- What is Mold Flow Analysis?
- Why is Mold Flow Analysis Crucial?
- 1. Evaluating and Optimizing Product Design
- 2. Determining the Best Design Before Mold Design, Simplifying Processes, and Improving Yield
- 3. Evaluating and Optimizing Existing Design Plans, Enhancing Mold Design Accuracy
- 4. Identifying the Causes of Trial Mold Issues and Formulating Solutions, Reducing Mold Trial Frequency
- How is Mold Flow Analysis Different from DFM?
- How Does Mold Flow Analysis Work?
- Preparation Steps
- Formal Analysis Steps
- 1. Filling Analysis
- 2. Pressure Distribution Check
- 3. Melt Front Temperature Monitoring
- 4. Clamp Force Monitoring
- 5. Maximum Shear Rate & Shear Stress at Wall Monitoring
- 6. Weld Lines Monitoring
- 7. Ventilation and Air Trap Analysis
- 8. Shrinkage and Warpage Prediction
- 9. Frozen Layer Fraction Monitoring
- 10. Sink Mark Estimate
- 11. Cooling Analysis
- 12. Deflection Analysis
- Key Factors Analyzed During Mold Flow Analysis
- What Are the Key Benefits of Mold Flow Analysis?
- What Features to Look for in Mold Flow Software?
- How is Mold Flow Analysis Applied in Industry?
- Examples of Specific Products or Case Studies
- How KingStar Mold Uses Mold Flow Analysis
- Conclusion
What is Mold Flow Analysis?
Mold Flow Analysis (MFA) is a simulation-based tool used in the injection molding process to predict and optimize the flow of molten plastic within a mold. It helps manufacturers identify potential issues such as material distribution, cooling times, and pressure variations, which can affect the quality and efficiency of the final product.
By analyzing how the material flows, cools, and solidifies inside the mold, MFA allows engineers to optimize the design before physical production begins. This reduces the risk of defects such as warping, short shots, and air traps, and ensures more efficient production with less waste and faster cycle times.
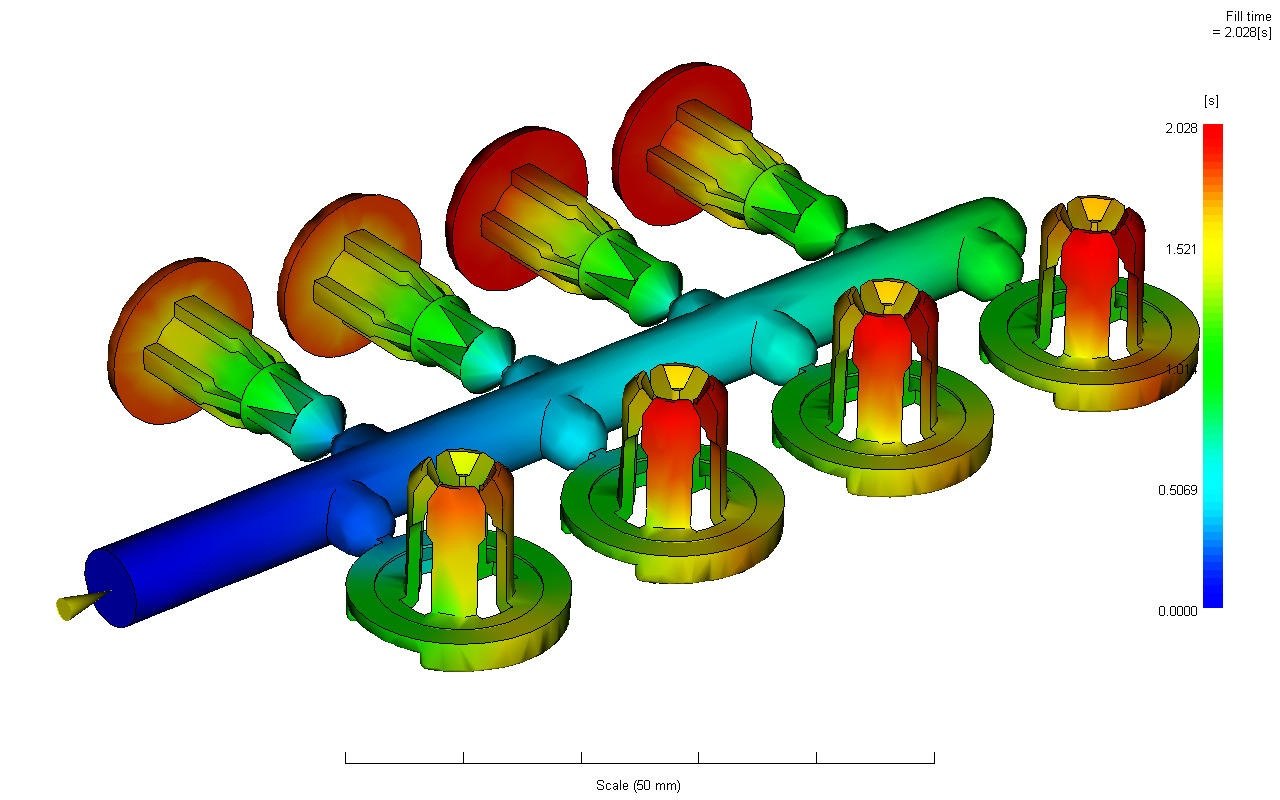
Why is Mold Flow Analysis Crucial?
Current Mold Flow Analysis software can load 3D files of almost any product and offers various functions such as automatic finite element meshing, geometric modeling, solving calculations, and data output. The results generated by the software provide valuable insights, helping us obtain information about the product’s filling process, packing pressure, surface quality, deformation state, cooling efficiency, optimal molding process, machine requirements, and more.
With this information, we can directly observe whether the product filling is balanced, whether there are issues like hesitation or short shots, which areas may have insufficient packing pressure, the presence of weld lines and their strength and visibility, locations where air traps exist and whether they are positioned at easy-to-vent areas, areas prone to shrinkage due to poor product or mold design, areas likely to suffer from burning, discoloration, or even cracking, the deformation trend and amount of deformation, local flatness, the number and size of the gate positions, which areas require venting design, which regions of the cooling system need improvement, and the best molding parameters for producing higher-quality products.
