Metal 3D printing has transformed modern manufacturing, enabling the creation of highly complex, lightweight, and customized parts. However, while 3D printing offers incredible design freedom, it’s important to note that the parts usually require post-processing to enhance their performance, surface finish, and dimensional accuracy.
In this post, we will explore essential post-processing techniques—such as surface finishing, heat treatments, powder analysis, mechanical testing, and post-process machining—that can optimize your metal 3D-printed parts for both functional and aesthetic requirements. Whether you’re looking to improve strength, appearance, or precision, the right post-processing approach will ensure that your parts meet the necessary standards for demanding applications.
1. Surface Finishing
Surface finishing improves the appearance, reduces surface roughness, and removes any artifacts left from the printing process.
Techniques:
- Sanding: Sanding smooths the surface by removing layer lines, support marks, and edges, which enhances the overall smoothness and uniformity of the part.
- Spray Painting: A quick and effective solution for adding color to your parts. It’s ideal for decorative purposes and can be customized to specific color schemes, including Pantone and RAL shades.
- Plating: Applying a metallic coating can enhance the surface’s corrosion resistance, improve durability, and create a reflective, visually appealing finish.
- Brushed Finishes: A method where various grit levels are used to produce a uniform, directional texture on the part’s surface. This is particularly suited for parts that require a matte or industrial finish.
- Satin and Polished Finishes:
- Satin Finish offers a smooth, non-reflective surface with a soft sheen, perfect for applications where glare reduction is required.
- Polished Finish produces a high-gloss, reflective surface that gives parts a premium look and feel, ideal for high-end or decorative applications.
Importance:
These surface finishing methods not only improve aesthetics but also help with the part’s performance in harsh environments, offering benefits such as better corrosion resistance and enhanced wear properties.
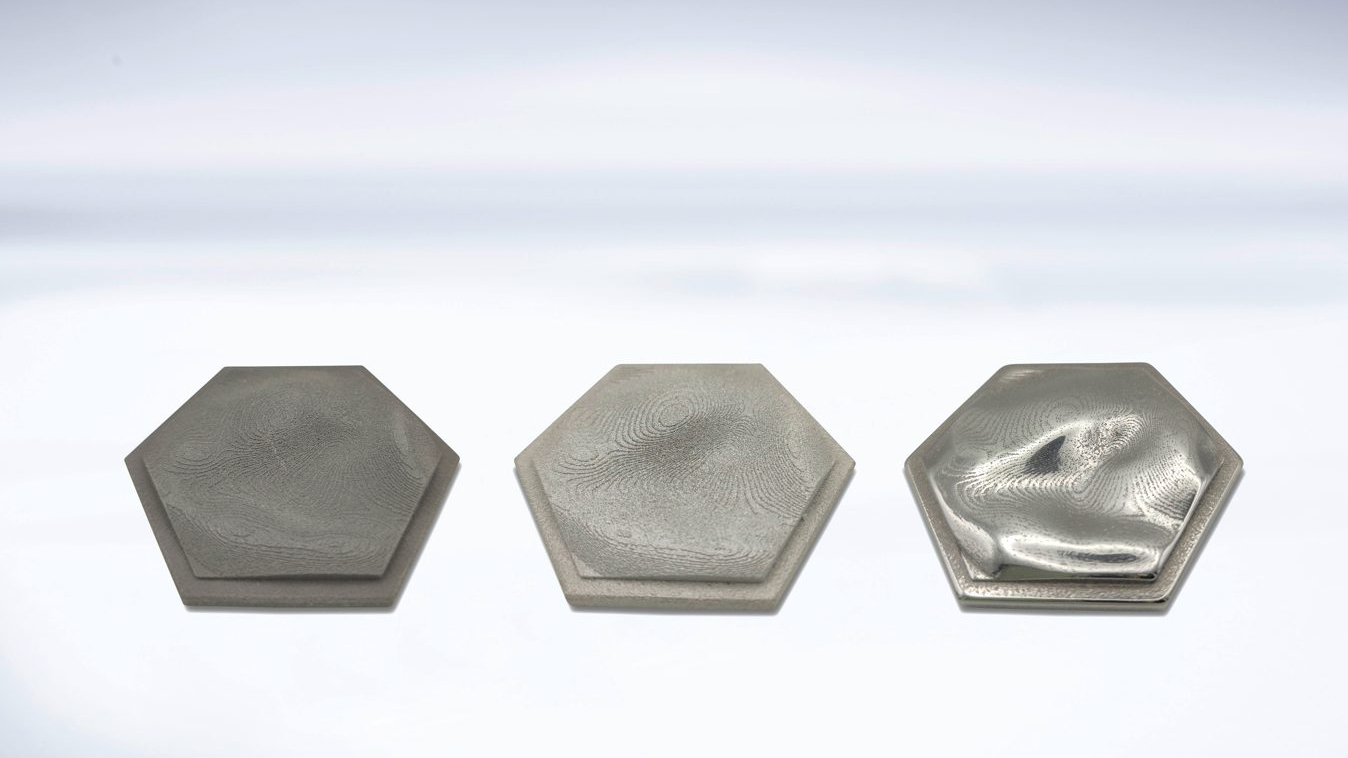
2. Heat Treatments
Heat treatments refine the material’s properties, reduce internal stresses, and improve mechanical performance, including strength, toughness, and resistance to wear and corrosion.
