In today’s highly competitive and regulated manufacturing landscape, ensuring product quality and transparency throughout the production process is crucial. Traceability is a key concept that allows manufacturers to track and document every step of a product’s lifecycle—from raw material sourcing to final delivery. By maintaining detailed records of where, when, how, and by whom a product was made, traceability provides a clear and accountable view of the entire production process.
This post will delve into the importance of traceability in manufacturing, exploring why it’s essential for compliance, quality control, and efficiency. We’ll examine how traceability impacts different industries, its role in enhancing supply chain transparency, and the technologies driving its adoption. By the end, you’ll understand why integrating traceability is no longer just an option but a necessity for modern manufacturers.
- 1. Types of Traceability
- 2. Why Traceability Matters
- 3. Common Challenges Without Traceability
- 4. How Traceability Works in Practice
- 5. Key Industry Examples
- 6. Benefits of a Robust Traceability System
- 7. Implementing a Traceability System: Key Considerations
- 8. Digital Transformation and the Future of Traceability
- 9. What Makes KingStar a Reliable Partner for Traceable Manufacturing
- Conclusion
1. Types of Traceability
In manufacturing, traceability can be categorized into different types based on what is being tracked and monitored during the production process. Each type serves a specific purpose and contributes to the overall goal of ensuring product quality, safety, and compliance. Below are the main types of traceability used in modern manufacturing:
1.1 Lot Traceability: Tracking Batches of Materials or Components
Lot traceability is essential for tracking batches of materials or components during production. It ensures that if any issues arise, manufacturers can quickly trace back to the source. For example, in the food industry, lot traceability helps isolate a contaminated batch, preventing the spread of contamination across multiple products. This level of traceability is also critical in industries like pharmaceuticals, where quality control and regulatory compliance are top priorities.
Unlike individual product tracking, which focuses on the final product, lot traceability deals with the broader batch, allowing for faster identification of the root cause when multiple units are affected by a common issue.
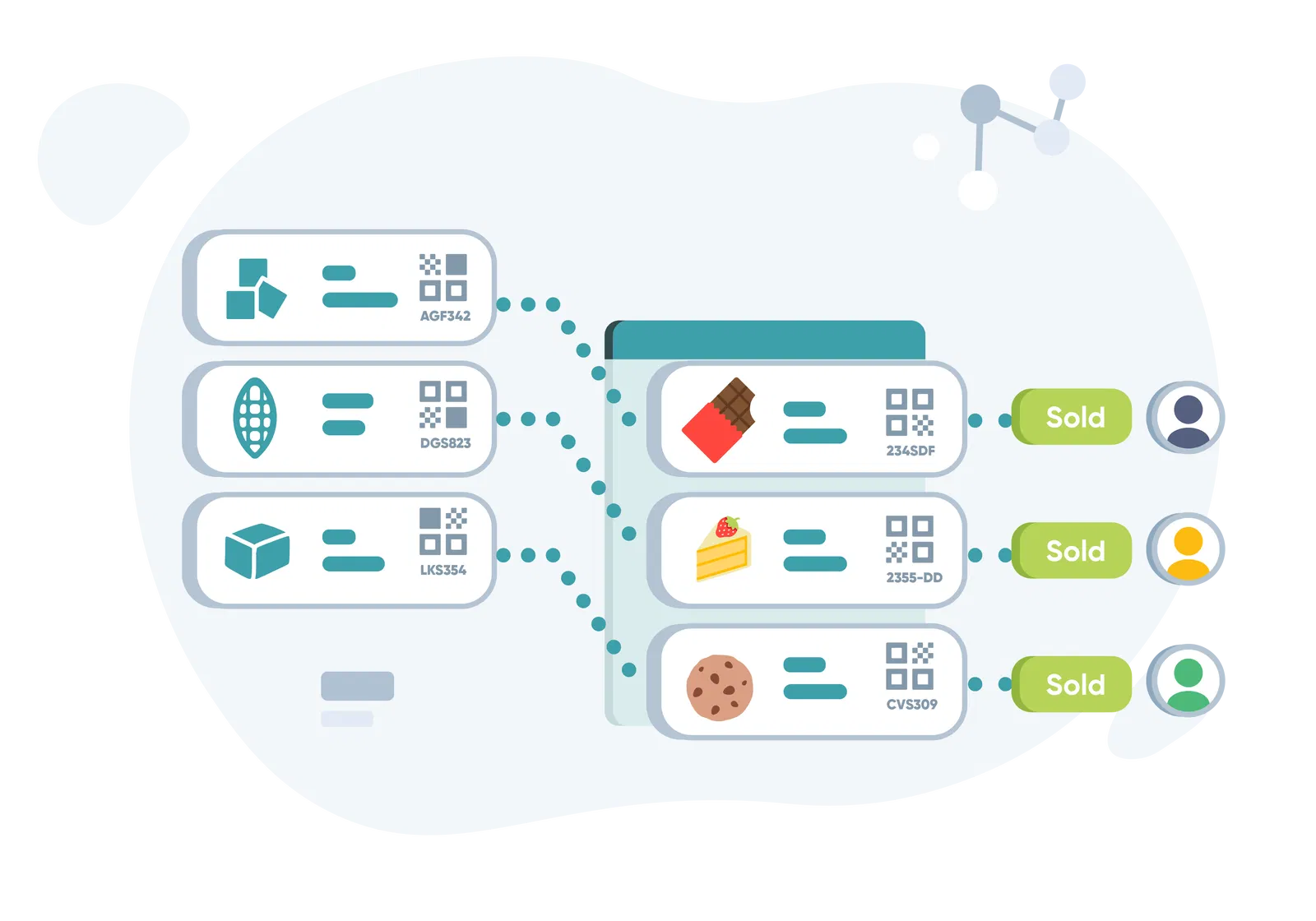
1.2 Material Traceability: Tracing Raw Materials Through Processing Stages
In material traceability, the focus is on monitoring the journey of raw materials from sourcing to processing. This form is essential when the raw materials directly influence the end product’s quality, performance, or compliance with industry standards.
- Tracking Materials Through Production: Material traceability tracks everything from raw materials’ origin, handling, and storage conditions to their transformation into finished goods. It’s especially critical in industries with stringent regulatory requirements, such as aerospace and medical device manufacturing.