By analyzing these results, we can identify potential issues during the product design stage, before and after mold design, and during product trial runs. This allows us to proactively reduce and avoid possible problems, formulate corresponding countermeasures, and significantly reduce unnecessary costs and major losses caused by the “trial-and-error” approach during mold processing and usage.
The role of Mold Flow Analysis is also specifically reflected in the following four aspects:
1. Evaluating and Optimizing Product Design
By analyzing the results of filling, deformation, shrinkage, weld lines, air traps, pressure, and other factors, Mold Flow Analysis helps determine which areas of the product need reinforcement ribs, adjustments in shape design, or modifications to wall thickness to improve overall performance and manufacturability.

2. Determining the Best Design Before Mold Design, Simplifying Processes, and Improving Yield
By analyzing results such as filling, deformation, shrinkage, weld lines, air traps, pressure, cooling, packing pressure, and temperature distribution, Mold Flow Analysis helps quickly identify the optimal mold design from multiple initial or conceptual design options. This approach avoids blind design iterations and reduces the need for repeated mold adjustments and trials, thereby shortening molding cycles, saving significant costs, and completely eliminating the risk of mold failure due to continuous rework.
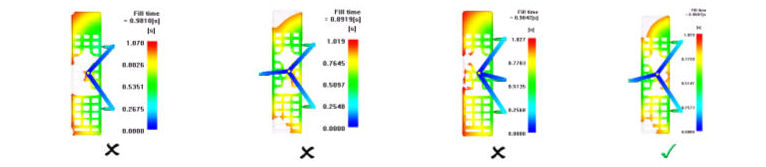
3. Evaluating and Optimizing Existing Design Plans, Enhancing Mold Design Accuracy
By importing existing design plans into Mold Flow Analysis software for simulation, we can comprehensively assess factors such as filling, packing pressure, surface quality, deformation, shrinkage, and cooling. This allows us to determine whether changes or optimizations are necessary to improve the current design, helping to prevent issues caused by unreasonable or flawed design choices.

4. Identifying the Causes of Trial Mold Issues and Formulating Solutions, Reducing Mold Trial Frequency
By importing the existing design and molding plan into Mold Flow Analysis software for simulation, we can analyze various results to identify issues that may not be detected through experience during trial runs. This allows us to pinpoint the root causes of problems and develop targeted solutions, helping to find the correct solution on the first attempt. Additionally, the software enables us to verify the feasibility of improvement solutions in advance, reducing the need for repeated mold trials and revisions.

How is Mold Flow Analysis Different from DFM?
While both Mold Flow Analysis (MFA) and Design for Manufacturability (DFM) are essential in product development, they focus on different aspects of the manufacturing process.
Mold Flow Analysis (MFA)
MFA focuses specifically on the injection molding process. It simulates the flow of molten material inside the mold to predict and address issues related to material distribution, cooling, and solidification. MFA helps optimize the mold design to prevent defects like warping, short shots, and air traps, ensuring the final product is of high quality and produced efficiently.
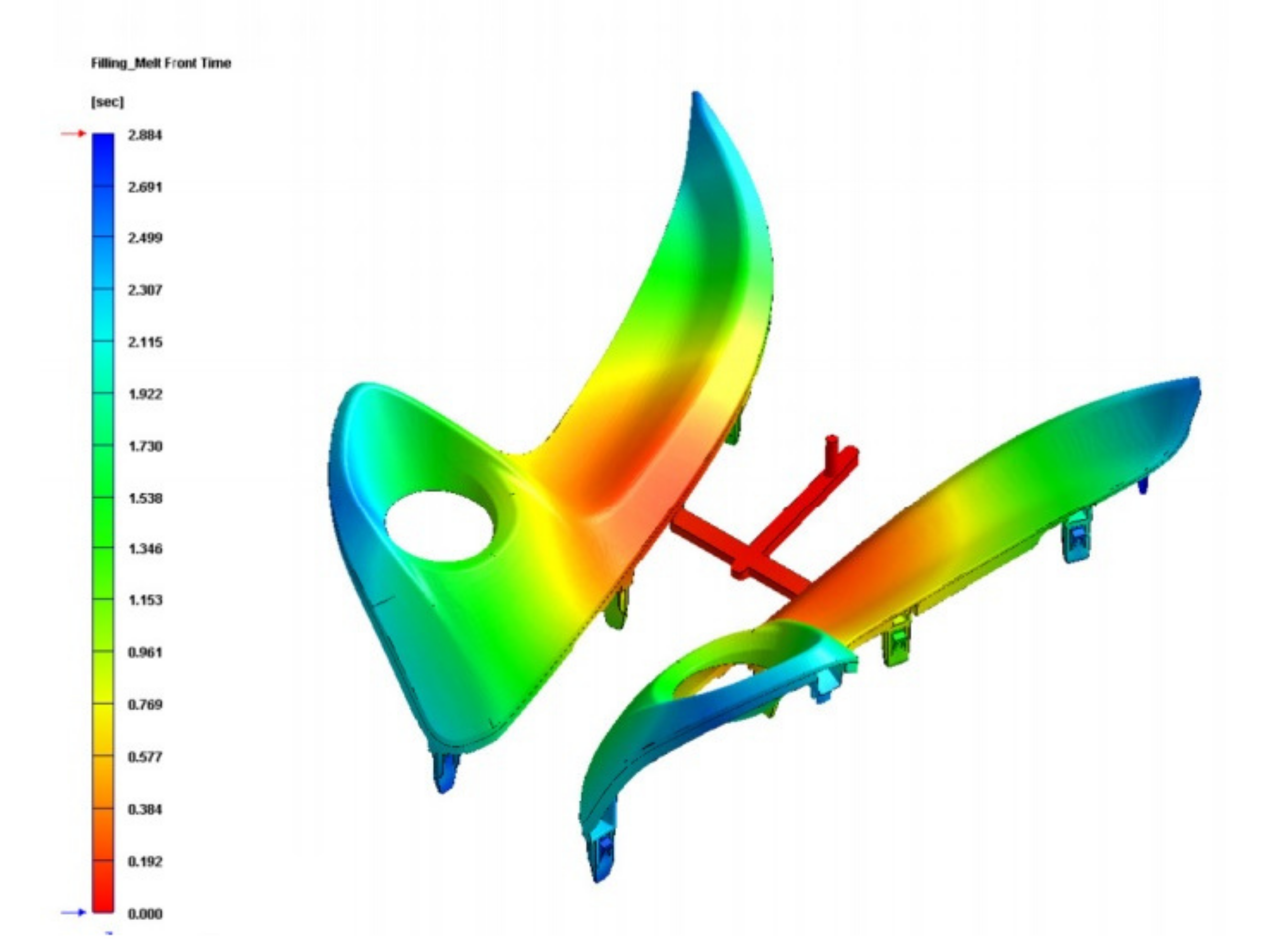

Design for Manufacturability (DFM)
DFM, on the other hand, is a broader approach that looks at the entire product design to ensure it can be easily and cost-effectively manufactured. DFM focuses on simplifying the design to reduce production complexity, avoid manufacturing challenges, and lower overall costs. It considers factors such as material selection, part geometry, assembly, and ease of processing.
