PS Injection Molding at KingStar Mold
KingStar Mold can utilize PS materials in processes like overmolding and two-color injection molding. We are skilled in molding a wide range of PS materials, including HIPS, high-temperature resistant modified PS, antistatic modified PS, PS + talc powder, PS + fiberglass and more.
KingStar Mold has consistently delivered precision PS injection molded parts, such as high-end automotive lights and intricate medical components. Our expert designers specialize in precision PS mold design, supported by mold flow analysis, ensuring high-quality assurance throughout the process.
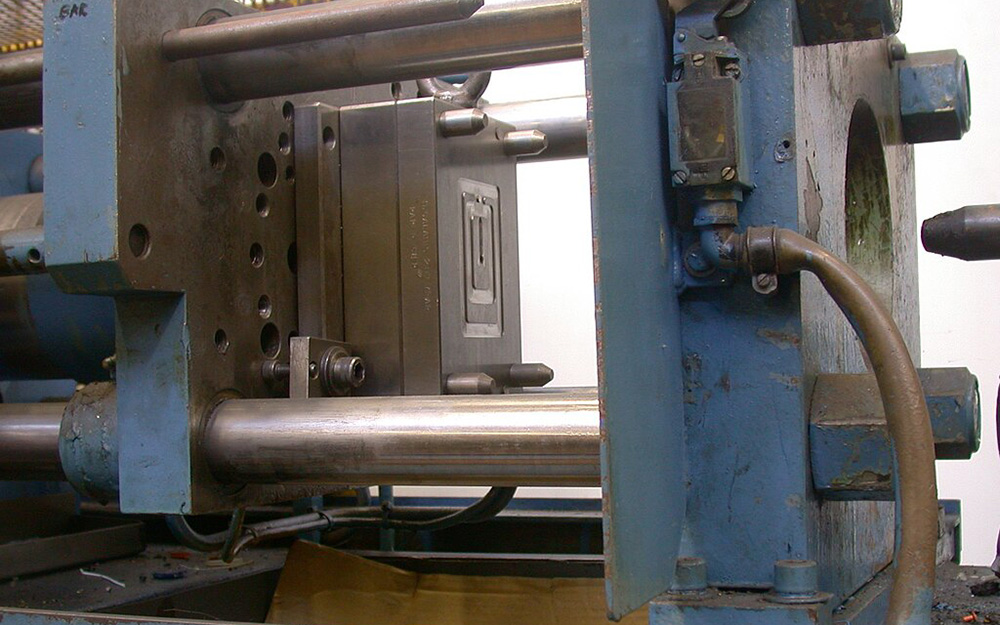