- Why It Matters: For instance, if a certain batch of titanium used in aerospace parts is sourced from a specific supplier, and it later fails quality control, material traceability helps identify where it came from, who handled it, and what processing steps it went through before it became part of a product.
1.3 Product Traceability: Following the Finished Product from Factory to Customer
This involves tracking the final product once it’s completed and ready for distribution. While similar to lot traceability, product traceability focuses more on individual items, tracking them from factory to customer and beyond.
- Full Product Journey: Product traceability includes serial numbers, shipping data, and maintenance history, ensuring each product can be traced back to its manufacturing origin. This is critical in industries like automotive and medical devices, where individual product performance must be monitored over time.
- Real-Life Example: In automotive manufacturing, being able to trace the history of a specific car part—like a brake system or airbag—can help identify issues after the product is in use, potentially preventing major safety risks and enabling targeted recalls.
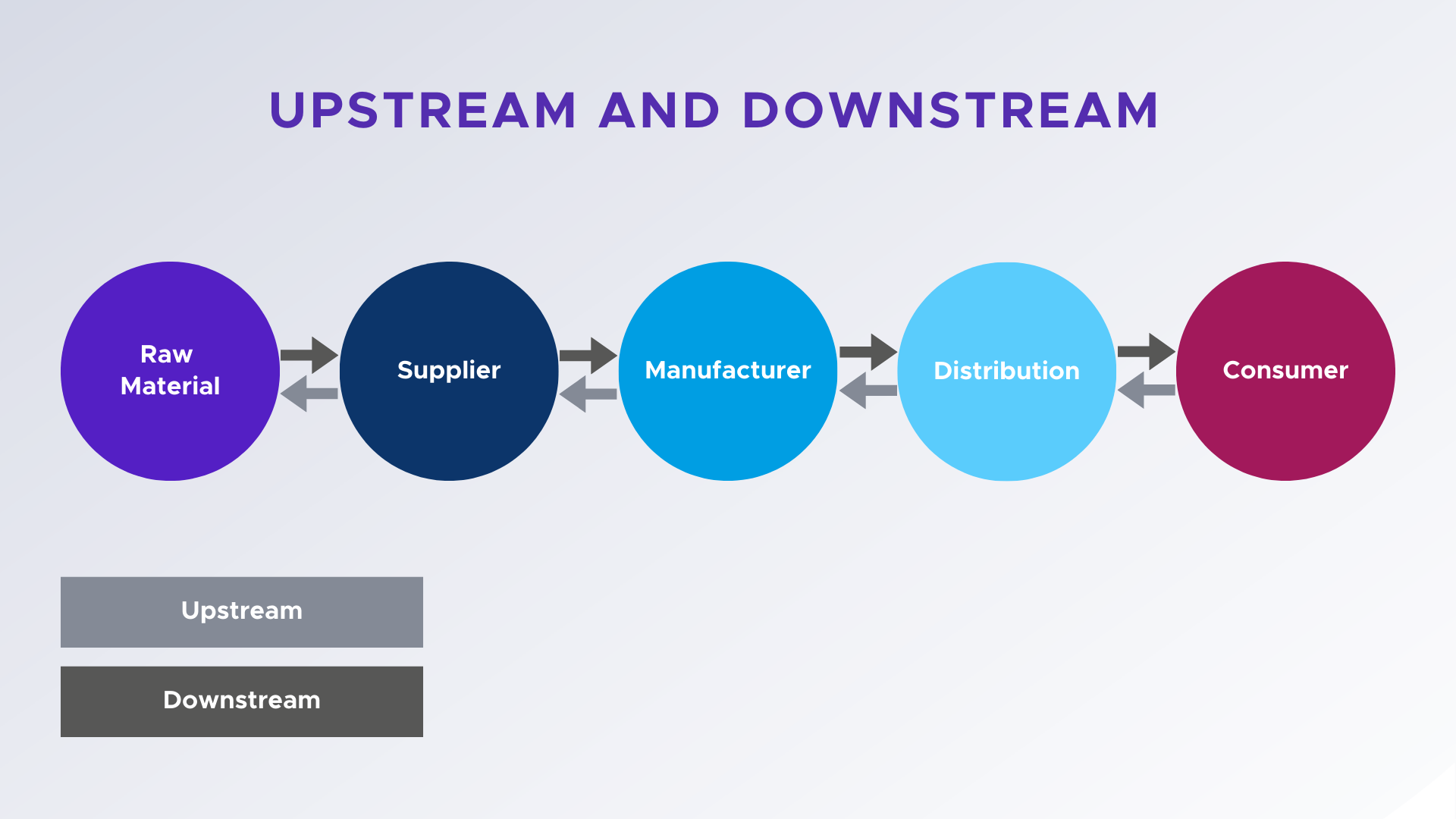
2. Why Traceability Matters
Traceability is no longer a mere operational tool; it has become a cornerstone for success in modern manufacturing. From ensuring compliance with regulations to maintaining high-quality standards, traceability plays a pivotal role across various industries. Below, we’ll break down why traceability is essential and how it impacts manufacturers at different levels.
