Electric Scooter Wheel Hubs Producing by Insert Molding
Parts Material | PA6+30%GF, Steel |
Application Industry | Tools & Equipment |
Manufacturing Process | Mold Making Service & Insert Molding Service |
Mold Type | Production Tooling |
Tolerance(Accuracy) | Parts: ±0.1mm(±0.004″) |
Surface Treatment | Standard Smooth |
The Problems We Ran Into
How We Fixed It
What Happened Next
Requirement Category | Details |
---|---|
Material Combination | Wheel body: PA6+30%GF (for lightweight and wear resistance); core: Steel hardware (for structural rigidity) |
Bond Strength | Steel-plastic interface must withstand ≥1,200N of force (to resist curb impacts in urban use) without separation |
Alignment Stability | Steel hardware must remain centered in the PA6+30%GF body to avoid wheel wobble during operation (typical commuting speeds: 15–20km/h) |
Resistance to Internal Stress | Minimize micro-cracking at the steel-plastic interface, even after 500+ rotation cycles (to ensure long-term structural integrity) |
Durability | Withstand repeated urban use (including uneven roads and curb impacts) over the scooter’s typical lifespan |
Dimensions | Confidential (optimized for scooter wheel assembly) |
Cost Parameters | Confidential (aligned with production feasibility and market competitiveness) |
Frequently Asked Questions
No worries—our case studies focus on the usual kinds of problems, but we deal with unique or tricky challenges all the time. Even if your specific issue isn’t featured, the problem-solving approach and technical skills you see in the case studies still apply. Send us a note with what you’re up against, and we’ll walk through how we’d tackle it for you.
We keep our case studies fresh—they show the methods we actually use right now. When we start using new tools, materials, or process fixes (like better mold simulation software or greener plastics), we update the case studies to include those too. That way, what you’re seeing matches how we work in today’s manufacturing landscape.
If a case study clicks with what you’re working on, just get in touch with our team. Share the details of your project, and we’ll talk through how the strategies highlighted—like material pairing, mold tweaks, or process adjustments—might fit your goals. If needed, we can also craft custom solutions that match what you need.
Feel free to reach out at sales@kingstarmold.com to start the conversation.
Yes, all our case studies are based on real client collaborations. To protect our clients’ rights, we only share details that have been approved for disclosure—including specific timelines, challenges, solutions, and measurable outcomes, all backed by data from client production records or third-party testing.
Each case study delves deeply into specific issues, such as how to extend the lifespan of components or how to accelerate production speed, and shows you how we solved these problems. Even if your project is not exactly the same as them, these cases can help you clearly understand how we handled the issues: breaking down the problem, adjusting the method, and achieving results. This enables you not only to see the outcomes we have achieved, but also to understand how we think about solutions – so you can roughly judge whether we can meet the requirements of your project.
Note:
We maintain pre-market confidentiality agreements and sign NDA/NNN with all our customers. Every case you see has been shared with client approval. To protect sensitive information, some details have been blurred or modified. All photos were taken internally by KingStar Mold. Thank you for your support and cooperation.
One-Stop Manufacturing Service that Fits Your Product Life Cycle
Our Custom Manufacturing Services
Your one-stop solution for enhancing your product’s market potential.
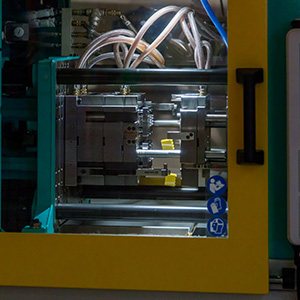
Injection Molding
We offer comprehensive services of injection molding, producing a wide range of parts through two-shot molding, overmolding and custom molding techniques.
Mold Making
At KingstarMold, we develop and produce precision die-casting molds, injection molds, stack molds, and two-color molds using state-of-the-art equipment.
