A-Side
Also known as the cavity side of a mold, it forms the exterior of a cosmetic part and typically does not have any moving parts.
Absenteeism
Refers to the failure of employees to attend work as scheduled, potentially leading to reduced productivity, increased expenses, and safety risks.
ACIS
A widely used computer file format for transferring CAD data, especially from AutoCAD programs. The acronym originally stood for “Andy, Charles, and Ian’s System.”
Activity-Based Costing System
A cost accounting method that assigns costs to specific activities in manufacturing, offering a more accurate reflection of production expenses.
Add-On Work
Additional tasks added to a maintenance schedule after the designated cutoff time.
Additive Manufacturing, 3D Printing
A process in which a three-dimensional object is created layer by layer from a CAD model or scan. Common techniques include stereolithography, selective laser sintering, fused deposition modeling, and direct metal laser sintering.
Advanced Planning and Scheduling System
A software tool used in manufacturing to optimize production schedules by utilizing real-time data, improving resource use, and enhancing efficiency.
Advanced Product Quality Planning
A methodology in manufacturing aimed at ensuring product quality by addressing potential issues during design, production, and delivery.
Agile Manufacturing
Refers to the strategies and tools that allow a company to adapt quickly to market changes or customer needs by reconfiguring operations and leveraging strategic partnerships.
Annual Total Inventory Turns
A metric used in manufacturing to measure how often a company’s inventory is sold and replaced over the course of a year, reflecting the efficiency of inventory management.
Approved Manufacturer List (AML)
A list of authorized third-party manufacturers and their parts that meet the company’s internal requirements, often compiled by the R&D team.
Approved Vendor List (AVL)
A compilation of suppliers that provide materials for a company’s production processes.
Asset Maintenance
Involves tracking and maintaining company assets to optimize their use and create value.
Asset Turnover
A financial ratio that indicates how effectively a company generates sales from its assets by dividing total sales by average total assets.
Assembly Line
A manufacturing process where parts are added to a semi-finished product as it moves sequentially from one workstation to another, speeding up production and reducing labor.
Axial Hole
A hole that runs parallel to the axis of a turned part, but not necessarily concentric with it.
Availability %
Represents the proportion of time a machine is available for production relative to the total planned production time, calculated through downtime data collected from alarms and operator inputs.
B-Side
Also known as the core side of a mold, it contains ejectors, side-action cams, and other components. On cosmetic parts, the B-side typically forms the interior of the part.
Barrel
The part of the injection-molding machine where resin pellets are heated, compressed, and melted before being injected into the mold’s runner system.
Barcoding
A data capture technology that enables rapid and accurate collection of information across various areas of a company’s operations, including manufacturing, inspection, transportation, and inventory management.
Bead Blasting
The process of applying abrasives with pressurized air to create a textured surface on a part.
Bevel
Also referred to as a “chamfer,” it is a flat, truncated edge or corner on a part.
Bill of Materials (BOM)
An extensive list of raw materials, components, and instructions needed to construct, manufacture, or repair a product or service.
Bill of Materials
In manufacturing, a bill of materials (BOM) is a comprehensive list of materials and parts required to complete a particular product.
Belt
The main component of a conveyor system, responsible for carrying materials. Made from flexible and durable materials like rubber, plastic, or metal, it forms a continuous loop that moves items through the system.
Benchmarking
A process used in manufacturing to compare a company’s products, services, and practices against industry leaders or competitors to identify best practices and improve performance and competitiveness.
Beverage Blush
A cosmetic imperfection that appears on a part where resin is injected, typically showing as a blotchy discoloration near the gate area.
Bottleneck
A point in the manufacturing process where production is slowed or limited due to constraints like material shortages, equipment downtime, or inefficiencies, leading to reduced productivity and increased costs.
Boss
A raised stud feature on a part designed to accommodate fasteners or support other parts passing through them.
Bridge Tool
A temporary mold used to produce parts while awaiting a high-volume production mold to be completed.
Breakdown
Equipment that fails to operate and is considered unusable due to mechanical failure.
Breakdown Maintenance
The process of repairing equipment that has failed and is no longer functional, returning it to operational status.
Bumpoff
A feature in a mold that creates an undercut, requiring the part to bend or stretch to eject from the mold.
Build Platform
The base support of an additive manufacturing machine where parts are constructed. The maximum part size depends on the platform’s dimensions, and it can accommodate multiple parts of different geometries.
CAD (Computer-Aided Design)
A technology that utilizes software to design, modify, and optimize products or components digitally. CAD plays a pivotal role in reducing the time and cost associated with product development, enabling rapid prototyping and testing.
CAM (Computer-Aided Manufacturing)
This refers to the software-driven automation of manufacturing processes. CAM enhances production efficiency and precision by directly linking design data from CAD to manufacturing systems, improving both productivity and consistency.
CAPA(Corrective Action/Protective Action )
A methodology for identifying and resolving product failures through both corrective and preventive actions, ensuring that future issues are minimized or eliminated.
Cavity:
The space between the A-side and B-side of a mold that gets filled with molten resin to form the molded part. The cavity is integral to the creation of the final product, shaping its exterior.
Chamfer
A beveled or truncated edge, often applied to parts to eliminate sharp corners, which can prevent damage during assembly or use.
Clamp Force
The amount of force required to securely close the mold and prevent material from leaking out during injection. The clamp force is essential for ensuring the consistency and integrity of the molded part.
Contoured Pins
Ejector pins designed to match the specific contours of the part’s surface. These pins are vital for smooth part ejection, particularly in designs with sloped or irregular surfaces.
Core
A component placed within a mold to form the hollow interior of a part. Typically located on the B-side, it is essential for creating internal features like cavities or channels.
Core Pin
A pin used in the mold to create internal voids within the part. These are often separate from the core itself and are inserted into either the A-side or B-side of the mold.
Core-Cavity
A term describing a mold system created by joining the A-side and B-side mold halves, where the core side creates the internal features and the cavity side shapes the outer form.
Cycle Time
The total time it takes to complete one production cycle, from the moment the mold closes, the material is injected, the part solidifies, the mold opens, and the part is ejected.
Cell
In manufacturing, a “cell” refers to a small, self-contained unit of equipment or workers designed to handle a specific task or set of tasks. The goal is to streamline production and improve flow efficiency by minimizing bottlenecks.