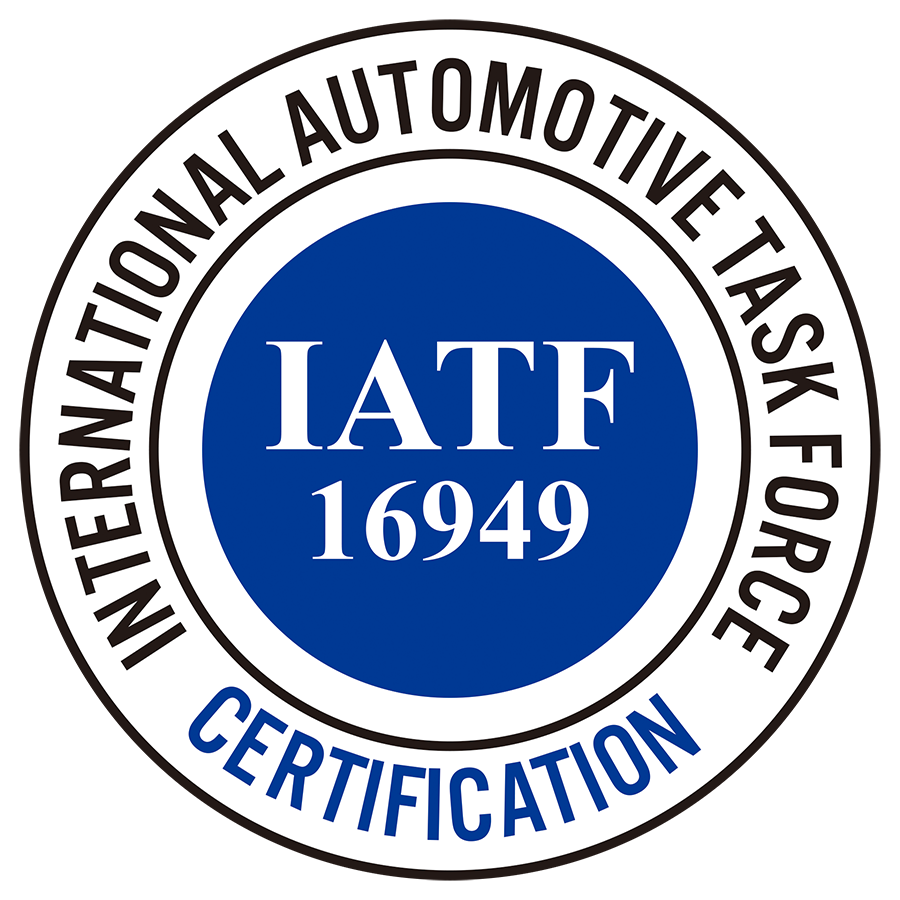
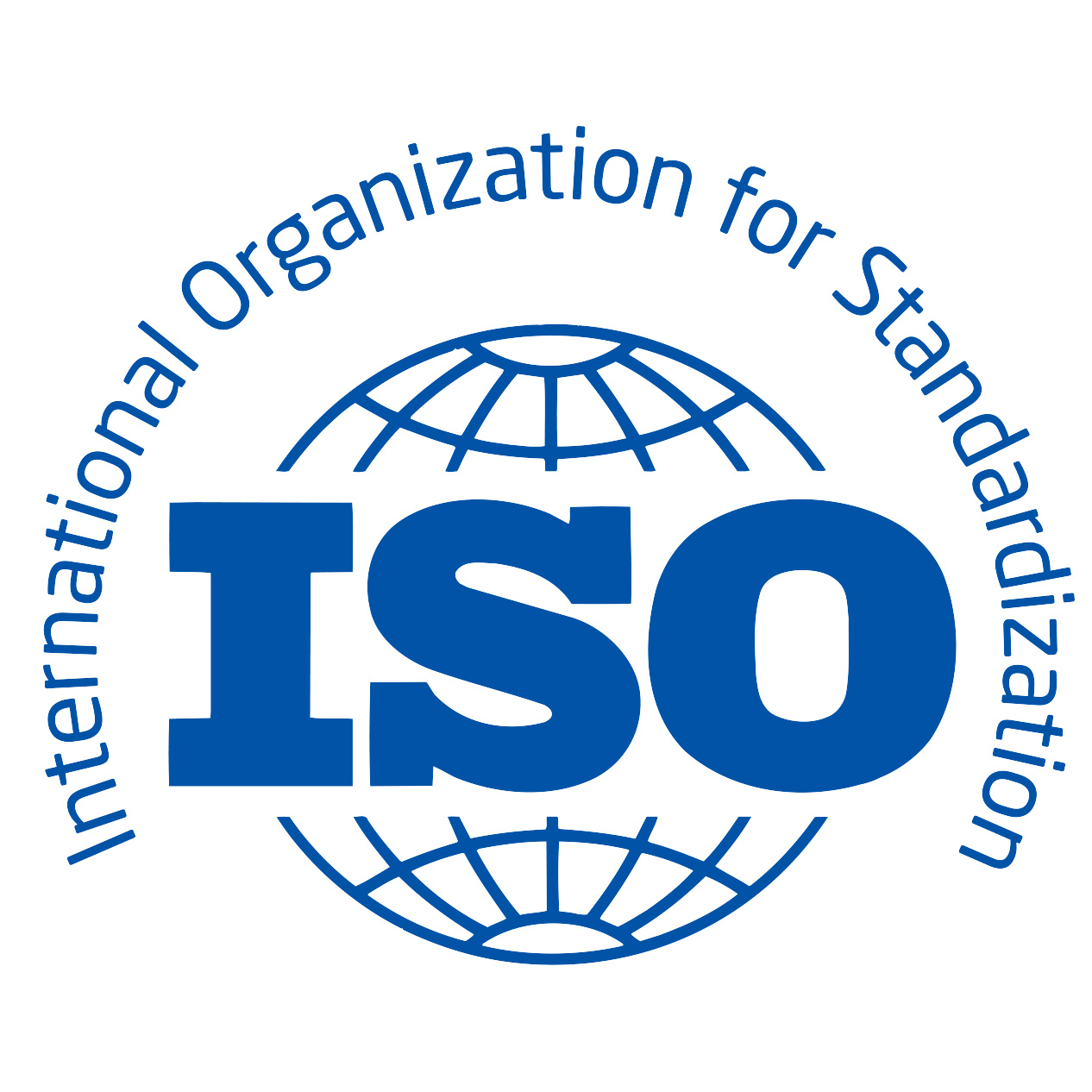
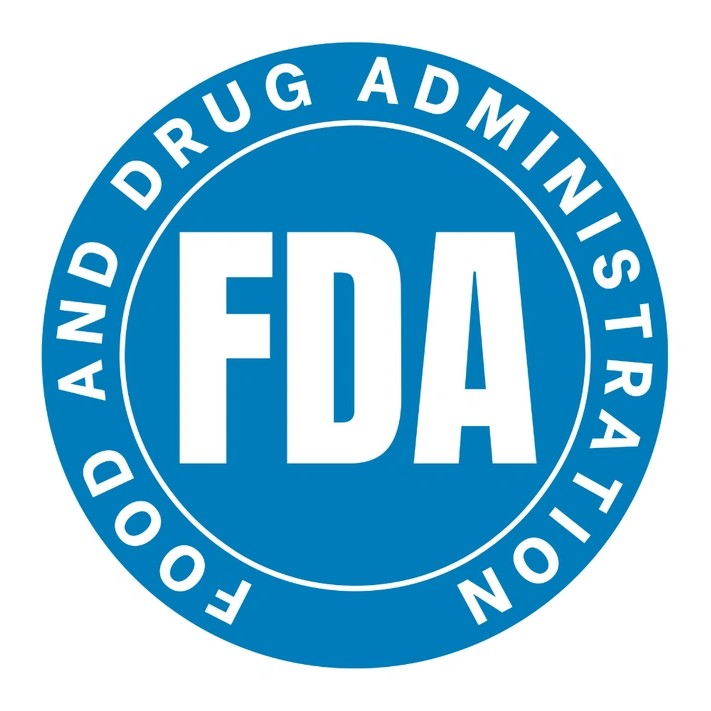
2.1 Regulatory Compliance: Meeting Industry Standards
- Why It Matters: In industries like medical devices, automotive, aerospace, and food production, regulatory compliance is mandatory. Regulatory bodies such as the FDA, ISO, and IATF 16949 require manufacturers to maintain detailed records of materials and processes used during production.
