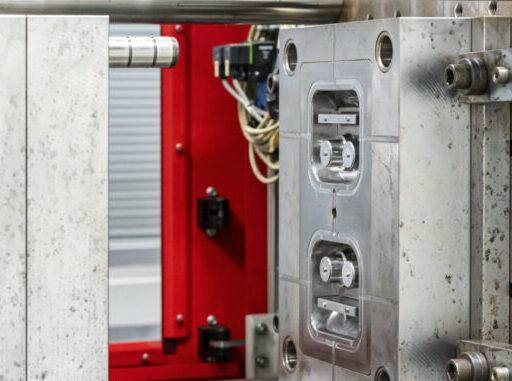
PPS Injection Molding Overview
PPS (Polyphenylene Sulfide) is a high-performance material known for its excellent resistance to high temperatures and flame retardancy, often outperforming other engineering plastics. By incorporating glass fibers, carbon fibers, and various fillers, PPS can be modified to enhance its mechanical properties, making it suitable for challenging applications in industries like automotive, electronics, and aerospace.
Despite its higher cost, PPS is becoming increasingly favored due to its superior performance in extreme conditions. At KingStar Mold, we bring over ten years of experience in PPS injection molding, ensuring efficient production and quick resolution of any molding defects, delivering precise and reliable parts for diverse industries.
Automotive Components
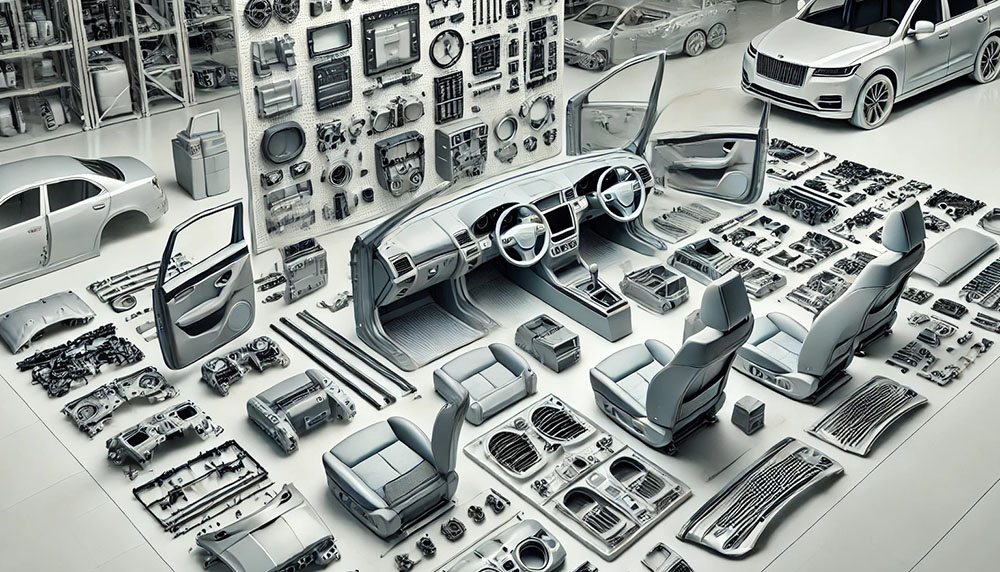
Consumer Goods
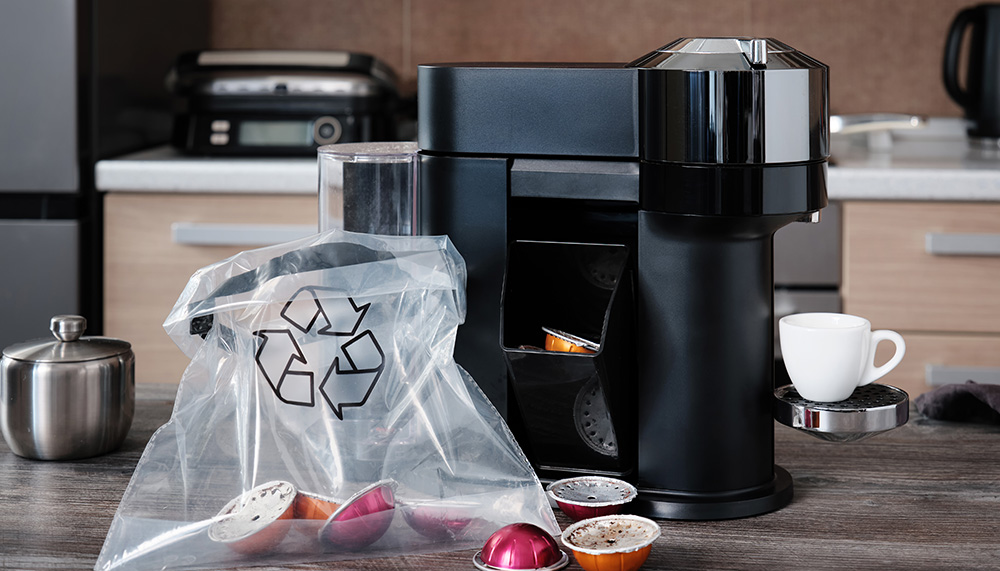
Industrial Equipment
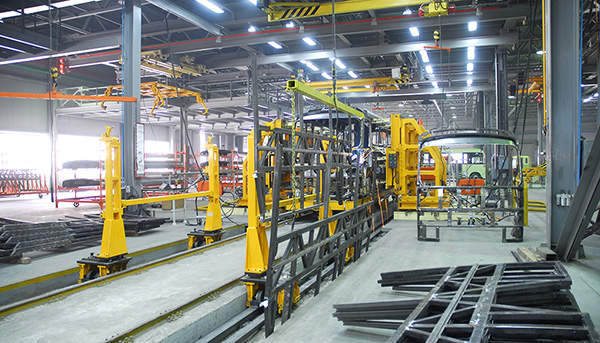
Consumer Electronics
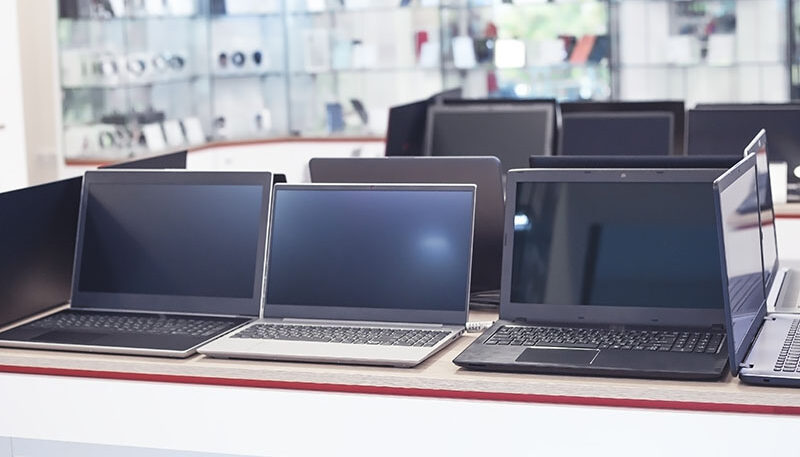
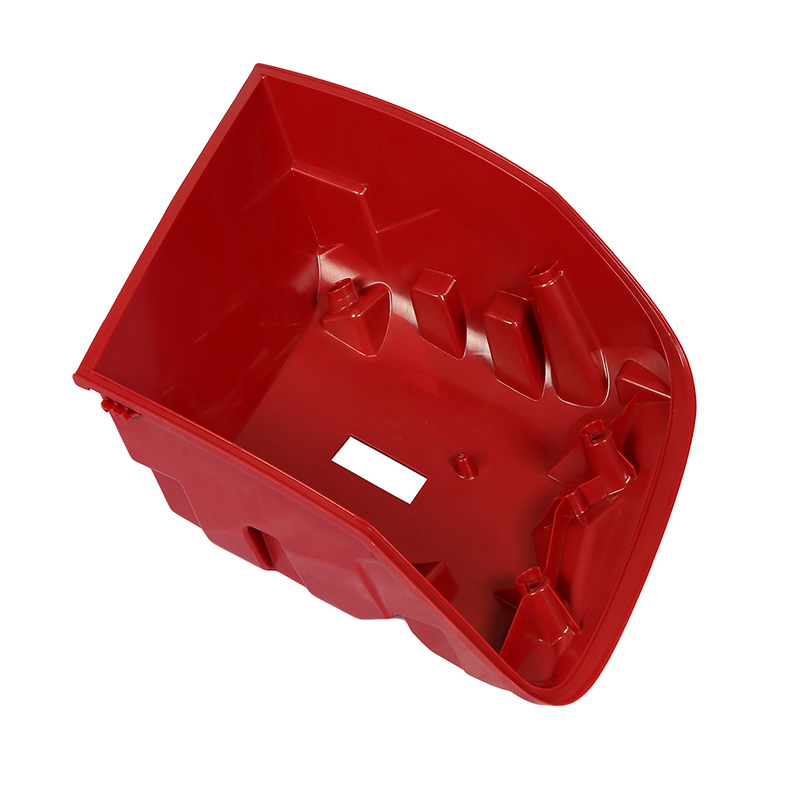
