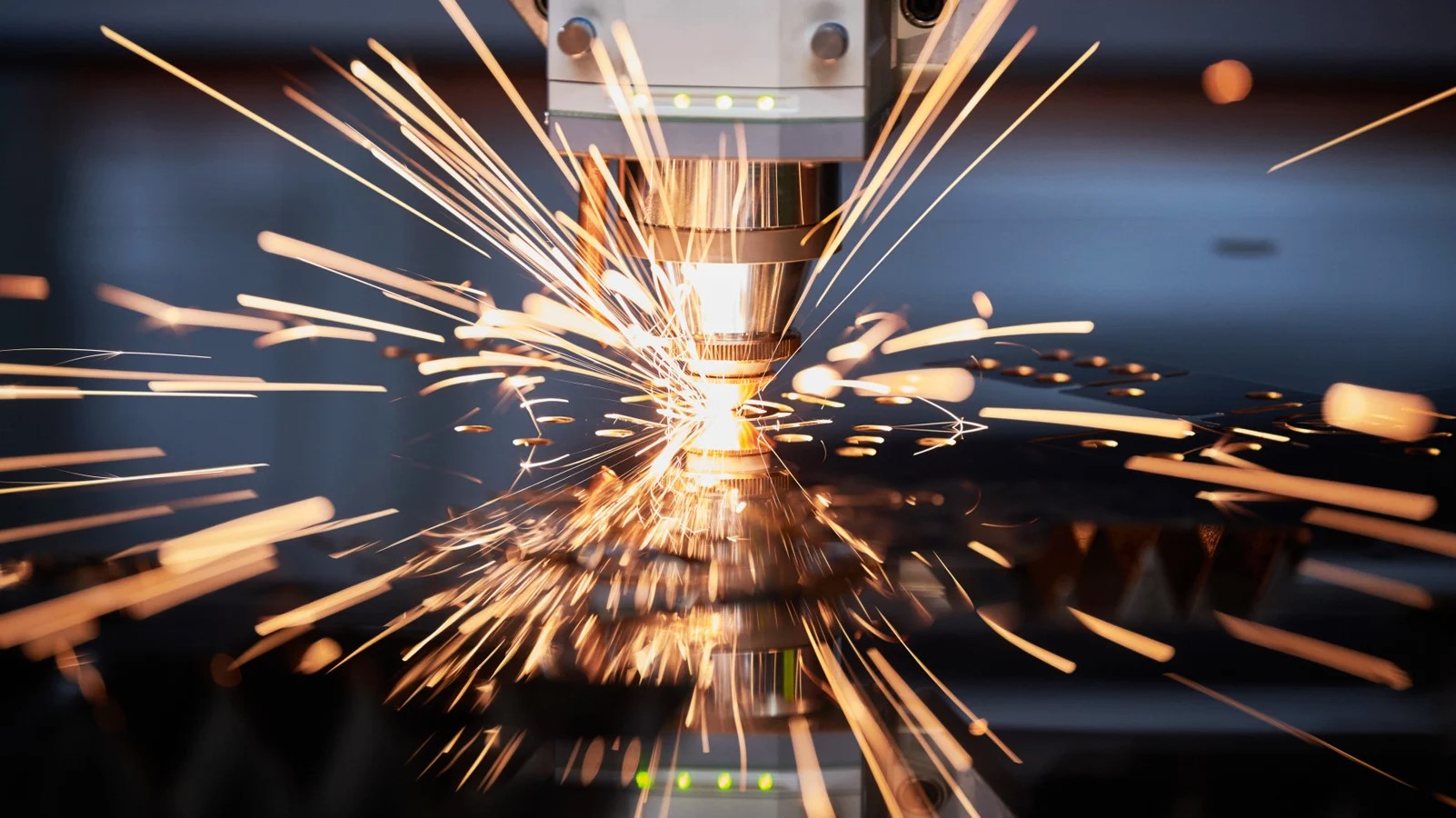
What is Laser Cutting?
Laser cutting is a precise and efficient manufacturing process that utilizes a high-powered laser to cut through materials, producing detailed and accurate flat shapes. It’s ideal for creating complex components from metals, plastics, and other materials with minimal material waste.
