PMMA Injection Molding Overview
PMMA (Polymethyl Methacrylate), commonly known as acrylic, is a transparent, high-performance material widely used for its exceptional clarity, UV resistance, and weatherability. With its excellent optical properties, PMMA is ideal for applications requiring clear, durable parts, such as lenses, light diffusers, and display covers. Additionally, PMMA can be modified with colors, coatings, and additives to meet specific design and performance needs.
Though PMMA may be more expensive than other plastics, its superior optical qualities and durability in outdoor environments make it a popular choice. At KingStar Mold, we bring extensive experience in PMMA injection molding, ensuring the production of high-quality, defect-free parts with outstanding clarity and durability for various industries, including automotive, electronics, and signage.
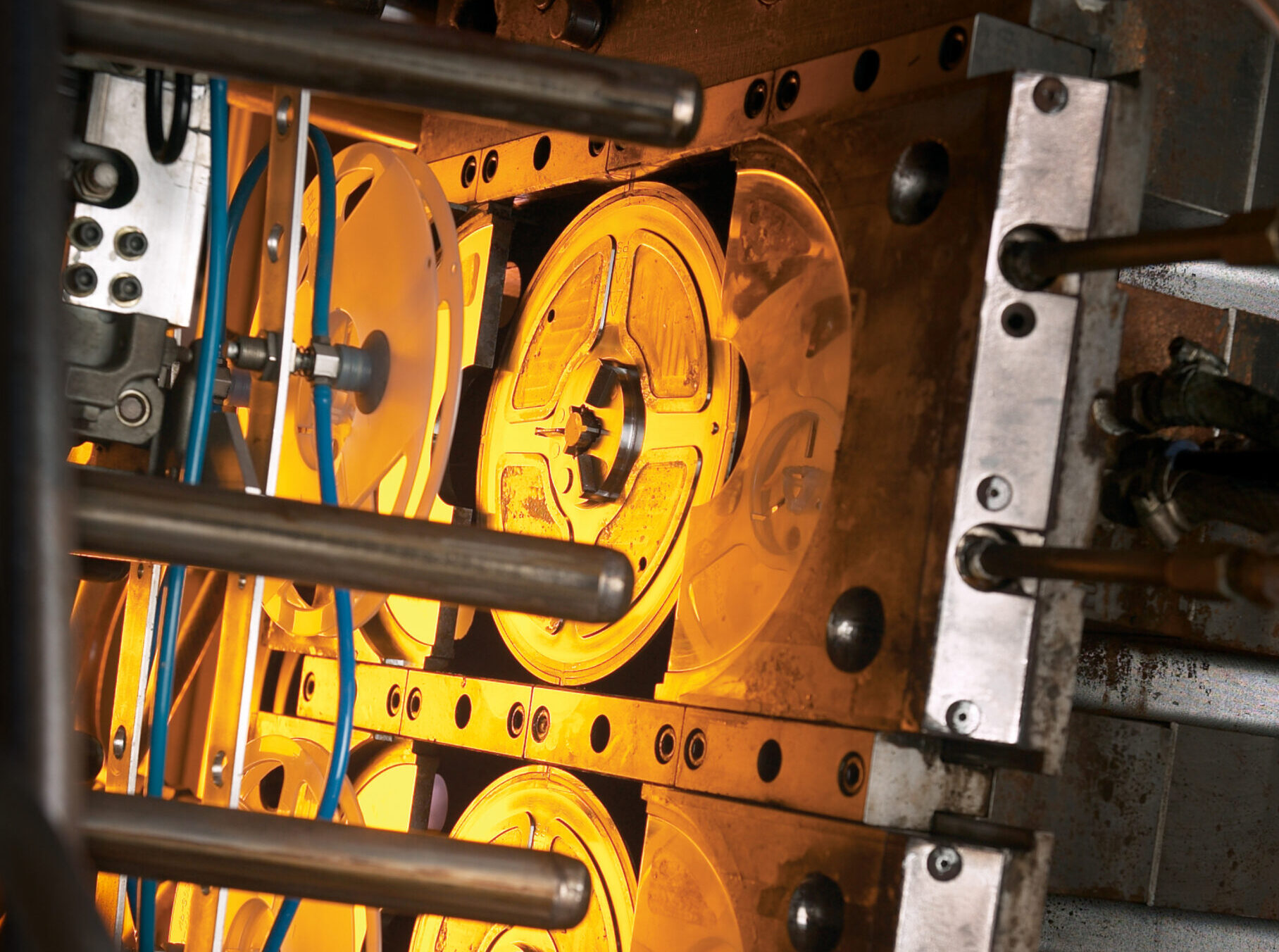
