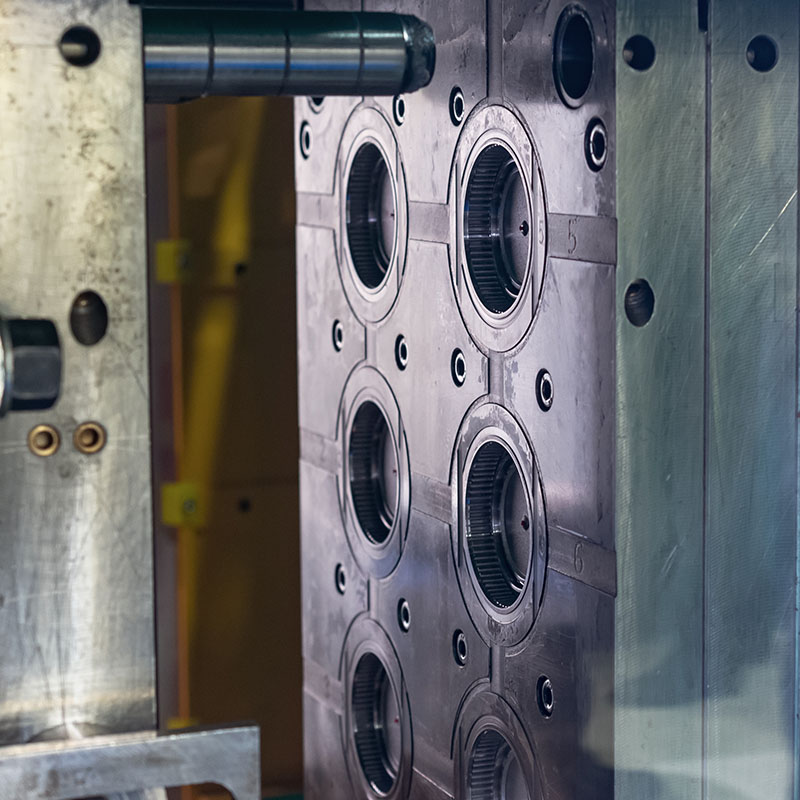
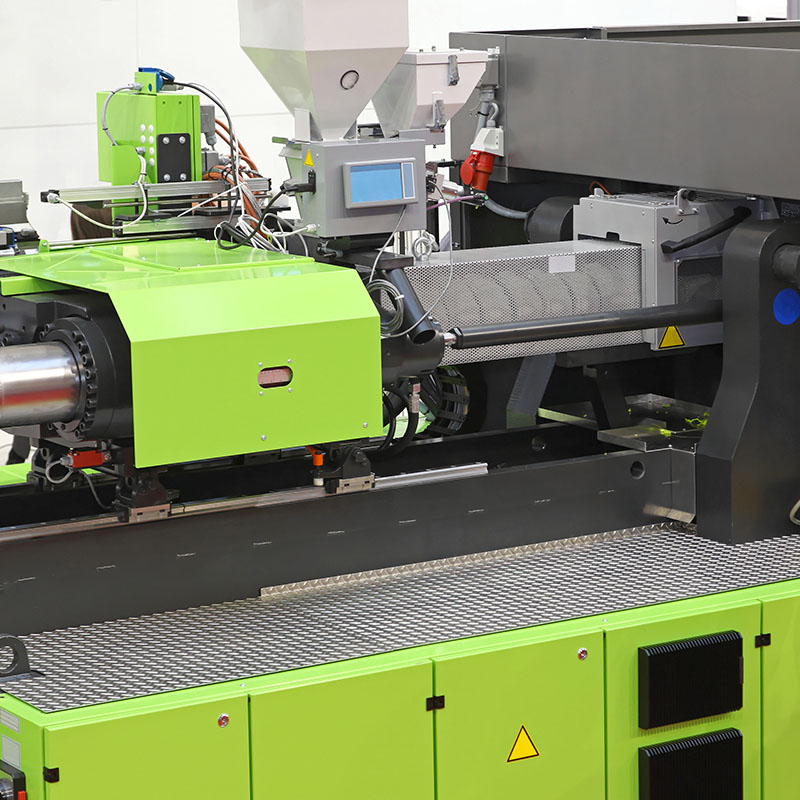
Mold Fabrication
Rapid Tooling at KingStar Mold
KingStar Mold’s rapid tooling process accelerates mold production, completing it 1.5 times faster than traditional methods. This service is perfect for R&D trials and low-output production stages.