Techniques:
- Stress Relief (Applicable to all metals): This process involves controlled heating to relieve the residual stresses generated during 3D printing. It helps prevent warping and dimensional instability.
- NADCAP Heat Treatment (Applicable to Titanium, Nickel Alloys, and Aerospace Parts): Certified for aerospace applications, NADCAP heat treatment optimizes the material’s mechanical properties, ensuring the part meets rigorous industry standards.
- Hot Isostatic Pressing (HIP) (Applicable to Titanium, Inconel, Steel): HIP applies high pressure and temperature simultaneously to eliminate any internal porosity, improving density, strength, and fatigue resistance—critical for aerospace and automotive applications.
- Solution Annealing (Applicable to Stainless Steel, Inconel): This heat treatment process dissolves precipitates in the material, refining the grain structure and improving the part’s resistance to corrosion. It’s particularly useful for parts exposed to harsh environmental conditions.
- Aging (Applicable to Nickel Alloys, Titanium): By controlling the heating and cooling rates, aging enhances material hardness and increases wear resistance, ensuring the part performs well in high-stress environments.
Why It Matters:
Heat treatments are vital for improving the mechanical properties of parts used in demanding industries such as aerospace, automotive, and energy. They allow metal 3D-printed parts to withstand higher loads, resist fatigue, and offer greater long-term performance.
3. Powder Analysis & Material Verification
Material quality and consistency are essential to ensuring that the printed part performs as expected. Powder analysis verifies that the material used for 3D printing meets specific criteria for quality and safety.
Techniques:
- Traceability: Ensures that materials used in the 3D printing process are traceable to their source, maintaining transparency and quality control. This is especially important in industries like aerospace and healthcare.
- Chemical Analysis: Verifies the chemical composition of the metal powder. Ensuring the powder meets the required standards is critical for ensuring the desired mechanical and chemical properties of the final part.
- Particle Size and Distribution Analysis: The consistency of powder particle size is key to achieving uniform layer deposition. Proper particle distribution improves print quality, part density, and strength.
Importance:
By verifying the material properties before and after the printing process, manufacturers can ensure that parts meet the required standards and perform reliably throughout their lifecycle.
4. Mechanical Testing
Mechanical testing validates the structural integrity and performance of 3D-printed parts by assessing their response under stress, ensuring they meet application-specific requirements.
Testing Methods:
- Tensile Testing: This test measures a part’s tensile strength, yield strength, and elongation by applying a uniaxial force until failure. It is essential for understanding the material’s ability to resist deformation under tension.
- Hardness Testing (Rockwell): Hardness testing evaluates a part’s resistance to indentation and surface deformation. It is important for determining wear resistance, especially for parts that will be subjected to friction or high mechanical loads.
Why It Matters:
Mechanical testing ensures that the part will function properly in real-world conditions. Whether your parts are exposed to high temperatures, wear, or intense pressure, mechanical testing confirms that they can withstand the operational stresses.
5. Post-Process Machining
Post-processing machining is used to achieve higher dimensional accuracy, finer surface finishes, and more complex geometries that might not be achievable through 3D printing alone.
Techniques:
- CNC Machining (3, 4, and 5-Axis): CNC machining is used for producing precision features, tight tolerances, and smooth surfaces. It’s ideal for parts that require intricate geometries or high precision.
- CNC Turning: CNC turning allows for the creation of cylindrical or rounded components with high precision. It is especially useful for parts with rotating features or that require round surfaces.
