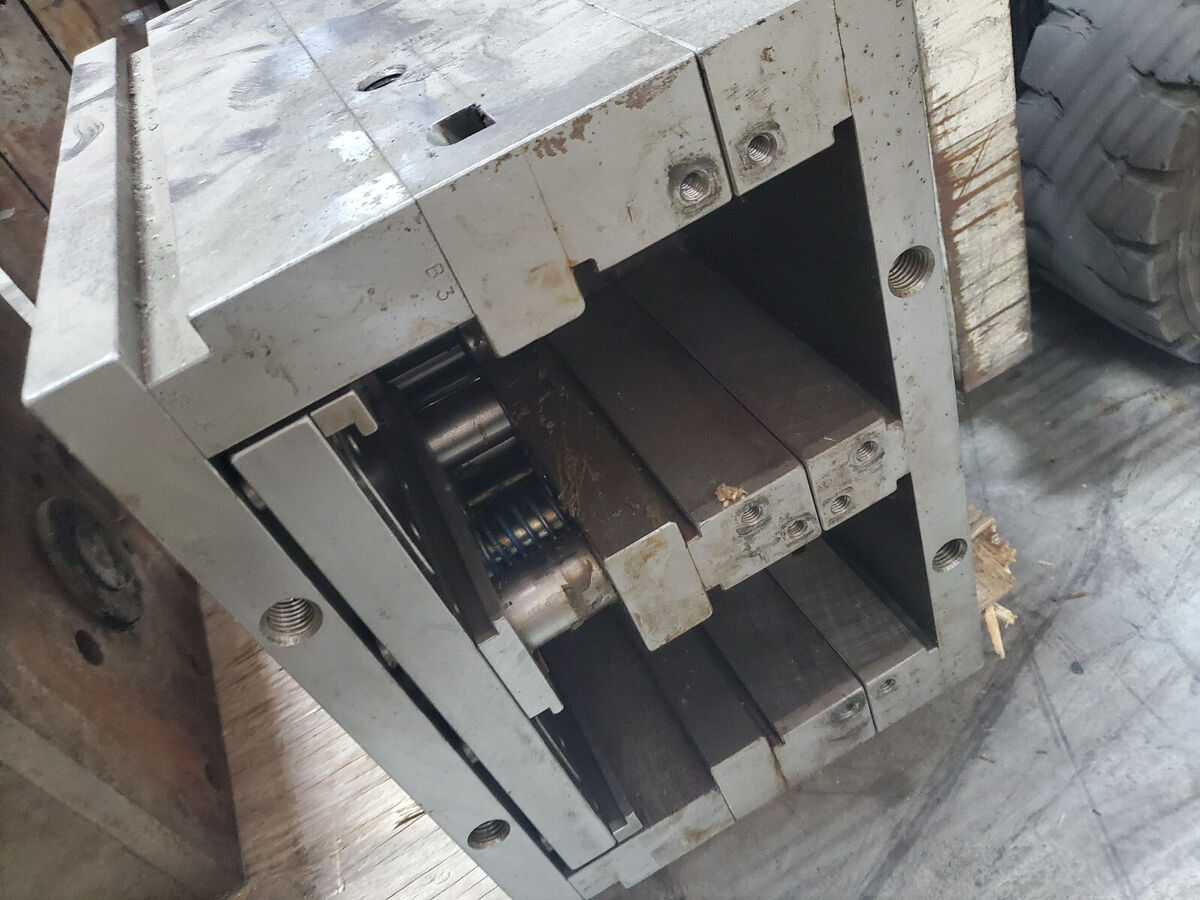
What is MUD Injection Mold?
Our MUD Injection Mold Types
The Master Unit Die Quick-Change (MUD) System includes a straightforward frame designed to hold various inserts. There are four types of frames, tailored to the part size and production volume:
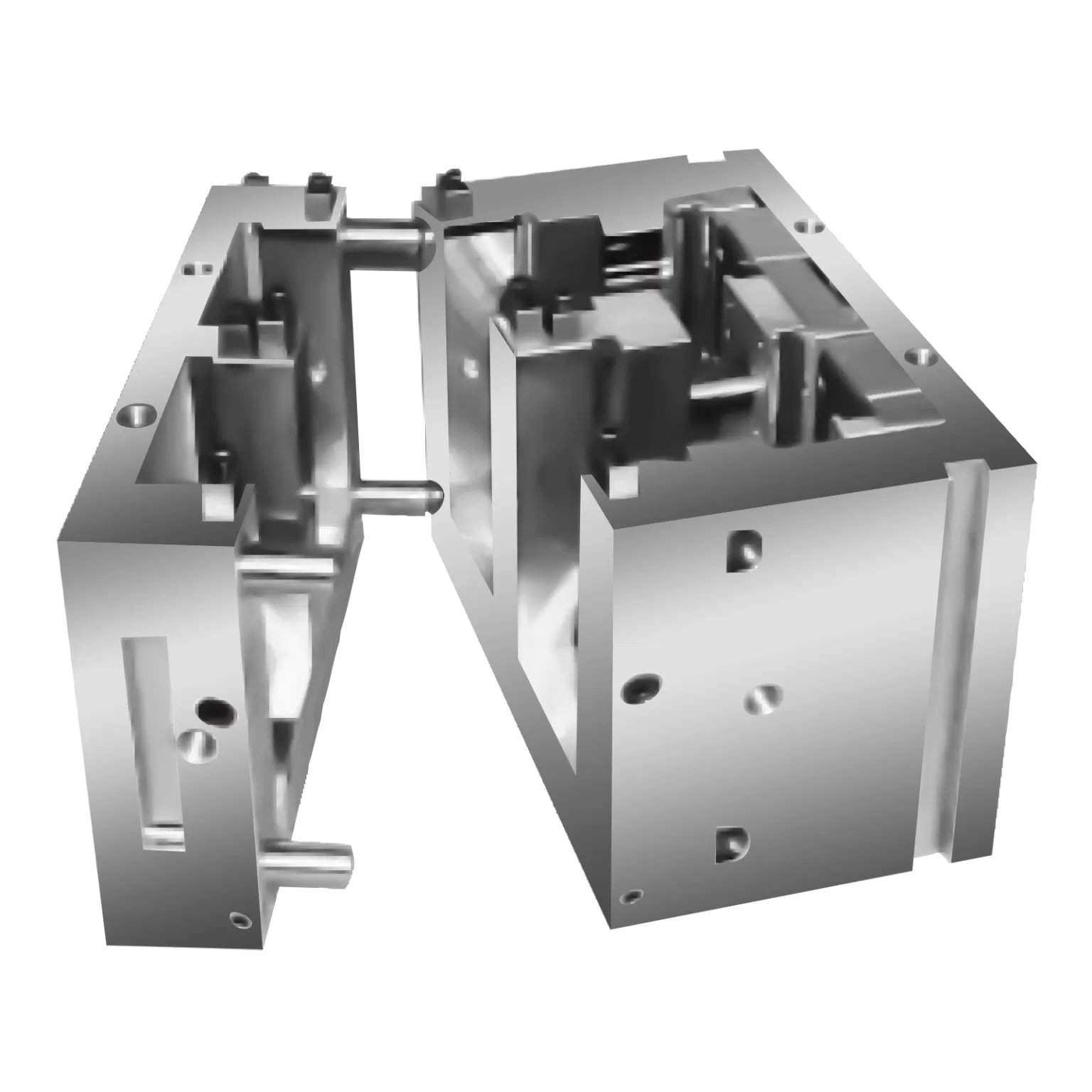
E-Frame
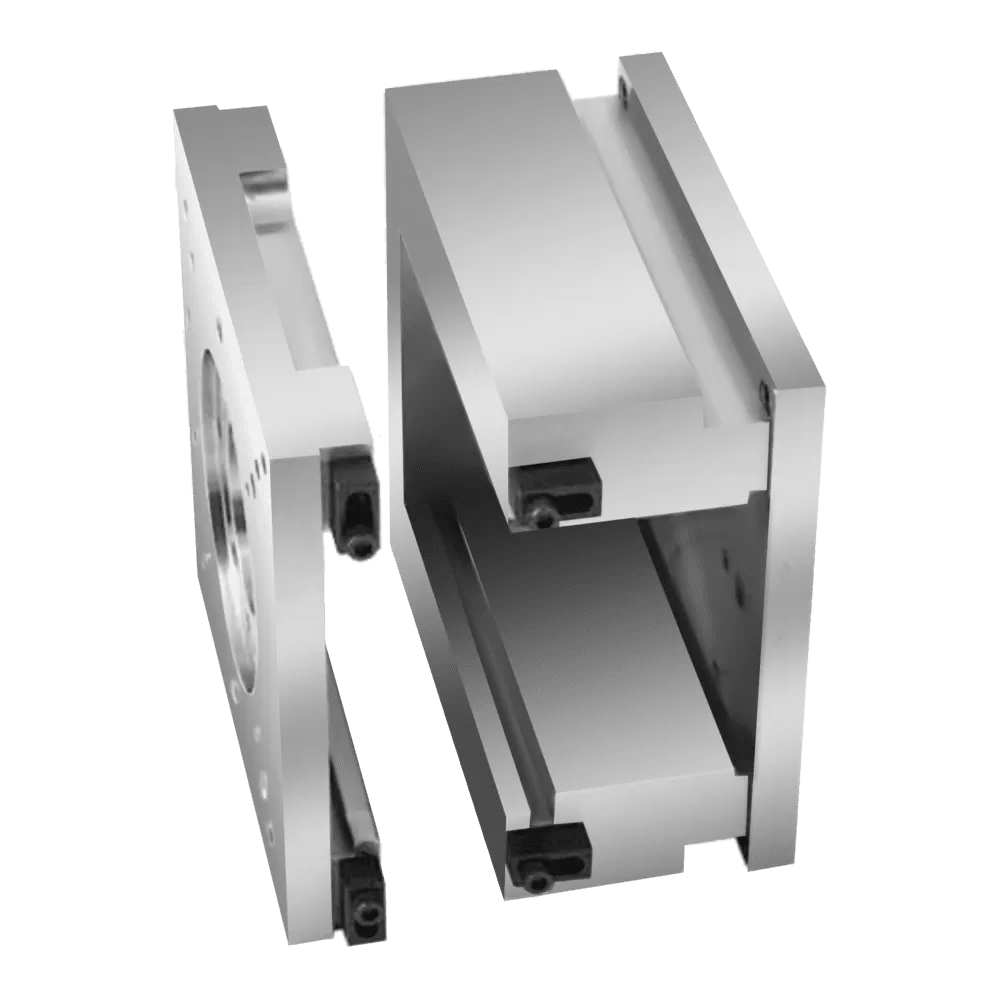
U-Frame
