Cooperative Partners
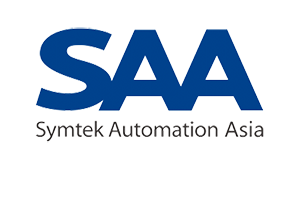
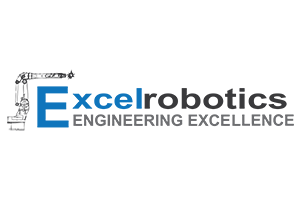
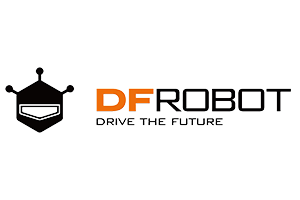
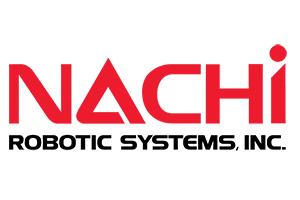
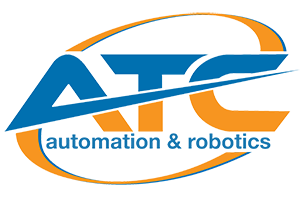
Precision-Engineered Robotic Components by KingStar Mold
At KingStar Mold, we specialize in designing and manufacturing high-precision components for robotic systems, including complex robot arms. With advanced mold-making expertise and strict quality control, we deliver parts that meet tight tolerances, ensure mechanical reliability, and support high-performance automation applications. Whether it’s multi-joint movement or load-bearing functionality, our tooling and molding solutions are tailored for demanding robotic assemblies.
How We Support Robotics and Automation Companies
Rapid Prototyping for Robotic Systems
At KingStar Mold, we help robotics engineers move fast from concept to functional prototype. Our instant DFM (Design for Manufacturability) feedback allows design teams to optimize for performance, precision, and manufacturability before production begins. Whether you’re prototyping grippers, housings, or joint assemblies, we help you iterate quickly and confidently.
Flexible Production for Custom Robotic Parts
We offer low-volume injection molding and precision machining tailored to the needs of robotic systems. From one-off designs to small-batch runs, our process supports agile development—ideal for startups and R&D teams building custom robot arms, end-effectors, and sensor housings.
Reliable Quality and Traceability
KingStar Mold operates under ISO 9001-certified processes to ensure part consistency and performance. We also offer full traceability for materials used in robotic applications—especially important for industrial and collaborative robot systems requiring high reliability.
Material Versatility for Robotic Components
From durable thermoplastics like POM and PA6 to high-strength metals such as aluminum, stainless steel 17-4 PH, and titanium, we support a wide range of materials for load-bearing, wear-resistant, or lightweight robotic components. Our material options ensure the right mechanical properties for every moving or structural part.
Maintenance and Repair on Demand
For MRO needs in robotics, we provide fast turnaround on replacement parts to reduce downtime and maintain operational efficiency. Whether it’s a custom joint, housing, or bracket, we help keep your automation systems running without disruption.
