Services for Low Volume Production
What is Low Volume Injection Molding?
Low-volume injection molding is a manufacturing process used to produce a small number of parts, including rapid prototyping(CNC prototyping, vacuum casting and 3D printing) and injection molding, typically ranging from a few hundred to a few thousand units. It is ideal for prototypes, small production runs, and testing, offering quick turnaround times and cost-effective solutions compared to high-volume production.
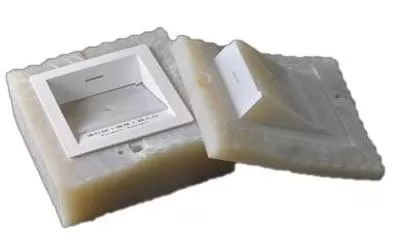
Advantages of Low Volume Production
Cost-Effective for Small Runs
Low-volume production reduces tooling and setup costs, making it more affordable for small batch runs, compared to traditional large-scale manufacturing.
Faster Time to Market
The streamlined process of low-volume production, including rapid prototyping and injection molding, allows for quicker turnaround times, helping businesses get products to market faster.
Design Flexibility and Iteration
Low-volume production enables greater flexibility in design changes, allowing companies to iterate on their product and make adjustments quickly without the need for large investments.
High Precision and Quality
Despite the smaller production scale, low-volume injection molding ensures high-quality, precise parts, ideal for prototypes, functional testing, or low-volume production of end-use components.
Applications of Low Volume Injection Molding
Prototyping
Small-scale production
Low Volume Injection Molding is good for making small runs of parts for niche markets, specialty products, or limited-edition items.
Customized products
Low Volume Injection Molding is perfect for making custom parts with unique designs, shapes, or materials.
Small businesses
Low Volume Injection Molding is good for small businesses or startups that don’t have a lot of resources.
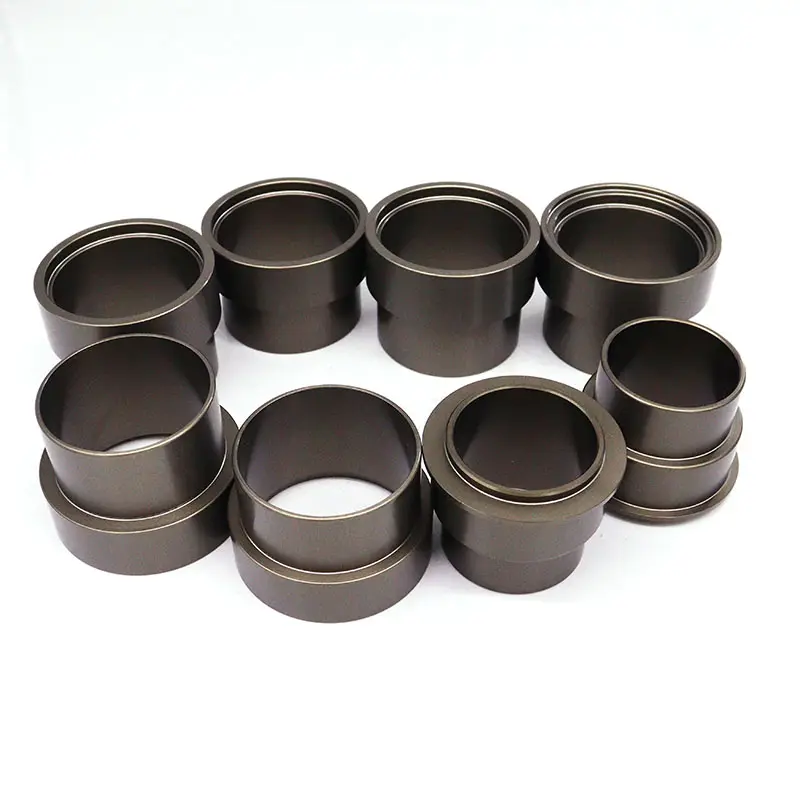
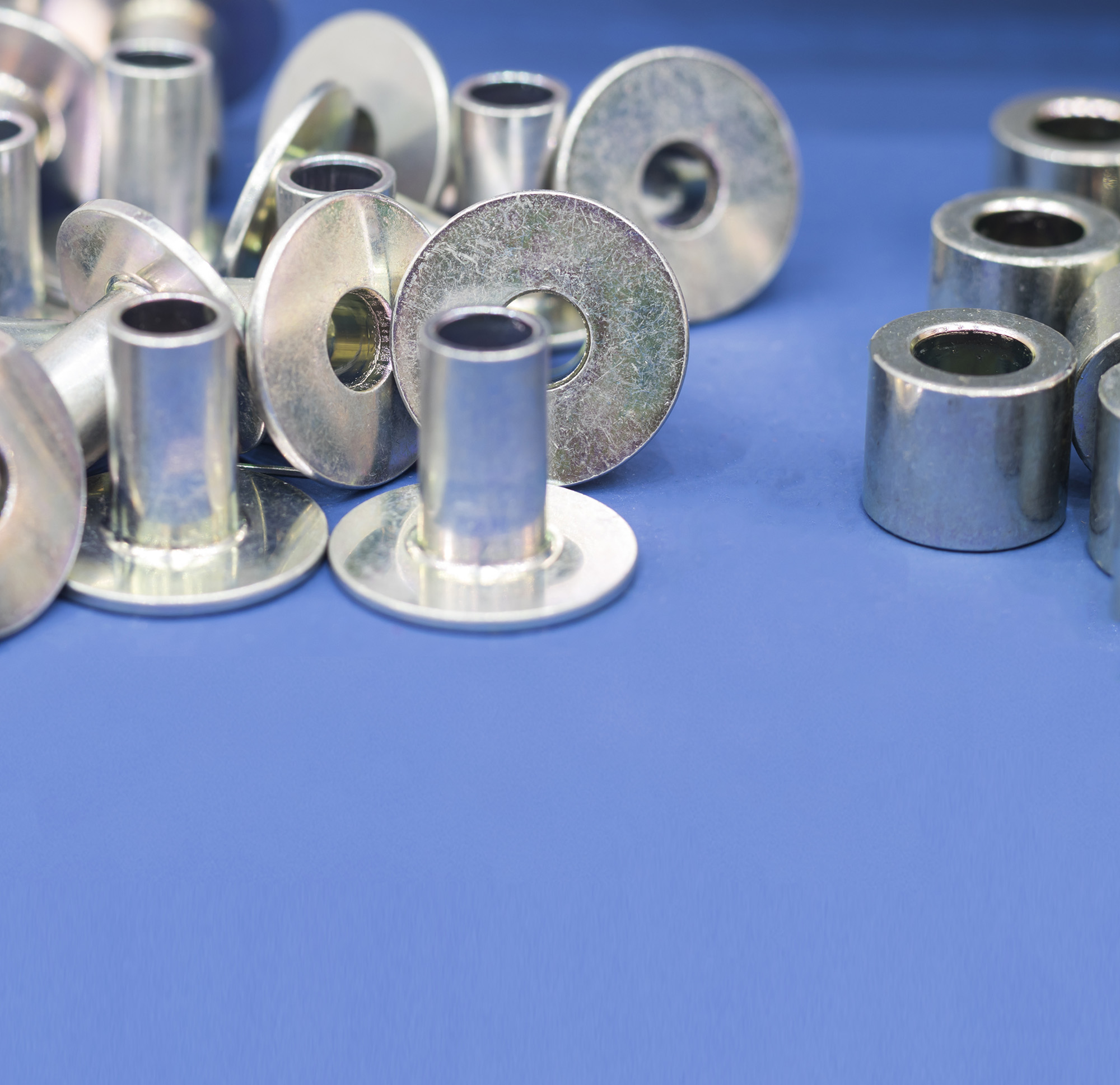
Low Volume Injection Mold Building & Production At KingStar Mold
At KingStar Mold, we specialize in providing low-volume injection mold building and production services, offering a cost-effective solution for businesses needing small to medium production runs. Our experienced team uses advanced technology to create high-quality molds quickly, allowing for rapid prototyping and testing before scaling up to full production. This service is ideal for startups, product testing, or industries with fluctuating demand, helping you reduce costs while ensuring product quality and performance.
