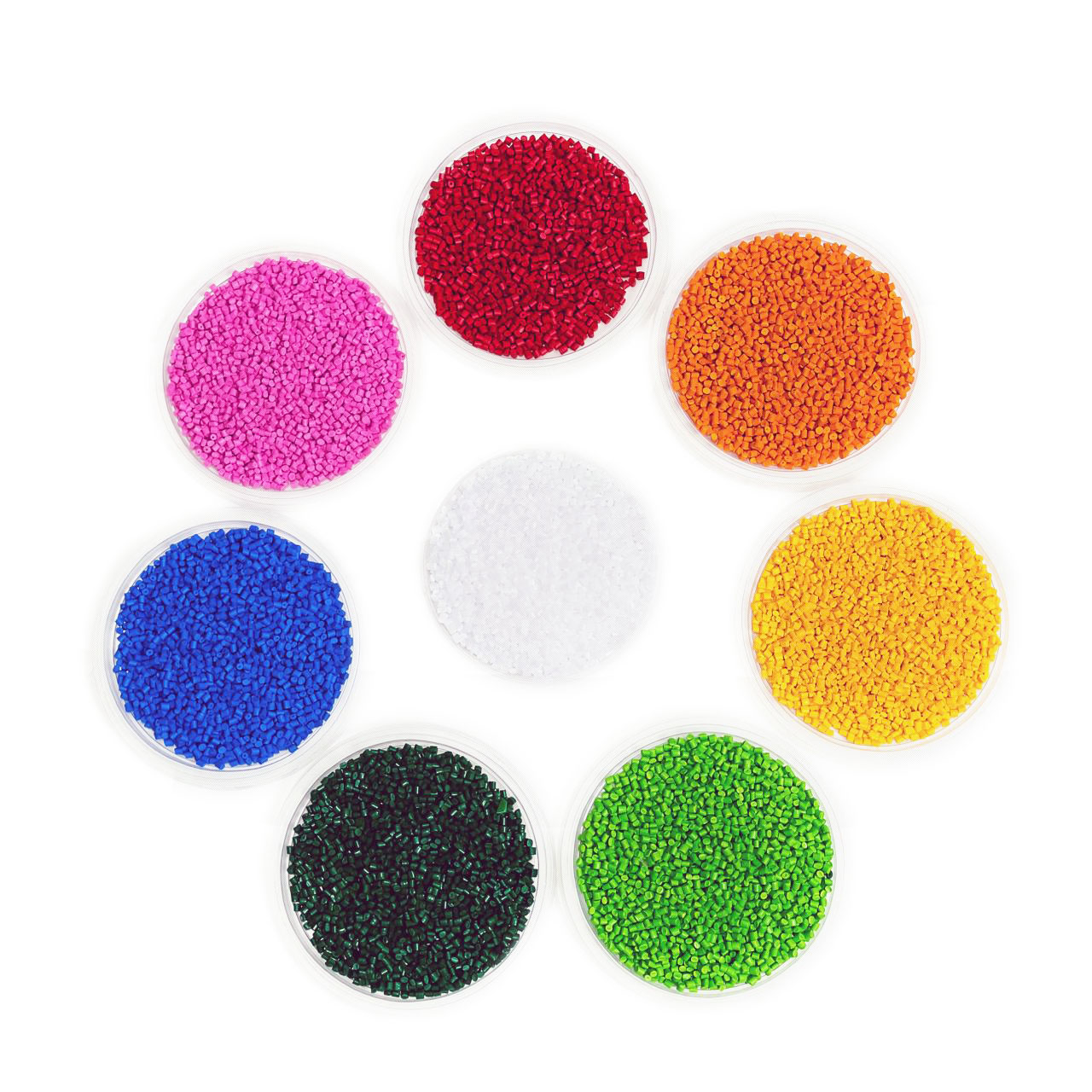
Resins
Material selection is driven by the mechanical and environmental needs of the final part. KingStar Mold frequently works with a broad range of thermoplastics, including LLDPE, MDPE, HDPE, XLPE, Repro, PVC, PP, Acetal, Hytrel, Soft Touch materials, and Nylene 494. Each resin type offers distinct advantages in impact strength, chemical resistance, UV stability, and flexibility.