PMMA injection molding is widely utilized in industries that require high clarity and weather resistance. Known for its exceptional transparency and UV stability, PMMA is a go-to material for automotive lighting, display covers, and optical lenses. In the electronics sector, PMMA is commonly used for protective covers, housings, and light diffusers due to its impact resistance and ability to withstand harsh environmental conditions. Its excellent weatherability also makes it ideal for outdoor applications like street lighting covers and signage.
PMMA’s versatility extends to a variety of industries, from consumer goods to medical devices, where clear, durable components are essential. Modified versions of PMMA, such as those with added UV resistance or scratch-resistant coatings, enhance its performance further. This makes PMMA injection molding an invaluable solution for producing high-quality, visually appealing parts across many demanding applications.
Automotive Components
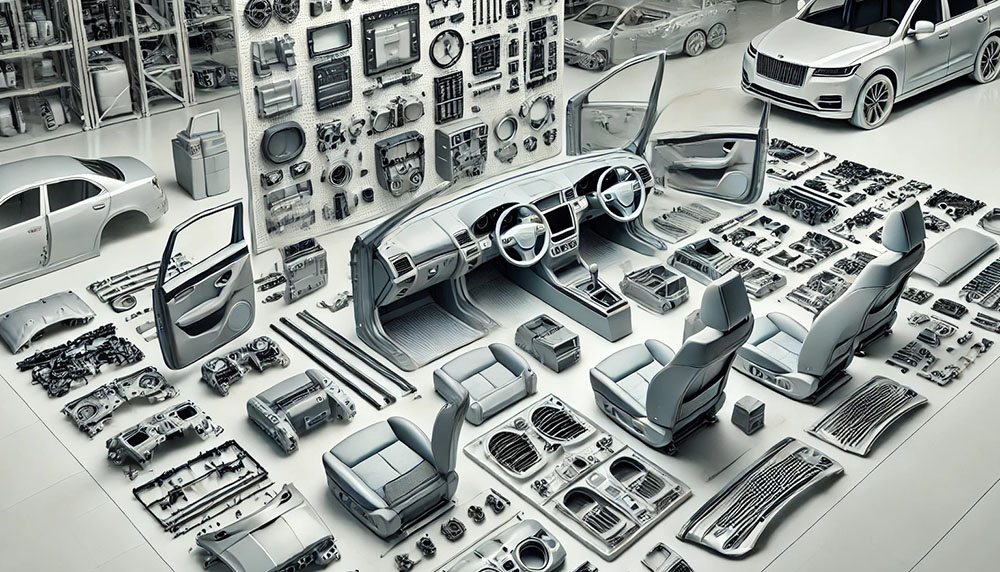
Medical Devices

Signage and Lighting
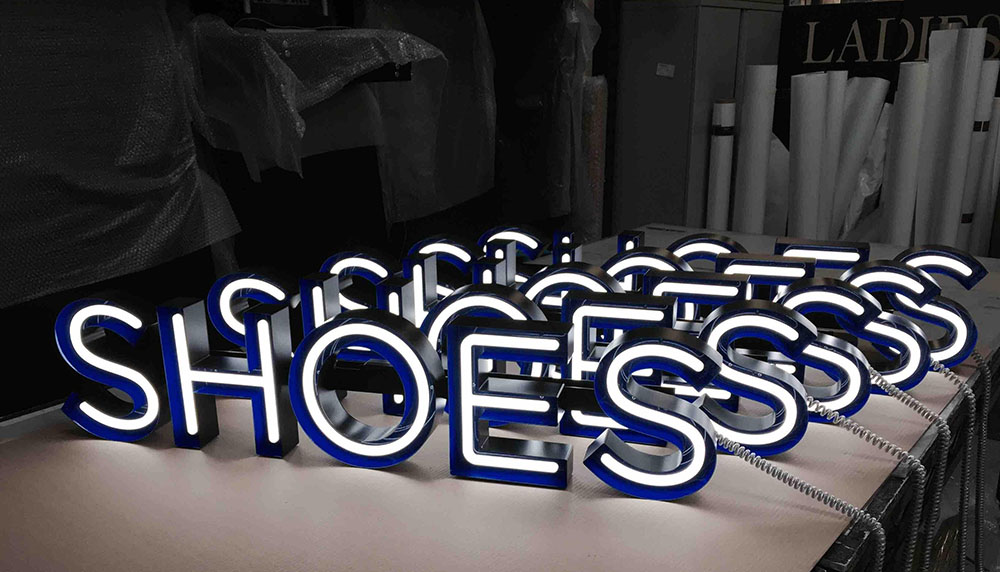