Laser cutting is commonly used for:
KingStar Mold’s Laser Cutting Capabilities
Capability | Details |
---|---|
Maximum Part Size | 500 mm x 500 mm (19.69 in. x 19.69 in.) |
Minimum Part Size | 2X material thickness, with a minimum of 1.5 mm (0.06 in.) |
Distance Dimensions | ISO 2768-c standards. Tolerance: +/- 0.1 mm (0.004 in.) for length, width, diameter, and location |
Maximum Material Thickness | Carbon Steel: < 20 mm (0.79 in.) Stainless Steel: < 12 mm (0.47 in.) Aluminum: < 12 mm (0.47 in.) Copper: < 10 mm (0.39 in.) |
Kerf (Slit Size) | Approximately 0.3 mm (0.012 in.) |
Edge Condition | Laser-cut edges are smooth, clean, and have a fine vertical finish. |
Laser Sources | CO2 and fiber lasers, up to 8 kW for precise cutting. |
Repeatability | +/- 0.03 mm (0.0012 in.) |
Positioning Accuracy | +/- 0.05 mm (0.002 in.) |
Lead Time | 3-5 days for standard orders |
Various Options for Laser Cutting
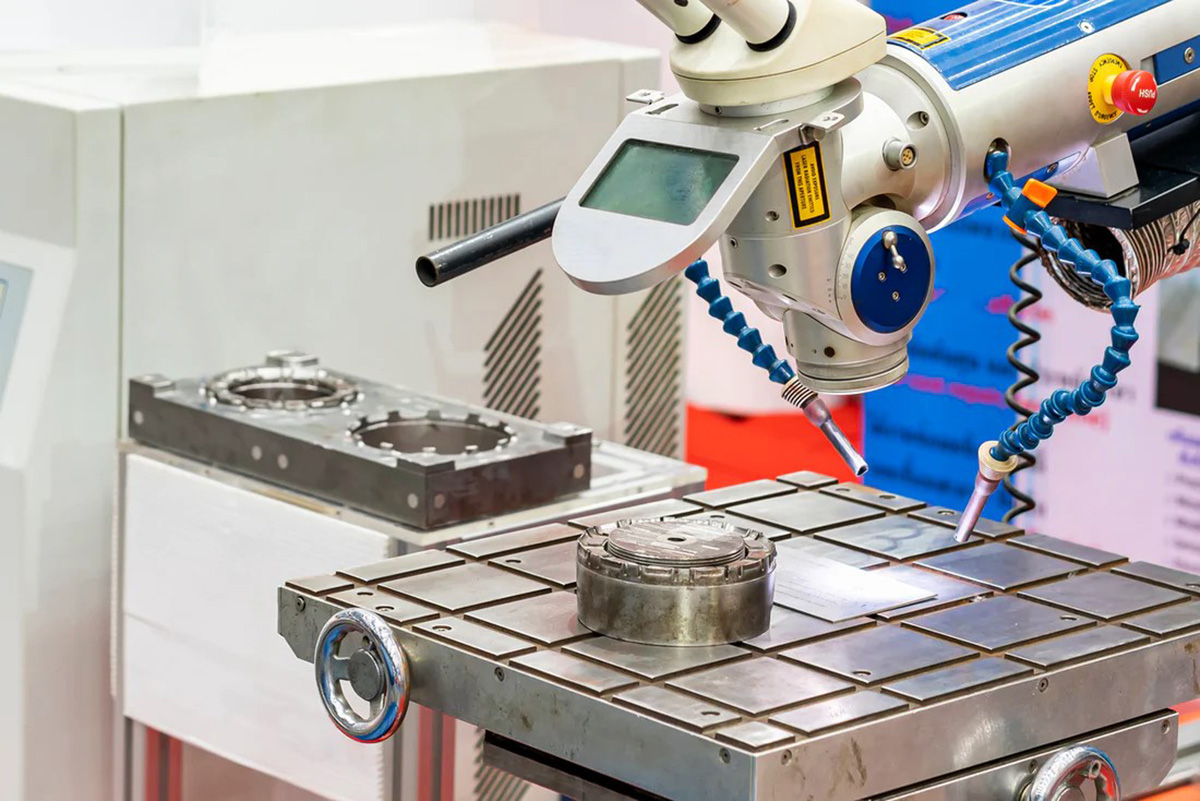
Nd:YAG Laser Cutting
Nd:YAG laser cutters are highly regarded for their ability to cut through thick and tough materials. We use this advanced technology for projects requiring high precision and deep cutting capabilities, especially in complex industrial and design applications.