Custom Solutions for Low Volume Production
At KingStar Mold, we offer tailored low-volume production solutions to meet the unique needs of various industries. Our expert team leverages advanced technologies to deliver high-quality, precise results while keeping costs low and production timelines short. Whether you’re testing a new product or require limited runs, we provide reliable, efficient services to ensure success at every stage.
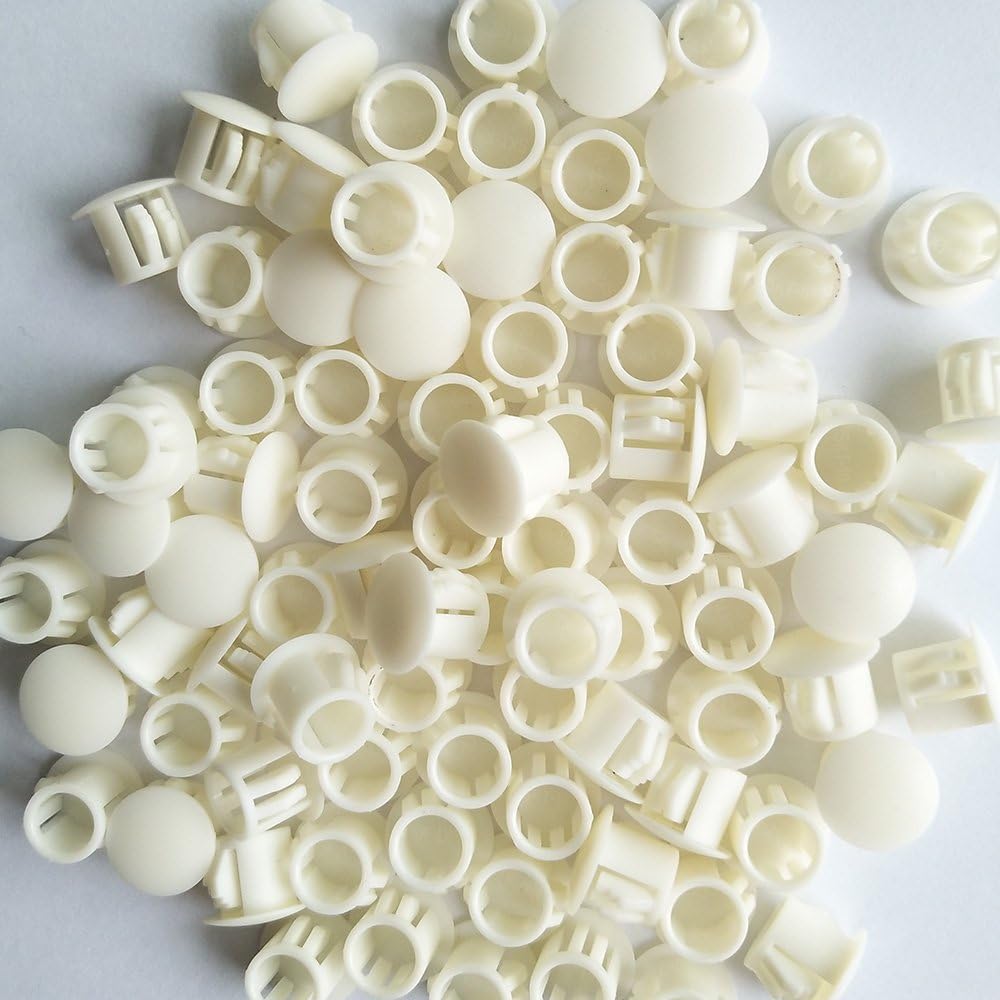
Key Advantages of Choosing KingStar Mold For Small Batch Production
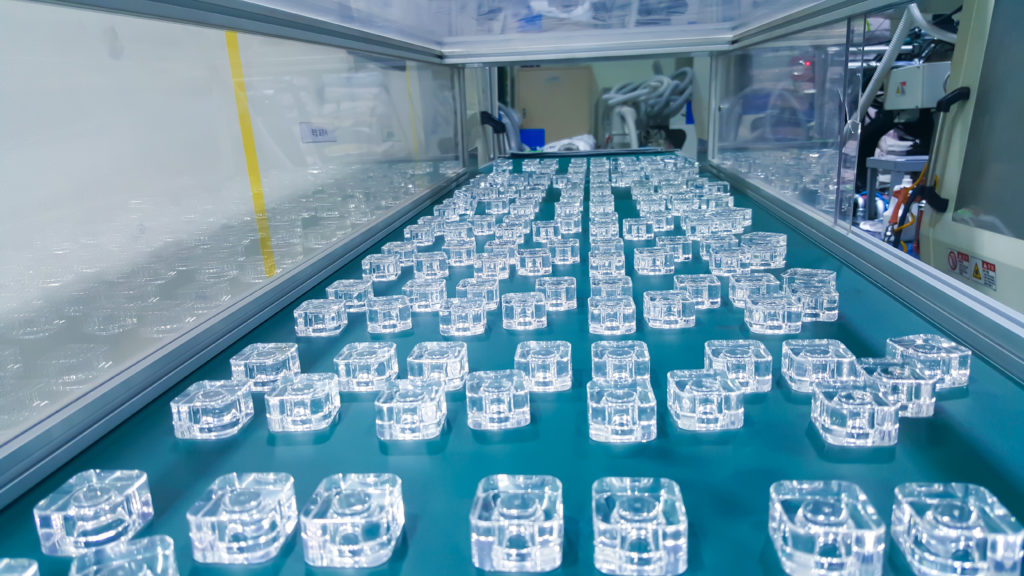
Cost-Effective
Low-volume production reduces initial setup costs, allowing you to manage smaller budgets while still achieving high-quality results.Faster Time to Market
With rapid prototyping and quicker production runs, low-volume services help bring your products to market faster, allowing for timely feedback and adjustments.
Scalability
Low-volume production offers the flexibility to scale your output based on demand, without the pressure of large-scale manufacturing commitments.Flexibility in Design
Low-volume production enables easy changes to designs, helping you iterate and refine your product without significant retooling costs.
Risk Mitigation
By testing your products in small batches, you can identify potential issues early in the production process, reducing the risks associated with large-scale manufacturing.High Precision
Low-volume production methods, such as CNC machining and injection molding, ensure high precision and high-quality results, even in limited quantities.
