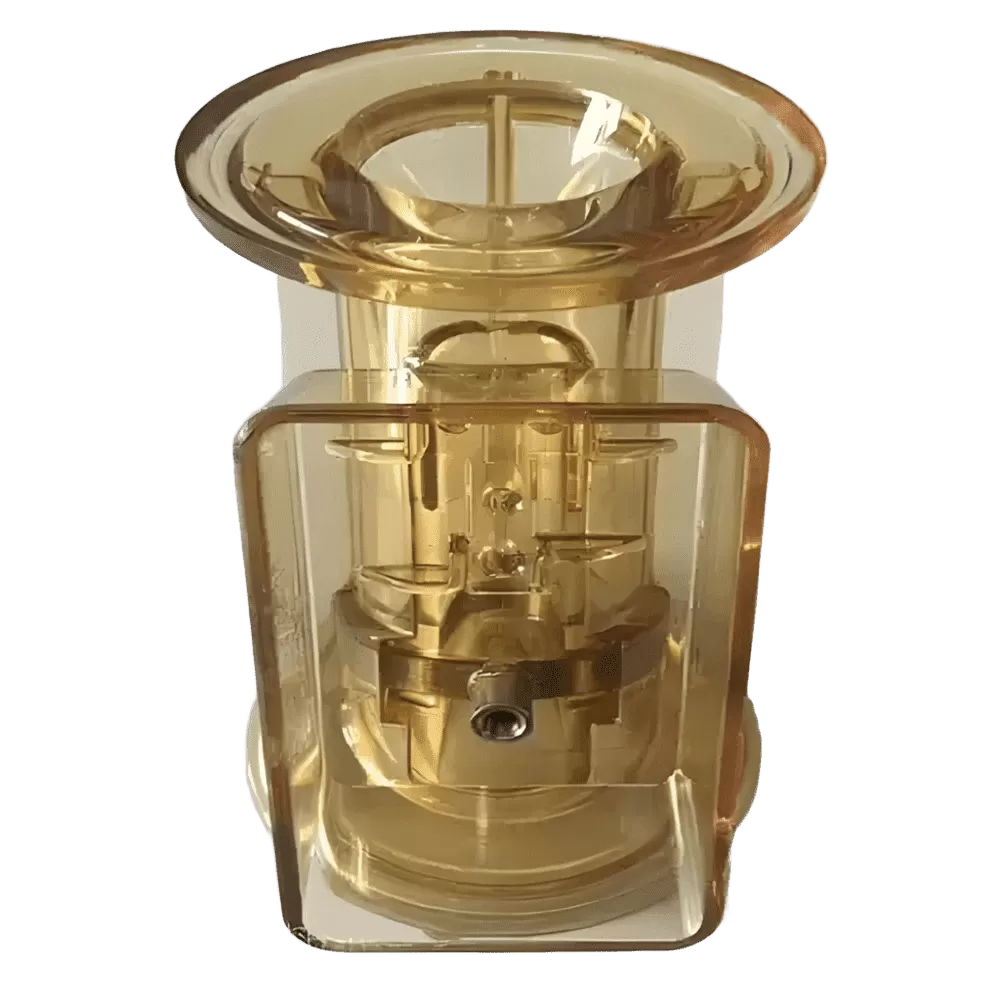
Resources for The Complete Guide to PPSU Injection Molding
What is PPSU?

What types of PPSU materials are there?
