PP Injection Molding at KingStar Mold
At KingStar Mold, we specialize in maximizing the potential of customized Polypropylene (PP) materials through our advanced PP injection molding services. By incorporating materials like glass-filled PP for enhanced structural strength, mineral-filled PP for superior stiffness and thermal resistance, and talc-filled PP for improved impact resistance and dimensional stability, we deliver high-performance solutions that meet the diverse and demanding needs of various industries.
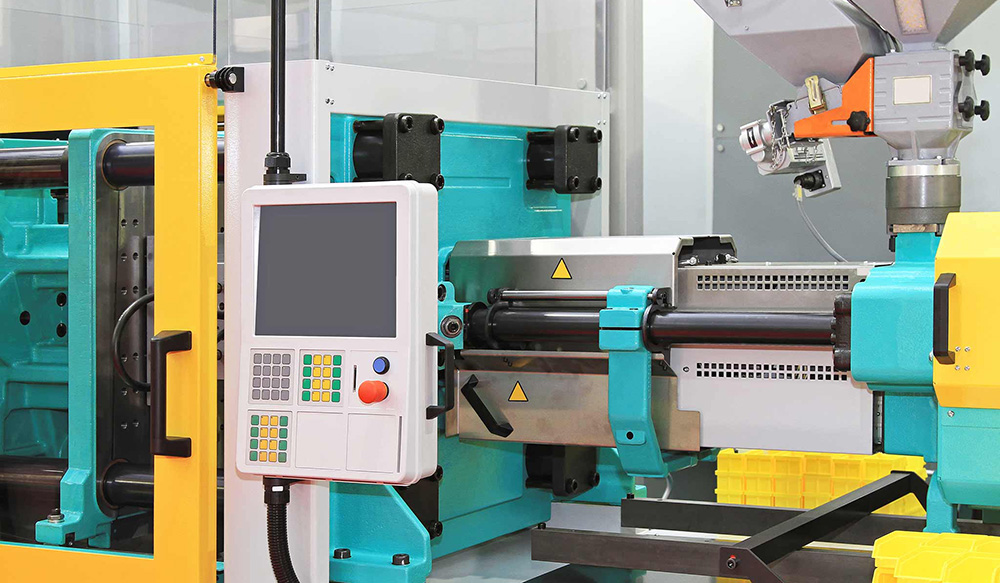
Polypropylene (PP) is a versatile material known for its lightweight, chemical resistance, and exceptional durability. Its ability to be easily molded, stretched, and formed into various shapes makes it ideal for a wide range of