Knowledge Center
For mold making, plastic injection molding, prototyping, machining, die casting, stamping and on demand manufacturing
Browse our articles
Don’t know where to start? Try these articles
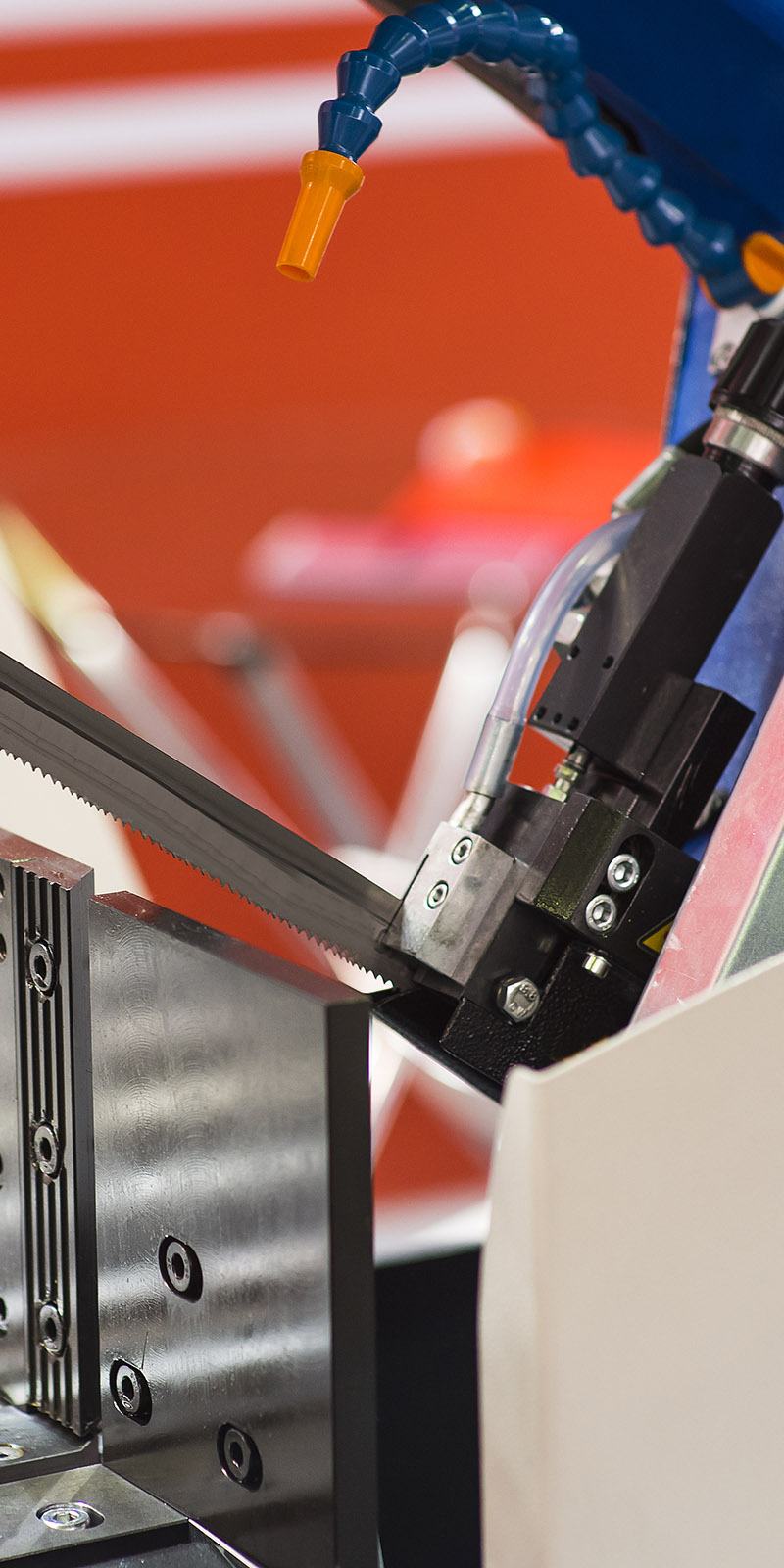
Why Choose Us
We Believe You Will Choose Us Again
Only companies with extensive market experience and a deep understanding of customer needs can offer the best service.
Skilled
High-precision production equipment, skilled production staff, and guaranteed delivery times.