80%+
Fortune 500 Robotic Companies Served
750 Million
Parts Manufactured
300,000+
Customers Served Globally
80+
Countries Served Worldwide
Recommended Manufacturing Solution for Robotics
Integrating 3D Printing into Robotic Component Manufacturing
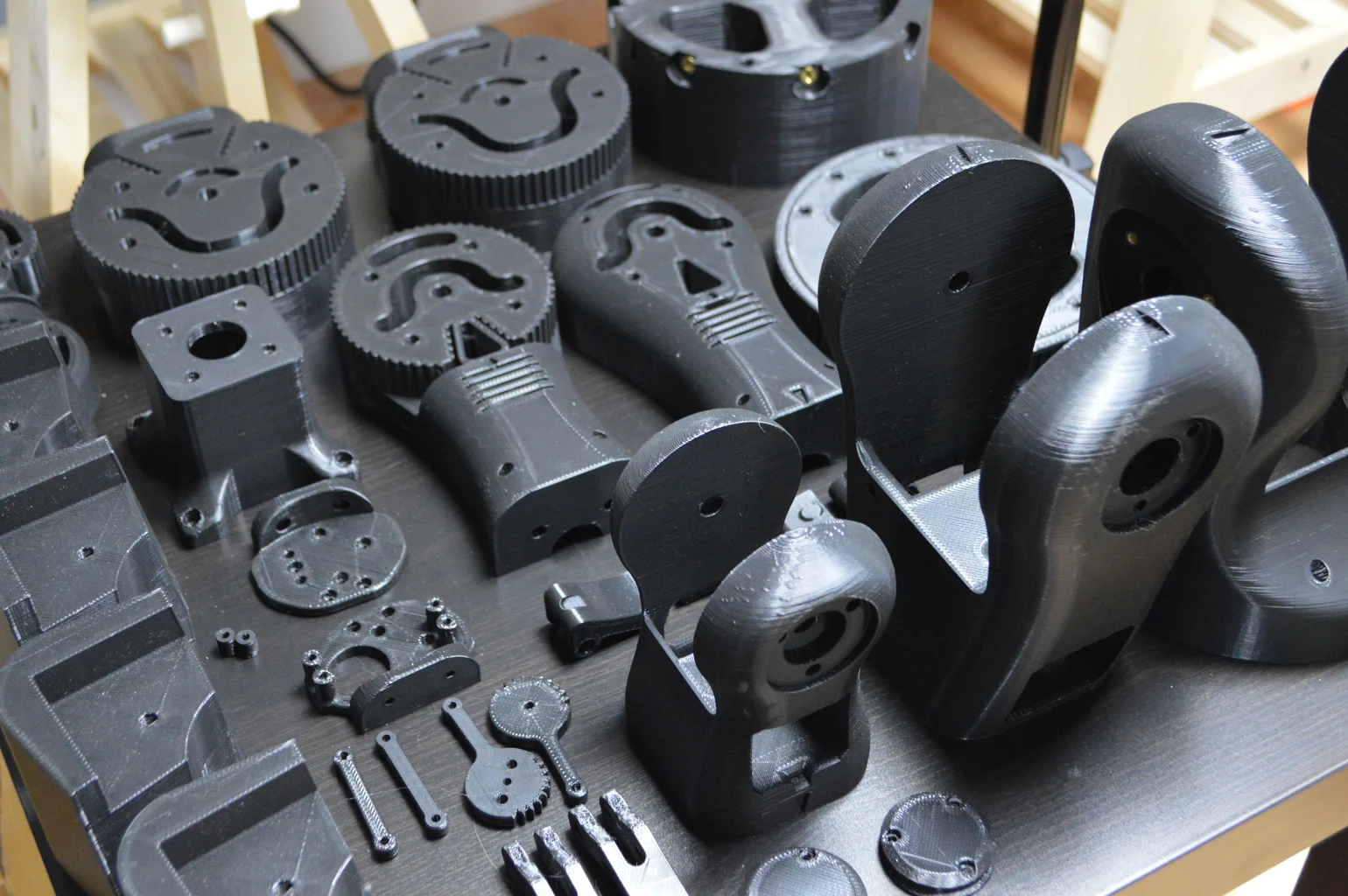
At KingStar Mold, we leverage 3D printing to accelerate the development and production of advanced robotic components. This additive process allows for highly complex geometries, weight-optimized designs, and part consolidation—making it ideal for parts like custom grippers, sensor mounts, and internal frames.
With access to a broad selection of industrial-grade plastics and metals, we can rapidly prototype and produce functional parts that meet both structural and performance needs. 3D printing also helps reduce assembly time and tooling costs, offering robotics teams greater design freedom and faster iteration.