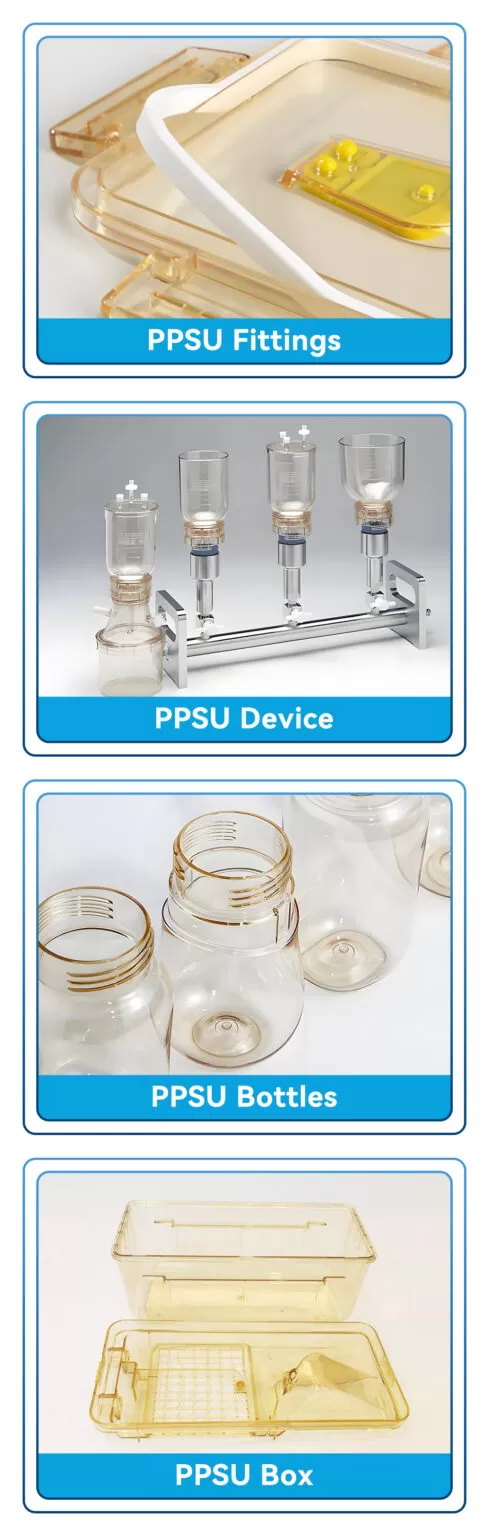
What are the properties of PPSU?
Property | Polyphenylsulfone (BPA Type) | Polyphenylsulfone | Polyethersulfone |
PSU/PSF | PPSU | PES | |
Heat Distortion Temperature (℃) | 174 | 207 | 204 |
Relative Density | 1.24 | 1.29 | 1.37 |
Tensile Strength (MPa) | 70 | 94 | 86 |
Elongation (%) | 50–60 | 60–120 | 40–80 |
Compressive Strength (MPa) | 280 | 150 | 130 |
Flexural Strength (MPa) | 107 | 127 | 136 |
Impact Strength (Notched) (KJ/m²) | - | 690 | 23 |
Hardness (Rockwell) | M69 (R120) | M110 | M88 |
Flexural Modulus, 23℃ (GPa) | 2.7 | 2.6 | 2.6 |
Tensile Modulus, 23℃ (GPa) | 2.2 | 2.4 | - |
Specific Heat (J/Kg·K) | 1004.83 | - | - |
Thermal Expansion Coefficient 10cm/cm (℃) | 1.7 | - | - |
Heat Distortion Temperature (1.86 MPa) (℃) | 174 | 207 | 203 |
Heat Distortion Temperature (0.45 MPa) (℃) | 181 | - | 210 |
Maximum Continuous Service Temperature (℃) | 140 | 180 | 180 |
Electrical Resistivity 23℃ (Ω·cm) | 5×10 | 3.2×10 | 10 |
Dielectric Strength (KV/mm) (Short-term) | 3 | 6.3 | 16 |
Dielectric Constant 60Hz | 3.07 | 3.94 | 3.5 |
Dielectric Constant 1000Hz | 3.06 | 3.24 | 3.5 |
Dielectric Loss 60Hz | 0.0008 | - | - |
Dielectric Loss 1000Hz | 0.001 | - | - |
Water Absorption 24h, 3.2mm Sample (%) | 0.22 | 0.37 | 0.43 |
What are the advantages of PPSU Injection Molding?
What are the shortcomings of PPSU Injection Molding?
PPSU (polyphenylsulfone) injection molding offers numerous benefits, but there are a few limitations to consider:
- High Melting Point: PPSU has a very high melting point, which requires precise heating before injection molding to ensure it flows properly. This high-temperature requirement adds complexity and demands careful temperature control during processing.