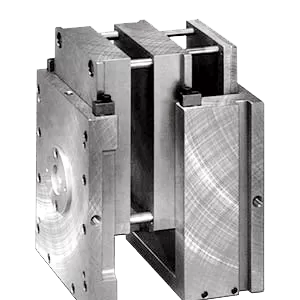
T-Frame
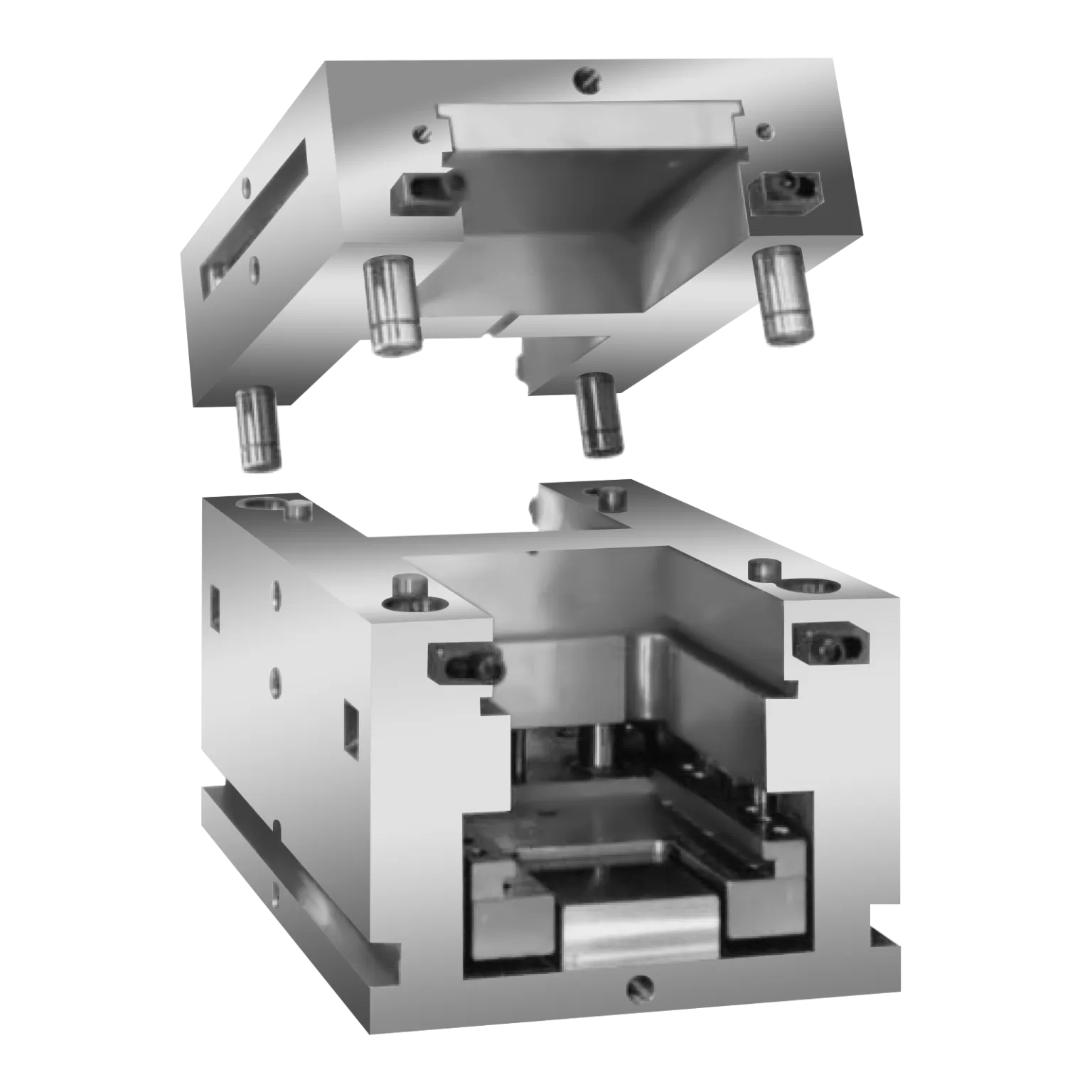
H-Frame
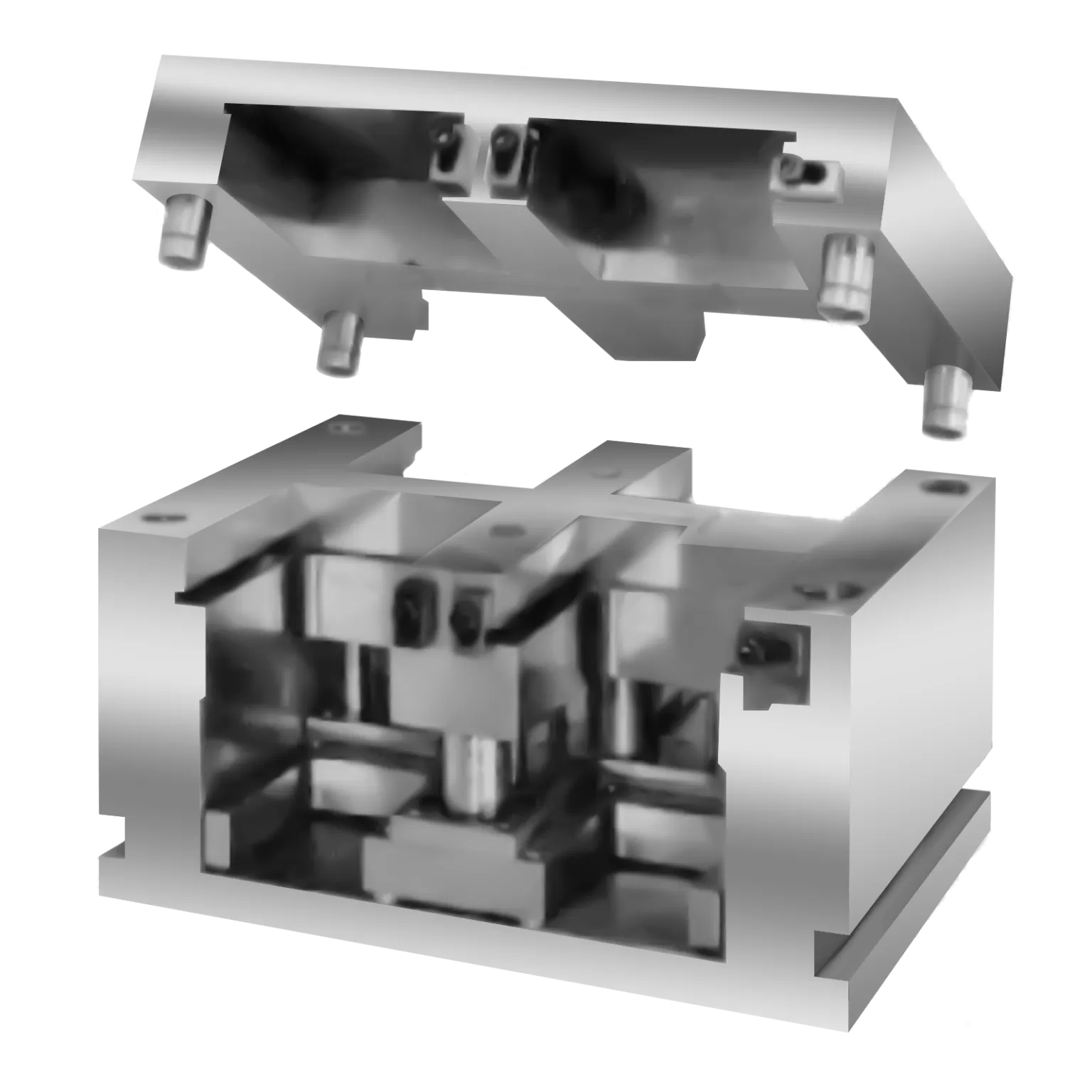
Double H-Frame
MUD Mold Materials
Why Choose MUD Injection Molds
Details of MUD Frame Types
U-Frame & T-Frame
Features & Benefits
Specifications
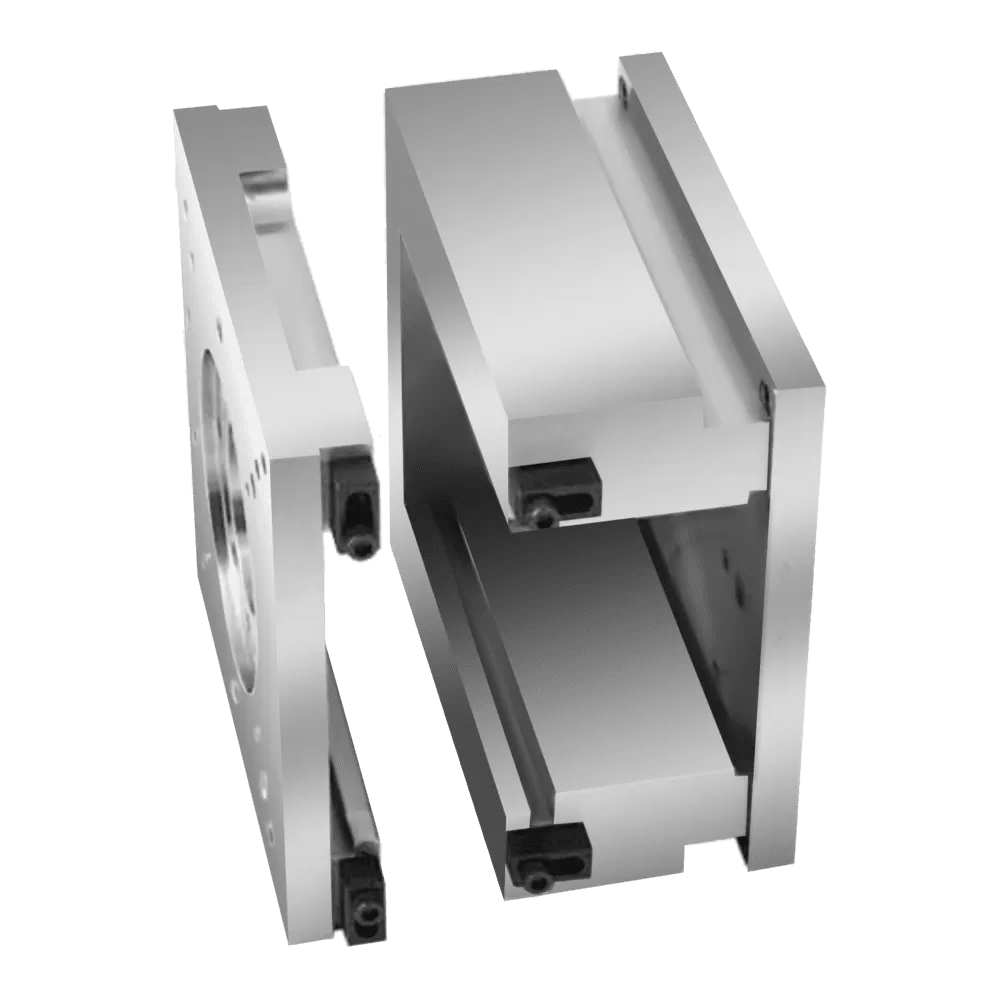
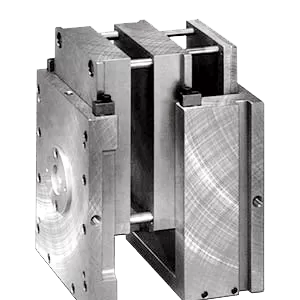
H-Frame & Double H-Frame
H-Frame: Features & Benefits
