Personal Care Tool & Beauty Device Components Production
Cooperative Partners

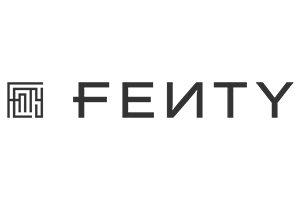
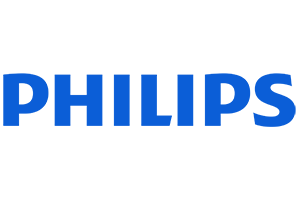
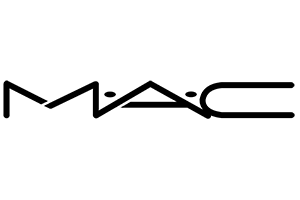
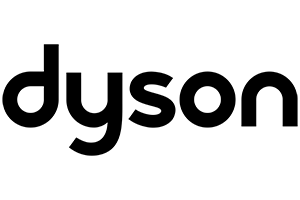
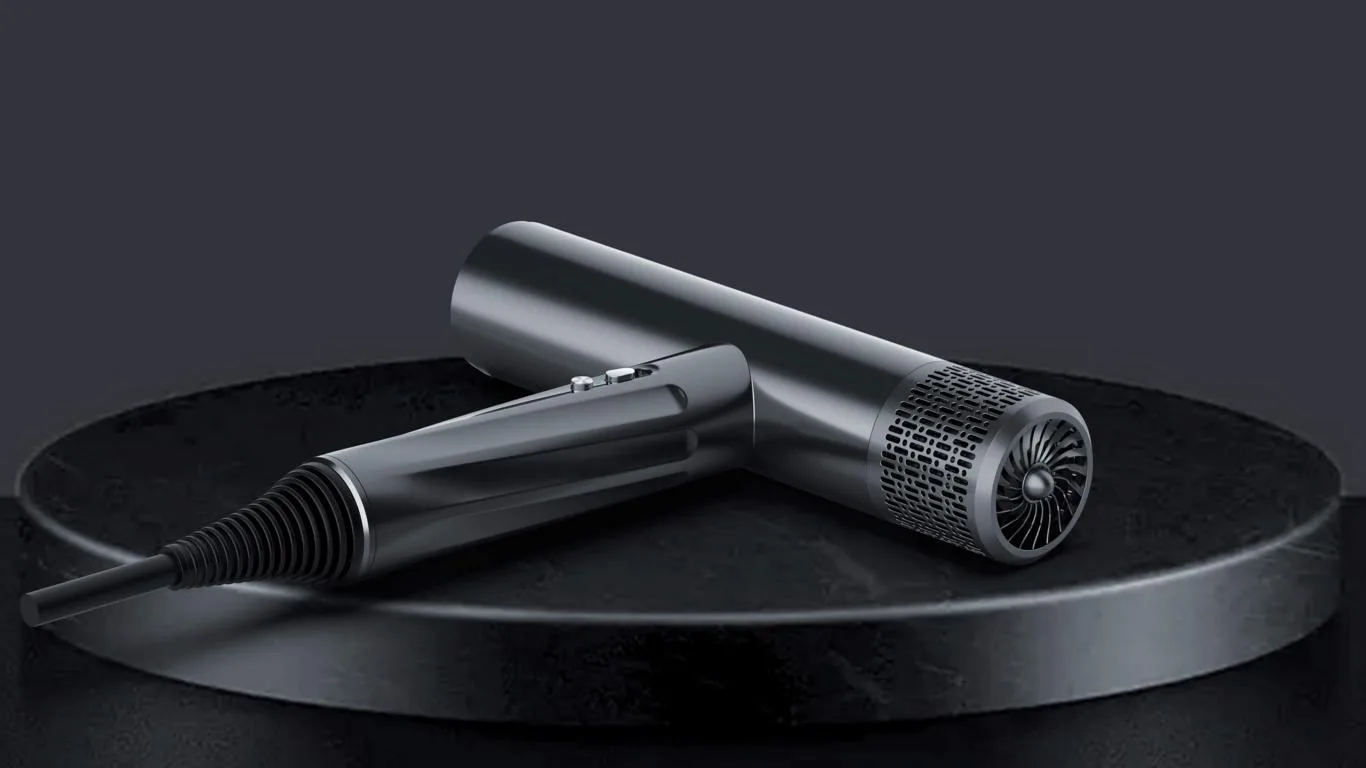
High-Quality Personal Care & Beauty Components for the Global Market
Over 10 Years of Expertise in Personal Care Manufacturing
Certified Material Selection & Traceability
Fast Turnaround for Custom Orders
KingStar Mold offers custom, on-demand machining and production services for personal care and beauty components worldwide. We are known for our quick lead times, thorough material verification, and stringent quality control measures integrated at each step of the production process.
We understand the importance of both aesthetics and functionality in personal care and beauty products. Our team works closely with clients to ensure that each component is produced to meet exact specifications, ensuring high performance, durability, and flawless finishes that align with industry standards. With KingStar Mold, you can trust that your products will meet the highest quality benchmarks while also being delivered on time.
