One Stop Manufacturing Service
Help You Turn An Idea Into A Product
8-Step Product Development Process
Step | Step Description | How KingStar Helps/Contributes |
---|---|---|
1. NDA Signing | Sign a Non-Disclosure Agreement to protect the client's intellectual property | KingStar is ready to sign NDAs upon request to ensure complete confidentiality of all shared files |
2. Idea Sharing | The client shares product ideas or existing samples, including photos or sketches | Accepts photos, videos, hand-drawings, or samples to start understanding the product requirements |
3. 3D Drawing Creation | Convert initial concepts or sketches into 3D CAD models | Offers professional 3D drawing services if the client does not have their own design |
4. DFM Optimization | Evaluate and optimize design for manufacturability (Design For Manufacturing) | Provides DFM advice to improve part structure, cost-efficiency, and mold feasibility |
5. Quotation | Quote for mold making and part production after analyzing the 3D design | Delivers competitive quotes based on optimized designs, with detailed cost breakdowns |
6. Mold Design | Create detailed mold design including gating, cooling, and parting line planning | KingStar’s experienced engineers handle the complete mold design in-house |
7. Mold Fabrication | Manufacture the mold based on approved design | In-house tooling capabilities ensure quality mold fabrication and lead time control |
8. Trial & Tuning | Perform mold trials (T1, T2, etc.) and make necessary adjustments | Conducts multiple mold trials and sends sample parts for approval before mass production |
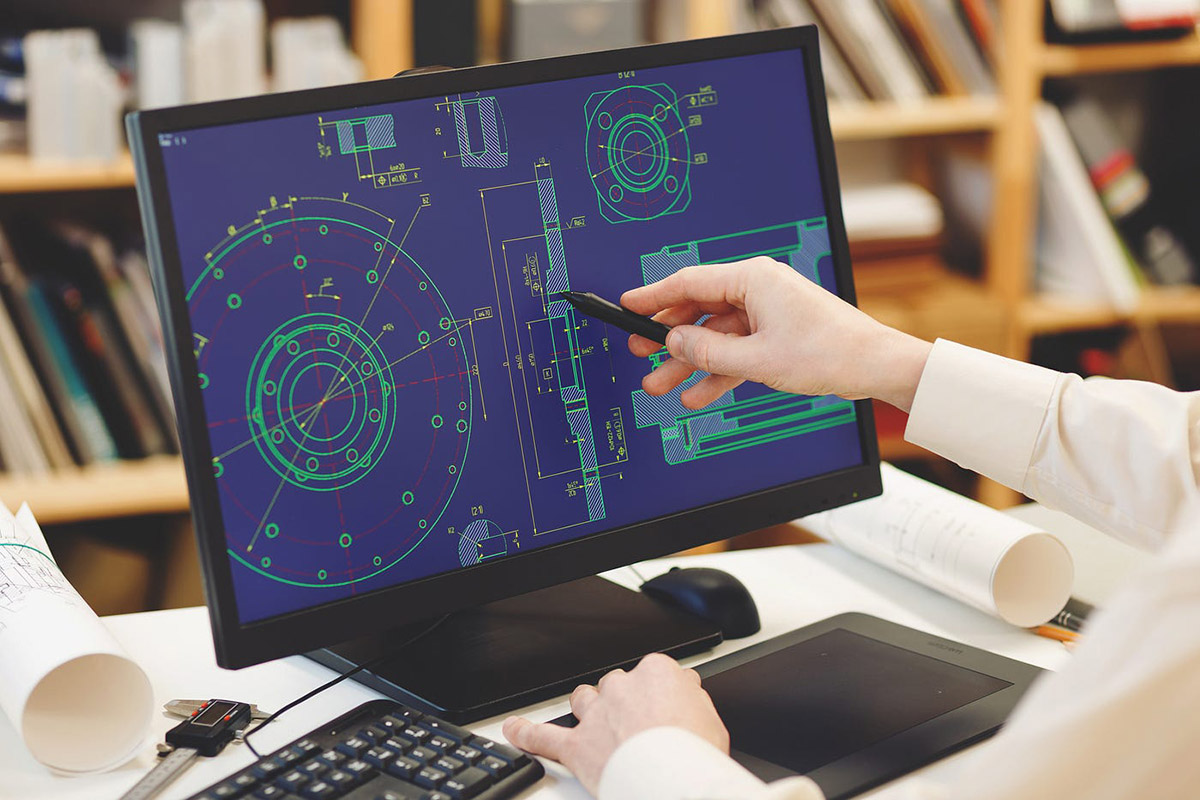
From Concept to CAD
We help you turn ideas into manufacturable designs. Our team of engineers and product designers refine your concepts, define technical requirements, and create precise 2D and 3D CAD models. Every design is developed with manufacturability in mind—ensuring a smooth handoff to prototyping and production.
