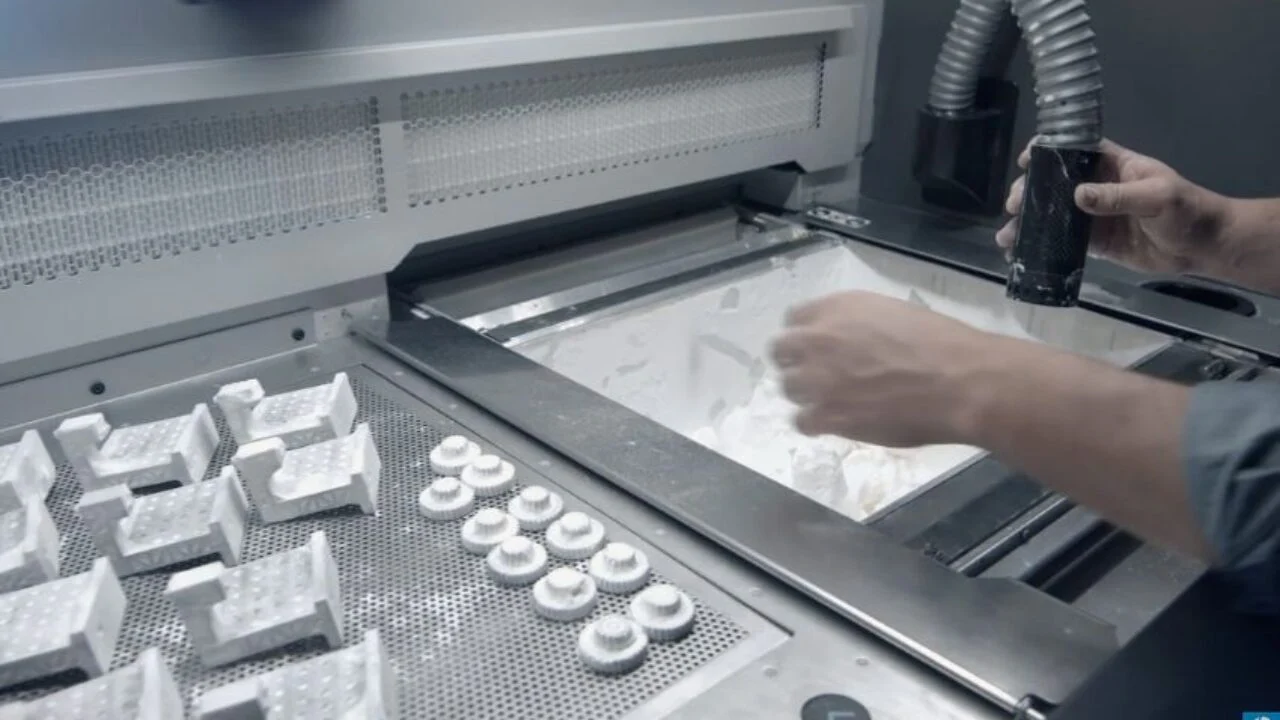
MJF (Multi Jet Fusion) 3D Printing Overview
MJF (Multi Jet Fusion) as one of the 3d printing services, is a cutting-edge additive manufacturing process that uses high-speed inkjet printing and fusing agents to build durable, high-precision parts layer by layer. The technology excels in producing functional prototypes and end-use parts with superior strength, fine detail, and consistent mechanical properties. MJF stands out for its fast production speed, cost-effectiveness, and ability to create complex geometries, making it a top choice for industries requiring rapid, high-quality part manufacturing.
