Free Design Review for Punching Projects
We offer a complimentary 30-minute virtual meeting with one of our sheet metal applications engineers to review your punching project design. This is an opportunity to address any questions or concerns you may have. Common topics discussed during the review include:
Selection of in-house punch tooling
Material thickness and type considerations
Tolerances and precision requirements
Optimization for efficiency and cost-effectiveness
Punch Form Tooling We Provide
Lance Tab
This tool cuts and raises a section of the sheet metal to form a hook or tab shape, typically used for clips, stops, hanging, ventilation, and mechanical fastening.
Single hit vs. progressive tooling: single hit only
Bridge Lance
Bridge lances create a bridge-like feature using two points of contact with the sheet, commonly used for decorative or functional purposes like clips, airflow, cable pass-throughs, or fastening.
Single hit vs. progressive tooling: single hit only
Extrusion
Extrusions are formed by pushing material through a die to create a raised shape, commonly used for electrical contact points, threaded holes, standoffs, and airflow channels.
Single hit vs. progressive tooling: single hit only
Half Shear
Half shear tools partially cut through the sheet, creating raised features or deformations that can act as markers for assembly or serve as alternatives to tabs or lances.
Single hit vs. progressive tooling: single hit only
Perforation Pattern (Cluster Tool)
Perforations create a hole/slot design with material left between features, commonly used for ventilation, filtration, drainage, decoration, or weight reduction.
Single hit vs. progressive tooling: single hit only
Louver
Louver tools create slotted openings or vents, typically used in panels or enclosures for thermal and ventilation management in electronics.
