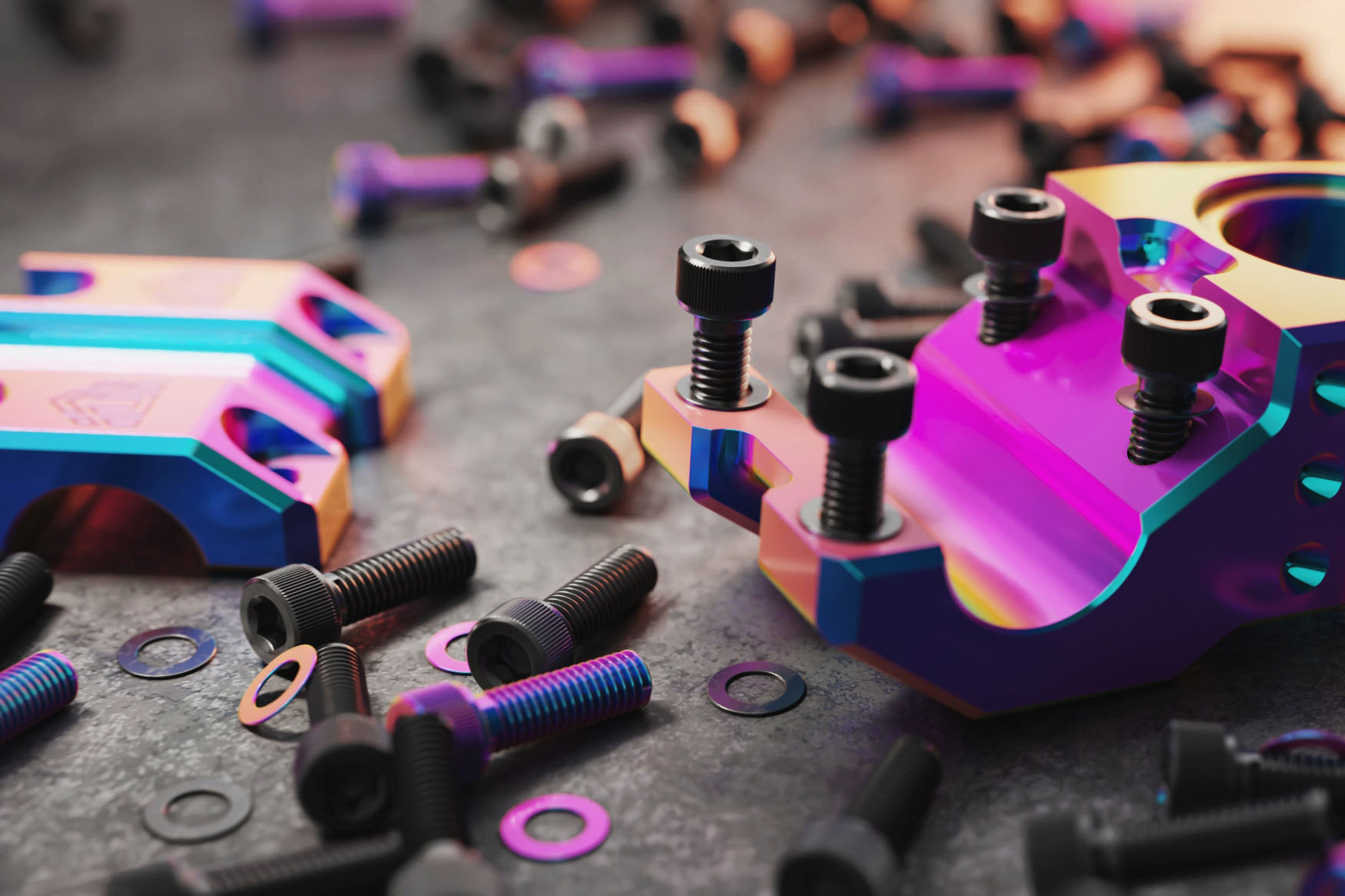
What is PVD Coating?
PVD (Physical Vapor Deposition) coating is an advanced, eco-friendly process that applies thin, durable coatings to various materials by vaporizing metals or compounds in a vacuum. This method creates a strong bond, enhancing surface properties and providing excellent resistance to corrosion, wear, and oxidation, making it ideal for automotive, tool, and electronic components.