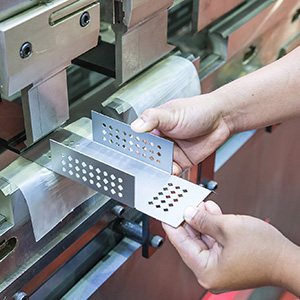
Sheet Metal Fabrication
We provide precise sheet metal fabrication solutions, offering custom-made parts with exceptional durability, tailored to meet the specific requirements of your project.
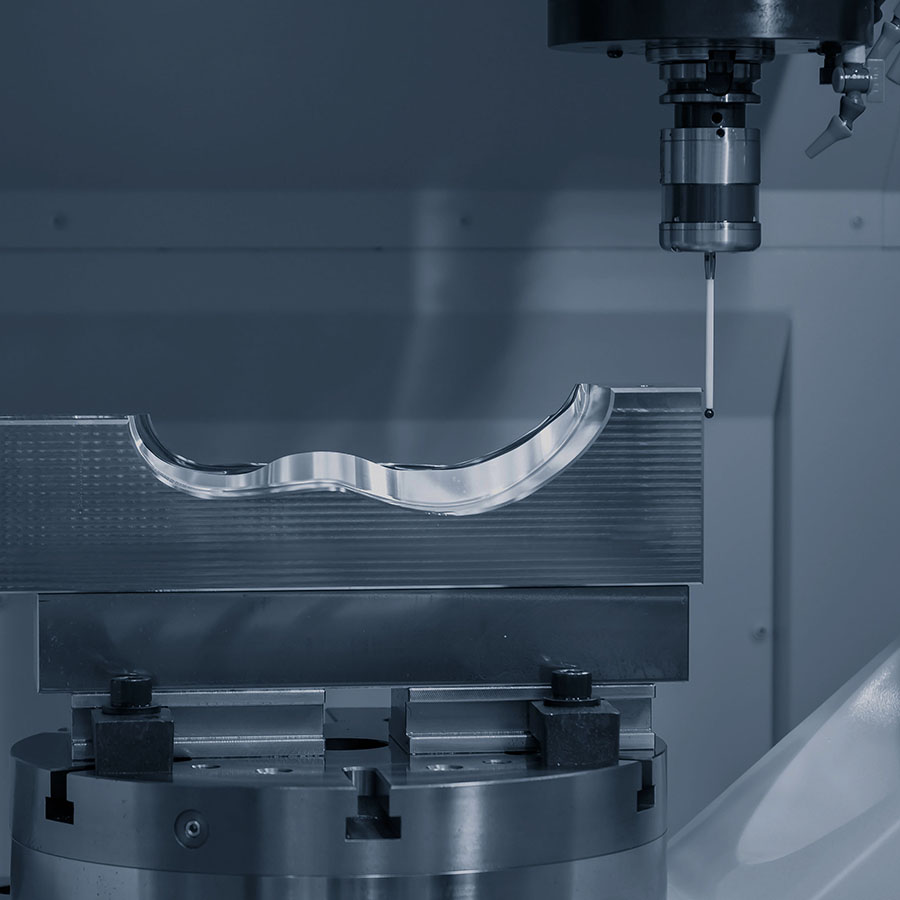
CNC Machining
Our CNC machining includes both 4-axis and 5-axis capabilities, with a focus on optimizing equipment arrangement to enhance efficiency.
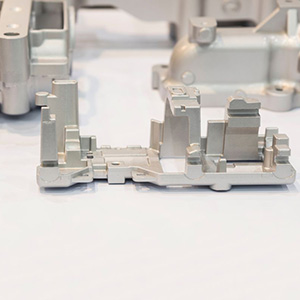
Die Casting
Our die casting service ensures high-precision, high-volume production of metal parts with excellent surface finishes and tight tolerances.
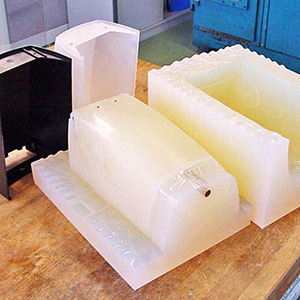
Vacuum Casting
With vacuum casting, we produce high-quality, detailed prototypes and low-volume parts with exceptional accuracy.