Single hit vs. progressive tooling: both
Rib
Ribs are raised, oblong features that enhance strength, rigidity, or stiffness without adding weight, commonly used in electronics enclosures for thermal management and structural support.
Single hit vs. progressive tooling: progressive only
Emboss
Emboss tools form functional or aesthetic enhancements, such as spacers or mounting points, and can be used to conceal hardware or add visual appeal.
Single hit vs. progressive tooling: single hit only
Material Thicknesses for Punching
Material | Thickness Range (inches) | Thickness Range (mm) |
---|---|---|
Aluminum 5052-H32 | 0.040 in. - 0.250 in. | 1.016 mm - 6.35 mm |
Aluminum 6061-T651 | 0.040 in. - 0.250 in. | 1.016 mm - 6.35 mm |
Aluminum 6061 (Profile/Perimeter) | 0.040 in. - 0.250 in. | 1.016 mm - 6.35 mm |
Low Carbon Steel CR 1008 | 0.036 in. - 0.119 in. | 0.914 mm - 3.023 mm |
CR Galvanized | 0.036 in. - 0.119 in. | 0.914 mm - 3.023 mm |
CR Galvannealed | 0.036 in. - 0.119 in. | 0.914 mm - 3.023 mm |
Copper C101, C110 | 0.040 in. - 0.125 in. | 1.016 mm - 3.175 mm |
Brass C260 | 0.040 in. - 0.125 in. | 1.016 mm - 3.175 mm |
Stainless Steel 304/304L, 316/316L | 0.036 in. - 0.074 in. | 0.914 mm - 1.88 mm |
KingStar Mold’s Other Attached Capabilities
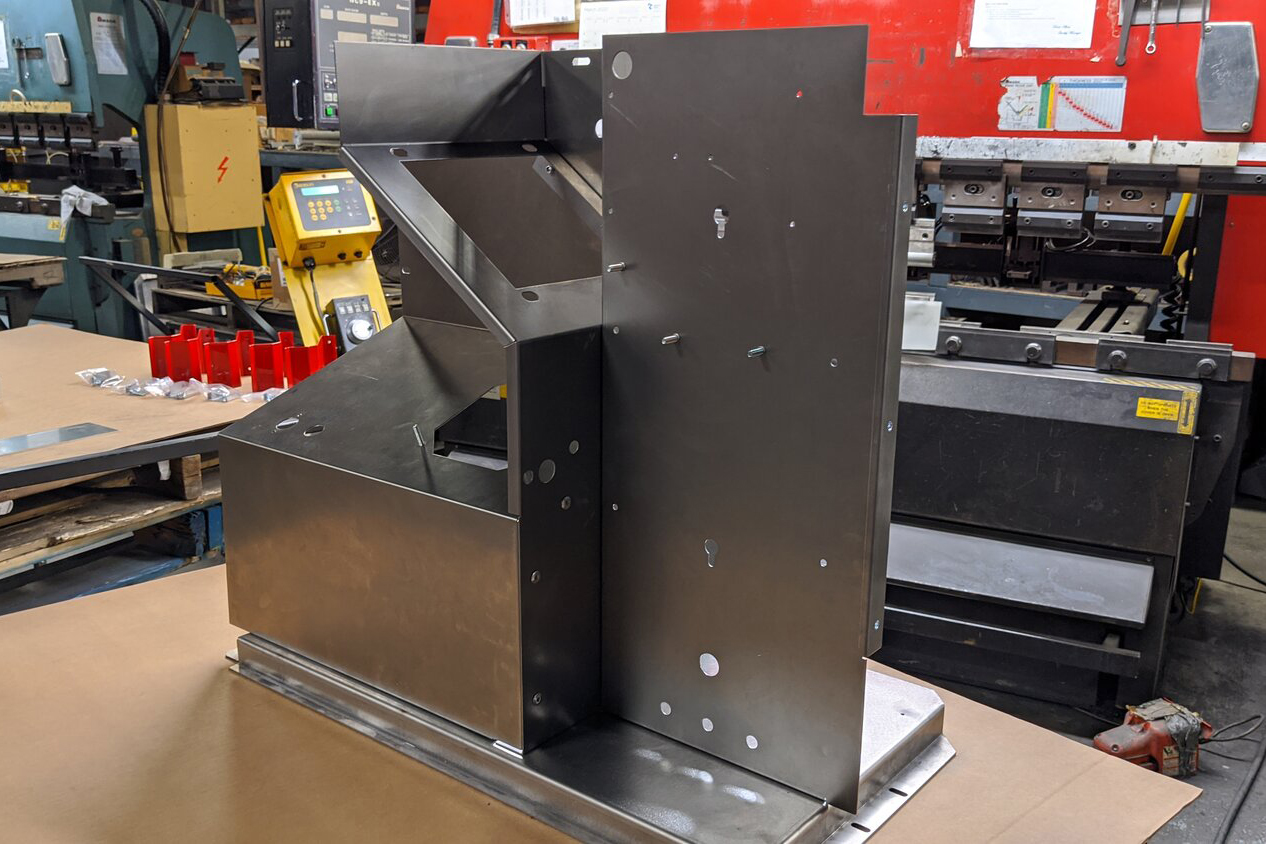
Assembly
Sheet metal components with punched features can function independently, but they are more commonly integrated into weldments, sub-assemblies, or larger assemblies for added functionality.
We provide the following assembly services to ensure your project is ready for immediate use upon delivery:
- Welding (single and multi-component)
- Hardware insertion
- Riveting
Lead time: Assembly adds 1-3 days, depending on the number of components.