Double H-Frame: Features & Benefits
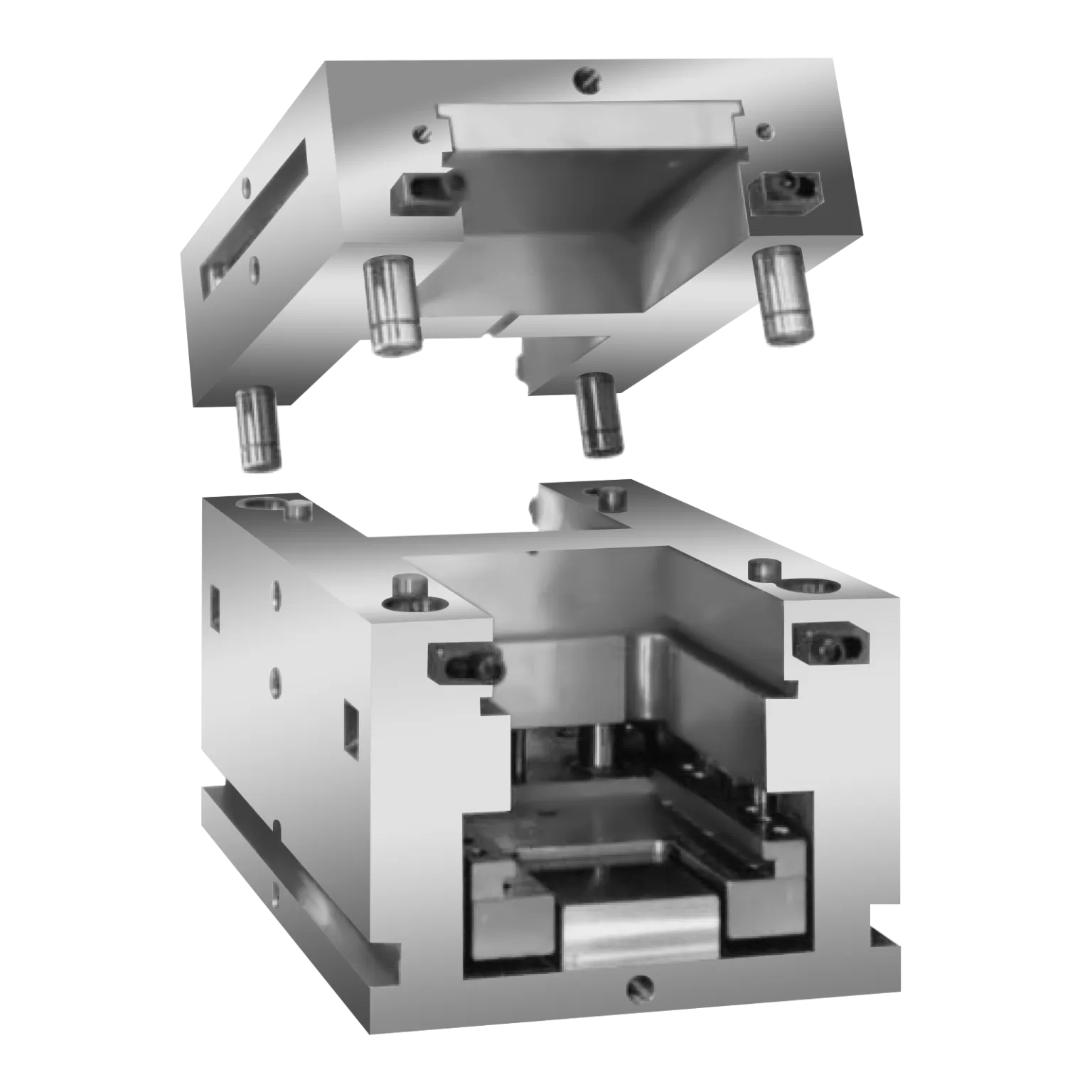
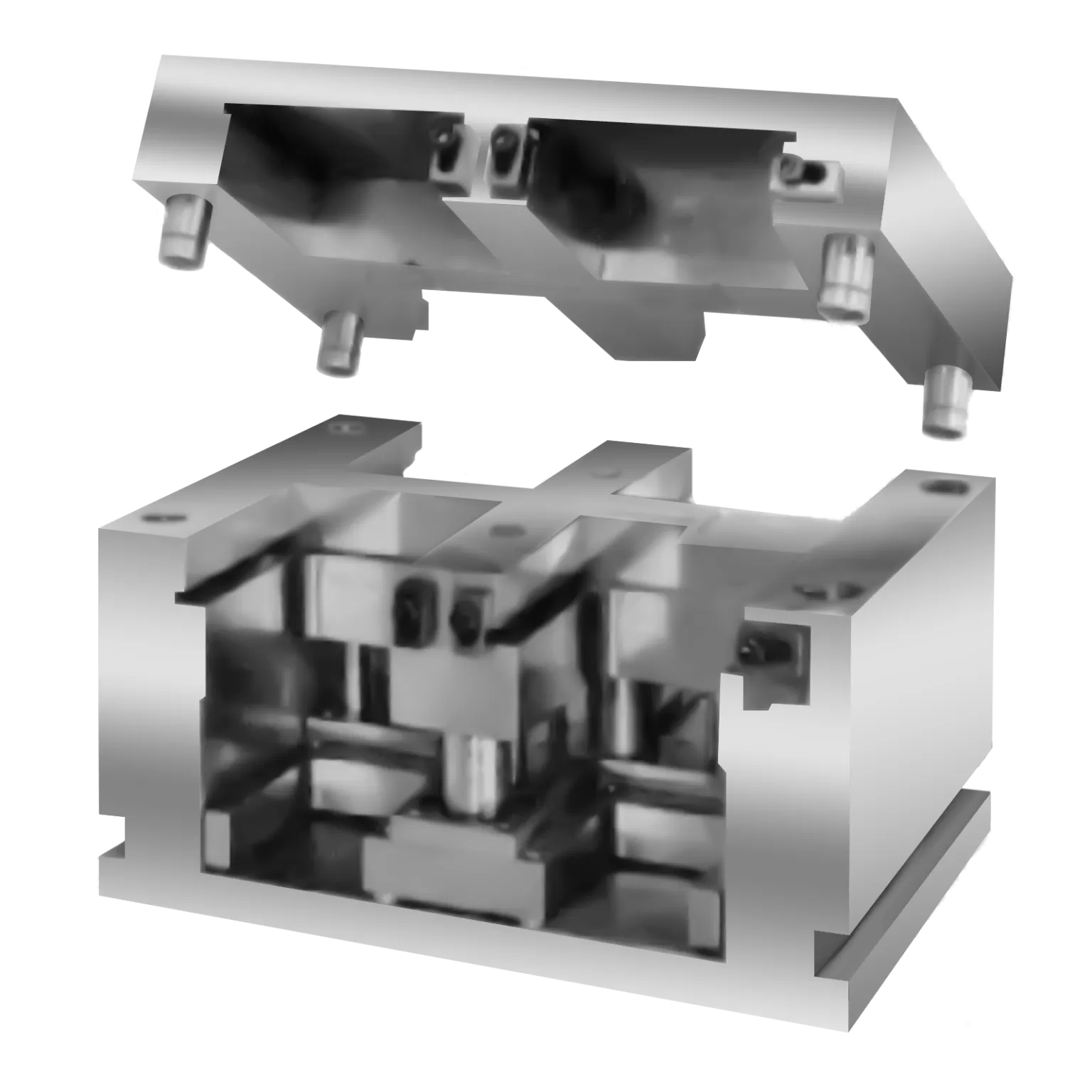
E-Frame
Features & Benefits
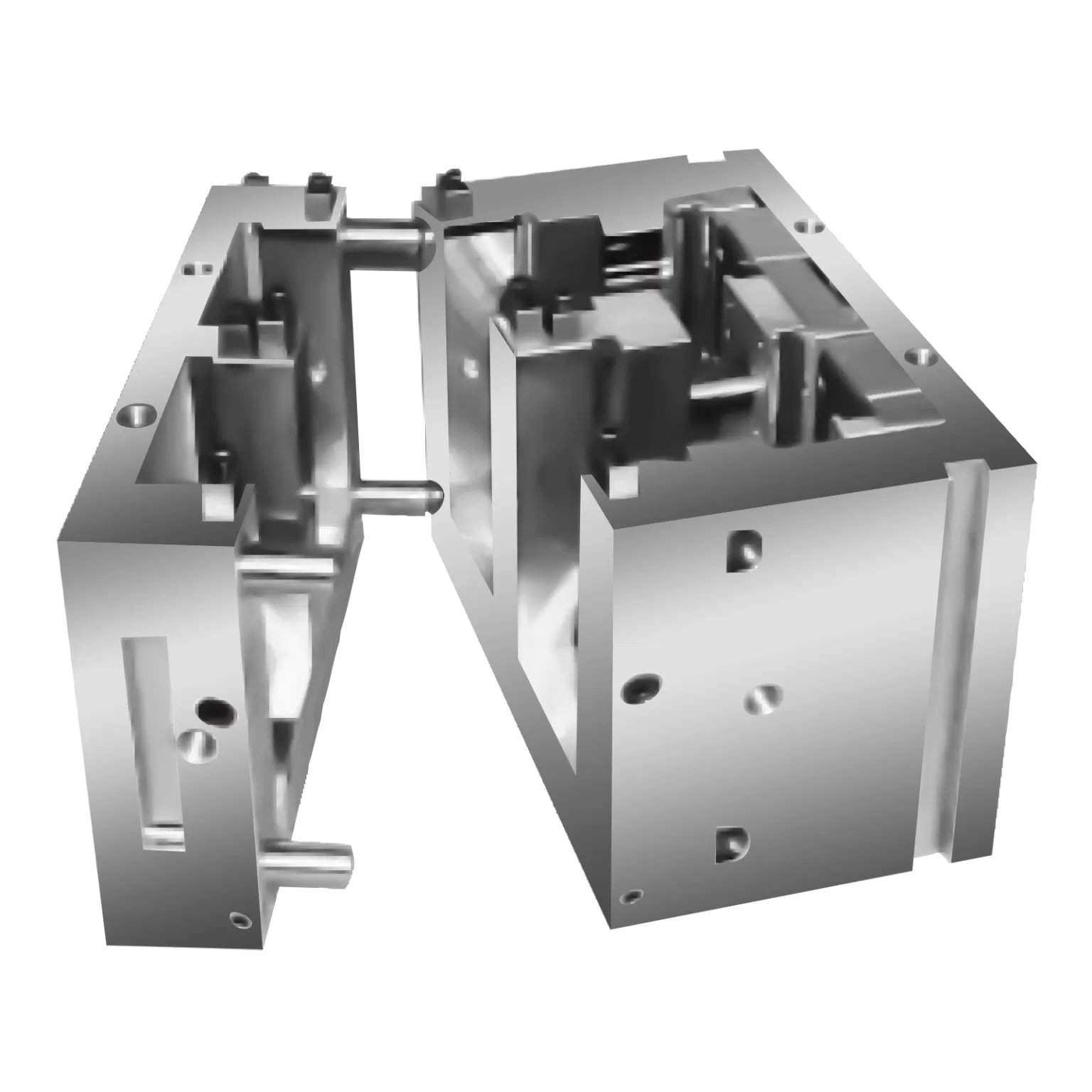
MUD Mold Insert Types
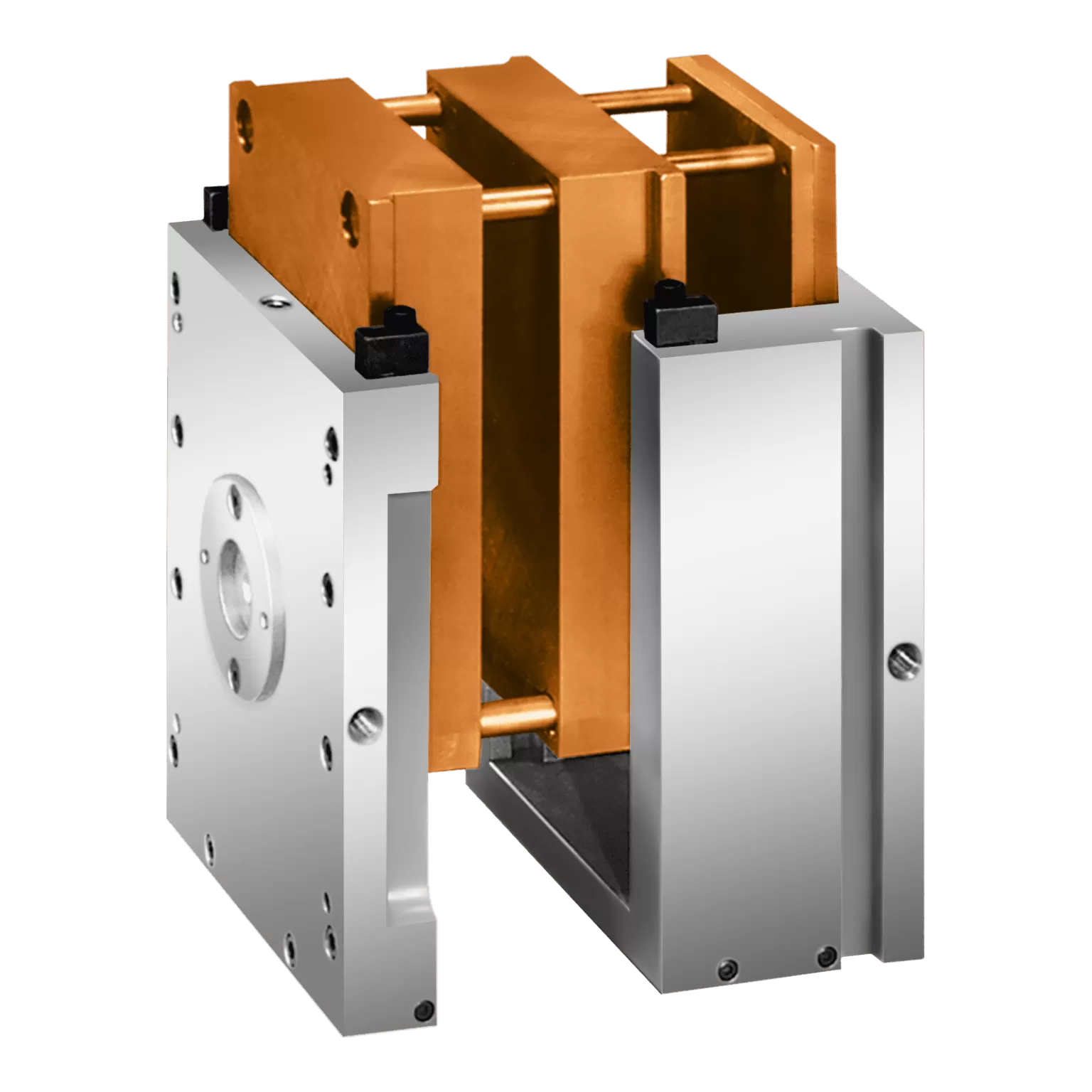
Standard Insert
Standard insert molds offer a budget-friendly solution when additional mold width isn’t required. They come in both solid and laminated