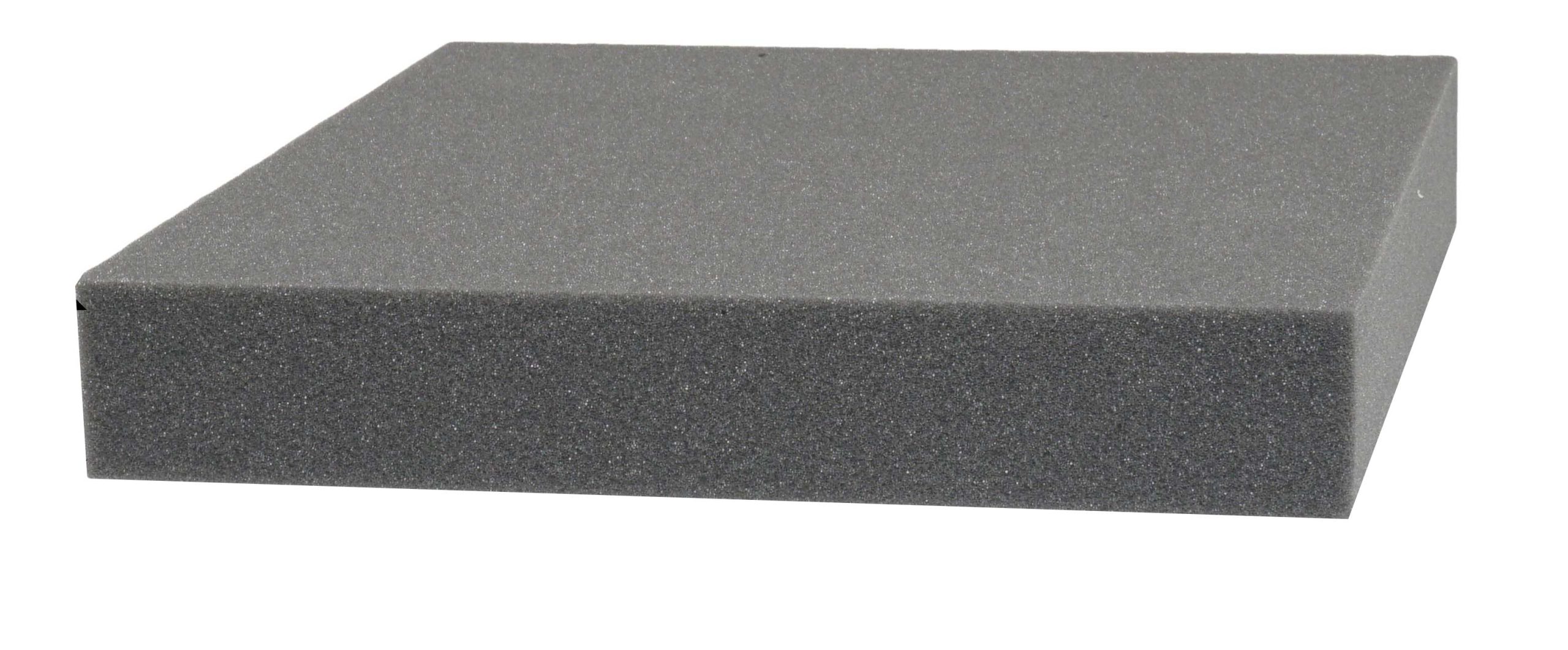
Polyurethane Foam Filling
Polyurethane foam is added inside hollow parts to provide thermal insulation, structural support, noise dampening, or improved rigidity. It’s ideal for applications like coolers, tanks, and industrial housings.
