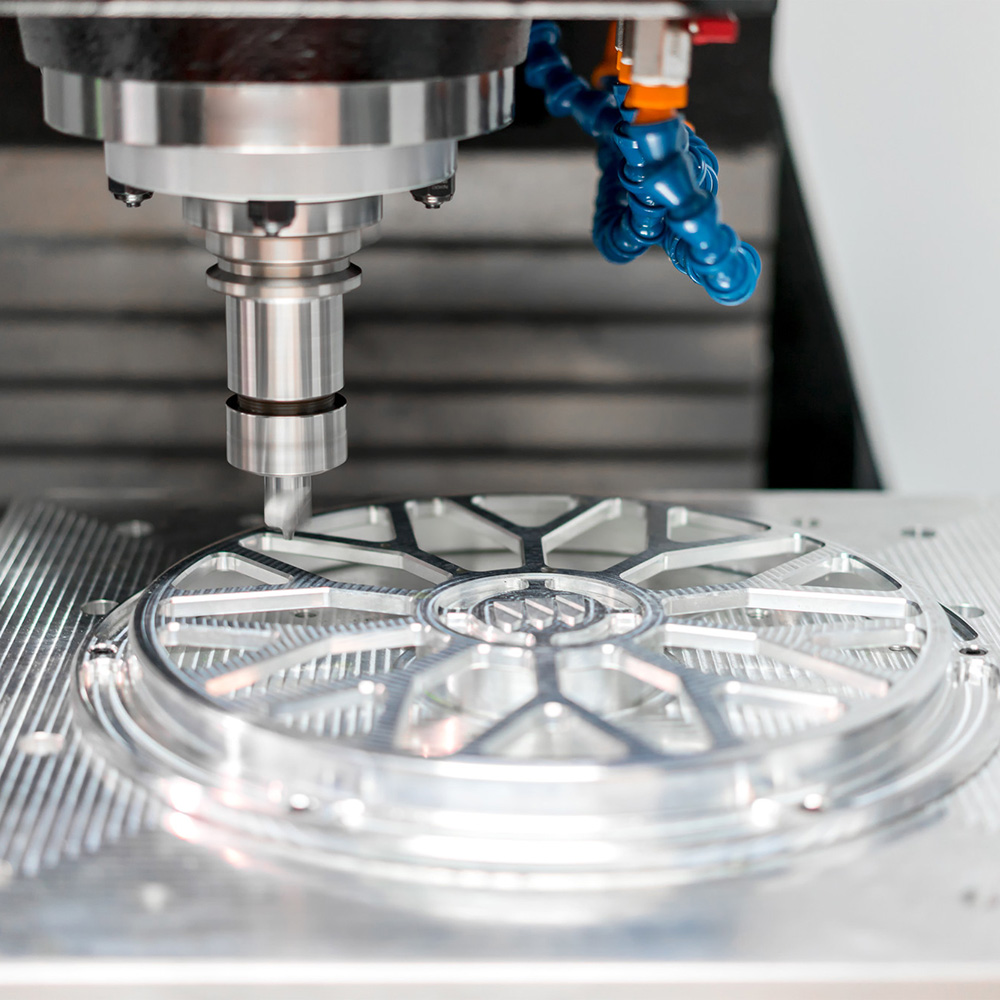
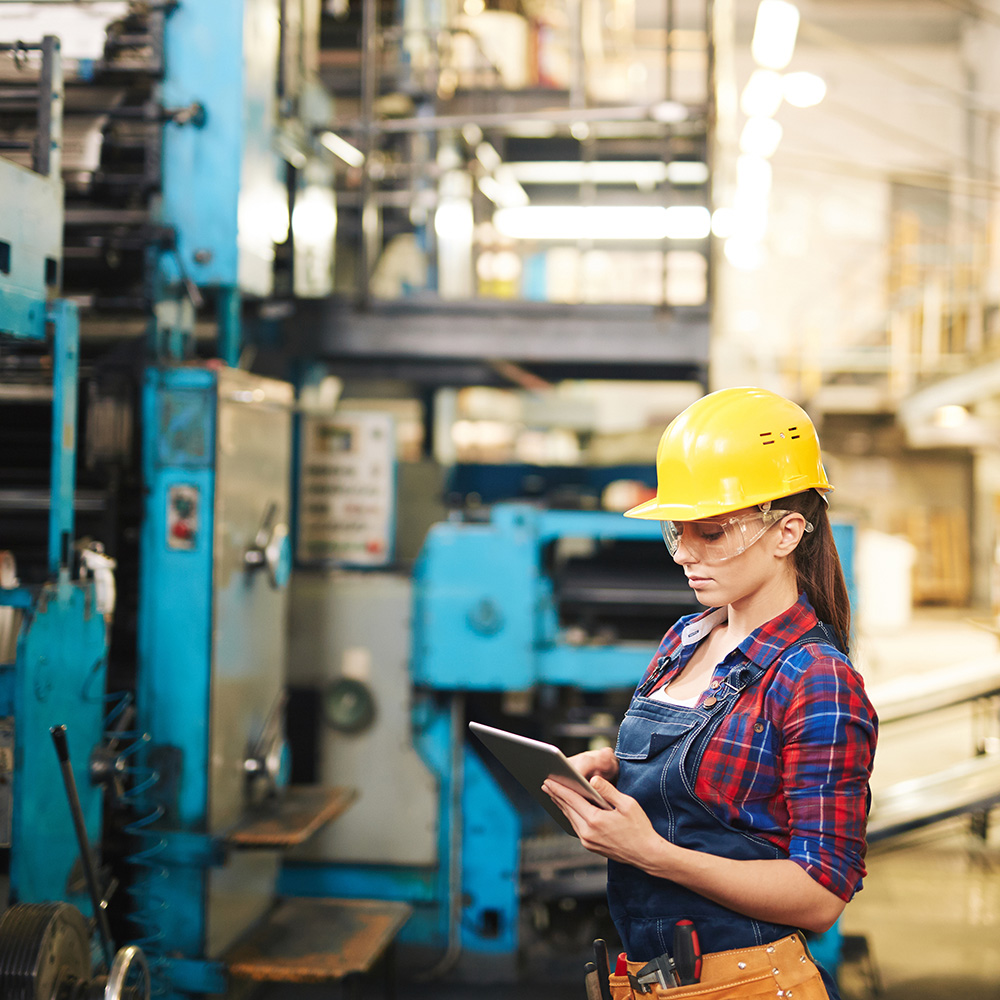
Production Tooling Making Service at KingStar Mold
Efficient, High-Quality Tooling for Mass Production
At KingStar Mold, we provide precision production tooling designed to enhance efficiency and product quality for high-volume manufacturing. Using advanced technology and top-grade materials, we create durable, accurate tools tailored to your production needs, whether for injection molding, die casting, or stamping.
Our service is focused on delivering quick turnaround times without compromising quality. We ensure that your tooling optimizes production processes, minimizes downtime, and maintains consistent precision throughout your manufacturing runs.