In summary, MFA is a process-specific tool used for optimizing the injection molding process, while DFM is a design strategy aimed at making the overall product easier and more cost-effective to produce across various manufacturing methods. Both tools complement each other but serve different purposes in the design and production phases.
How Does Mold Flow Analysis Work?
To illustrate the steps involved in Mold Flow Analysis (MFA), let’s walk through a specific case study step by step. The process can be divided into two main stages: the preparation steps and the formal analysis steps. Each stage plays a crucial role in ensuring a successful outcome for the injection molding process.
Preparation Steps
1. Clarify the Analysis Objective
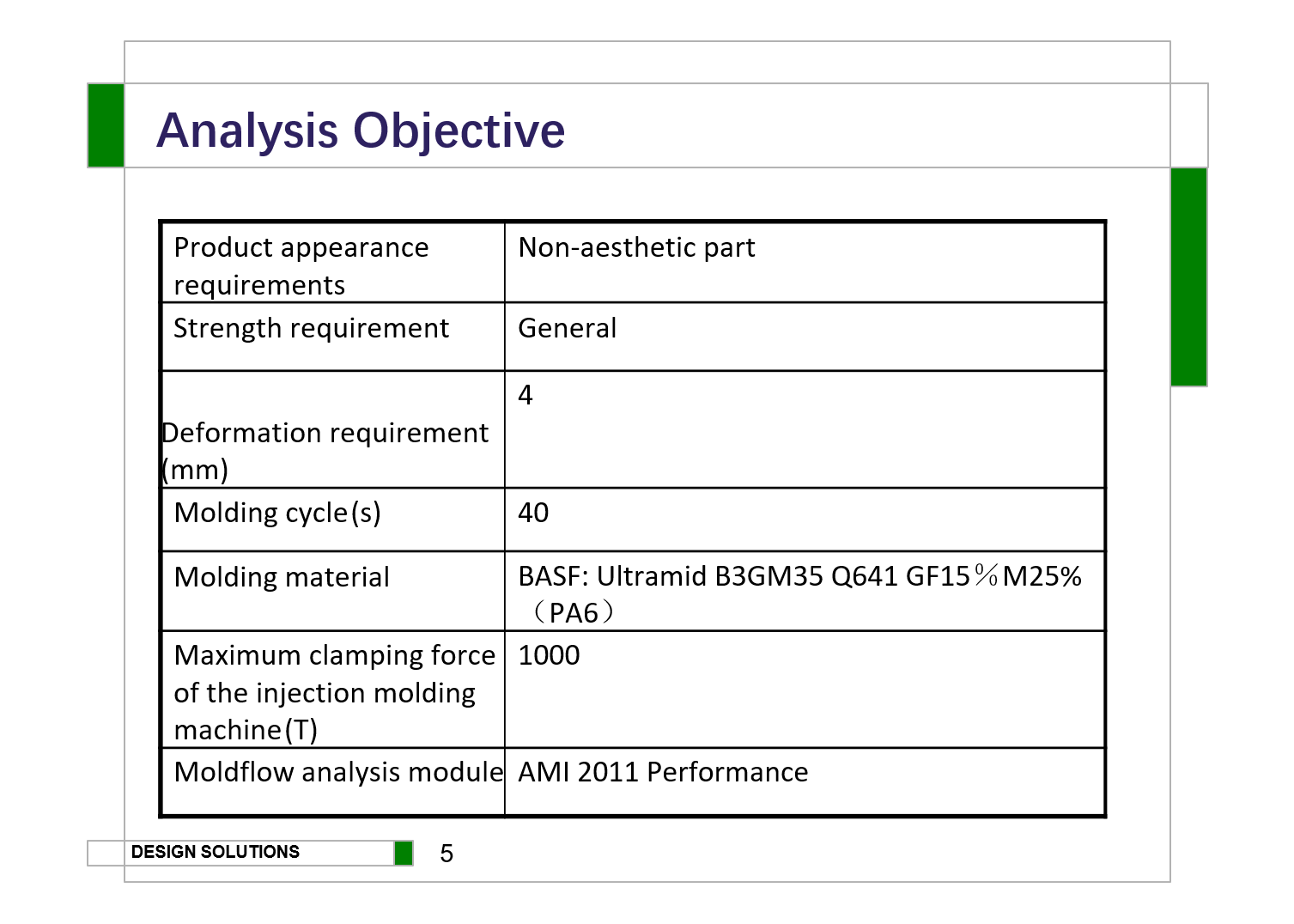
Before starting Mold Flow Analysis, it’s important to clarify the analysis objectives. For new molds, the analysis helps identify potential issues and ensures design feasibility; for existing molds, it aids in solving real-world problems such as incomplete filling or warping.