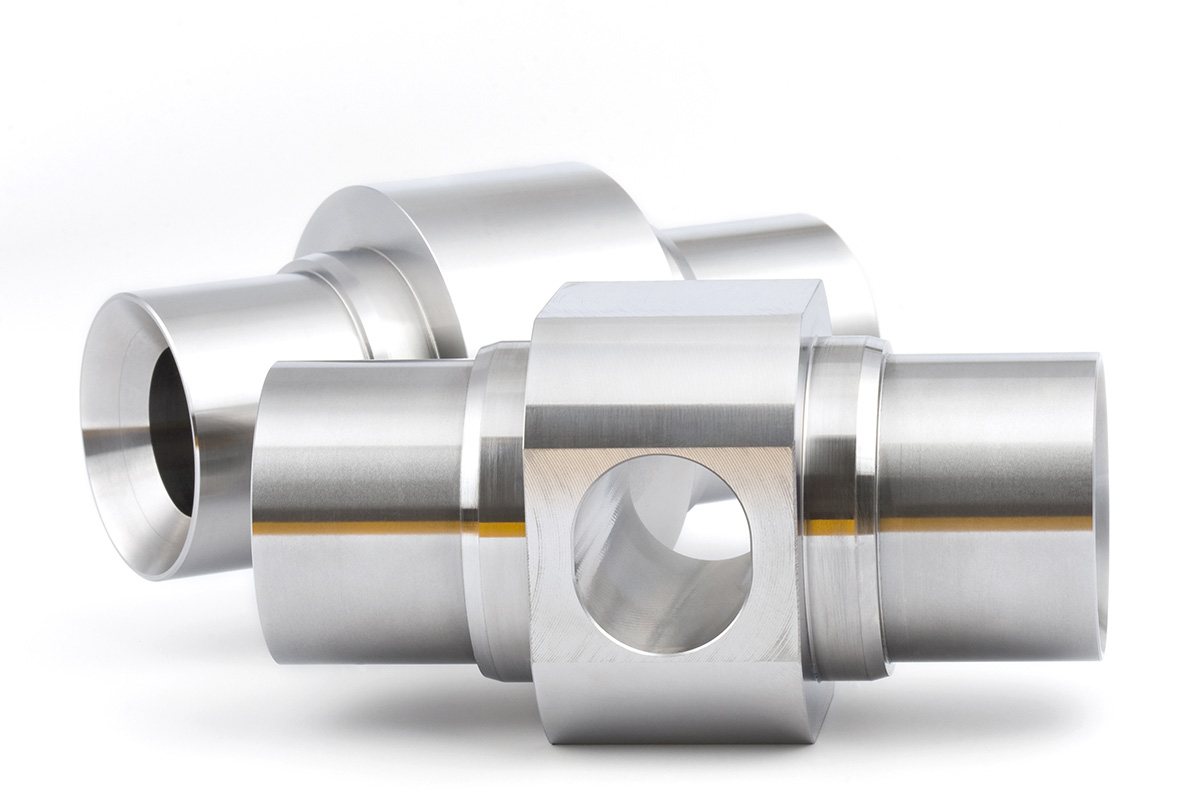
Low-volume Production Ordering Process

Consultation
Discuss your project requirements to establish clear goals, design needs, and production volume.
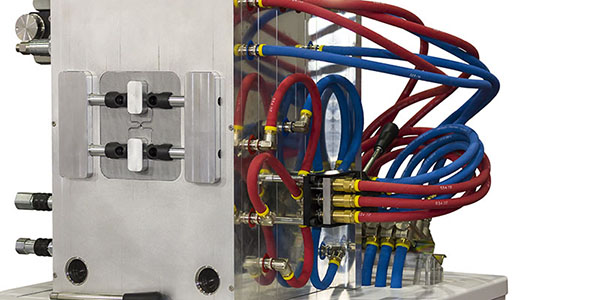
Prototype Development
Create a prototype for evaluation, ensuring your design meets expectations before full production.
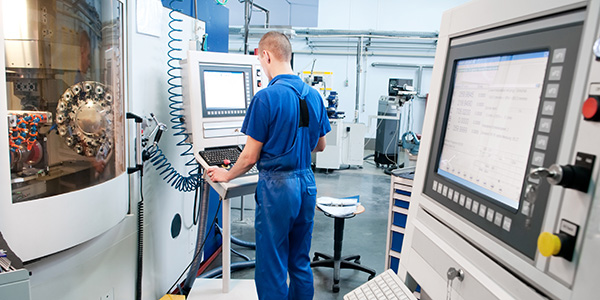
Production Setup
Set up the necessary tools, select materials, and prepare the production line for efficient manufacturing.
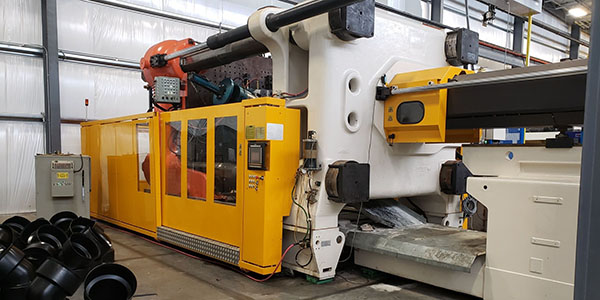
Manufacturing & Delivery
Produce the batch with high precision and deliver the final products on time for your next steps.
Materials for Low Volume Production
At KingStar Mold, we provide a comprehensive range of materials for low-volume production, including high-performance thermoplastics, metals, and rubber compounds. Our selection includes durable plastics such as ABS, PE, and PP, along with specialized materials like PLA and PEEK for environmentally conscious or technical applications. For metal components, we offer robust options like aluminum, stainless steel, and brass, ideal for strength and corrosion resistance. Additionally, we provide flexible rubber materials, such as silicone and TPU, to meet the needs of applications requiring elasticity and durability. With our expertise in material selection, we ensure the right fit for your low-volume production needs, delivering high-quality, cost-effective solutions for a wide range of industries.
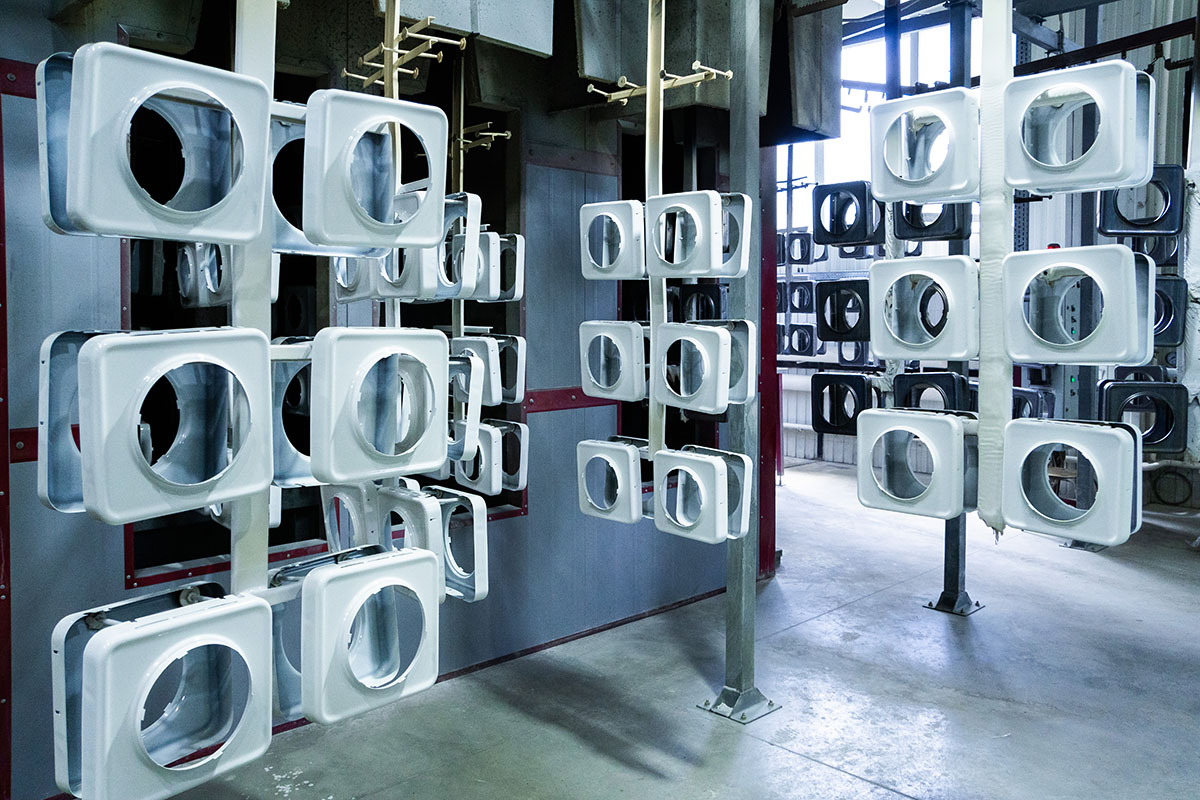
Low-Volume Production Finishes
3D Printing
3D printing is a rapidly evolving field that has revolutionized how we design and manufacture products. Previously, it was mainly used to create and test prototypes for later injection molding. However, advancements in printer accuracy, surface finish, and material options now allow 3D printers to produce injection molds as well.
