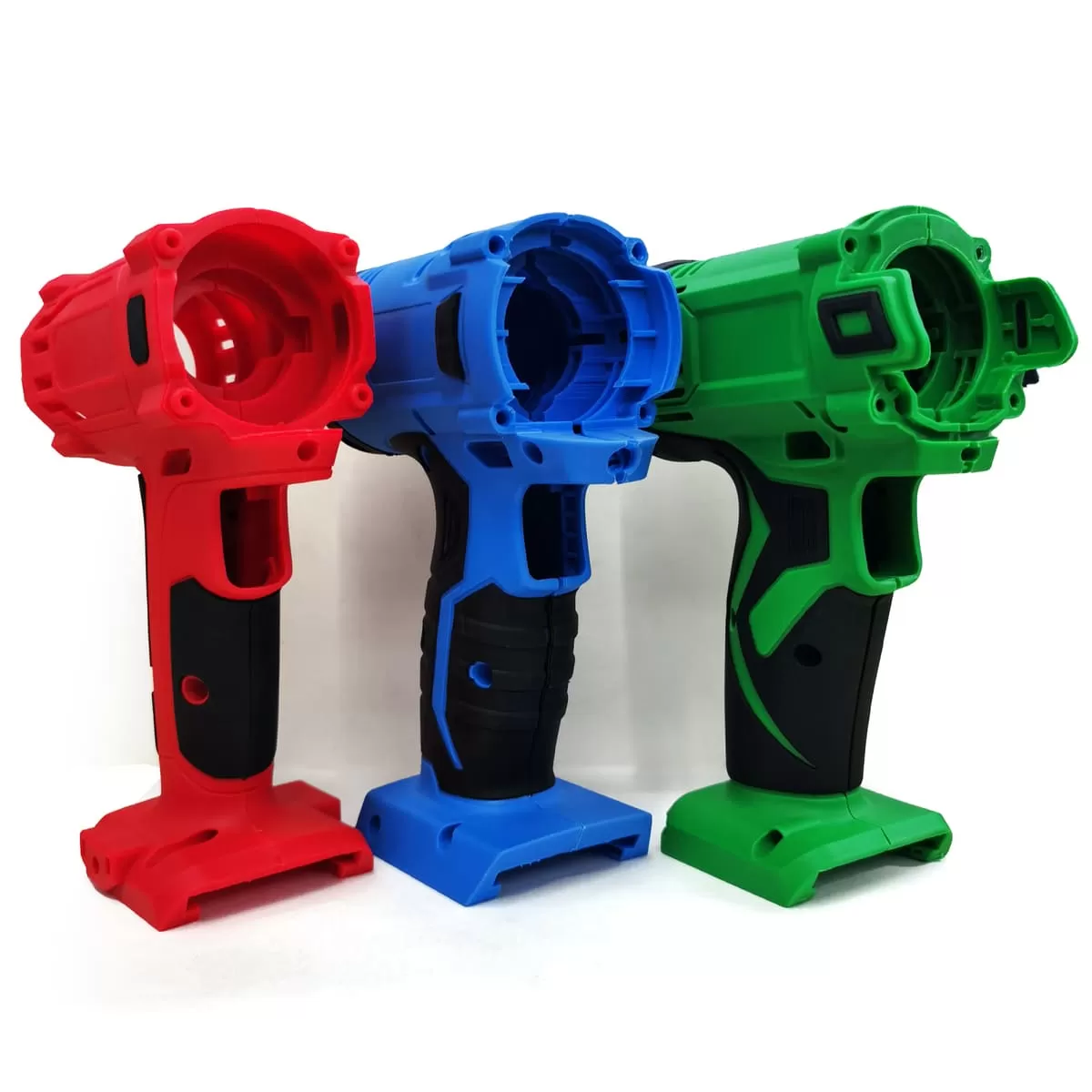
-
Resources for The Complete Guide to Overmolding
What is Overmolding?