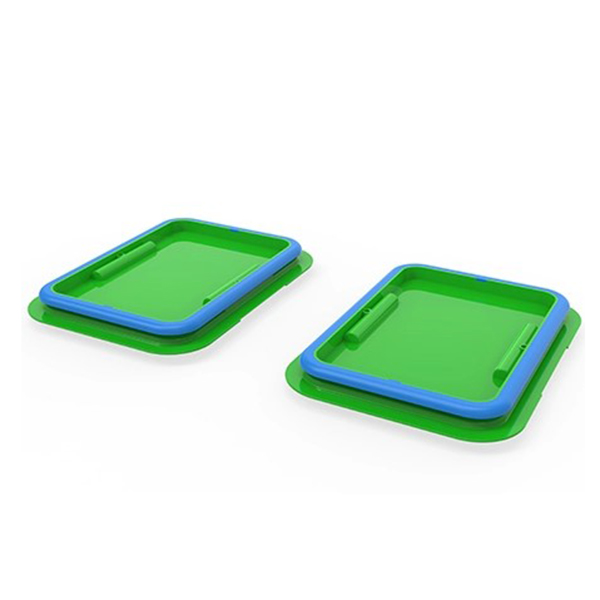
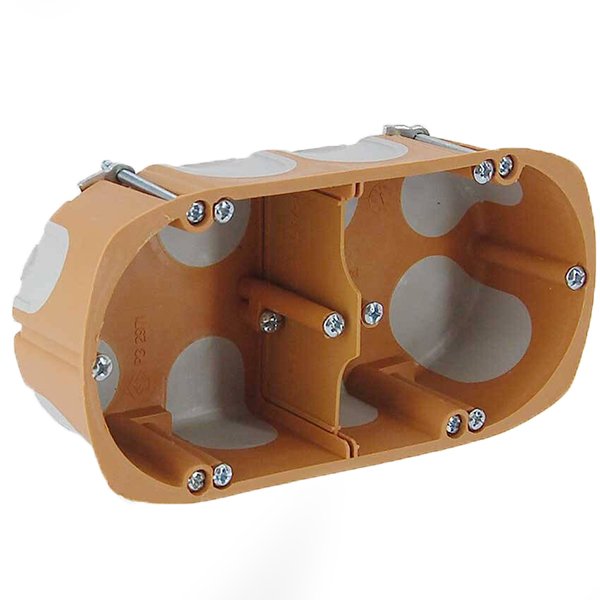
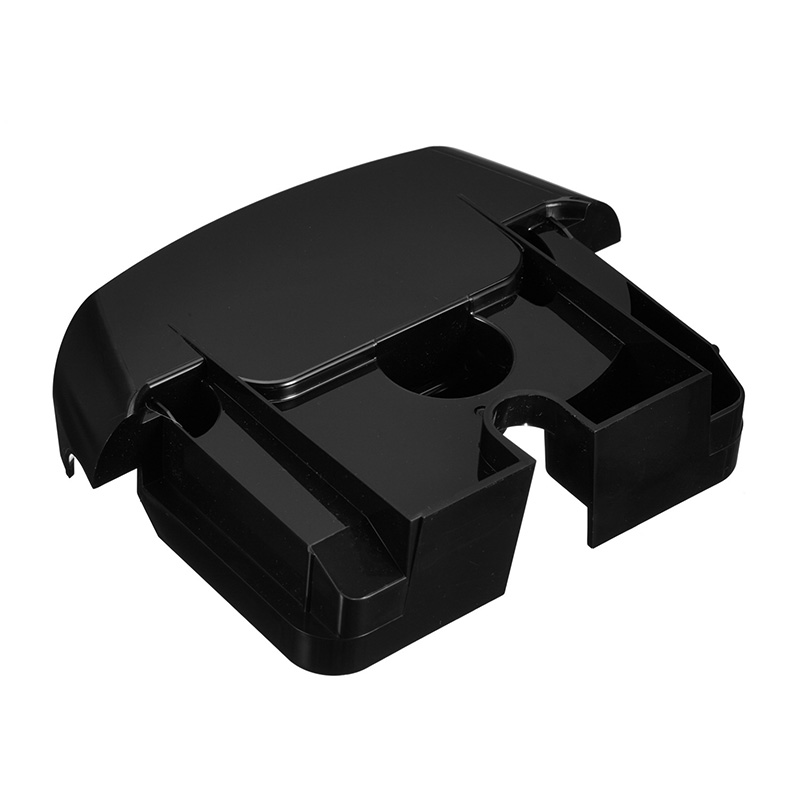
PPS Injection Molding
KingStar Mold’s Capabilities
Expert PPS Mold Design
At KingStar Mold, we specialize in designing custom molds for PPS injection molding that ensure precision and efficiency. Our team utilizes advanced mold flow analysis to optimize the design process, reducing material waste and ensuring consistent quality in every part produced.
We use state-of-the-art manufacturing equipment and techniques, including CNC machining and high-precision injection molding machines, to produce PPS parts with exceptional accuracy. Our focus on advanced technology ensures that every PPS component meets the highest standards of durability and performance.
Tailored Solutions
With extensive experience in PPS injection molding, KingStar Mold is adept at delivering solutions for a variety of demanding industries, including automotive, electronics, and industrial sectors. Whether it’s enhancing flame resistance or improving mechanical properties with glass or carbon fiber reinforcements, we provide custom solutions to meet the unique needs of each project.