CMM (Coordinate Measuring Machine)
A tool used to measure the physical geometrical characteristics of an object. Often used for high-precision manufacturing, the CMM ensures parts meet exact specifications.
Center Drive & Take-up
This conveyor system uses a central motorized pulley to drive the belt, with a take-up system to maintain tension and prevent sagging, crucial for maintaining a steady flow in manufacturing processes.
Cellular Manufacturing
This lean manufacturing technique organizes production into “cells,” where machines and workers are grouped to optimize workflow and reduce lead time. The aim is to streamline processes and increase efficiency.
Change Management
A structured approach to managing engineering changes, ensuring that revisions to a product or process are systematically planned, reviewed, and approved to avoid errors and delays.
Change Request
A formal document proposing changes to a product or process to resolve identified issues. Change requests may involve documentation, engineering, field failures, or supplier-related adjustments.
Changeover
The process of setting up manufacturing equipment for a new product or production run. This involves adjusting machinery, cleaning, and verifying that everything is configured for optimal performance.
Compliance
Ensuring products meet both regulatory and internal standards. It includes adhering to industry regulations such as RoHS for electronics or FDA standards for medical devices.
Compliance Mark
A certification label affixed to products or packaging to indicate compliance with specific regulations, such as UL, CE, or FCC certifications.
Computer-Aided Process Planning (CAPP)
A technology that optimizes the planning phase of manufacturing by selecting the best methods, tools, and equipment for production based on detailed design specifications.
Computer-Integrated Manufacturing (CIM)
A comprehensive manufacturing approach that integrates various functions—such as design, production, and quality control—through computer systems to enhance overall efficiency and coordination.
Computerized Maintenance Management Systems (CMMS)
Software solutions used to track, schedule, and manage maintenance activities, ensuring equipment reliability and reducing downtime through proactive monitoring and reporting.
Computerized Process Simulation:
Simulating manufacturing processes digitally to predict outcomes and optimize systems before actual production begins. This approach allows manufacturers to identify inefficiencies and reduce risks.
Computerized Statistical Process Control (SPC)
A quality control method that uses real-time data to monitor and improve manufacturing processes. It helps detect defects early by analyzing statistical trends and variations.
Concurrent Engineering
An approach where product design and manufacturing processes are developed simultaneously to reduce time-to-market, improve product quality, and enhance collaboration across departments.
Continuous-Replenishment Programs
Supply chain strategies that automatically replenish inventory based on real-time data, improving efficiency and reducing the risk of stockouts or overstocking.
Contract Manufacturer (CM)
A third-party company hired to produce goods or components on behalf of another company. This arrangement helps businesses scale production without investing in their own manufacturing facilities.
Conveyor
A mechanical system used to move goods or materials from one point to another in production or packaging lines. Conveyors increase operational efficiency by automating material handling.
Core Competency
A company’s key capabilities and strengths that contribute to its competitive advantage in the market. These competencies are integral to the firm’s success and long-term sustainability.
Corrective Action Request (CAR)
A formal request issued when a defect or problem is identified in a product, outlining corrective measures to address the issue and prevent recurrence.
Cost of Quality
A measure that calculates the costs associated with ensuring that products meet quality standards. This includes prevention, appraisal, and failure costs, helping manufacturers track their investment in quality management.
Cpk (Process Capability Index)
A statistical measure used to assess the consistency of a manufacturing process, evaluating whether it can produce products within specified tolerances without defects.
Cross-Functional Teams
Teams made up of individuals from various departments, such as engineering, manufacturing, and marketing, who work together to tackle problems and innovate solutions across the organization.
Cross-Training
A practice where employees are trained in multiple job functions, increasing flexibility and enhancing operational efficiency by allowing workers to cover for each other.
Customer Leadtime
The time from receiving an order to delivering the finished product to the customer. It is a critical factor in customer satisfaction and inventory management.
Customer Reject Rate (PPM)
This metric measures the number of parts per million that are rejected by customers due to defects, serving as a critical quality indicator.
Customer Retention Rate
The percentage of customers who continue to purchase from a company over time, often calculated over a three-year period, and is a key measure of customer loyalty.
Design for Assembly
The practice of designing products to simplify and reduce assembly time and costs. The aim is to enhance efficiency in the assembly process and minimize the steps required to put together the final product.
Design for Logistics
Optimizing product design to facilitate easy transportation, storage, and distribution. The goal is to reduce logistics costs while ensuring the product can be moved and delivered without difficulties.
Design for Manufacturability
Designing products with manufacturing ease and cost-effectiveness in mind. The objective is to ensure that the product is easy to produce, maintain high quality, and is cost-efficient to manufacture.
Design for Procurement
Collaborating with suppliers and sourcing teams during product design to use standardized components, reduce procurement costs, and ensure efficient material flow across multiple products.
Design for Quality
Incorporating quality assurance into the design process to ensure that products meet or exceed customer expectations. The goal is to enhance product reliability and value from the start.
Design for Recycling/Disposal
Considering the end-of-life stage of a product during design, with a focus on making it easy to recycle or dispose of in an environmentally friendly way. The aim is to reduce waste and environmental impact.
Design of Experiments
A method used to determine optimal product and process parameters through a controlled set of experiments. The goal is to identify critical variables that impact quality and reduce process variability.
Discrete Manufacturing
The production of distinct parts or products that are identifiable and measurable. These products are often labeled with serial numbers and produced in quantities, focusing on efficiency and quality.
Direct Metal Laser Sintering (DMLS)
A process using a fiber laser to fuse metal powder into solid parts, layer by layer. The process repeats with each layer until the final metal component is completed.
Direction of Pull
The path that mold surfaces follow as they move away from the part, whether during the mold’s opening or part ejection process.
Draft
A slight taper on the part’s surfaces designed to prevent them from being parallel to the mold’s opening direction. This reduces the risk of part damage during ejection.
Drying of Plastics
Plastics that absorb moisture must be dried before injection molding to preserve material properties and ensure a high-quality finish.
Durometer
A measure of material hardness, rated on a numeric scale where lower values represent softer materials and higher values indicate greater hardness.
Downtime
The period when a machine, production line, or facility is non-operational and not producing products, often due to maintenance or operational issues.
Days of Inventory
A metric to calculate how many days a company’s inventory can sustain production, considering raw materials, work-in-progress, and finished goods inventory.