- Limited Post-Molding Operations: Due to its sensitivity to heat, moisture, and chemicals, PPSU can be easily damaged after molding. This limits post-molding processes like machining, grinding, or assembly, making it more difficult to work with once formed.
- High Warpage: PPSU tends to warp significantly during cooling, making it challenging to control during the molding process. This warpage may require design adjustments or additional steps to mitigate.
- Limited Recycling Options: PPSU’s complex chemical structure and high molecular weight make it difficult to recycle. This results in environmental concerns and adds to material waste.
- High Viscosity: PPSU’s high viscosity makes it difficult to perform complex molding operations. The material resists flowing smoothly, making precision molding and processing a challenge.
- Long Cycle Time: The high viscosity of PPSU means it takes longer to flow during the injection molding process. This increases production time and costs, slowing down the overall manufacturing process.
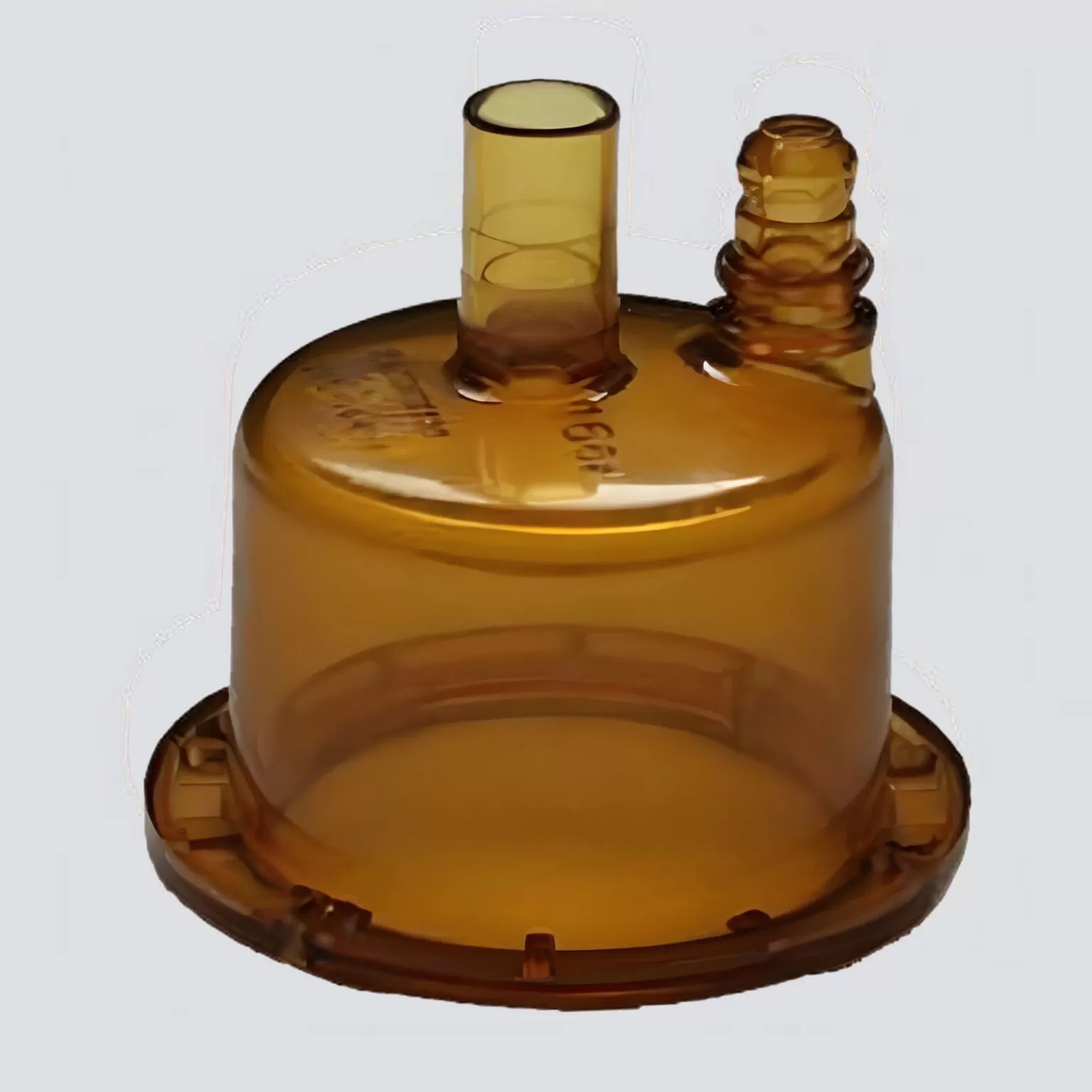
Can PPSU be Injection Molded?