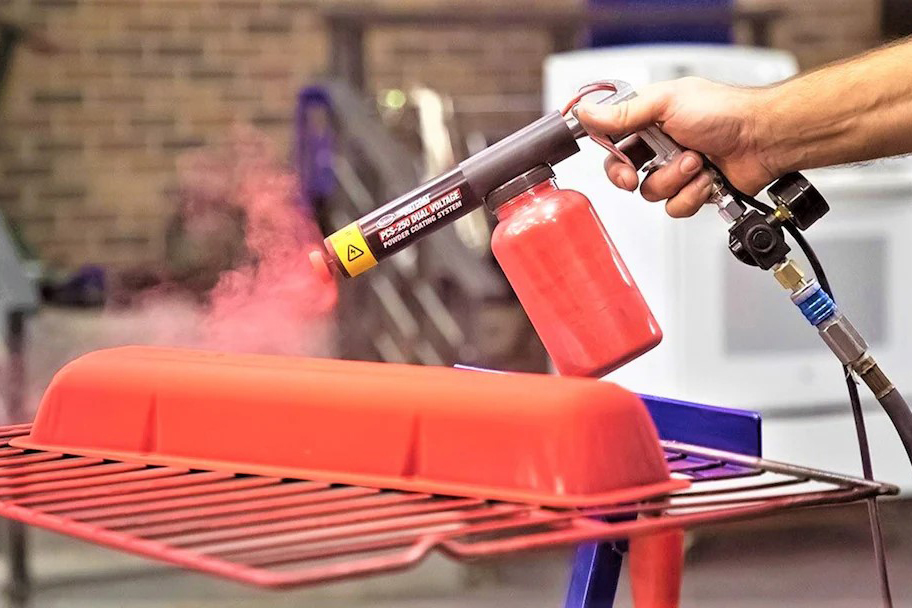
Finishing Options for Punched Parts
Beyond feature and geometry customization, we offer a variety of finishing services for punched components and assemblies to meet your aesthetic requirements. Our available finishing options include:
- Plating
- Powder coating
- Wet paint
- Masking
- Part marking
- Metal surface finishing
Lead time: Most finishing options add 1-2 days per finish. Additional details are available on our finishing options page.
Advantages of Punching Your Metal Part
High Precision and Accuracy
This process ensures consistent part quality with tight tolerances, making it ideal for applications requiring exact specifications.
Versatility in Design
Punching can produce complex shapes and holes in various metal thicknesses, providing flexibility in part design and functionality.
Cost-Effective Production
Design Guidelines for Punching Sheet Metal Parts
Punching sheet metal can be intricate, so to help integrate this process into your next project, here are some practical manufacturability tips to consider during design. These guidelines aim to optimize cost management while ensuring high-quality results.
- Hole Spacing: Space holes at a minimum of 1.5 times the material thickness. For tools that create clusters, holes can be spaced at 1x material thickness, but single-hit tools need additional material to maintain consistent hole quality.
- Smallest Hole Design: Design the smallest holes to be 1.2 times the material thickness.
- Reduce Feature Variety: Minimize the number of unique punch features in your design. Using consistent feature sizes helps reduce machine setup time and tooling costs.
- Punch Feature Tolerances: Specify typical tolerances for punched features within +/-.005 in. (+/- 0.127 mm). Keep in mind that tolerances differ between the flat and formed states. For more details on handling tolerances across bends, consult our tolerance guide.
- Progressive Punch Features: Pay attention to the length of any progressive features (e.g., ribs, louvers, cluster patterns). Long features may cause quality issues like warping.
- Uniform Feature Orientation: Ensure all formed features face the same direction. Designs with mixed form and form-down features may lead to quality challenges.
Additional Punching Design Tips:
- Maximum Formed Feature Height: Limit to 4 times the material thickness.
- Feature Spacing and Tool Station Diameter: The space between punch-formed features should be approximately 50% of the tool station diameter.