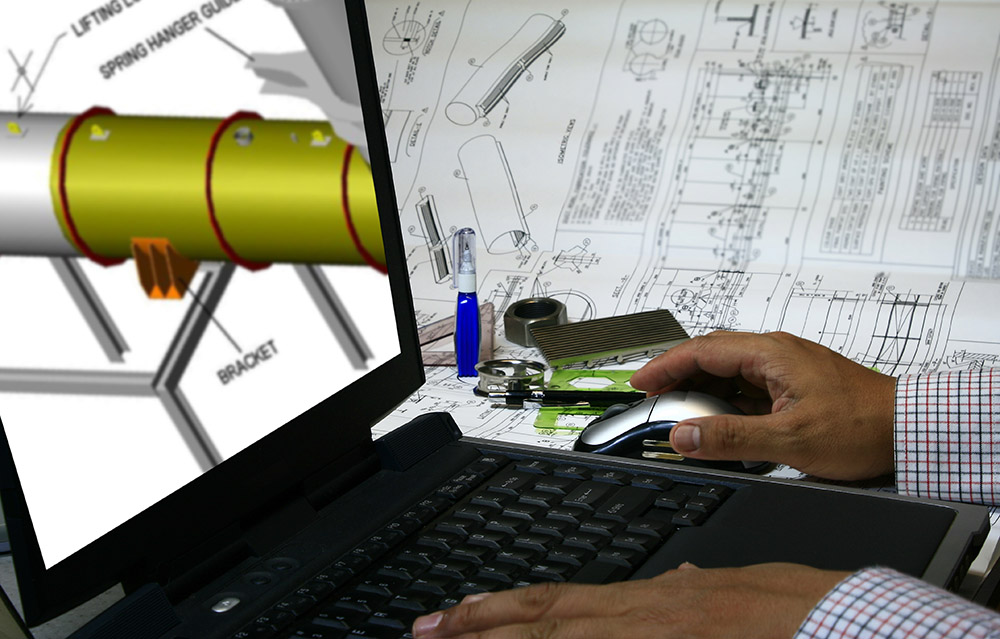
Mold Design
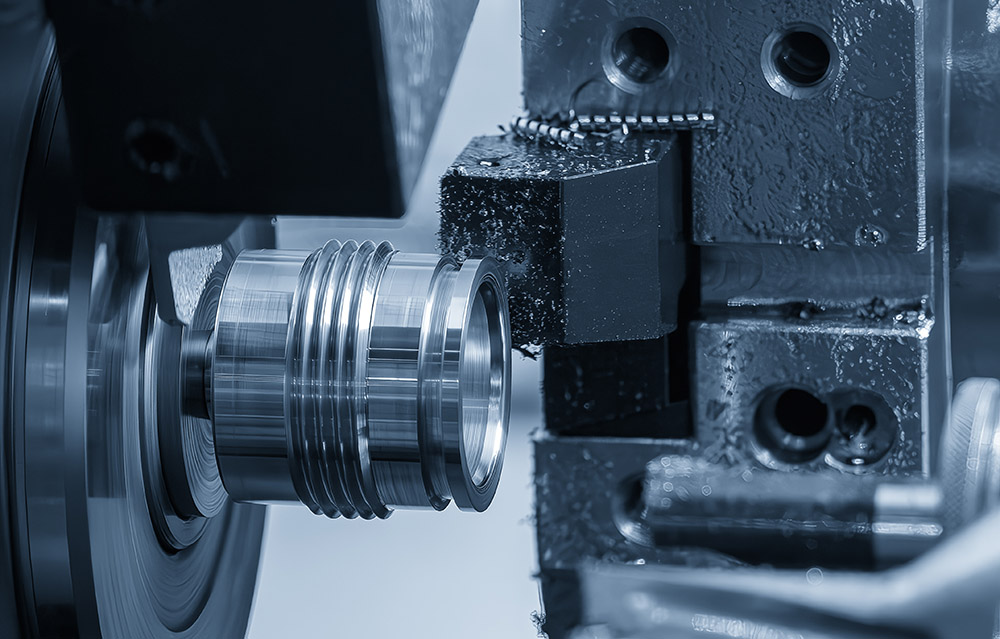
Mold Making
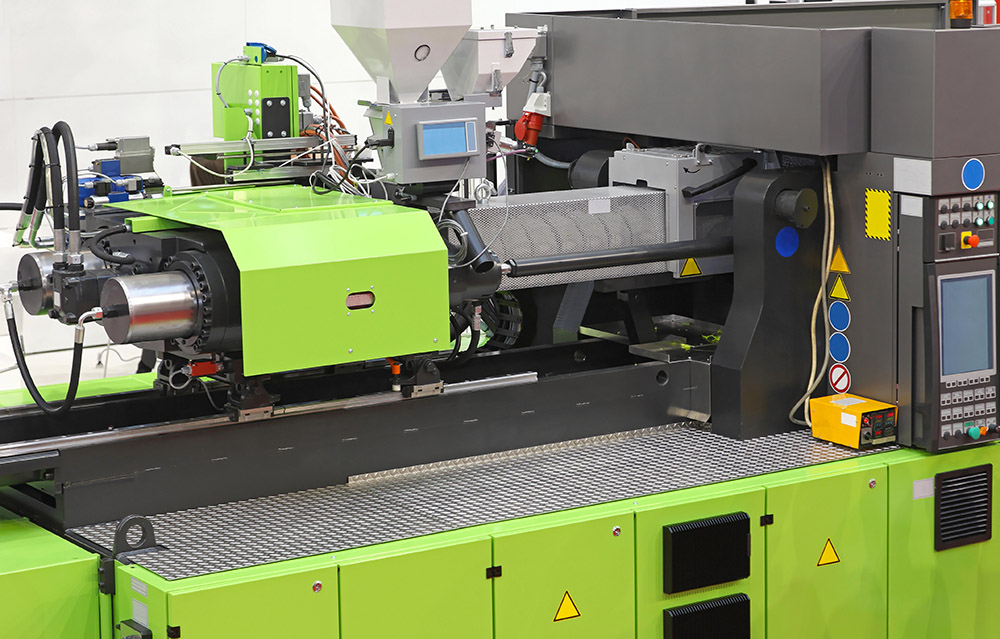
Mass Production
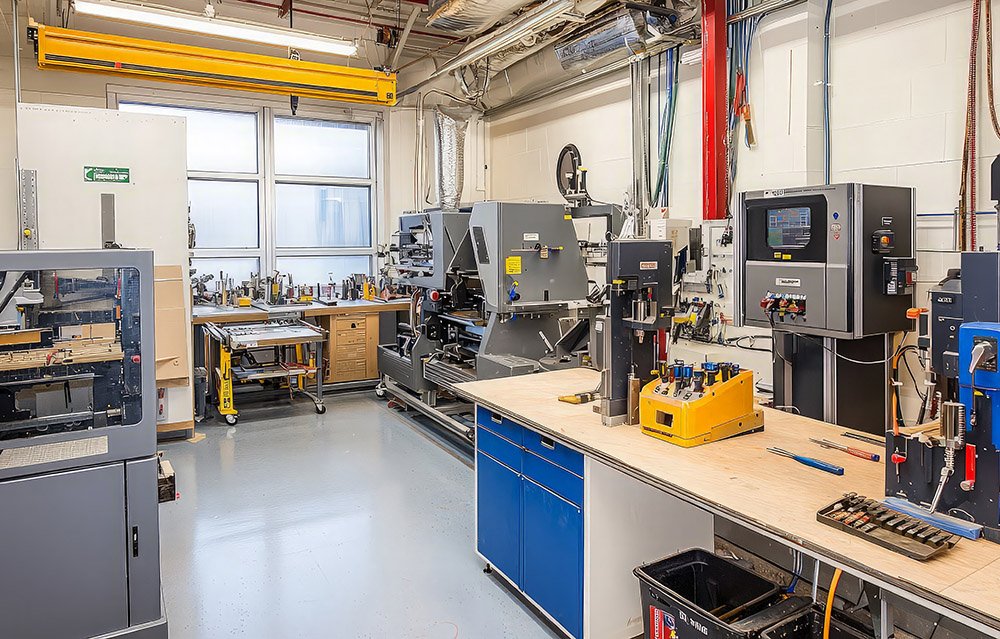
Quality Control
Production Tooling Gallery
Mold Classifications and Standards
Mold classifications and standards play a crucial role in selecting the appropriate mold for a specific manufacturing project. These standards define the mold’s durability, material choice, and suitability for various production volumes. Higher-class molds are designed for long-lasting, high-volume production, ensuring greater precision and fewer maintenance needs. Lower-class molds are often used for shorter production runs or prototypes, where cost-effectiveness and speed are prioritized over longevity. Understanding these classifications allows businesses to make informed decisions, balancing quality, cost, and production requirements for each project.