Common applications of MJF include:
Our MJF 3D Printing Capabilities
Capability | Details |
---|---|
Maximum Build Size | 294 x 144 x 211 mm (11.6″ x 5.7″ x 8.3″) |
Lead Time | 3-4 days |
Resolution | ± 0.3 mm |
Prototyping Applications | High-fidelity, functional prototypes for testing and design validation |
End-Use Applications | Low to medium volume production of functional parts with durability and strength |
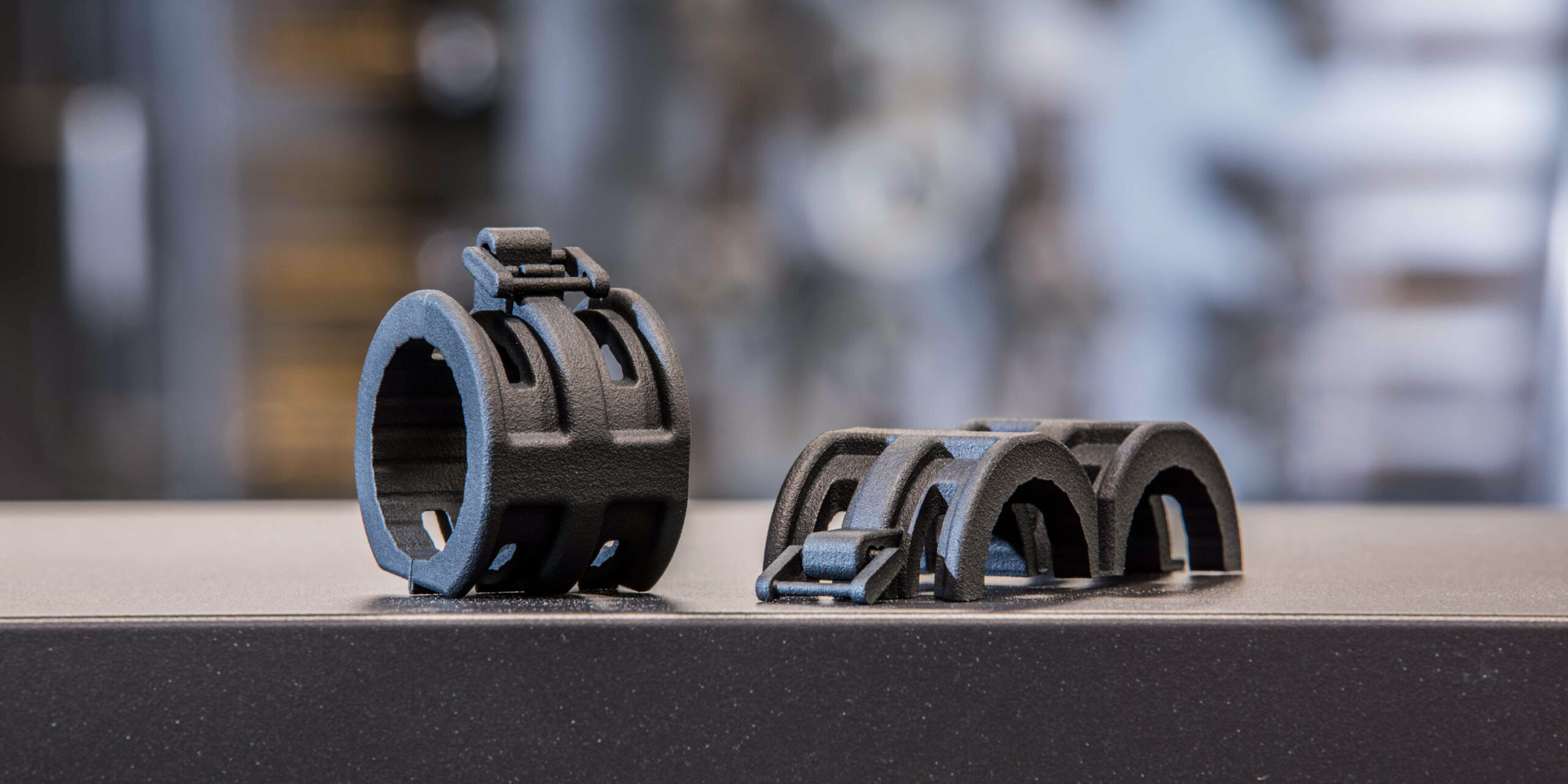
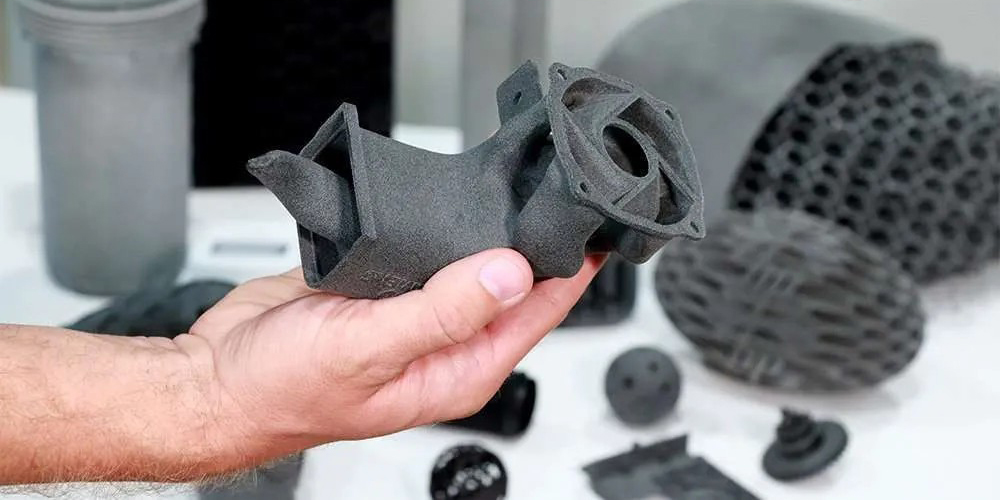
MJF Design Guidelines
Design Parameter | US | Metric |
---|---|---|
Maximum Part Size | 11.1 x 14.9 x 14.9 in | 284 x 380 x 380 mm |
Layer Thickness | 0.00315 in | 80 microns |
Minimum Feature Size | 0.020 in | 0.5 mm |
Wall Thickness | 0.020 in | 0.5 mm |