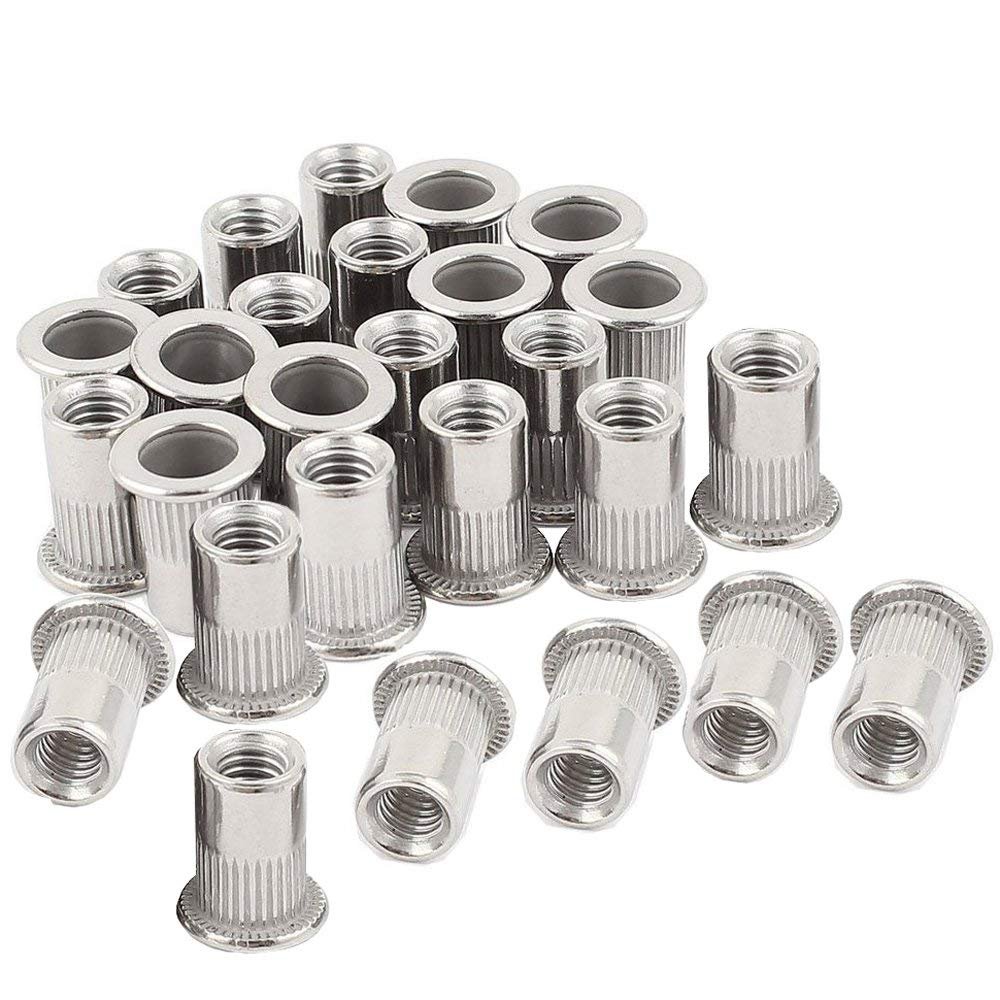
Inserts, Rivets & Rivnuts
For parts requiring mechanical connections or reinforcement, metal components such as threaded inserts, rivets, and rivnuts are either molded-in during production or added afterward. This allows for reliable fastening and long-term durability.