Demand-Driven Scheduling Systems
Software systems that adapt manufacturing processes based on real-time demand, ensuring production aligns with customer orders to meet deadlines.
Economic Value Added (EVA)
A metric used to evaluate the wealth created for shareholders by an investment center, assessing financial performance beyond basic profitability.
Electronic Data Interchange (EDI)
A system for exchanging business documents like purchase orders and invoices electronically between companies, eliminating manual input and reducing errors.
Empowered Natural Work Teams
Teams responsible for specific processes or segments within manufacturing. These teams are empowered to implement process improvements and ensure quality while managing production schedules.
Enterprise Integration (EI)
The use of information technology to link various functional areas of a business and integrate external partners. In manufacturing, it connects systems such as CIM, inventory management, and financial decision-support.
Enterprise Resource Planning (ERP)
A system that integrates various business functions, including production, supply chain, finance, and human resources, to streamline operations across multiple locations.
Expert Systems
Software that mimics the expertise of professionals in a specific field, providing guidance and decision-making support for less experienced personnel.
Extranet
A secure network that connects external partners like customers and suppliers to an organization’s internal system, enabling controlled access to shared information.
Edge Gate
A mold gate located along the parting line, allowing resin to flow into the mold cavity. Typically placed at the outside edge of the part.
EDM (Electric Discharge Machining)
A method for creating intricate shapes and details in moldmaking, capable of forming thin ribs, text, and precise edges, especially where milling isn’t effective.
Ejection
The process of removing the molded part from the mold once it has cooled, usually facilitated by pins or other ejection mechanisms.
Ejector Pins
Pins installed on the B-side of the mold that push the part out after cooling to facilitate removal.
Elongation at Break
A material property indicating how much it can stretch before breaking, essential for some parts that need to be removed from molds. For example, LR 3003/50 has a 480% elongation at break.
End Mill
A cutting tool used in machining molds, allowing for precise shaping and detailing of the mold cavity.
ESD (Electrostatic Discharge)
The transfer of electrical charge that may require mitigation in certain applications. Some plastics, especially specialized grades, are conductive or dissipative to reduce ESD.
Family Mold
A mold designed with multiple cavities to produce several parts made from the same material in a single cycle. Each cavity typically forms a different part number, streamlining production.
Fillet
A curved edge where a rib meets a wall, designed to enhance material flow and reduce mechanical stress on the final part.
Finish
A surface treatment applied to the part, varying from smooth, polished finishes to textured patterns. It enhances aesthetics, hides imperfections, or improves the part’s feel.
Flame Retardant
A material or resin formulation that is resistant to burning, designed to increase fire safety.
Flash
Unwanted resin that escapes through small gaps in the mold’s parting lines, creating a thin layer of excess plastic or silicone rubber.
Flow Marks
Visible lines or patterns on a molded part that indicate the movement of material as it flows into the mold before solidifying.
Food Grade
Resins or coatings approved for use in parts that will come into contact with food, ensuring safety in food-related applications.
Fused Deposition Modeling (FDM)
A 3D printing process where a material wire coil is extruded layer by layer to form solid, three-dimensional objects.
Finished Goods
Products that have completed all production stages and are ready for distribution to customers. Tracking finished goods helps manufacturers prevent overproduction and assess profitability.
Flexible Conveyor
A conveyor system that can expand or contract to fit specific needs, typically made up of interconnected rollers or skate wheels, allowing for easy movement and adjustment.
Finished-Goods Turn Rate
A metric used to measure how efficiently finished goods are sold or shipped, calculated by dividing the value of annual shipments by the average inventory of finished goods.
Finite Capacity Scheduling
Software systems that simulate production schedules, providing accurate delivery dates based on the real capacity available at each stage of the production process.
Finite Element Analysis (FEA)
A computational technique used in product design to analyze the behavior of a product under various load conditions, helping assess stress and potential failure points.
First-Pass Yield
A measure of quality, indicating the percentage of products that pass all quality checks without needing rework or adjustments after the first attempt.
Flexible Assembly Systems
Systems incorporating automated assembly equipment or cross-trained teams, designed to adapt to different product configurations produced in small batches.
Flexible Machining Systems
Automated machining tools that can be easily reprogrammed to handle different products or component configurations in small, versatile production runs.
Flexible Manufacturing System (FMS)
A system composed of automated manufacturing equipment and cross-trained workers designed to produce a variety of parts in small quantities efficiently.
Focused-Factory Production
A production setup that creates “mini-businesses” within a plant, each focusing on a specific product line or customer need, optimizing efficiency and specialization.
Forecast/Demand Management Software
Software that aids in master production scheduling by analyzing historical demand trends, sales promotions, and other variables to optimize inventory and planning.
Gate
The part of the mold where resin enters the cavity, initiating the injection molding process.
GF (Glass-Filled)
A resin mixed with glass fibers, increasing strength and rigidity compared to unfilled resins. However, glass-filled resins tend to be more brittle.
Gusset
A triangular rib designed to reinforce weak areas, such as a wall to a floor or a boss to a floor, adding strength and stability.
Good Manufacturing Practice (GMP)
A set of guidelines ensuring proper management of production and testing processes that affect product quality. These practices are crucial for producing safe pharmaceuticals, food products, medical devices, and other regulated items.
Gravity Conveyor
A conveyor system utilizing gravity to move materials along an incline or decline. It typically uses rollers or skate wheels to transport products without external power.
Hot Tip Gate
A specialized gate that injects resin directly into a face on the A-side of the mold, eliminating the need for a runner or sprue.
HMI (Human-Machine Interface)
The interface connecting a human user to a machine, allowing operators to interact with and control machines. For instance, the Mingo platform includes an HMI for machine operators to input data during production.
IGES
Initial Graphics Exchange Specification. A widely used file format for transferring CAD data, enabling companies like Protolabs to create molded parts from IGES solid or surface files.
Injection Molding
The process of forcing molten resin into a mold to form the desired part.
Insert Molding
A part of the mold installed either permanently after machining the mold base or temporarily between mold cycles to modify mold geometry.
IoT (Internet of Things)
A system of interconnected smart devices. In manufacturing, IoT supports remote monitoring, predictive maintenance, smart asset management, and autonomous production.