Tolerance | ± 0.012 in + 0.1% per inch | ± 0.30 mm + 0.1% per 25.4 mm |
Warpage Susceptibility | Parts >7 in prone to warping | Use ≥ 0.125 in thickness |
Clearance for Assemblies | 0.006 - 0.010 in | 0.15 - 0.25 mm |
Hole Diameter | ≥ 0.04 in | ≥ 1.0 mm |
Embossed & Engraved Details | ≥ 0.02 in depth | ≥ 0.5 mm depth |
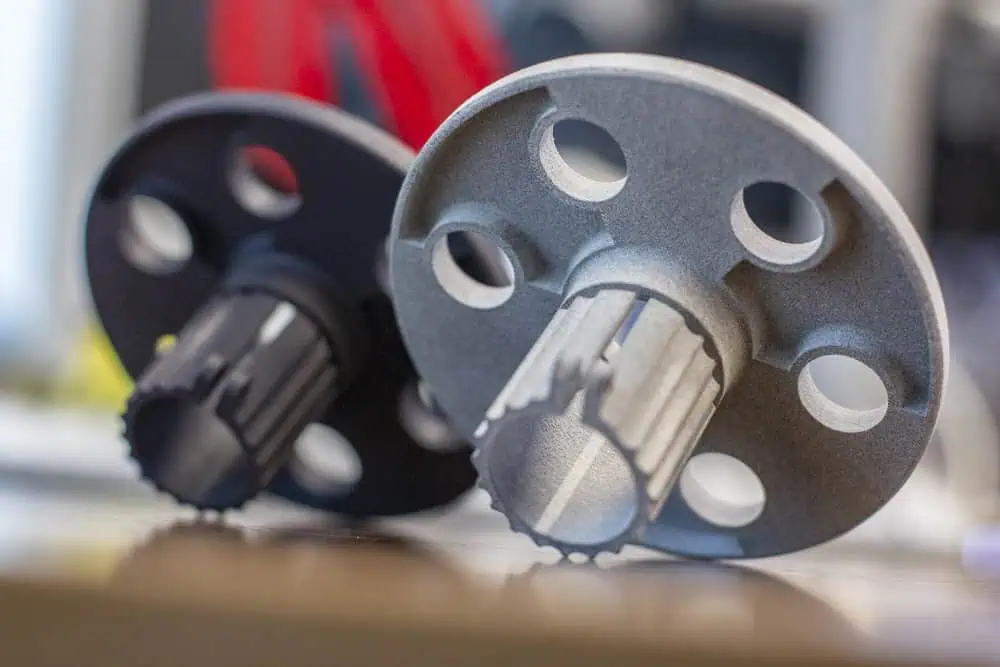
MJF Material Options
PA 12 Black is a high-tensile strength nylon known for its durability and smooth surface finish. The final parts are dyed black and offer slightly more isotropic mechanical properties compared to SLS materials. With a smaller minimum feature resolution of 0.02 in (versus 0.03 in for SLS), PA 12 Black is ideal for detailed designs and is the preferred choice for living hinges due to its flexibility and strength.