applications, including automotive parts, consumer goods, packaging, and medical devices. PP’s adaptability ensures it meets the needs of diverse industries while offering long-lasting performance.
Consumer Goods
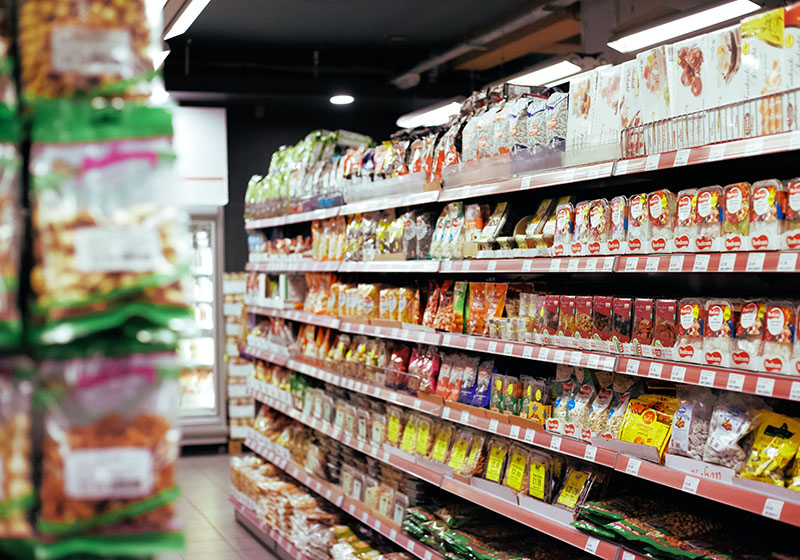
Packaging Solutions
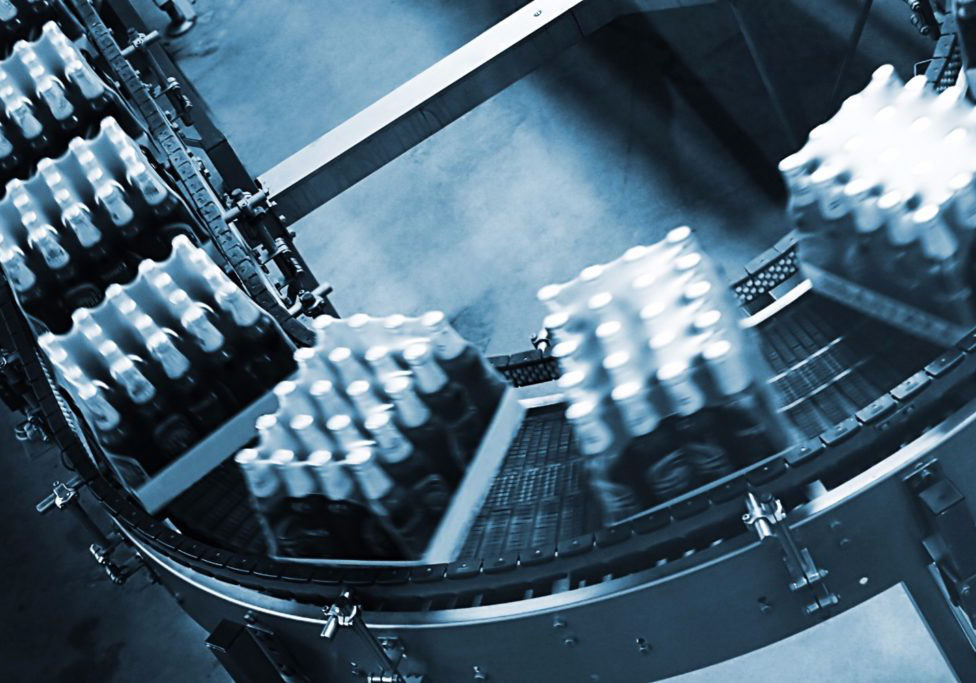
Medical Applications
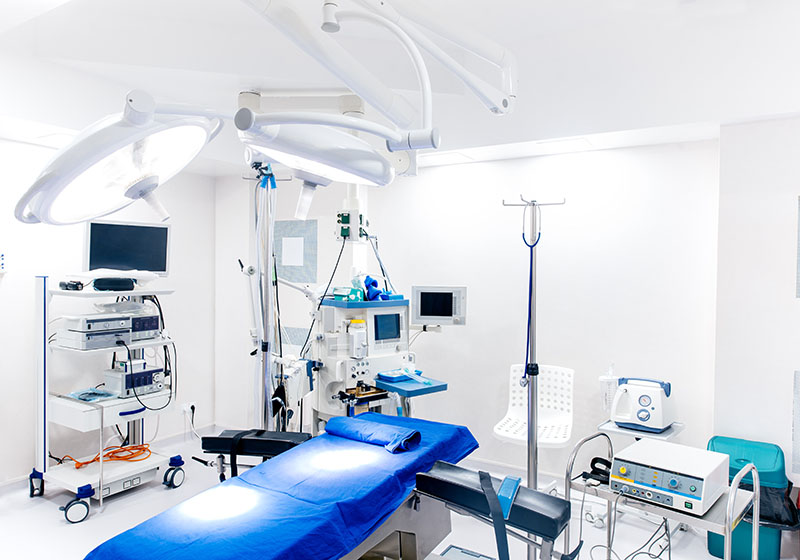
Automotive Components
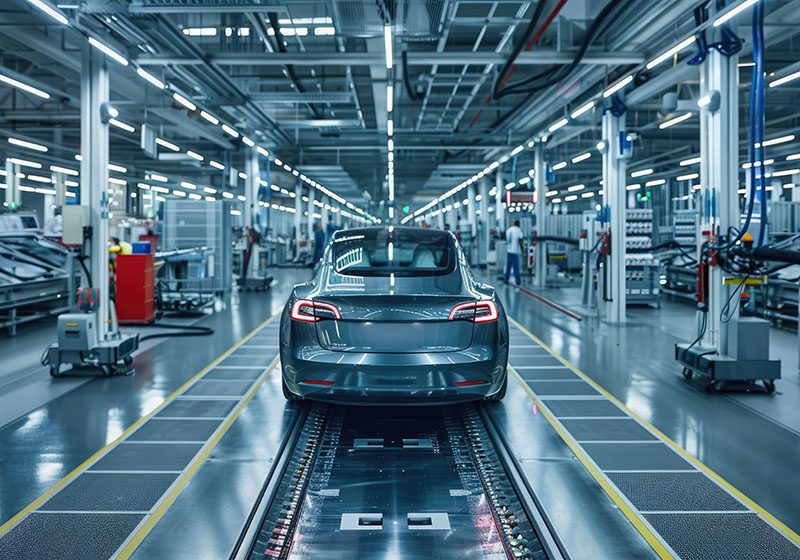
Of course, the application of PP injection molding goes well beyond these examples. At KingStar Mold, we bring extensive experience in PP material molding, particularly in the automotive, medical, and equipment casing sectors. Our expertise allows us to deliver high-quality, precision-engineered parts that meet the rigorous standards of these demanding industries.