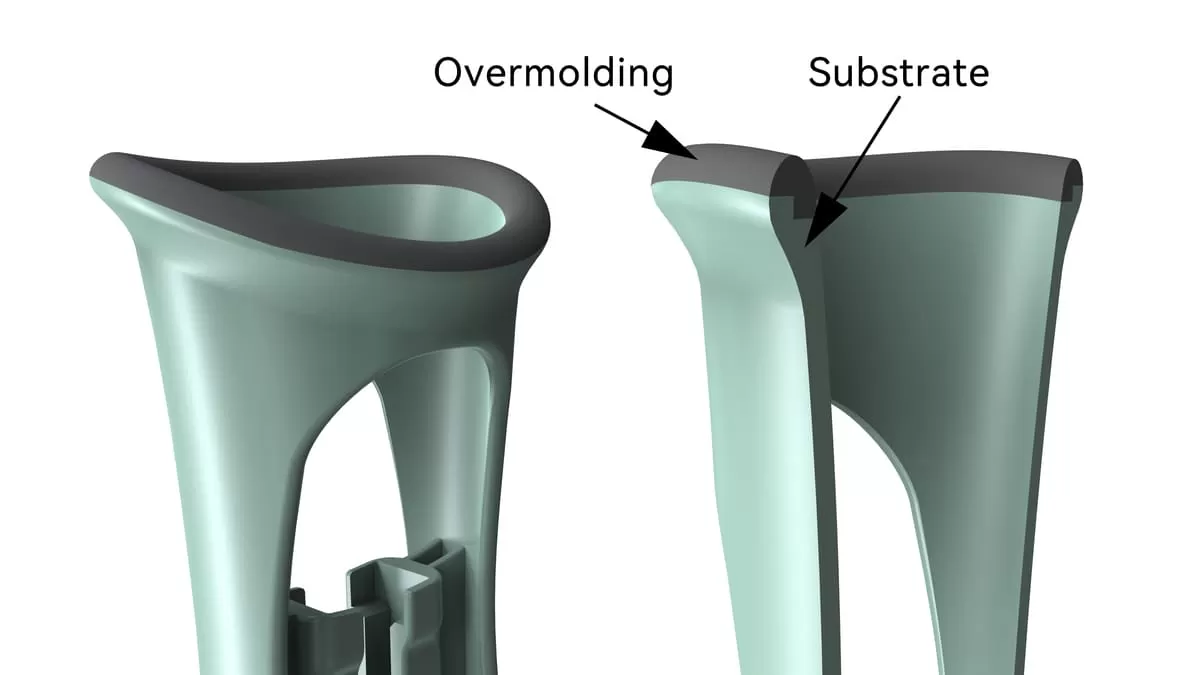
Overmolding is an injection molding process where you mold one material over top of another material or substrate. The first material is usually made of a different material or has a different shape than the second material. Overmolding is used in many industries including medical devices, automotive, aerospace, and consumer products.
To overmold, you first mold or make the first part. Then you mold the second material over top of the first part. The second material can be a different plastic, rubber, or other material that gives the part special properties like flexibility, durability, or looks.
How Does Overmolding Work?
Overmolding is a tricky process that has a bunch of steps and needs you to plan and do it right. Here’s a quick look at how overmolding works:
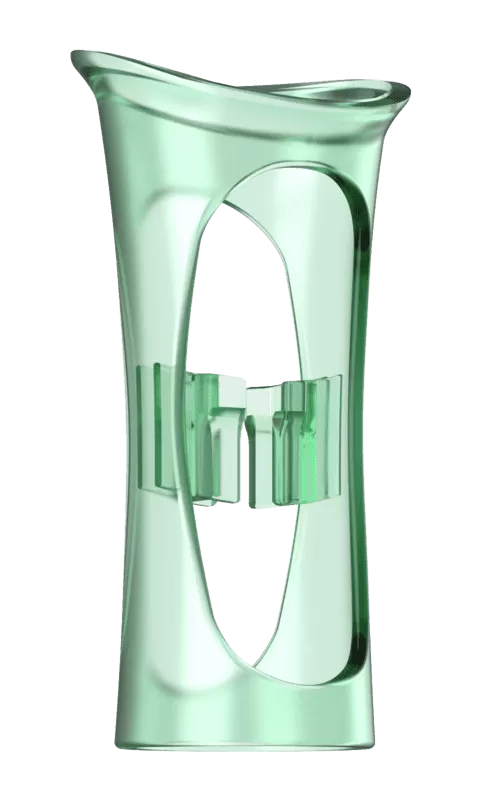
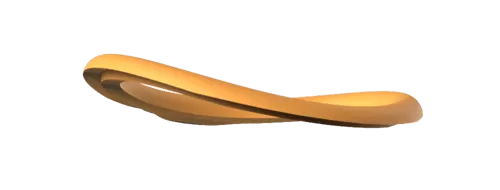
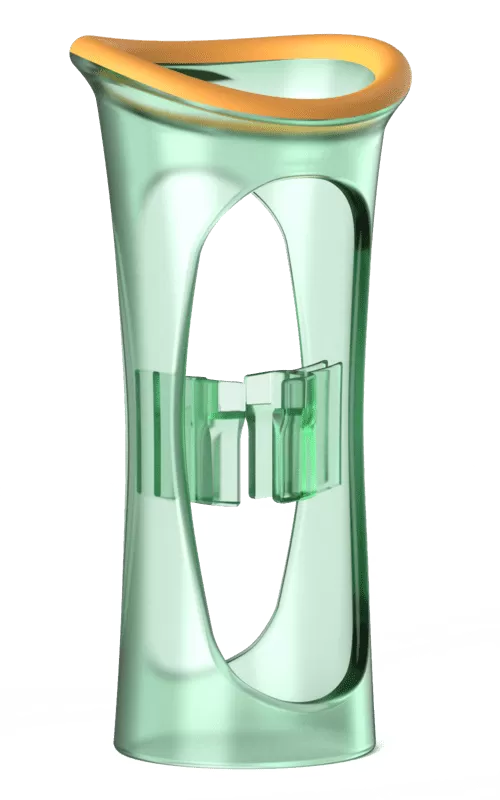
Overmolding Material Bonding Chart
You can bond overmolded materials together, but you need to make sure the materials work together to get the bond strength you want. If you really need the bond, you should definitely add a mechanical bond. An undercut is a good example of a mechanical bond.
