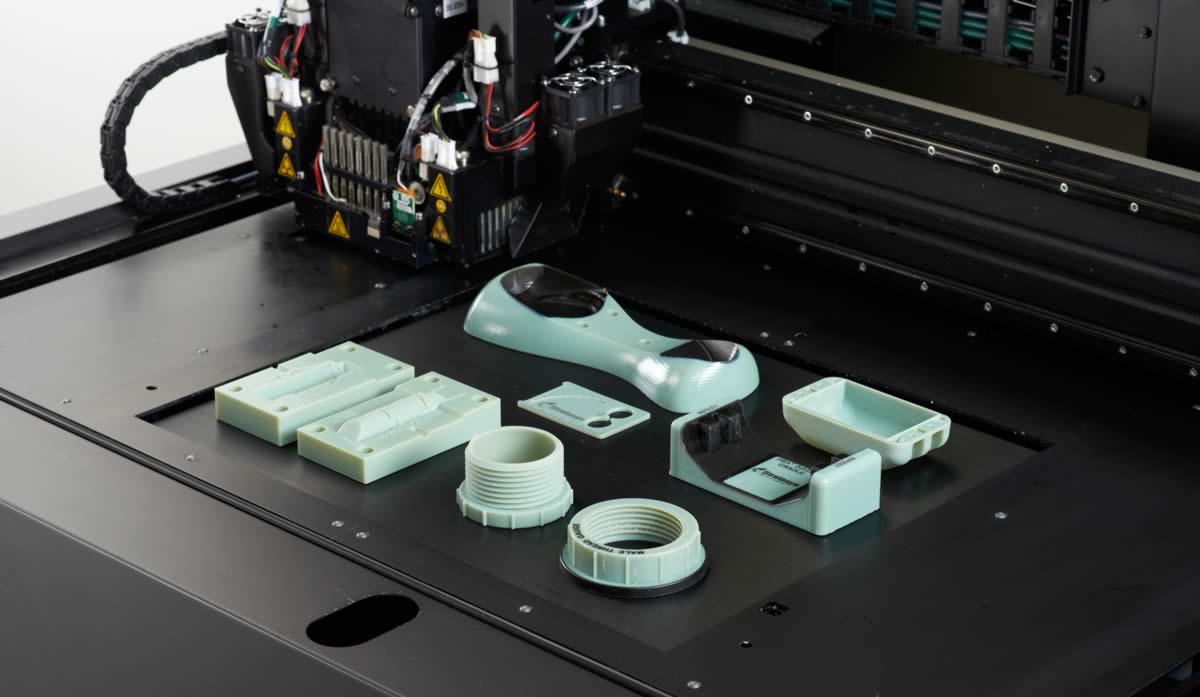
MJP 3D Printing Overview
Multi-Jet Printing (MJP) is an advanced additive manufacturing process that produces high-precision plastic and elastomer parts by jetting and curing liquid photopolymer layer by layer. This technology enables the creation of complex geometries, fine details, and smooth surface finishes that are challenging to achieve with traditional manufacturing methods. MJP is ideal for producing detailed prototypes, functional parts, and intricate models with exceptional accuracy and consistency, making it a preferred solution for industries requiring precision and aesthetic quality.