2 Different Types of 3D Printing
Inserts within mold bases
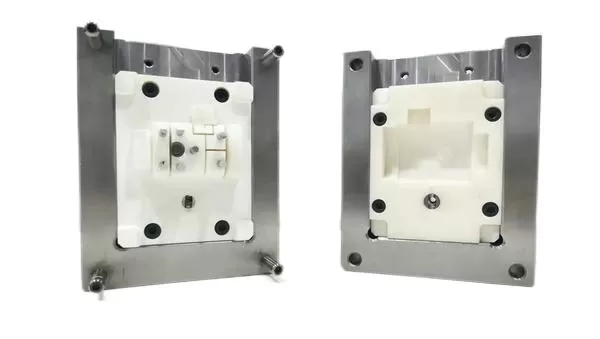
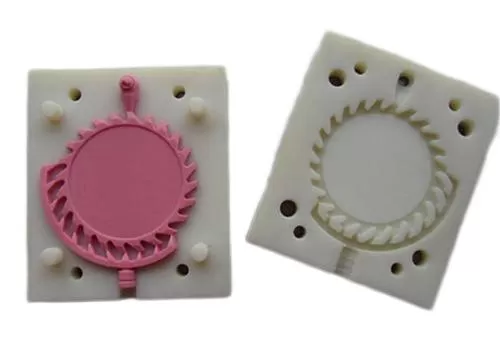
Fully 3D printed injection mold
Applications of 3D Printing
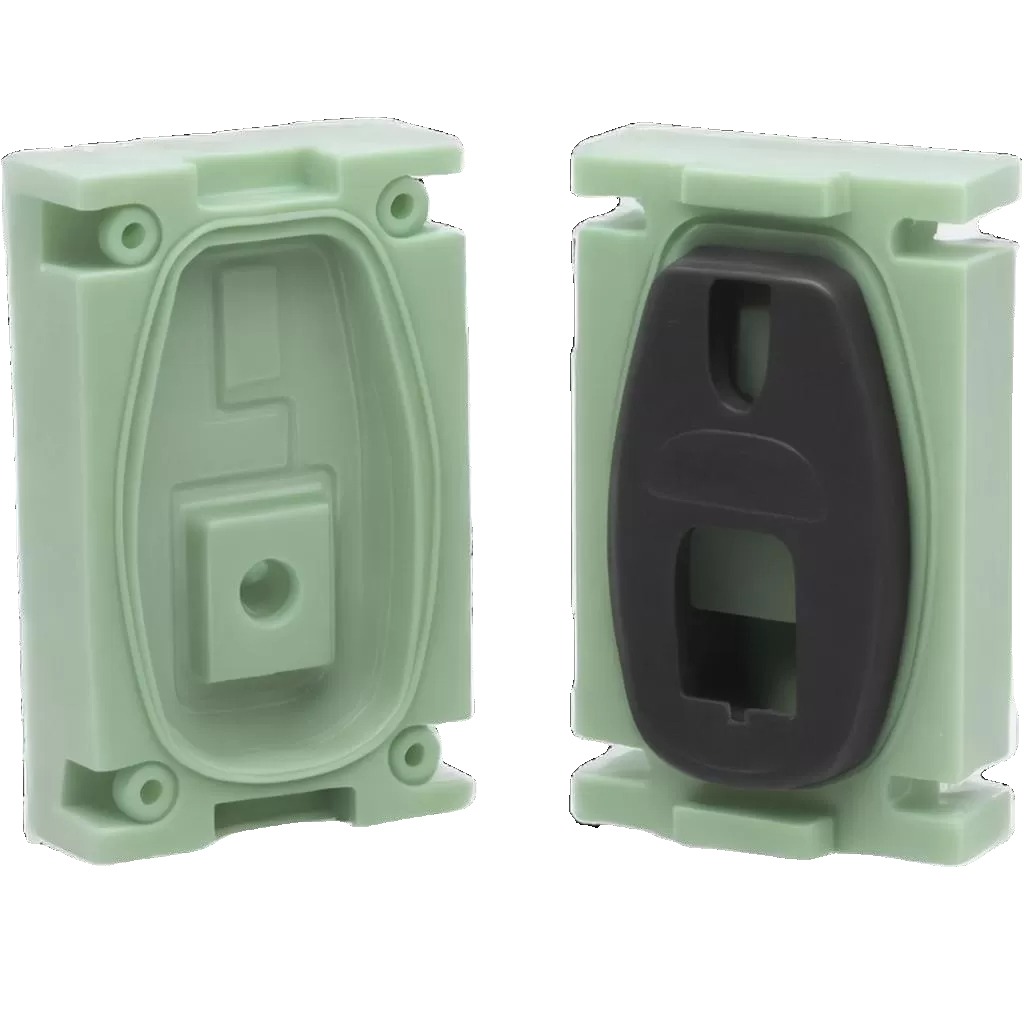
Faster lead times
Small-scale production
3D printing is great for small production runs of products, like custom parts or specialty items.
More flexible
3D printing makes it easy to change the design and the mold, so you can adapt to new product requirements.
Comparison of different processes for 3D printing injection molds
There are different ways to make molds with 3D printing. Here are some of them: Fused Deposition Modeling (FDM), Stereolithography (SLA), Selective Laser Sintering (SLS), and Digital Light Processing (DLP). You’ll choose which 3D printer and material to use based on how complicated the mold is and how long you want it to last. Here’s how these processes compare.
3D Printing Process | Mold Accuracy | Mold Strength | Mold Size | Cost Effective |
FDM | ★ | ★★★ | ★★★★ | ★★★★ |
SLA | ★★★★ | ★★ | ★★★ | ★★ |
SLS | ★★★ | ★★★★ | ★★ | ★ |
DLP | ★★★★ | ★★ | ★ | ★★★ |
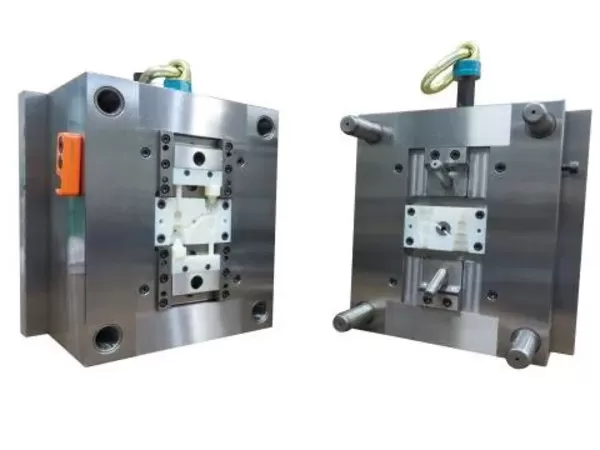
Vacuum Casting
Vacuum casting mold is a fast and cheap way to make small quantities of injection parts. Typically, we use 3D printed SLA parts or CNC-produced parts as prototypes. We make a mold out of silicone material, and then we pour PU material into the mold using the vacuum process of injection molding to make replica products.
Characteristics of Vacuum Casting
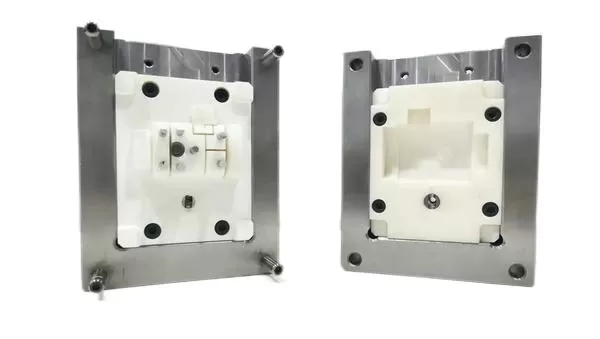
Characteristic | Description |
---|---|
Accuracy | The product is accurate to less than 100mm and within ±0.1mm. Above 100mm, it’s generally within ±0.3mm. |
Wall Thickness | Keep the wall thickness between 0.75 mm and 1.5 mm minimum. At least 0.75 mm ensures the mold is filled correctly and 1.5 mm achieve the best results. |
Mold Shoots | It’s about 20 shots per mold. |
Surface Treatment | You can achieve both a matte and glossy finish. |
Product Size | The size of the mold depends on the dimensions of the vacuum chamber and the volume of the product. You can produce parts up to 2m long. |
Benefits of Vacuum Casting
High accuracy
Shorter lead time
From sketch to shipment, it usually takes about a week to make 200 replica products. That’s because once you’ve made the mold, you don’t need to do any additional tooling or machining.