Consumer Electronics
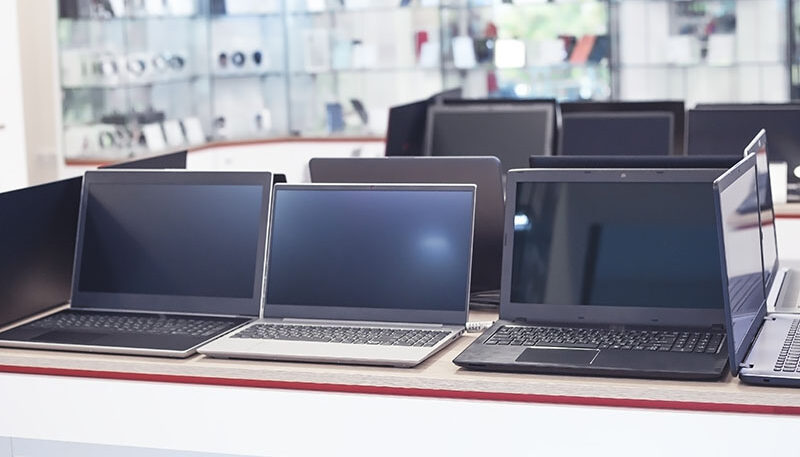
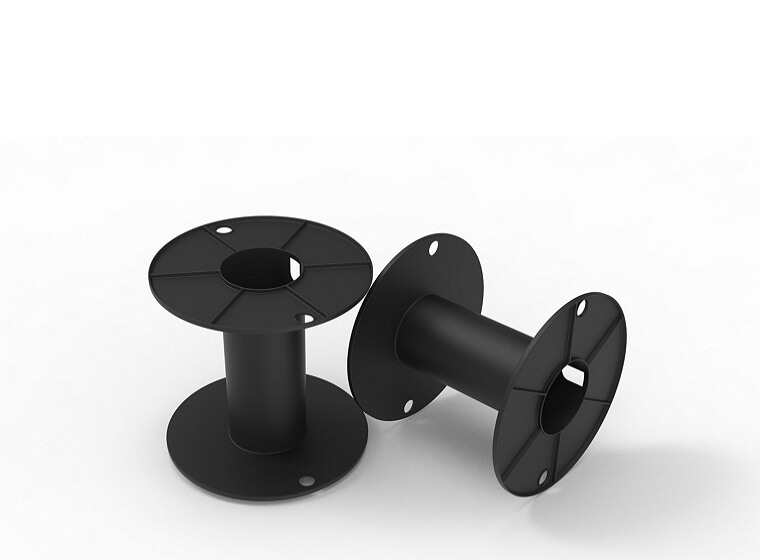
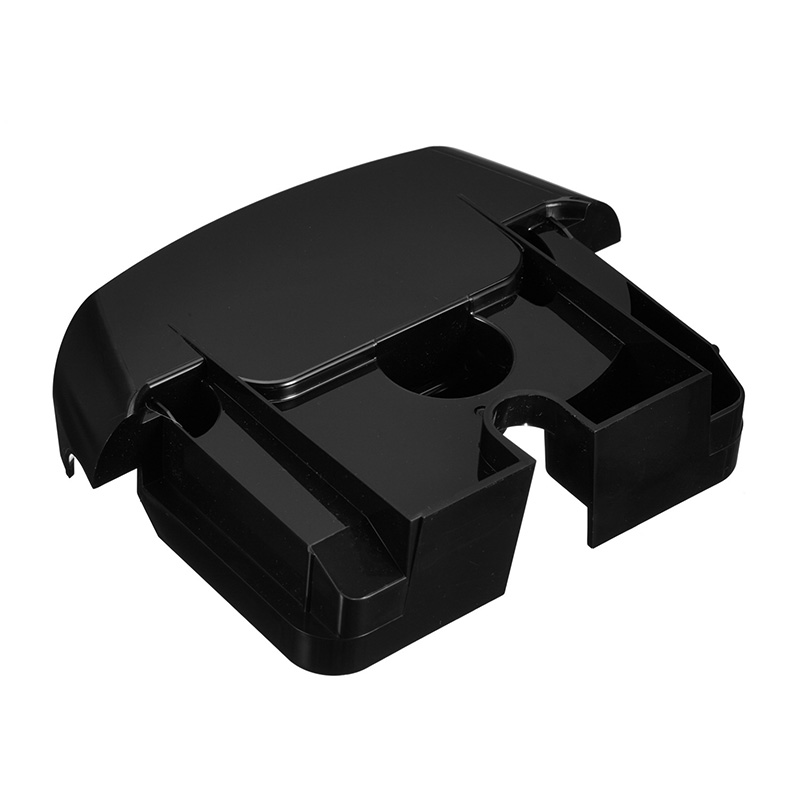
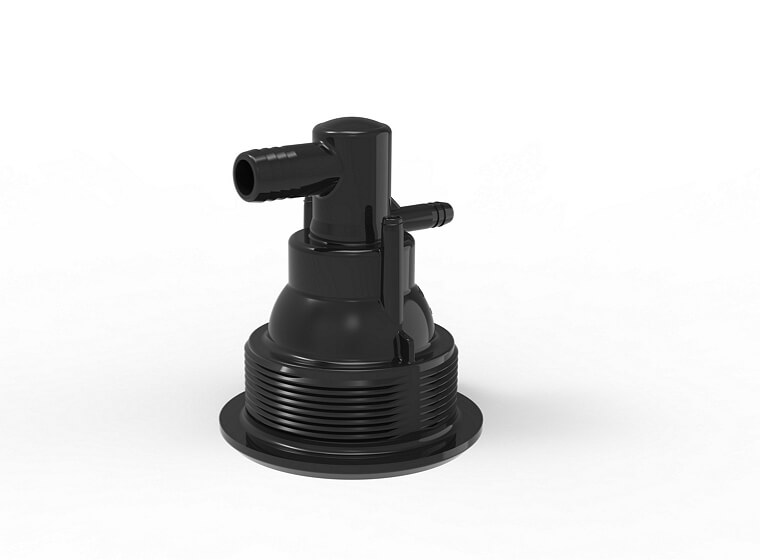
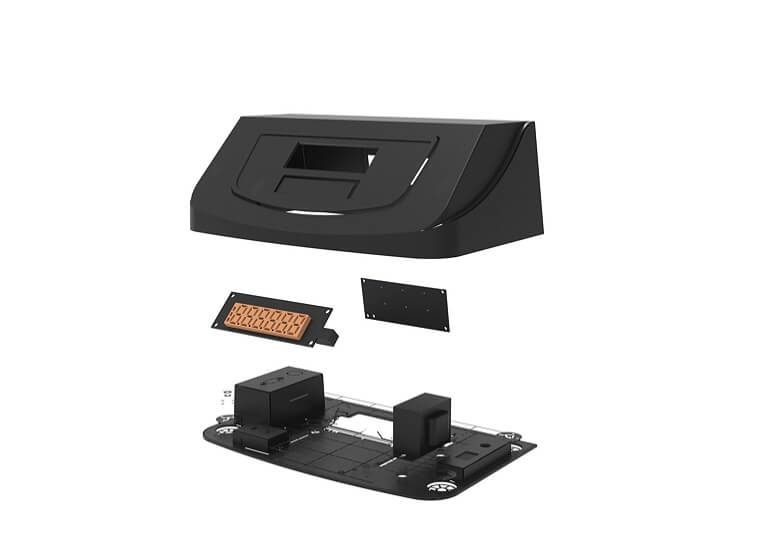
PPMA Injection Molding
KingStar Mold’s Capabilities
Expert PMMA Mold Design
At KingStar Mold, our experienced designers focus on creating precise and optimized mold designs for PMMA injection molding. Using advanced tools like mold flow analysis, we ensure optimal material distribution, reducing defects and enhancing production efficiency.
Our state-of-the-art CNC machining and injection molding technology allow us to produce PMMA parts with exceptional accuracy and consistency. With rigorous quality control systems in place, we guarantee that every part meets the highest standards for clarity, durability, and performance.
Versatility Across Industries