Common applications of MJP include:
Our MJP 3D Printing Capabilities
Specification | Details |
---|---|
Maximum Build Size | 294 x 211 x 144 mm (11.6″ x 8.3″ x 5.7″) |
Lead Time | 2-3 business days for most projects |
Resolution | ± 0.03 mm (0.0012″) for fine features |
Layer Thickness | 16-32 µm (0.0006″-0.0012″) per layer |
Surface Finish | Smooth, polished appearance with minimal post-processing |
Material Options | Rigid plastics, elastomers, and wax-like materials |
Prototyping Applications | High-detail concept models, intricate geometries, and visually aesthetic prototypes |
End-Use Applications | Low-volume, functional parts, detailed assemblies, and precision components |
Tolerances | ± 0.1-0.2% of part dimensions, depending on size |
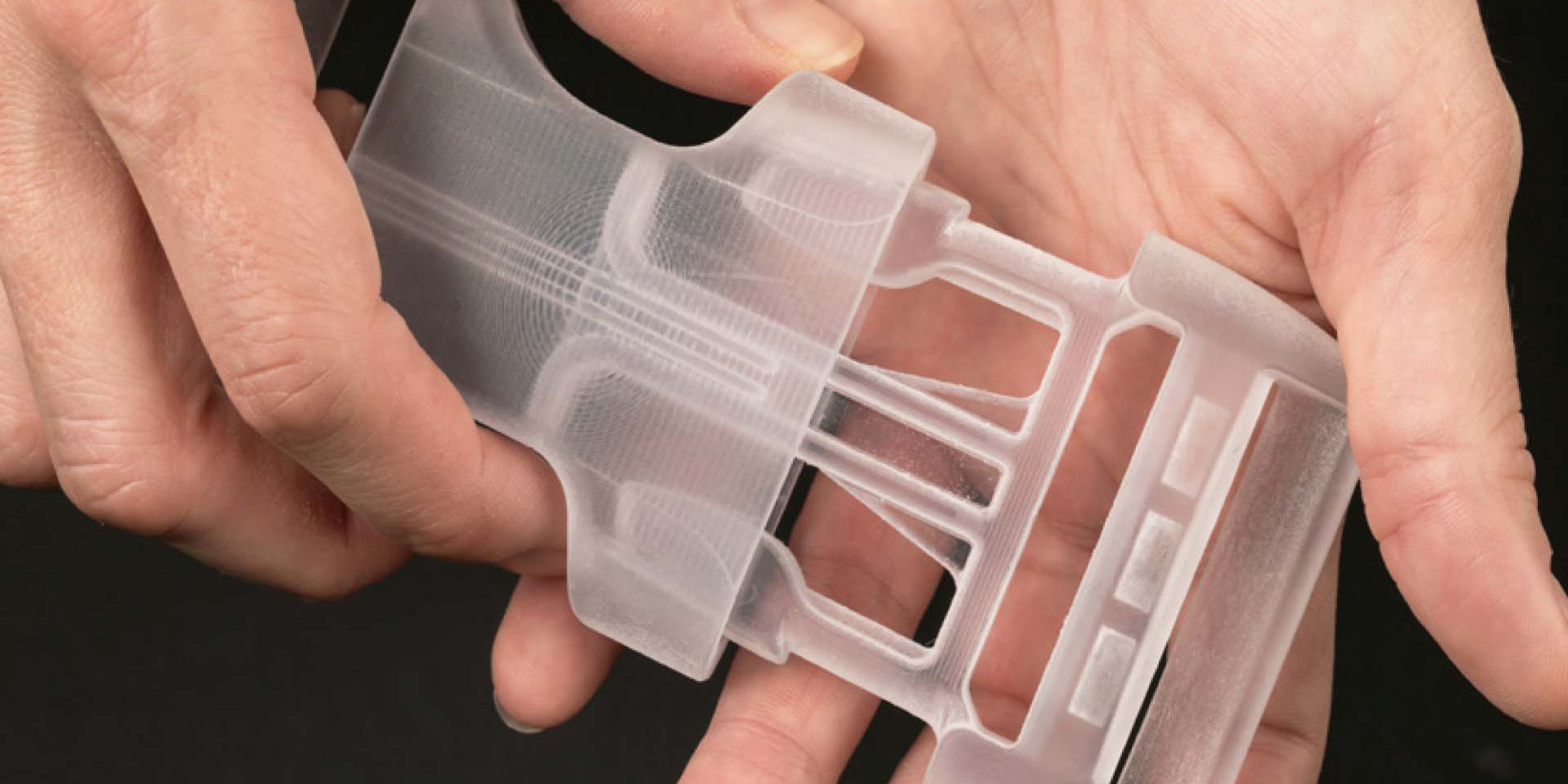
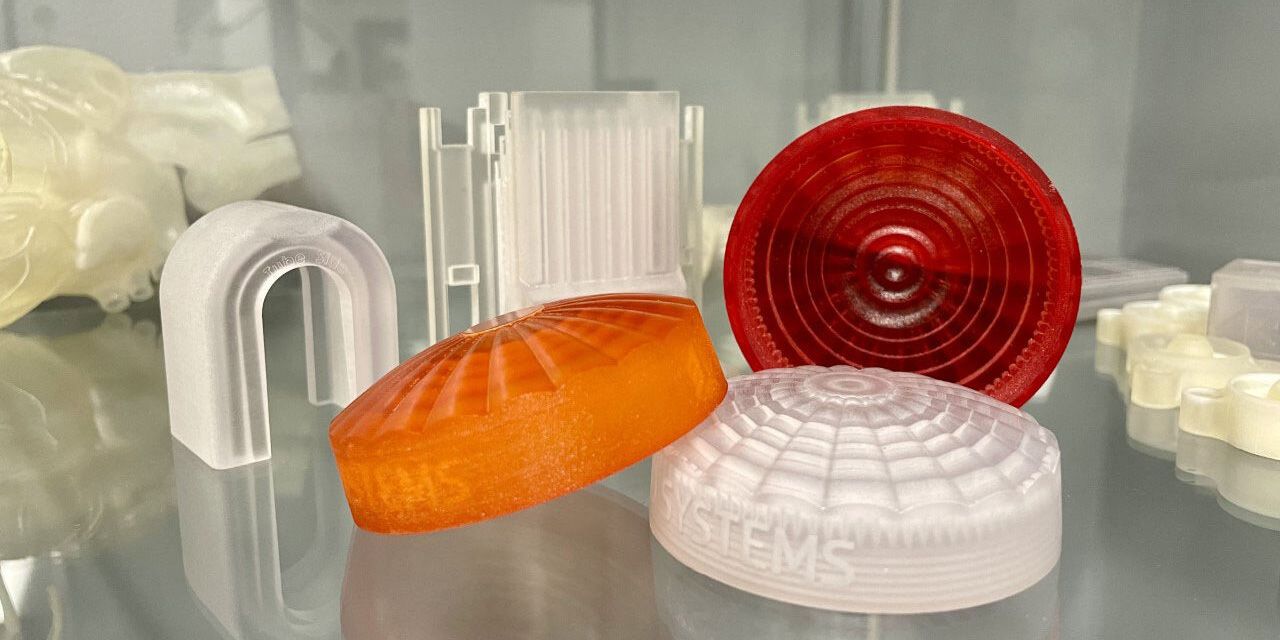
MJP Material Options
A high-performance engineered plastic designed for durability and stability, making it ideal for functional testing and rapid tooling applications. This material offers a true plastic look and feel, making it suitable for a wide range of prototyping and end-use parts. VisiJet Crystal is also USP Class VI certified, making it approved for select medical applications.
View Datasheet
Offers the look, feel, and performance of injection-molded ABS plastic, making it ideal for prototyping and product mockups. Suitable for end-use applications demanding exceptional toughness and high-temperature resistance, with a sleek, stunning white finish.
VisiJet® M3 Black is a standout material in the MJP family of professional printers, offering the look and feel of injection-molded plastic. Its black, durable finish makes it ideal for rigorous testing and functional use. This material is particularly suited for applications requiring snap-fit capabilities and enhanced strength.