- Wire EDM (Electrical Discharge Machining): Wire EDM is a technique used for cutting intricate shapes and features with high precision. This is useful for detailed, complex parts that require tight tolerances.
- CNC Tapping: CNC tapping creates precise threads in parts, ensuring consistent and reliable threading quality. It is particularly important for parts that need to be assembled or mated with other components.
Why It Matters:
Post-process machining ensures that parts meet precise tolerances and quality standards, improving both their functionality and aesthetics. It also allows for features that may be challenging to achieve through the 3D printing process alone.
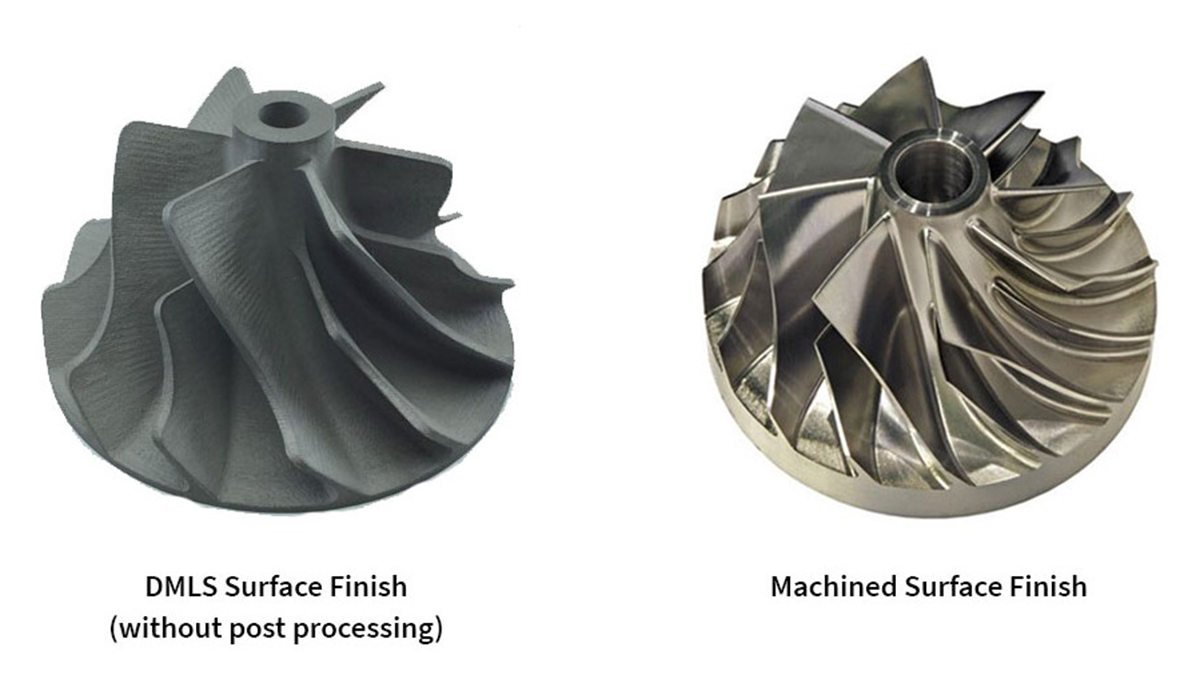
6. Integration of Post-Processing Techniques
Combining Techniques for Optimal Results:
In many cases, integrating multiple post-processing techniques will yield the best overall results. By combining surface finishing, heat treatments, and machining, manufacturers can produce parts that are both visually appealing and functionally reliable.
For example, parts may first undergo heat treatment to relieve stress, followed by surface finishing to improve aesthetics, and then be subjected to post-process machining for tight tolerances and complex features. This multi-step approach ensures that every aspect of the part meets the required standards.
Conclusion
Post-processing plays a crucial role in ensuring the success of metal 3D-printed parts. From improving mechanical properties with heat treatments to enhancing surface finishes and achieving precision with post-process machining, these techniques ensure that your parts meet or exceed the necessary performance standards.
At KingStar Mold, we are committed to delivering high-quality, durable parts through advanced post-processing techniques. Whether you need surface finishing, heat treatment, or post-process machining, our expertise guarantees that your parts will be optimized for both functionality and appearance.
As 3D printing technology continues to evolve, new post-processing techniques will emerge, offering even more possibilities to enhance part performance. Embrace these advanced techniques with KingStar Mold to ensure your metal 3D-printed parts reach the highest level of quality and performance.
For more detailed datasheets, please refer to our page: Metal 3D Printing Service