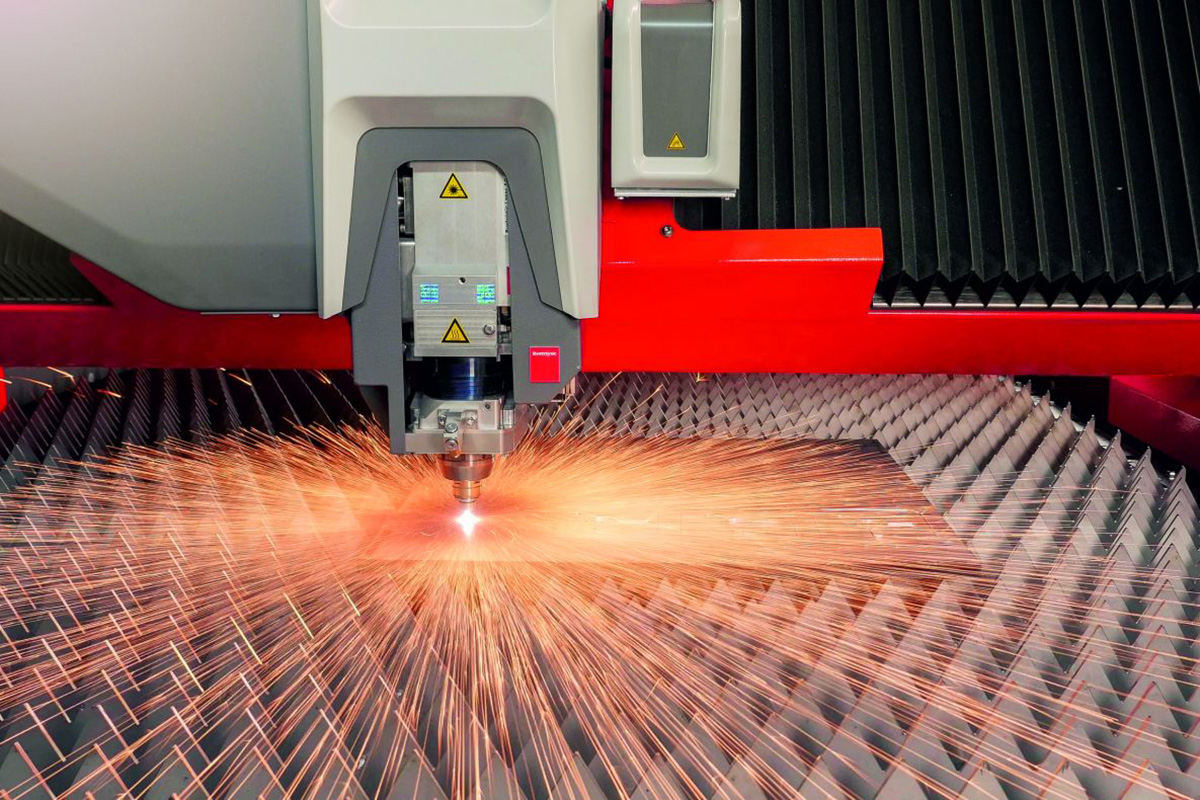
Fiber Laser Cutting
Fiber laser cutters deliver outstanding accuracy with quick setup times, making them ideal for cutting reflective metals. Known for their high energy efficiency and rapid cutting speeds, they are perfect for both large-scale and customized metal cutting tasks.
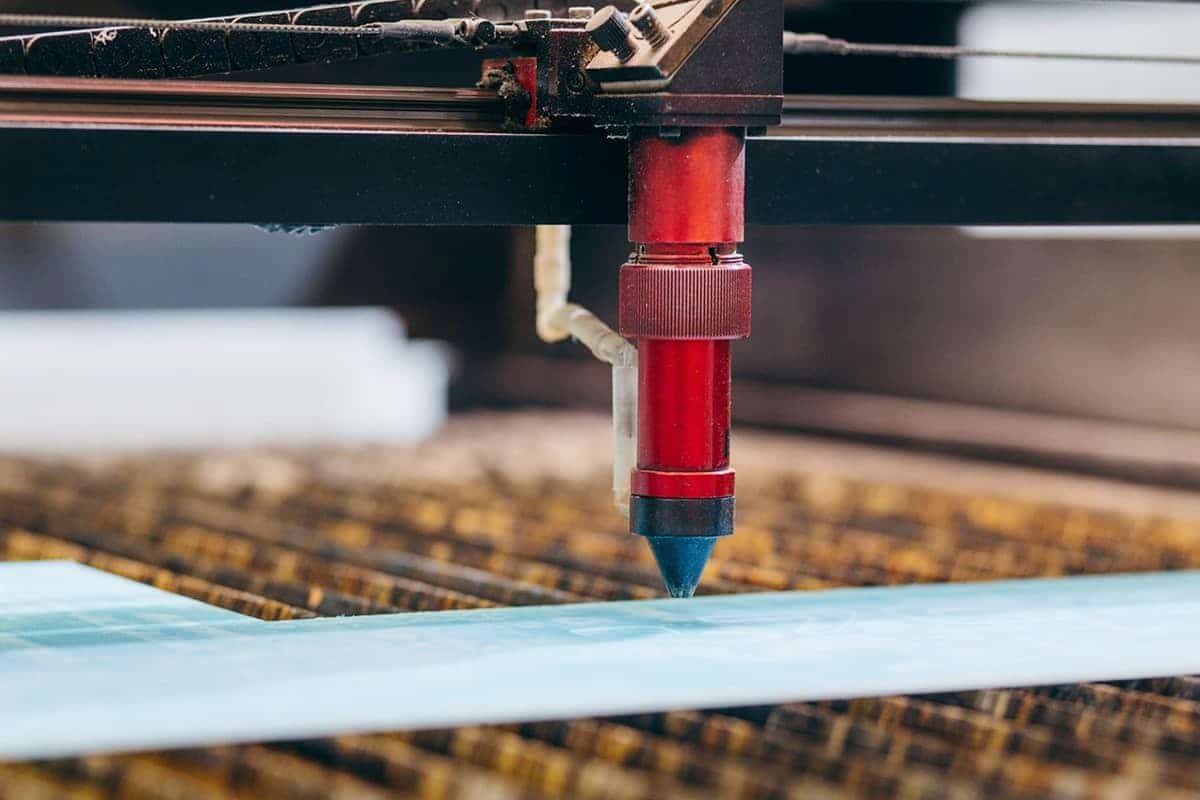
CO2 Laser Cutting
Our CO2 laser cutters excel in processing a variety of materials such as metals, plastics, and wood. The fine laser beam produced by CO2 