Validate Before You Scale
Bring your ideas to life with functional and visual prototypes. We offer SLA, SLS, MJF, and CNC prototyping options to test form, fit, and performance. Whether you’re checking ergonomics or running field tests, our validation process minimizes risk before committing to production.
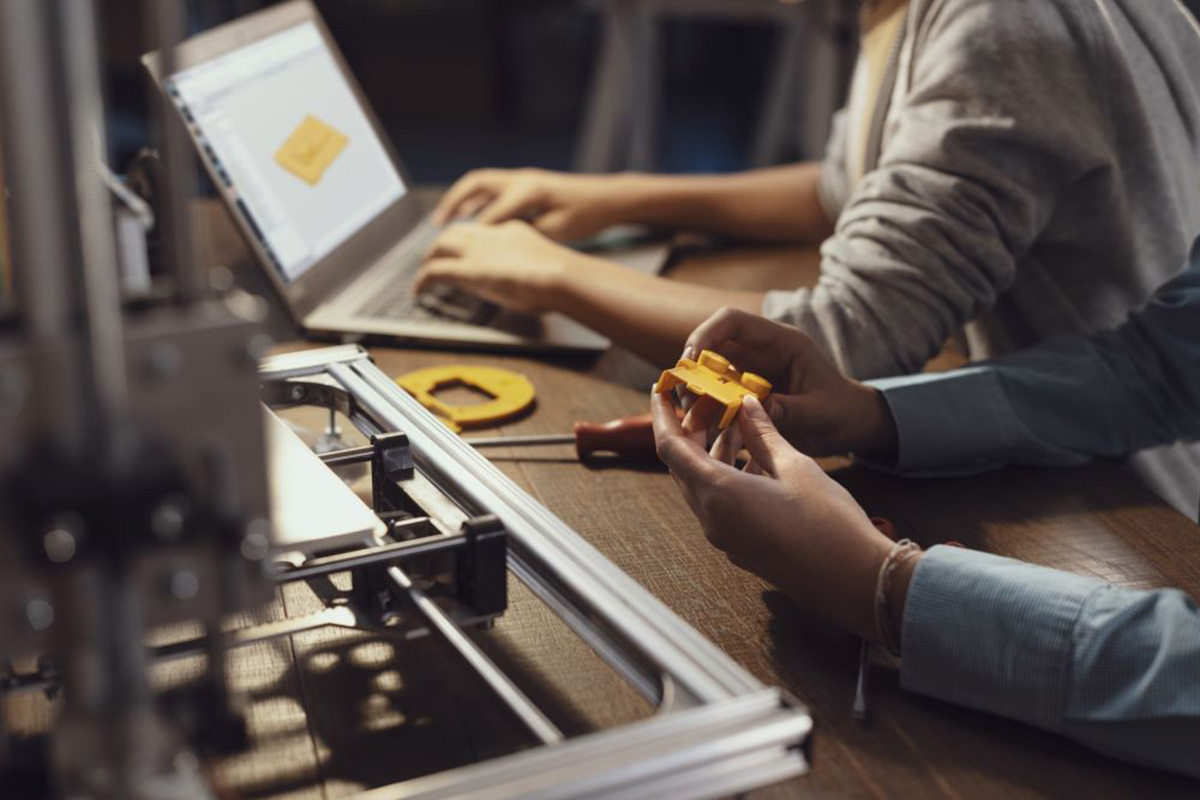
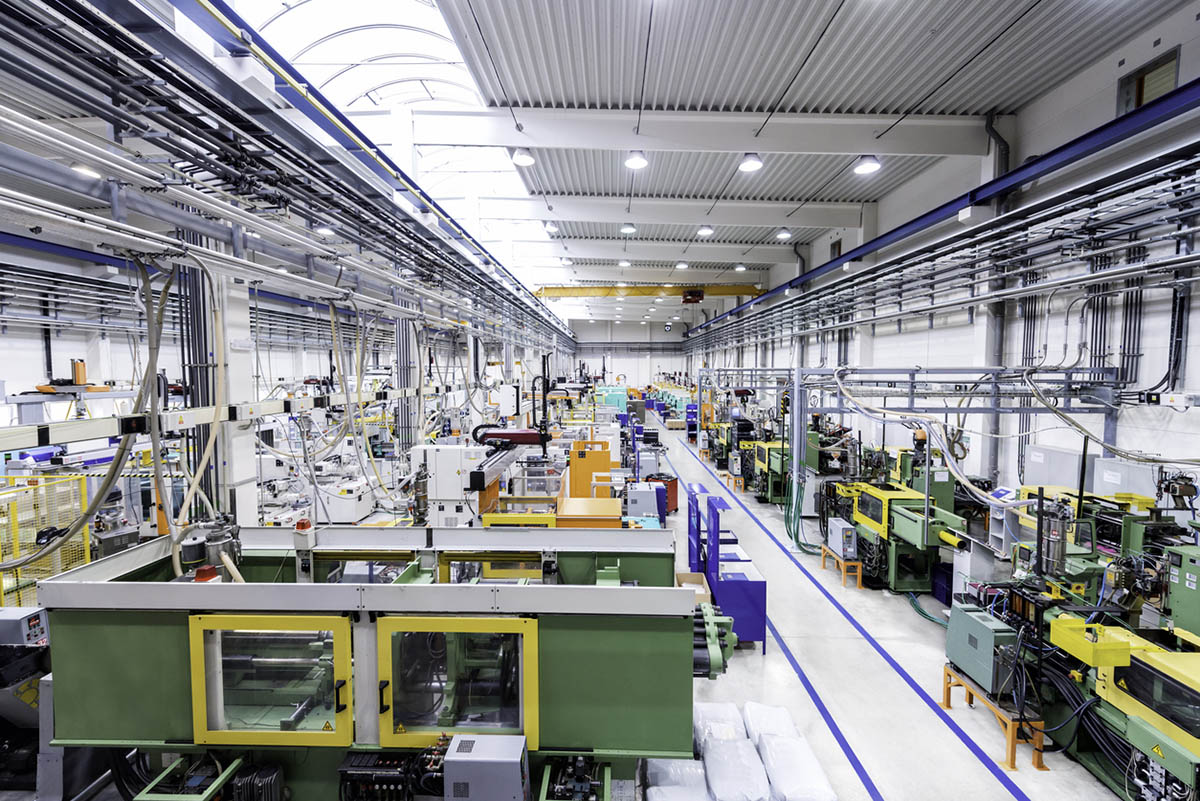
Scalable Manufacturing Solutions
We manufacture high-quality parts with processes like injection molding, CNC machining, die casting, and sheet metal fabrication. Whether you need 100 or 100,000 units, we adapt to your volume and timeline. Every production run meets rigorous quality and precision standards.
Assembly to Market-Ready
Beyond production, we support final assembly, labeling, kitting, and packaging services. Our ISO-certified workflows ensure consistent quality from component to finished product. Let us help you deliver a market-ready product—fully assembled and packed to spec.