Medical Devices

Consumer Electronics
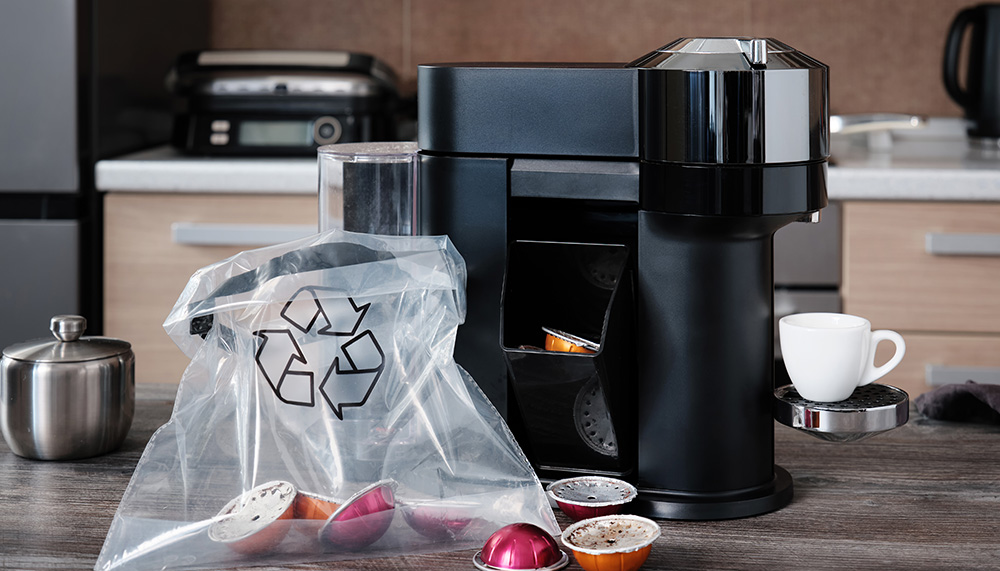
Industrial Equipment
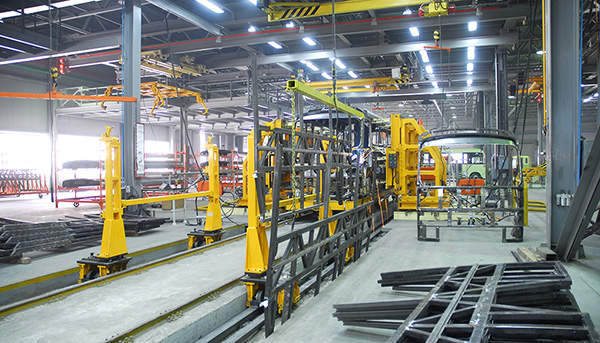
Automotive & EV
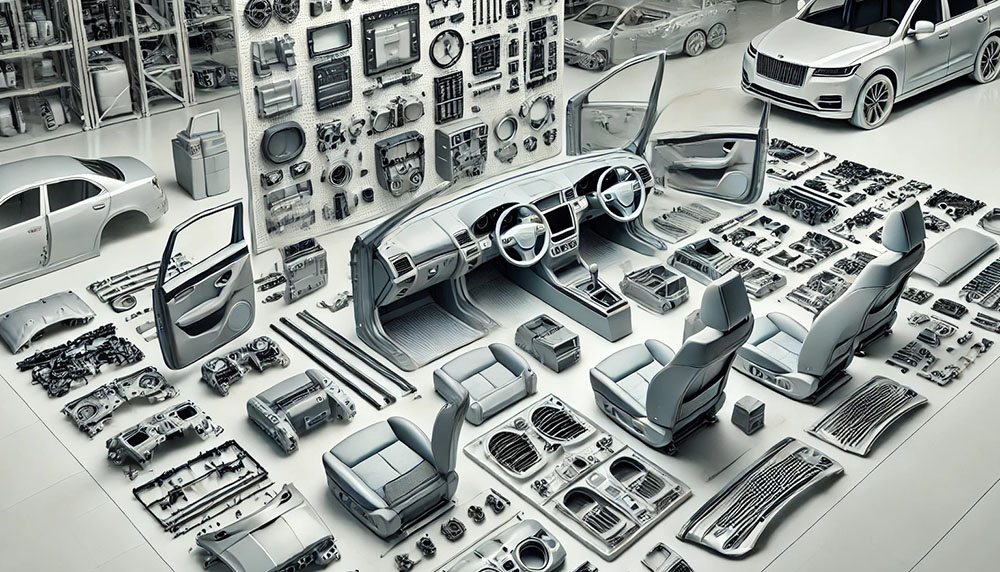
PC injection molding is widely utilized across numerous industries, including Telecommunications, Art and Design, Energy, Construction, and beyond. Commonly used modified plastics such as Glass-Fiber Reinforced PC, PC/PBT, and PC/ABS blends provide enhanced performance and versatility. These materials deliver improved heat resistance, increased durability, and higher strength, making them ideal for demanding applications and environments.