Overmolding Material | PP T30S | ABS DG417 | ABS/PC AC2300 | PC Makrolon® 2405 | PBT HR5330 | PA J2700 |
TPE | C | M | M | M | M | M |
TPR | C | C | C | M | M | M |
TPU | M | C | C | C | C | M |
TPV | C | M | M | M | M | M |
TPC | M | C | C | C | C | C |
What are the Benefits of Overmolding?
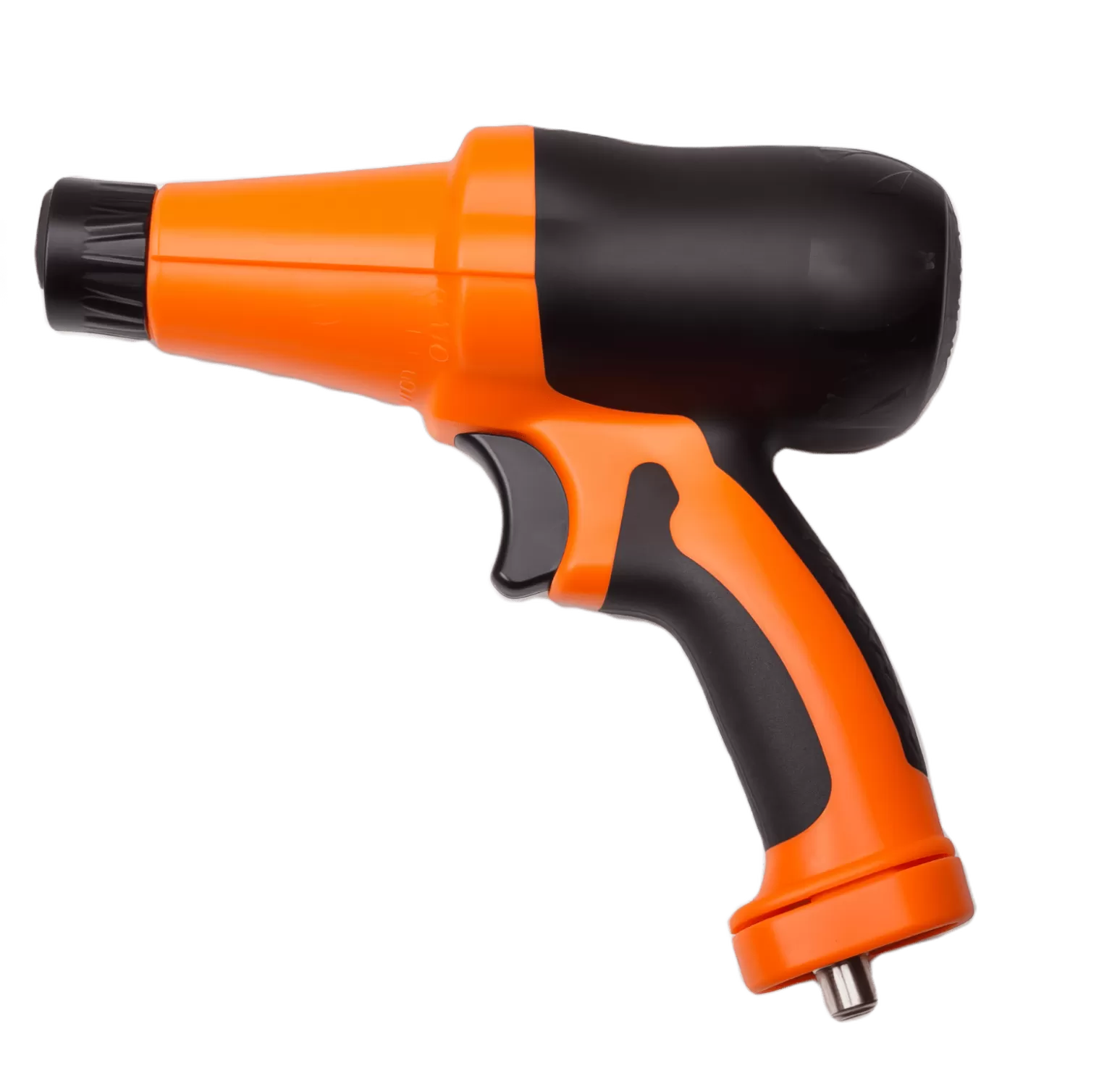
Better Performance: Overmolding can be used to make the primary part better by adding new materials or properties that make it work better.
Make it Look Good: Overmolding can make the main part look better. It makes it look nice.
Lose Weight: Overmolding can help you lose weight. It makes your main part lighter, but still strong and tough. It makes it easier to carry and handle.
Better Thermal Resistance: Overmolding can be used to make the primary part more resistant to heat, so it won’t get too hot or cold.
Stronger and Tougher: Overmolding can make your part stronger and tougher, so it lasts longer and performs better.
Better Electrical Insulation: Overmolding can be used to improve the electrical insulation of the main part, which helps protect it from electrical shock and damage.
Better Looking: Overmolding can make the main part look better. It can be made to look more attractive.
What are the Applications of Overmolding?
Overmolding is a versatile manufacturing process that can be used to create complex parts with unique properties and functionality, making it applicable to a wide range of industries.
Handware tools: Overmolding can be used to make hand tools like wrenches, pliers, and screwdrivers, knives, saw blades, and drill bits tougher and easier to hold.
Medical Devices: Overmolding is used in medical devices like syringes, needles, and implantable devices, where precision and accuracy are crucial.
Automotive: Overmolding is used in car stuff like dashboards, door handles, and trim components, where you need them to last and work good.
Industrial Equipment: Overmolding is used in industrial equipment like machines, pumps, and valves where you need them to be tough and work good.
Consumer Products: Overmolding is used in consumer products like toys, appliances, and electronics, where looks and how it works are important.
Overmolding Design Guide: Top 10 Tips For Overmolding
Overmolding design is hard. But you’ve got to make sure your parts are designed right for the overmolding process. Here are some design tips for overmolding.