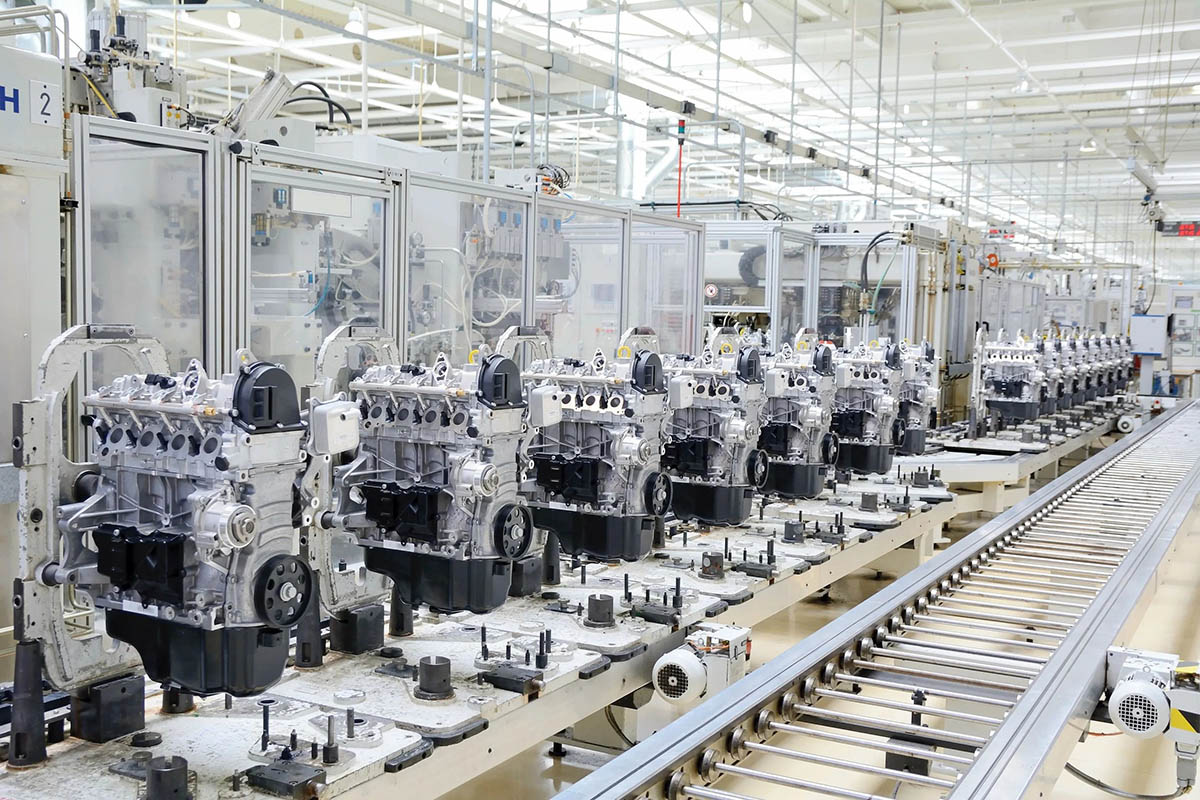
Our Services
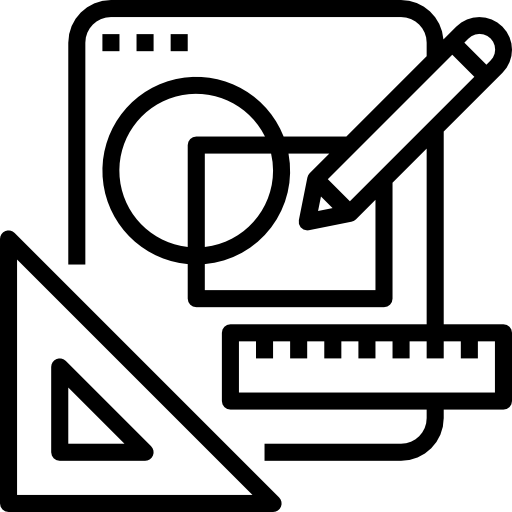
Industrial & Mechanical Design
Our experienced designers and engineers work closely with you to turn initial concepts into detailed, production-ready models. We focus on both aesthetics and functionality, ensuring your product is not only manufacturable but optimized for performance. From industrial equipment to consumer goods, we deliver precise and practical design solutions.
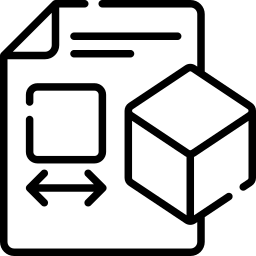
Prototyping
We provide fast and accurate prototyping using a variety of technologies including SLA, MJF, SLS, and CNC machining. Whether you need visual models for presentation or functional prototypes for testing, we help validate every detail before mass production. This critical stage minimizes costly revisions and speeds up product development.
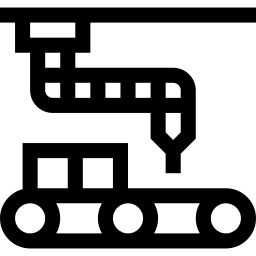
Production
Our in-house capabilities and trusted network of partners allow us to handle small to large production runs across multiple processes, including injection molding, CNC machining, die casting, and more. Every part we produce meets strict quality standards. We adapt our services to your volume, budget, and delivery goals.