2. Data Collection
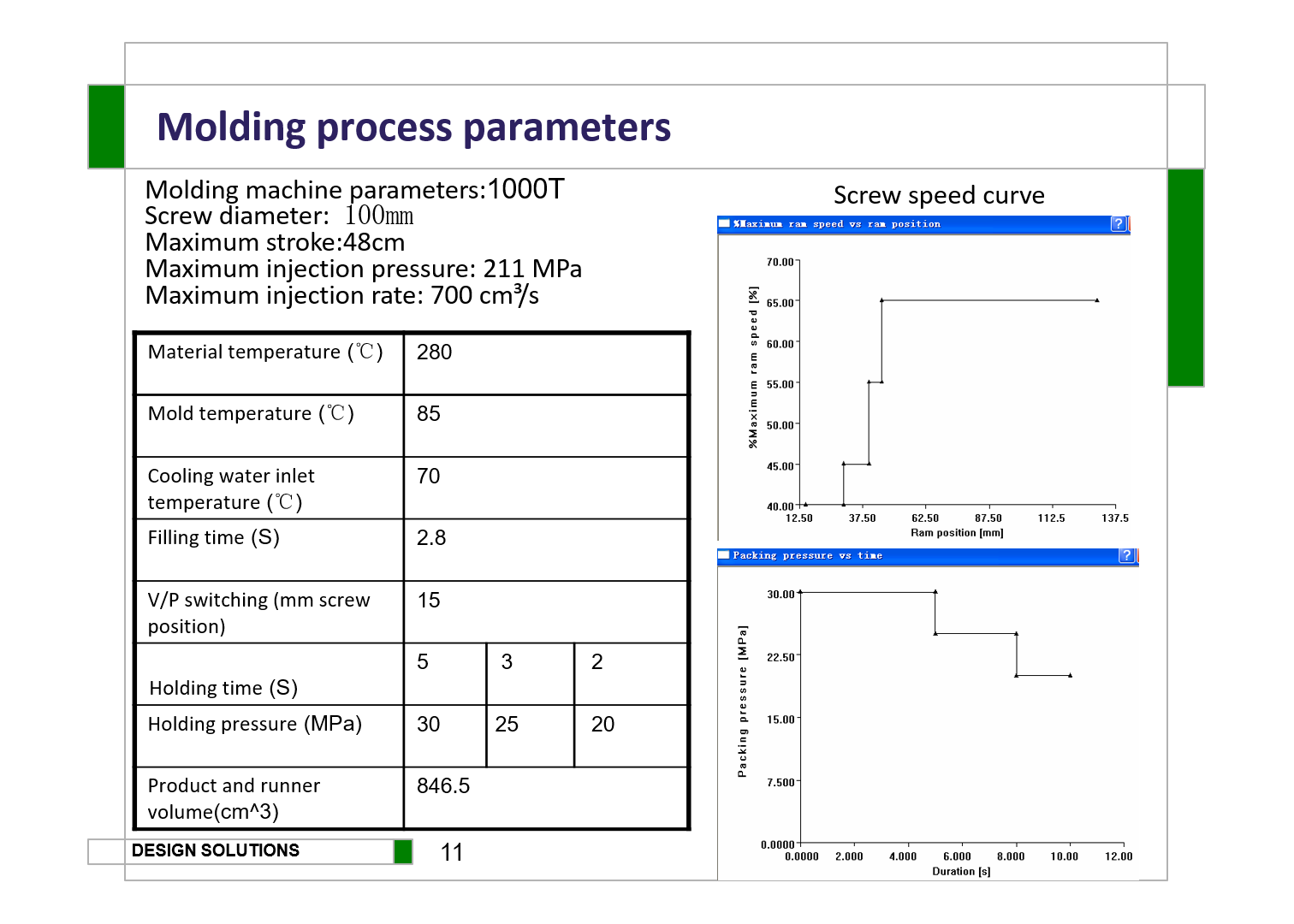
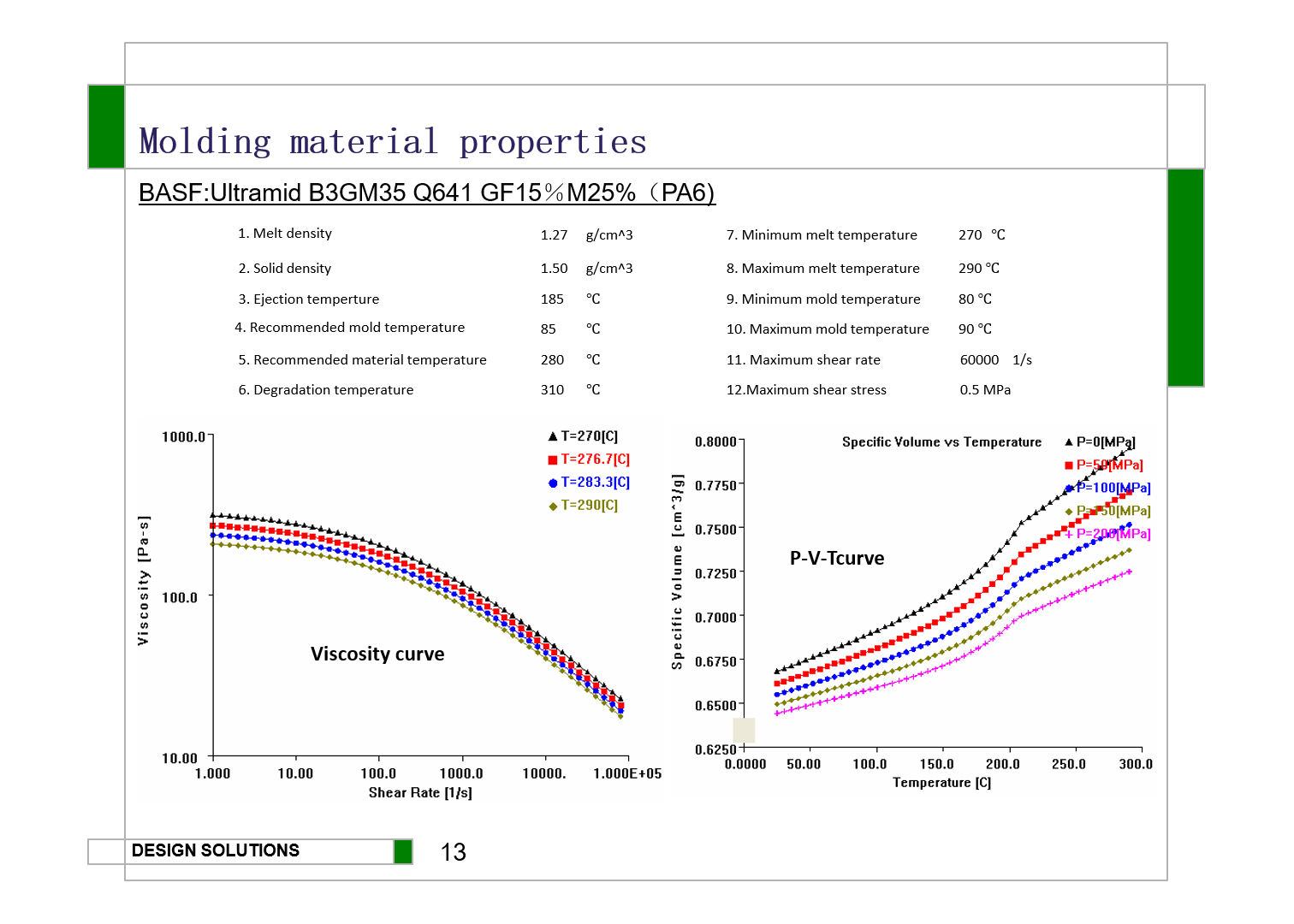
Gather all relevant design and process data, including material properties, process parameters, the product’s 3D model, and mold structure. Material properties are fitted into a UDB file and then imported into the flow analysis software, including data such as material rheology, thermal conductivity, PVT, and filler aspect ratio.