IIoT (Industrial Internet of Things)
The use of advanced technologies in the industrial sector to create a smart factory, integrating machinery, analytics, and operators to enhance manufacturing efficiency.
In-Plant Defect Rate
The ratio of defective components that fail quality tests during production, often expressed as parts per million (ppm).
Inventory Turn Rate
A metric to assess asset management efficiency by measuring how quickly inventory is used or replaced within a set period.
ISO 9000
An international quality management standard for assessing processes and certifying that manufacturing plants comply with their defined quality practices.
ISO 13485
Quality management standards specifically tailored for the development and manufacturing of medical devices.
ISO 14000
Environmental management system standards aimed at reducing the environmental impact of manufacturing operations.
Jetting
Flow marks created when resin enters a mold at high speed, often occurring near a gate.
JIT/Continuous-Flow Production
A production system that utilizes “just-in-time” principles to minimize lot sizes, setup times, work-in-process inventory, waste, and cycle time, while improving throughput. It uses “pull” signals triggered by customer orders or shipment dates to initiate production, as opposed to the “push” method based on forecasted demand.
JIT Delivery
The practice of delivering parts and materials in small, frequent lots, timed to align with the production system’s immediate needs.
Kaizen
A structured approach to process improvement involving individuals directly engaged in the processes. It emphasizes continuous improvement and the immediate action-oriented mindset through simple analysis techniques.
Kaizen Event
A focused effort, usually spanning several days, where a team plans and implements significant process changes leading to notable performance improvements. It involves participants from various areas of the organization, including non-production staff.
Kanban Signal
A communication method used in just-in-time systems to signal that it is time to replenish inventory of components or subassemblies. Traditionally using cards in Japan, today it includes methods such as empty containers or electronic messages.
Kitting
A process where all parts needed for assembling a product are grouped into a kit. This reduces inventory movement and places the kit directly at the production point where it will be used.
Knit Lines
Also known as “stitch lines” or “weld lines,” and “meld lines” when multiple gates are involved. These imperfections occur where separated flows of cooling material meet and rejoin, often leading to incomplete bonds and visible lines on the part.
Labor Turnover Rate
A measure of a plant’s ability to retain workers, expressed as the percentage of the workforce that departs annually, regardless of reason (e.g., layoff, quit, retirement). High turnover rates may signal employee dissatisfaction with working conditions or compensation.
Layer Thickness
The precise thickness of a single additive layer, which can be as thin as microns. Parts typically contain thousands of such layers.
Lean Manufacturing
A practice focused on reducing wasted time, effort, and resources in the production process while maintaining productivity and efficiency. It emphasizes that cutting waste can be more profitable than increasing sales.
LIM (Liquid Injection Molding)
The process used for molding liquid silicone rubber (LSR).
Lineshaft
A conveyor system where a long rotating shaft runs beneath the length of the conveyor, powering a series of rollers through belts or chains, driven by a motor at one end to move the product along.
Live Tooling
Machining actions in a lathe where rotating tools remove material from stock, enabling features like flats, grooves, slots, and holes to be created within the lathe.
Living Hinge
A thin section of plastic that connects two parts while allowing them to open and close. Proper design and gate placement are critical for functionality. Commonly used in products like the top and bottom of boxes.
LSR (Liquid Silicone Rubber)
A type of silicone rubber used in molding processes, commonly for flexible, durable parts.
Machine Availability
The amount of time a machine is available for product production, usually expressed as a percentage of total planned production time.
Machine Vision
A system where optical equipment guides robotic or automated equipment, or is used in visual inspection for quality control.
Make to Assemble (MTA)
A production process where parts are pre-made but the final assembly is deferred until an order is received, allowing for some customization.
Make to Order (MTO)
A manufacturing process where a product is made only after a customer places an order, often involving highly personalized products.
Make to Stock (MTS)
A strategy where products are made in advance and stocked to meet anticipated customer demand, relying on accurate forecasts to manage inventory.
Manufacturing Cost
The total costs involved in manufacturing operations, including labor, equipment, maintenance, and quality control, but not including non-production costs like sales.
Manufacturing Cycle Time
The time taken to complete the production of a product, from the release of the customer order to completion of manufacturing, assembly, and testing.
Manufacturing Deviation
A temporary change in the production process, such as using a substitute part. It can be planned or unplanned.
Manufacturing Execution System (MES)
Software that connects planning and administrative systems to the production floor, handling scheduling, tracking, quality management, and other tasks.
Manufacturing Order
Documents authorizing the manufacture of parts or products in specified quantities. Also known as production orders, shop orders, or work orders.
Manufacturing Order Receipt
A document where the costs of materials, labor, and machine time are applied to finished goods upon receipt into inventory.
Manufacturing Order Routing
A set of instructions specifying all the necessary resources (workers, machines, raw materials) to complete a manufacturing order.
Manufacturing Picklist
A list of items and quantities required to fulfill a manufacturing order.
Mean Time Between Failures (MTBF)
A KPI measuring the time between failures of machinery or equipment, helping assess reliability.
Mean Time Between Repairs (MTBR)
A KPI indicating the average time equipment operates between breakdowns.
Mean Time to Repair (MTR or MTTR)
A KPI that calculates the average time required to repair failed equipment and restore it to normal operation.
Manufacturing Resources Planning (MRP II)
Systems that link forecasts to production schedules, track inventory, generate work orders, and manage materials and resources for production.
Motorized Roller Chain
A type of conveyor system that uses motorized rollers connected by a continuous chain to transport products. Ideal for heavy loads and easy maintenance.
MRP Shortage
A situation where there are insufficient resources to meet production requirements, despite entering manufacturing orders. It can occur when material stock is low.
Net Shape
The final shape of a part that requires no additional processing before use.
Nozzle
The tapered component at the end of the injection-molding press barrel, where resin flows into the sprue.
North American Industry Classification System (NAICS)
A system used by the U.S., Mexican, and Canadian governments to categorize economic sectors. It replaced the U.S. Standard Industrial Classification (SIC) system, with codes for manufacturers falling within numbers 31 through 33.
Natural Work Team
A team of employees, usually hourly workers, who collaborate in a shared workspace and are jointly responsible for a specific process or portion of a production task.
OEE – Overall Equipment Effectiveness
This is a prominent metric used in the manufacturing industry to evaluate the effectiveness of machines. It measures availability, performance, and quality, and these factors are multiplied together using a formula developed by Toyota to obtain a single metric. OEE plays a crucial role in the production of goods, and it is important for manufacturers to understand its significance.