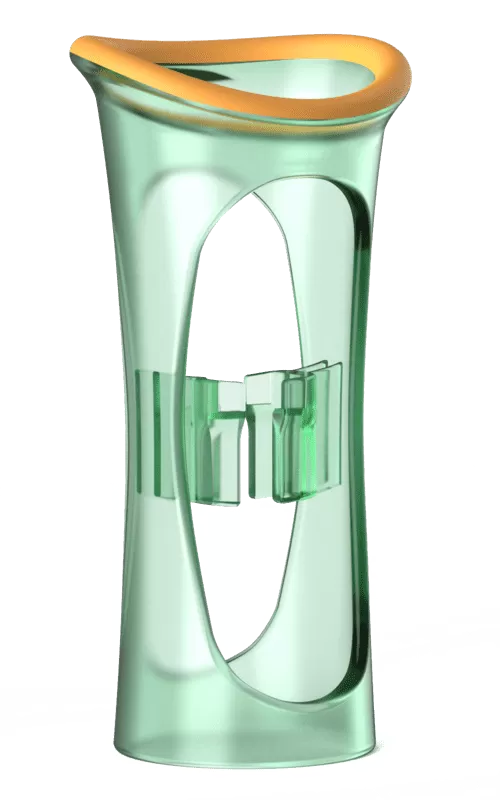
① Don’t overmold the whole base substrate. Overmold it in sections.
② Don’t make edges that are too thin or that come to a point. When you inject the plastic, the flow slows and then cools. That makes the plastic stick to the part less.
③ Keep the overmolding thickness consistent: the overmolding should be between 1.5 and 3 millimeters (0.060 and 0.120 inches).
④ Try not to have sudden changes in thickness. If you need different thicknesses, try to make them as smooth as possible.
⑤ Lots of overmolding materials are stretchy, so you can put smooth bumps into the design.
⑥ Make sure the overmolding layer is thinner than the substrate underneath to help prevent warping.
⑦ To make sure the overmolding cavity bonds well, you need to account for substrate shrinkage.
⑧ Use a TPE or TPU that has a melt temperature lower than the substrate.
What are the Common Problems and Solutions for Overmolding?
The typical challenges in overmolding include incomplete filling of the overmold or substrate, flashing, and adhesion issues. Here’s how you can address these problems effectively.
Observation | Potential Causes | Corrective Actions |
---|---|---|
Adhesion Problems | Incompatible materials or insufficient bonding area | Use compatible materials, increase bonding surface, optimize mold temperature. |
Incomplete Filling | Low injection pressure or insufficient material flow | Increase injection pressure, adjust flow rate, or redesign mold gating. |