styles and can be configured as three-plate or four-plate systems, depending on the application.
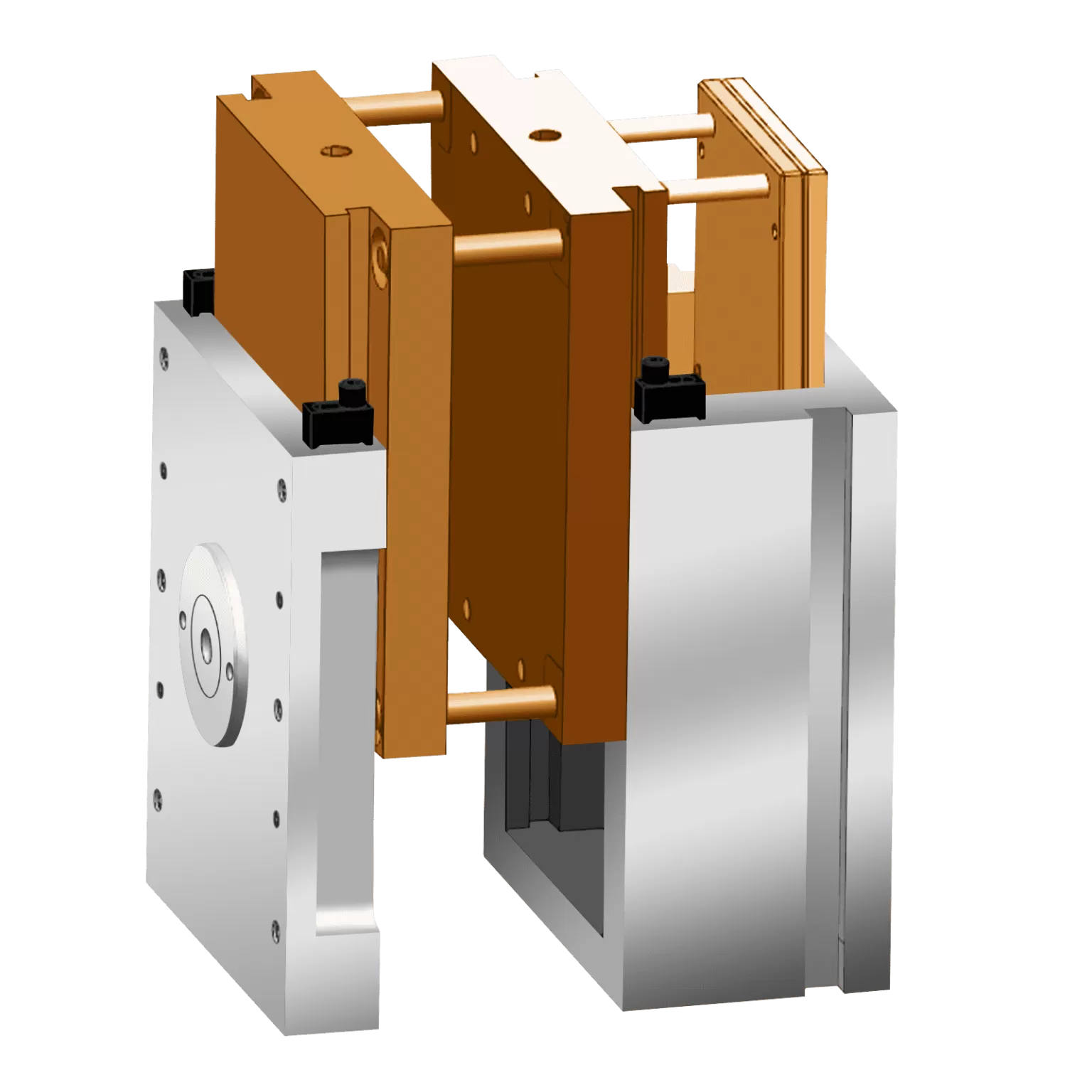
T-style Insert
T-style insert molds are ideal for maximizing cavity space within the frame. Typically available in laminated configurations with three- or four-plate designs, smaller versions can also be produced in either solid or laminated form for added flexibility.