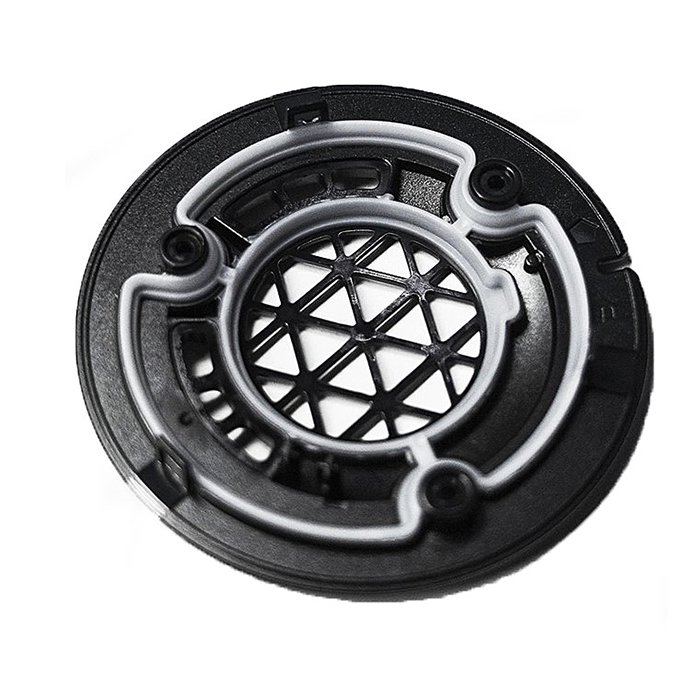
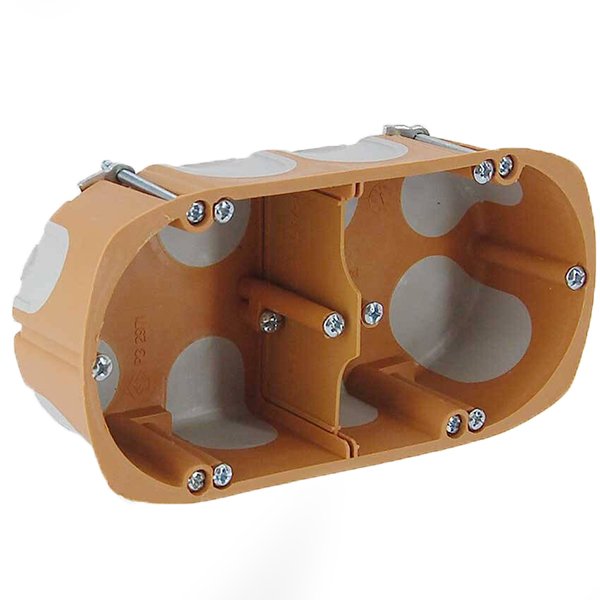
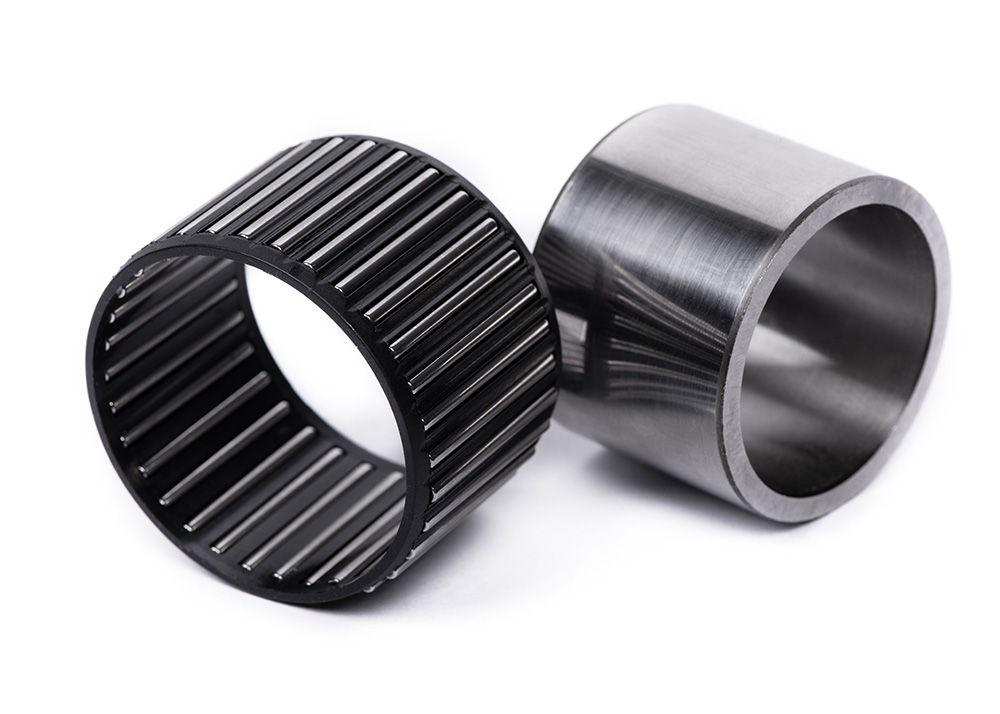
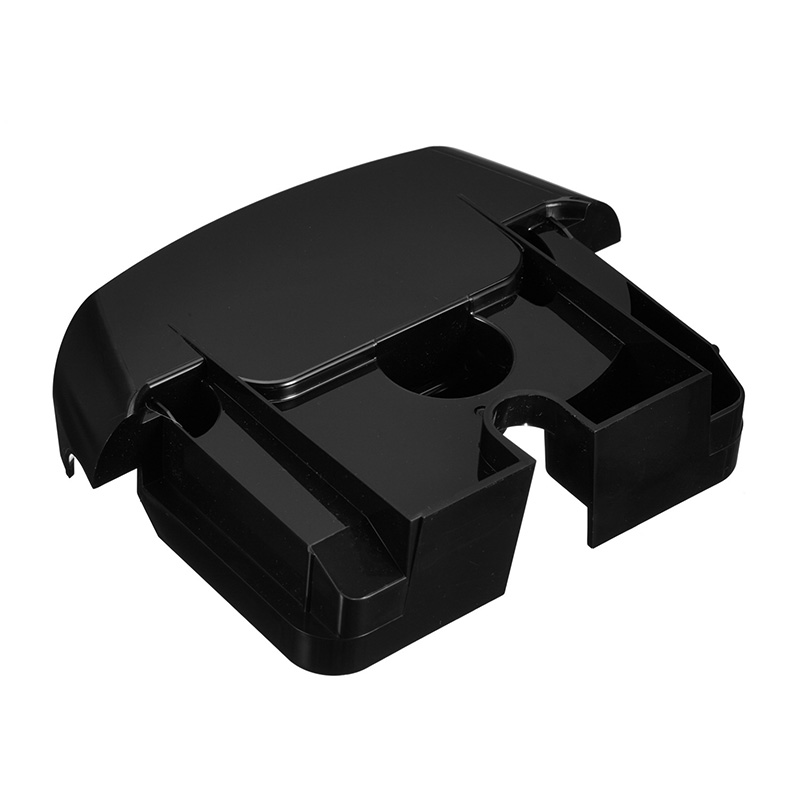

Optimizing PS Material Flow
KingStar Mold ensures smooth material flow during the injection molding process, preventing common defects like short shots and inconsistent fills. Our expertise in process optimization guarantees high-quality, reliable parts every time.
We specialize in designing molds for PS injection molding with tight tolerances and intricate details. Our experienced team uses advanced mold flow analysis to achieve precise and repeatable results.
Effective PS Defect Resolution
KingStar Mold quickly identifies and addresses defects such as warping, sink marks, and surface imperfections. With our thorough testing and quality control systems, we ensure all PS injection molded parts meet the highest standards.