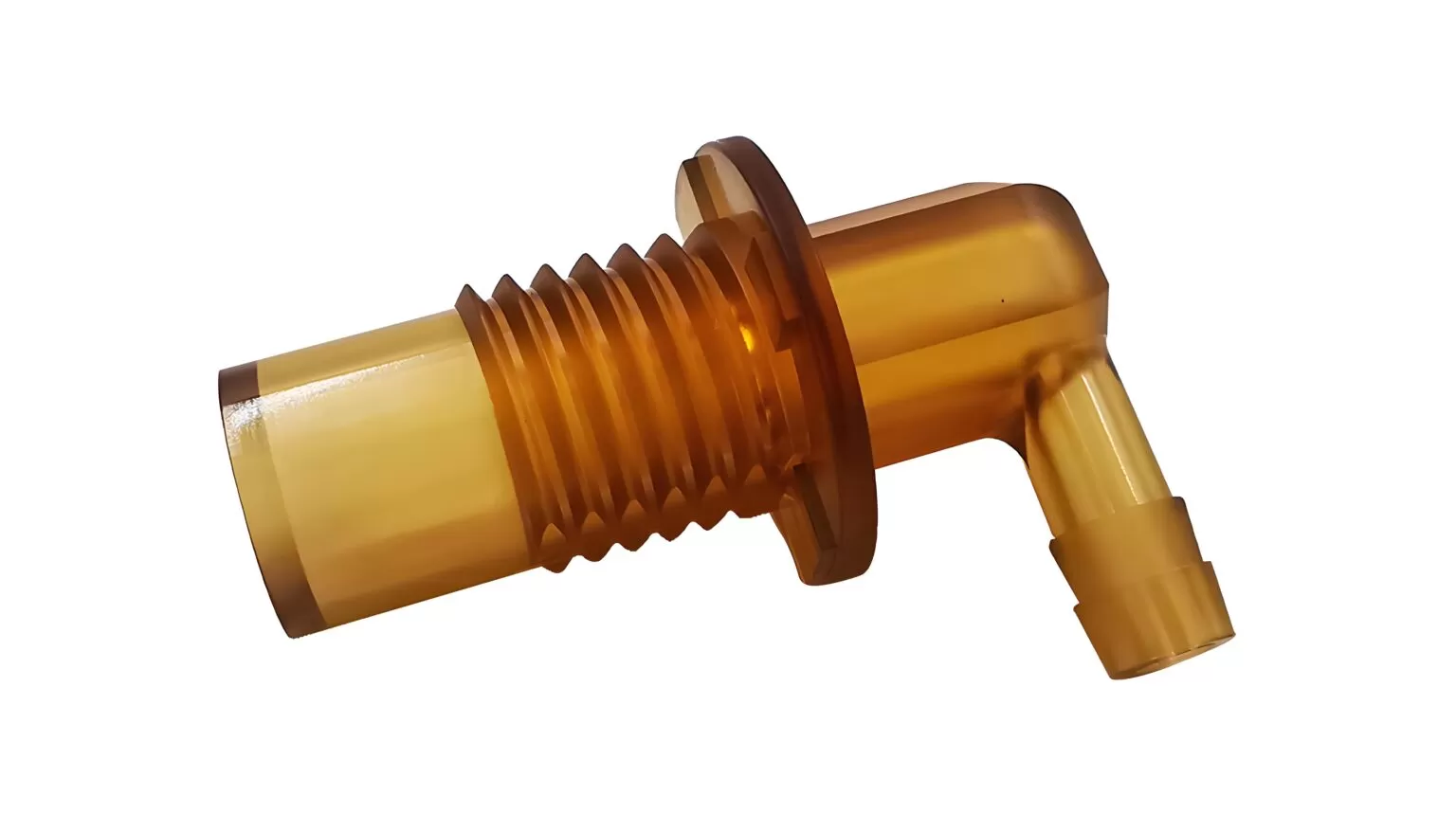
How to Perform PPSU Injection Molding: A Step-by-Step Guide
PPSU injection molding is a widely used method for creating durable, high-performance parts from thermoplastic materials. This guide will walk you through the entire process, from preparation to completion, ensuring you achieve optimal results with PPSU.