KingStar Mold’s PMMA injection molding services cater to a wide range of industries, including automotive, consumer electronics, and signage. We provide tailored solutions to meet specific requirements, whether for transparent, impact-resistant components or high-end aesthetic parts.
Why Choose Us
Advantages of KingStar Mold
Tailored Solutions for Complex Designs
Advanced Technology Integration
Dedicated Customer Support
Competitive Pricing
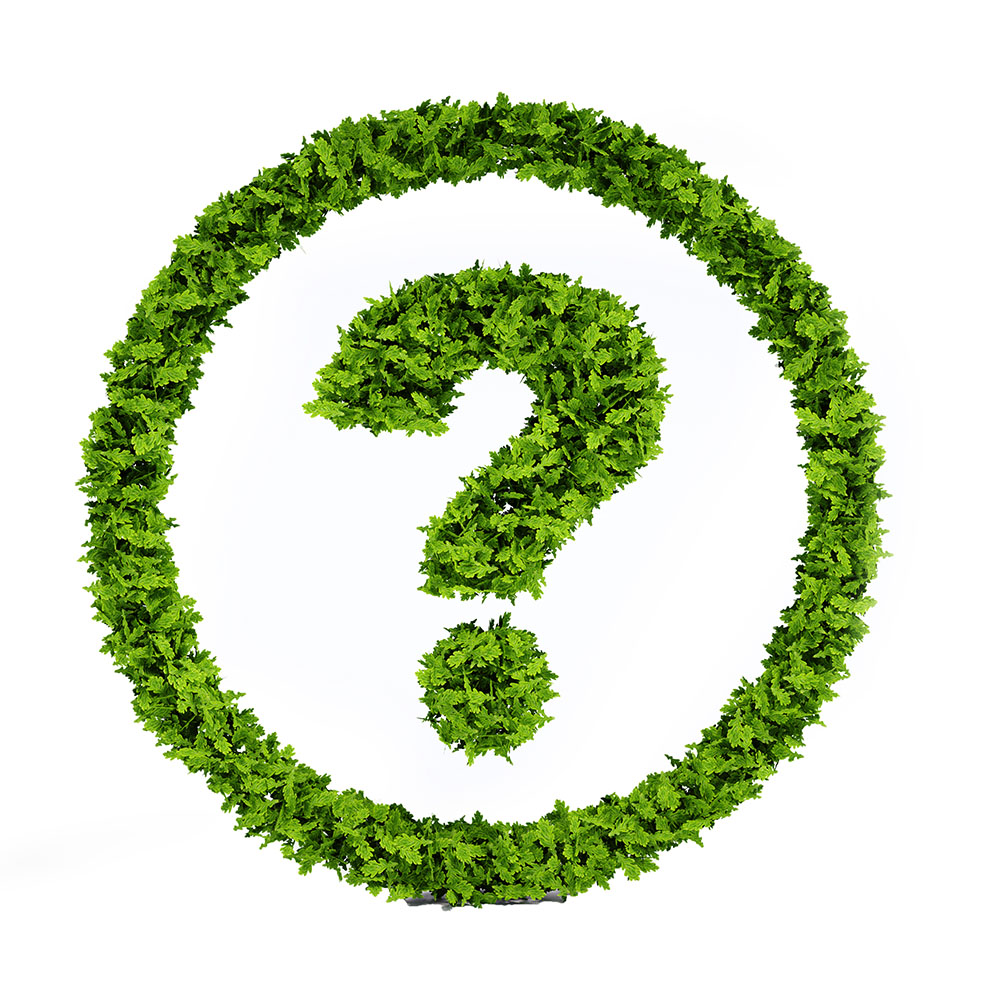
PMMA is known for its superior clarity and UV resistance, making it ideal for outdoor applications. However, polycarbonate offers better impact resistance but is more prone to yellowing and scratching compared to PMMA.
PMMA injection molding is used across various industries, including automotive (lighting), medical (surgical devices), consumer electronics (displays), and retail (store signage), due to its clarity and durability.
KingStar Mold uses advanced technologies like mold flow analysis and CNC machining to produce precise molds. We also conduct rigorous quality checks throughout the process to ensure the final product meets industry standards.
