China plays a dominant role in the global cooler market, supplying a vast range of products from rugged hard coolers to portable cooler jugs. With its extensive manufacturing infrastructure, skilled labor force, and cost-effective production capabilities, China has become the go-to hub for international brands seeking to source high-quality coolers at competitive prices.
However, not all suppliers are created equal. The sheer volume of manufacturers can make it difficult to identify reliable partners who consistently deliver on quality, lead times, and customization. Many importers have learned the hard way that low pricing alone doesn’t guarantee dependable service or durable products.
That’s where KingStar sets itself apart. As a seasoned plastic product manufacturer, KingStar combines engineering expertise with state-of-the-art production to offer factory-direct coolers that rival top brands—at a fraction of the cost. With a commitment to quality, responsive service, and flexible solutions, KingStar is the partner you can count on in China’s competitive cooler industry.
- 1. Who We Are: KingStar’s Manufacturing Strength
- 2. Our Cooler Product Line
- 3. Manufacturing Excellence at KingStar
- 4. Competitive Advantages of Choosing KingStar
- 5. What to Look for in a Wholesale Cooler Manufacturer
- 6. KingStar’s Clients and Export Markets
- 7. Customization and OEM/ODM Capabilities
- 8. Sustainable and Durable Materials
- Conclusion: Partner with KingStar for Reliable, Affordable Coolers
1. Who We Are: KingStar’s Manufacturing Strength
As one of China’s most reliable factory-direct suppliers, KingStar brings together engineering precision, manufacturing scalability, and product innovation—all under one roof. Our journey from mold-making experts to trusted cooler manufacturers is backed by decades of hands-on industrial experience.
1.1 Precision Mold Making: The Foundation of Our Manufacturing Strength
At our core, KingStar is a mold and plastic parts manufacturer with a sharp focus on precision and performance. This background sets us apart in the cooler industry.
- Years of Industrial Experience
We’ve spent years serving sectors like automotive, furniture, and appliances—industries where durability, tolerance control, and consistency are non-negotiable. That same level of precision now powers our cooler production line. - Advanced Equipment and Skilled Engineering Team
Our factory is equipped with CNC machining centers, EDM, and automated injection systems. Backed by a team of experienced engineers and mold technicians, we ensure every mold we build is accurate down to the micrometer. - Full Quality Control System
We maintain strict in-house QC protocols throughout the production process. From raw materials to finished coolers, every stage is monitored for dimensional accuracy, material integrity, and functional performance.
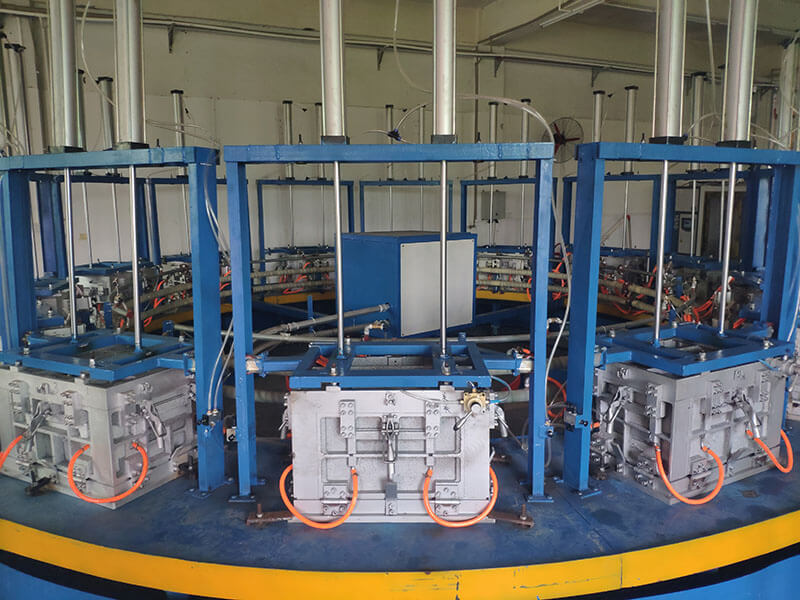
1.2 Cooler Manufacturing: Powered by Engineering, Not Guesswork
We didn’t jump into cooler manufacturing blindly—we engineered our way into it. Every KingStar cooler is the result of rigorous R&D, material analysis, and user-focused design.
- From Mold to Market, In-House
We design and manufacture our own cooler molds, giving us full control over the structure, insulation thickness, lid fit, and hardware integration. This translates to better durability, longer ice retention, and stronger structural performance. - Rotomolding & Injection: Dual Production Capabilities
Depending on the product type, we use both rotomolding (for rugged hard coolers) and injection molding (for lightweight, portable options). Our technical versatility allows us to meet a wide range of market needs. - Design with Real-World Use in Mind
From non-slip feet and pressure-release valves to secure latches and UV-resistant shells, KingStar coolers are built for the real outdoors—not just the showroom floor.