Before mass production, a set of rapid tooling is created to test and verify the design, identifying any issues with the engineering structure.
Our rapid tooling is cost-effective, quick, and allows for early detection of design flaws, giving R&D teams the opportunity to make adjustments that enhance the production tooling’s performance and lifespan.
Rapid Tooling Gallery
Advantages of rapid tooling in KingStar Mold
Faster Production Time
Cost-Effective Prototyping
Design Flaw Detection
Improved Tool Longevity
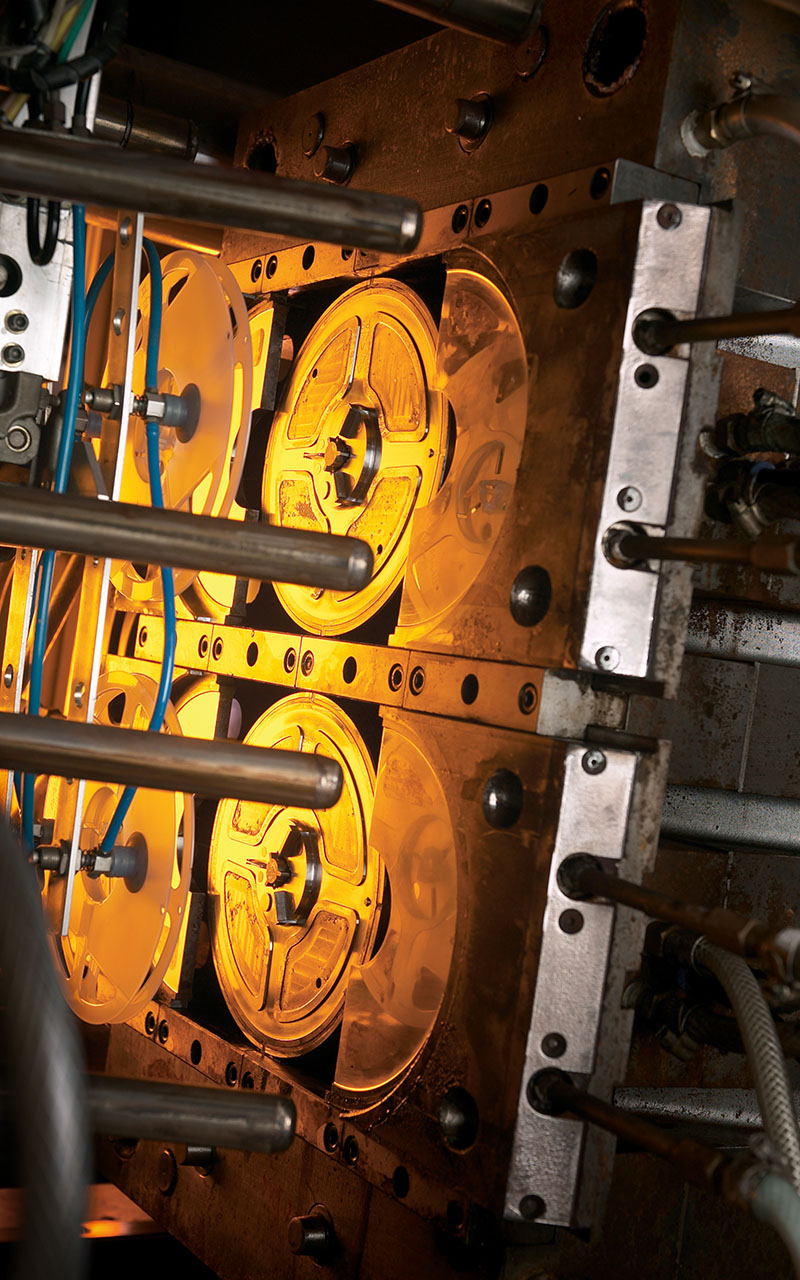
KingStar Mold’s Rapid Tooling Capabilities
Structural Design Verification
Strength Testing of Parts
Tooling Design Evaluation
Various Material Verification
Mass Production Stability Testing
Other Required Verifications
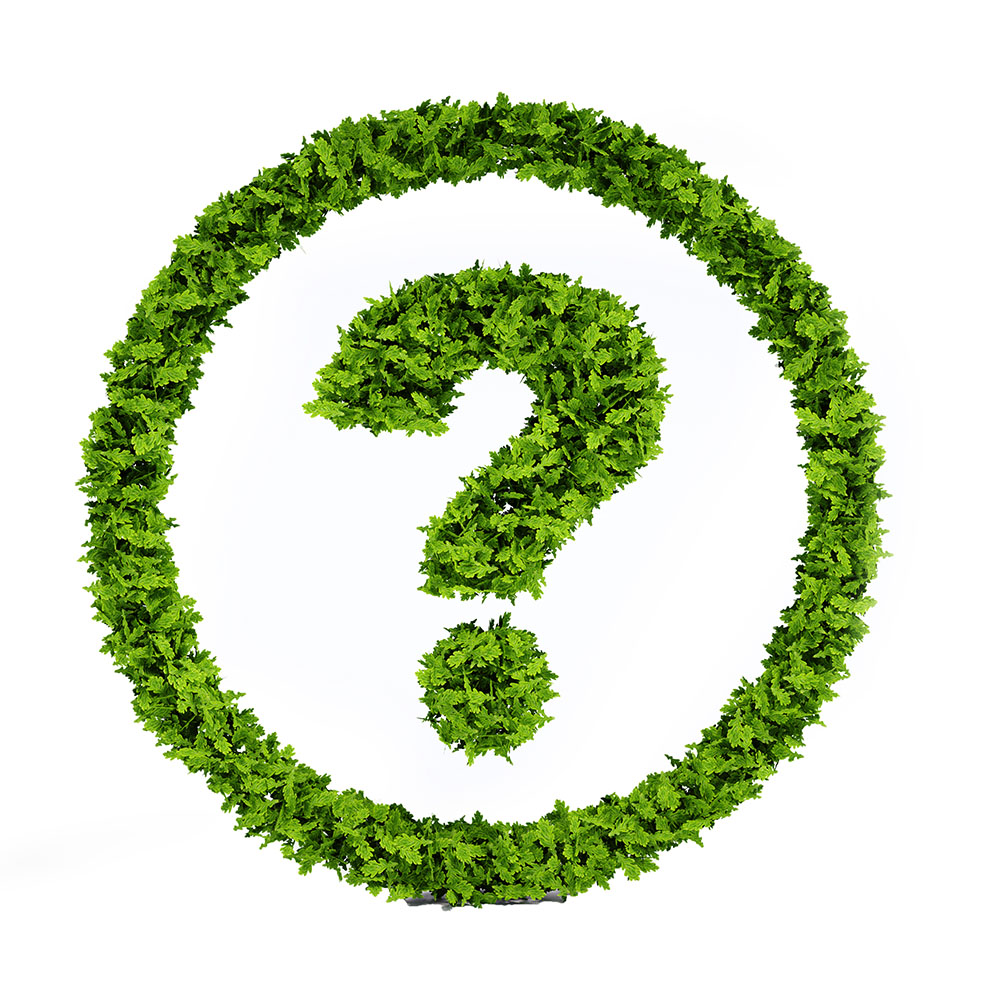
PA materials outperform many plastics in terms of mechanical strength, durability, and resistance to harsh environments.
PA offers high strength, resistance to wear, and good heat and chemical resistance, making it suitable for demanding applications.
PA injection molding is widely used in automotive, aerospace, medical devices, consumer electronics, and industrial equipment.
Common types include PA6, PA66, glass-filled PA, and mineral-filled PA, each offering unique performance characteristics.
PA materials offer excellent mechanical strength, impact resistance, and durability, making them ideal for automotive, industrial, and consumer applications.
PA (Polyamide) injection molding is a process that uses PA-based materials to create durable, high-performance parts through injection molding.
KingStar Mold ensures high-quality results through advanced technology, precision engineering, and strict quality control throughout the rapid tooling process, ensuring that your parts meet the required standards.
At KingStar Mold, we understand the importance of quick turnarounds. Our efficient process typically delivers rapid tooling within a few days to a few weeks, depending on the project scope and complexity.
Yes, KingStar Mold specializes in creating rapid tools for parts with complex geometries. Our advanced CAD software and expertise allow us to design and manufacture tools capable of producing intricate, high-precision components.
The cost of rapid tooling is generally lower than traditional tooling, particularly for small or low-volume production. KingStar Mold provides competitive pricing, ensuring cost-effective solutions for your project’s requirements.
Parts made with rapid tooling can achieve high precision, often within tight tolerances, making them suitable for functional prototypes, testing, and small production runs.
Materials commonly used in rapid tooling include aluminum, steel, resin, and various composites. KingStar Mold works with a wide range of materials to meet the specific needs of your parts.