OFC – Operational Technology (OT)
Refers to the software used by personnel on the factory floor to control and adjust machine processes in a plant or factory. For example, the software may regulate the use of valves or pumps.
Online Order Entry System
This is a computer-based tool that allows distributors, field sales representatives, and even customers to place orders directly, via the internet or a corporate intranet, without the need for an inside salesperson to intervene. Users may access a designated webpage, select a sales-order-entry option, and the system often includes a product configurator and pricing engine, which may also be linked to production scheduling systems.
On-Time Delivery Rate
The on-time delivery rate is the percentage of products ordered by customers that are delivered by the specified time or date.
On-axis Hole
This is a hole that is concentric to the axis of revolution of the turned part. It is simply a hole on the end of a part and in the center.
Open Platform Communications (OPC)
A set of standards used for industrial telecommunications. According to Wikipedia, it specifies the “communication of real-time plant data between control devices from different manufacturers.”
Occupational Safety and Health Administration (OSHA)
This is a United States government agency that is responsible for ensuring safe and healthy working conditions for employees. OSHA was created in 1970 through the Occupational Safety and Health Act, and it sets and enforces safety standards, provides training and education, and conducts inspections to ensure that employers are following safety regulations.
Off-the-Shelf
This is an item that is procured from a supplier as-is, with no modifications.
Operation Code
Operation codes define the various processes that are performed to manufacture the final product or parent item.
Overflow
A mass of material away from the part, typically at the end of fill, connected by a thin cross-section. The overflow is added to improve part quality and is removed as a secondary operation.
Order Fill Rate
Annual sales orders filled completely divided by the total annual number of sales orders.
Order-To-Delivery Leadtime
The time from when a specific customer order is received by the plant until the product is delivered to the customer, including any warehousing, cross-docking, and transportation time.
Order-To-Shipment Leadtime
The time from when a specific order is released to the shop floor until that order is shipped to the customer, including any storage time in finished goods inventory.
Original Equipment Manufacturer (OEM)
The original manufacturer of a product that may be sold or marketed by another company.
Packing
This refers to applying increased pressure when injecting a part to force more plastic into the mold, typically to address sink or fill issues. However, this practice may increase the likelihood of flash and cause parts to stick in the mold.
Parasolid
A file format used for exchanging CAD data between different software applications, enabling seamless collaboration in design processes.
Part A/Part B
In Liquid Silicone Rubber (LSR) molding, Part A and Part B are two separate compounds kept distinct until the molding process begins, where they are mixed to form the final part.
Parting Line
The edge of a part where the mold separates during the ejection process.
Pickouts
A mold insert that becomes stuck to the ejected part and must be removed and placed back into the mold for the next cycle.
PolyJet
A 3D printing technology where liquid photopolymer droplets are sprayed and cured in layers to form elastomeric parts.
Porosity
Undesired voids within a part, which can occur in various shapes and sizes, weakening the part’s strength.
Post Gate
A specialized gate that uses a hole through which an ejector pin passes to inject resin into the mold cavity, leaving a post vestige that needs to be trimmed.
Press
An injection molding machine used for producing plastic parts.
Pareto
The Pareto principle, or 80/20 rule, indicates that 80% of consequences come from 20% of causes, such as identifying the top issues affecting machine downtime in manufacturing.
Performance %
A measure of performance that compares the actual cycle time to the ideal cycle time, reflecting a machine’s ability to meet production goals.
PLC – Programmable Logic Controller
An industrial computer that automates and controls manufacturing processes, such as assembly lines, machines, and robotic devices.
Poka-Yoke
A mistake-proofing technique used in Lean manufacturing to prevent errors and defects, aiming to reduce the need for rework and improve quality.
Pallet Pro
Refers to products and services related to pallets, such as manufacturing equipment or software for pallet management.
Parent Item
A parent item contains another item (child item) within its bill of materials, typically in an assembly or subassembly relationship.
Part Name
A unique designation given to a part.
Part Number
A unique numerical identifier assigned to a part.
Pathway™ Lineshaft
A type of roller conveyor system that uses a central shaft to drive multiple rollers, offering efficient operation and reduced maintenance.
Pick-To-Ship Lead Time
The time from when an order is released for picking from inventory until it is shipped to the customer.
Technologies For Planning And Scheduling
Software systems used for advanced planning, scheduling, and optimization in manufacturing.
Planned Maintenance (PM)
Scheduled maintenance tasks aimed at reducing equipment failure, performed while the equipment is still in operation.
Planned Maintenance Optimization
Improving maintenance strategies by evaluating current preventive maintenance routines and failure history.
Planned Maintenance Percentage (PMP)
The percentage of maintenance time dedicated to planned tasks versus total maintenance hours within a specified time period.
Poka-Yoke
Techniques used in production to eliminate defects by preventing or correcting human errors, ensuring higher quality outcomes.
Pop-Up Transfer
A conveyor system component that allows smooth transfer of products between conveyor lines by raising or lowering a section of the conveyor belt.
Power Conveyor
A conveyor system powered by motors to move products or materials, often used in manufacturing and distribution for efficiency.
Power Feeder
A device in conveyor systems that ensures a controlled flow of material onto a conveyor belt at a set rate.
Precision Maintenance
Maintenance carried out with accuracy and consistency according to industry best practices.
Predictive Maintenance (PdM)
A maintenance strategy based on monitoring equipment with sensors to predict when maintenance will be required, minimizing downtime.
Premium Freight
An expedited shipping method used to meet urgent delivery deadlines, often incurring higher transportation and labor costs.
Preventive Maintenance (PM)
Routine maintenance to prevent unexpected equipment breakdowns, performed while the equipment is still functioning.
Programmable Logic Controller (PLC)
An industrial computer used for automating manufacturing processes, controlling machines, and diagnosing faults.
Proactive Environmental Practices
Advanced environmental practices implemented voluntarily by plant management to reduce pollutants and environmental impacts before regulations are enforced.
Problem-Solving Methodologies
Approaches to resolving issues within an organization, such as the Deming Circle (Plan-Do-Check-Act), focused on teamwork and process improvement.
Process Manufacturing
The production of products in batch quantities, such as chemicals or food items, that cannot be separated into distinct units.