CNC Machining for Robotics Applications
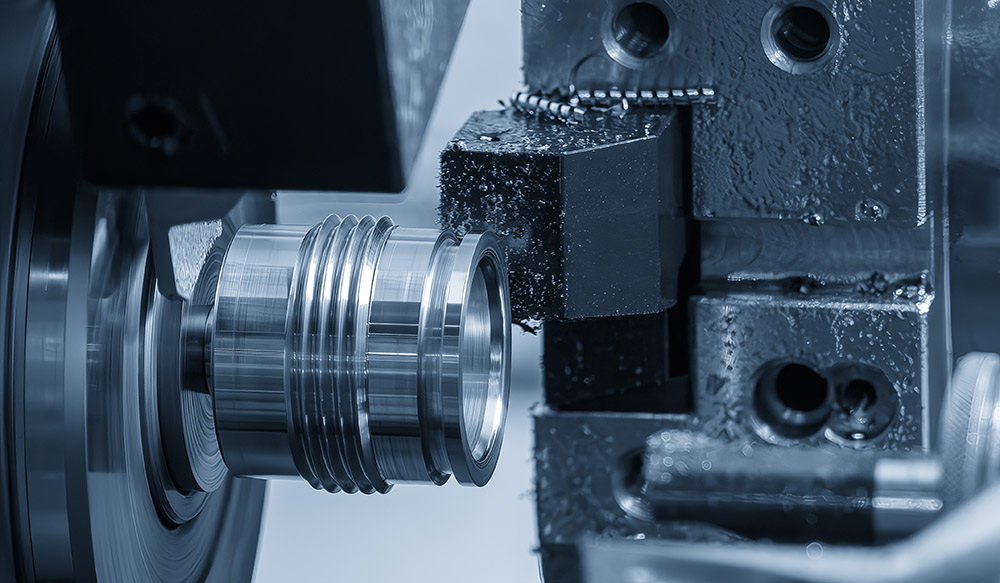
CNC machining plays a critical role in robotics manufacturing by delivering exceptional precision, tight tolerances, and material versatility. Its ability to maintain dimensional accuracy makes it ideal for producing components that require exact fits and repeatable movements, such as motor housings, gear interfaces, and joint assemblies.
Advanced 5-axis machining allows for the creation of intricate geometries, supporting the design of lightweight, space-efficient robotic systems. Additionally, CNC processes offer controlled surface finishes that reduce friction—crucial for components involved in motion or interaction. With quick turnaround and scalability for both prototyping and low-volume production, CNC machining remains a go-to solution for custom, high-performance robotic parts.
Injection Molding in the Robotics Industry
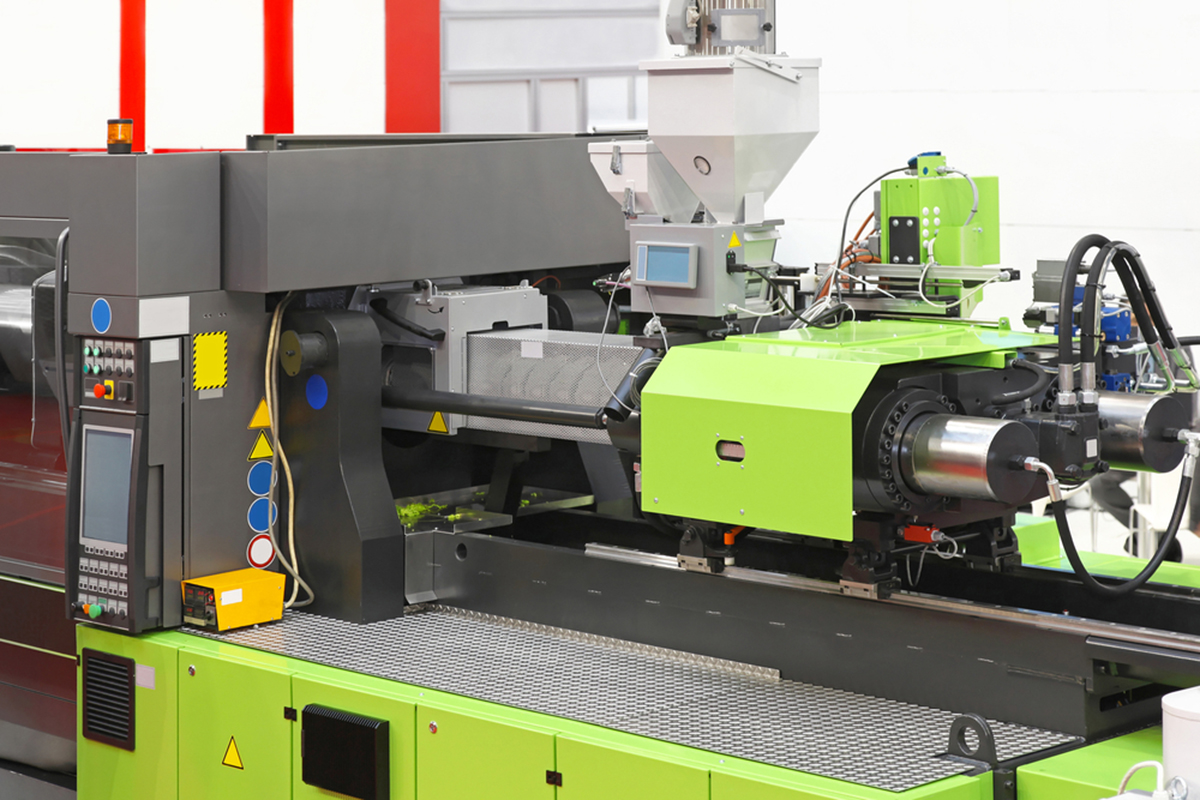
Injection molding is a reliable and cost-effective manufacturing process, particularly for low to mid-volume production runs. As production quantities increase, the piece-part cost typically decreases, making it a scalable solution. While injection molding isn’t