Cost effective
Vacuum casting is an affordable way to make small- to medium-sized parts in small- to medium-sized quantities. That makes it a good option for small businesses and start-ups.

How Does Vacuum Casting Work
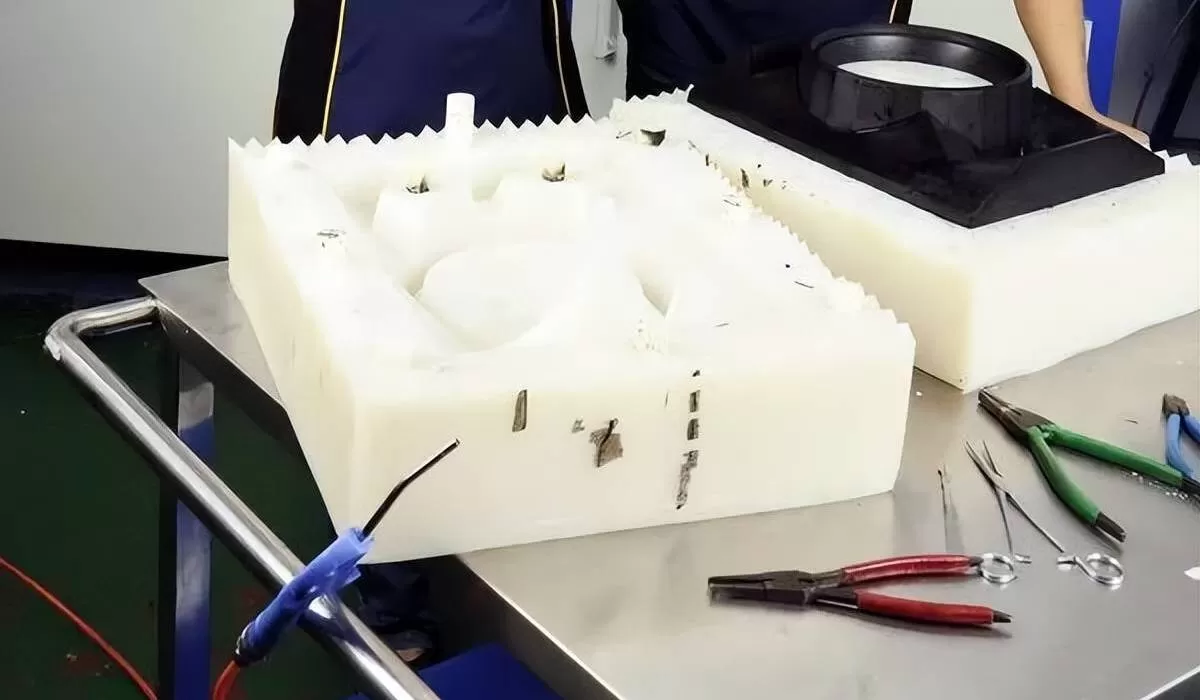
Quality of the prototype determines the quality of the copy products. We can spray texture or do other processing on the surface of the SLA prototype to simulate the final details of the product. The silicone mold will copy the details and texture of the prototype, so the surface of the copy products will look very much like the prototype.
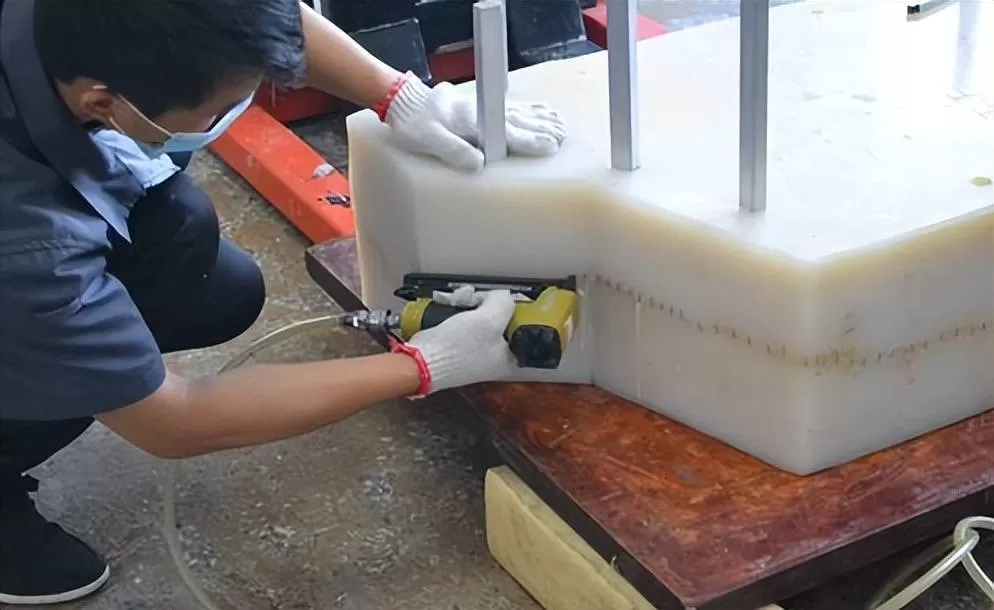
First, apply tape to a flat area around the prototype to make mold opening easier later; this will also serve as the parting surface of the final mold. Next, suspend the prototype in a box and place glue sticks around it to create sprues and vents. Then, inject silicone into the box, remove any air, and place it in the oven at 40°C for 8-16 hours, depending on the mold’s volume. Finally, once the silicone is cured, remove the box and glue sticks, take out the prototype, and carve out the cavity to complete the silicone mold.
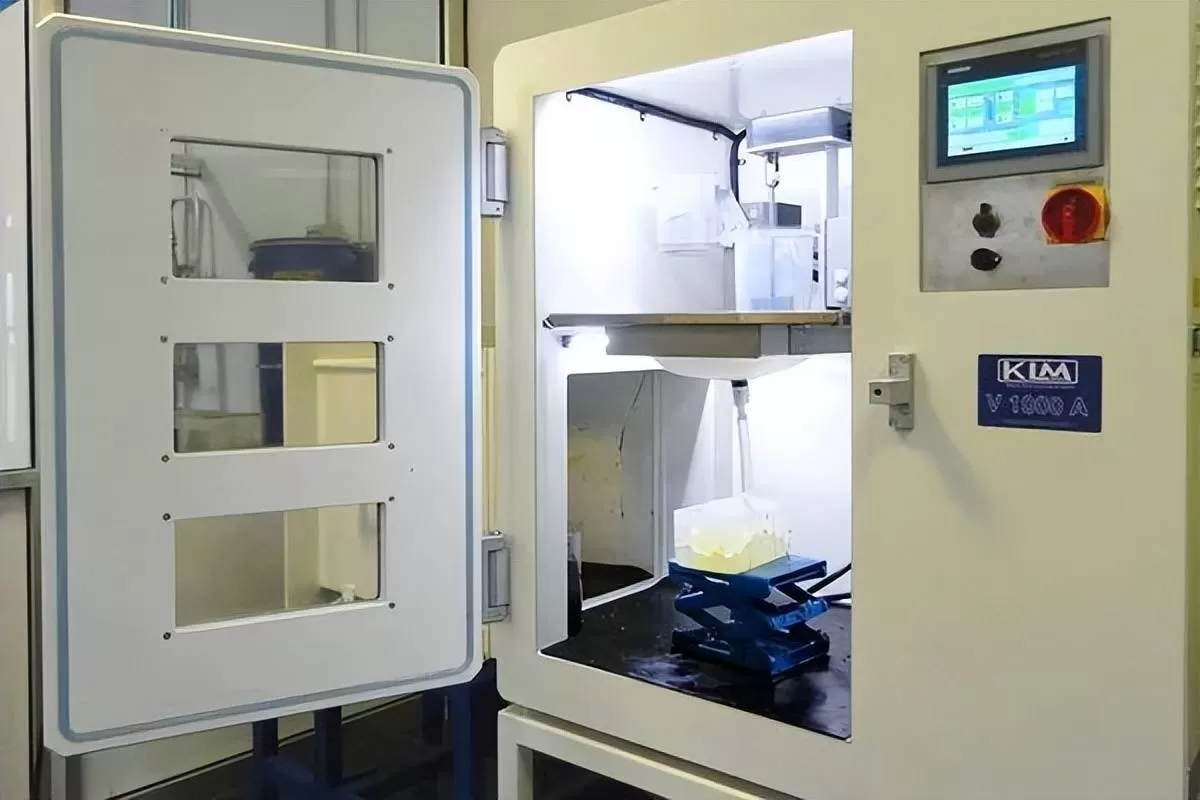
Begin by placing your silicone mold in the oven and setting it to preheat at 60-70°C. Ensure you apply a quality release agent to the mold before sealing it, to avoid sticking and surface imperfections. Next, heat your polyurethane resin to around 40°C. Mix the two-part resin in the proper proportions, stir thoroughly, and degas it under vacuum for 50-60 seconds. Once ready, pour the resin into the mold within a vacuum chamber and cure it in the oven for about 1 hour. After curing, carefully extract the cast product from the mold. You can repeat this process to produce more replicas.