Product Data Management (PDM)
Software systems that manage and organize product-related data, streamlining design processes and enhancing communication across teams.
Product Development Cycle
The period from design and development to the commercial availability of a product, also known as “time to market.”
Productivity Change
The change in value-added per employee within a year, used to measure overall productivity improvements.
Process Manufacturing
A production method for creating products in batches, where the final product cannot be separated into its raw materials.
Pull System
A system that controls workflow based on demand, where resources are pulled from feeding processes as needed rather than pushed in advance.
Quality %
This term refers to the quality of the products being manufactured by a machine. To determine this quality, manufacturers rely on a set of key performance metrics. By using manufacturing analytics, it’s possible to assess product quality by tracking the quantity of produced parts and reasons for any defects, while supplementing this data with feedback from human operators.
Quality Function Deployment (QFD)
QFD is a technique focused on identifying and analyzing customer needs at the early stages of product design. The purpose is to transform these customer requirements into specific product and process specifications, ensuring that suppliers meet or exceed these expectations in the final product.
Quick-Changeover Methods
This refers to a group of strategies that aim to reduce the time required to change equipment or production setups. Techniques such as SMED (single-minute exchange of dies) are employed to improve equipment flexibility, minimize lot sizes, and decrease lead times.
QS 9000
QS 9000 is a quality standard certification used primarily by automotive suppliers. It builds upon the basic principles of ISO 9000 but includes additional requirements that are specific to the automotive industry to ensure product quality and reliability.
Radial Hole
A hole formed by live tooling that is perpendicular to the axis of revolution of a turned part, which could be considered a side hole. The center line of these holes is not required to intersect the axis of revolution.
Radiused
An edge or vertex that has been rounded. Typically, this occurs on part geometries as a natural result of the milling process. When a radius is intentionally added to an edge on a part, it is referred to as a fillet.
Ram
A hydraulic mechanism that pushes the screw forward in the barrel and forces resin into the mold.
Recess
An indentation in the plastic part caused by the impact of the ejector pins.
Reinforced Resin
Refers to base resins with fillers added for strength. They are particularly susceptible to warp because the fiber orientation tends to follow flow lines, resulting in asymmetric stresses. These resins are typically harder and stronger but also more brittle (e.g., less tough).
Resin
A generic name for chemical compounds that, when injected, form a plastic part. Sometimes just called “plastic.”
Resolution
The degree of detail achieved in parts produced via additive manufacturing. Techniques such as stereolithography and direct metal laser sintering enable the creation of highly detailed parts with minute features.
Rapid Prototyping
A set of methods used to swiftly turn CAD-designed products into precise physical models, often using computer-controlled systems. One example is stereolithography, where lasers, directed by CAD data, solidify liquid resins layer by layer to create detailed plastic models.
Return On Invested Capital (ROIC)
A measure of how effectively a company uses the money (borrowed or owned) invested in its operations. It is calculated as net operating profit after taxes divided by capital invested.
Rib
A thin, wall-like feature parallel to the mold opening direction, common on plastic parts and used to add support to walls or bosses.
Runner
A channel that resin passes through from the sprue to the gate/s. Typically, runners are parallel to, and contained within, the parting surfaces of the mold.
Raw-Materials Turn Rate
A metric used to measure asset management by dividing the value of total annual shipments at plant cost by the average raw-material value at plant cost. This includes material, labor, and plant overhead.
Real-Time Feedback
The instantaneous communication of electronically captured data, such as quality data, to process operators or equipment to enable rapid or automated adjustments that keep production processes operating within quality parameters.
Redline
The marking of an assembly drawing or bill of materials (BOM) to indicate a modification.
Rolled-Throughput Yield (Multiple-Point Yield)
A measure that multiplies quality yield values at various points in a production process, not just at the end of the line. This helps to make problem areas within a process more visible.
Safety Improvement Programs
These are practices implemented to continuously enhance safety within a plant or across a company. These may include safety teams, safety awareness programs and communications, safety training, safety “days,” and setting continuous improvement goals that target safety metrics such as OSHA incidents or lost-workday rates.
Screw
A component within the barrel that compacts resin pellets, applying pressure and heat to melt them before injection into the mold.
Selective laser sintering (SLS)
During the SLS process, a CO2 laser draws onto a hot bed of thermoplastic powder, where it lightly sinters (fuses) the powder into a solid. After each layer, a roller lays a fresh layer of powder on top of the bed and the process repeats.
Shear
The force between layers of resin as they slide against each other or the surface of the mold. The resulting friction causes some heating of the resin.
Short shot
A part that wasn’t completely filled with resin, causing short or missing features.
Shrink
The change in part size as it cools during the molding process. This is anticipated based on material manufacturer recommendations and built into the mold design before manufacturing.
Shutoff
A feature that forms an internal through-hole in a part by bringing the A-side and B-side in contact, preventing the flow of resin into the through-hole.
Side-action
A section of the mold that is moved into position when the mold closes, usually by a cam-driven slide. Side-actions are primarily used to address undercuts or allow for undrafted outer walls. When the mold opens, the side action retracts, facilitating part ejection. It is also referred to as a “cam.”
Sink
Dimples or other distortion in the surface of the part as different areas of the part cool at different rates. These are most commonly caused by excessive material thickness.
Splay
Discolored, visible streaks in the part, typically caused by moisture in the resin.
Sprue
The first stage in the resin distribution system, where the resin enters the mold. The sprue is perpendicular to the parting faces of the mold and brings resin to the runners, which are typically in the parting surfaces of the mold.
Steel pins
A cylindrical pin for formatting high-aspect-ratio, small-diameter holes in a part. A steel pin is strong enough to handle the stress of ejection and its surface is smooth enough to release cleanly from the part without draft.
Steel safe
Also known as “metal safe” (the preferred term when working with aluminum molds). This refers to a change to the part design that requires only the removal of metal from the mold to produce the desired geometry. Typically most important when a part design is changed after the mold has been manufactured, because then the mold can be modified rather than entirely re-machined.
STEP
Stands for Standard for the Exchange of Product Model Data. It is a common format for exchanging CAD data.
Stereolithography (SL)
SL uses an ultraviolet laser focused to a small point to draw on the surface of a liquid thermoset resin. Where it draws, the liquid turns to solid. This is repeated in thin, two-dimensional cross-sections that are layered to form complex three-dimensional parts.