How We Support Personal Care & Beauty Companies
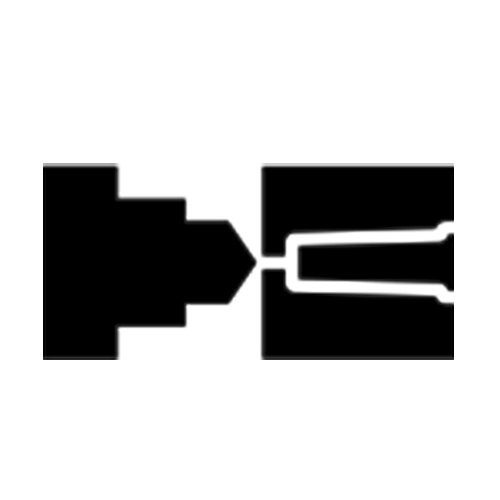
Injection Molding
At KingStar Mold, injection molding is our core service for producing high-quality plastic components like bottles, jars, and applicators. We ensure precise detail, smooth finishes, and efficient scalability for both mid and high-volume production.
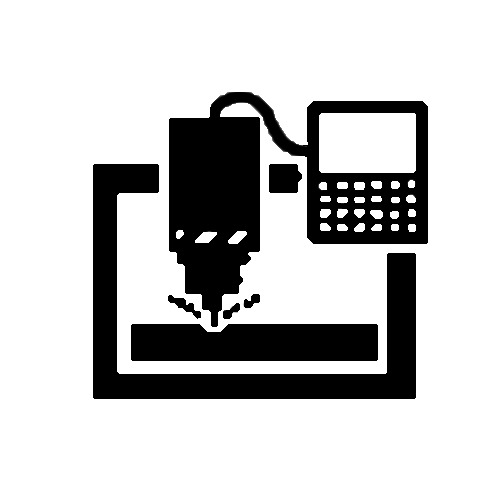
CNC Machining
For high-end beauty devices and metal packaging parts, our CNC machining services deliver tight tolerances and a premium finish. We support both prototyping and low-volume runs with fast turnaround and exceptional accuracy.
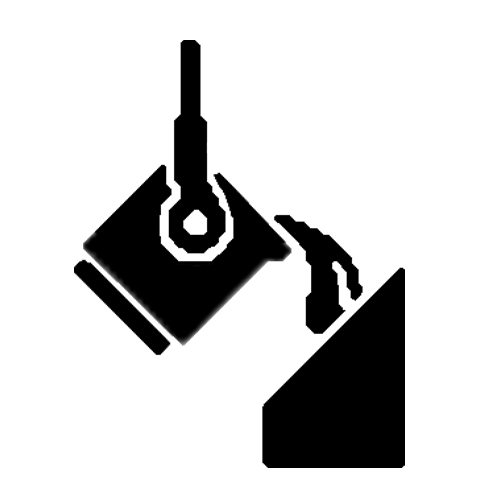
Die Casting
Our die casting solutions are perfect for sleek, durable metal parts such as compact lids, perfume caps, and decorative housings. We provide consistent quality in large volumes using aluminum and zinc alloys.
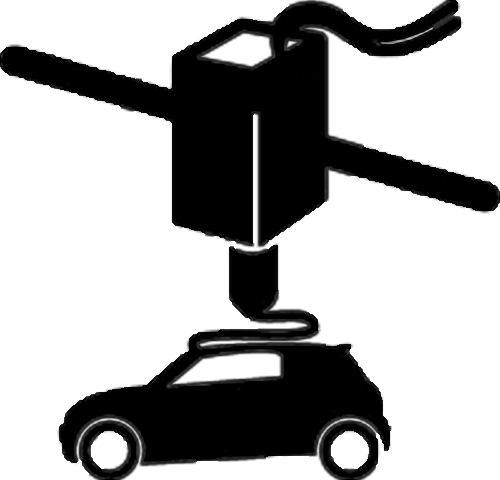
3D Printing
Need a fast prototype or design validation? KingStar Mold offers rapid 3D printing for beauty packaging concepts and functional samples, helping you accelerate development without sacrificing creativity.
What We Can Make for You
Personal Care & Beauty Gallery
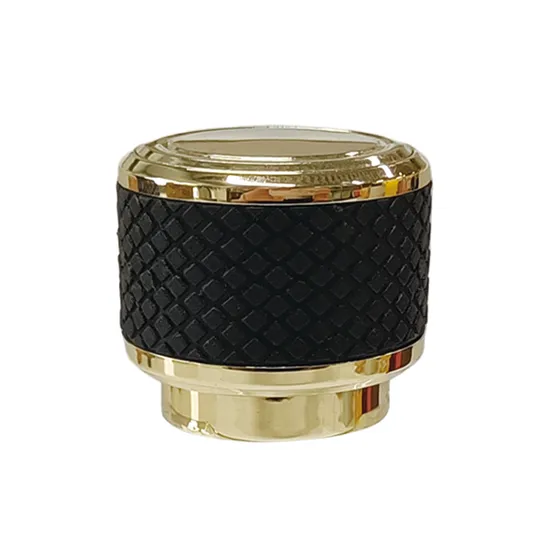
KingStar Mold offers a comprehensive range of manufacturing services tailored to the beauty industry.