Flashing | Excessive injection pressure or mold misalignment | Reduce injection pressure, inspect mold alignment, and repair damaged mold areas. |
Surface Defects or Voids | Trapped air or uneven cooling | Add or optimize venting, adjust cooling time, and balance material temperature. |
Shrinkage or Warping | Improper cooling or uneven material shrinkage | Ensure uniform cooling and use materials with low shrinkage rates. |
Burn Marks or Discoloration | Overheating material or trapped gases | Lower injection temperature and improve mold venting to avoid gas buildup. |
Inconsistent Overmolding | Variations in material flow or temperature | Standardize material preheating, monitor injection parameters, and maintain consistent cycle times. |
Cracking or Brittle Parts | Material incompatibility or excessive stress | Choose compatible materials, reduce ejection force, and optimize mold design to minimize stress points. |
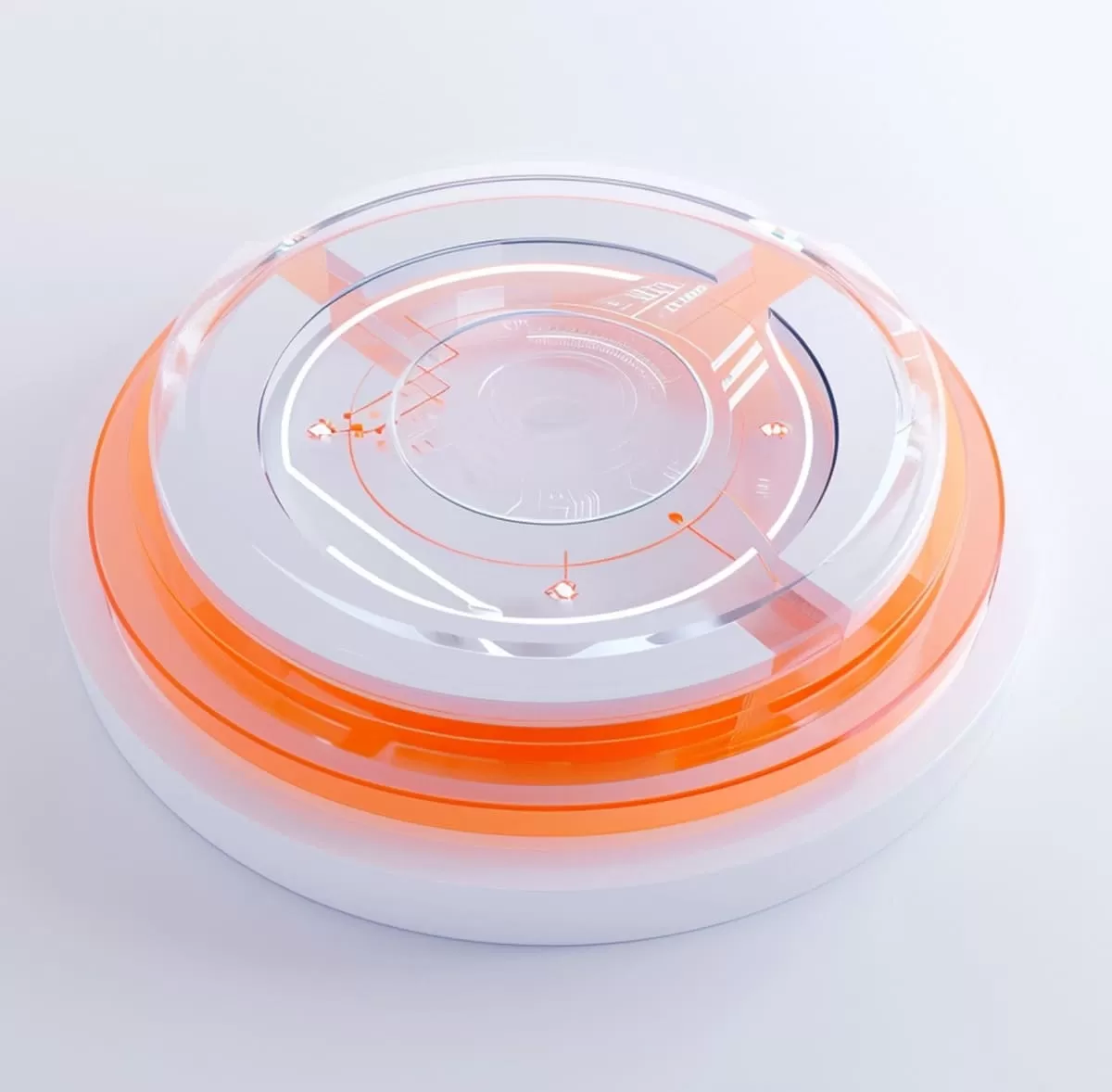
What is 2K Injection Molding?
2K injection molding, also known as 2K molding, is a manufacturing process where you inject two different materials or colors of plastic into a mold to make one part with unique properties and looks. This process is also known as “two-color injection molding” or “dual-color injection molding.”
In 2K injection molding, you usually inject the two materials at the same time, but separately, into the mold through two different gates. This is different from two-shot injection molding, where you inject the two materials one after the other.
How Does 2K Injection Molding Work?
