KingStar Mold’s Advice on Choosing Your PE Product Supplier
At KingStar Mold, our injection molding applications for PE materials are primarily centered on automotive components and other specialized products, where we have extensive experience. While PE is commonly used for packaging, films, barrels, and boxes, some specialized suppliers, particularly those focused on blow molding or specific container manufacturing, may offer these products with greater affordability and expertise.
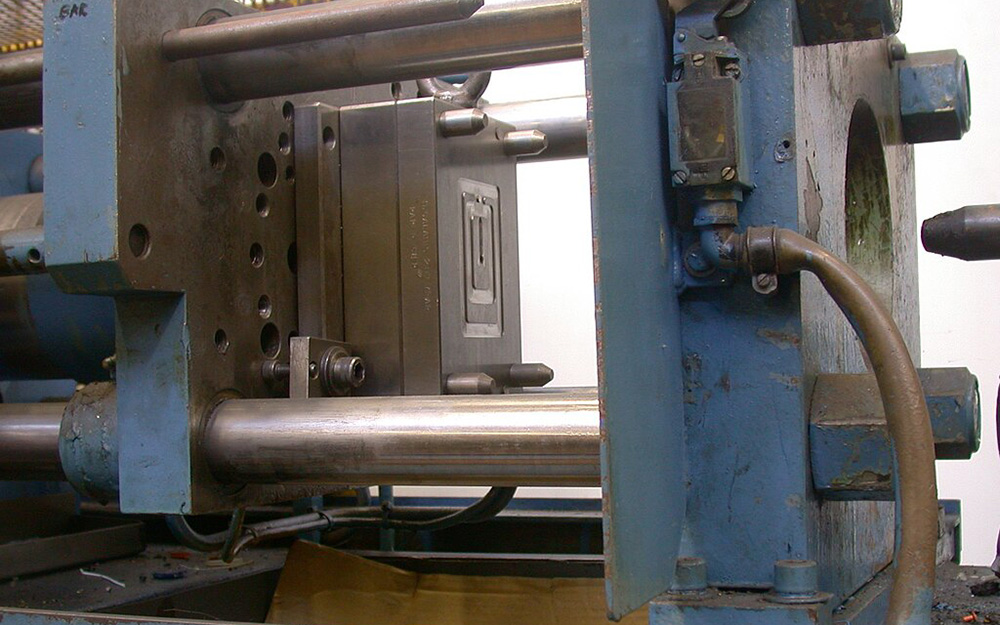
KingStar Mold’s injection molding applications for PE materials primarily focus on the automotive and electronics sectors, resulting in a relatively broader application of HDPE injection molding at KingStar Mold.
Polyethylene Type |