Our core processes include:
Grooming Devices & Tools
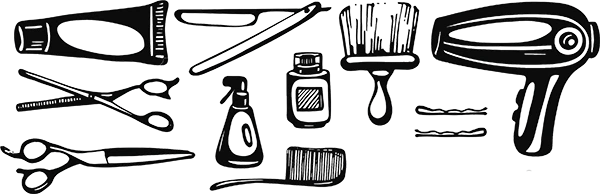
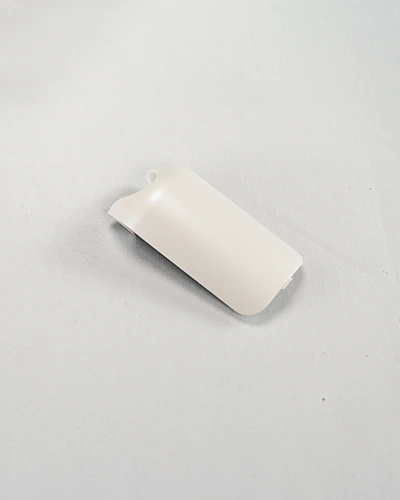
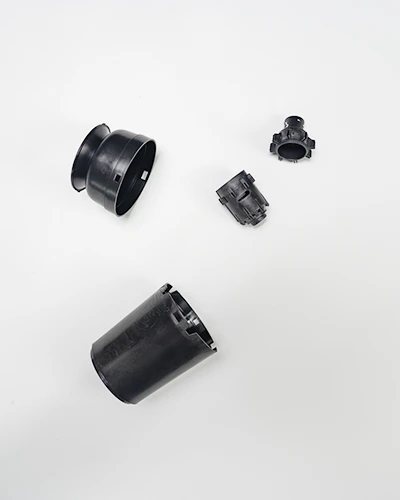
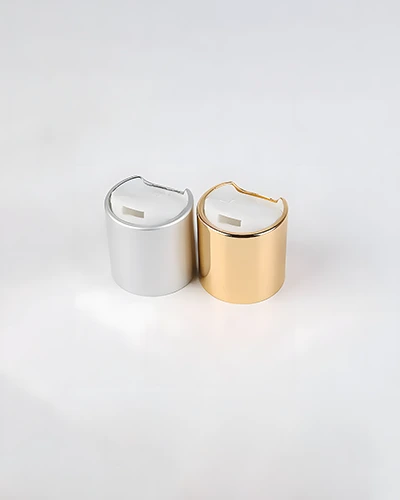
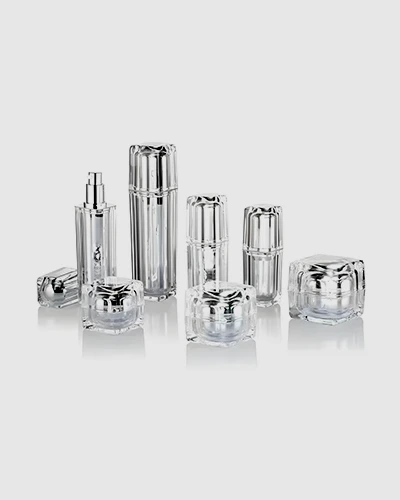
Cosmetic Housings
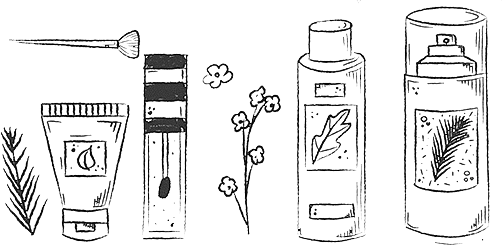
Dedicated Full-Scale Production Support
Our experienced manufacturing team oversees every stage of your production order, from start to finish. We handle the entire process with precision and efficiency—while keeping you informed with timely updates throughout.

Account Manager
Your dedicated account manager offers personalized assistance—from platform navigation to file uploads—ensuring smooth communication and project handling.
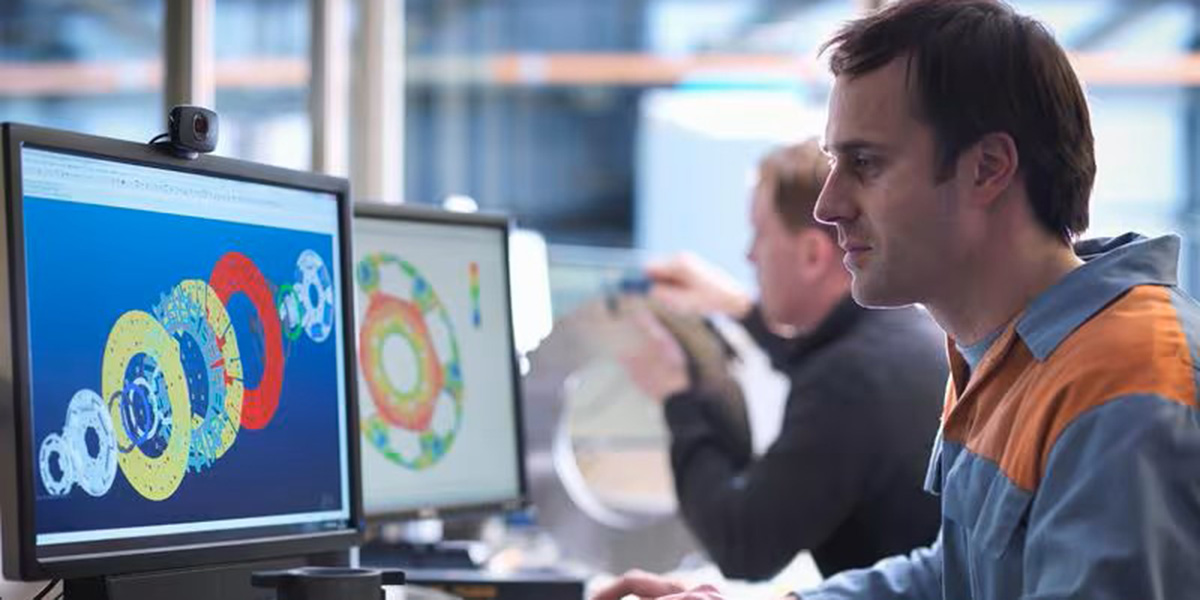
Application Engineers
Our in-house application engineers provide expert CAD support and design optimization, helping you reduce costs while maintaining performance and manufacturability.