the primary process for every robotic component, it is widely used for producing essential parts like housings, frames, and protective casings that require durability and precise dimensions. The versatility of injection molding also extends to the production of intricate designs with complex geometries. Moreover, the rise of soft robotics has fueled the adoption of liquid silicone rubber (LSR) molding, enabling the creation of flexible, lightweight parts that enhance the performance of robotic systems.
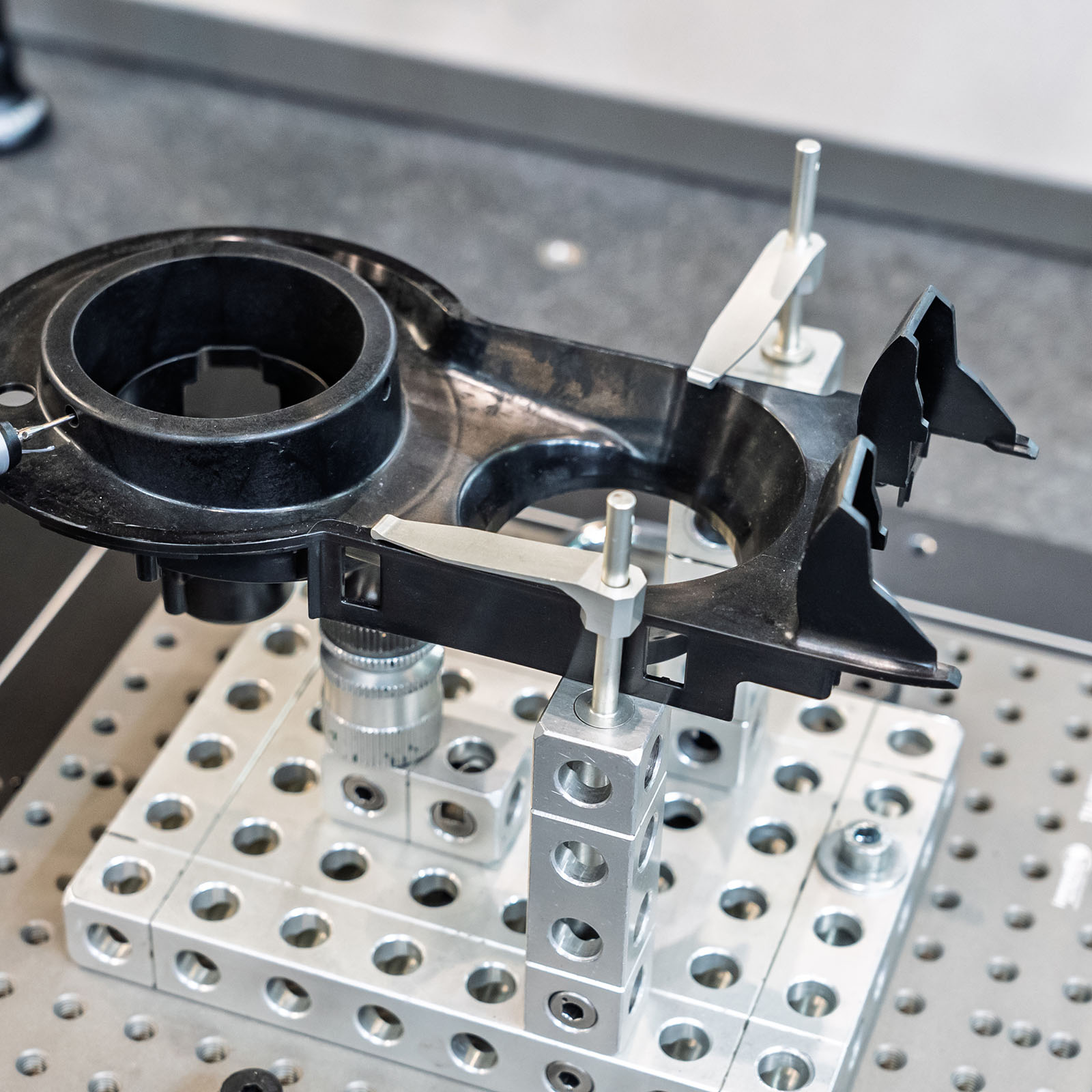
Robotics Industry Quality Assurance
At KingStar Mold, we adhere to stringent quality control protocols and internationally recognized standards to ensure that every robotics component meets regulatory requirements and customer expectations.
KingStar Mold’s commitment to quality gives you the confidence to trust us with even your most demanding aerospace components.
Factory Gallery
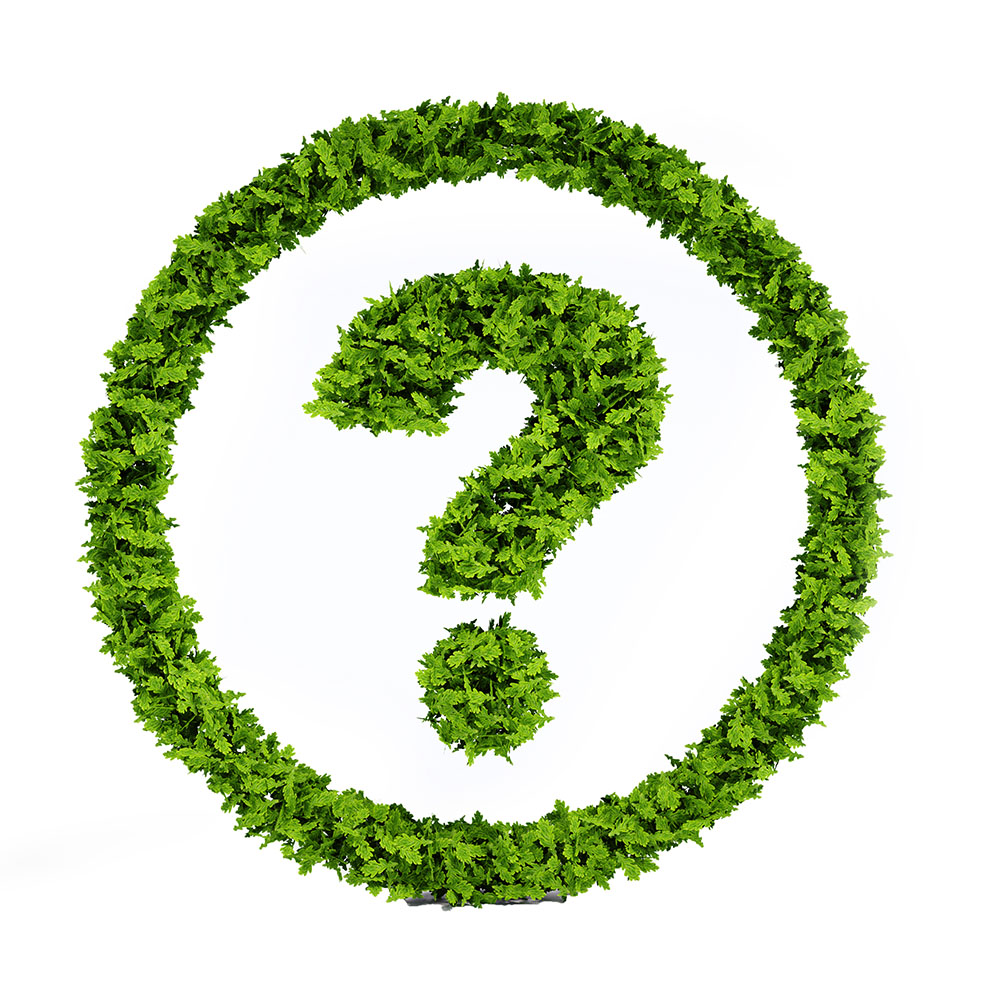
Frequently Asked Questions
We fully respect and protect the intellectual property of our clients. When you submit your design drafts or 3D models, KingStar Mold enforces strict NDA protocols and secure data handling practices. All design files are stored securely, and access is limited to only authorized engineering and production staff. Your proprietary designs remain confidential from quote to final delivery.