VisiJet Techplast Plastic Material (gray) offers an economical solution for general modeling needs. It is also commonly used for sacrificial patterns in various direct casting applications, providing versatility and cost-effectiveness.
VisiJet Pearlstone dental material is crafted to produce precise, cost-effective dental models that closely resemble dental stone. Compatible with intraoral, impression, and plaster scanners, it’s perfect for creating models for crowns, bridges, orthodontic devices, implants, and partial dentures.
VisiJet Procast Plastic Material offers the industry’s best direct micro-casting performance, making it ideal for applications such as small and delicate medical instruments, devices, and other custom metal casting applications.
VisiJet Hi-Cast Material delivers exceptional resolution performance for high-end lost-wax casting, ideal for fine-detail items like jewelry, micro-medical devices, and electrical components. Exclusively used in the ProJet CPX 3500 3D printers, Hi-Cast sets the standard for feature definition, accuracy, and precision.
VisiJet Prowax Material provides 100% RealWax patterns for lost-wax casting in mid-sized and large foundry applications across various industries. These RealWax patterns can seamlessly replace traditional casting waxes in standard casting processes without the need for special modifications.
VisiJet Proplast Plastic Material (white/natural) offers an economical solution for general modeling needs. It is also commonly used for sacrificial patterns in various direct casting applications, providing a cost-effective and versatile option.