1.3 Factory-Direct Supply: Your Cost-Effective, Scalable Partner
Working with KingStar means partnering directly with the source. We’re not a trading company or reseller—we’re the people who build the molds, produce the parts, and assemble the coolers.
- Shorter Lead Times, Better Pricing
Because we control every stage in-house, we can deliver faster and price more competitively than many brands relying on outsourced production. - Flexible Order Volumes
Whether you’re launching a startup brand or replenishing inventory for retail chains, our scalable production model supports low-MOQ trial orders as well as large-scale shipments. - OEM/ODM Ready
Need custom branding or a unique cooler design? Our in-house team works with you to develop and manufacture tailored solutions that reflect your brand identity while meeting your performance expectations.
2. Our Cooler Product Line
At KingStar, we offer a diverse cooler product line designed to meet both everyday use and extreme outdoor conditions. From rugged hard coolers to lightweight cooler jugs, each product is engineered for performance, longevity, and style.
2.1 Product Categories: A Full Range to Fit Every Application
We manufacture a wide selection of coolers to suit different markets and end-users, whether for backyard BBQs, long-haul fishing trips, or professional outdoor use.
- Hard Coolers
Our hard coolers come in two structural types—rotomolded and injection molded—each designed for specific durability and cost targets.
– Rotomolded Coolers: Built with seamless, one-piece construction and thick insulated walls, these are ideal for extended ice retention and extreme environments like camping, off-roading, or marine use.
– Injection Molded Coolers: Lightweight, cost-effective, and ideal for everyday use or short outings. These offer quicker production turnaround and sleek modern aesthetics. - Soft Coolers & Cooler Bags
- Specialty Coolers
We also offer niche-specific coolers tailored to particular use cases:
– Fishing Coolers: Include features like ruler-embedded lids, fish-keeping insulation, and UV-resistant shells.
– Camping Coolers: Durable, bear-resistant designs with multi-day ice retention.
– Travel Coolers: Compact, lightweight options that fit easily in cars or luggage.
2.2 Customization Options: Make It Yours
Customization is one of KingStar’s biggest strengths. As a factory-direct OEM/ODM supplier, we offer full flexibility in adapting our cooler designs to your brand and market needs.
- Sizes and Capacities
From 5L lunch box coolers to 100L outdoor coolers, we support a wide range of volume options. Internal layouts and compartments can be adjusted based on user requirements. - Color Options and Surface Finishes
We offer both standard and custom color matching. Whether you want classic matte finishes, camo prints, or high-gloss colorways, our production lines support detailed surface treatments and UV-resistant coatings. - OEM/ODM Branding Support
Whether you’re a retailer, distributor, or launching your own brand, we can add your logo via screen printing, laser engraving, embossing, or molded-in branding. Our team can also help you develop exclusive cooler designs, from concept sketches to mold development and packaging design.
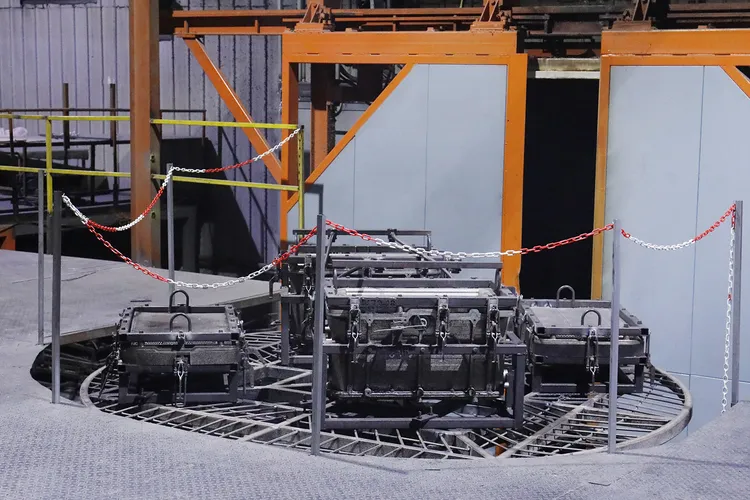
3. Manufacturing Excellence at KingStar
At KingStar, manufacturing isn’t just about producing coolers—it’s about delivering performance, reliability, and consistency with every unit. Our cooler production process reflects the same precision and control that has made us a trusted mold manufacturer for years.