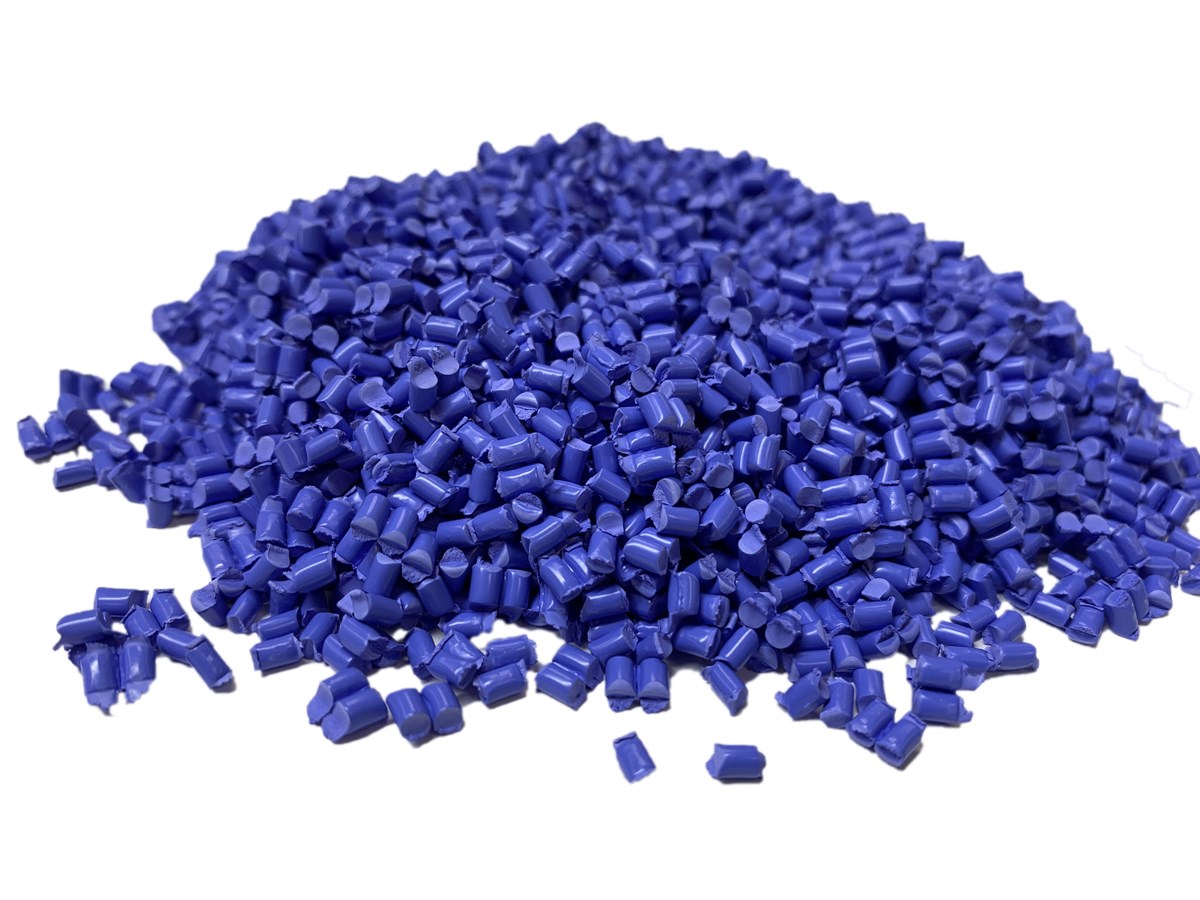
Color Concentrates and UV Stabilizers
Added to the resin before molding to achieve desired colors and improve outdoor weathering resistance, especially for parts exposed to sunlight. While not standalone structural materials like foam or inserts, colorants and UV stabilizers are still core components in rotomolding formulations due to their universal usage.