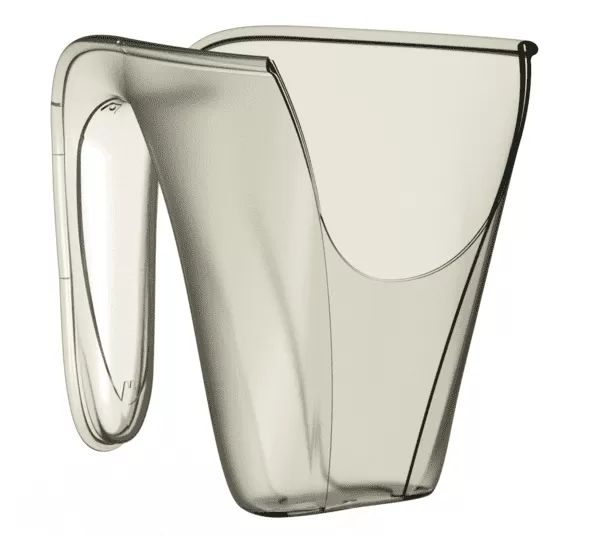
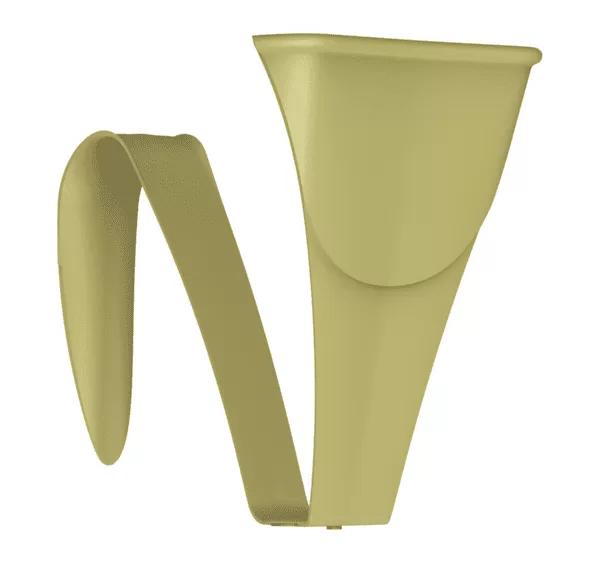
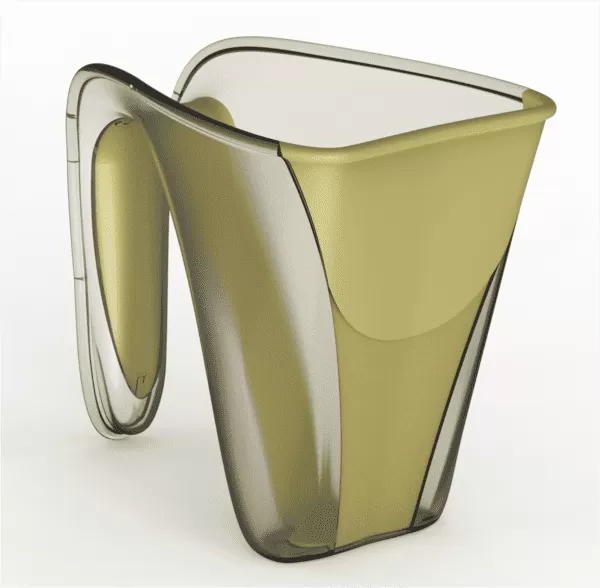
2K Injection Molding vs. Overmolding
2K injection molding and overmolding are two different manufacturing processes used to create complex plastic parts with multiple components. The choice between 2K injection molding and overmolding depends on the specific requirements of the part, including design complexity, material properties, and production volume.
Specific Requirements | 2K Injection Molding | Overmolding |
Design Complexity | ① Simple Geometries ② Limited design complexity | ① Complex Geometries ② Complex Designs |
Production Volume | ① high-volume production | ① Medium and lower-volume production |
Injection Machine | ① 2K injection molding machine ② Injection Machine Expensive | ① Single nozzle injection molding machine ② Injection Machine Cheap |
Injection Process | ① Two materials are molded together in the same process | ① Two materials are molded separately |
What are the Benefits of 2K Injection Molding?
2K injection molding offers a bunch of benefits, including:
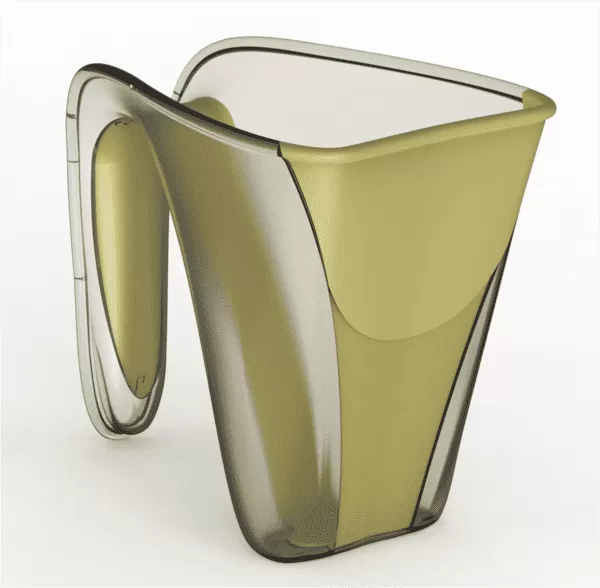
- Creative Aesthetics
Achieve eye-catching designs, unique color combinations, and intricate patterns that are unattainable with standard injection molding. - Streamlined Assembly
By integrating materials during the production process, 2K molding removes the need for separate part assembly, saving labor costs and improving efficiency. - Improved Part Quality
Parts benefit from increased strength, enhanced durability, and appealing aesthetics by combining two materials. - Enhanced Functionality
Tailor materials to provide specific advantages, such as better grip, electrical conductivity, or superior thermal insulation. - Greater Design Flexibility
Complex shapes and geometries become achievable, offering unparalleled design possibilities compared to traditional methods.