3.1 Advanced Rotomolding and Insulation Technology
We apply cutting-edge rotomolding techniques to build coolers with seamless construction and exceptional durability.
- Seamless, One-Piece Construction
Our rotomolded coolers are created in a single mold cycle, resulting in a thick, uniform wall without any joints or weak points. This construction enhances impact resistance and helps the cooler withstand rugged outdoor use. - Superior Ice Retention Performance
Each cooler is filled with high-density polyurethane foam insulation, optimized for thermal efficiency. Combined with tight-sealing gaskets and secure latches, our coolers can keep ice frozen for days—making them ideal for camping, fishing, and travel. - Consistency Across Batches
Thanks to automated temperature and rotation controls during molding, we ensure uniform wall thickness and cavity fill across every unit, reducing product variation and failure rates.
3.2 In-House Mold Design: Precision Starts at the Source
As a company rooted in mold engineering, we don’t rely on outsourced tooling. Every cooler mold is designed and fabricated in our own factory.
- High-Precision Tooling
We use CNC machining, EDM, and advanced CAD/CAM software to craft complex mold structures with extreme dimensional accuracy. This ensures that all parts—from cooler bodies to lids and drain plugs—fit and function perfectly. - Faster Product Development
By handling tooling in-house, we reduce lead times for new product development, enabling faster iterations and quicker delivery for OEM/ODM clients. - Durable Mold Materials
We build our molds from hardened steel and aluminum, designed for long production lifecycles and minimal maintenance, which translates to cost efficiency and production stability for our customers.
3.3 Rigorous Quality Control at Every Stage
Quality isn’t just a checkpoint—it’s built into every step of our manufacturing.
- Incoming Material Checks
We inspect all raw materials—including PE plastics, insulation foam, and hardware components—for compliance with quality standards before they enter production. - In-Process Inspections
During manufacturing, we monitor temperature, pressure, and molding consistency. Each product undergoes structural integrity testing, seal verification, and visual inspection before assembly. - Final Product Testing
Finished coolers are tested for ice retention, drop resistance, lid seal strength, and overall functionality to ensure they meet both KingStar standards and customer specifications.
4. Competitive Advantages of Choosing KingStar
Factory-Direct Pricing Without Middlemen
As a direct manufacturer, we eliminate unnecessary markup layers, allowing you to access premium coolers at a much lower cost than brand-name alternatives.
Lower MOQs for Startups and Flexible Scaling for Bulk Orders
Whether you’re launching a new outdoor brand or managing large retail channels, our order quantities are designed to fit your growth stage.
Fast Lead Times and Reliable Export Logistics
We streamline production and shipping with an experienced logistics team to ensure your coolers arrive on time, wherever you are in the world.
24/7 Customer Support for Global Clients
Our dedicated team provides around-the-clock service, helping you track orders, adjust specs, and solve problems across any time zone.
5. What to Look for in a Wholesale Cooler Manufacturer
Choosing the right cooler manufacturer is critical to ensuring your products meet customer expectations and are delivered on time. Here’s what you should prioritize when selecting a supplier and how KingStar stands out in each area.
5.1 Product Quality: Ensuring Longevity and Performance
- Material Integrity
Ensure the manufacturer uses durable, high-quality materials. KingStar uses premium rotomolded plastic and high-density polyurethane foam for superior insulation and long-lasting performance. - Construction Quality
Our in-house precision tooling ensures every cooler is built to last, with seamless construction that enhances durability and ice retention.
5.2 Production Capacity: Meeting Your Volume Needs
Whether you’re a startup or an established brand, it’s important to work with a manufacturer that can accommodate both small orders and large-scale production. At KingStar, we offer flexible order quantities, ensuring we can meet the demand no matter how large or small.
Our advanced production systems and in-house mold design enable us to maintain fast lead times without compromising on quality.
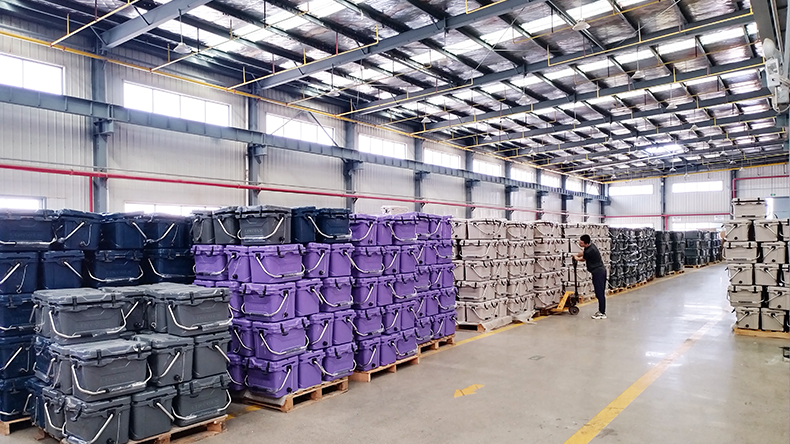
5.3 Customer Service: Partnering for Success
A reliable manufacturer should offer prompt responses and support. KingStar provides 24/7 customer service to ensure your questions are addressed promptly and any issues are resolved quickly.