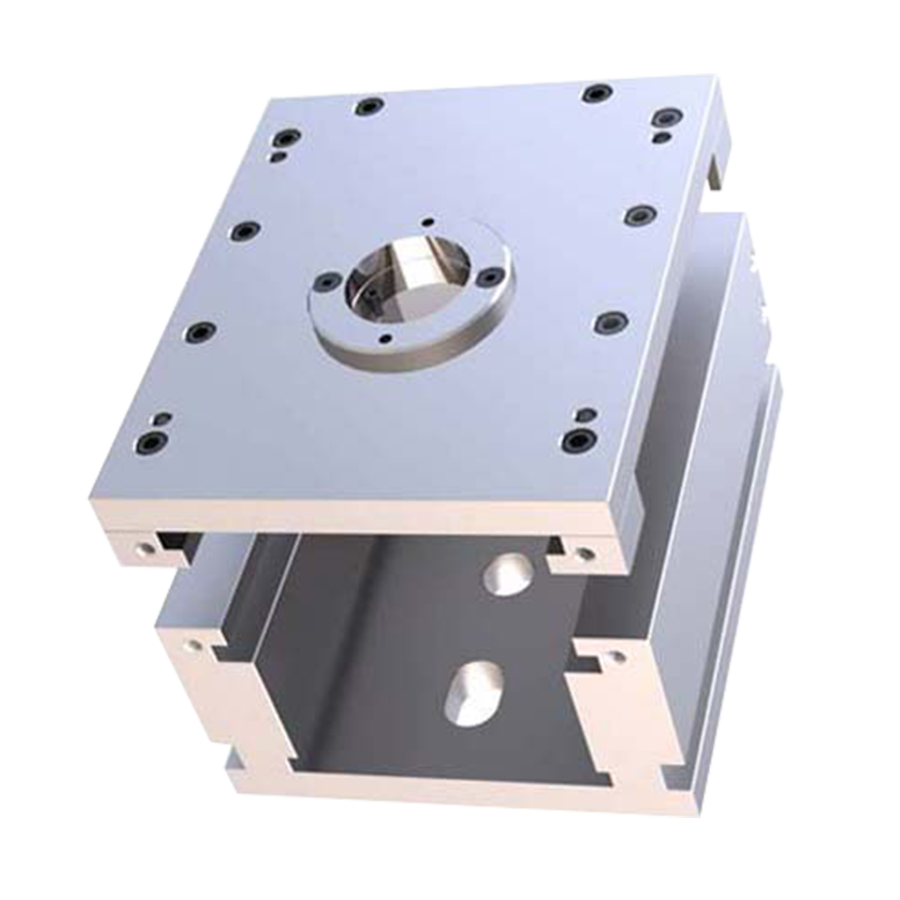
U-style Insert
U-style insert molds are designed for front-loading applications and are commonly used in molding systems where fast changeovers are critical. These molds allow easy access for maintenance and quick insert swaps, making them a practical option for high-mix, low-volume production environments.
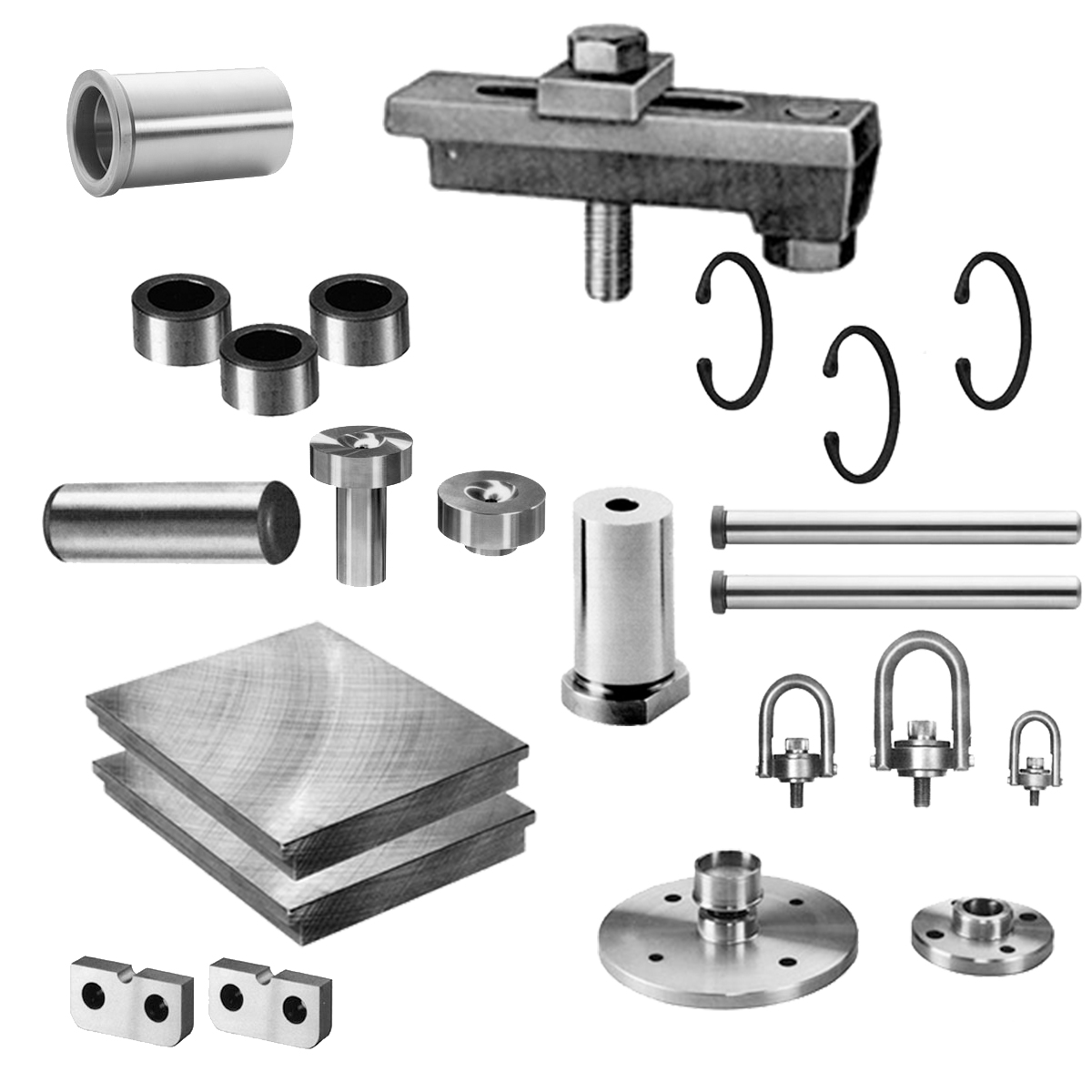
MUD Components
MUD Quick-Change® frames and companion insert mold series are designed to bring efficiency and cost savings to injection molding operations of all sizes. Compatible with machines up to 500 tons, these systems include a comprehensive range of components that allow full customization to meet various production needs. Their rapid changeover capability reduces downtime, improves productivity, and aligns perfectly with lean manufacturing strategies.
At KingStar Mold, we integrate MUD Quick-Change Systems to help our clients optimize performance while lowering operational costs. Our team ensures that every MUD setup is tailored for precise fit, fast turnaround, and long-term durability—making it an ideal solution for both prototyping and full-scale production. Whether you’re looking to shorten lead times or improve tooling flexibility, KingStar Mold delivers expert guidance and support throughout your mold design and manufacturing journey.