Save money: By using a 2K mold, you can cut costs by not having to assemble separate parts and using less material.
More complex designs: 2K molding allows you to create parts with intricate designs and shapes that would be tough to make with traditional molding.
Better durability: The two materials can be made to be more durable and last longer.
2K injection molding has a wide range of applications across various industries like:
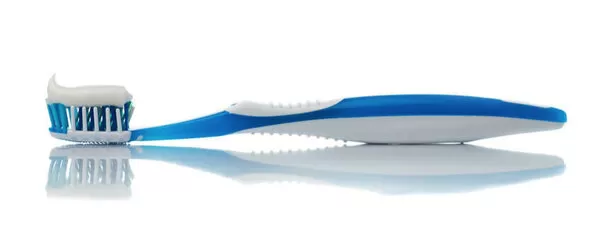
- Medical: Test strips, implantable devices, and syringes.
- Electronics: Connectors, enclosures, and other essential electronic parts.
- Automotive: Door handles, dashboard trim, and various interior elements.
- Industrial: Components for pumps, valves, and other industrial machinery.
- Aerospace: Satellite parts, high-performance aircraft components, and other critical applications.
- Consumer Products: Household goods, toothbrushes, toys, and games.
2K Injection Molding vs Overmolding: Which Is Better?
Here’s a price comparison of 2K Injection Molding and Overmolding for a specific project at quantities of 5,000, 10,000, 50,000, and 100,000 Pcs/Order.
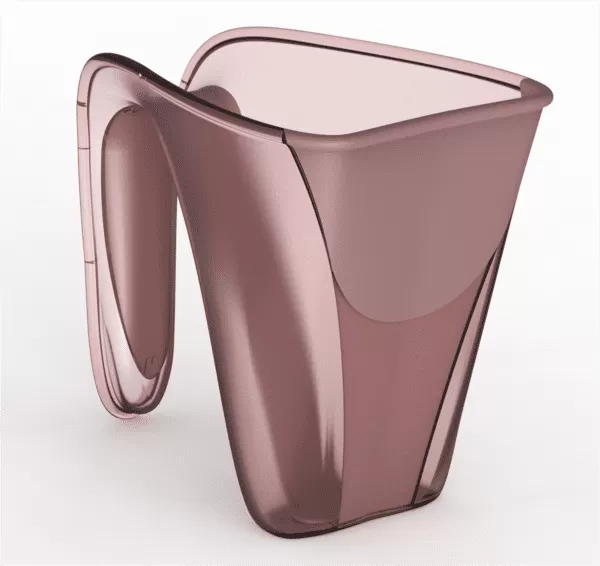
Product Quantity/ PCS | Mold Cost/ $ | Part Price/ $ | Total Price/ $ | Average Part Cost/ $ | Mold Cost / $ | Part Price/ $ | Total Price/ $ | Average Part Cost/ $ | 2K Injection Molding Vs. Overmolding |
5000 | 18000 | 0.65 | 21250 | 4.25 | 12000 | 0.78 | 15900 | 3.18 | Overmolding |
10000 | 18000 | 0.63 | 24300 | 2.43 | 12000 | 0.76 | 19500 | 1.96 | Overmolding |
50000 | 18000 | 0.58 | 47000 | 0.94 | 12000 | 0.74 | 49000 | 0.98 | 2K Injection Molding |
100000 | 18000 | 0.54 | 72000 | 0.72 | 12000 | 0.72 | 84000 | 0.84 | 2K Injection Molding |