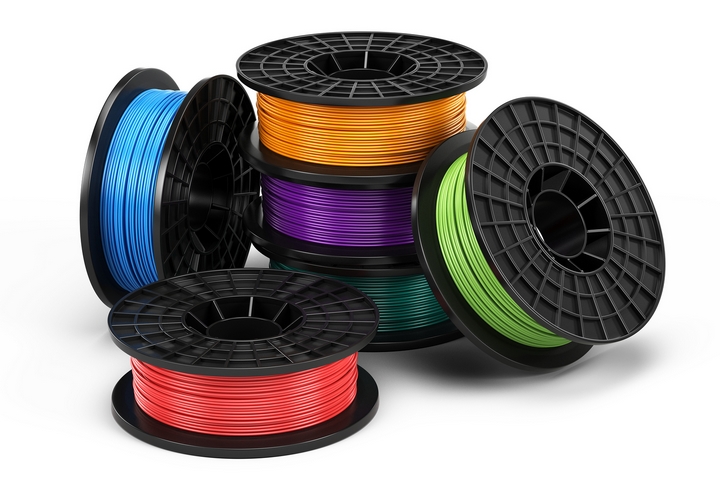
MJP Surface Finishing Options
Finishing Method | Applicable Materials | Color | Description |
---|---|---|---|
As Printed | – | Transparent | MJP parts are often left as printed, as they naturally have an aesthetic, smooth finish. |
Painting | All | Black, Pantone/RAL colors | Enhances aesthetics by adding color with a smooth, even coat. Ideal for visual prototypes. |
Dyeing | All | Black, Pantone/RAL colors | A fast, cost-effective method to color MJP parts, primarily for aesthetic improvement. |
Polishing | All | N/A | Refines surface texture, reducing layer lines for a smoother, shinier finish. |
Spray Painting | All | Custom colors | Adds a uniform, glossy finish with custom color options, improving visual appeal. |
Vapour Smoothing | Select plastics | N/A | Chemical process that smooths surfaces, enhancing gloss and reducing layer lines. |
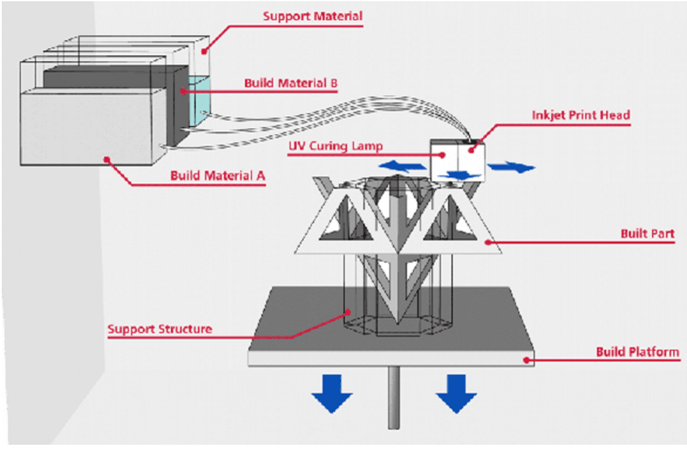
How Does MJP 3D Printing Work?
The MJP 3D printing process begins with CAD model preparation, where a 3D design is sliced into thin layers to create a digital blueprint. During material jetting, the printer deposits tiny droplets of liquid photopolymer material onto the build platform, while wax-based support material is simultaneously applied to reinforce overhangs and complex areas. Each layer is immediately cured with UV light, solidifying the material and gradually forming the part. Once printing is complete, the part is allowed to cool before being carefully removed from the platform, with excess wax support material still attached. The part then undergoes support removal in a heated bath or oven, melting away the wax and leaving behind a detailed, smooth-finished part. Finally, optional post-processing steps, such as polishing, painting, or dyeing, can be applied to enhance the part’s appearance and surface quality.
Why Use MJP 3D Printing?
Exceptional Precision and Detail
MJP delivers true-to-CAD accuracy with ultra-fine layer resolution, making it ideal for intricate geometries and complex parts. Its high dimensional stability ensures consistent, reliable results for both prototypes and end-use components.
Multi-Material Capability
MJP printers can simultaneously print multiple materials, including rigid plastics and elastomers. This allows for the creation of functional, multi-material assemblies in a single build.