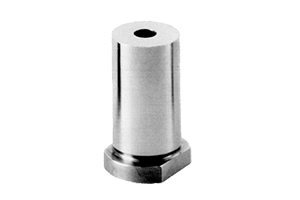
Sprue Puller Plug
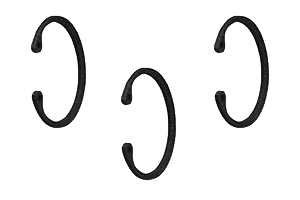
Snap Rings
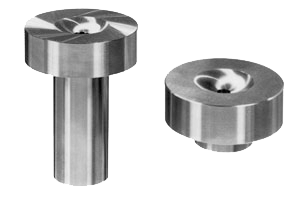
Sprue Bushings
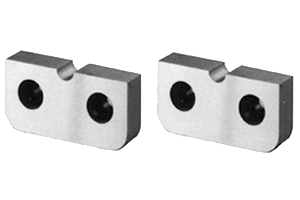
Hardened Runner Pads
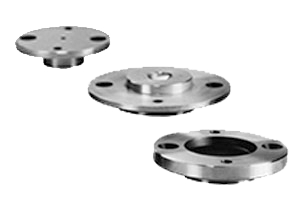
Top Locating Rings
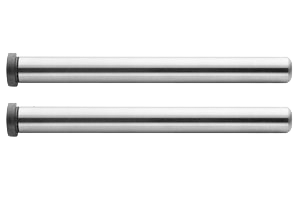
Straight Leader Pins
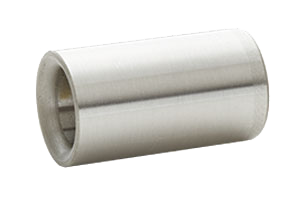
Straight Bushings
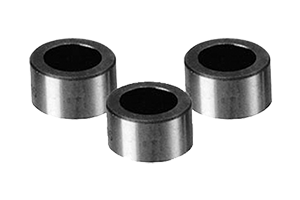
Spacers
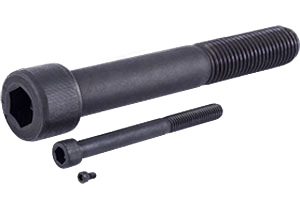
Frame Screw Shoulder
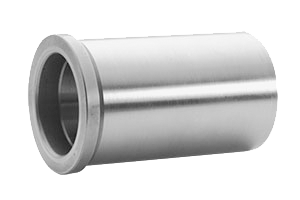
Shoulder Bushings
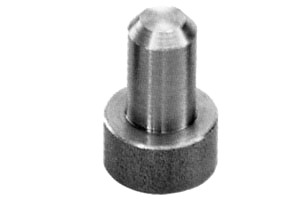
Rest Button
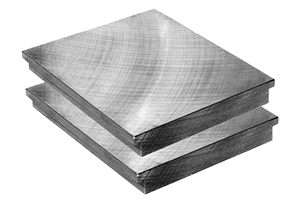
Ear Plates
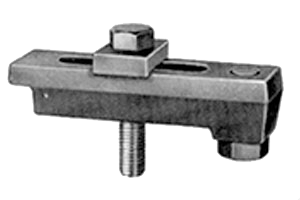
Mold Clamps
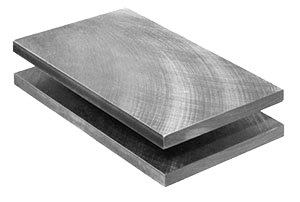
Standard Ejector Plate Sets
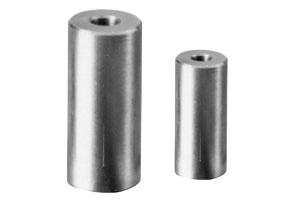
Insert Mold Pillar Post
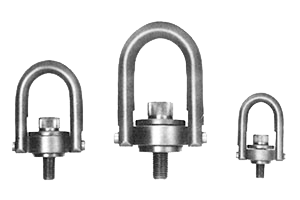
Snap Rings
MUD Quick-Change Mold Base Adapter
What Is Our Adapter System?
Our Adapter System is a modular solution designed to convert traditional mold bases into a quick-change setup. It transforms your existing mold base into a MUD-compatible system, significantly increasing efficiency without the need to replace your entire tooling setup.
How Does the System Work?
• The adapter frame is mounted directly onto the molding machine. It can be clamped using traditional mold clamps or bolted in place using socket head cap screws and optional pre-drilled mounting holes.
• Ear plates are fastened to the existing standard mold base using socket head cap screws and locating dowels, ensuring secure alignment.
• Water lines are quickly connected via the system’s built-in water manifold, allowing fast and clean utility setup.
Key Benefits
• Rapid Mold Changes: Enables fast insert removal and installation, reducing downtime
• Streamlined Water Connections: Integrated water manifold allows instant utility hookup
• Minimal Setup Time: Greatly shortens changeover time without major equipment modifications
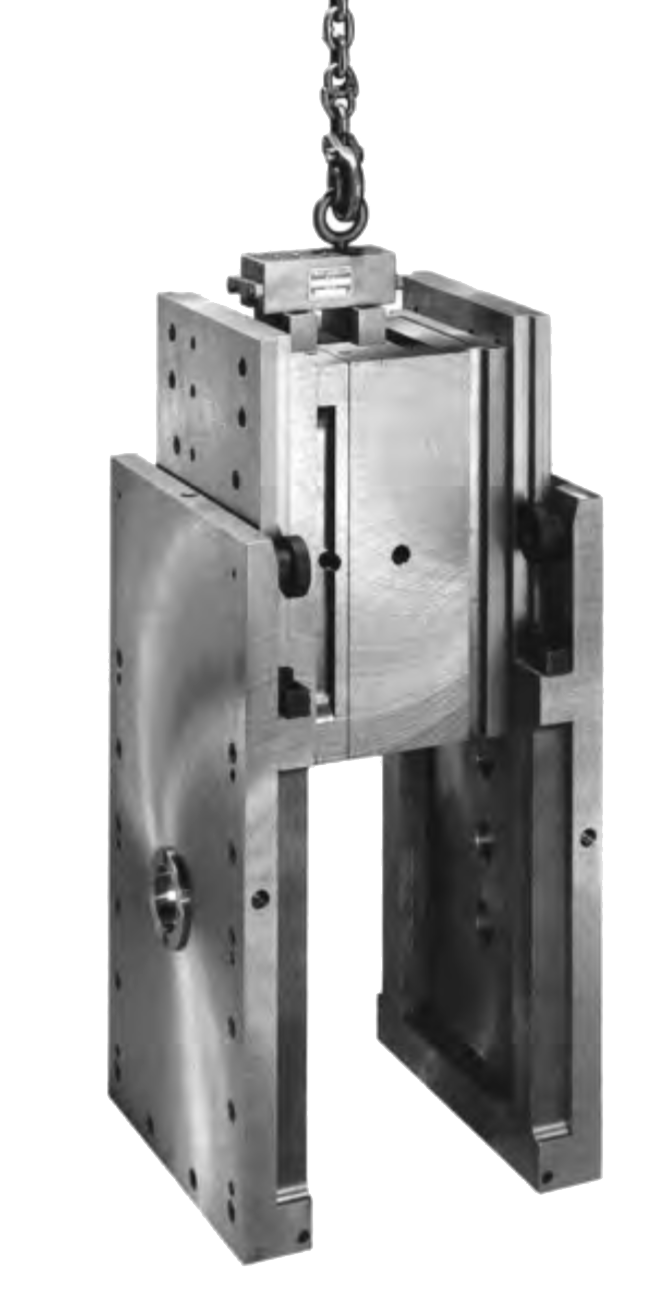
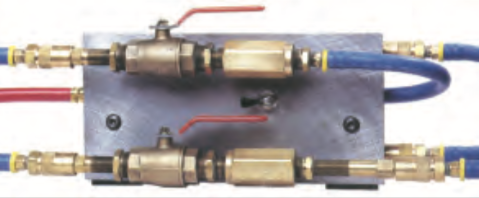
Key Benefits:
-
Purges waterlines in 30 seconds or less
-
No electrical components – simple and reliable mechanical operation
-
Reduces downtime and helps prevent corrosion in idle molds
-
Installs directly on the machine and becomes a permanent part of your setup
MUD Waterline Purge System
The MUD Waterline Purge System is the perfect solution for molders who want to flush waterlines before storing their molds. Engineered for efficiency, this fully mechanical system requires virtually no maintenance and is seamlessly integrated into the molding machine’s waterline system.
Easy 3-Step Operation:
-
Shut off the water supply using the two integrated valves
-
Activate the air switch to inject air and purge the cooling media
-
Reopen the valves when ready to resume water flow
For closed-loop systems, be sure to collect the purged media in a holding container to prevent spills.
The MUD Waterline Purge System simplifies maintenance, protects your tooling investment, and speeds up changeovers—making it an essential upgrade for any quick-change molding setup.
MUD Quick-Change Prototype Adapter
Achieve RAPID SUCCESS by transforming your MUD mold base into a Prototyping Base. There are times when prototypes made from actual production materials are necessary, particularly for low to mid quantities of parts where traditional production tooling may not be cost-effective. Your clients frequently face strict deadlines to launch new products for market testing. By incorporating our Quick-Change Prototype Adapter into your current MUD Mold System, you can swiftly produce high-quality parts that are suitable for real-world applications.
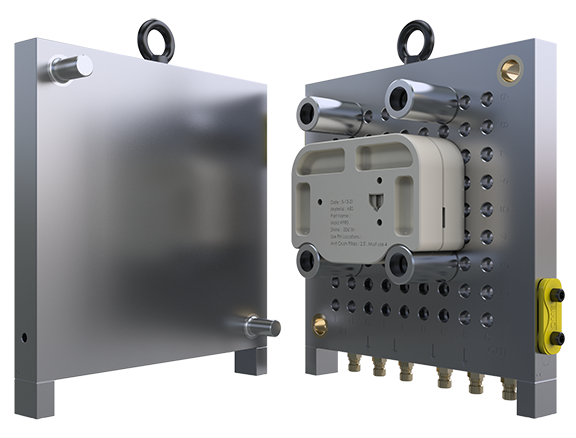
How We Work
Get Your Request
Get your detailed requirements for injection mold manufacturing, including mold materials, mold life, number of mold cavities, runner requirements, and surface treatment requirements
Confirm DFM Report
Our engineering team begins to conduct mold flow analysis and provides DFM ( Design for Manufacturing) report according to your detailed requirements and confirms all details with you
Mold Deisgn
Our engineering team make a 3D drawing design of the injection mold based on the confirmed DFM report, including all details of the mold and confirm the mold design drawings with you
Injection Mold Manufacturing
Based on the finalized mold drawings, we export the 2D drawings with key dimensions and tolerance requirements. Our plastic injection mold makers then begin manufacturing the injection mold and perform tolerance inspections at each processing step.
Mold Final Acceptance
Mold Assembly & Testing
Once the injection mold is created, we proceed with fitting, assembling, and testing the mold. This process is repeated until the product meets your specifications, after which we send you samples for confirmation.