Plus, we don’t just wait for issues to arise—we work closely with you to anticipate needs and optimize designs, ensuring smooth project execution from start to finish.
5.4 Competitive Pricing: Value Without Compromise
- Direct-to-Customer Pricing
By eliminating intermediaries, KingStar offers factory-direct pricing that keeps costs down while maintaining high standards for materials and craftsmanship. - Affordable Customization
We provide cost-effective options for custom designs and branding, ensuring that you can offer tailored products without excessive price hikes.
6. KingStar’s Clients and Export Markets
KingStar’s coolers are trusted by customers across the globe, with our products reaching markets in North America, Europe, Oceania, and beyond. We have built a reputation for delivering reliable, high-performance coolers that meet the demands of diverse outdoor activities, from fishing and camping to beach outings and tailgating.
Our clients include outdoor retailers, wholesalers, and private brands that rely on KingStar’s factory-direct pricing and premium product quality. These partners appreciate our ability to scale production to their needs, whether they require small quantities for new product lines or large orders for established brands.
We are proud of the relationships we’ve developed with clients who value our fast lead times, excellent customer support, and cost-effective solutions. Their success with KingStar coolers speaks to our commitment to excellence and our ability to deliver on promises.
7. Customization and OEM/ODM Capabilities
At KingStar, we offer a comprehensive one-stop solution for custom cooler development, from initial design to mass production. Our integrated approach allows us to handle every step of the process, ensuring high-quality, tailored products delivered efficiently.
7.1 One-Stop Product Development: From Concept to Completion
- Design and Prototyping
Our team works closely with you to create custom cooler designs that align with your brand’s vision. Using advanced 3D modeling software and rapid prototyping, we bring your ideas to life quickly and accurately. - Mold Making and Tooling
We leverage our expertise in mold design and manufacturing to produce high-precision molds tailored to your product’s unique specifications. This ensures that each cooler is crafted with exacting standards for durability and functionality. - Mass Production
Once the design and prototyping phases are complete, we move to mass production, where we efficiently produce large volumes of your custom coolers, maintaining consistent quality and timely delivery.
For more details on our full customization capabilities, check out our One-Stop Product Development Page.
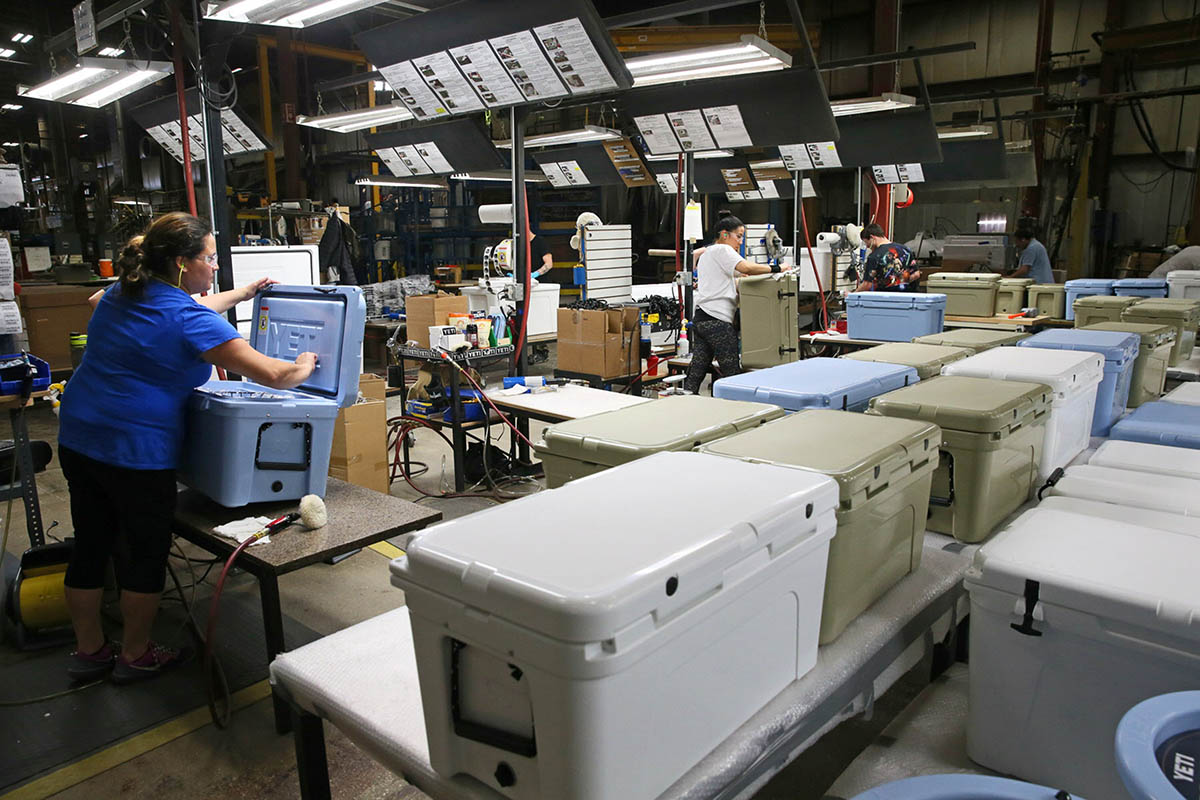
7.2 Tailored Branding for Your Business
- Custom Logos and Branding
We offer complete customization of your cooler’s branding, from logo printing to color schemes, helping your products stand out in a crowded market. - Custom Handles, Colors, and Packaging
Beyond the basic design, we also customize functional elements such as handles, latches, and packaging to match your brand’s aesthetic and operational needs.
7.3 Protecting Your Ideas with NDA