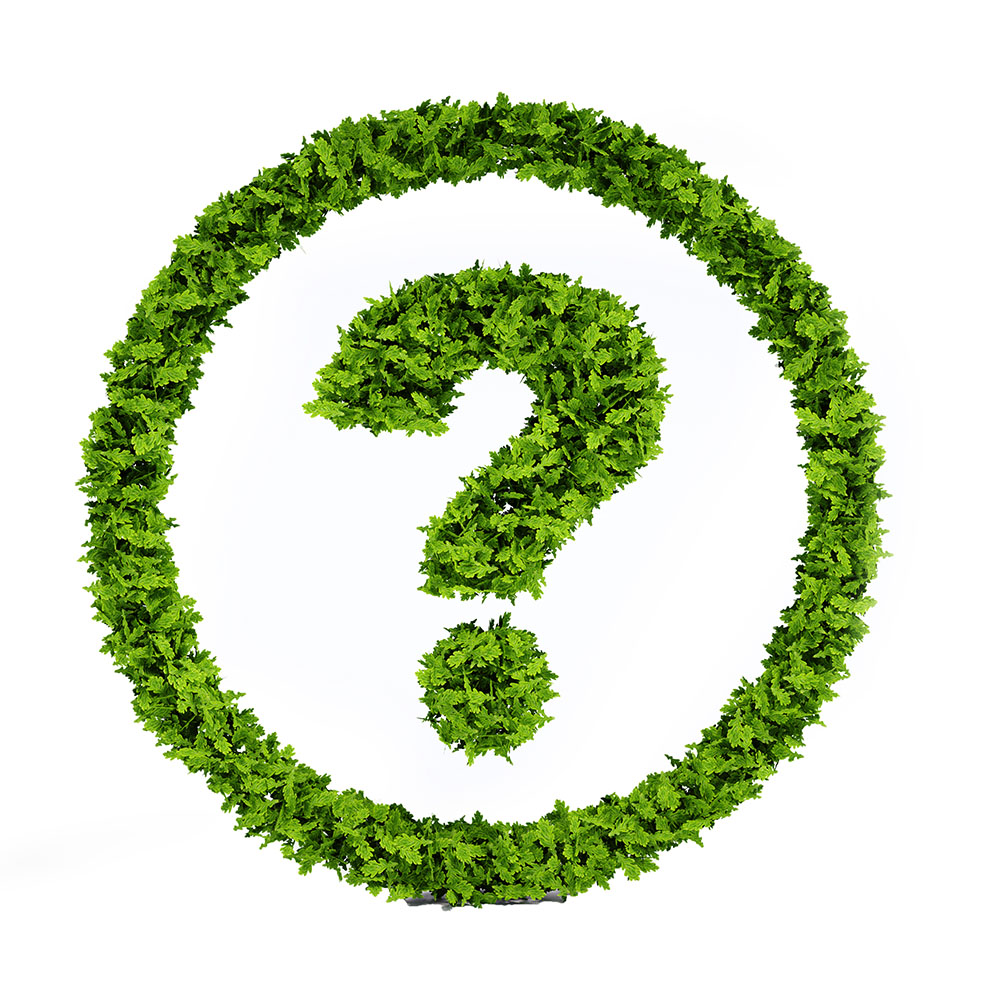
PPS stands out for its superior thermal stability, flame resistance, and chemical resistance when compared to other engineering plastics like PBT or nylon. It is especially advantageous in applications requiring high performance in extreme environments.
Yes, PPS can be modified with glass fibers, carbon fibers, and flame retardants to enhance its mechanical properties, strength, and flame resistance. These modifications allow PPS to be tailored to specific industry needs, such as automotive or electronics components.
PPS is widely used in automotive, aerospace, electronics, and industrial applications. Its resistance to high temperatures and harsh chemicals makes it suitable for parts like automotive fuel systems, electronic connectors, and industrial pumps.
At KingStar Mold, we use advanced technologies such as mold flow analysis and CNC machining to optimize PPS mold designs and ensure high-precision production. Our experienced team also implements strict quality control measures to guarantee that every PPS part meets the highest industry standards.