Applications for Rotational Molding
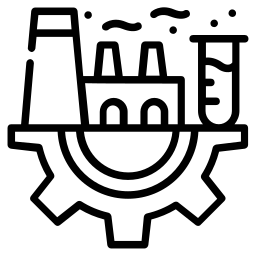
Industrial & Chemical
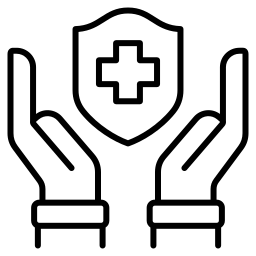
Medical & Safety
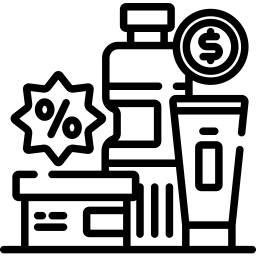
Consumer & Commercial
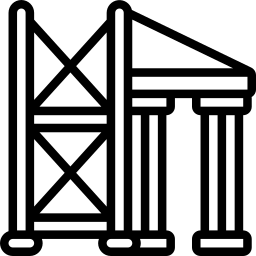
Outdoor & Structural
KingStar Mold’s Rotational Molding Equipment
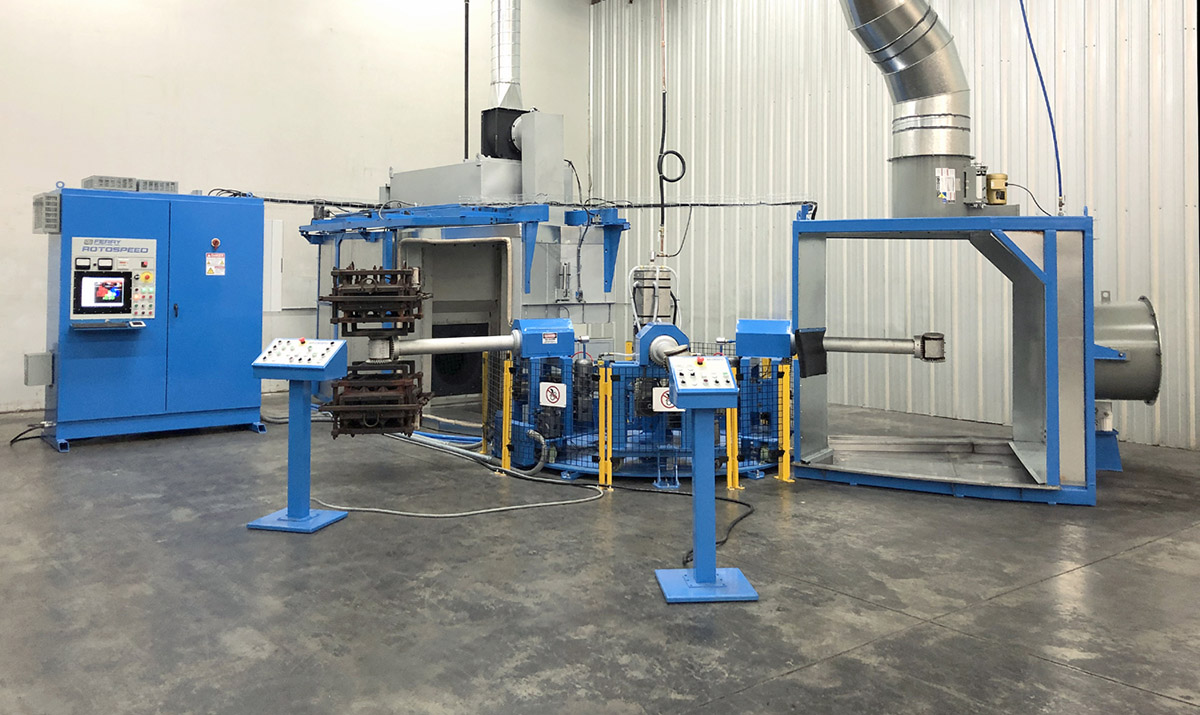
Rotational Molding Machines
Our production floor features advanced Ferry Rotospeed RS-220 and RS2-3300 machines, each equipped with offset arms to handle various molding cycles efficiently. The largest machine offers a swing of up to 125 inches, allowing us to manufacture a wide range of custom rotomolded parts—from compact components like spray manifolds to larger items such as small boats.
High-Intensity Mixing Equipment
We utilize a 1000-lb. capacity Ribbon/Paddle Blender for consistent material blending. Additionally, our high-intensity mixer, with a 300-lb. capacity, delivers faster cycles and enhanced mixing performance. This machine creates a controlled vortex that generates heat and shear, minimizing material agglomeration while improving color uniformity, reducing porosity, and enhancing the final product’s physical properties.