Key Benefits:
-
Near-isotropic mechanical properties for consistent performance
-
Cost-effective material with high tensile strength
-
Excellent for living hinges and fine-feature designs
PA 12 40% Glass-Filled Black is a nylon material reinforced with 40% glass fibers, enhancing its stiffness and thermal resistance. The final parts are dyed black and offer superior heat deflection of 347°F (66 psi), making it the second-best performer in heat resistance after PA 12 Mineral-Filled. This material is well-suited for applications requiring strength, stability, and heat tolerance.
Key Benefits:
-
Highly economical material for strong, durable parts
-
Excellent heat deflection, suitable for high-temperature applications
-
Enhanced stiffness and dimensional stability
Material | Color | Elongation | Tensile Modulus | Tensile Strength |
---|---|---|---|---|
PA 12 Black | Black | 8.5% | 276 ksi / 1,900 Mpa | 7.1 ksi / 49 Mpa |
Column 1 Value 2 | Black | 8.5% | 508 ksi / 3,500 Mpa | 4.35 ksi / 30 Mpa |
These figures are approximate and influenced by various factors, such as machine settings and process parameters. As a result, the information provided is not binding or certified. For critical performance requirements, independent lab testing of additive materials or final parts is recommended.
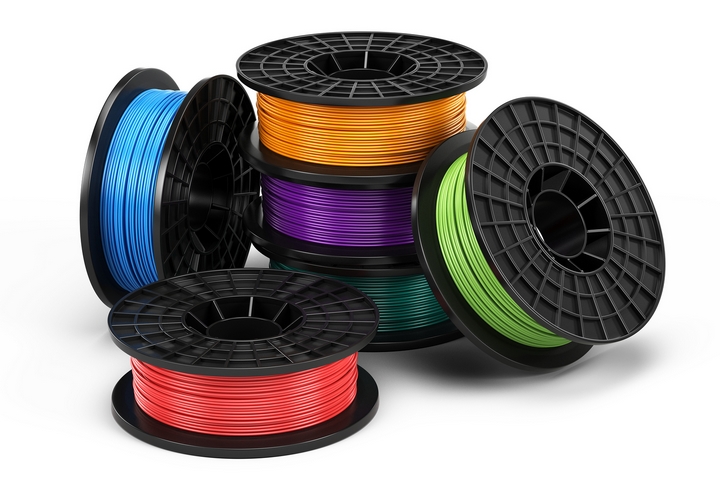
MJF Post-processing Options
Surface Finishing | Description |
---|---|
Standard | Bead blasting removes all excess powder, leaving a uniform texture. Parts are then dyed standard black. |
Vapor Smoothing | Reduces surface roughness from 250+ μin RA (as-printed) to 64 – 100 μin RA. Available for PA12 Black. |
Custom Finishing | Includes secondary options such as priming, tapping, and inserts for enhanced part functionality. |
Other post-processing services we provide are:
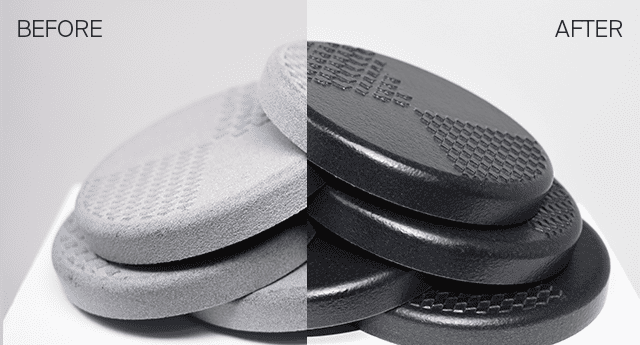
Vapour Smoothing
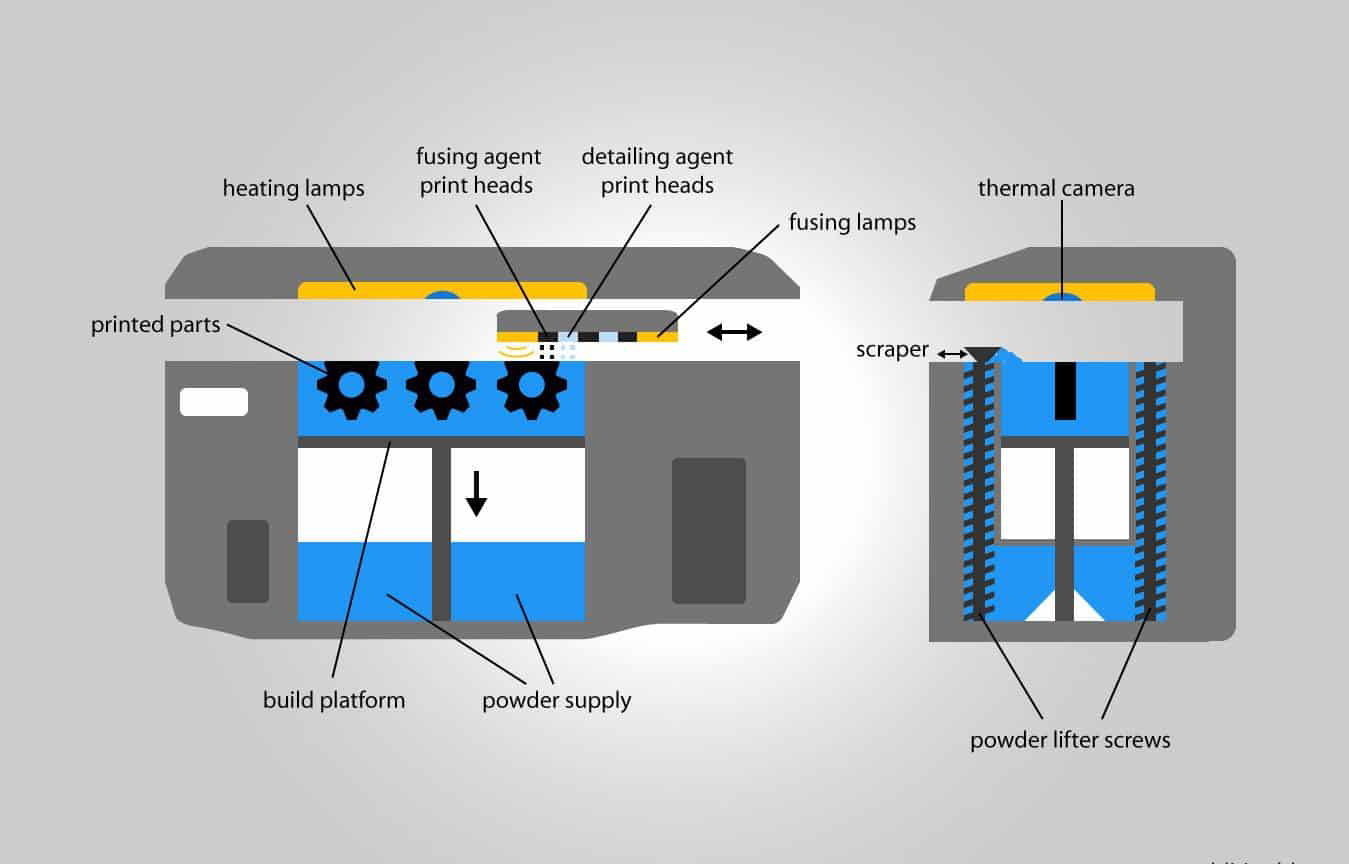
How Does MJF 3D Printing Work?