Applications in Injection Mold Building |
---|---|
HDPE Injection Molding |
|
LDPE Injection Molding |
|
LLDPE Injection Molding |
|
Automotive & Industrial Applications
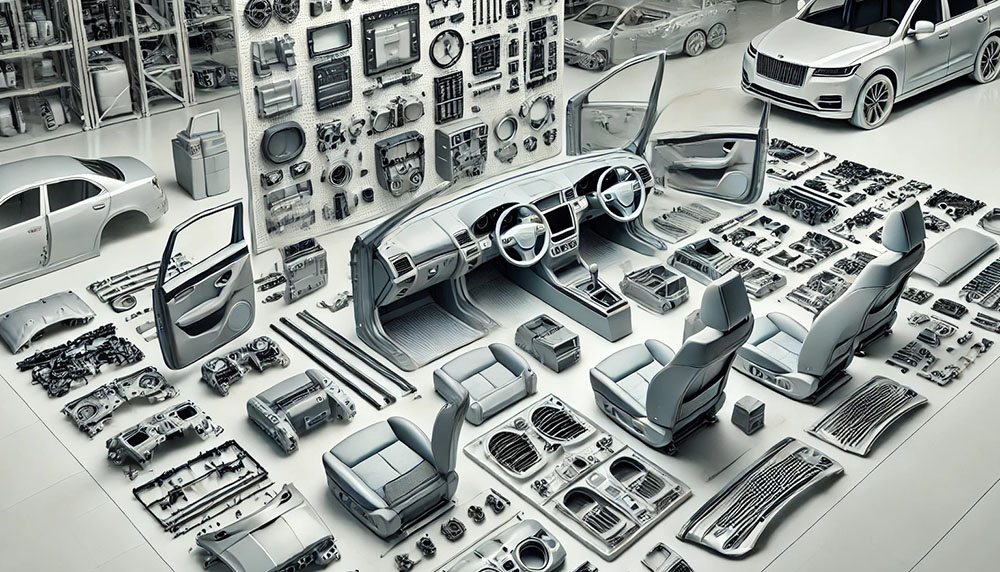
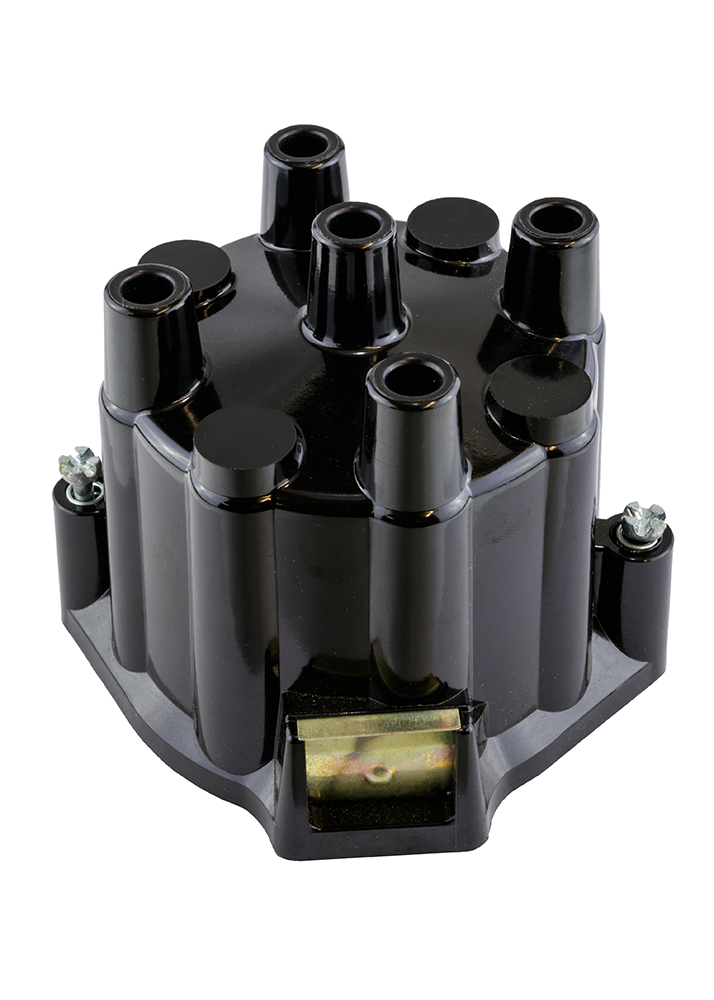
Packaging & Consumer Goods
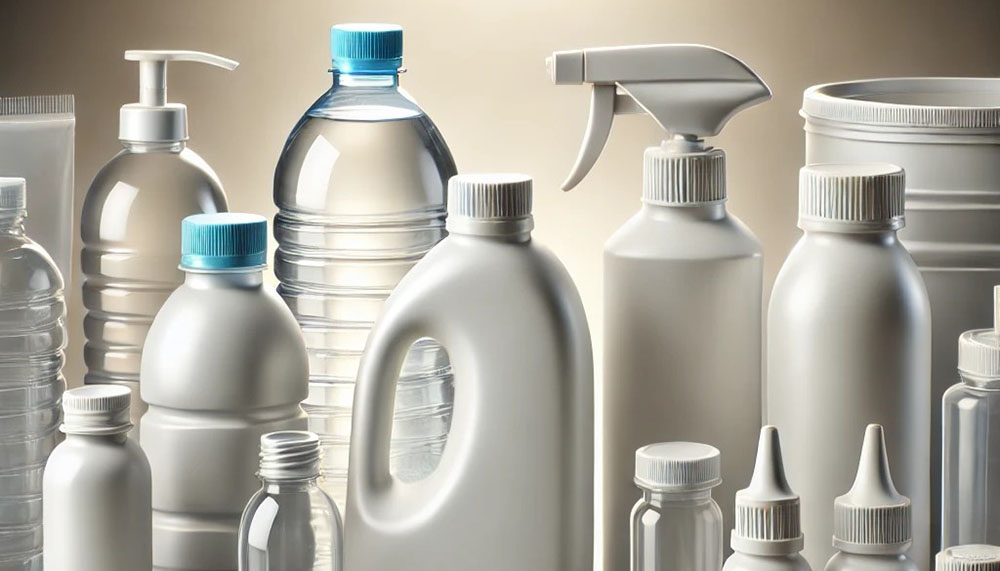
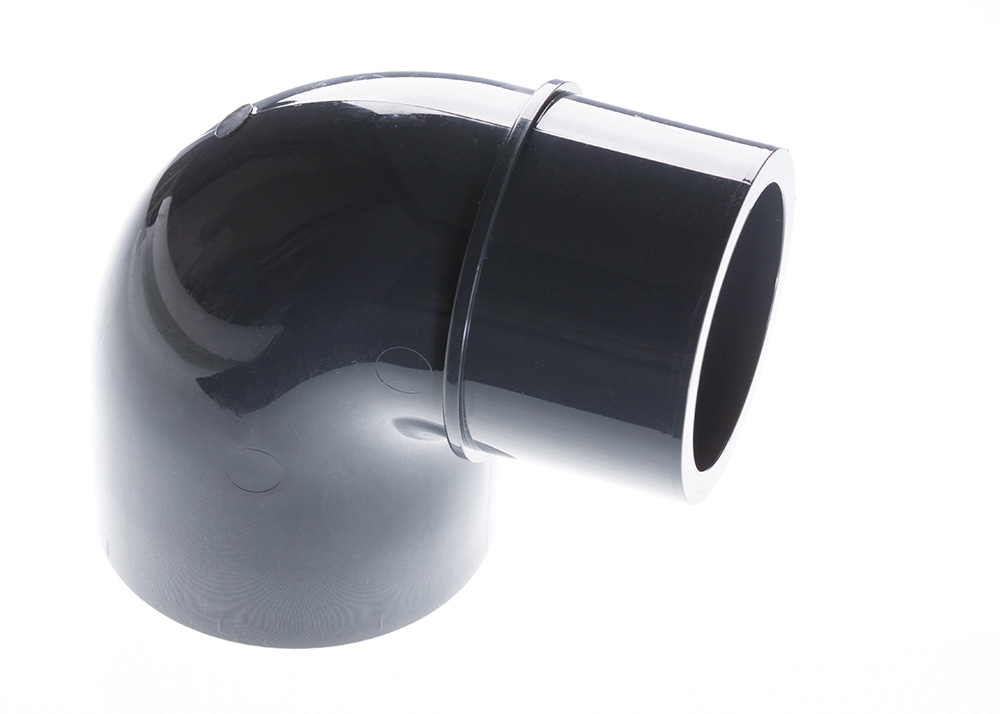
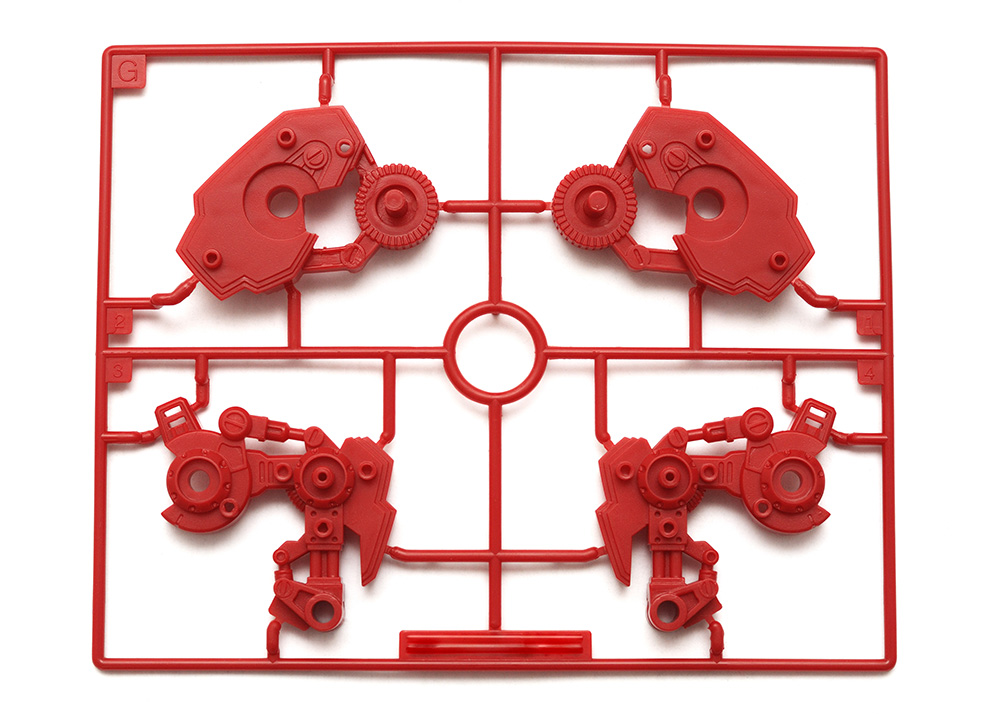