Sticking
A problem during the ejection phase of molding, where a part becomes lodged in one or the other half of the mold, making removal difficult. This is a common issue when the part is not designed with sufficient draft.
Stitch lines
Also known as “weld lines” or “knit lines,” and when multiple gates are present, “meld lines.” These are imperfections in the part where separated flows of cooling material meet and rejoin, often resulting in incomplete bonds and/or a visible line.
STL
Originally stood for “STereoLithography.” It is a common format for transmitting CAD data to rapid prototyping machines and is not suitable for injection molding.
Straight-pull mold
A mold that uses only two halves to form a cavity that resin is injected into. Generally, this term refers to molds with no side-actions or other special features used to resolve undercuts.
Tab gate
An opening aligned with the parting line of the mold where resin flows into the cavity. These are also referred to as “edge-gates” and are typically placed on an outside edge of the part.
Takt Time
The optimal frequency of production required to meet customer demand, calculated by dividing the available work time per shift by actual customer demand.
Tear Strip
A feature added to the mold that will be removed from the part after molding to aid in creating a crisp end on the part. This is often done in conjunction with an overflow to improve the final part quality.
Texture
A specific type of surface treatment applied to some or all faces of the part. This treatment can range from a smooth, polished finish to a highly contoured pattern that can obscure surface imperfections and create a better looking or better feeling part.
Time Study
A time study analyzes every step of the manufacturing process to determine on average how long each step takes.
Time To Market (TTM)
The period of time from the development of a product concept to the availability of the finished product. It starts when a development project has been agreed to and resources have been committed and ends when the final product is shipped to customers.
Title 21 CFR Part 11
Code of Federal Regulations that deals with the Food and Drug Administration (FDA) guidelines on electronic records and electronic signatures in the United States. Defines the criteria under which electronic records and electronic signatures are considered to be trustworthy, reliable, and equivalent to paper records.
Title 21 CFR Part 820
Quality system regulation set forth by the United States Food and Drug Administration (FDA). The purpose is to ensure that quality systems involved in the manufacture of pharmaceutical products and medical devices are appropriate for the specific items designed or manufactured.
Total Cost Of Quality
This refers to the overall expenses resulting from product defects or poor quality, which encompass costs such as scrap, rework, and warranty claims. It also includes the resources spent on preventing or addressing quality issues, including inspection costs.
Total Logistics Costs
The overall cost for inbound delivery and storage of material and parts, plus the cost to store, transport, and deliver (and potentially set up) the final product to the customer. Calculating and monitoring such costs demonstrates that management is focused not only on improving efficiencies within the factory but also on the entire order-fulfillment process.
Total Productive Maintenance (TPM)
A comprehensive program to maximize equipment availability, where production operators are trained to perform routine maintenance tasks regularly while technicians and engineers handle more specialized tasks. The scope of TPM programs includes unscheduled maintenance prevention (through the selection of easy-to-service equipment), equipment improvements, preventive maintenance, and predictive maintenance (determining when to replace components before they fail).
Total Quality Management (TQM)
TQM is a company-wide initiative focused on enhancing all aspects of quality and customer satisfaction, which includes prompt service and product excellence. The process starts with top management and extends to all employees and managers responsible for influencing quality and satisfaction. It employs various tools like QFD, Taguchi methods, SPC, corrective action teams, cause-and-effect analysis, problem-solving techniques, and fail-safe systems.
Transitional Work Program
A program that provides various options to assist an injured worker in gradually performing the duties of a targeted job.
Undercut
A portion of the part that shadows another portion of the part, creating an interlock between the part and one or both of the mold halves. An example is a hole perpendicular to the mold opening direction bored into the side of a part. An undercut prevents the part from being ejected, or the mold from opening, or both.
Unit Of Measure (UOM)
The Unit of Measure defines how a part is purchased or used by manufacturers. While “each” is the most commonly used UOM, other units like inches, feet, pints, boxes, drops, etc., can also be applied.
Utilization
Typically paired with capacity, the term “capacity utilization” refers to the percentage or KPI that indicates how much of the available capacity is being utilized at a given time.
Value-Added Per Employee
This metric is calculated by subtracting the cost of materials, components, and services from the value of shipments, then dividing by the number of employees. It’s a key performance indicator used to assess productivity.
Vent
A small opening (ranging from 0.001 to 0.005 inches) typically located at the shutoff surface or via an ejector pin tunnel, allowing air to escape from the mold during resin injection.
Vendor-Managed Inventory
A system where on-site vendors or “resident suppliers” manage the inventory of materials, components, or subassemblies, ensuring their availability based on pre-established agreements with the plant.
Visibility Systems
These systems, including signal lights and kanban methods, provide real-time visual communication on the plant floor. They help workers quickly assess the status of tasks and respond to priorities efficiently.
Voice Recognition/Response
These systems use computerized voice recognition or synthesis to capture data for quality control, inventory management, or activate equipment with voice commands. They are particularly useful when workers’ hands are occupied.
Vestige
A small imperfection left on a part after the molding process, typically seen where the runner system or hot tip gate was connected to the part. Once trimmed, a vestige is a leftover mark from the gating system.
Wall
Refers to the faces of a hollow part. Consistency in wall thickness is crucial for maintaining part integrity.
Warp
Occurs when a part bends or curves as it cools due to different portions cooling and shrinking at different rates. For parts made with filled resins, warping may also happen because fillers and matrix resin shrink at varying rates, causing anisotropic stresses due to aligned fibers.
Weld Lines
Also called “stitch lines” or “knit lines”—in cases with multiple gates, they are referred to as “meld lines.” These imperfections appear where cooling material flows meet and merge, potentially leaving a visible line and/or an incomplete bond.
Wireframe
A CAD model made up of only lines and curves in 2D or 3D. Wireframe models are unsuitable for rapid injection molding due to their lack of surface definition.
Wear Strip Deck
A part of a conveyor belt system composed of plastic or metal strips attached to the top of the conveyor frame. These strips reduce friction and wear on the conveyor belt, ensuring it slides smoothly over a low-friction surface.
WIP Turn Rate
A performance metric used to measure how quickly work-in-process flows through a manufacturing plant. It is calculated by dividing the total annual shipment value at plant cost by the average WIP value at plant cost.