PVD coating also offers customizable finishes, from glossy to matte, with a variety of colors, combining both functionality and aesthetics. It’s perfect for industries like aerospace, medical devices, and decorative products, providing smooth, uniform coatings with reduced environmental impact compared to traditional methods.
KingStar Mold utilizes PVD technology (through cooperative suppliers) primarily in the scenarios of plastic molds, die-casting molds, and CNC prototypes, enhancing the durability and appearance of these components.
Showcase of Anodizing Finished Products
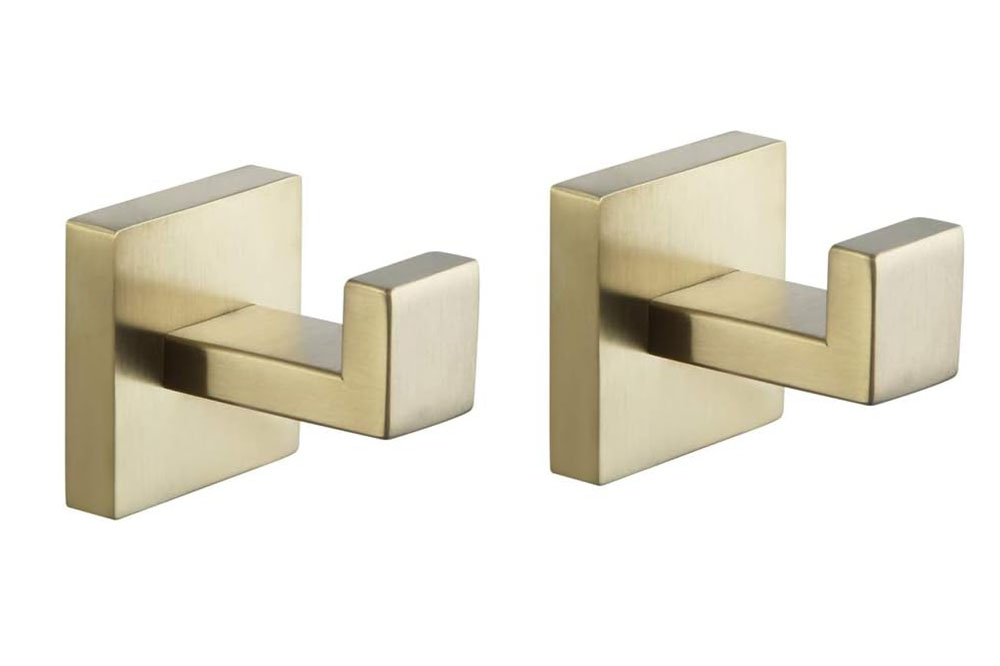
Bathroom Towel Hooks
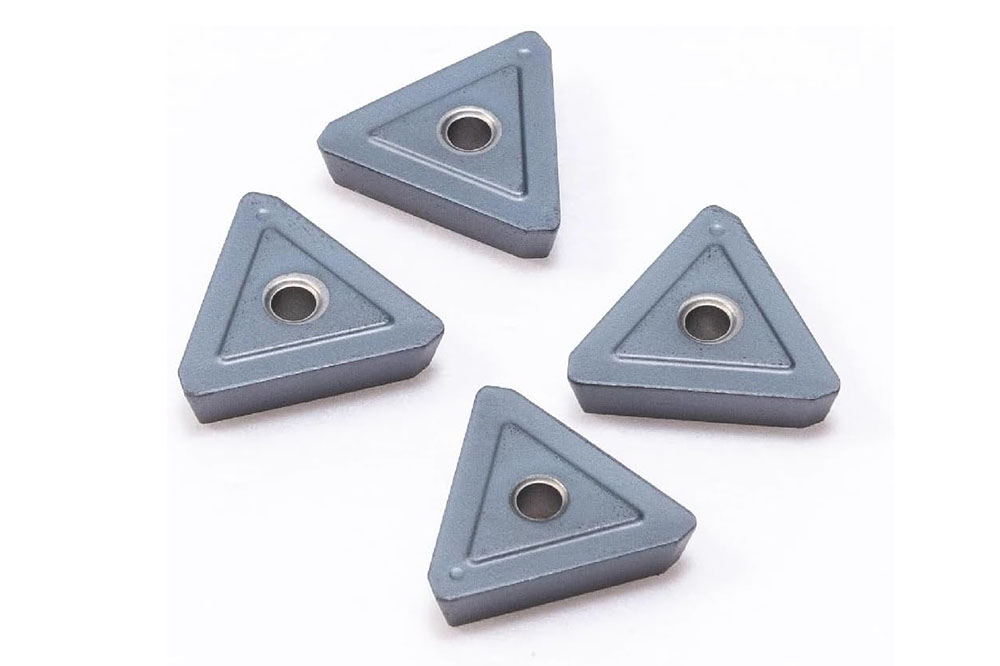
CNC External Turning Tool
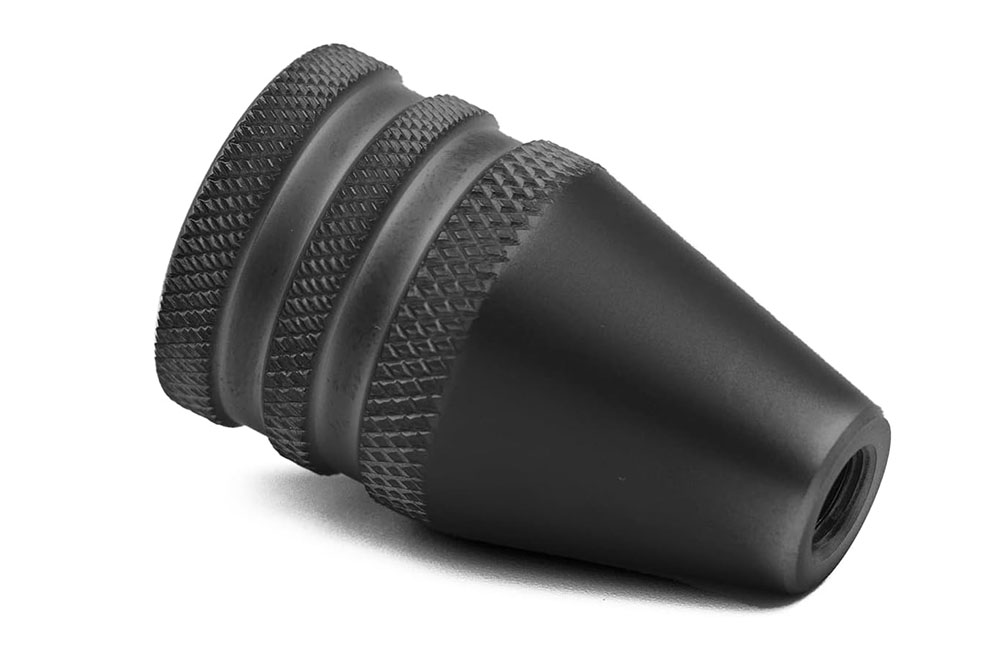
Diamond Knurl
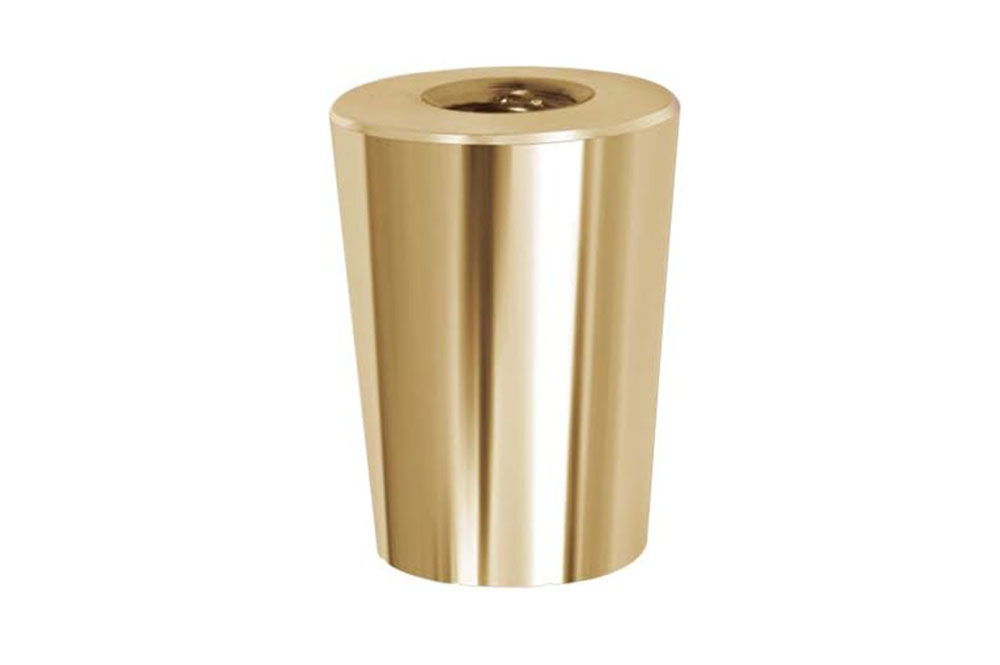