technology ensures smooth cuts and detailed designs, elevating the quality of your finished parts.
Metal Materials and Thicknesses for Laser Cut Parts
Material | Grade | Thicknesses Available |
---|---|---|
Aluminum | 5052-H32, 6061-T6 | 0.025 in. - 0.250 in. (0.635 mm - 6.35 mm) |
Steel | CRS/HRPO, Galvanneal, Galvanized | 0.025 in. - 0.250 in. (0.635 mm - 6.35 mm) |
Stainless Steel | 304-2B, 304 #4, 316-2B | 0.025 in. - 0.250 in. (0.635 mm - 6.35 mm) |
Copper | C1010, C1100 | 0.025 in. - 0.125 in. (0.635 mm - 3.175 mm) |
Brass | C260 | 0.025 in. - 0.125 in. (0.635 mm - 3.175 mm) |
Typical Applications of Laser Cutting
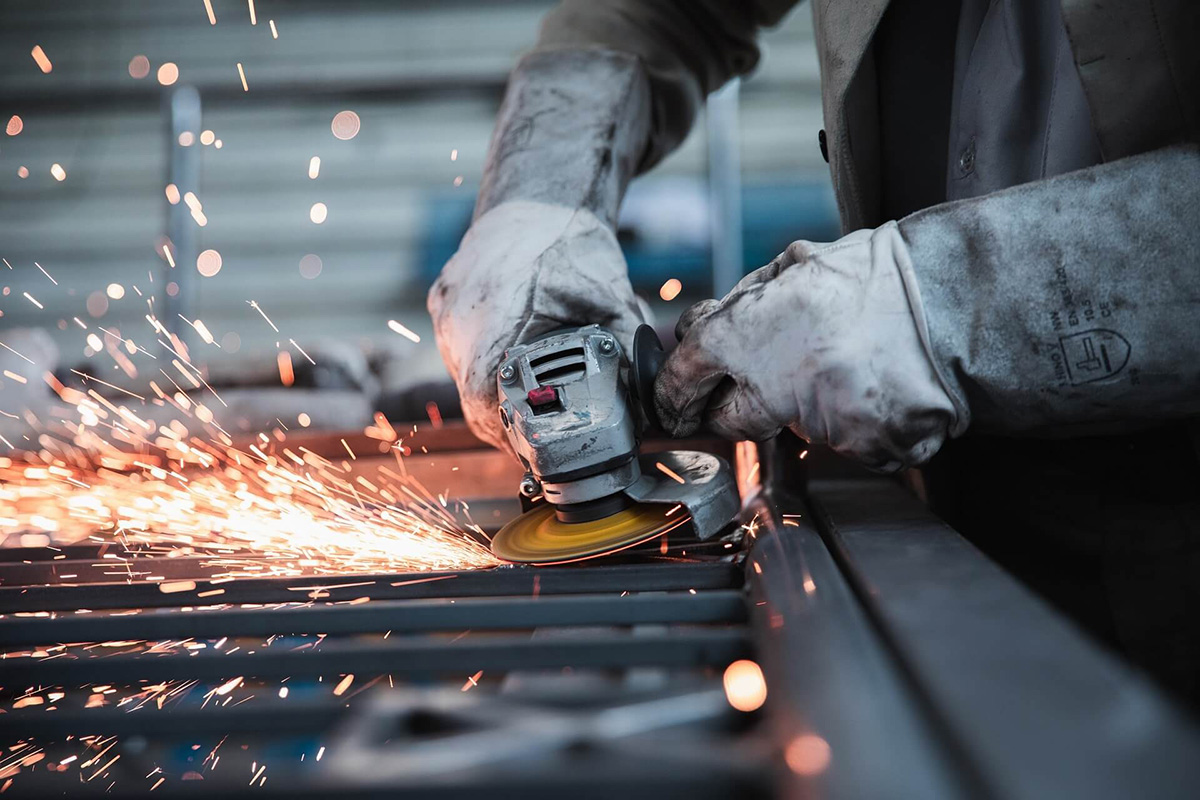
Metal Fabrication
Laser cutting is commonly used in metal fabrication for creating parts like brackets, mounts, washers, and enclosures with high precision.
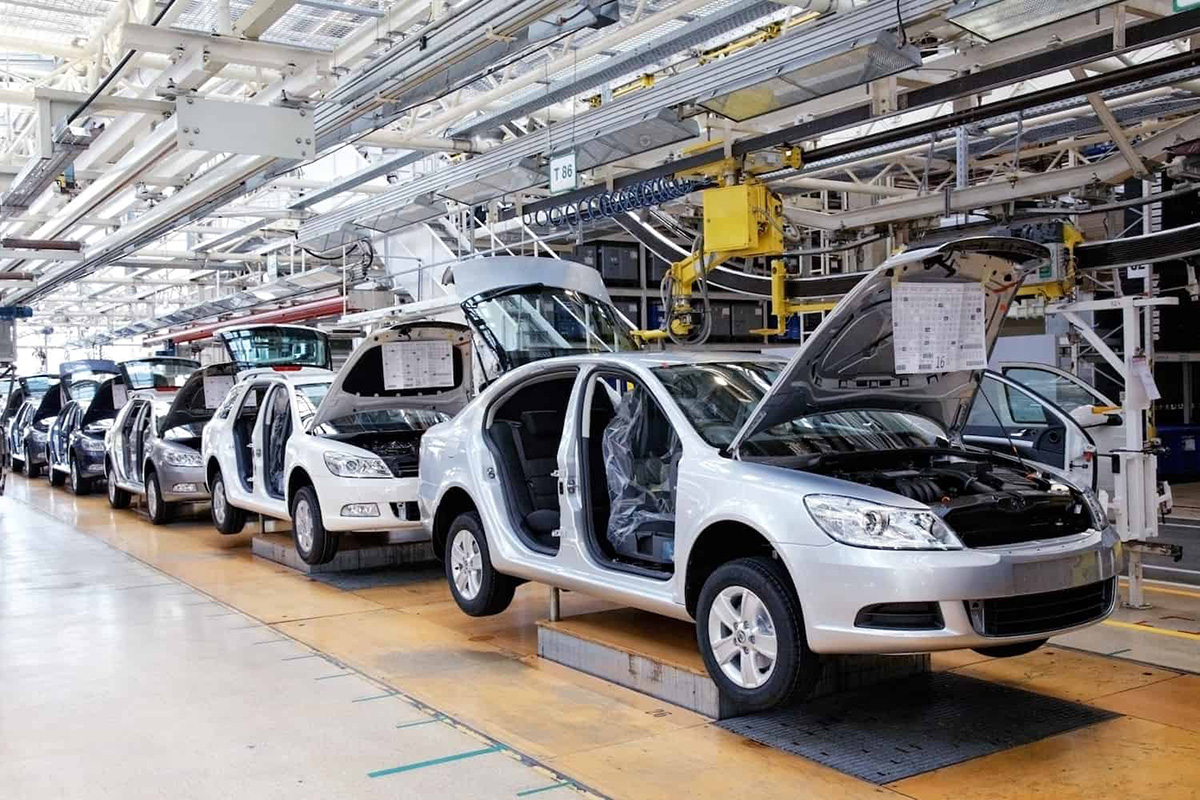
In the automotive industry, laser cutting is used to produce parts such as body panels, exhaust components, and engine components that require detailed precision and tight tolerances.