Applications of Vacuum Casting Mold
Vacuum casting molds are perfect for making small batches of high-quality plastic prototypes. When you don’t need enough parts to justify the cost of a steel mold, vacuum casting is the fastest and most economical way to get a small batch of parts. It’s used in a wide range of industries, including automotive, medical, consumer products, industrial equipment, agricultural equipment, sports equipment, and musical instruments.
The vacuum casting process, along with cost-effective silicone molds, allows for easy and affordable engineering verification and design adjustments, making it an excellent choice for functional testing prior to mass production.
Vaccum Casting products can be a complete set of new products. If you don’t know which one is most suitable for mass production under the same design concept, you can make a silicone mold and make 10-15 replica products. And in each replica, different colors and finishes were designed on the modules to allow for internal discussion within the design department.
Small-batch replica products are perfect for consumer evaluation. Displaying models at exhibitions or releasing product photos in corporate brochures and on official websites helps generate early publicity, attracting potential customers and contributing to product optimization.
CNC Prototyping
Characteristics of CNC Prototyping
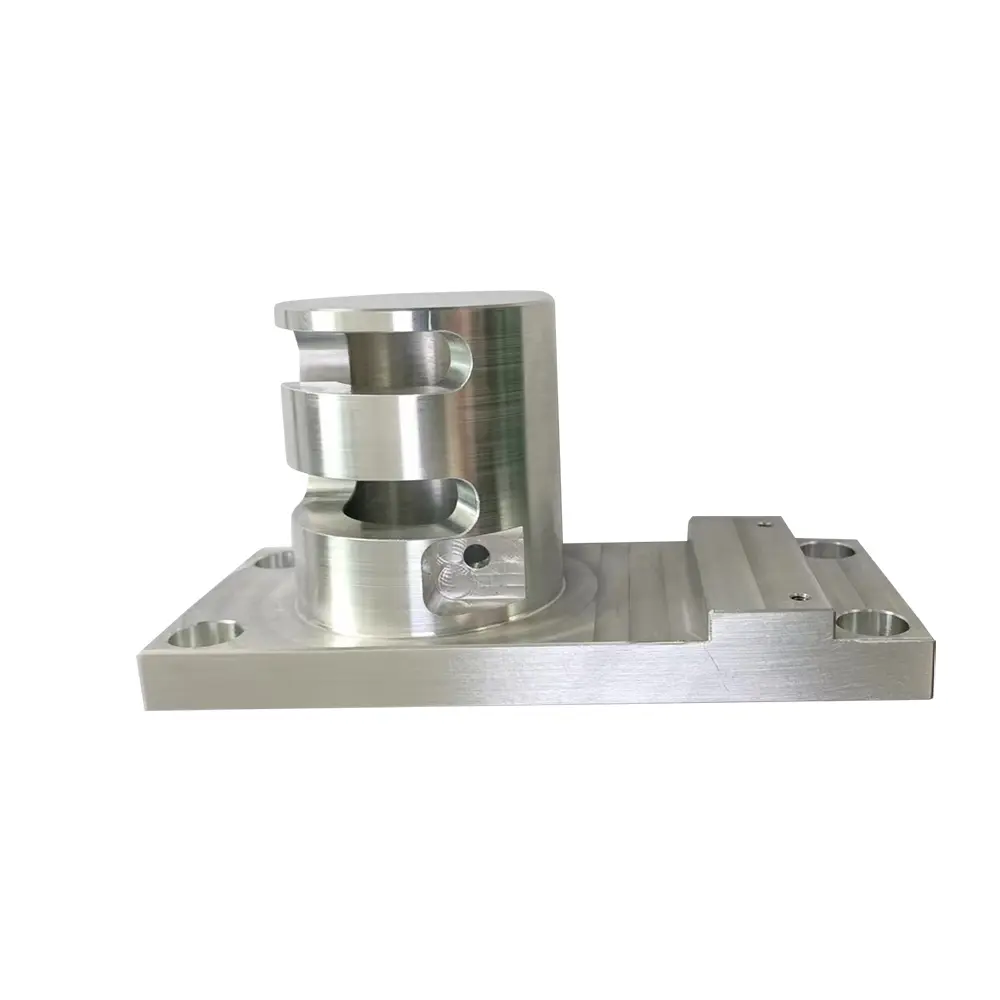
Characteristic | Description |
---|---|
Precision & Accuracy | Delivers high precision with tolerances typically ranging from ±0.05mm to ±0.2mm, ideal for complex geometries. |
Material Versatility | Supports a wide range of materials such as aluminum, steel, ABS, POM, and Delrin, offering flexibility for different applications. |
Surface Finish | Achieves smooth surface finishes, typically with a roughness range of Ra 1.6-3.2 µm, requiring minimal post-processing. |
Speed & Efficiency | Provides fast turnaround times, typically ranging from 1 to 5 days depending on complexity, with reduced setup times for efficiency. |
Benefits of CNC Prototyping
High Precision and Accuracy
CNC prototyping offers exceptional precision, ensuring that prototypes are crafted to exact specifications with minimal deviations.
Material Flexibility
It can work with a variety of materials, including metals, plastics, and composites, allowing for tailored prototypes to meet specific functional requirements.
Fast Turnaround Times
CNC prototyping enables quick production, often completing projects in just a few days, allowing for faster iterations and time-to-market.