Faucet Handle Ferrule
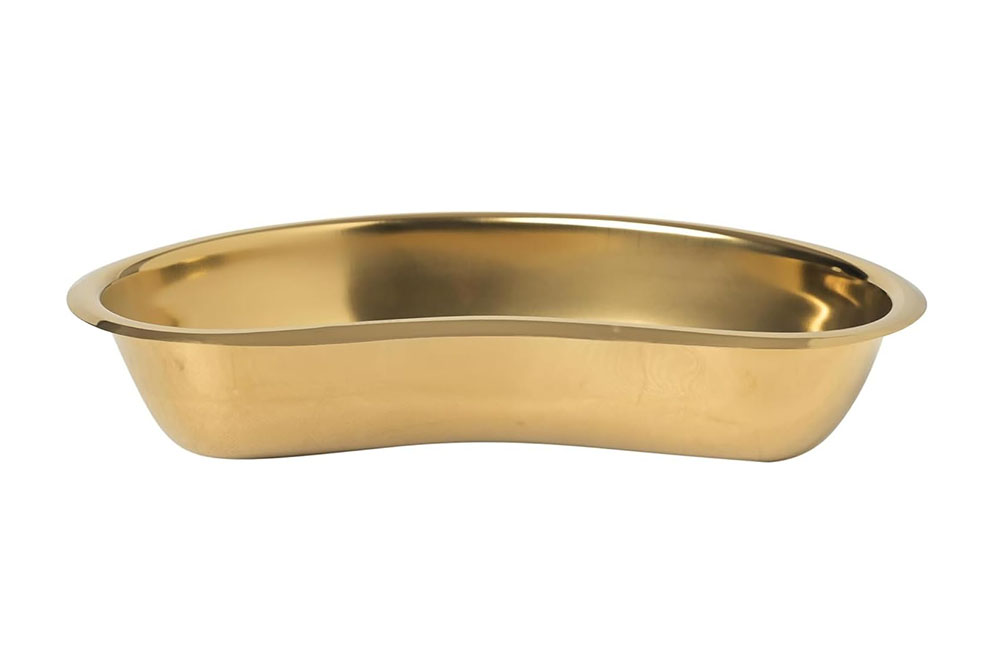
Heavy Duty Stainless Steel Kidney Tray
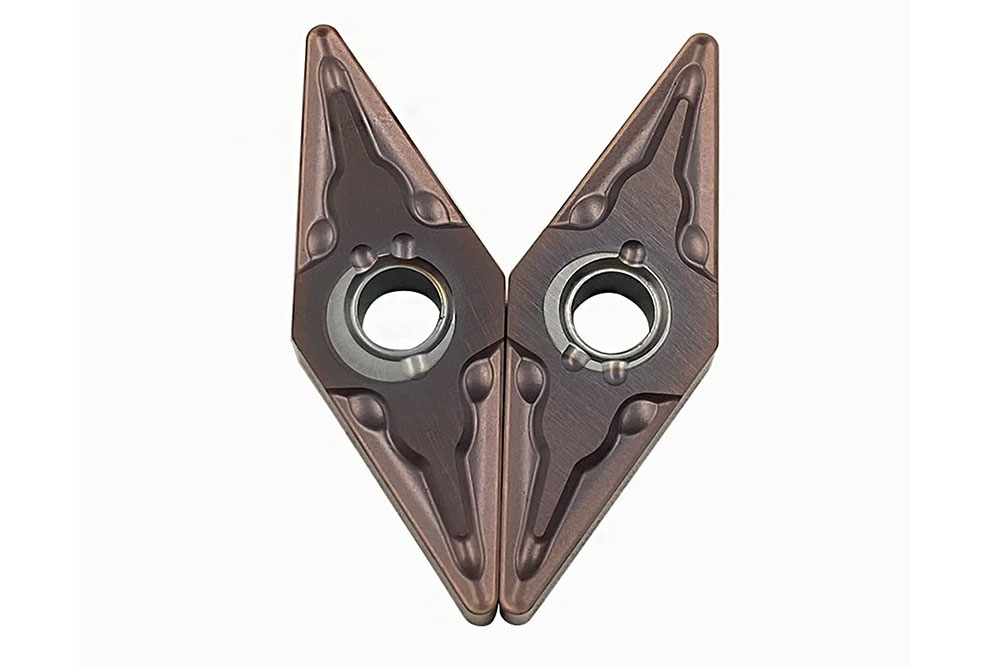
Lathe Turning Carbide Inserts
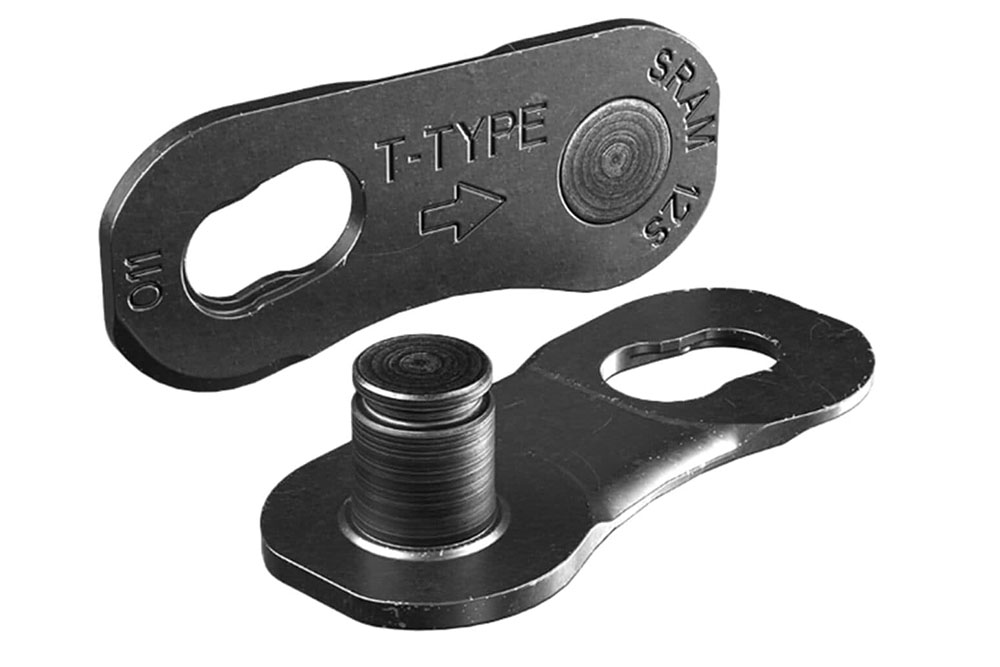
Sram Eagle Chain Link
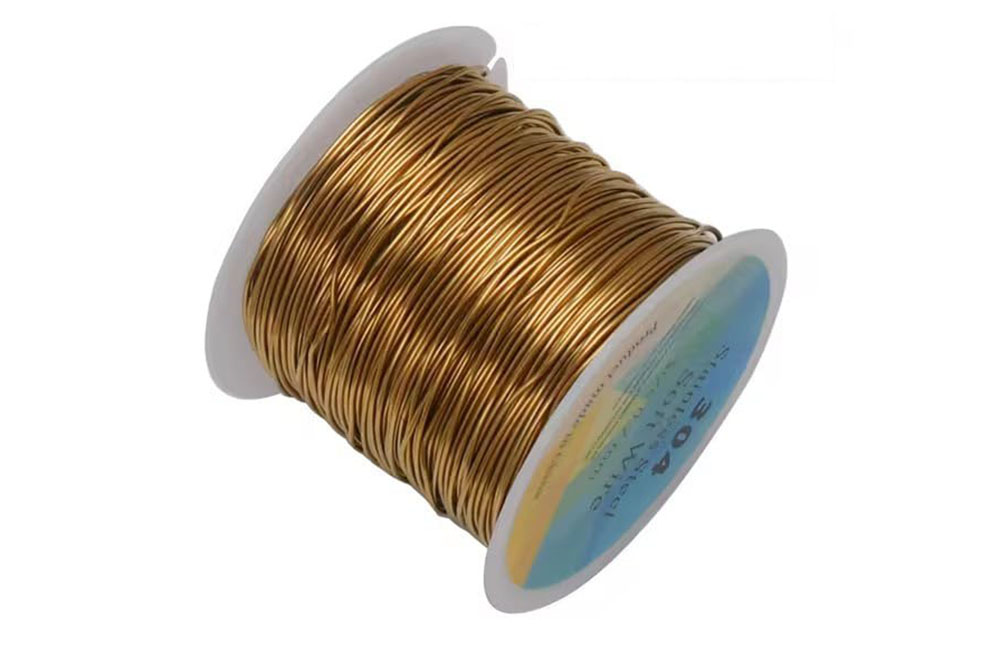
Stainless Steel Wire
Advantages of PVD Coating Your Product
Enhanced Durability
PVD coatings significantly improve the wear and scratch resistance of your products, extending their lifespan even in harsh environments.
Corrosion Resistance
The coating provides excellent protection against rust and corrosion, ensuring longevity and maintaining product integrity over time.
Aesthetic Appeal
Environmental Friendliness
Increased Performance
Minimal Maintenance
Various Options for PVD Coating