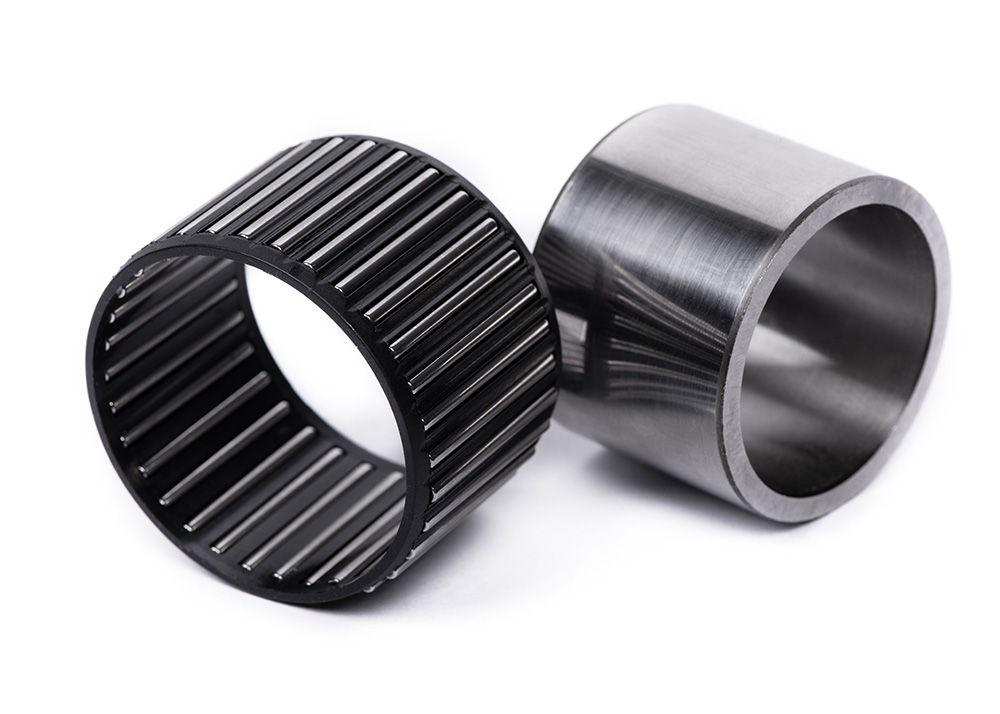
Expanding the Horizons of PE Injection Molding
At KingStar Mold, we are constantly exploring new applications and pioneering techniques that expand the potential of PE injection molding. Our commitment to innovation ensures we stay ahead of industry trends, delivering advanced, tailored solutions to meet the evolving needs of our clients.