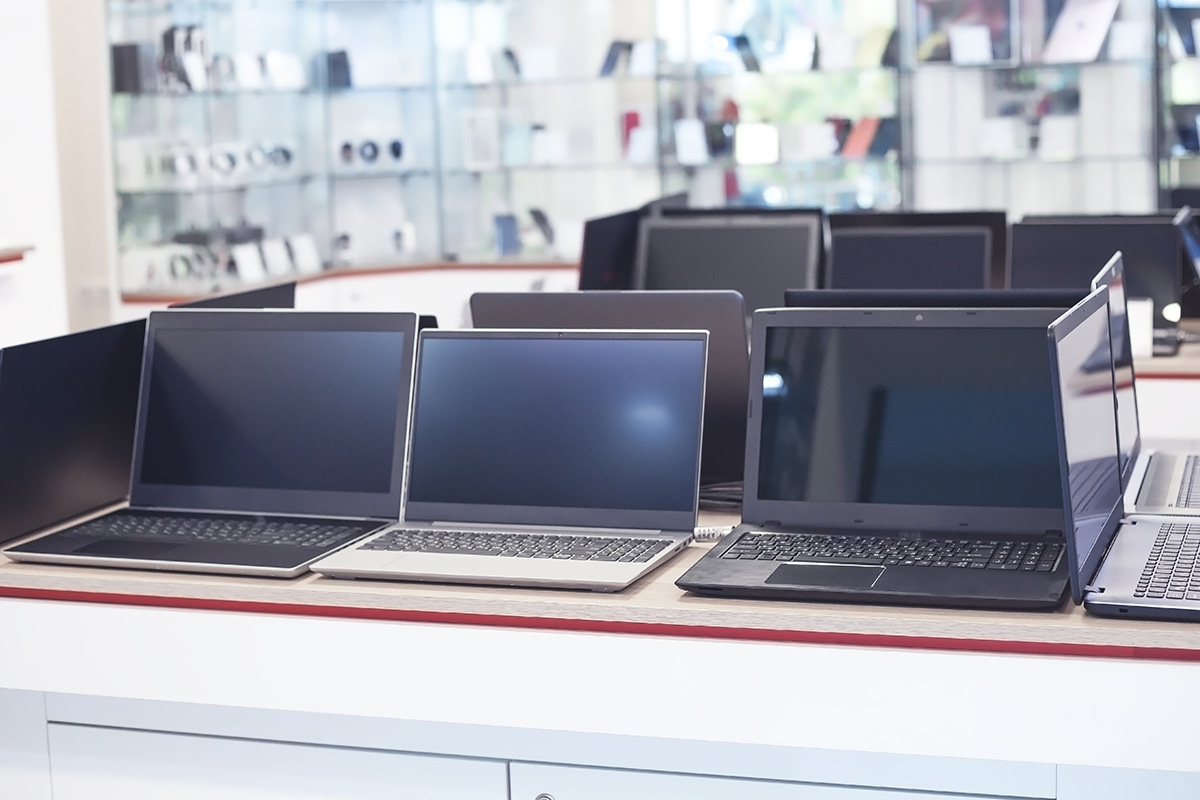
Laser cutting is ideal for producing precise components like connectors, housings, and heat sinks for electronic devices, ensuring minimal material waste and high accuracy.