3. Select the Appropriate Mold Flow Analysis Software
Choose the appropriate mold flow analysis software based on the project requirements, such as Moldflow, Moldex3D, etc.
4. Mesh Division
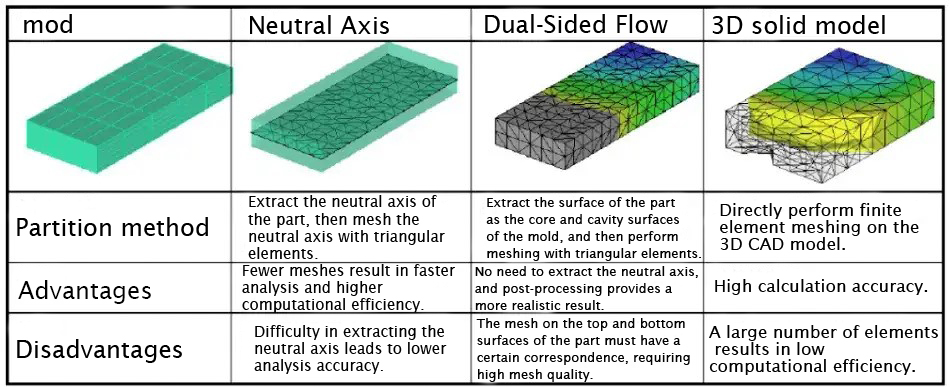
The mesh is the core of Mold Flow Analysis, and high-quality meshing directly impacts the accuracy of the analysis. Ensure the mesh meets the following requirements:
- No free boundaries;
- For dual-sided flow analysis, the mesh matching rate between the upper and lower surfaces must reach 90%;
- The edge length ratio of triangular elements: average <3:1, maximum <6:1;
- No intersections or overlaps between meshes.
Formal Analysis Steps
1. Filling Analysis
The first step in Mold Flow Analysis is filling analysis, which focuses on how the molten material fills the mold cavity. The primary goal is to ensure the injection and packing pressures are balanced and that the injection completes 95%-99% of the part volume. If the injection volume