Mold Making Process
Challenges You Might Be Facing
In the past, you may have encountered the following issues with your current suppliers:
Excessive Molding Defects
Hidden Cost Increases
Long injection cycle times and poor communication lead to unexpected delays and rising costs, affecting your bottom line.
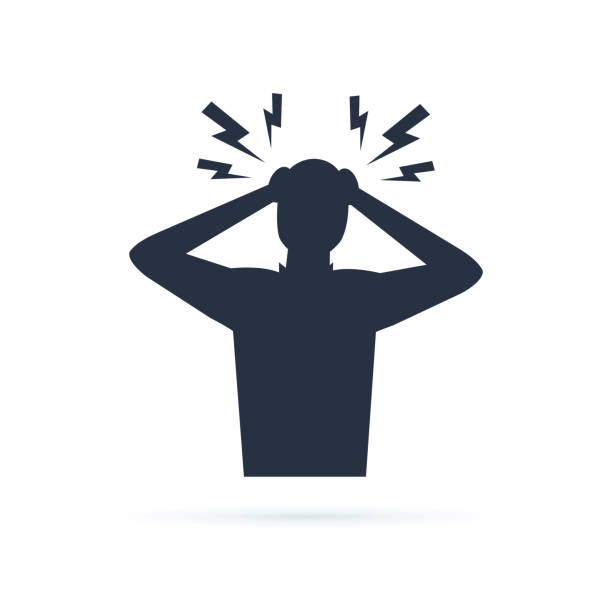
Frequent Mold Revisions
Frequent mold repairs and adjustments due to design or process issues often delay project timelines, leading to inefficiencies.
Missed Deadlines
Suppliers consistently push back delivery dates with numerous excuses, leaving you with delayed production and missed commitments.