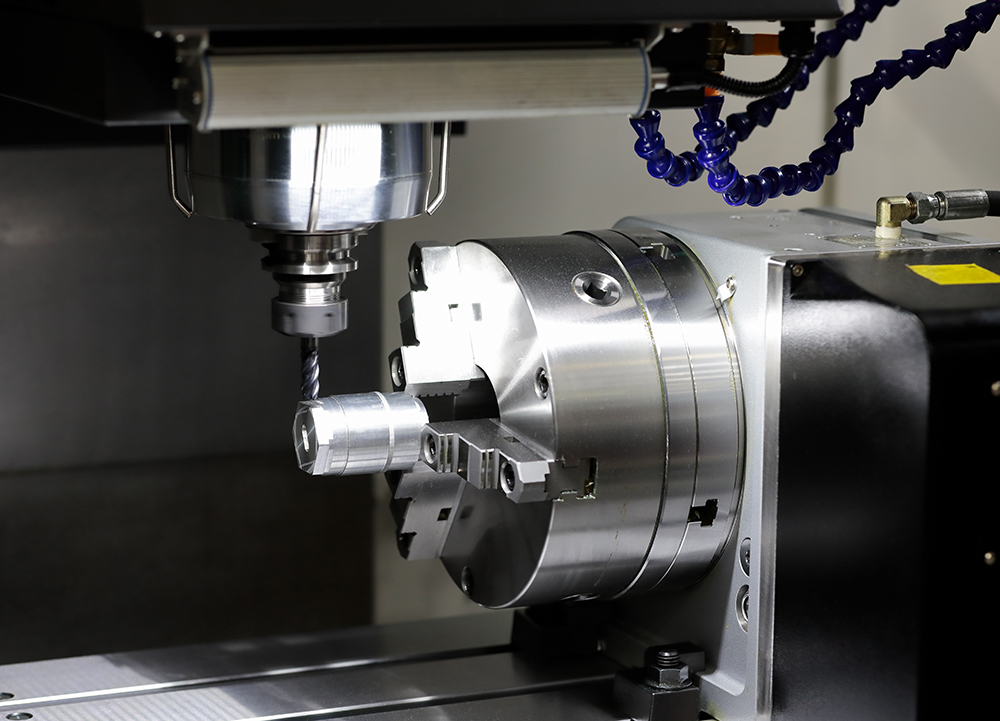
Mold Classification | Description | Typical Materials | Expected Lifespan | Applications |
---|---|---|---|---|
Class 101 | High-performance mold for high-volume, long-lasting production. | P20, H13, stainless steel | 1,000,000+ cycles | Automotive, consumer electronics |
Class 102 | Suitable for medium-volume production with good durability. | P20, H13, beryllium copper | 500,000–1,000,000 cycles | Medical devices, appliances |
Class 103 | Ideal for low to medium-volume runs, with moderate longevity. | Aluminum, P20 | 100,000–500,000 cycles | Toys, packaging, small appliances |
Class 104 | Short-run production molds, less durable but cost-effective. | Aluminum, tool steel | 10,000–100,000 cycles | Prototype molds, low-volume manufacturing |
Class 105 | Prototyping or research molds, used for limited cycles. | Aluminum, soft steels | 1,000–10,000 cycles | Prototyping, rapid tooling |
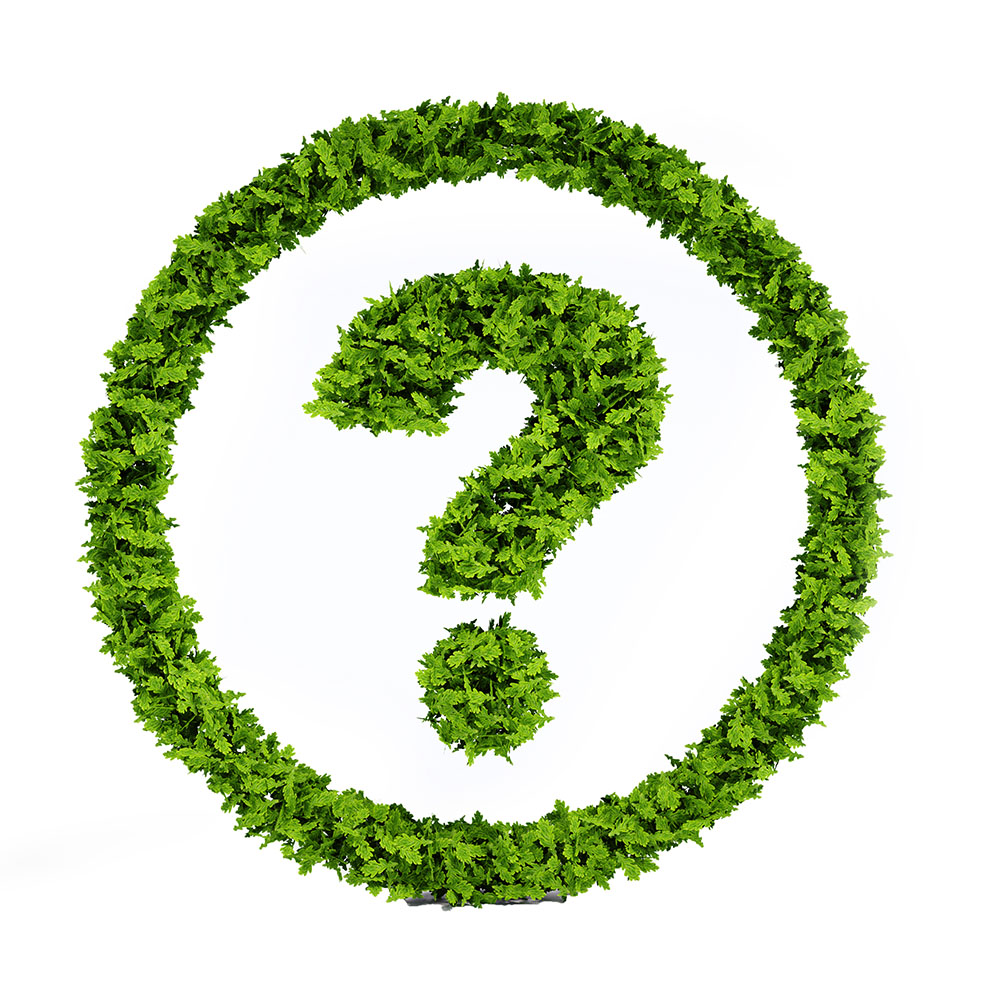
The cost of production tooling depends on factors like design complexity, material choice, and production volume. KingStar Mold provides competitive pricing tailored to your project.
KingStar Mold uses advanced CNC machining, rigorous quality control checks, and high-quality materials to ensure that all production tooling meets the highest standards.
Production tooling is used in industries such as automotive, aerospace, consumer goods, medical devices, electronics, and more.
The time to create production tooling varies based on the complexity and material requirements but typically ranges from a few weeks to a few months.
Common materials include tool steels (P20, H13), beryllium copper, aluminum, and various high-strength alloys depending on the production requirements.
It ensures that parts are produced with high precision and consistency, helping to reduce defects and increase efficiency in mass production.
Production tooling refers to the tools, molds, and dies used in the manufacturing process to produce high-quality, consistent parts in large quantities.
Simply contact KingStar Mold with your project specifications, and our team will guide you through the tooling design and production process, from concept to delivery.
Regular inspection and maintenance are required to ensure tools remain in optimal condition, including cleaning, lubrication, and part replacements when necessary.
KingStar Mold offers design revisions and tooling adjustments to accommodate changes during production without compromising on quality or timelines.
Prototype tooling is designed for testing and validation of product designs, while production tooling is built for high-volume manufacturing and durability.
Yes, KingStar Mold is equipped to handle both small prototype runs and large-scale production, ensuring flexibility to meet customer needs.