MJF (Multi Jet Fusion) 3D printing is an advanced additive manufacturing process that creates parts by selectively fusing powdered material using chemical agents and heat. The process starts with a thin layer of powder, typically nylon or similar polymers, being evenly spread across the build platform. Specialized printheads then deposit a fusing agent on areas intended to become solid and a detailing agent along the edges to sharpen boundaries and enhance precision.
Once the agents are applied, a powerful infrared heating element passes over the layer, causing the treated areas to fuse together while the untreated powder remains loose. This layering process continues, with new layers of powder being spread and selectively fused, gradually building the part.
MJF is known for its high precision and efficiency, enabling the production of complex geometries and fine details with consistent strength throughout the part. Once the build is complete, the part is extracted from the loose powder and can undergo post-processing such as cleaning, dyeing, smoothing, or coating to enhance its appearance and performance.
Why Use MJF 3D Printing?
High Precision and Accuracy
MJF 3D printing delivers parts with high precision and consistent accuracy. The process controls the fusing agent placement and material fusion with extreme detail, ensuring parts meet tight tolerances. This level of precision is ideal for industries that require reliable, functional prototypes or end-use components.
Versatility in Materials
MJF offers a wide range of material options, including standard polymers, elastomers, and composite materials. The flexibility in materials allows designers to choose the best option for their specific application, whether it’s flexibility, strength, or heat resistance. This versatility supports various industries, including automotive, medical, and consumer goods.
Fast Production Speed
MJF is known for its fast production time compared to other 3D printing methods. The printing process allows for multiple parts to be printed simultaneously, significantly reducing production time. This speed makes MJF a cost-effective solution for rapid prototyping and short-run production.
Strong Mechanical Properties
Parts produced with MJF are known for their excellent mechanical properties, including durability and strength. The process fuses material layers thoroughly, resulting in parts with isotropic properties that are consistent in all directions. These strong components are suitable for demanding applications that require long-lasting performance.
Typical Applications for MJP 3D Printing
Prototyping and Product Development
Functional Prototypes: Examples include mechanical test parts, housings, and brackets designed for product validation.
Rapid Prototypes: Concept models, form and fit prototypes, or parts to visualize design ideas quickly.
Design Iteration Parts: Parts used for multiple iterations in the product development process, such as prototypes for ergonomic testing.
Bridge and Short-Run Production
Small-Batch Production Parts: Low-volume production of custom gears, tools, or brackets for limited runs.
End-use Test Parts: Components produced for market testing or low-volume product introductions, such as custom enclosures or functional snap-fit parts.
Replacement Parts: Parts produced on-demand for replacement in ongoing production, such as machine components or tooling parts.
Durable End-Use Parts
Automotive Components: Custom connectors, housings, or brackets that are used in functional automotive parts like interior components or engine enclosures.
Medical Devices: Surgical guides, anatomical models, or functional prototypes for implants and dental appliances.
Consumer Goods: Custom housings for electronics, wearables, or accessories that require both functionality and durability.
Complex Geometries and Fine Details
Organic Geometries: Medical models or prosthetics designed with intricate, organic shapes like complex bone structures or custom orthodontic devices.
Parts with Fine Features: Small components with fine features, such as clips, brackets, or detailed electronics enclosures, requiring high resolution and surface finish.