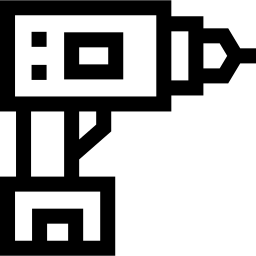
Assembly
We offer full product assembly services—from simple sub-assemblies to complex, multi-component builds. Our trained team ensures consistency, precision, and reliability at every stage. We also handle component integration, functional testing, and pre-shipment inspections as needed.
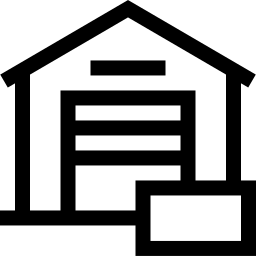
Warehousing
KingStar Mold offers secure warehousing options to store your finished products, components, or inventory in a well-organized environment. This helps you manage production cycles and order fulfillment more efficiently. We provide flexible storage plans to support businesses of all sizes.
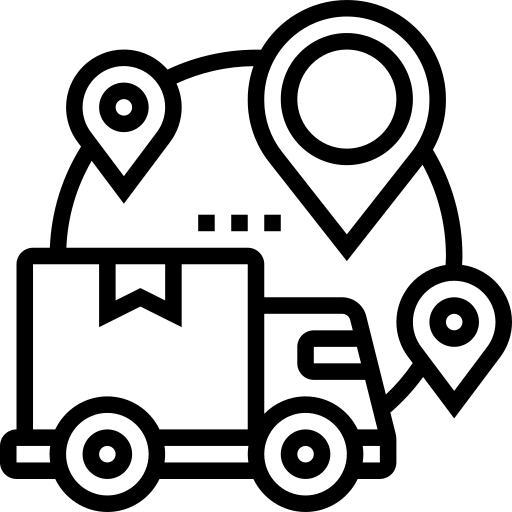
Logistics
We coordinate shipping and logistics to ensure your products are delivered on time and in perfect condition. From domestic freight to international exports, we handle customs, documentation, and carrier management. Our end-to-end service reduces your workload and simplifies distribution.
KingStar’s One-stop Manufacturing System
KingStar Mold’s one-stop manufacturing system simplifies your product journey from concept to production. We handle everything from design to prototyping and manufacturing, ensuring smooth transitions and quality at every stage. For a detailed guide, check out our post – How to Design and Manufacture a Product from Scratch.
Advantages of Partnering with KingStar
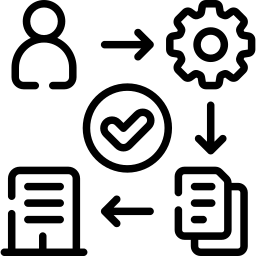
One-Stop Manufacturing Partner
From concept to final delivery, we handle every stage of your product journey under one roof. This integrated approach saves you time, reduces coordination hassle, and ensures quality at every step.

Engineering-Driven Precision
Our team of seasoned designers and engineers ensures every part is optimized for manufacturability and performance. We don’t just make products—we refine them for cost-efficiency, durability, and scalability.
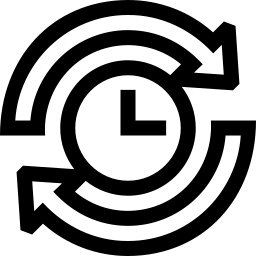
Flexible Volumes, Fast Turnarounds
Whether you need 10 prototypes or 10,000 units, we tailor production to your scale and schedule. With agile processes and responsive teams, we help you meet deadlines without compromising quality.
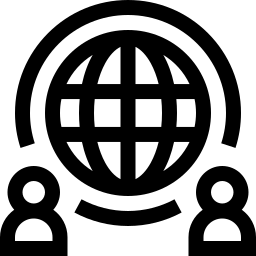
Global Reach with Local Support
Based in China and serving clients worldwide, we combine global manufacturing capabilities with personalized support. No matter where you are, our team is available 24/7 to keep your project moving forward.
