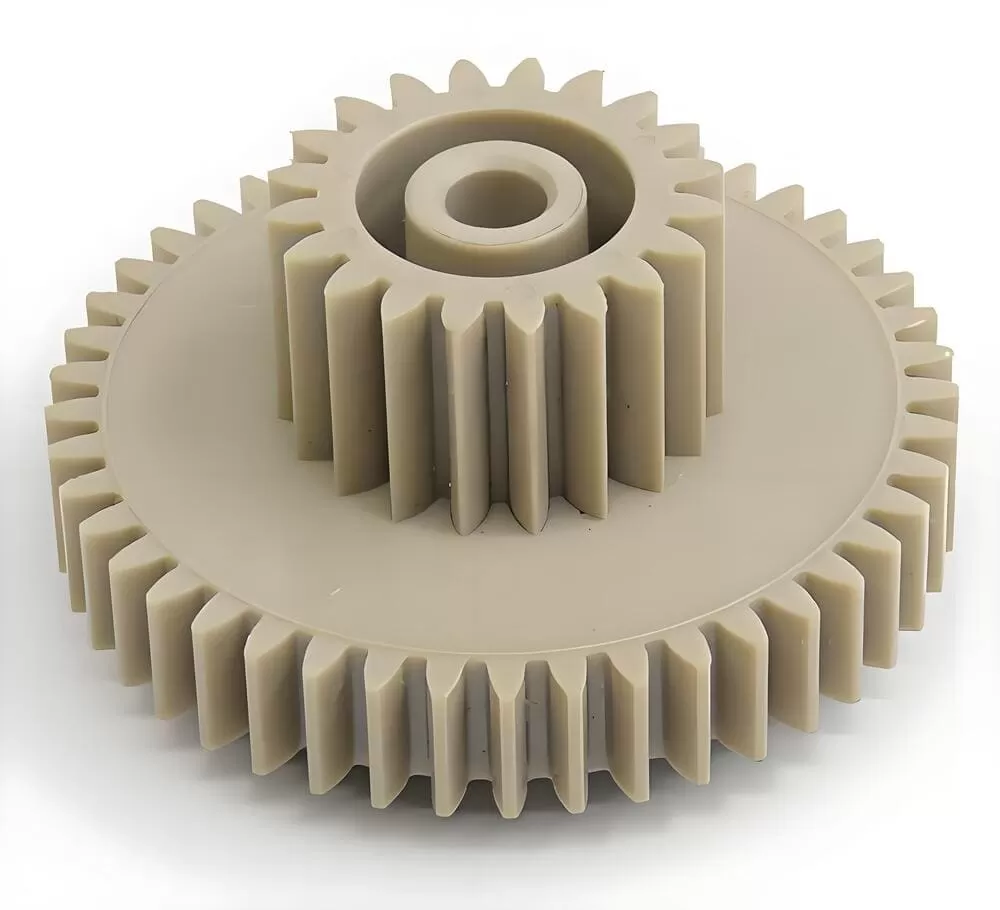
-
Resources for The Complete Guide to PEEK Injection Molding
What is PEEK?
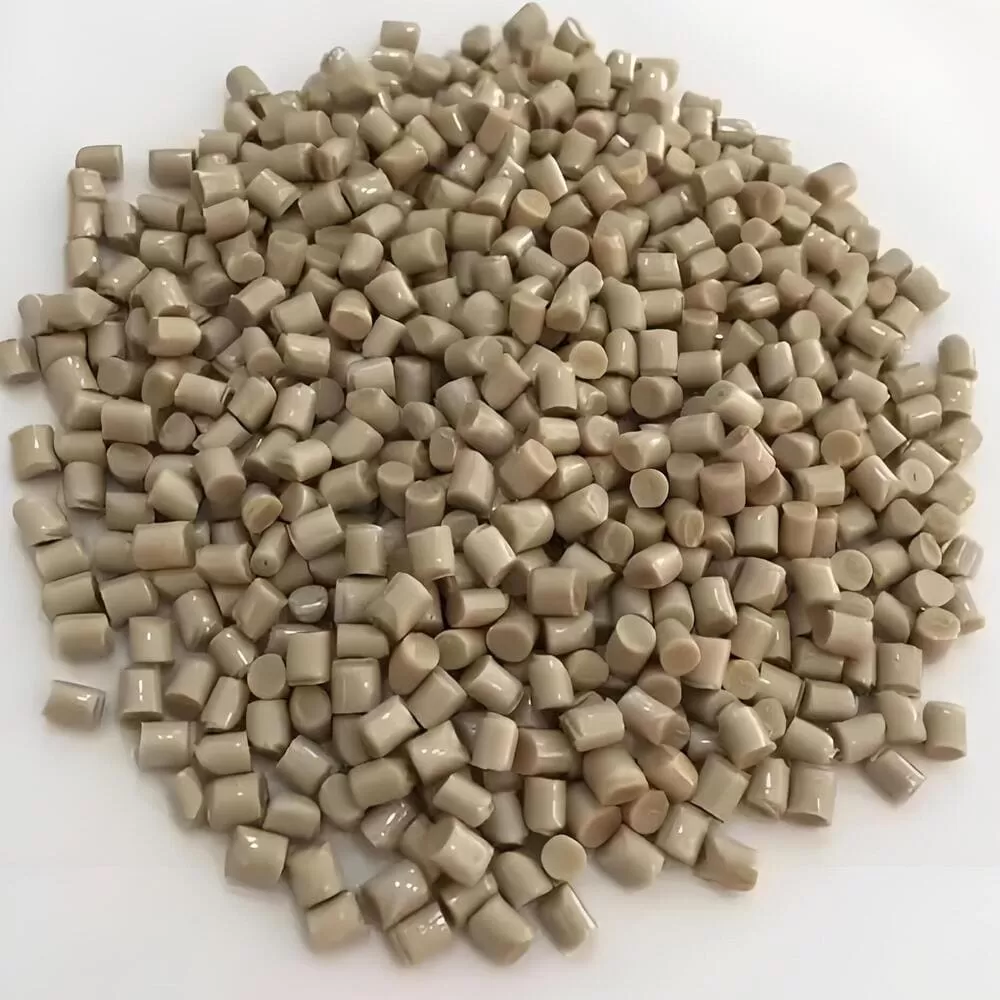
PEEK (Polyether ether ketone) is a high-strength, semi-crystalline thermoplastic polymer valued for its outstanding thermal stability, chemical inertness, and mechanical durability.