- Injection Molding Process:
a. Machine Setup: Use standard injection molding machines with a clamp tonnage around 5.5 kN/cm² (4 T/in²). The screw should have a compression ratio between 1.8:1 and 2.4:1, with a length-to-diameter (L/D) ratio of 18:1 to 22:1. Opt for a ring-check valve instead of a ball-check valve for improved performance.
b. Injection Parameters: Set appropriate injection speed, pressure, and temperature. For PPSU, typical melt temperatures range from 350°C to 400°C (662°F to 752°F). Injection cycle times typically range from 15 to 60 seconds, depending on the part size and complexity.
c. Mold Filling: Ensure the injection speed is controlled to avoid issues like splay or short shots. Monitor the melt flow and adjust settings to ensure the mold cavity is completely filled.
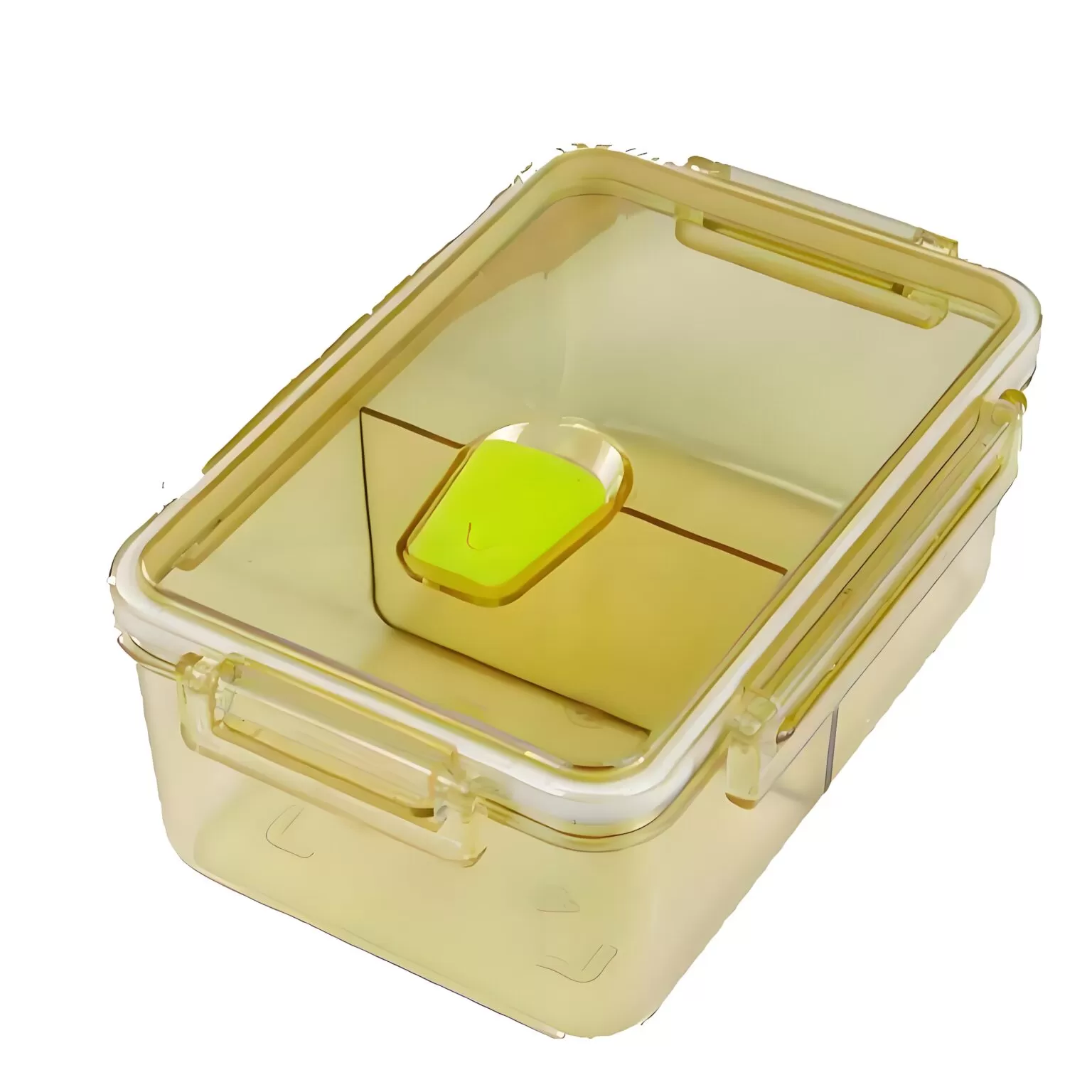
What are the challenges of PPSU Injection Molding?