is less than 95% of the part’s total volume, it can lead to insufficient packing pressure, resulting in defects such as shrinkage or material shortages in certain areas.
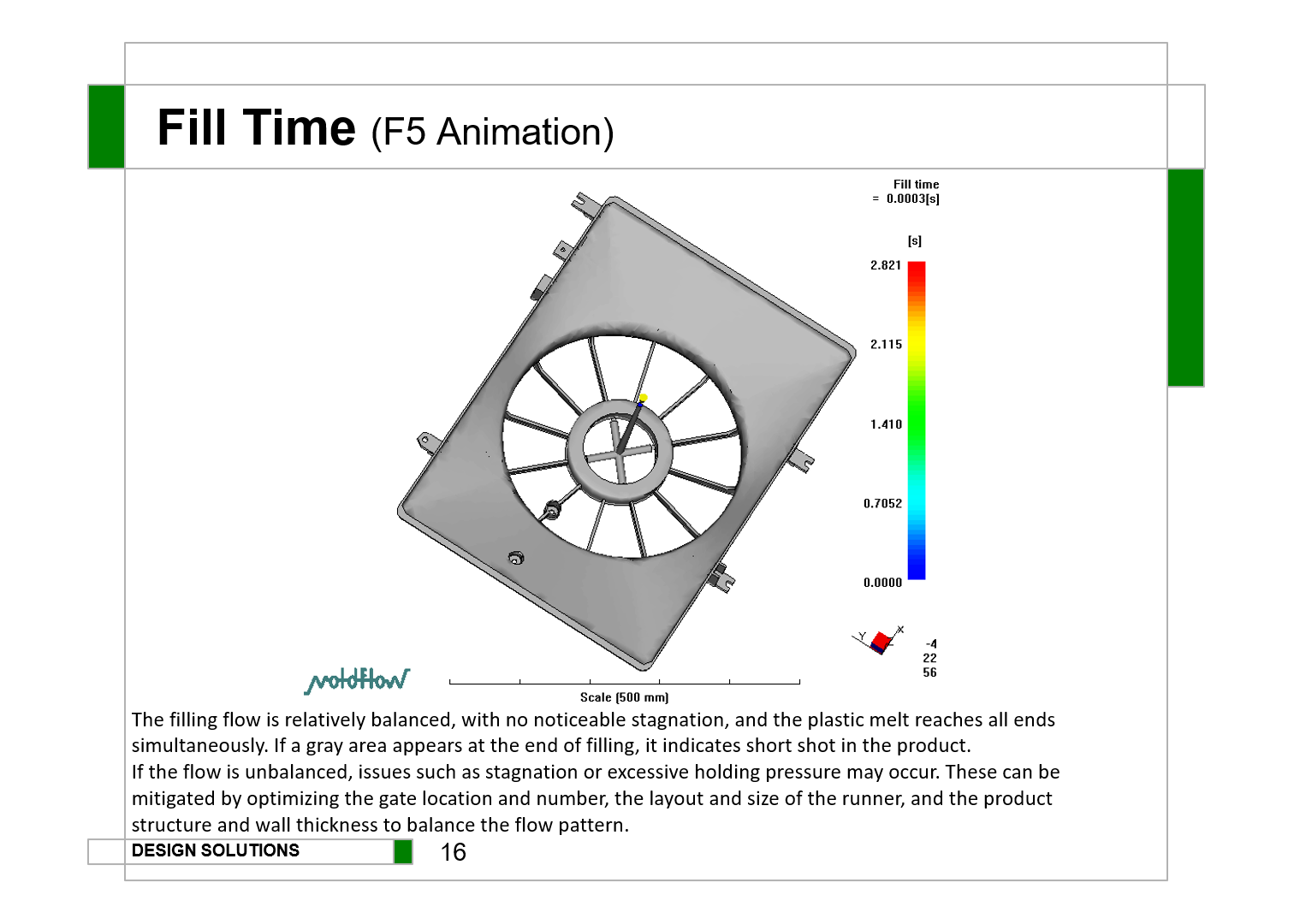
2. Pressure Distribution Check
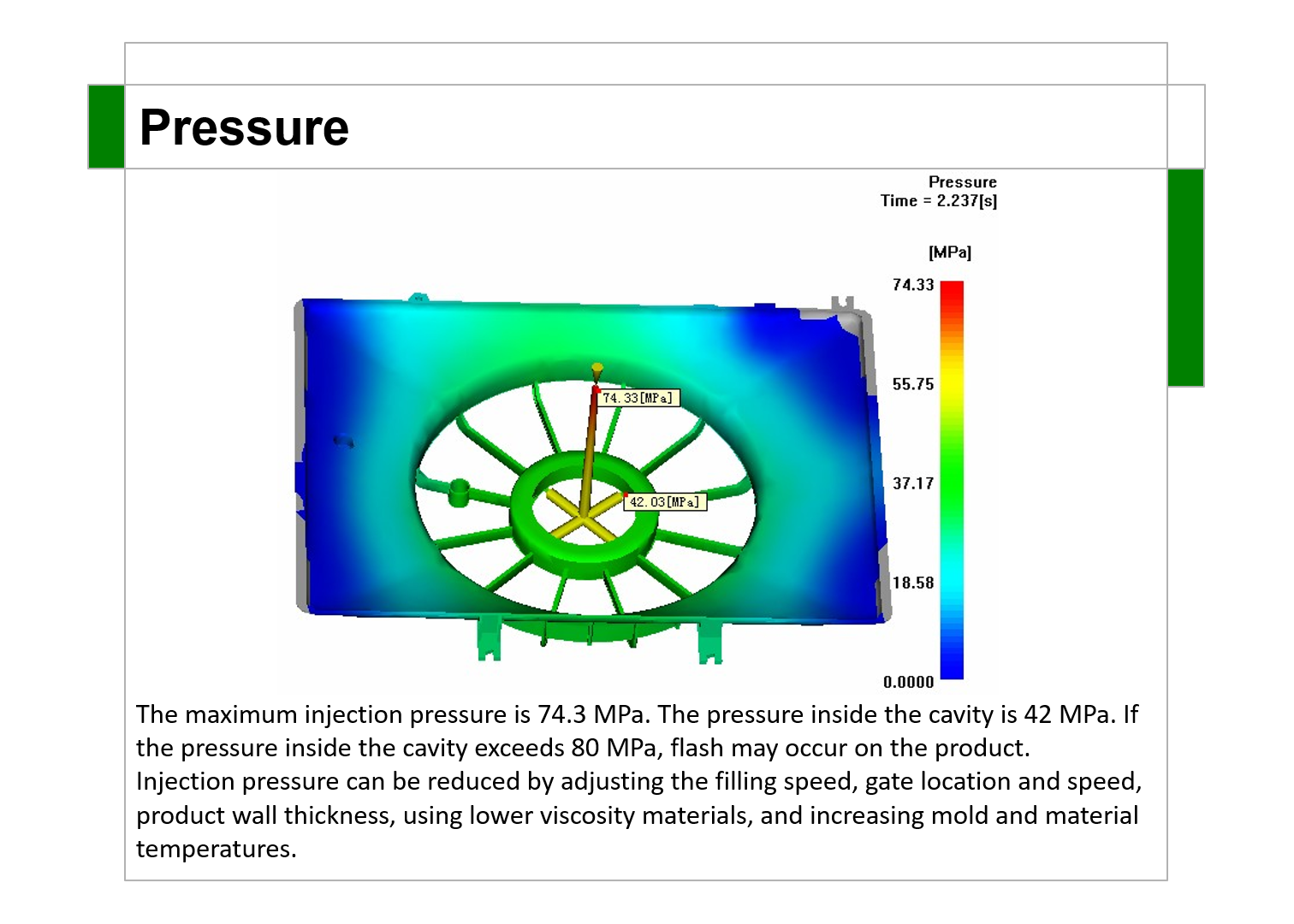
Pressure distribution is checked to ensure it is balanced and symmetrical across the mold cavity. Uneven pressure can cause inconsistent material shrinkage, leading to defects such as sink marks or areas with insufficient packing. This step ensures the mold does not experience excessive pressure that could negatively impact part quality.
3. Melt Front Temperature Monitoring
Monitoring the temperature of the melt front is essential to avoid significant temperature fluctuations that could induce residual stress or warping within the part. Maintaining a consistent temperature distribution throughout the mold helps ensure uniform material flow and prevents deformation during solidification.