Comprehensive Project Support
Our dedicated team offers full project support, from design consultation and prototyping to production optimization, ensuring your projects receive the quality and accuracy they demand.
Precision Molding for Complex Designs
With expertise in handling intricate geometries, we specialize in producing components that require high precision, intricate details, and tight tolerance values.
Advanced Material Manufacturing Solutions
KingStar Mold provides a diverse range of PP and modified PP solutions, including custom OEM, low-volume molding, mass production, and overmolded manufacturing, tailored to meet the unique needs of each project.
PP Injection Molding Cases
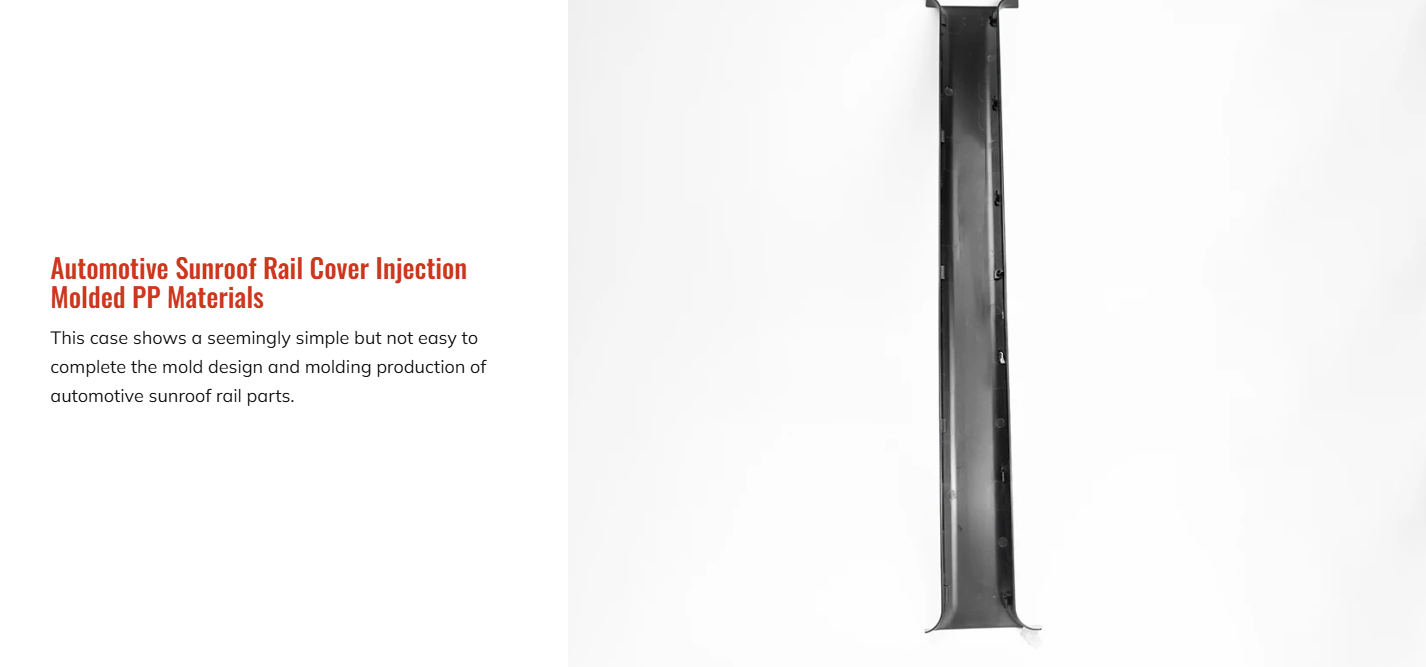
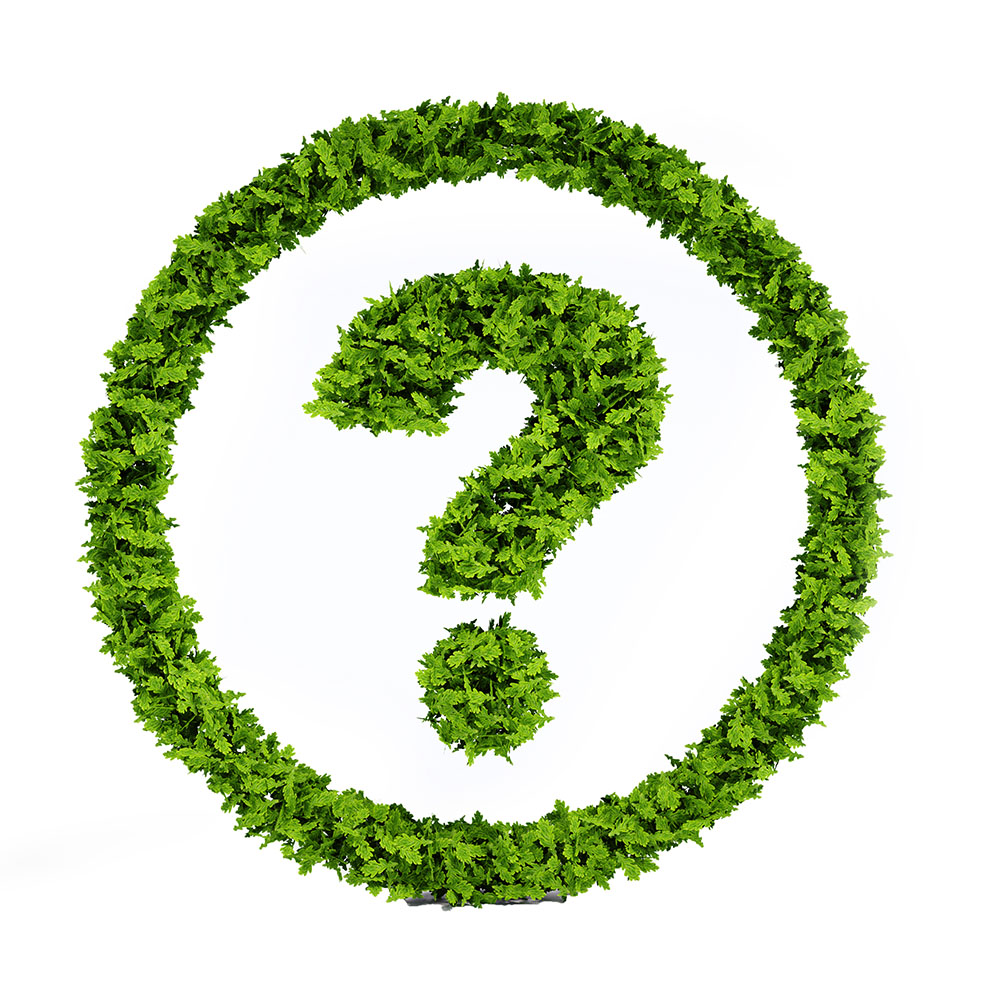
Talc-filled PP is ideal for automotive components, appliance parts, and structural applications due to its enhanced dimensional stability and impact resistance. It’s commonly used for parts that need added rigidity.
Yes, we offer color matching services to meet your branding or aesthetic needs. Custom colors can be incorporated directly into the PP resin during the molding process.
PP is highly durable and resists impacts, chemicals, and moisture. These properties make it suitable for parts that must withstand rigorous use, extreme environments, or exposure to chemicals.
PP is widely used in automotive, consumer goods, medical, and packaging industries. Its versatility makes it ideal for applications such as automotive components, food containers, medical device housings, and household products.
We work with various types of PP, including glass-filled, mineral-filled, and talc-filled grades. Each type offers unique properties, like increased stiffness or impact resistance, to meet specific application needs.
PP is recyclable and has a low environmental impact compared to some other plastics. We also offer sustainable manufacturing practices to minimize waste and energy use during production.
Yes, food-grade and medical-grade PP are commonly used for applications requiring hygiene and safety. PP’s chemical resistance and low reactivity make it safe for use in food containers and certain medical devices.
Yes, we offer overmolding services with PP, which allows you to combine different materials or add layers for enhanced functionality. This technique is often used to add soft-touch grips or secondary features.
Lead times depend on project complexity, but typically range from 4-8 weeks for production molds. We work closely with clients to set realistic timelines and ensure on-time delivery.
PP is one of the most cost-effective materials for injection molding, especially in high volumes. Its low cost, combined with its durability and ease of processing, makes it a popular choice across industries.