PMMA offers high light transmittance, excellent clarity, and a glossy finish, making it ideal for applications where transparency is essential, such as optical lenses, light covers, and display panels.
PMMA is commonly used for automotive lighting covers, optical lenses, medical device parts, and display panels. Its transparency, durability, and UV stability make it an ideal material for these applications.
PMMA (Polymethyl Methacrylate) injection molding is a process where molten PMMA plastic is injected into a mold to form various transparent or colored components. It is widely used for producing clear, durable parts in industries like automotive, medical, and electronics.
Common defects include sink marks, warping, and bubbles. KingStar Mold’s expert team quickly identifies and addresses these issues using optimized processing parameters and post-processing techniques to achieve the highest quality.
KingStar Mold’s skilled designers work closely with clients to ensure complex PMMA components meet functional and aesthetic requirements. We utilize advanced simulation tools and prototype testing to guarantee precision.
PMMA injection molding can use both standard and modified versions of the material, such as UV-stabilized PMMA or impact-resistant PMMA. The choice of material depends on the specific requirements of the final product.
Yes, PMMA can be modified to enhance specific properties, such as adding color, improving impact resistance, or increasing UV stability, making it suitable for a wide range of applications, including both indoor and outdoor uses.
PMMA is used in automotive lighting due to its excellent light transmission and weather resistance. It helps enhance vehicle aesthetics and durability while also offering protection from UV degradation.
Yes, KingStar Mold specializes in both small and large-scale production runs. With over a decade of experience in injection molding, we can efficiently handle both high-volume orders and custom part requirements.