PPSU is a polymer known for its high temperature resistance, chemical stability, rigidity, and dimensional stability. These features make it a popular choice for industries such as medical equipment, electronics, automotive, and food-grade products. However, despite its many advantages, the injection molding of PPSU presents certain challenges, as outlined below:

- High Melting Point: PPSU has a very high melting point, making it difficult to melt and inject into the mold. It requires precise temperature control and specialized equipment to process the material effectively.
- High Viscosity: PPSU has a high viscosity, which makes high-precision or complex injection molding difficult. Reducing its viscosity and increasing fluidity requires the use of special injection molding technology or additives.
- High Material Cost: Compared to other plastics, PPSU material is relatively expensive, and the production cost is increased further by its difficult processing characteristics.
- Low Impact Strength: Due to its relatively low impact strength, PPSU is more prone to damage during the injection molding process, especially when using general molding techniques.
What are the Applications of PPSU Injection Molding?
PPSU (Polyphenylsulfone) is a high-performance thermoplastic known for its exceptional heat and pressure resistance, making it ideal for injection molding. It’s used across various industries because of its ability to withstand high temperatures and harsh chemicals. Here are some of the most common applications of PPSU injection molding:
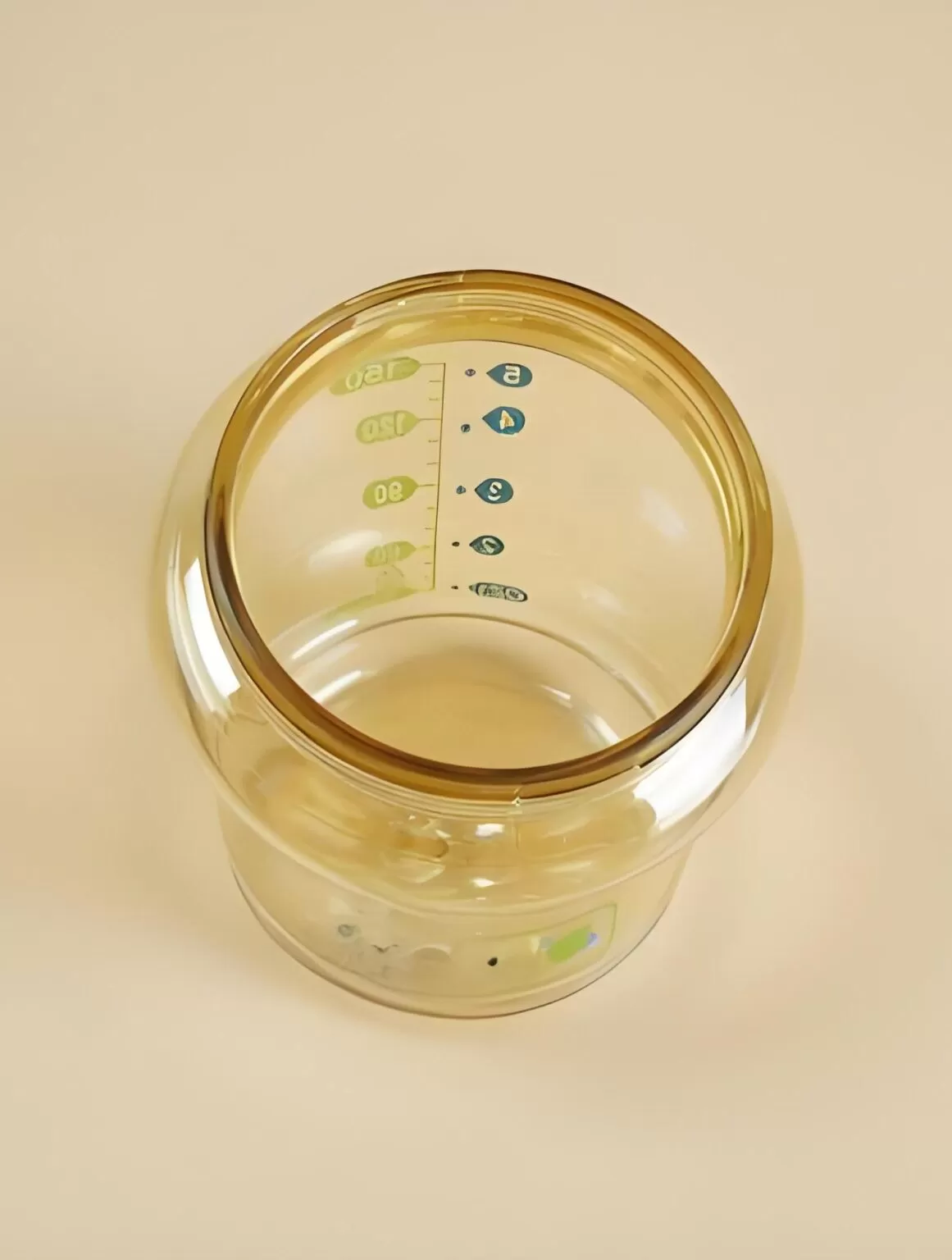
- Food Processing: PPSU is widely used in food processing equipment such as valves, pumps, and pipes due to its ability to resist corrosion, withstand high temperatures, and handle chemicals without degradation.
- Aerospace: In the aerospace sector, PPSU is utilized to produce lightweight, high-performance parts, including components for airplanes, satellites, and engines, thanks to its durability and resistance to extreme conditions.