At KingStar, we understand the importance of protecting your intellectual property and product designs. To ensure confidentiality and secure your ideas, we offer Non-Disclosure Agreements (NDAs) to all our clients, safeguarding your proprietary information throughout the entire development process.
8. Sustainable and Durable Materials
At KingStar, we prioritize sustainability and durability in every cooler we produce. Our commitment to using eco-friendly and long-lasting materials ensures that your coolers are built to withstand the elements while minimizing environmental impact.
8.1 Eco-Friendly Insulation and Materials
- Polyurethane Foam Insulation
We use high-density polyurethane foam for superior insulation performance. Not only does it provide excellent ice retention, but it is also eco-friendly, contributing to a greener manufacturing process. - Rotomolded Plastic
Our coolers are made from rotomolded polyethylene plastic, a durable and environmentally responsible material that resists impact, corrosion, and UV damage. This material ensures the cooler’s longevity, even in harsh outdoor conditions.
Other high-performance plastics we use include:
- High-Density Polyethylene (HDPE): Known for its exceptional strength, UV resistance, and low moisture absorption, HDPE makes our coolers durable and weather-resistant.
- Polypropylene (PP): A lightweight yet strong plastic, PP offers superior impact resistance and is known for being resistant to chemicals and fatigue, making it ideal for the rugged outdoors.
- ABS (Acrylonitrile Butadiene Styrene): Known for its toughness and high impact resistance, ABS ensures that the coolers maintain structural integrity even under harsh conditions.
8.2 Rugged and Reusable Construction
- Heavy-Duty, UV-Resistant Shell
The rotomolded plastic shell is designed to withstand extreme outdoor environments, offering robust protection against wear and tear. Its UV resistance ensures the cooler won’t degrade from prolonged exposure to sunlight, making it perfect for camping, fishing, and other outdoor activities. - Long-Lasting Hardware and Components
We use corrosion-resistant stainless steel for latches and handles, ensuring that all components are rugged and durable, capable of withstanding heavy use.
8.3 Outstanding Material Features
- Recyclability
All of our coolers are designed with recyclable materials, promoting sustainability and reducing waste at the end of the product’s life cycle. - Impact Resistance
Our coolers are built to survive tough conditions, from being dropped on rocky surfaces to withstanding extreme temperature fluctuations, ensuring they perform reliably for years.
Conclusion: Partner with KingStar for Reliable, Affordable Coolers
When you choose KingStar, you’re partnering with a factory-direct manufacturer committed to delivering premium coolers at competitive prices. With our expertise in mold design, advanced materials, and customization options, we provide coolers that are not only durable and eco-friendly but also tailored to meet your unique needs.
Our factory-direct pricing eliminates the middleman, ensuring you get high-quality products at the best possible value. Whether you’re looking for hard coolers, soft coolers, or specialized options, KingStar offers reliable solutions backed by exceptional customer service and fast lead times.
Ready to take the next step? Contact us today for a catalog, sample, or quotation, and let us help you provide the best coolers for your customers.