- Traceability’s Role: By ensuring each step in the production process is recorded, traceability allows manufacturers to prove compliance during audits and inspections. This reduces the risk of non-compliance penalties and ensures the company meets industry standards.
- Example: A medical device manufacturer needs traceability to meet FDA regulations. If a defect arises, they can provide records showing the exact materials used and the specific processes followed, helping them avoid costly legal issues.
2.2 Quality Control and Defect Containment: Ensuring High Standards
- Why It Matters: In industries like medical devices, automotive, aerospace, and food production, regulatory compliance is mandatory. Regulatory bodies such as the FDA, ISO, and IATF 16949 require manufacturers to maintain detailed records of materials and processes used during production.
- Traceability’s Role: By ensuring each step in the production process is recorded, traceability allows manufacturers to prove compliance during audits and inspections. This reduces the risk of non-compliance penalties and ensures the company meets industry standards.
- Example: A medical device manufacturer needs traceability to meet FDA regulations. If a defect arises, they can provide records showing the exact materials used and the specific processes followed, helping them avoid costly legal issues.
2.3 Recall Management: Minimizing Impact
- Efficient Targeting: In the event of a product recall, traceability allows manufacturers to pinpoint the affected batches or product lines. This reduces the scope of the recall, minimizing costs and damage to the brand.
- Reduced Cost: Instead of recalling an entire product range, traceability makes it possible to target specific products or batches, significantly lowering the cost associated with recalls.
- Example: If a defective batch of food products is identified, traceability can help locate and recall only those specific products, preventing an unnecessary recall of unaffected goods.
2.4 Customer Confidence and Transparency: Building Trust
- Transparency for Consumers: Today’s consumers are more aware of the origin and production processes behind the products they buy. Traceability enables manufacturers to share detailed information about product sourcing, production processes, and quality control measures.
- B2B Relationships: For B2B manufacturers, traceability provides transparency that helps foster trust with business partners. Knowing that products are thoroughly tracked and meet all required standards assures partners of the manufacturer’s reliability.
- Example: A customer buying a food product wants to know where the ingredients came from and how they were processed. Through traceability, the manufacturer can provide a transparent history of each product’s lifecycle, boosting customer confidence.
2.5 Supply Chain Visibility: Enhanced Control Over Operations
- Better Tracking: Traceability allows manufacturers to track every step of the supply chain, from raw material sourcing to product delivery. This level of oversight ensures smoother operations and allows for better management of supplier relationships.
- Identifying Bottlenecks: Traceability highlights potential delays or quality issues at various stages of the supply chain, enabling manufacturers to proactively address problems before they escalate.
- Example: A manufacturer can spot delays in the delivery of a key component from a supplier. With traceability, they can quickly identify the issue, communicate with the supplier, and adjust the production schedule to minimize delays.
3. Common Challenges Without Traceability
The absence of traceability in manufacturing leads to several significant challenges that hinder efficiency, increase costs, and compromise quality. Below, I’ll outline the most common issues manufacturers face when traceability is lacking.
3.1 Inability to Perform Root Cause Analysis
Without traceability, identifying the source of defects or inefficiencies becomes a prolonged and complex task. When quality problems arise, manufacturers cannot quickly trace back through the production stages to determine where things went wrong. This can severely delay corrective actions.
- Delayed Issue Resolution: Without accurate data, it’s difficult to pinpoint whether the issue lies with a supplier, a specific machine, or a production batch. As a result, manufacturers may end up troubleshooting across multiple stages of production, wasting time and resources.
- Inconsistent Investigations: The lack of clear records for each step in the production process means investigations often yield inconsistent results. This makes addressing the issue and preventing recurrence more challenging.
3.2 Broader, More Expensive Recalls
In the event of a product defect, manufacturers without traceability often face the dilemma of conducting a broad recall, which can incur high costs and damage customer trust. A comprehensive recall typically affects more products than necessary, simply because the manufacturer cannot trace the exact scope of the defect.
- Unnecessary Recalls: If manufacturers can’t trace a defective product back to a specific batch or supplier, they may end up recalling entire production lots, resulting in unnecessary operational costs and disruptions.
- Reputation Damage: When recalls are too broad, consumers might perceive the company as inefficient or untrustworthy, which could have a long-term negative effect on brand loyalty.
3.3 Compliance Risks and Potential Penalties
Many industries, such as automotive, aerospace, and medical devices, are subject to strict regulatory requirements for traceability. Without a traceability system, companies may fail to meet these regulations, risking costly fines, production stoppages, or legal action.
- Increased Risk of Non-Compliance: Many standards, such as ISO and FDA regulations, require manufacturers to maintain detailed records of every step in the production process. Without proper traceability, companies cannot demonstrate compliance, which opens the door for audits and penalties.
- Reputation Risks: Non-compliance with regulatory requirements not only results in fines but can also severely damage a company’s reputation, especially if the issue affects product safety or quality.
3.4 Fragmented Data Across Systems
Manufacturers that lack traceability often struggle with fragmented data across different systems, making it difficult to gain a holistic view of production operations. Data may be stored in separate systems—such as inventory management, quality control, and production monitoring—without any integration.