First synthesized in 1977 and commercially produced by 1981, it stands out for its ability to operate continuously at temperatures up to 250°C while maintaining excellent mechanical and electrical properties. Additionally, it performs reliably in high-pressure water or steam environments up to 300°C.
Unlike fluoropolymers like PTFE or PFA, PEEK does not include fluorine. Its unique molecular structure, comprising ether and ketone bonds, ensures outstanding thermal stability and durability under extreme conditions, making it a go-to material for challenging industrial uses.
Can PEEK materials be injection molded?
Yes, you can injection mold PEEK (Polyether Ether Ketone). PEEK has a high melting point (around 343°C/649°F), so you need specialized equipment and processing conditions. Also, PEEK has a high viscosity and a relatively low flow rate, so it’s hard to fill complex geometries and cavities. But, with the right equipment, know-how, and processing conditions, you can injection mold PEEK.
Here are some key considerations:
What are the properties of PEEK injection molding?
Property | Description |
---|---|
High Temperature Resistance | Can withstand temperatures up to 250°C (482°F) without losing strength. |
Mechanical Strength | Offers high tensile and compressive strength, ensuring durability. |
Chemical Resistance | Resists acids, alkalis, and organic solvents, making it ideal for harsh environments. |
Wear Resistance | Exceptional wear and abrasion resistance, ensuring long service life. |
Fatigue Resistance | Withstands repeated stress and strain without failure. |
Impact Resistance | Exhibits high impact strength, resistant to cracking or breaking. |
Flame Retardancy | Self-extinguishing and resistant to flame propagation. |
Radiation Resistance | Resistant to degradation from exposure to radiation. |
Electrical Insulation | Excellent dielectric properties, making it a good insulator. |
Dimensional Stability | Maintains its shape and size even under extreme temperatures and stresses. |
Low Moisture Absorption | Minimal water absorption, making it suitable for sensitive environments. |
Biocompatibility | Safe for medical and healthcare applications, including implants. |
Processing Temperature Range | Suitable for injection molding at temperatures of 370°C to 390°C. |
High Toughness | Retains toughness even at high temperatures, reducing brittleness. |
Surface Quality | Provides excellent surface finishes with minimal post-processing. |
Why is PEEK injection molding’s price so high?
- Longer Cycle Times: Due to the high melting point and viscosity of PEEK, the injection molding process for PEEK parts is slower, leading to longer cycle times and lower throughput compared to standard thermoplastics.
- Mold Wear and Tear: PEEK’s hardness and high processing temperatures can lead to greater wear on molds, requiring them to be made from high-quality, heat-resistant steel, which is more costly.
- Material Preparation: PEEK must be thoroughly dried before injection molding to avoid moisture-related defects. This additional step adds to both material and labor costs.
- Specialized Labor: Manufacturing with PEEK requires highly skilled technicians who are familiar with the material’s specific handling and molding requirements, leading to higher labor costs.
- Limited Availability: PEEK is produced in limited quantities, and only a few suppliers offer the raw material, which increases its cost due to supply-demand factors.
- Post-Processing Needs: After molding, PEEK parts often require additional finishing processes, such as trimming, grinding, or surface treatments, which can further increase overall production costs.
PEEK injection molding: Applications
PEEK is a material with excellent comprehensive properties. It can replace traditional materials such as metals and ceramics in many special fields. Its high temperature resistance, self-lubrication, wear resistance, and fatigue resistance make it one of the most popular high-performance engineering plastics today. It is mainly used in aerospace, automotive, electronics and electrical, medical equipment, and other fields.
Industry | Application Examples | Benefits of Using PEEK |
---|---|---|
Aerospace | Aircraft brackets, bushings, and insulators | High-temperature resistance, lightweight, and durable |
Automotive | Gears, seals, and fuel system components | Chemical resistance and wear resistance |
Medical | Implantable devices, surgical tools, and dental instruments | Biocompatibility and sterilization compatibility |
Electronics | Connectors, insulators, and microchip sockets | Excellent electrical insulation and heat resistance |
Oil and Gas | Valve seats, seals, and downhole tools | High pressure and chemical resistance |
Industrial | Pumps, compressor components, and wear plates | Durability and wear resistance in harsh environments |
Food Processing | Bearings, gears, and non-stick coatings | FDA compliance and chemical resistance |
Semiconductors | Wafer carriers, chip testing sockets, and cleanroom parts | Low outgassing and dimensional stability |
Energy | Battery components and insulators for renewable systems | Thermal stability and chemical resistance |
Consumer Goods | High-performance sports equipment and electronic casings | Strength, durability, and lightweight properties |