Small Batch Of Table Connectors Producing by Insert Molding Process
Application Industry | Tools & Equipment |
Tolerance(Accuracy) | Parts: ±0.03mm |
Manufacturing Process | Insert Molding Service |
Mold Type | Rapid Tooling |
Parts Material | PA66+50%GF, Brass |
Surface Treatment | None |
What mattered most to them
The tricky parts of small-batch work
How we fixed it
What happened in the end
Requirement Category | Specific Data |
---|---|
Production Volume | – Base quantity: 300 units per quarter – Flexibility: Adjustable to 200–400 units with 2 weeks’ notice |
Durability | – Static load resistance: Withstand 35kg (equivalent to typical desktop loads) without deformation – Assembly cycle endurance: Maintain integrity through 800+ assembly/disassembly cycles (matching 3–4 year workstation lifespan) |
Dimensional Precision | – Alignment tolerance: ±0.03mm (to fit pre-drilled tabletop holes for seamless assembly) |
Turnaround Time | – Batch delivery: Complete within 10 business days of order confirmation to avoid client production delays |
Cost Parameters | – Per-unit production cost cap: Under $3 (to support mid-tier pricing competitive with mass-produced alternatives) |
Frequently Asked Questions
No worries—our case studies focus on the usual kinds of problems, but we deal with unique or tricky challenges all the time. Even if your specific issue isn’t featured, the problem-solving approach and technical skills you see in the case studies still apply. Send us a note with what you’re up against, and we’ll walk through how we’d tackle it for you.
We keep our case studies fresh—they show the methods we actually use right now. When we start using new tools, materials, or process fixes (like better mold simulation software or greener plastics), we update the case studies to include those too. That way, what you’re seeing matches how we work in today’s manufacturing landscape.
If a case study clicks with what you’re working on, just get in touch with our team. Share the details of your project, and we’ll talk through how the strategies highlighted—like material pairing, mold tweaks, or process adjustments—might fit your goals. If needed, we can also craft custom solutions that match what you need.
Feel free to reach out at sales@kingstarmold.com to start the conversation.
Yes, all our case studies are based on real client collaborations. To protect our clients’ rights, we only share details that have been approved for disclosure—including specific timelines, challenges, solutions, and measurable outcomes, all backed by data from client production records or third-party testing.
Each case study delves deeply into specific issues, such as how to extend the lifespan of components or how to accelerate production speed, and shows you how we solved these problems. Even if your project is not exactly the same as them, these cases can help you clearly understand how we handled the issues: breaking down the problem, adjusting the method, and achieving results. This enables you not only to see the outcomes we have achieved, but also to understand how we think about solutions – so you can roughly judge whether we can meet the requirements of your project.
Note:
We maintain pre-market confidentiality agreements and sign NDA/NNN with all our customers. Every case you see has been shared with client approval. To protect sensitive information, some details have been blurred or modified. All photos were taken internally by KingStar Mold. Thank you for your support and cooperation.
One-Stop Manufacturing Service that Fits Your Product Life Cycle
Our Custom Manufacturing Services
Your one-stop solution for enhancing your product’s market potential.
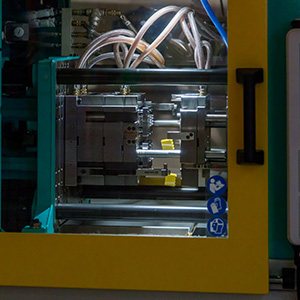
Injection Molding
We offer comprehensive services of injection molding, producing a wide range of parts through two-shot molding, overmolding and custom molding techniques.
Mold Making
At KingstarMold, we develop and produce precision die-casting molds, injection molds, stack molds, and two-color molds using state-of-the-art equipment.
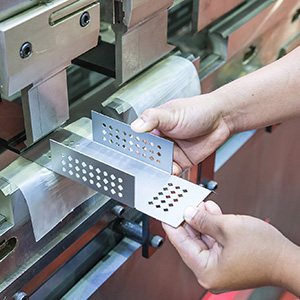
Sheet Metal Fabrication
We provide precise sheet metal fabrication solutions, offering custom-made parts with exceptional durability, tailored to meet the specific requirements of your project.