- Inefficient Data Management: When data is isolated in different systems, it becomes harder to track product performance, monitor quality, or identify trends in manufacturing. This lack of unified data leads to inefficiencies in decision-making.
- Missed Opportunities for Optimization: Without integrated data, manufacturers miss opportunities to optimize processes or improve product quality, as they lack the insights needed to make informed changes across the production process.
4. How Traceability Works in Practice
Traceability in manufacturing is an intricate process that involves various tools and integrated systems, each contributing to the smooth operation of product tracking. Let’s break down how this works in practice:
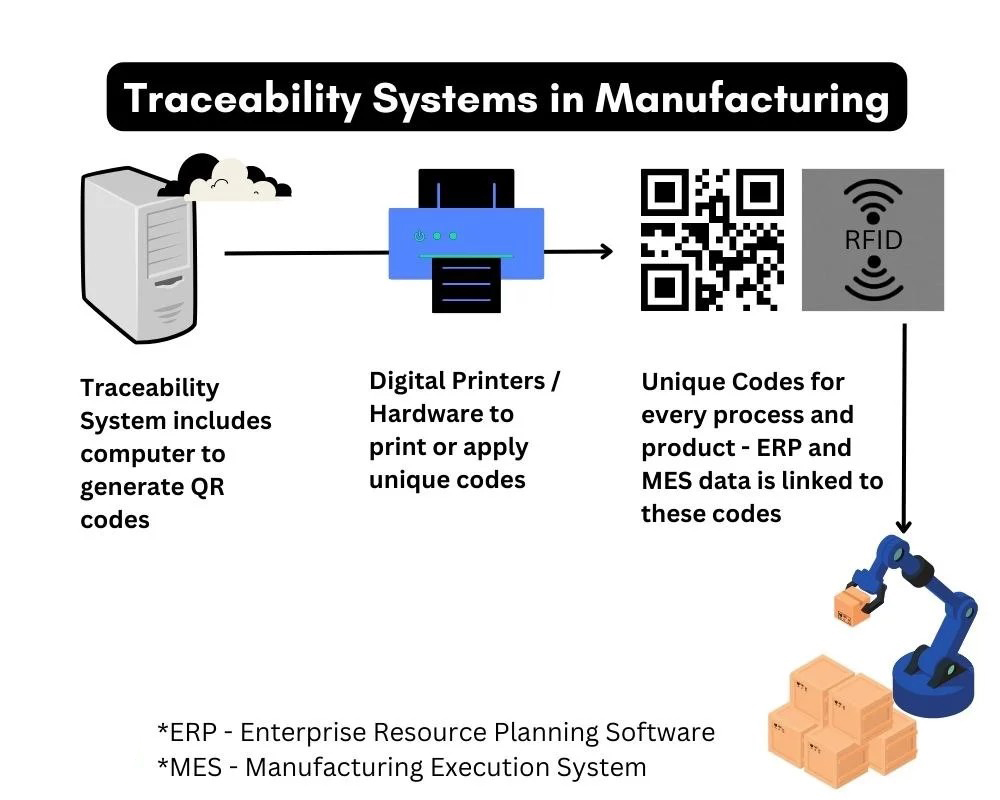
4.1 Technology for Tracking
Traceability relies on different technologies, each suited to varying needs in manufacturing:
- Barcodes: A simple and cost-effective solution, used primarily in environments where basic tracking suffices. Barcodes are easy to print and scan, providing a quick link between products and their production histories.
- RFID Tags: These are a more advanced solution, offering real-time tracking. RFID tags can store data that’s transmitted wirelessly, which makes them ideal for larger operations or for items that need to be tracked across vast networks or geographical distances.
- QR Codes: Although similar to barcodes, QR codes can hold much more information, such as detailed product specifications or even manufacturing steps. They are often used in smaller production environments or for specialized products that need additional traceability.
These technologies each serve a specific purpose, depending on the scale and complexity of the manufacturing process.
4.2 Integration of Systems: MES and ERP
Traceability systems work best when they are integrated into the overall management infrastructure of the company. Two key systems that support traceability are:
- MES (Manufacturing Execution Systems): These systems monitor and control production activities in real-time. MES can track the flow of materials through each production stage, ensuring that each step is logged with precision. In an automotive parts plant, for example, MES can track each car part’s journey from the first assembly step to the final inspection, ensuring that each stage is performed according to specification.
- ERP (Enterprise Resource Planning): ERP systems manage the broader business processes such as inventory, order processing, and shipping. By integrating ERP with MES, manufacturers can link production data with sales orders, allowing for real-time updates on inventory levels and shipment statuses.
Together, MES and ERP provide a holistic view of production and inventory management, improving coordination across departments and boosting the overall accuracy of traceability.
4.3 Real-Time Data Capture and Digital Records
Real-time data capture is one of the most powerful aspects of traceability. With the advent of smart technologies, manufacturers can continuously monitor product progress throughout the production lifecycle.
- Automated Sensors: Sensors embedded within machinery can capture data such as temperature, humidity, or pressure in real-time. This data can be used to ensure the product is being produced under the right conditions, preventing defects before they occur. For example, temperature sensors in a food manufacturing line can help maintain the quality of perishable goods by ensuring they remain within safe temperature ranges throughout production.
- Digital Records: Along with real-time data, digital record-keeping systems ensure that every action taken on the production floor is logged. From machine settings to operator input, every piece of information is stored digitally, creating a comprehensive trail that can be easily accessed when needed.
4.4 Documentation Flow Across Departments
Traceability doesn’t only rely on technology; it requires a seamless flow of documentation across departments. From manufacturing to quality control and logistics, every department must have access to accurate, timely data.
For example, in the medical device industry, production teams might log each batch’s specific details, including the raw materials used and the exact machinery settings. This documentation is passed to the quality control team for inspection results and then onto compliance departments to verify adherence to industry regulations.
This interdepartmental flow ensures that information is consistently shared and up to date, helping manufacturers quickly identify issues and take corrective actions.
5. Key Industry Examples
Traceability is not a one-size-fits-all solution—it plays very different roles depending on the industry. Below are a few major sectors where traceability is not just helpful but essential, each with their own reasons and implementation methods.