Thin-Walled Parts: Lightweight structures for applications like drone parts, small housings, or intricate components where weight and strength are critical.
Case Studies
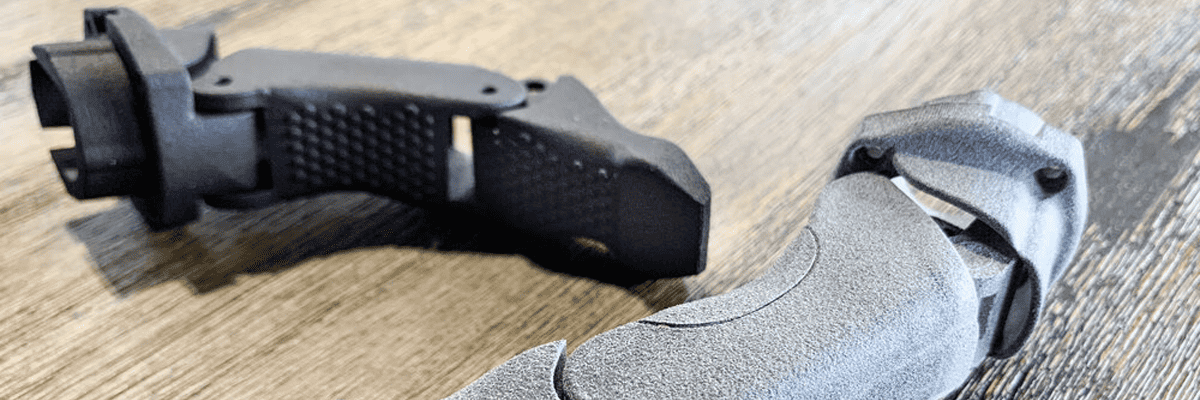
Project: Redesigned Assistive Robot Finger
Additive Technology Used: HP Multi Jet Fusion (MJF) with Nylon 12
Original Materials: 12 off-the-shelf hardware components and 5 injection-molded system parts
Redesigned Materials: A single print-in-place assembly, one small hardware access cover, and one steel spring
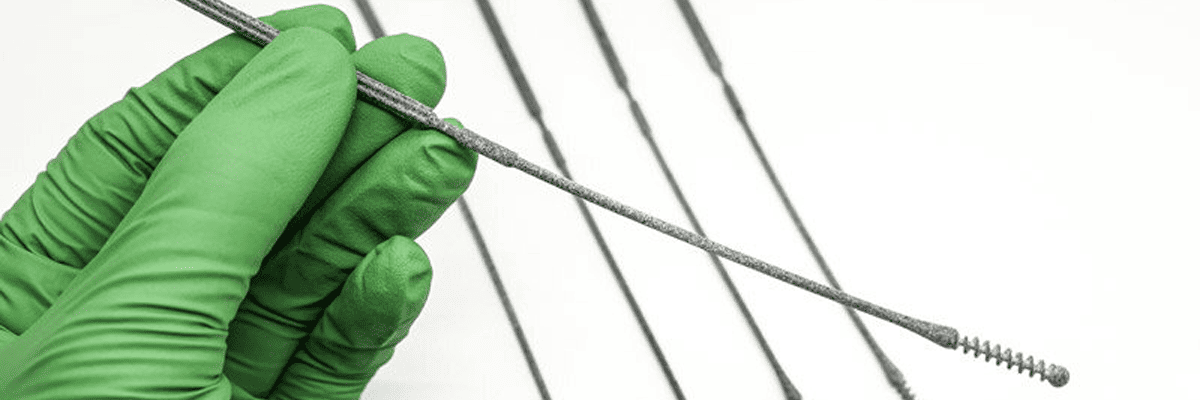
Project: FAST Spiral Nasopharyngeal Swab
Additive Technology Used: HP Multi Jet Fusion (MJF) with Nylon 12
Original Materials: Traditional injection-molded plastic swabs with multiple assembly steps