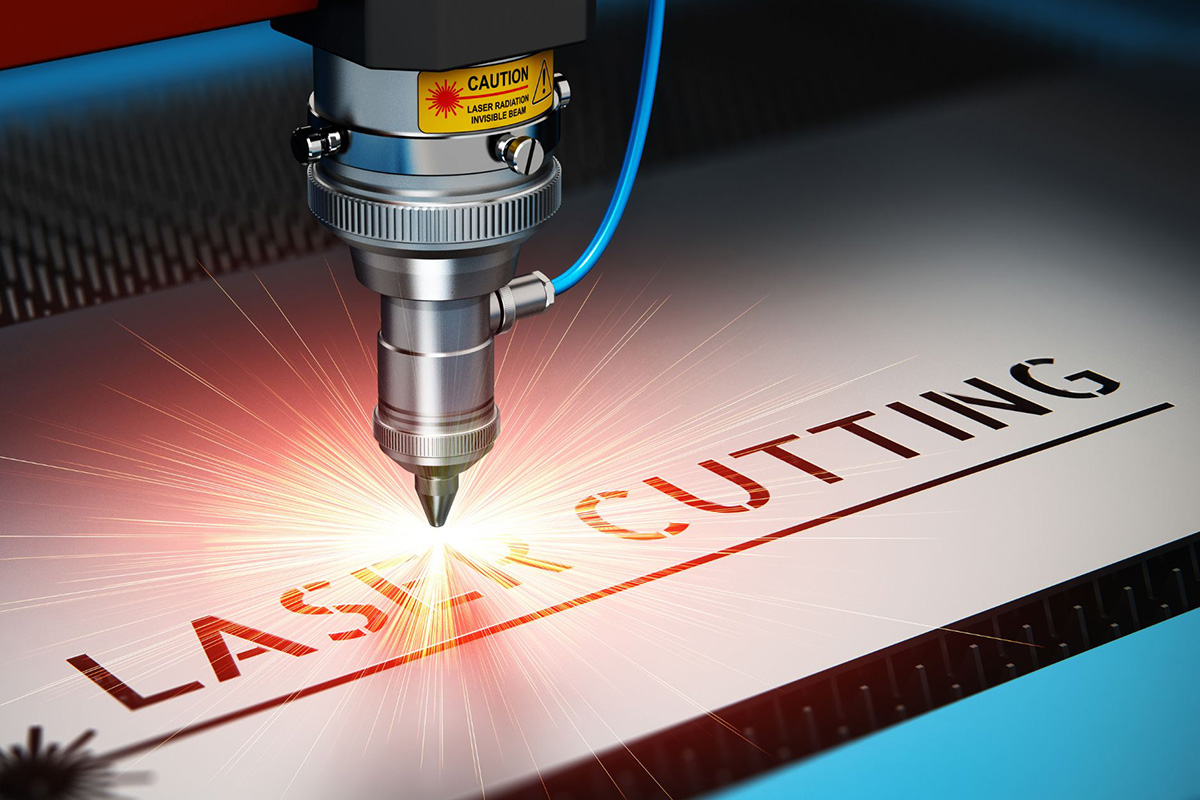
Custom Signage & Graphics
Laser cutting is often employed in creating custom signage, lettering, and graphics, offering clean, intricate designs on materials like acrylic, wood, and metal.
Orders Workflow
Initial Consultation & Design Review
We begin by discussing your project’s goals and reviewing the design to ensure it’s optimized for the specific manufacturing process. At this stage, we suggest improvements or adjustments to enhance efficiency, functionality, and manufacturability.
Material Selection
Our experts assist in selecting the right materials for your product based on performance requirements and compatibility with the manufacturing process. The correct material choice ensures durability, cost-effectiveness, and the desired product functionality.
Design & Engineering
Using advanced CAD and simulation tools, we develop a custom design for your project. This step ensures precise details and identifies potential challenges early in the process, optimizing the design for efficient manufacturing.
Prototyping & Sample Testing
A prototype or sample is created to verify design accuracy, functionality, and performance. Rigorous testing is conducted to ensure the product meets your specifications before moving into full-scale production.
Production Setup & Initial Production
We set up the required machines, molds, or tools for the manufacturing process. The initial production run is performed to confirm the setup, assess quality, and fine-tune settings for optimal results.
Final Production & Quality Control
After final approval, we proceed with full-scale production, ensuring continuous quality checks. Comprehensive inspections at each stage ensure that every part meets the highest standards before delivery.
Advantages of Laser Cutting Your Product
Precision and Accuracy
Laser cutting offers unparalleled precision, ensuring your product is manufactured to tight tolerances and exact specifications, which is crucial for parts that need to fit or function seamlessly.
Versatility in Material Choice
Laser cutting can process a wide variety of materials, from metals and plastics to composites, making it ideal for diverse applications across industries.