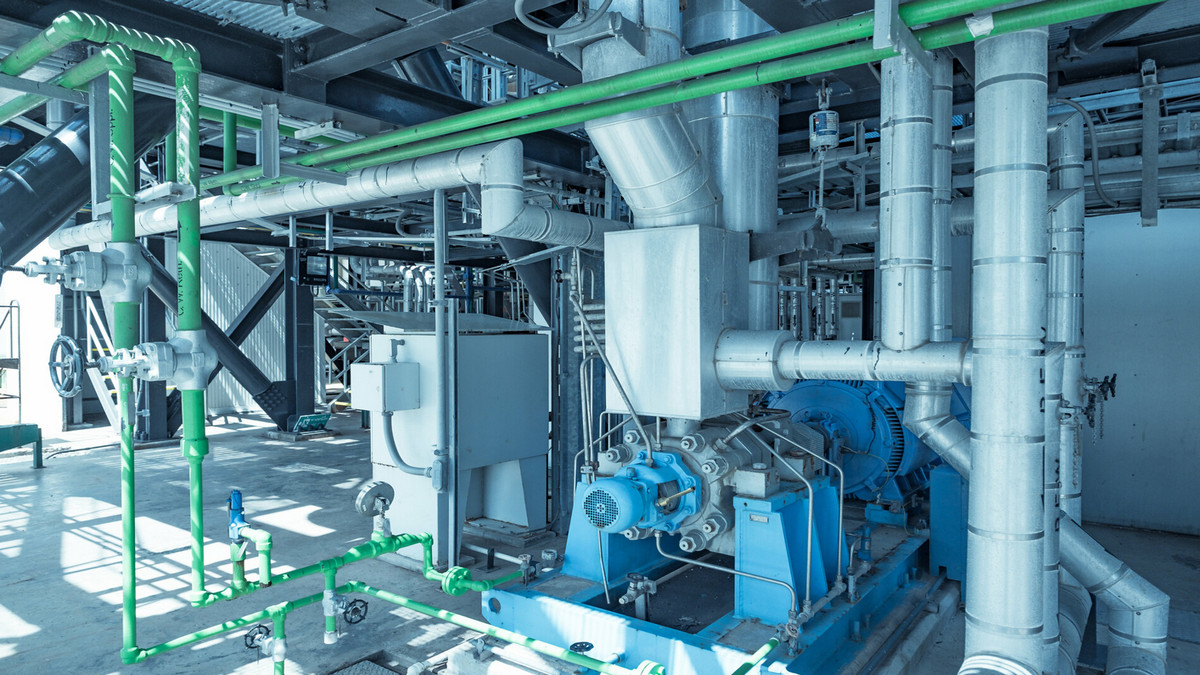
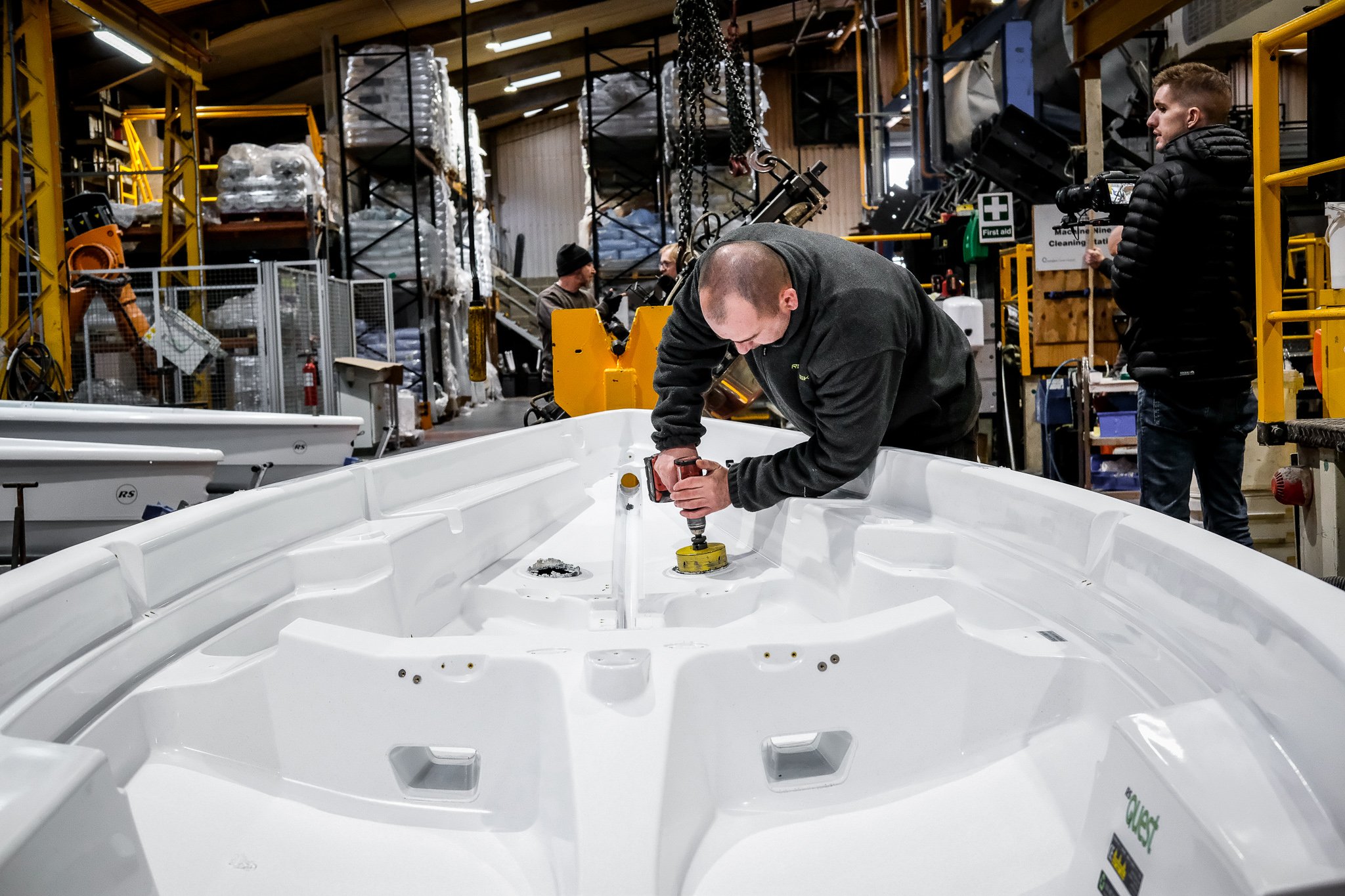
Polyurethane Foam Filling Systems
Our foam-filling equipment is designed for injecting polyurethane into hollow rotomolded parts to enhance their rigidity and thermal insulation. This is ideal for applications like coolers, where structural strength and insulation are critical. Our team has the expertise to ensure thorough and consistent foam filling for optimal performance.