- Medical Devices: PPSU’s biocompatibility and resistance to chemicals make it a top choice for medical devices, including surgical instruments, diagnostic tools, and implantable devices that require sterilization and long-term performance.
- Automotive: The automotive industry relies on PPSU for high-performance parts like fuel injectors, engine components, and brake parts, where its heat resistance and mechanical strength are essential.
- Industrial Equipment: PPSU’s resistance to chemicals, high temperatures, and mechanical stress makes it ideal for industrial applications such as pumps, valves, and gears that need to perform under tough conditions.
- Consumer Products: From household appliances to electronics and sporting goods, PPSU is favored for its toughness, chemical resistance, and appealing aesthetic qualities, making it a versatile material for a range of consumer products.
- Chemical Processing: PPSU is commonly used in chemical processing equipment such as reactors, tanks, and pipes due to its excellent resistance to corrosion, chemicals, and high temperatures, ensuring long-term durability and performance.
- Oil and Gas: In the oil and gas industry, PPSU is employed in parts like pumps, valves, and pipes, where its ability to resist corrosion, chemicals, and extreme temperatures makes it ideal for challenging environments.
- Pharmaceutical: PPSU is used in pharmaceutical equipment, including reactors, tanks, and pipes, because of its resistance to corrosion, chemicals, and high temperatures, making it a reliable choice for this demanding industry.
- Biomedical: PPSU is favored in biomedical applications, including surgical instruments, implantable devices, and diagnostic equipment, due to its biocompatibility, resistance to chemicals, and sterilizability, ensuring safety and effectiveness in medical environments.