Redesigned Materials: A single one-piece MJF-printed swab with a spiral tip for improved sample collection efficiency
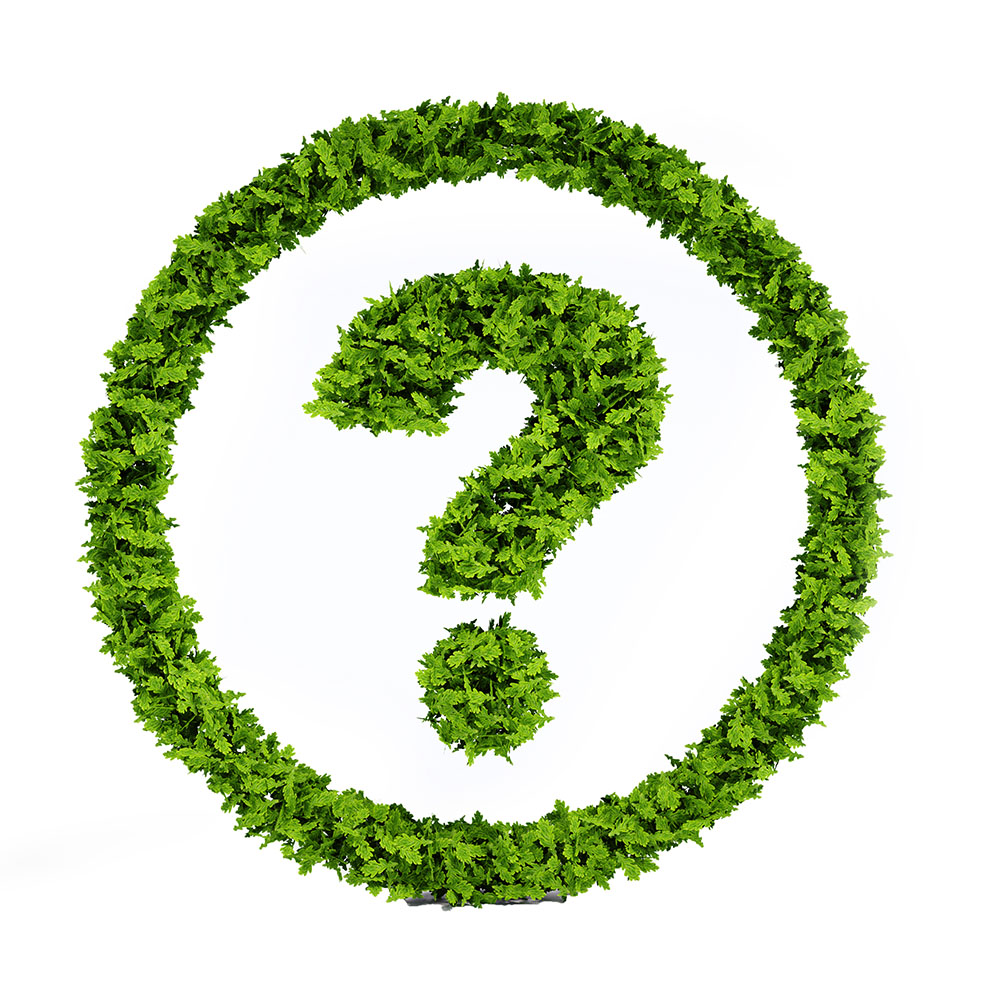
MJF parts can undergo various post-processing treatments, including bead blasting, dyeing, vapor smoothing, and painting. These processes enhance the parts’ appearance, surface quality, and performance.
MJF is widely used for functional prototypes, end-use parts, and low-volume production runs. Common applications include automotive components, medical devices, consumer products, and industrial tooling.
MJF primarily uses Nylon 12 (PA 12) and Nylon 12 Glass-Filled (PA 12 GF), offering excellent strength, flexibility, and durability. Other materials, such as TPU (thermoplastic polyurethane), are also used for producing flexible, rubber-like parts.