5.1 Automotive
In the automotive industry, traceability supports both safety and quality assurance. Manufacturers must be able to trace parts like airbags, brake systems, and sensors back to their production origins. If a failure is reported, engineers need to identify not only which supplier provided the part, but also which production lot it came from, who assembled it, and when.
This level of transparency enables:
- Rapid root cause identification
- Targeted recalls that avoid unnecessary disruption
- Compliance with global automotive standards like IATF 16949
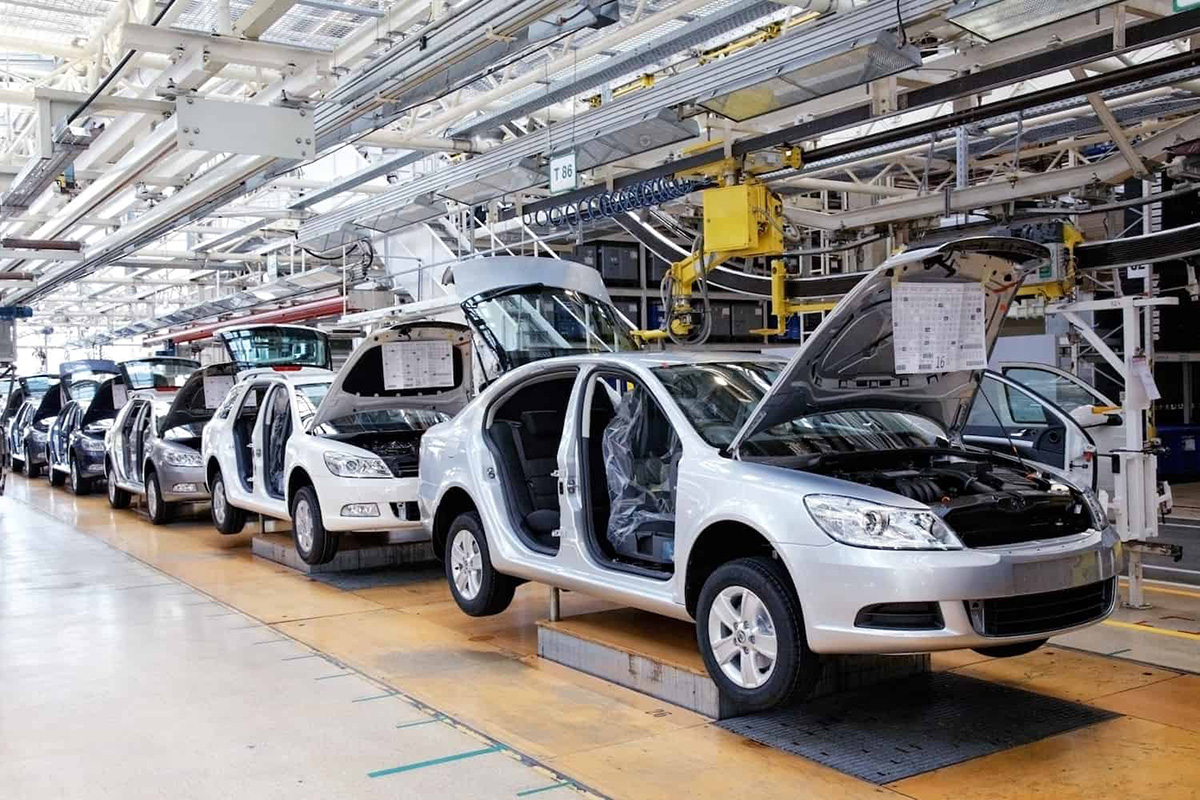
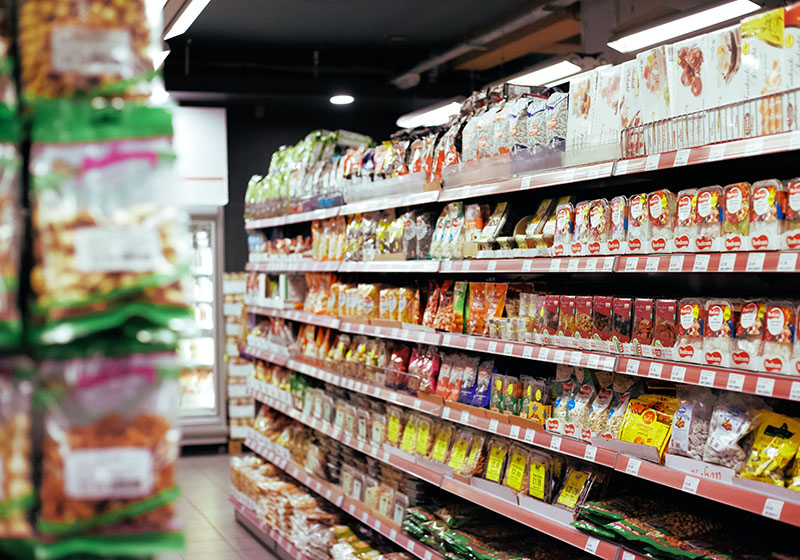
5.2 Food & Beverage
Food traceability focuses on batch-level tracking, which is especially important when dealing with contamination or expiration issues. In the case of a pathogen outbreak, companies need to recall only the affected lots, not entire product lines.
This industry typically uses:
- Barcode or lot number tracking on every packaged item
- Digital records that connect farm-to-fork data
- Integration with food safety frameworks such as HACCP and FSMA
5.3 Medical Devices
Traceability is strictly regulated here, with legal obligations enforced by agencies like the FDA. Every device must be linked to its full manufacturing history, including raw materials, machining processes, sterilization, and packaging.
Non-compliance doesn’t just result in fines—it can lead to loss of product approval or even patient harm. Manufacturers often use Unique Device Identifiers (UDI) and maintain records for up to 15 years, depending on risk classification.