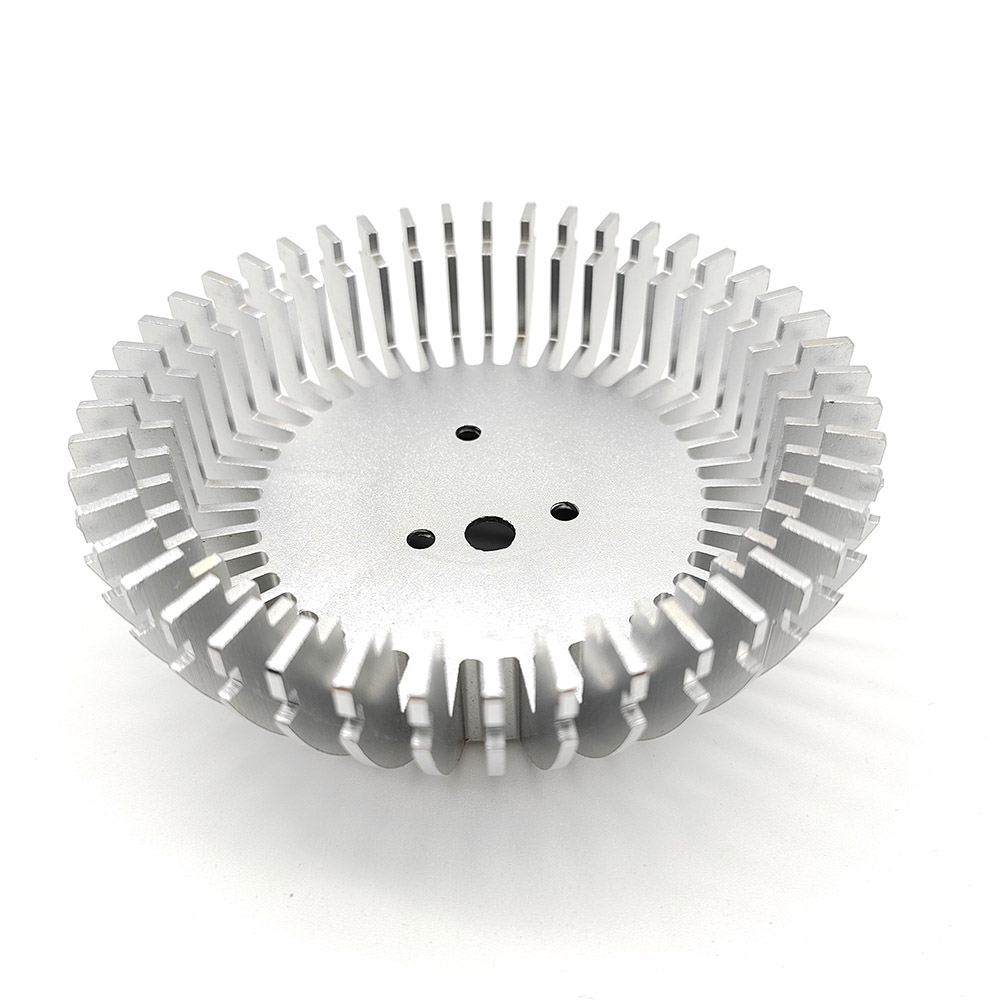
Applications of CNC Prototyping
CNC prototyping is ideal for producing custom parts in small quantities. It allows for the creation of highly specific components without the need for expensive tooling or molds, making it cost-effective for limited runs.
Low-volume production via CNC prototyping enables businesses to test products in the market before committing to large-scale manufacturing. This helps gather feedback and refine designs with minimal risk and investment.
CNC prototyping is used to create replacement parts for legacy equipment or specialized machinery. With low-volume production, manufacturers can quickly reproduce obsolete or hard-to-find components, ensuring smooth operations.
CNC prototyping supports the transition from prototype to production with minimal lead time. It ensures that the final product design is ready for mass production, with low-volume runs used to perfect the manufacturing process.
Low Volume Injection Molding
Characteristics of Low Volume Injection Molding
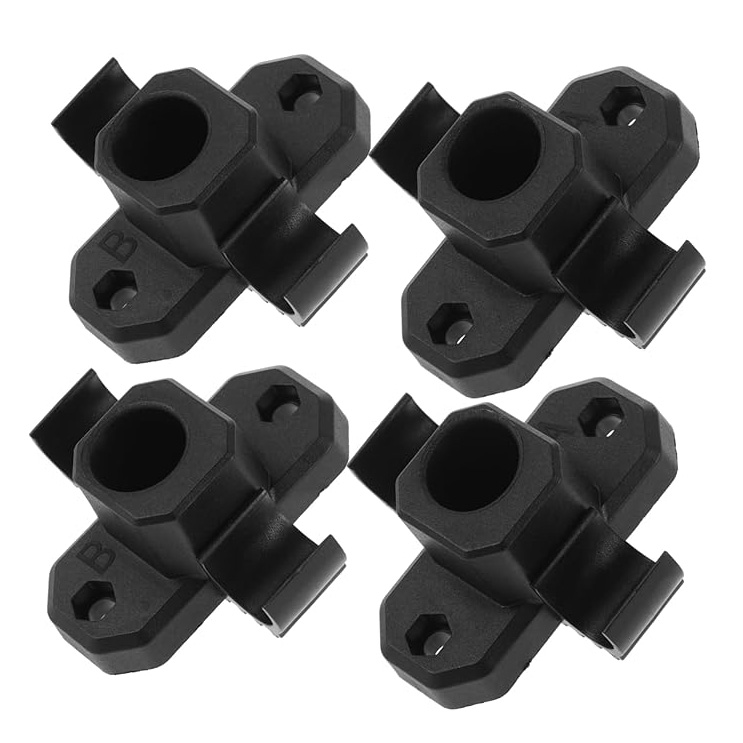
Characteristic | Description |
---|---|
Lower Initial Tooling Costs | Tooling for low volume injection molding typically ranges from $2,000 to $50,000, compared to $50,000 to $200,000 for high-volume molds. |
Quick Turnaround Times | Tool setup and production start can take 1 to 4 weeks, much faster than the 8 to 12 weeks required for high-volume production. |
Material Flexibility | A wide range of thermoplastics (e.g., ABS, PP, PC, nylon) can be used, with material costs ranging from $1 to $15 per pound depending on type. |
Lower Production Rates | Cycle times generally range from 15 to 60 seconds per part, slower than the 5-second cycle times in high-volume injection molding. |
Benefits of Low Volume Injection Molding
Cost-Effective for Small Batches
Low volume injection molding significantly reduces tooling and setup costs, making it ideal for producing small quantities at a fraction of the price of high-volume manufacturing.
Faster Time to Market
The shorter lead time for mold production and setup (1–4 weeks) allows companies to quickly move from design to production, accelerating product development cycles.
Design Flexibility
With a wide range of material options and the ability to easily modify molds, low volume injection molding supports rapid prototyping and design iteration for different industries.
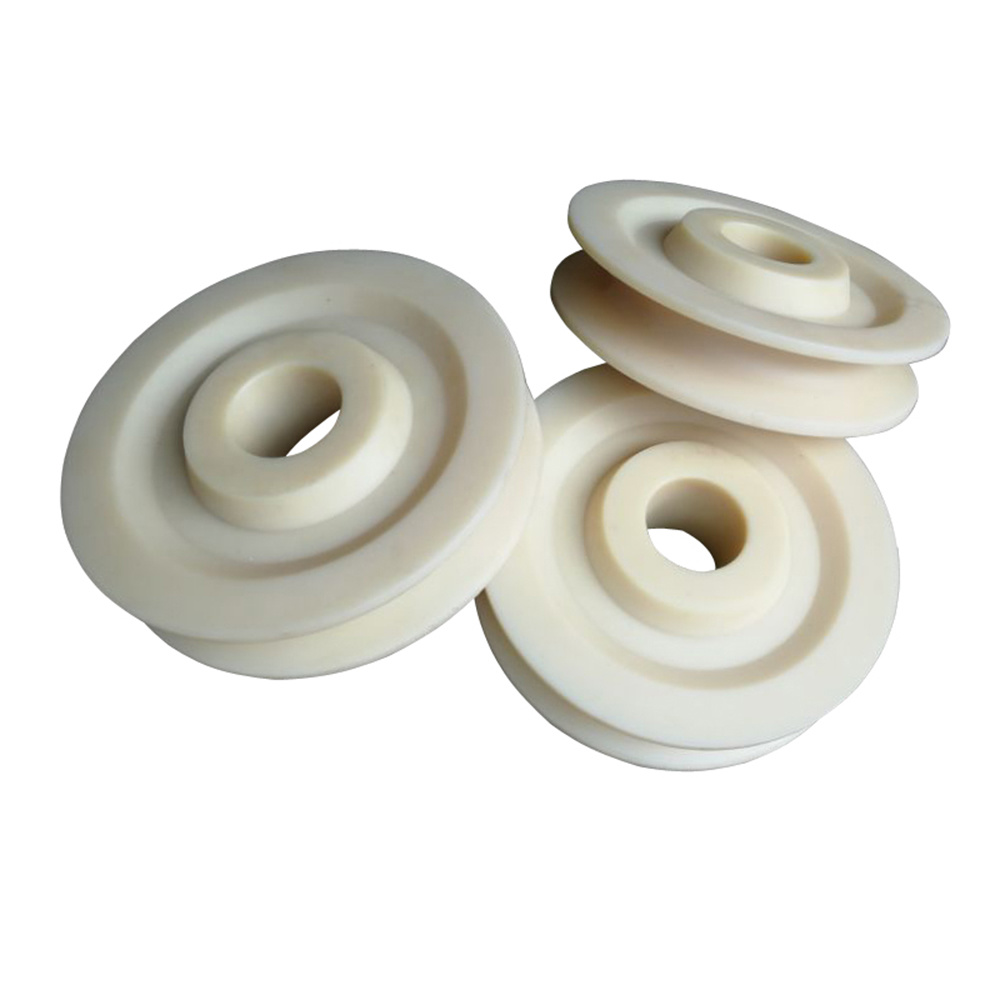
Applications of Low Volume Injection Molding
Low volume injection molding allows companies to quickly produce functional prototypes for design testing, user feedback, and validation. It’s much faster and more cost-effective compared to traditional methods, making it ideal for industries like automotive, electronics, and consumer products.