Efficient Support Removal
The wax-based support material melts away easily in a heated bath, leaving no residue or damage. This enables the production of intricate, delicate features without labor-intensive cleanup.
Ideal for Functional Testing
MJP-printed parts offer high durability and stability, making them suitable for real-world testing. Their strength and accuracy make them reliable for validating mechanical performance.
Typical Applications for MJP 3D Printing
Medical & Healthcare
- Medical devices with biocompatibility, meeting USP Class VI and/or ISO 10993 standards
- Guides for surgery, dental models, and detailed anatomical replicas
- Tailored prosthetics and orthotic parts
Manufacturing & Tooling
- Jigs, fixtures, and assembly tools
- Patterns, dies, and molds for rapid tooling
- Low-volume production of functional parts
Casting & Jewelry
- Investment casting patterns for industrial applications
- Jewelry casting patterns with fine details
- Sacrificial patterns for direct metal casting
Prototyping & Design
- Concept modeling and design visualization
- Rapid design iteration for rigid plastic or elastomeric products
- Validation prototyping and testing
Marketing & Sales
- Communication, sales, and display models
- Realistic product mockups for presentations
- Visually appealing prototypes for client demonstrations
Engineering & Simulation
- Validation of assemblies, including snap-fits and multi-material designs
- Sealing applications for fluid flow analysis
- Testing functionality of plastic and elastomeric components
Consumer Products
- Functional testing and validation of product designs
- Over-molding for multi-material prototypes
- Small-batch production of custom consumer items
Education & Research
- Educational models for teaching and demonstrations
- Research prototypes for experimental testing
- Hands-on learning with accurate, detailed models
Comparison between Different 3D Printing Services
Feature | SLA | SLS | DMLS | MJP | FDM | SLM | MJF |
---|---|---|---|---|---|---|---|
Range of Material Options | ⭐⭐⭐⭐ | ⭐⭐⭐⭐⭐ | ⭐⭐⭐ | ⭐⭐⭐ | ⭐⭐⭐ | ⭐⭐⭐ | ⭐⭐⭐⭐ |
Geometry Complexity | ⭐⭐⭐ | ⭐⭐⭐⭐ | ⭐⭐⭐⭐ | ⭐⭐⭐⭐ | ⭐⭐ | ⭐⭐⭐⭐ | ⭐⭐⭐⭐ |
Batch Discount | ⭐⭐⭐ | ⭐⭐⭐⭐ | ⭐⭐ | ⭐⭐⭐ | ⭐⭐⭐⭐⭐ | ⭐⭐ | ⭐⭐⭐⭐ |
Scalability | ⭐⭐⭐ | ⭐⭐⭐⭐ | ⭐⭐ | ⭐⭐⭐ | ⭐⭐⭐⭐ | ⭐⭐ | ⭐⭐⭐⭐ |
Precision Tolerance | ⭐⭐⭐⭐ | ⭐⭐⭐ | ⭐⭐⭐⭐⭐ | ⭐⭐⭐⭐ | ⭐⭐ | ⭐⭐⭐⭐⭐ | ⭐⭐⭐⭐ |