PVD Coating Type | Description | Typical Applications | Cost | Duration |
---|---|---|---|---|
Titanium Nitride (TiN) | A hard, gold-colored coating that enhances wear resistance and corrosion protection. | Cutting tools, automotive parts, medical devices, watches. | Moderate to High | Long-lasting, 5-10 years |
Zirconium Nitride (ZrN) | Similar to TiN but with a darker, gold-like finish, offering good hardness and corrosion resistance. | Aerospace components, decorative parts, industrial tools. | Moderate to High | Long-lasting, 5-10 years |
Aluminum Titanium Nitride (AlTiN) | High-temperature resistant coating that improves cutting performance, especially in high-speed machining. | Cutting tools, molds, automotive parts. | High | Very durable, 5-10 years |
Chromium (Cr) | Offers excellent hardness, corrosion, and wear resistance with a shiny, reflective finish. | Decorative items, medical instruments, industrial machinery. | Moderate | 3-5 years |
Molybdenum Disulfide (MoS2) | A dry lubricant coating that reduces friction and wear in moving parts. | Bearings, gears, automotive parts, aerospace components. | Moderate | Medium-term, 3-5 years |
Titanium Carbonitride (TiCN) | A coating with high hardness and wear resistance, offering a dark, grayish finish. | Cutting tools, aerospace components, automotive applications. | High | Long-lasting, 5-10 years |
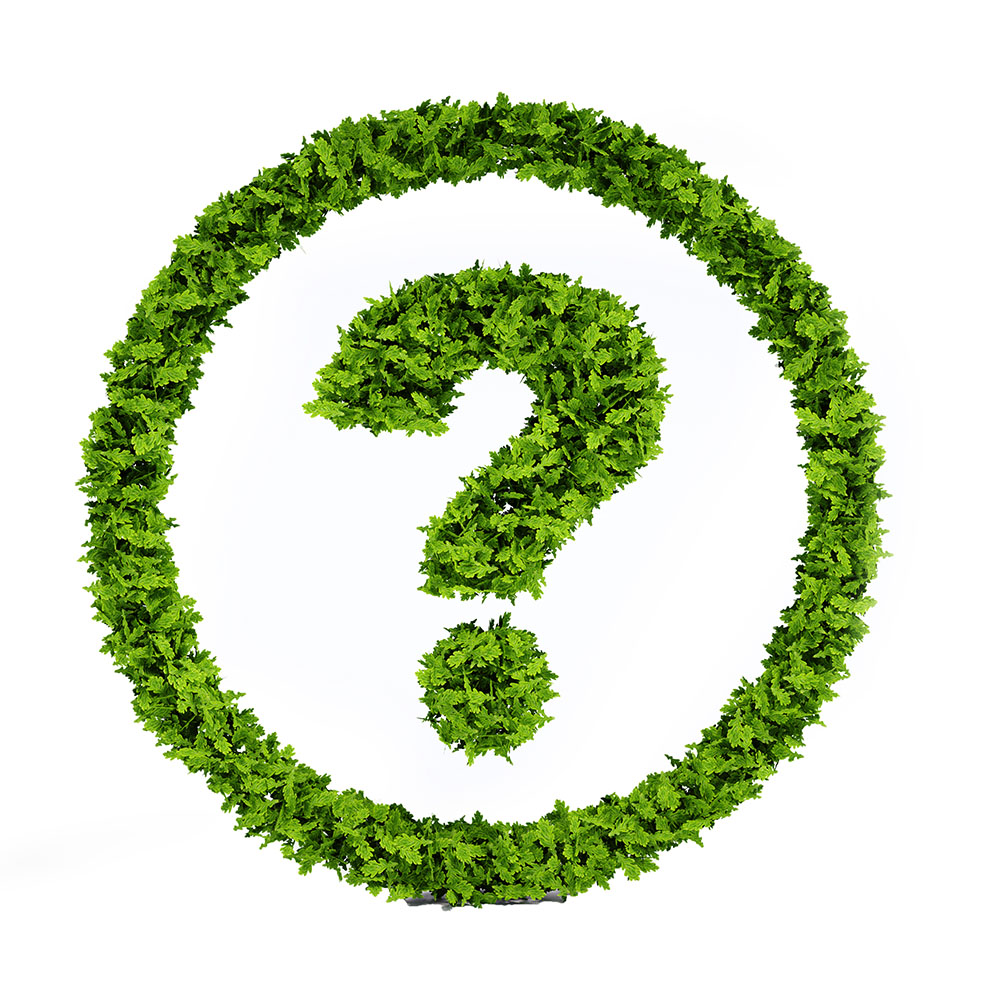
Some common PVD coatings include Titanium Nitride (TiN), Zirconium Nitride (ZrN), Aluminum Titanium Nitride (AlTiN), and Chromium (Cr).
PVD technology can coat a variety of materials, including metals, ceramics, and plastics, depending on the specific coating and application.
The durability of PVD coatings typically ranges from 5 to 10 years, depending on the material, application, and environmental exposure.
PVD coating is ideal for a range of products, including automotive parts, cutting tools, medical devices, and decorative items.
PVD coating provides improved durability, corrosion resistance, enhanced aesthetics, and reduced maintenance requirements for various products.
PVD (Physical Vapor Deposition) coating is a process that applies a thin, durable layer of material to a substrate, enhancing its wear, corrosion, and aesthetic properties.
The cost of PVD coating varies depending on factors such as material, coating type, and part size, but it generally offers a cost-effective solution compared to traditional coating methods.
Yes, PVD coatings can be customized in a variety of colors and finishes, making them suitable for both functional and decorative applications.
Yes, PVD is an eco-friendly process that produces fewer toxic by-products and requires less energy compared to traditional coating methods.
PVD coatings are widely used in industries such as aerospace, automotive, medical devices, electronics, and manufacturing.
KingStar Mold offers high-quality PVD coatings with expert precision, using advanced technology and eco-friendly methods to meet your specific requirements.
PVD coatings enhance wear resistance, reduce friction, and improve corrosion resistance, making products more durable and efficient.