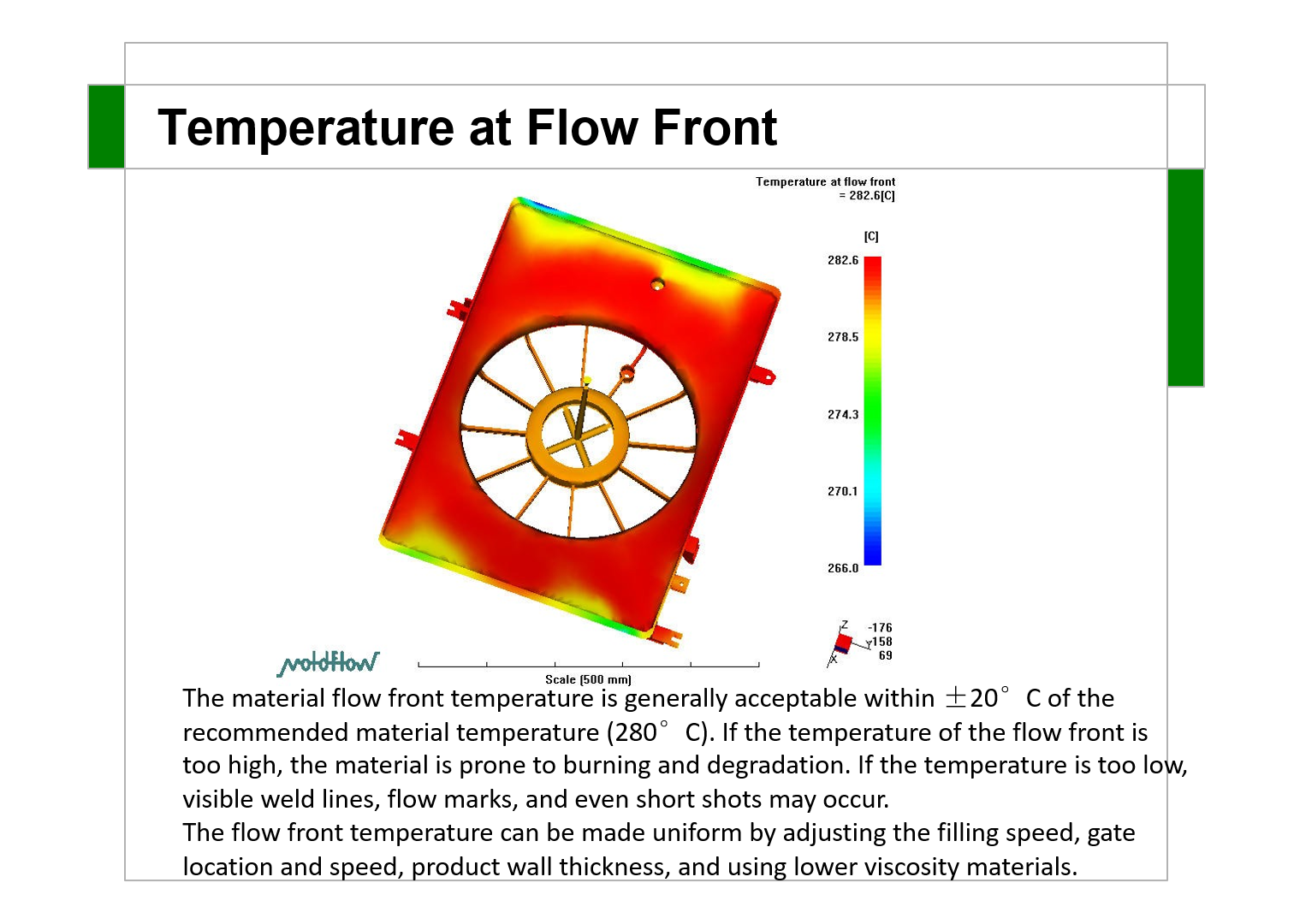
4. Clamp Force Monitoring
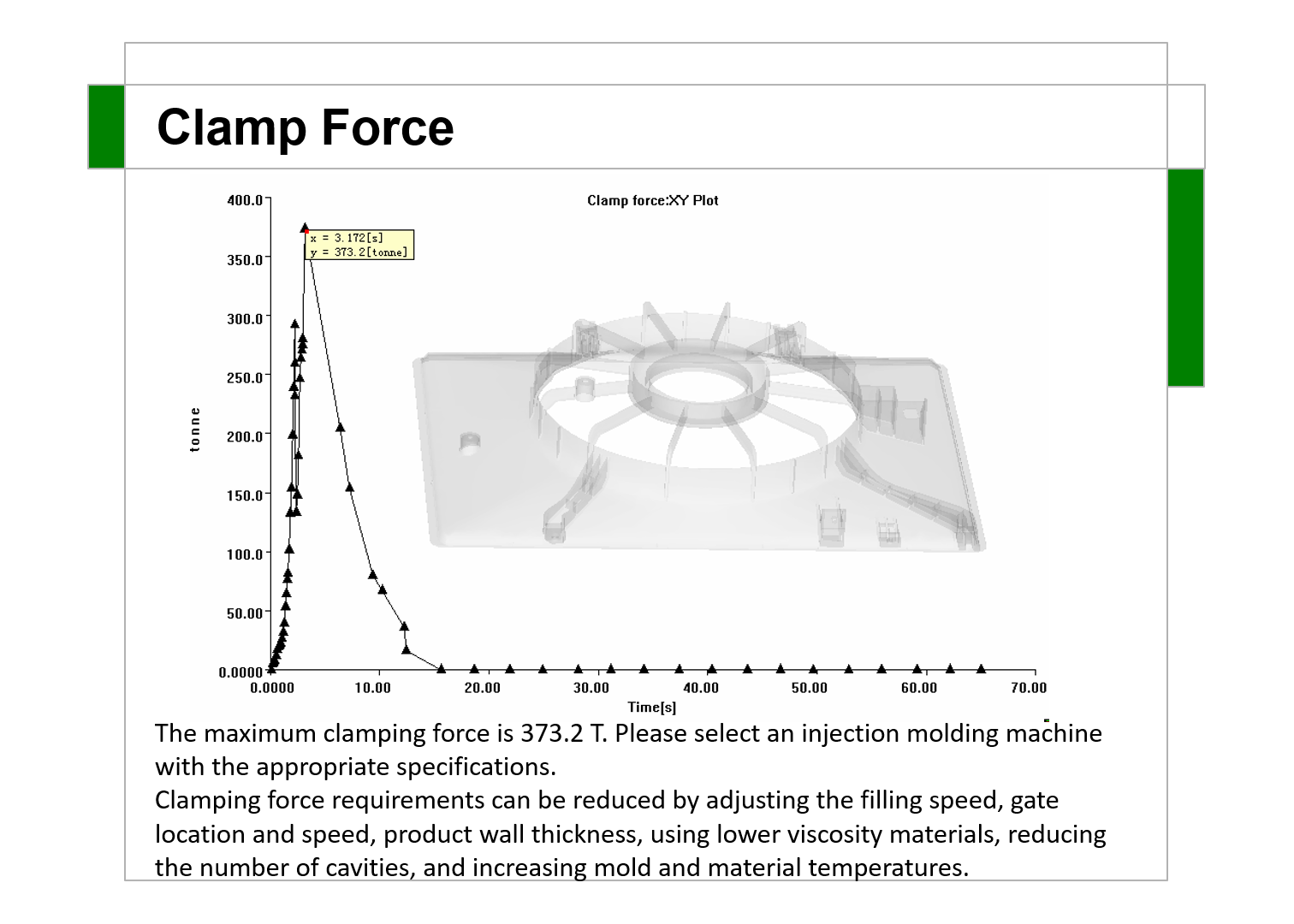
Monitoring the clamp force during the injection molding process is critical to ensure the mold stays securely closed under pressure. Insufficient clamp force can lead to mold separation or flash, while