Minimal Material Waste
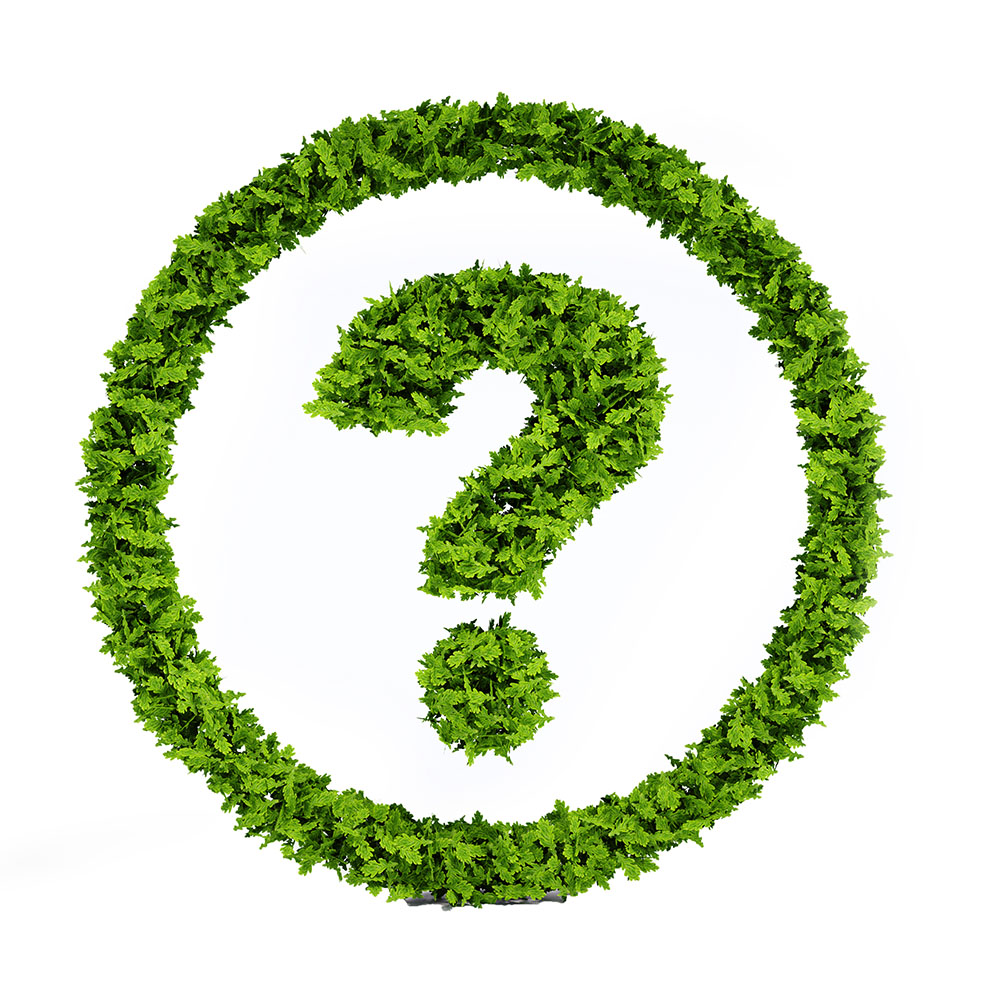
Laser cutting is used in various industries, including automotive, aerospace, medical devices, electronics, and consumer goods, for manufacturing parts, prototypes, and custom designs.
Laser cutting offers faster processing speeds, higher precision, minimal material waste, and no need for tooling, reducing overall production costs and time.
Laser cutting capabilities depend on the material. Generally, carbon steel can be cut up to 25mm, stainless steel and aluminum up to 15mm, and copper up to 12.7mm.
Laser cutting provides high precision, with typical tolerance ranges of ±0.1mm. For most applications, this ensures a perfect fit and clean cuts.
Laser cutting can handle materials such as stainless steel, aluminum, copper, brass, acrylic, and wood. Different materials may require specific laser types, such as CO2 or fiber lasers.
Laser cutting is a precise and advanced manufacturing process that uses a focused laser beam to cut or engrave materials. The laser beam generates intense heat that melts, burns, or vaporizes the material, leaving a clean and accurate cut. This method is highly versatile and can be used on a wide variety of materials, including metals, plastics, wood, ceramics, and composites. It’s especially favored for its high precision, speed, and ability to produce intricate and complex geometries.
KingStar Mold uses both CO2 and fiber lasers, depending on the material and cutting requirements. These lasers offer high energy efficiency and fast cutting speeds for both small and large-scale projects.
Yes, laser cutting is ideal for prototyping as it allows for rapid production of parts with precise specifications, making it an efficient method for testing designs before full-scale production.
We follow strict quality control standards, ensuring high precision and minimal defects, with tolerance levels maintained within ±0.1mm, and we provide comprehensive inspection before delivery.
Lead times vary based on material, complexity, and order volume. Typically, we offer fast turnaround times ranging from 5 to 7 days for laser cutting projects.
Yes, KingStar Mold’s laser cutting services can handle a range of material thicknesses. For example, we can cut carbon steel up to 25mm and stainless steel up to 15mm.
Yes, KingStar Mold provides custom laser cutting services tailored to your specifications, ensuring high-quality cuts and precision for a variety of materials.