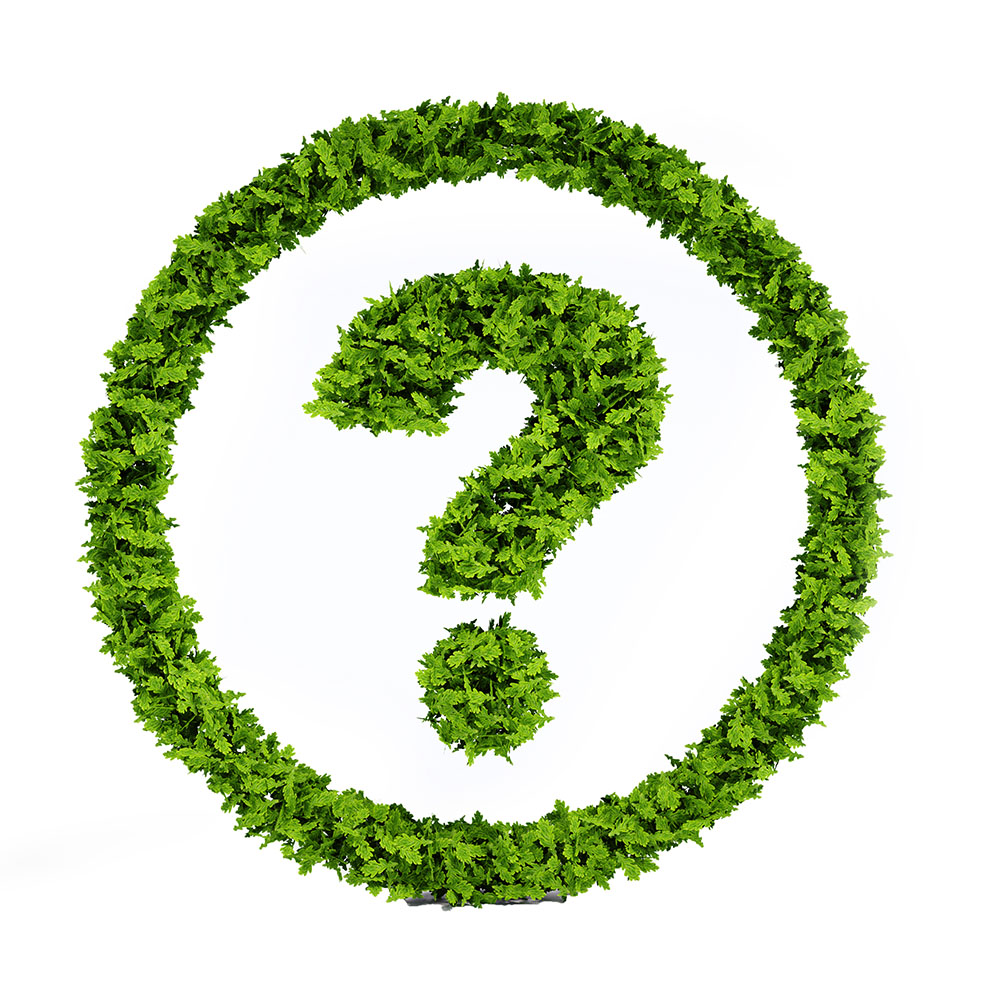
Frequently Asked Questions
Definitely. Iteration is a key part of product development. We encourage feedback during prototyping and can make adjustments to improve functionality, performance, or manufacturability before mass production begins.
Yes. We offer flexible logistics and warehousing support, especially for clients without their own distribution infrastructure. From final assembly to international shipping, we can help streamline the entire supply chain.
That’s perfectly fine. Many of our clients come to us with just a concept. Our design and engineering team at KingStar Mold will work with you step by step—refining your idea, building prototypes, and getting it production-ready.
Yes, having funding in place is important. Since product development can span several months and we operate on a work-for-hire basis, we typically require an upfront deposit to begin. This initial payment usually covers the first phase of work, so it’s best to ensure you’re financially prepared to support early-stage development.
We’re happy to sign a mutual Non-Disclosure Agreement (NDA) to protect confidential information on both sides. You can use ours, or if your company has its own NDA, we’re happy to review and sign it—just send it over by email.
Timelines vary based on the scope and depth of involvement you need from us. If we’re contributing to a specific phase—such as industrial design, mechanical engineering, or DFM support—the turnaround might be just a few weeks. However, when we manage the entire journey from concept to production-ready product, the process typically spans 3 to 12 months or more, depending on the product’s complexity and technical requirements.
Once we’ve refined your concept, completed engineering validation, and built functional prototypes, we prepare full documentation for production handoff. This allows manufacturers to quote accurately and confidently on full-scale manufacturing.
At KingStar Mold, we focus on creating smart, scalable solutions that not only function well but are cost-effective and appealing to end users. Our deliverables are production-ready and built with clear documentation to ensure smooth manufacturing transitions.