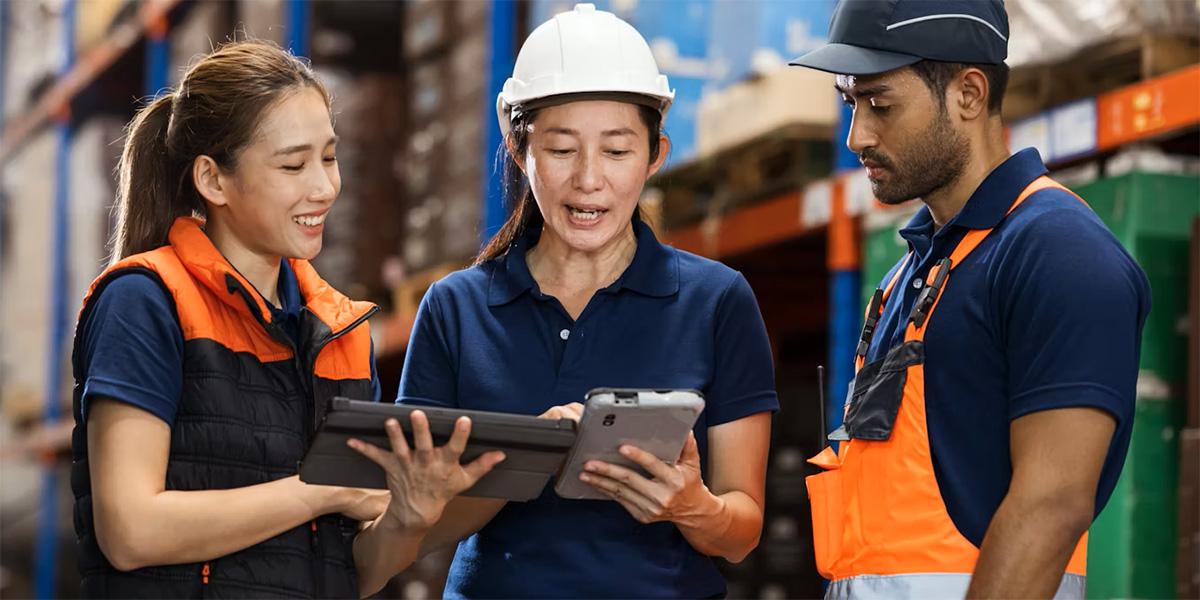
Logistics
Our operations specialists manage global logistics with precision, ensuring fast, reliable delivery and streamlined supply chain coordination.
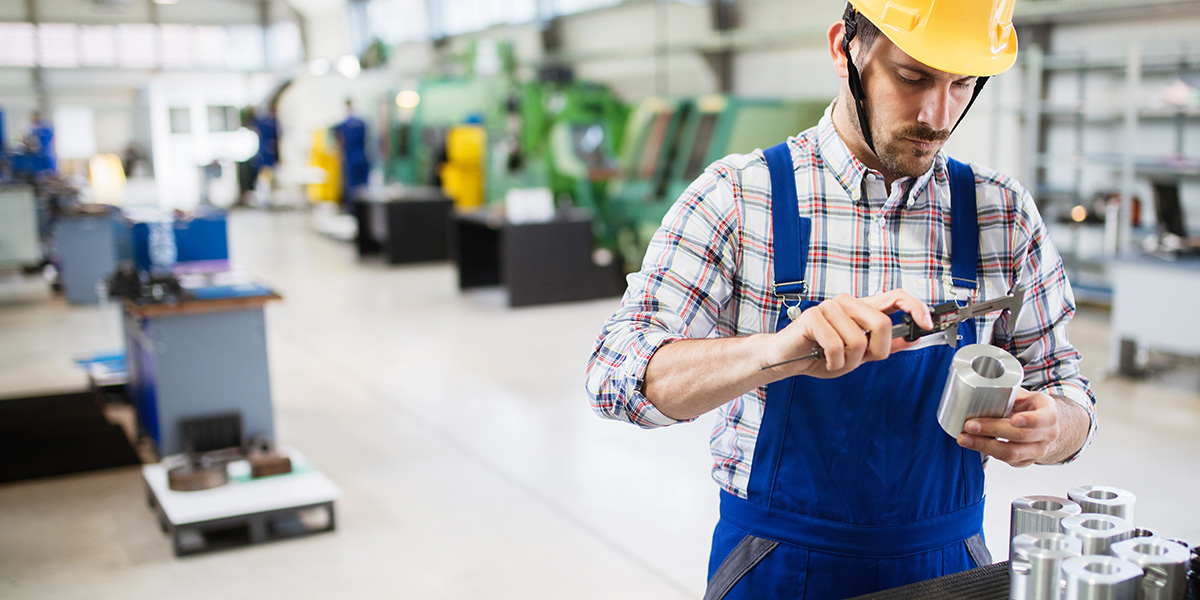
Recommended Cosmetic Manufacturing Solutions
Materials For the Cosmetic Components
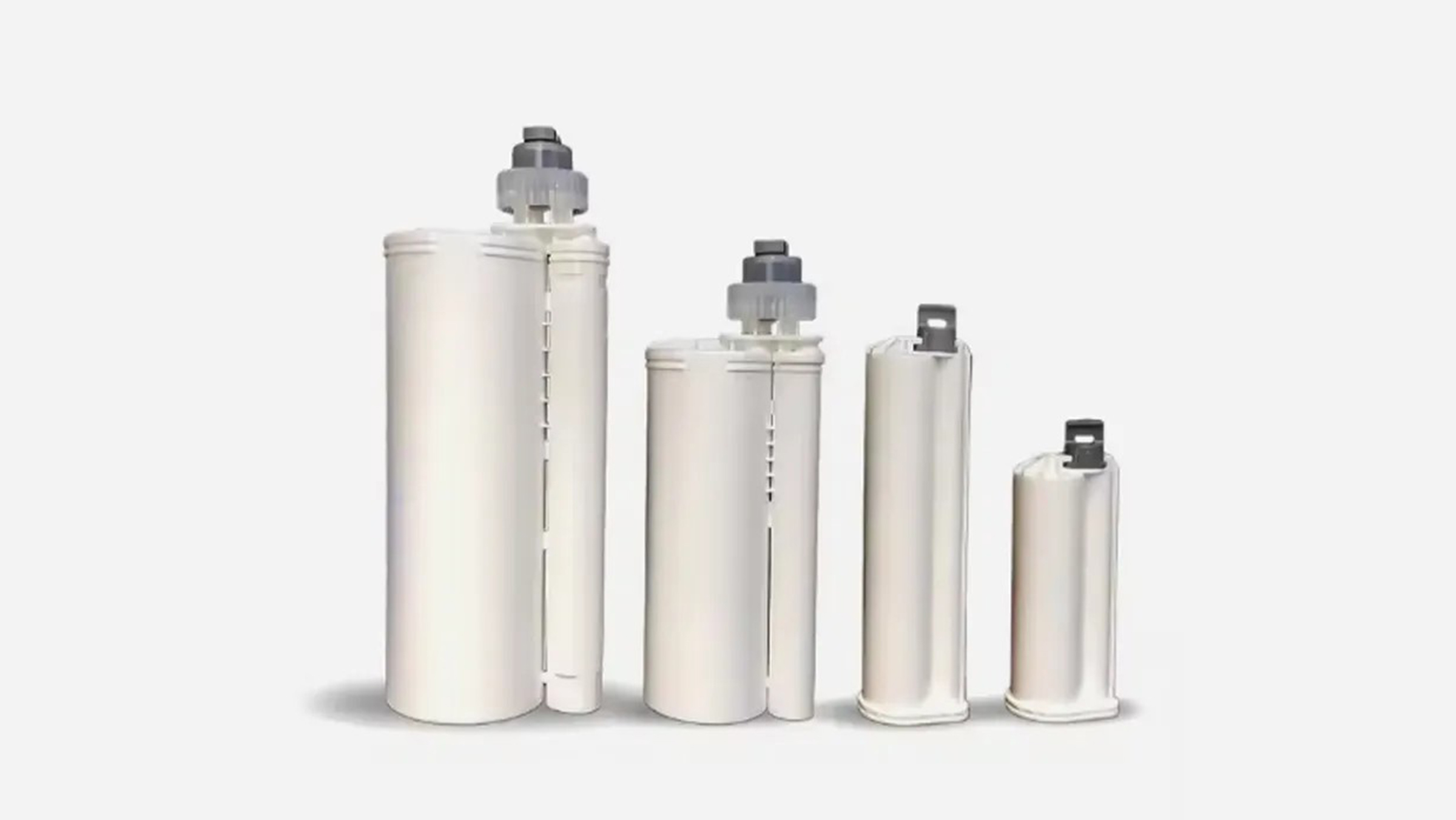
PBT
Hair dryer housing inserts, Electric toothbrush gears, Eyelash curler components, Compact motor casings, Heated straightener brackets…