Comprehensive Quality Checks
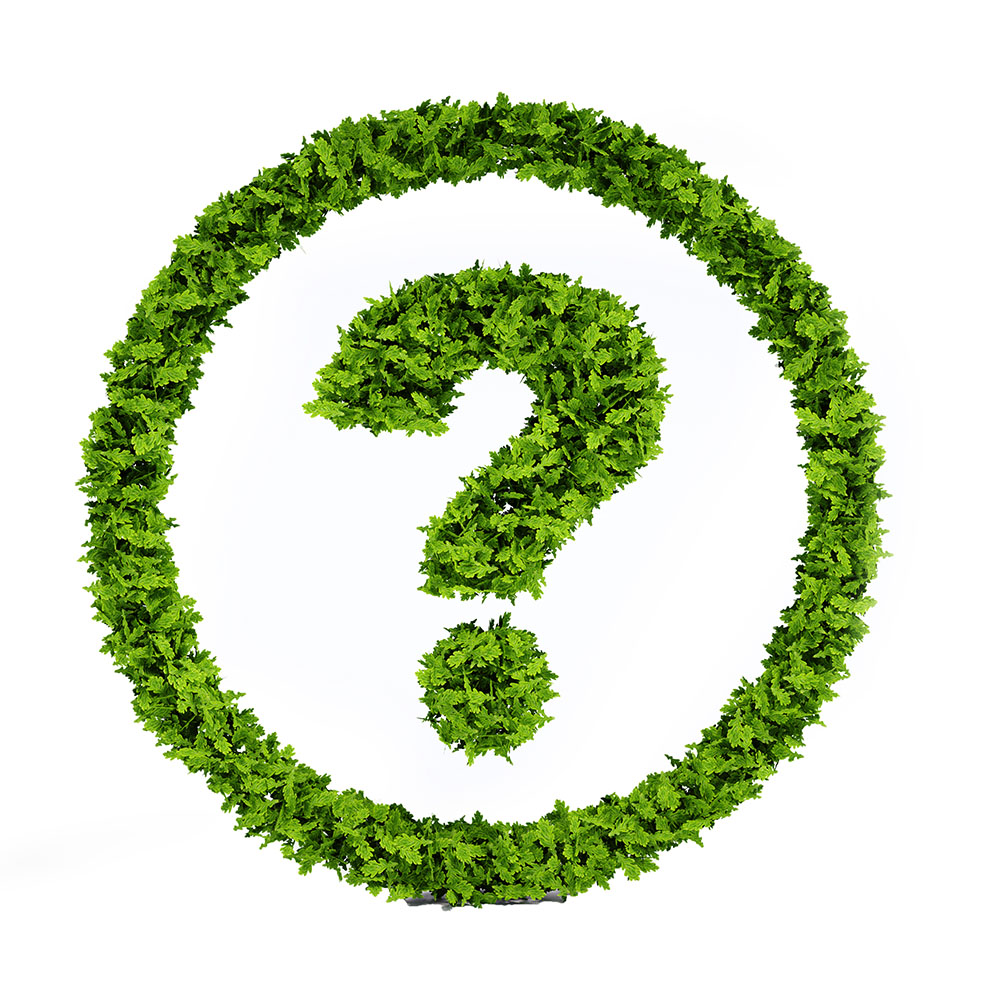
Frequently Asked Questions
Absolutely. KingStar Mold not only builds custom molds but also offers ongoing mold maintenance, repair, and modification services. Whether it’s restoring surface quality, adjusting dimensions, or adding new features, our in-house team ensures your tooling remains in top condition to support consistent, high-quality production over time.
Yes, rotomolding is ideal for producing large, hollow, and seamless plastic parts. At KingStar Mold, our equipment handles parts with up to a 125-inch swing, making it suitable for items such as storage tanks, kayaks, large containers, and outdoor equipment. The process allows for even wall distribution and excellent structural integrity, even in oversized components.
Lead time depends on the complexity of the design, tooling requirements, and production volume. For first-time projects, it generally takes 4–6 weeks from design finalization to part delivery. Repeat orders or parts using existing molds can be produced and shipped much faster, often within 1–2 weeks. KingStar Mold prioritizes efficiency and keeps customers updated throughout the process.
Yes, KingStar Mold offers polyurethane (PU) foam filling services to insulate rotomolded products such as coolers, beverage dispensers, and insulated containers. After the rotomolding process, we inject PU foam into the hollow cavities of the part. The foam expands and cures inside the shell, creating a solid insulating core.
This process significantly improves thermal retention, allowing coolers to maintain internal temperatures for extended periods. Our foam-filling equipment ensures precise and uniform distribution, eliminating air pockets and weak spots. Whether you need cold-chain logistics products or high-performance outdoor coolers, we can integrate efficient insulation into your design.