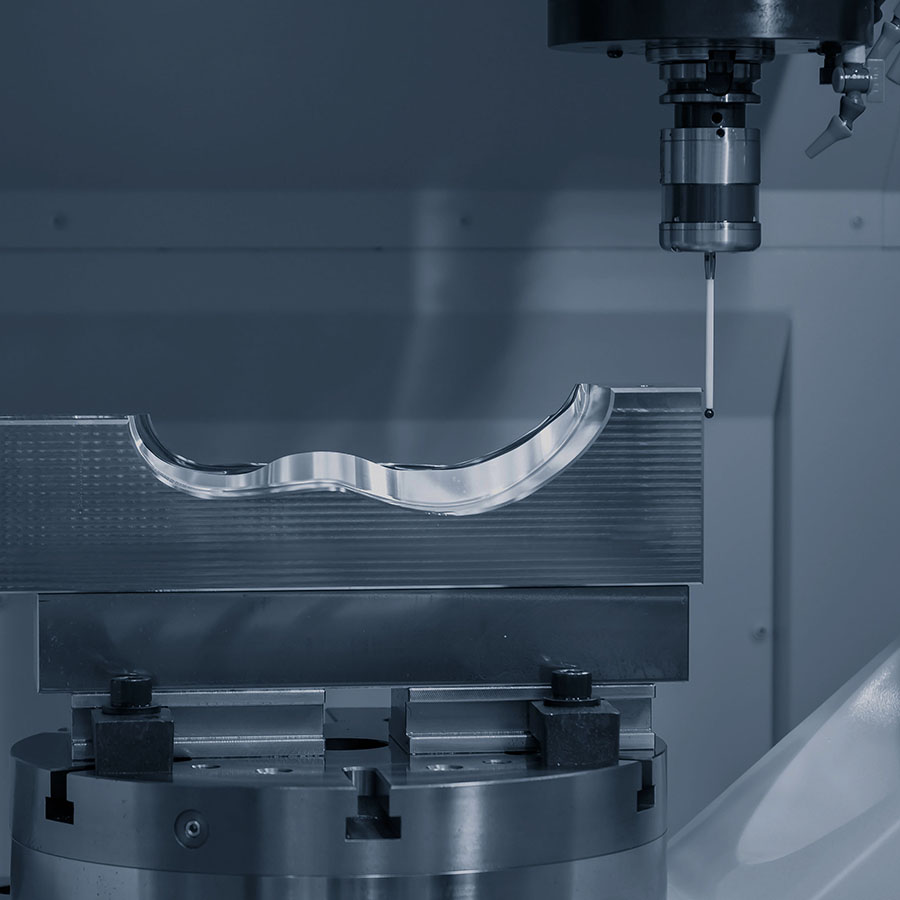
CNC Machining
Our CNC machining includes both 4-axis and 5-axis capabilities, with a focus on optimizing equipment arrangement to enhance efficiency.
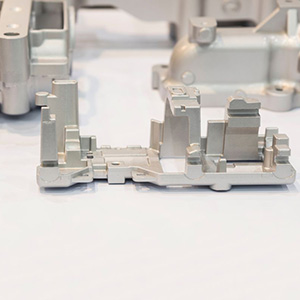
Die Casting
Our die casting service ensures high-precision, high-volume production of metal parts with excellent surface finishes and tight tolerances.
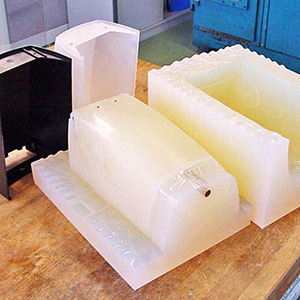
Vacuum Casting
With vacuum casting, we produce high-quality, detailed prototypes and low-volume parts with exceptional accuracy.