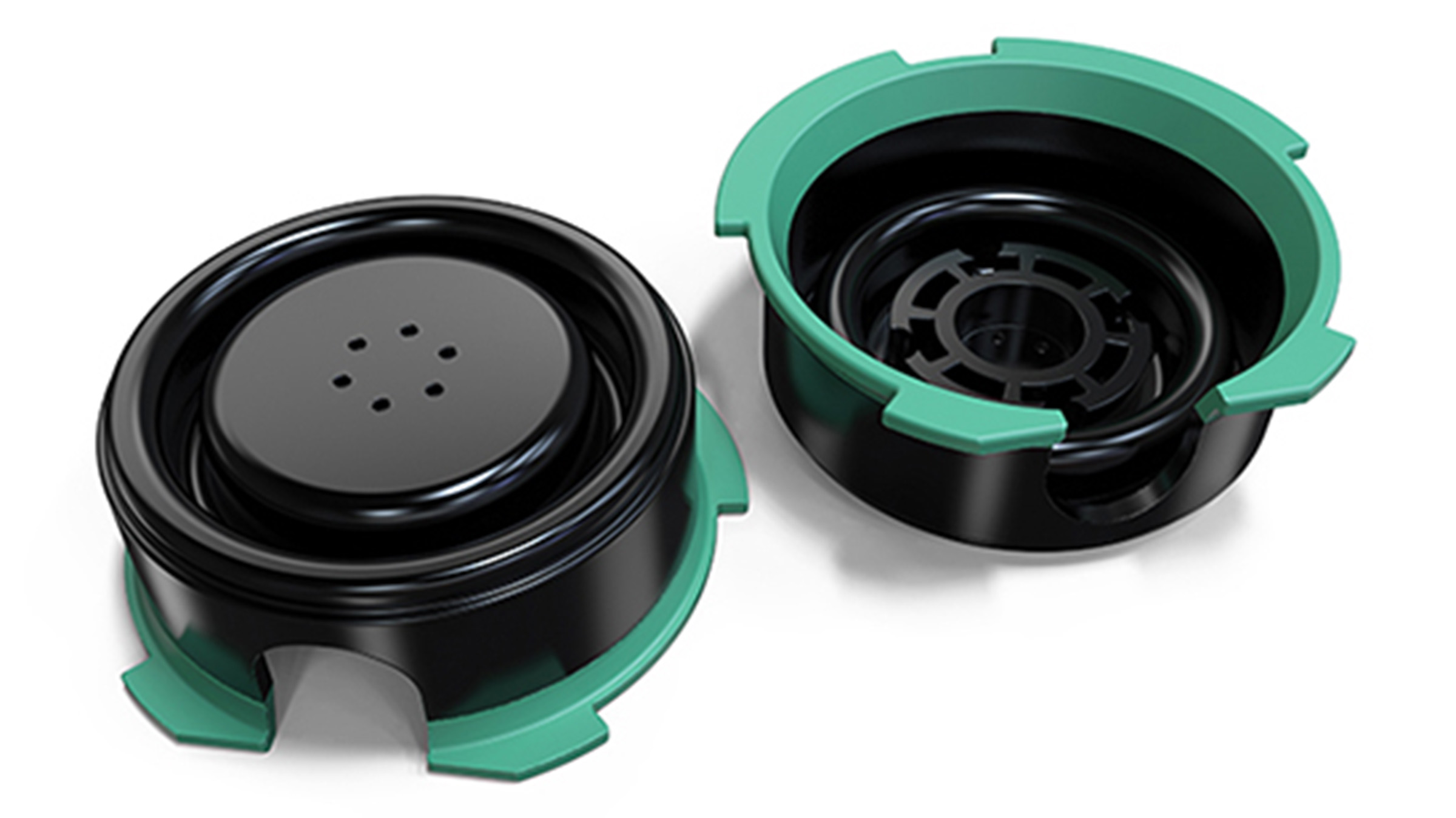
ABS
Lipstick tube shells, Compact powder cases, Perfume caps, Electric shaver housings, Nail polish bottle holders…
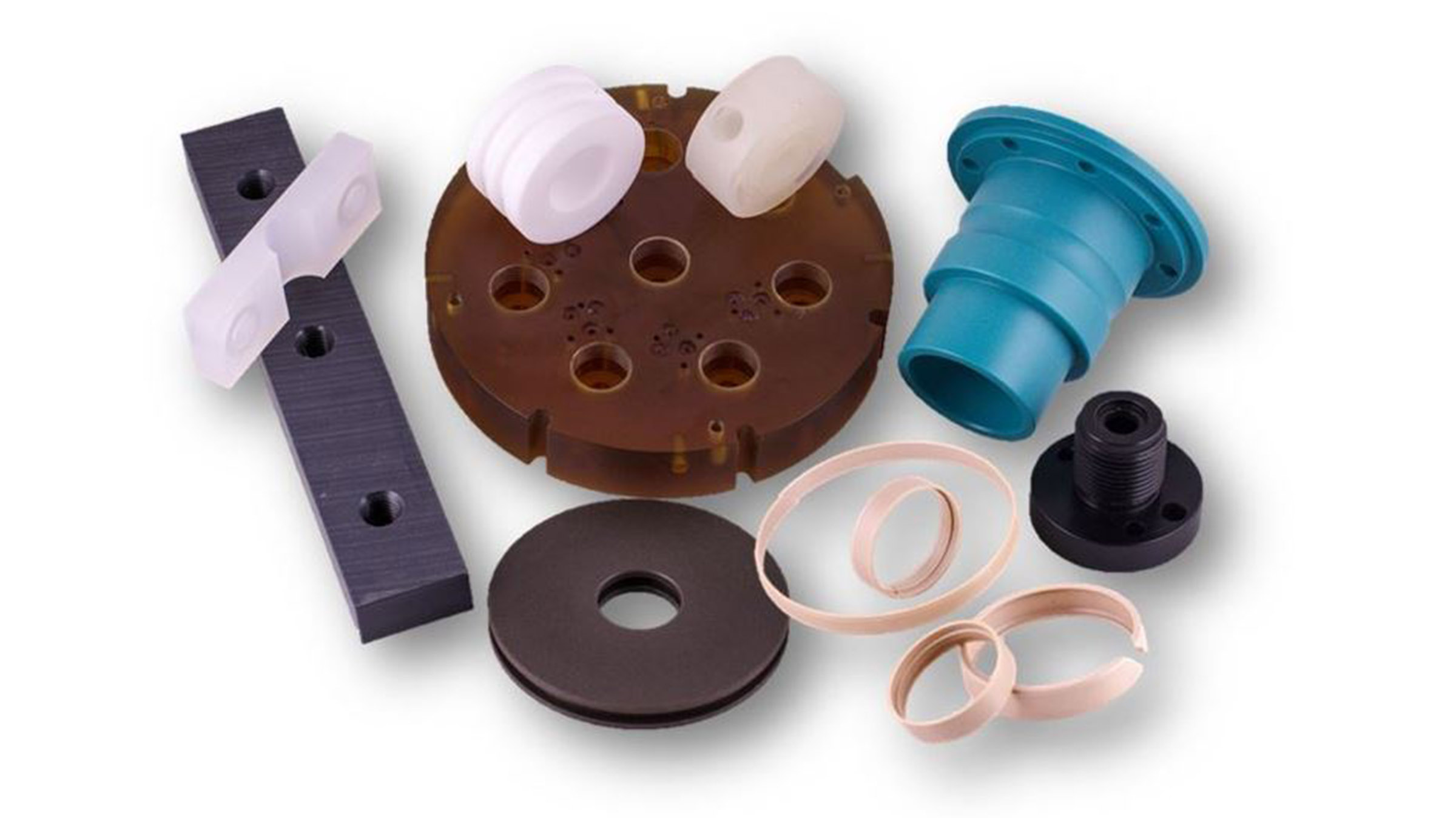
PA
Hairbrush bristles, Mascara wands, Compact hinges, Razor handle inserts, Skincare device gears…
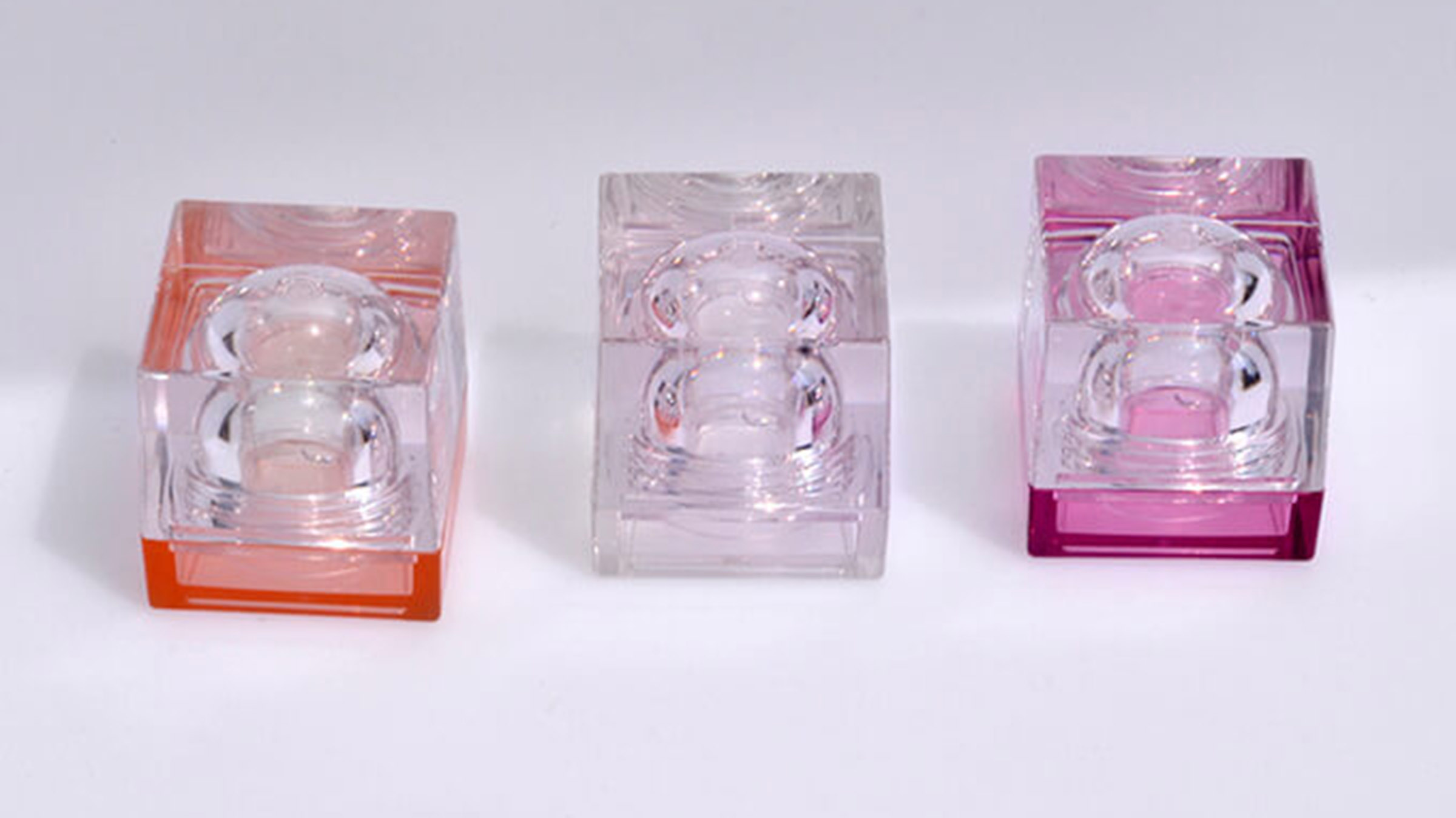
PMMA