Tool Station Diameter | Space Required Between Features |
---|---|
1.250 in. (31.75mm) | 0.625 in. (15.875mm) |
3.500 in. (88.9mm) | 1.750 in. (44.45mm) |
0.500 in. (12.7mm) | 0.250 in. (6.35mm) |
2.000 in. (50.8mm) | 1.000 in. (25.4mm) |
4.500 in. (101.6mm) | 2.250 in. (57.15mm) |
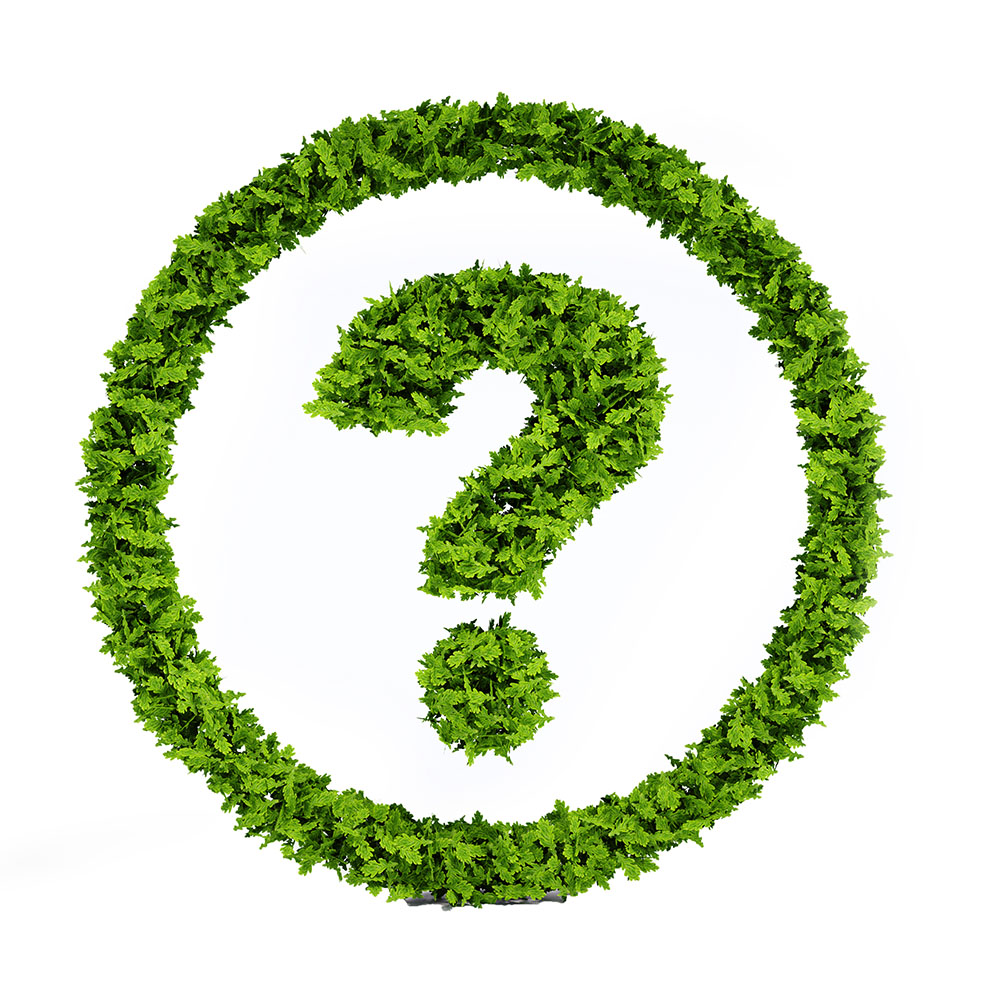
We handle a wide range of sheet metal thicknesses, typically from 0.2 mm to 10 mm, depending on the material and complexity of the design.
KingStar Mold ensures high-precision punching with tight tolerances, allowing for parts with minimal variation in dimensions and consistent quality.
Yes, we specialize in custom sheet metal punching, offering flexibility to meet your specific designs and product requirements.
Sheet metal punching offers cost-effective production, high accuracy, and versatility, enabling the creation of complex shapes and parts in large quantities.
KingStar Mold’s punching service works with a wide range of metals, including steel, aluminum, brass, copper, and other alloys, depending on your needs.
Sheet metal punching is a manufacturing process where a die and punch are used to create holes, slots, and shapes in metal sheets, ideal for high-precision applications.
To begin, simply send us your design specifications or drawings, and our team will assist you with material selection, pricing, and project planning.
We accommodate both small and large batch orders, so whether you need a few pieces or thousands, we can meet your production needs.
Yes, we offer prototyping services to test and refine designs before committing to full-scale production, ensuring the final product meets your specifications.
Lead times vary based on the complexity and volume of the order, but we aim to provide quick turnaround times without compromising quality.
Sheet metal punching is faster and more cost-effective than traditional methods like laser cutting or CNC machining, especially for high-volume production.
Our sheet metal punching service is used in a variety of industries, including automotive, aerospace, electronics, and general manufacturing.