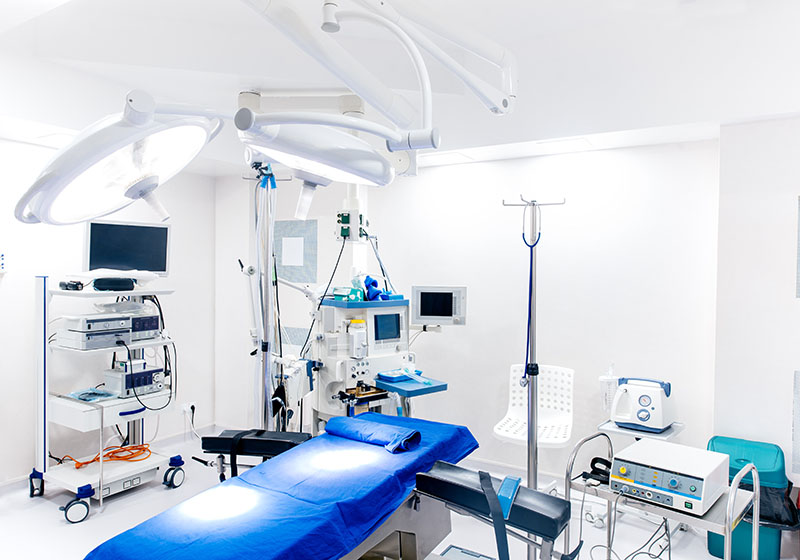
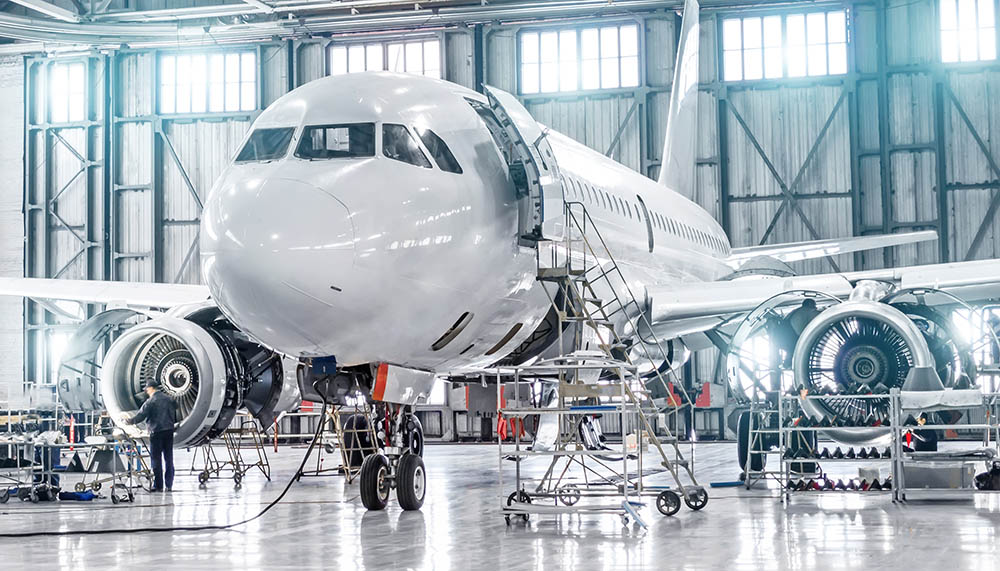
5.4 Aerospace
This is one of the most traceability-intensive sectors. Each aircraft part, no matter how small, must have a documented lifecycle. From turbine blades to fasteners, the system must show where the component came from, how it was tested, and when it’s due for maintenance or replacement.
Unlike most industries, aerospace traceability is essential even post-sale. Airlines and maintenance teams rely on historical records to make safety-critical decisions years after manufacturing.
6. Benefits of a Robust Traceability System
A well-implemented traceability system doesn’t just support compliance—it fundamentally strengthens the entire manufacturing operation. When properly integrated, it serves as a backbone for quality, responsiveness, and continuous improvement.
For manufacturers navigating high-stakes sectors like medical, aerospace, and automotive, traceability becomes a competitive asset, not just a technical tool.
Key benefits include:
- Enhanced Product Quality and Reliability
With the ability to trace each component back to its origin, manufacturers can enforce strict quality checks at every stage. Patterns of defects can be identified earlier, and corrective actions can be precisely targeted, improving consistency and reducing waste. - Faster Incident Response
When a defect or failure arises, companies with traceability can isolate the issue within hours—not days. This drastically reduces the financial and reputational damage of recalls, especially in safety-critical products. - Operational Efficiency Through Data
Traceability creates a rich pool of historical data. When paired with analytics tools, this data can highlight process inefficiencies, supply chain bottlenecks, and equipment issues before they escalate. - Stronger Position in Regulated Markets
In industries with heavy regulatory scrutiny, traceability systems provide a verifiable trail of compliance. Being able to show detailed production records builds trust with clients and auditors alike—and can open doors to new market segments that require such guarantees.
In short, robust traceability isn’t just about knowing what went wrong—it’s about building smarter, more resilient manufacturing from the ground up.
7. Implementing a Traceability System: Key Considerations
Introducing traceability isn’t just a matter of installing software—it requires thoughtful integration into your workflows, systems, and culture. Below are some essential aspects to consider when building or upgrading a traceability framework:
- Selecting the Right Tools
Your system should align with your production complexity. This may include MES (Manufacturing Execution Systems) for shop-floor control, ERP (Enterprise Resource Planning) for inventory and supply chain visibility, and QMS (Quality Management Systems) for compliance tracking. Choose platforms that support real-time data exchange and scale with your business. - Standardizing Data Collection Across Departments
Disparate departments often use different methods to log or label data. To ensure traceability is meaningful and accurate, unify your data input formats, barcode systems, and reporting structures. A lack of standardization leads to gaps or inconsistencies in trace data—especially during audits or investigations. - Ensuring People and Processes Are Aligned
Traceability is not just a technical upgrade—it’s also an operational shift. Staff must understand how their daily actions (labeling parts, logging materials, scanning shipments) contribute to the bigger picture. Cross-functional training and a shared commitment to documentation accuracy are critical to system success. - Aligning with Business Strategy, Not Just Compliance
A common mistake is to view traceability as a checkbox for regulatory compliance. In reality, it can drive broader business goals—from process optimization to customer satisfaction. Define what you want traceability to achieve beyond audits: faster recalls, better supplier oversight, or more accurate forecasting. - Starting Small, Then Scaling
For organizations without an existing system, a phased rollout often works best. Begin with a single product line or production step, validate the results, then extend traceability to upstream suppliers and downstream logistics. Trying to implement full-scale traceability in one go often leads to confusion and rework.