Fine Details | ⭐⭐⭐⭐⭐ | ⭐⭐⭐ | ⭐⭐⭐⭐ | ⭐⭐⭐⭐ | ⭐⭐ | ⭐⭐⭐⭐ | ⭐⭐⭐⭐ |
Large Parts | ⭐⭐⭐ | ⭐⭐⭐⭐⭐ | ⭐⭐⭐ | ⭐⭐⭐ | ⭐⭐⭐⭐⭐ | ⭐⭐⭐ | ⭐⭐⭐⭐ |
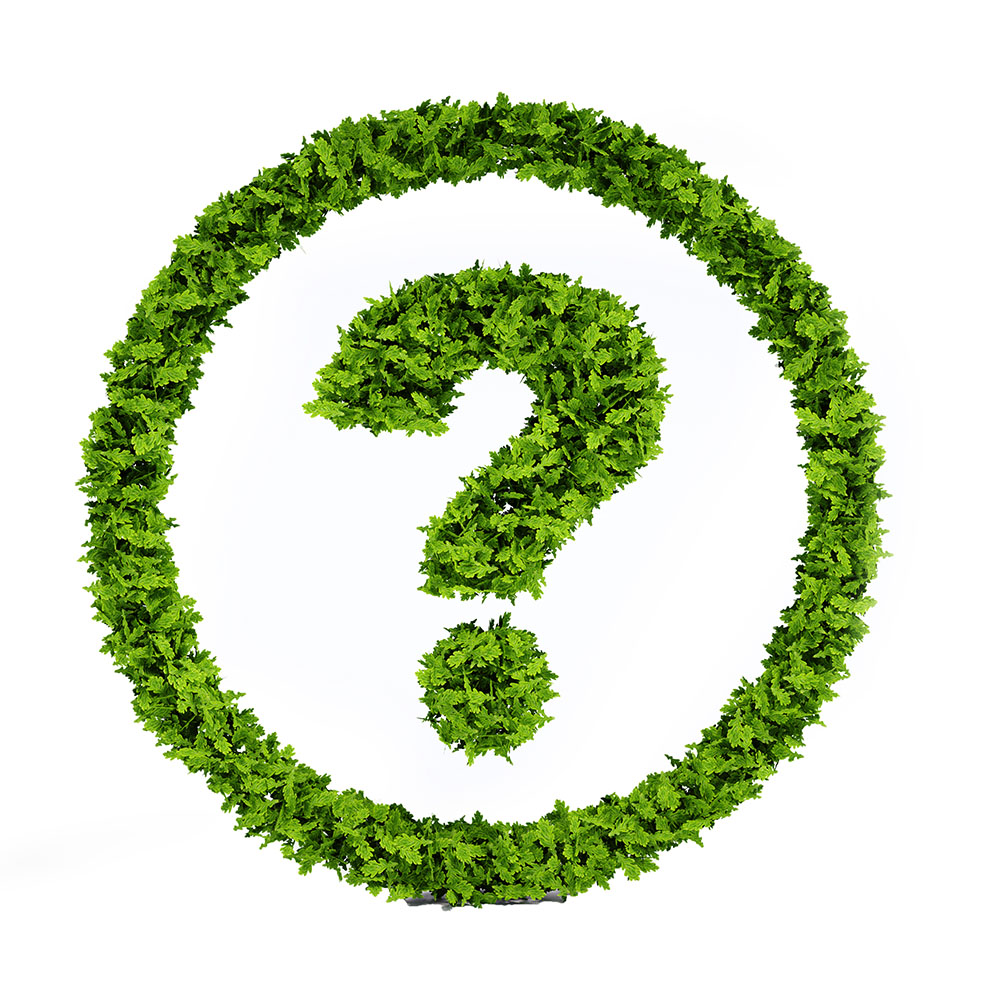
Yes, MJP 3D printing is ideal for producing custom medical devices, as it supports biocompatible materials that meet standards like USP Class VI and ISO 10993. It is widely used for creating custom implants, surgical tools, and dental prosthetics due to its high precision, ability to produce complex geometries, and biocompatibility, ensuring that the parts are safe for medical use.
The lead time for MJP 3D printing is typically 2-3 days, depending on the complexity and size of the parts. It is a fast prototyping technology that allows rapid turnaround, making it an ideal choice for businesses requiring quick iterations and testing of their designs.
No, MJP 3D printing is primarily designed for plastic, elastomeric, and composite materials. While it can produce high-precision parts for industries like automotive, aerospace, and healthcare, it is not suited for metal part production. For metal 3D printing, technologies like DMLS or SLM are recommended, as they are specifically designed to work with metal powders and achieve the high strength required for industrial applications.
MJP 3D printing excels in achieving high precision and fine details, often surpassing other technologies like FDM or SLA in terms of surface smoothness and dimensional accuracy. The jetting process, combined with precise UV curing, ensures that parts are produced with exceptional resolution, making it suitable for industries like aerospace and medical where exact tolerances and intricate geometries are required. However, it can be less precise for larger parts compared to DMLS or SLM, which are more suitable for metal-based applications requiring extreme accuracy.
MJP 3D printing supports a wide range of materials, including photopolymer resins, elastomers, composites, and waxes. These materials can be specifically formulated for different applications such as functional prototypes, investment casting patterns, and biocompatible medical devices. The process also allows for multi-material printing, making it ideal for complex geometries and functional parts that require different material properties. See detailed datasheets on the page above.