Workflow of Changing MUD Mold Insert
Hot Runner
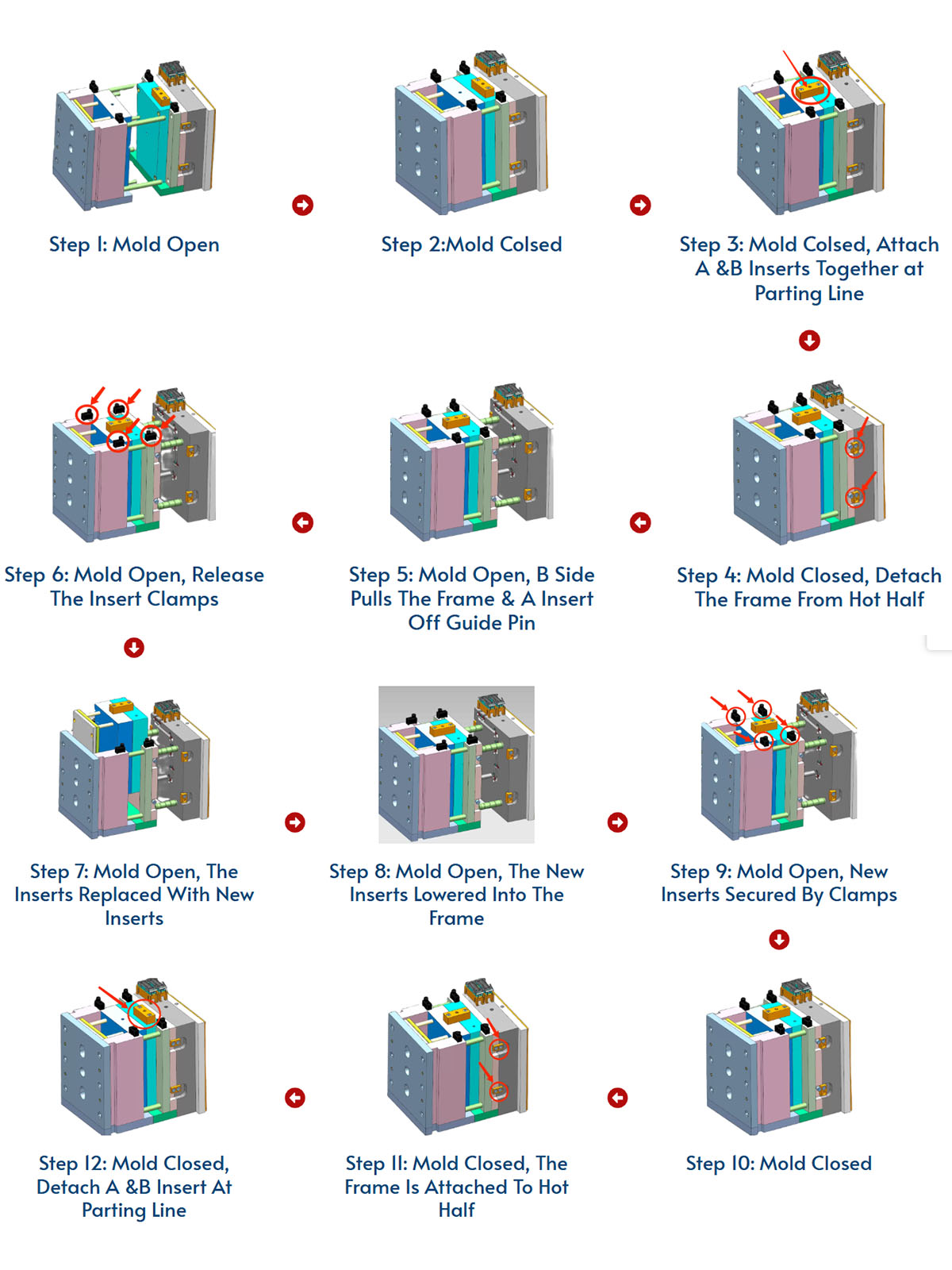
Cold Runner
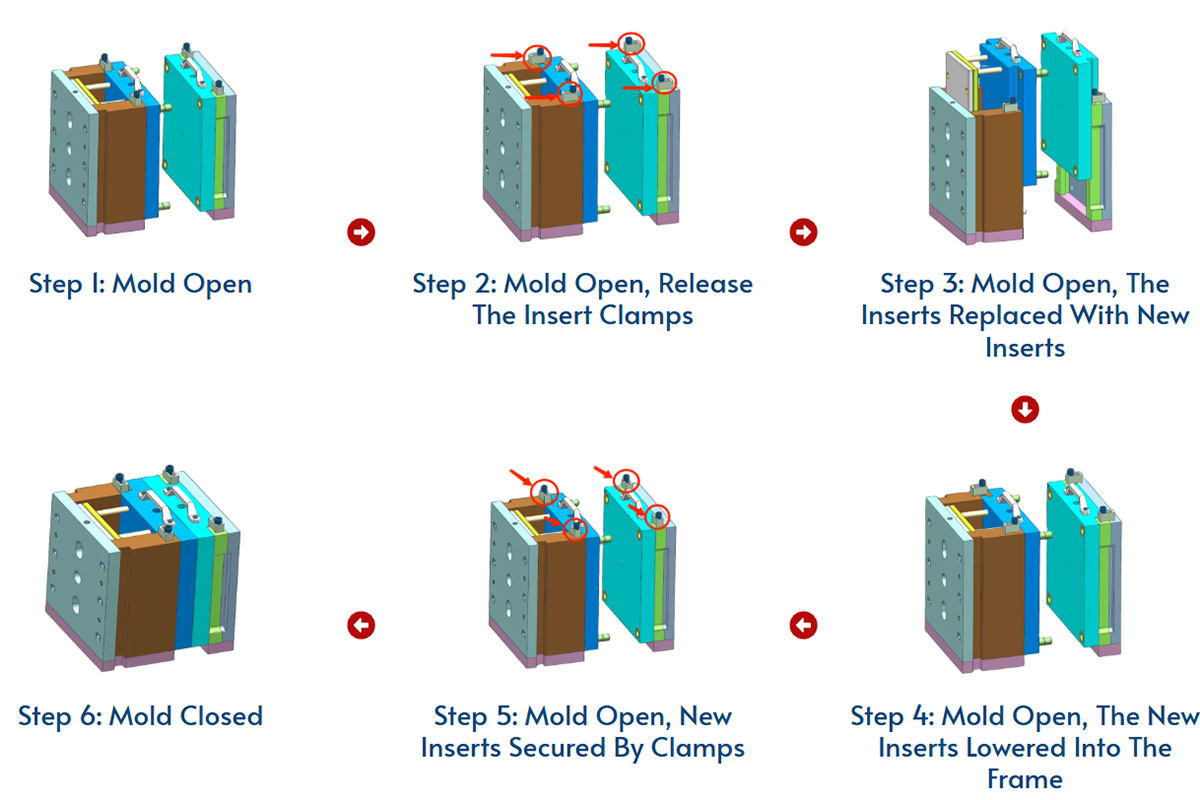
What Are the Applications of MUD Molds?
Typical applications of MUD injection molds center on scenarios requiring short product lifecycles, diverse styles, and moderate volumes where their strengths in fast mold swapping, cost reduction, and flexibility shine:
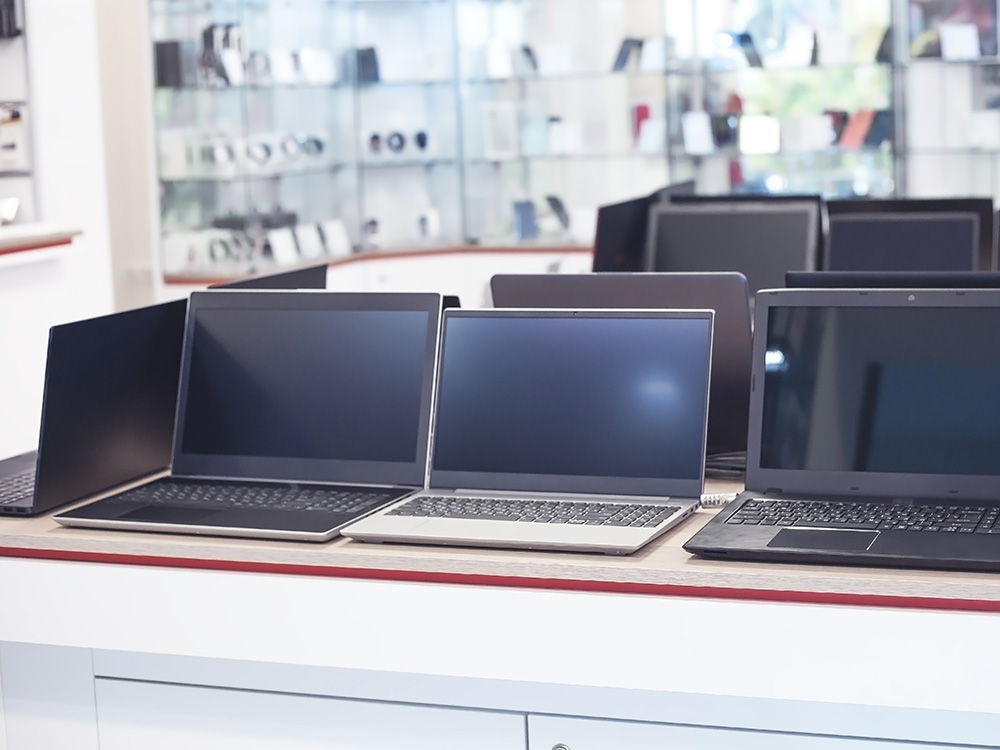
Consumer Electronics
Think headphone parts, charger housings, or smartwatch buttons. These products iterate quickly (every 6–12 months), and MUD molds enable fast switches between models. One client swapped 3 types of charging port molds in 3 days just by changing inserts.