Automotive Sector Applications
With extensive experience in the automotive industry, KingStar Mold produces high-precision components that meet the highest industry standards. From air ducts and fluid reservoirs to structural and sound-dampening panels, our molded parts are designed to enhance vehicle performance, safety, and durability.
Consumer Goods Applications
In the consumer goods sector, precision and durability are key. KingStar Mold’s injection molding ensures accurate fabrication of everyday items such as flexible packaging, storage containers, and components for household products. Our high-quality molds help deliver reliable, long-lasting solutions that meet the demands of the modern consumer.
Benefits of PE Injection Molding
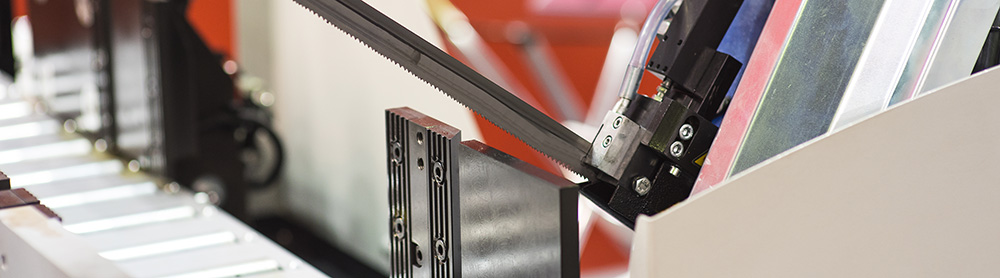
Flexibility and Versatility
LDPE and LLDPE offer exceptional flexibility, making them ideal for a wide range of applications, from squeezable bottles and soft-touch packaging to agricultural films and household containers. Their adaptability makes them perfect for products that require both shape retention and the ability to stretch or bend without cracking.
Chemical Resistance
PE materials, particularly HDPE, are highly resistant to a wide range of chemicals, making them an excellent choice for applications in industries such as automotive and chemical handling. This resistance ensures longevity and performance, even in harsh environments, like fuel tanks, piping systems, and fluid reservoirs.
Cost-Effectiveness and Efficiency
PE injection molding offers a highly cost-effective solution for mass production. The relatively low cost of raw PE materials combined with efficient molding processes allows manufacturers to produce high-quality products at competitive prices, making it a popular choice for consumer goods, packaging, and industrial applications.