Experienced
Over ten years of industry experience, with a mature quotation system and technical support.
Thoughtful
Customized processing options that save time and effort, with active support throughout pre-sales and post-sales.
Equipped
Engineers review designs to identify and resolve potential issues, backed by advanced testing equipment.
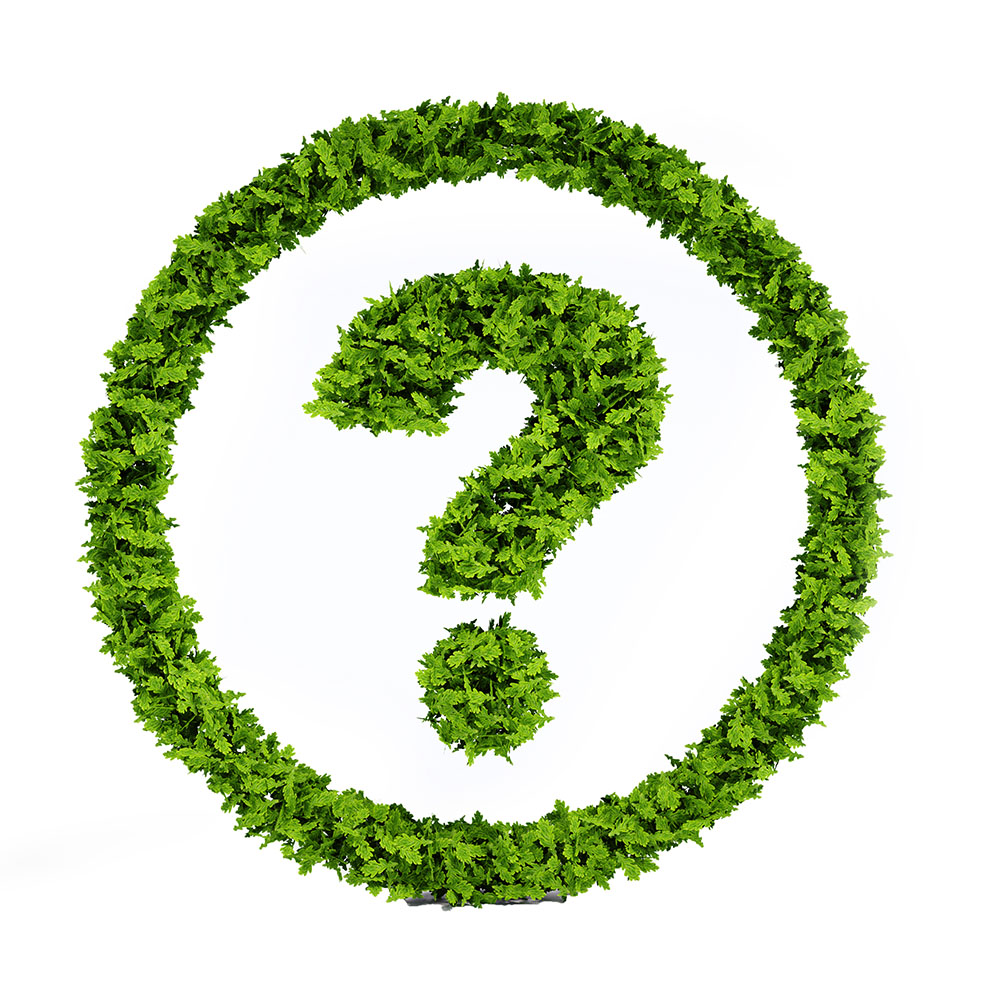
FAQs
We implement rigorous quality control processes throughout the manufacturing process, from design to final production, to ensure every product meets the highest standards.
You can request a quote directly from our website by providing your project details, including material requirements, design specifications, and quantities.
Yes, we offer custom solutions tailored to meet specific client needs, including OEM customization, prototype development, and precision machining.
Lead time varies based on the complexity and scale of the project. Typically, our lead time is between 2 to 6 weeks after confirming design and material specifications.
We specialize in manufacturing using high-quality materials like ABS, PA, PBT, PC, PE, PEEK, PLA, PMMA, POM, PP, PPS, PS, PPSU, PTFE, PVC, and TPU.
KingStar Mold provides precision manufacturing services for industries such as automotive, furniture, household, solar panel, pet products, plastic cutlery, plastic baskets, plastic POS displays, and baby products.