Small businesses or startups often need specific parts in limited quantities, and low volume injection molding provides an economical way to manufacture these components. This is particularly useful for industries such as medical devices, aerospace, or specialized consumer goods where the demand doesn’t justify the cost of large-scale production.
In certain cases, companies may need end-use parts for functional testing or limited market release. Low volume injection molding offers a way to create durable, high-quality parts quickly before moving on to full-scale production. This can be especially beneficial in fields like automotive or machinery.
For industries that need spare or replacement parts for products no longer in full-scale production, low volume injection molding provides a cost-effective solution. For example, in the automotive and home appliance sectors, manufacturers can produce low quantities of parts to support existing products without the need for expensive tooling setups or large production runs.
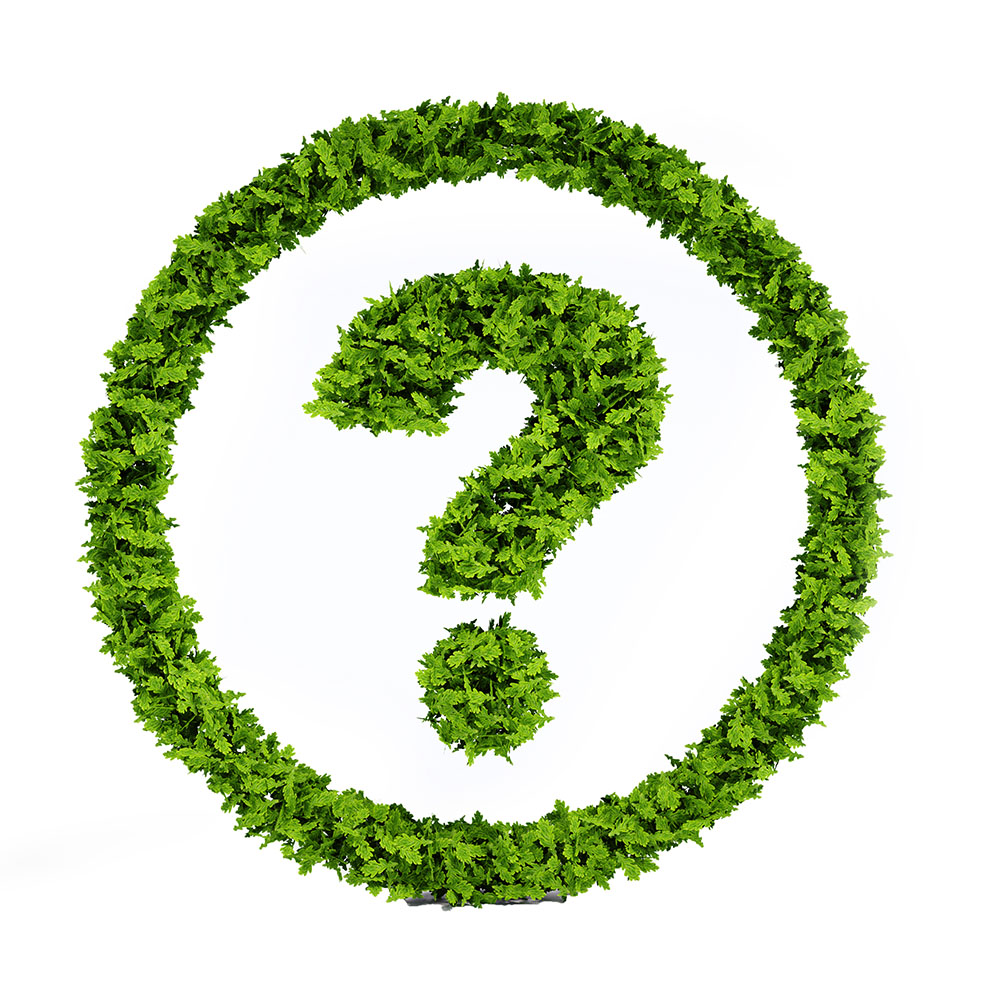
Low-volume production is beneficial for industries such as automotive, aerospace, medical devices, consumer electronics, and consumer goods, where fast iteration and testing are crucial.
Vacuum casting is used for creating high-quality prototypes and small production batches by casting parts in silicone molds, making it ideal for rapid prototyping, low-cost, and high-fidelity parts.
CNC prototyping is ideal for creating precise, functional prototypes from a variety of materials, while injection molding is better for producing durable, high-volume parts with complex geometries and tighter tolerances.
Benefits include reduced upfront costs, faster production times, increased flexibility in design and materials, and the ability to test market demand without committing to large-scale manufacturing.
- KingStar Mold provides efficient low-volume production services, using advanced injection molding, CNC prototyping, and 3D printing to deliver high-quality parts in small quantities at competitive prices.
Low-volume production refers to the manufacturing of a small number of parts or products, typically ranging from a few hundred to a few thousand units, often used for prototyping, small batch runs, or niche market needs.
KingStar Mold offers expertise in rapid prototyping and low-volume injection molding, CNC machining, and vacuum casting, providing end-to-end solutions with quick turnaround times and high precision.
3D printing is ideal for producing prototypes, complex geometries, and short production runs quickly and cost-effectively, offering flexibility in design and material selection.
The minimum order quantity for low-volume production typically ranges from 100 to 500 parts, depending on the production method, material, and part complexity.
KingStar Mold uses state-of-the-art equipment and experienced engineers to maintain high-quality standards, ensuring parts meet your exact specifications regardless of the production volume.
Low-volume production supports a wide variety of materials, including plastics (ABS, PP, PE), metals (aluminum, steel), and elastomers, depending on the method used (CNC, injection molding, etc.).
Lead times for low-volume production range from a few days to several weeks, depending on the complexity of the parts and the chosen production method (CNC, injection molding, etc.).
Optimization Solutions Provided For Free
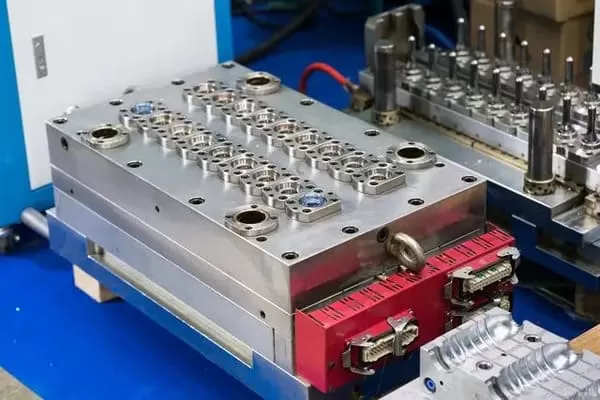