8. Digital Transformation and the Future of Traceability
Traceability is no longer just about scanning barcodes and storing batch numbers—it’s becoming a core pillar of digital manufacturing. As Industry 4.0 advances, traceability systems are evolving from reactive tools into predictive, intelligent networks.
- Industry 4.0 as the Backbone
Technologies like IoT, AI, and blockchain are reshaping traceability from the ground up. IoT sensors embedded in machines and products allow for continuous, automatic data capture without human input. AI can analyze that data in real time to detect anomalies or trends. Meanwhile, blockchain offers immutable, decentralized trace logs that enhance transparency—especially useful for industries requiring high trust and auditability. - From Monitoring to Predicting
Modern traceability systems don’t just show what happened—they help anticipate what might go wrong. By analyzing real-time production data, manufacturers can implement predictive maintenance, avoiding machine failures before they occur. Alerts can be triggered the moment deviations are detected, allowing operators to take immediate action and prevent defective output. - Cloud-Based, Scalable, and Global
Legacy systems often rely on localized databases and on-premise servers. In contrast, cloud-based platforms provide centralized access to traceability data across facilities, regions, or even countries. This global connectivity supports remote audits, supplier integration, and enterprise-wide analytics, all while reducing infrastructure costs and improving agility.
Looking ahead, traceability will be a key enabler of autonomous factories, adaptive quality control, and fully integrated supply chains. It’s no longer just a supporting function—it’s becoming a strategic advantage for digital-first manufacturers.
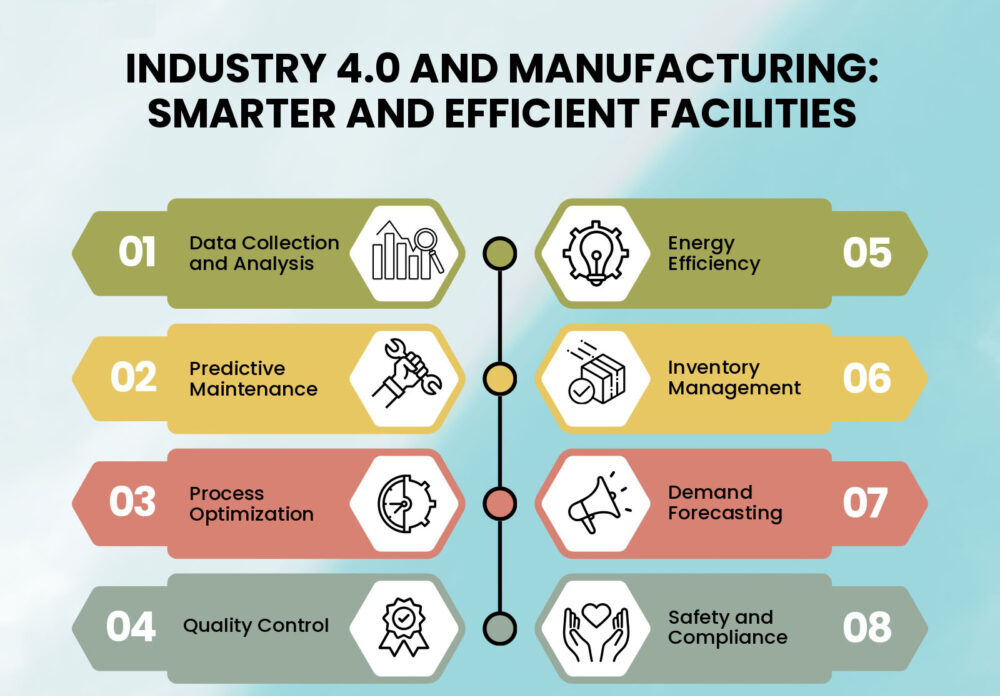
9. What Makes KingStar a Reliable Partner for Traceable Manufacturing
At KingStar, traceability isn’t an afterthought—it’s embedded in every stage of our injection molding process. With growing demands for quality, compliance, and transparency, we’ve positioned ourselves as a dependable partner for manufacturers seeking full visibility across production.
- Proven Experience in Highly Regulated Industries
We have extensive experience serving clients in automotive, medical devices, and consumer electronics—sectors where traceability is not optional but mandatory. Our familiarity with ISO, FDA, and IATF requirements allows us to implement systems that align with your regulatory expectations from day one. - End-to-End Traceability Integration
From tool design to final part delivery, our injection molding operations are built with traceability in mind. Each batch of materials, each production cycle, and every molded part is tracked using serial numbers, barcode systems, and digital logs. These records are integrated with our manufacturing execution system (MES) for real-time visibility. - Robust Documentation and Quality Systems
We maintain detailed documentation protocols for process validation, inspections, and corrective actions. Quality assurance is supported by automated data capture and traceable inspection points, ensuring that any deviation is flagged and addressed immediately. - Always-On Customer Support
Our support team operates 24/7 to assist with traceability-related requests—whether it’s tracking a specific component, reviewing quality records, or responding to a compliance audit. This responsiveness helps our clients reduce downtime, respond quickly to issues, and meet market demands without disruption.
With KingStar, you’re not just investing in parts—you’re investing in a transparent, accountable, and future-ready manufacturing partner.
Conclusion
Traceability in manufacturing is not just a luxury; it’s a critical requirement for ensuring product quality, compliance, and operational efficiency. As industries evolve, the ability to track materials and products throughout their entire lifecycle has become essential, not only for meeting regulatory standards but also for building customer trust and minimizing risks.
As the leading custom manufacturer, KingStar understands the importance of traceability in manufacturing. With our extensive experience in high-regulation sectors and our integration of advanced traceability tools in our injection molding processes, we help our clients maintain a transparent and efficient production environment. By implementing robust quality control protocols and offering 24/7 customer support, we ensure that your traceability systems are not only compliant but also optimized for operational excellence.
For manufacturers aiming to remain competitive and responsive, upgrading your traceability systems is a strategic move. At KingStar, we are ready to help you navigate the evolving landscape of traceability, safeguarding your operations and reinforcing your commitment to quality and accountability.