PPS offers excellent chemical resistance, high-temperature stability, and flame resistance, making it ideal for applications in automotive, electronics, aerospace, and industrial sectors. Its ability to withstand harsh environments and extreme temperatures gives it an edge over many other engineering plastics.
PPS (Polyphenylene Sulfide) is a high-performance thermoplastic known for its exceptional thermal stability, chemical resistance, and flame-retardant properties. PPS injection molding involves the process of injecting this durable material into molds to create complex, high-performance parts for various industries.
KingStar Mold uses a combination of expert design, precise CNC machining, and thorough quality inspection at every stage of production. We ensure that all PPS injection molded parts comply with industry standards and exceed customer expectations for performance and durability.
KingStar Mold specializes in working with various modified PPS materials, including glass fiber-reinforced PPS and flame-retardant PPS. We also offer custom solutions by blending PPS with other materials, such as PBT and PC, to meet specific application requirements.
At KingStar Mold, we are equipped with advanced diagnostic tools to identify and resolve any defects that may arise during the PPS injection molding process. Our team applies rigorous quality control and problem-solving techniques to ensure that every part meets the required standards.
Yes, PPS injection molding is highly suitable for high-volume production runs. The material’s consistent quality and durability, combined with the efficiency of injection molding, make it ideal for large-scale manufacturing.
Common applications of PPS injection molding include automotive fuel system parts, engine components, circuit boards, and electronic connectors. PPS’s ability to withstand extreme heat and chemicals makes it an ideal choice for demanding industrial parts.
With over a decade of experience in PPS injection molding, KingStar Mold combines technical expertise, advanced technology, and custom solutions to deliver high-performance parts for even the most challenging applications. Our commitment to innovation and quality sets us apart in the industry.