World-Class Manufacturer
A term used to describe manufacturers that excel in key performance metrics compared to industry standards. These manufacturers are recognized as leaders, consistently delivering high value at competitive prices.
Work-In-Process Inventory (WIP)
The value or quantity of materials, components, and subassemblies that are in various stages of completion, from raw material to finished goods. This includes material, direct labor, and overhead costs, all calculated at the plant’s cost.
X-bar Control Chart
A type of control chart used in statistical process control (SPC) to monitor the mean of a process over time. It helps identify variations and potential improvements in quality control.
X-Rays
A form of electromagnetic radiation used in industrial applications, such as non-destructive testing (NDT), to inspect the internal structure of materials and parts without causing damage.
Xenon Lamp
A high-intensity light source commonly used in applications requiring powerful light, such as in testing, curing, and in some industrial lighting systems.
Xylene
A solvent commonly used in the paint, coating, and printing industries, as well as in chemical production for cleaning, dissolving, and thinning various materials.
X-axis
The horizontal axis in a Cartesian coordinate system, often used in robotics and CNC machining to define the direction of movement along the width of the workpiece or machine platform.
Yield Improvement
A metric that tracks the percentage reduction in rejects over a five-year period, indicating the improvement in production quality and efficiency.
ZPA (Zone Powered Accumulation)
Zone Powered Accumulation refers to a type of conveyor system where products accumulate in distinct zones along the conveyor line. Each zone is controlled by sensors and powered rollers, allowing for precise control of product flow and accumulation. This system is commonly used in manufacturing and distribution facilities to improve the efficiency of product handling and minimize the risk of bottlenecks in the production line.
5S (Sort, Shine, Set in Order, Standardize, Sustain)
A method for maintaining an organized, clean workplace, aimed at identifying waste and preventing errors through structured activities.
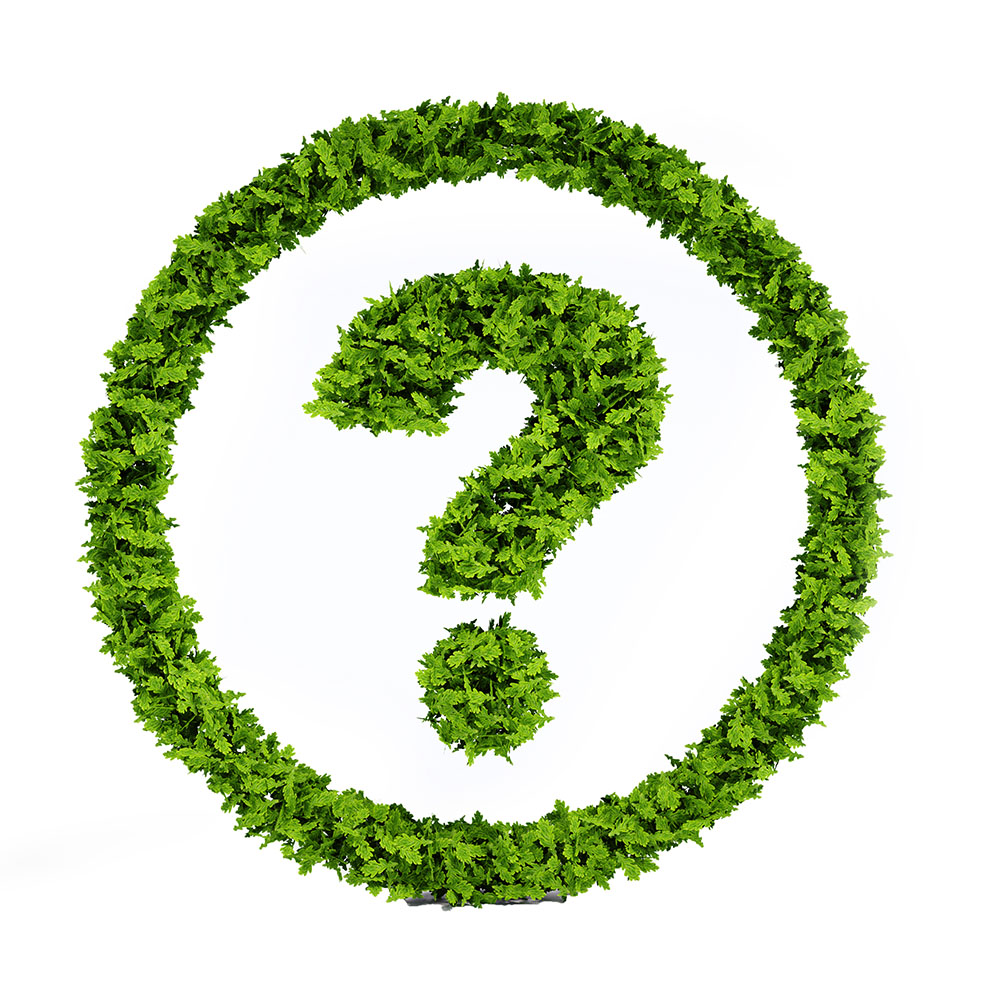
An undercut refers to a portion of the part that creates an interlock between the part and the mold. It can prevent the part from being ejected properly unless specific mold design considerations are made.
A glossary is essential for manufacturers as it streamlines training, helps onboard new employees, and improves communication between departments, ultimately increasing operational efficiency.
By providing standardized definitions, a manufacturing glossary ensures that everyone in the manufacturing process speaks the same language, reducing misunderstandings and promoting efficient collaboration across teams.
A manufacturing glossary is a comprehensive list of terms and definitions related to the manufacturing process, industry-specific terminology, equipment, and best practices. It helps professionals understand complex terminology and facilitates clear communication within the industry.
A weld line, or knit line, occurs when two separate flows of molten material meet and fail to fully fuse, leading to visible lines or weak spots on the finished part. It is an important factor to address in mold design to ensure part integrity.
Consistent wall thickness in injection molding is crucial to ensure uniform cooling and prevent warping. It also contributes to the overall strength and durability of the final part.
KingStar Mold uses state-of-the-art equipment, quality control measures, and experienced engineers to ensure that all molds meet the specific requirements of their customers, guaranteeing precision and durability.
KingStar Mold specializes in providing high-precision injection molding and mold-making services. With advanced technology and expertise, KingStar Mold ensures top-tier quality and efficiency for complex and intricate molds.