Perfume bottles, Lip gloss tubes, Display windows on packaging, Lotion pump tops, Transparent cosmetic organizer trays…
Factory Gallery
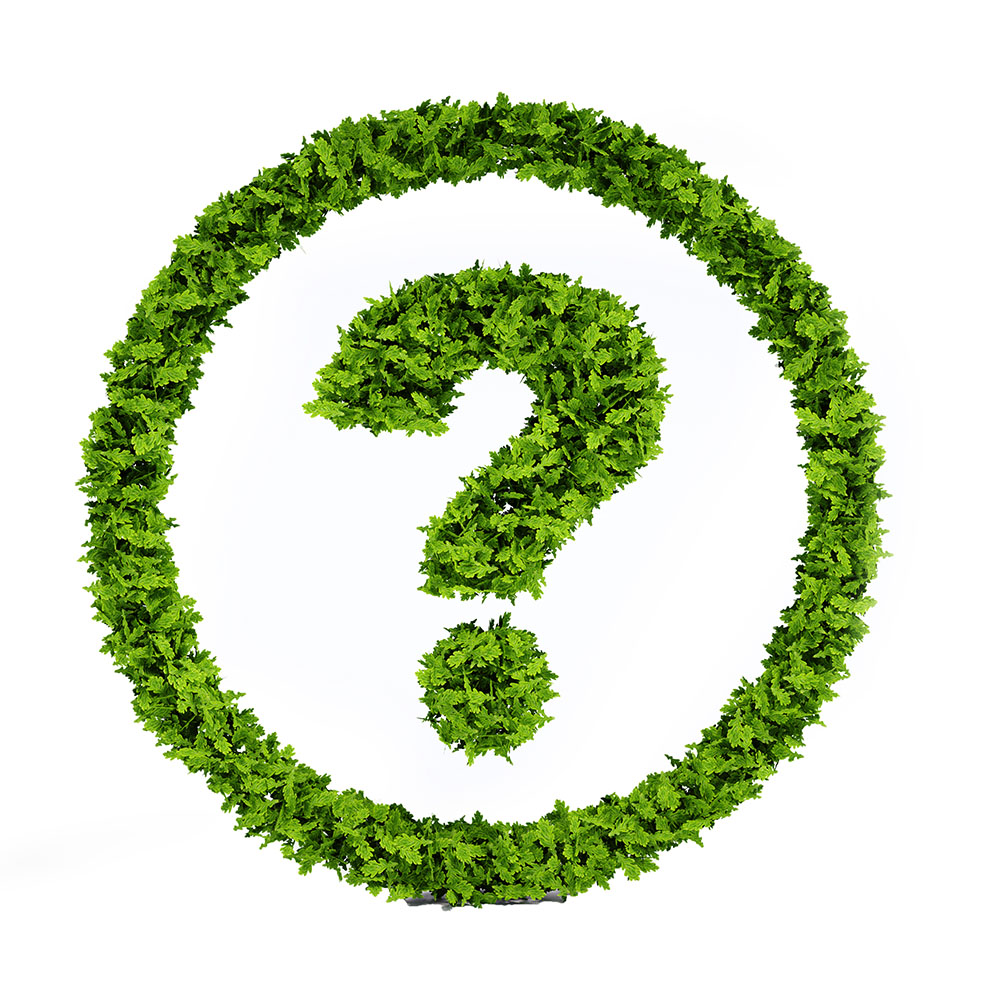
Frequently Asked Questions
Yes, we support both multi-cavity and family molds to improve production efficiency and reduce costs. This is especially useful for high-volume cosmetic items such as compact cases and lipsticks, where consistent part quality and reduced cycle time are crucial.
Yes, KingStar Mold offers professional DFM support to enhance manufacturability, reduce production costs, and improve overall product performance. For example, in a non-NDA project involving a facial brush housing, we optimized internal clip shapes, added fillets, and adjusted the core split for easier molding and improved durability. We also operate under NDAs when necessary to fully protect your proprietary designs throughout the process.
Absolutely. KingStar Mold provides low-volume injection molding and rapid prototyping using techniques like 3D printing (SLA, SLS, MJF) to validate designs and accelerate your product development timeline.
Yes, we offer full customization, including mold design based on your brand aesthetics, and surface finishing options like hot stamping, UV coating, silk screening, and pad printing to support premium, brand-aligned packaging.