How KingStar Mold Solved the Problem
At KingStar Mold, we focus on proactive communication and swift problem-solving to ensure smooth project execution and client satisfaction.
Design Process
We ensure rigorous mold design to maximize efficiency, with most molds being ready for mass production after just one trial.
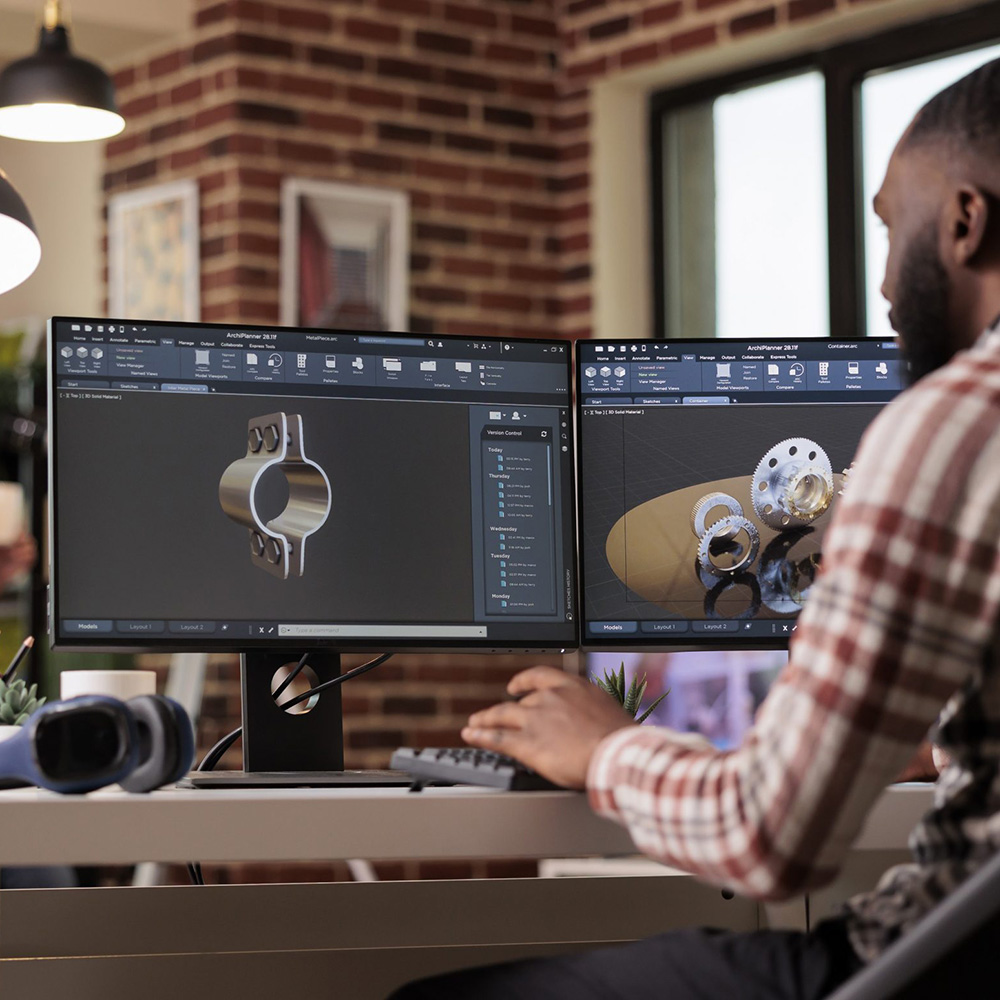
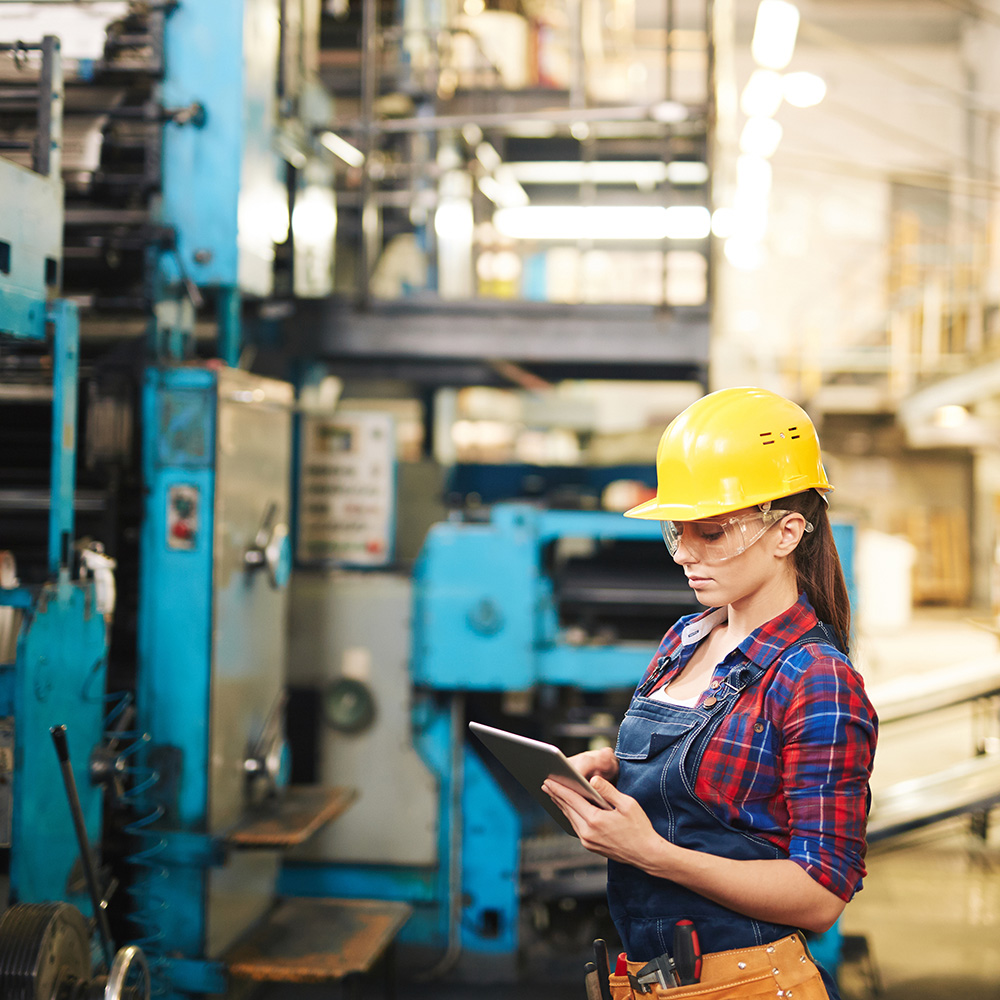
Quality Assurance
We ensure quality at every stage of the process to proactively identify potential issues before mass production begins.