Yes, KingStar Mold provides expert design support for robotic parts, whether you’re starting from a concept or refining an existing CAD model. Our engineering team offers design for manufacturability (DFM) analysis to optimize parts for injection molding, CNC machining, or 3D printing. We help ensure your components meet functional requirements while reducing manufacturing risks, costs, and lead times.
We support robotics applications in automation, healthcare, consumer electronics, agriculture, and logistics. Our expertise spans structural components, wearable robotic parts, manipulators, and lightweight enclosures tailored to each industry’s unique performance requirements.
For complex robotic assemblies, KingStar Mold implements a layered quality control approach that ensures every part functions correctly within its system. We begin with part-level dimensional verification using tools like CMMs and optical comparators to confirm tight tolerances. During assembly, precision jigs and fixtures are used to maintain alignment, while torque-controlled tools ensure consistent fastening. Functional tests are performed on moving assemblies to check articulation, range of motion, and mechanical fit. Additionally, we conduct test-fit validations for mating components and use end-of-line checks—such as continuity tests for integrated electronics or pressure tests for sealed modules—to guarantee the final assembly meets performance and reliability expectations.
KingStar Mold accelerates rapid prototyping for robotics components through a combination of in-house CNC machining, 3D printing, and soft tooling, delivering high-precision parts with fast turnaround. Our engineers provide immediate DFM feedback to optimize designs early, while post-processing options like assembly, insert fitting, and surface finishing help simulate real-world performance. This streamlined process allows robotics developers to iterate quickly, validate functionality, and confidently transition to low-volume production.
Overmolding and insert molding provide enhanced durability and reduce assembly time by combining multiple materials into one part. This is particularly useful for creating ergonomic handles, grips, and seals in robotic devices, optimizing performance and cost.