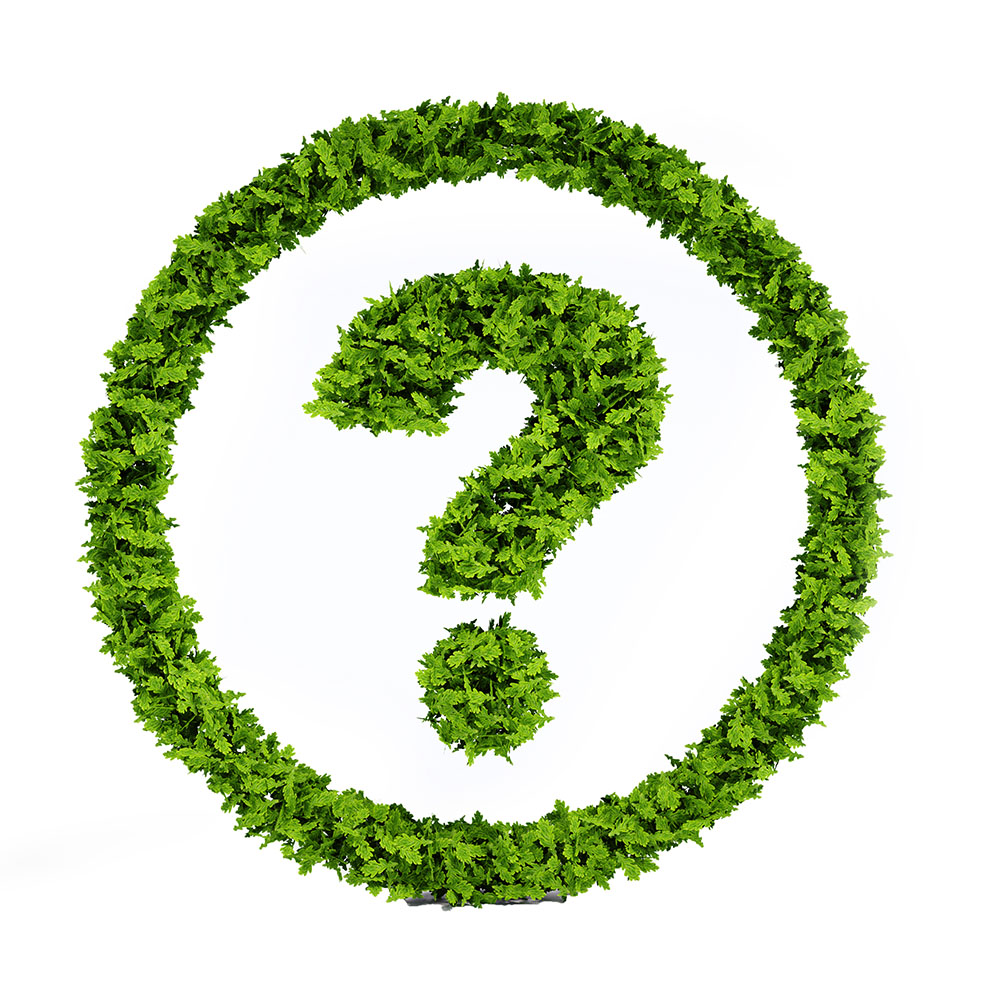
Yes, PS can be molded into both transparent parts, like packaging and light covers, and opaque parts, depending on the application and material formulation.
KingStar Mold uses advanced mold flow analysis, comprehensive quality inspections, and precision molding techniques to ensure that all PS parts meet the highest quality standards.
PS injection molding is widely used in the automotive, electronics, pharmaceutical, packaging, and consumer goods industries.
Common types include HIPS (High Impact Polystyrene), antistatic modified PS, and high-temperature resistant modified PS, each offering different performance characteristics.
PS offers excellent clarity, impact resistance, and low-cost manufacturing, making it ideal for mass production of clear and complex parts.
PS (Polystyrene) injection molding is a process where polystyrene plastic is melted and injected into molds to create various parts, often used for their transparency and ease of molding.
PS materials typically require minimal drying before injection molding, as they are less moisture-sensitive than other plastics, but precise temperature control is still essential to ensure optimal results.
KingStar Mold provides professional DFM (Design for Manufacturing) reviews, offers a comprehensive inspection system, and delivers tailored solutions to meet both anticipated and unanticipated needs in PS injection molding.
PS injection molding is commonly used for products such as automotive instrument housings, electrical casings, packaging materials, medical components, and consumer goods.
Cycle times for PS injection molding are relatively short, typically ranging from 10 to 30 seconds, depending on part size and complexity.
KingStar Mold has extensive experience resolving common and complex defects, using expert design reviews, real-time process monitoring, and thorough quality control checks.
Common defects include sink marks, warping, voids, jetting, and flow lines, which can often be minimized through proper mold design and process optimization.