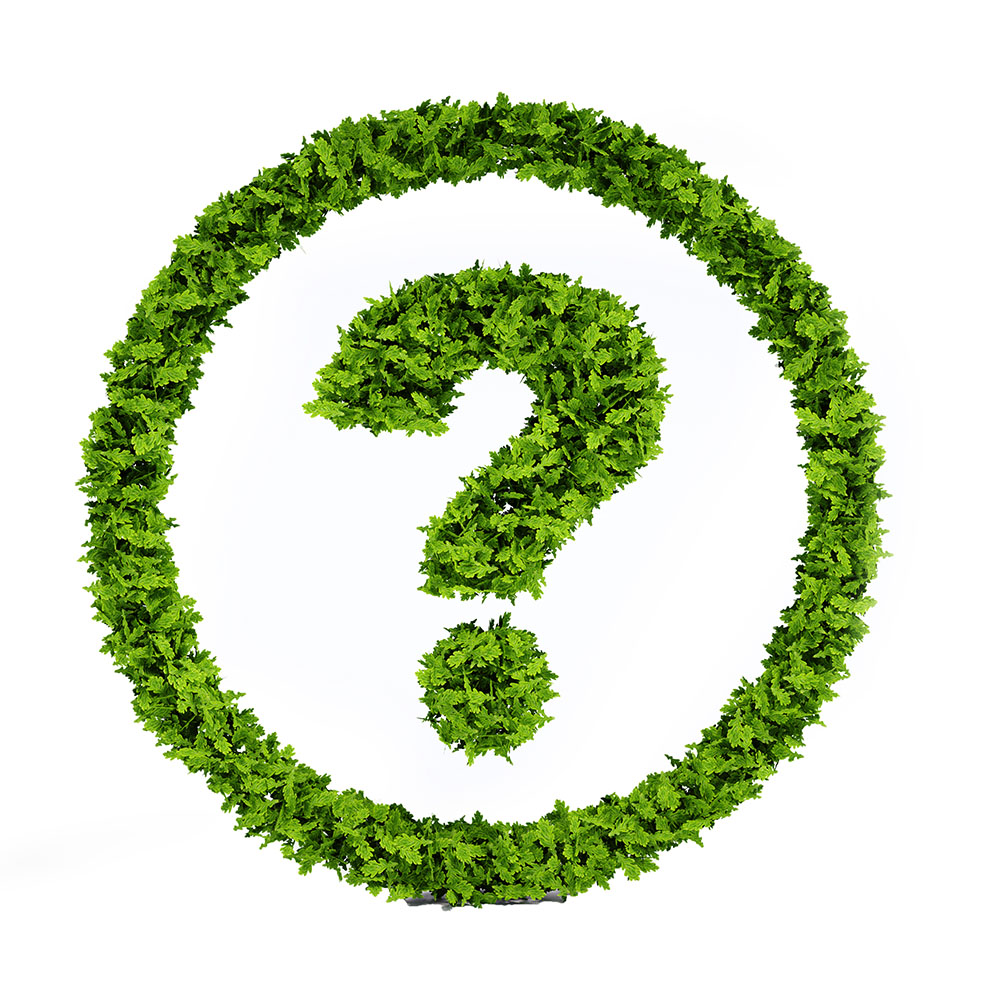
PE is more flexible and cost-effective than some other materials, making it a preferred choice for many applications, especially those requiring good chemical resistance and low production costs.
Yes, PE injection molding is highly suitable for high-volume production due to its ability to quickly produce large quantities of consistent, high-quality parts.
PE injection molding is used for manufacturing products such as plastic bottles, containers, toys, automotive parts, pipes, and packaging materials.
PE offers advantages such as high impact resistance, durability, flexibility, and excellent chemical resistance. It’s also cost-effective and ideal for producing lightweight, durable parts.
Common types of polyethylene used in injection molding are Low-Density Polyethylene (LDPE), High-Density Polyethylene (HDPE), and Linear Low-Density Polyethylene (LLDPE), each offering unique properties like flexibility, strength, and chemical resistance.
PE injection molding is a manufacturing process where molten polyethylene plastic is injected into a mold to create custom parts and components. At KingStar Mold, we specialize in delivering high-quality PE injection molding solutions tailored to your specific needs.
KingStar Mold employs rigorous quality control processes, including real-time monitoring, mold inspections, and compliance with industry standards, ensuring consistently high-quality parts.
PA injection molding typically uses steel molds, which offer durability and the ability to handle high-pressure molding processes.
Yes, PA injection molding is highly versatile and can produce complex, intricate parts with fine details and tight tolerances.
Glass-filled PA increases material strength, stiffness, and dimensional stability, making it ideal for high-performance parts.
PA materials need to be dried to a specific moisture content before molding to prevent defects such as bubbling or inconsistent part quality.
PA materials can absorb moisture, affecting the molding process and part quality, requiring precise drying and careful material handling.