Delivery Time
We ensure timely delivery by keeping you updated at every step of the process.
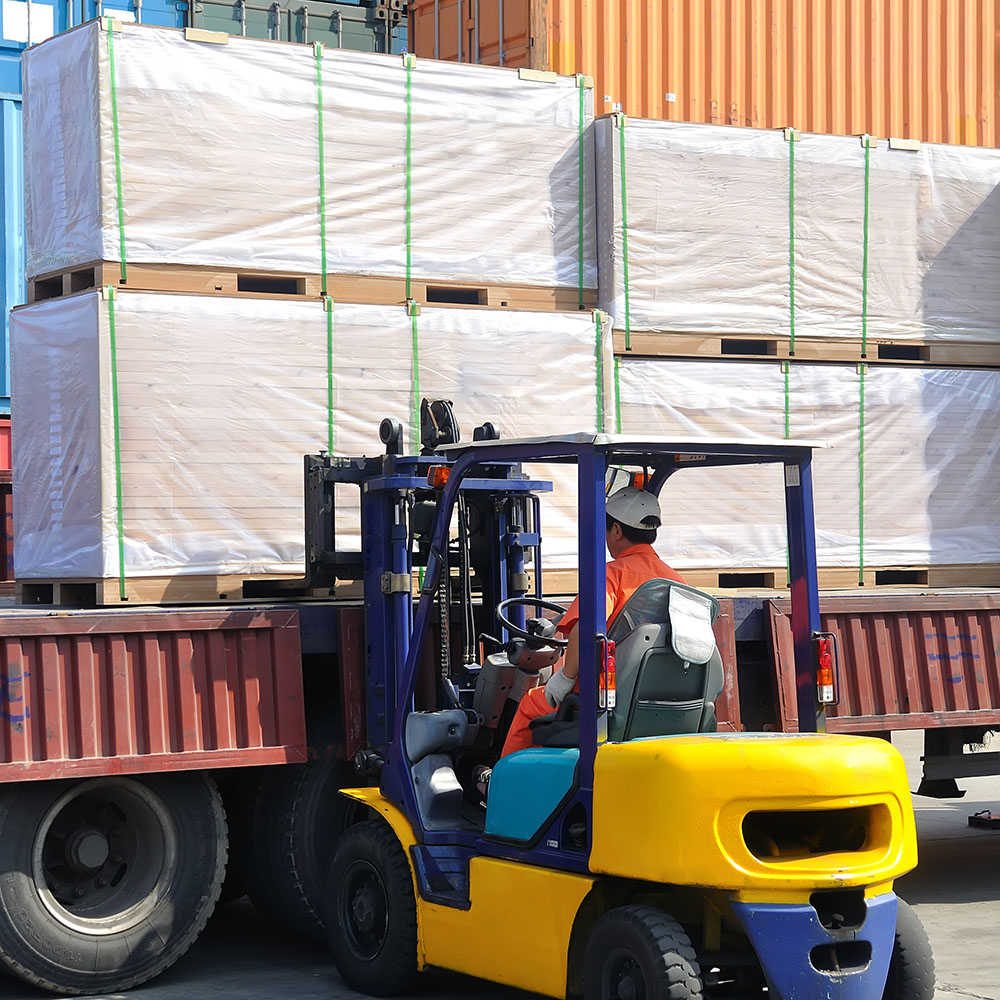
Custom Plastic Injection Mold Making Company
We are a leading custom plastic injection mold maker / tooling builder, recognized for our precision, innovation, and exceptional quality. With our state-of-the-art facility and skilled experts, we manufacture intricate plastic components using advanced molding techniques, consistently delivering top-tier solutions to meet the unique needs of our clients.