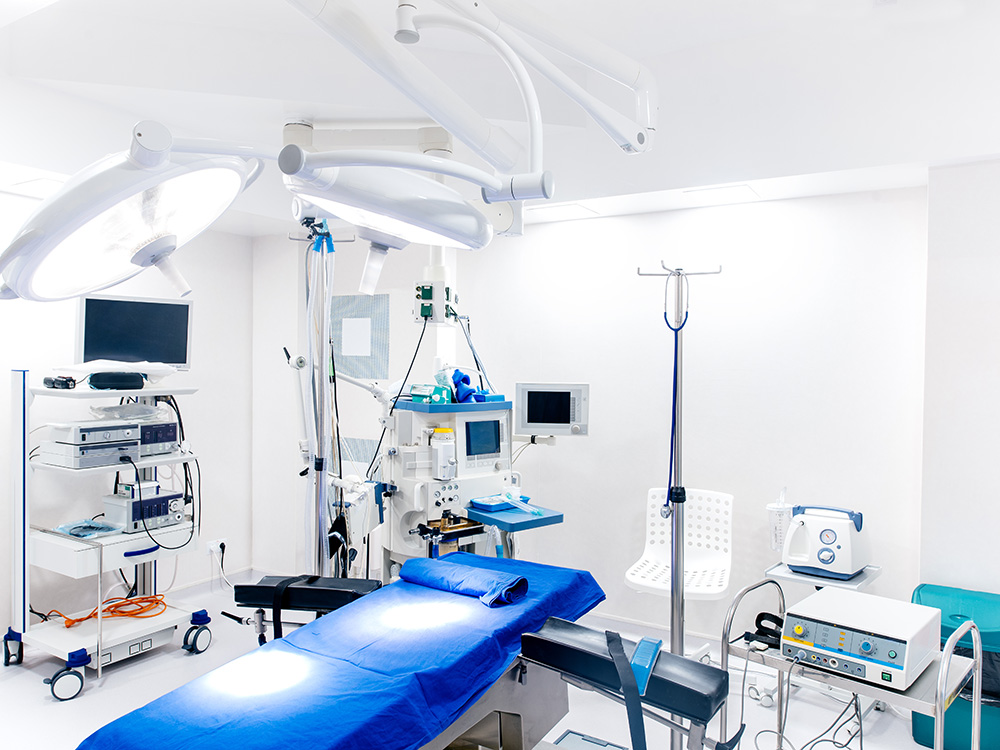
Medical Consumables
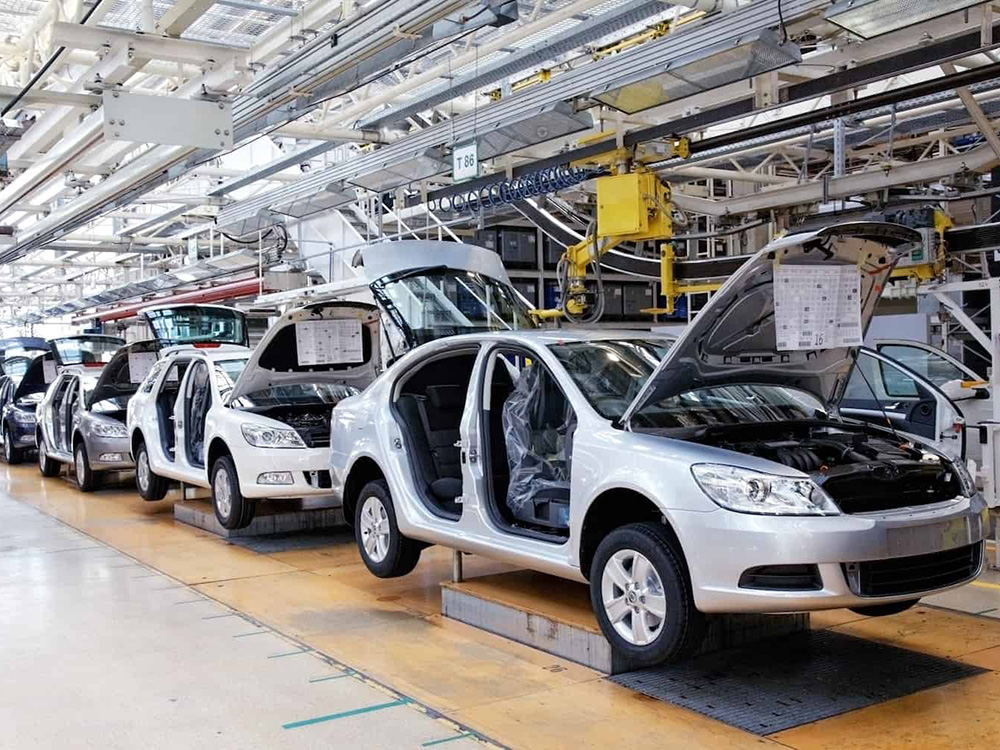
Automotive Small Parts
Sensor housings, clips, or interior plastic pieces, which often need to fit multiple vehicle models. MUD lets one production line handle 3–5 part types; a car parts maker used our double H-frame to produce two sensors simultaneously, boosting efficiency by 40%.
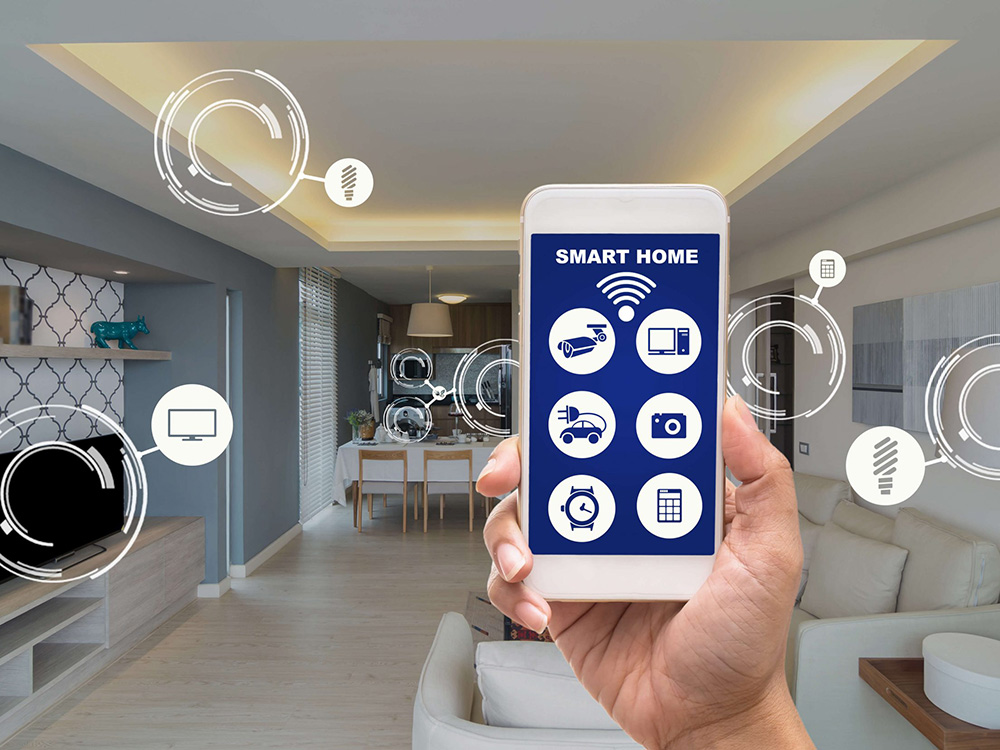
Smart Home Devices
Buttons for small appliances or remote control casings—styles vary, but single-model volumes are low. MUD’s cost-effective insert design cuts initial tooling investment by nearly 60% for clients launching multiple variants.
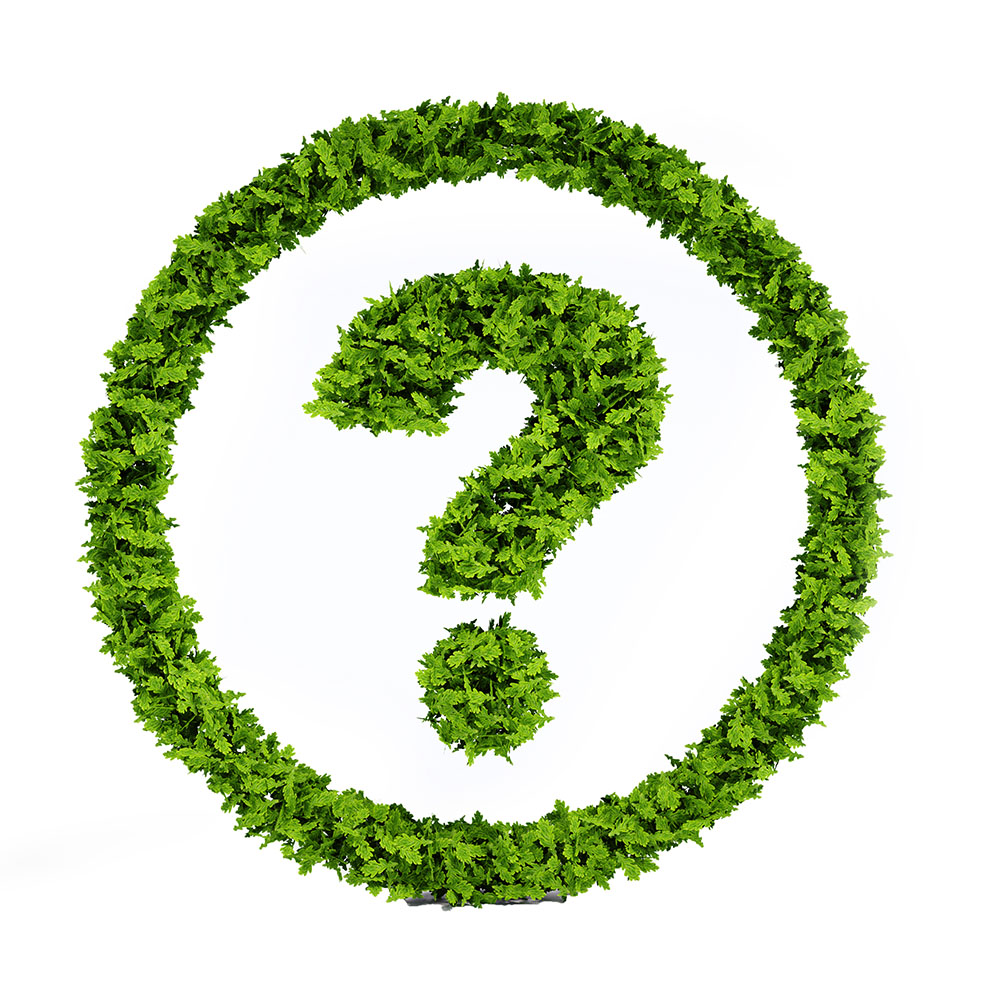
Frequently Asked Questions
MUD molds are designed for quick assembly and modification, allowing for fast production of prototypes. The modular design enables easy changes to mold inserts without requiring extensive retooling, making it possible to iterate designs swiftly and efficiently test new concepts in real production materials.
Our team is available to provide assistance throughout the entire process, from initial design to production. For more information about our one-stop manufacturing capability, you can refer to this page to learn how to turn your idea into a product.
For project details, please contact our customer support or consult with our technical specialists for tailored guidance regarding your specific project needs at sales@kingstarmold.com.