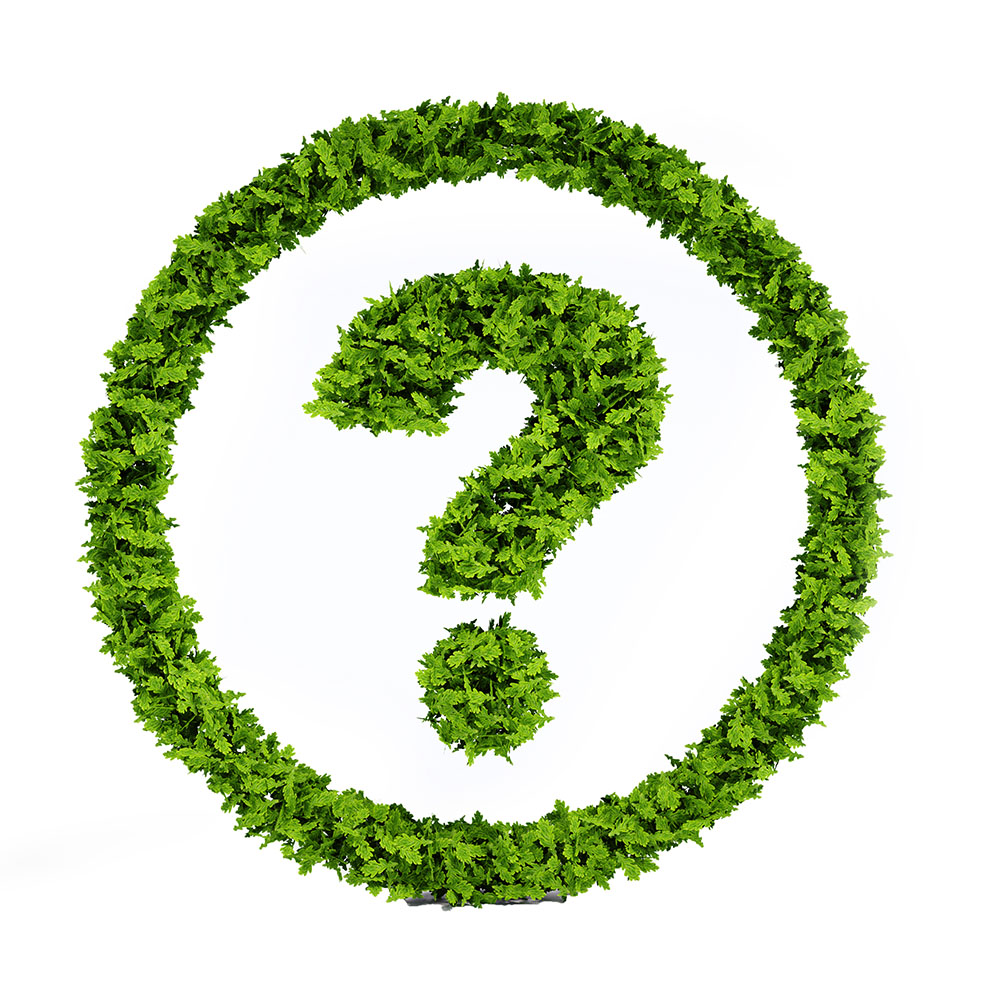