excessive clamp force can cause excessive wear on the mold or damage the part. Maintaining the correct clamp force ensures consistent molding quality and prevents defects like part distortion or improper filling.
5. Maximum Shear Rate & Shear Stress at Wall Monitoring
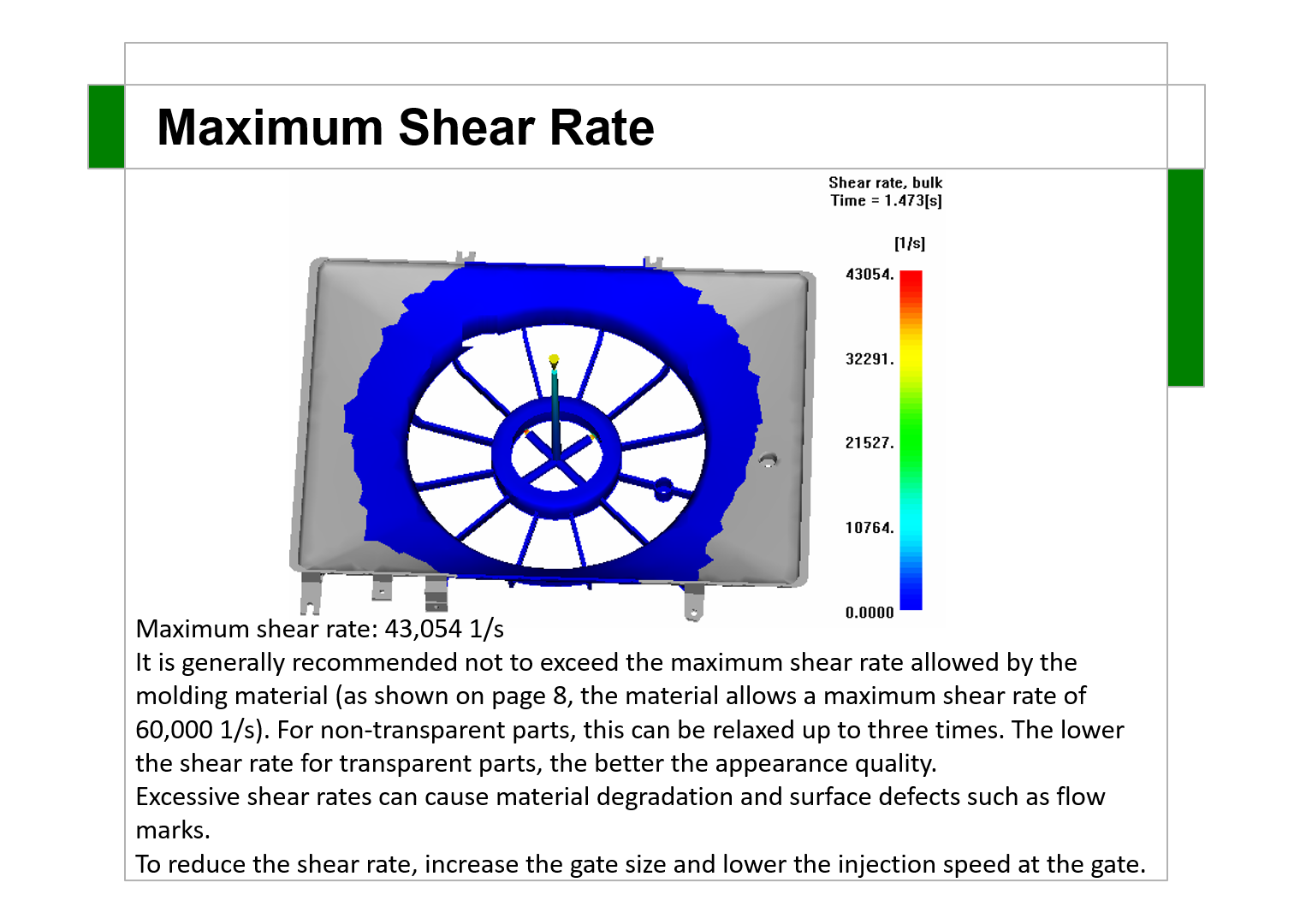
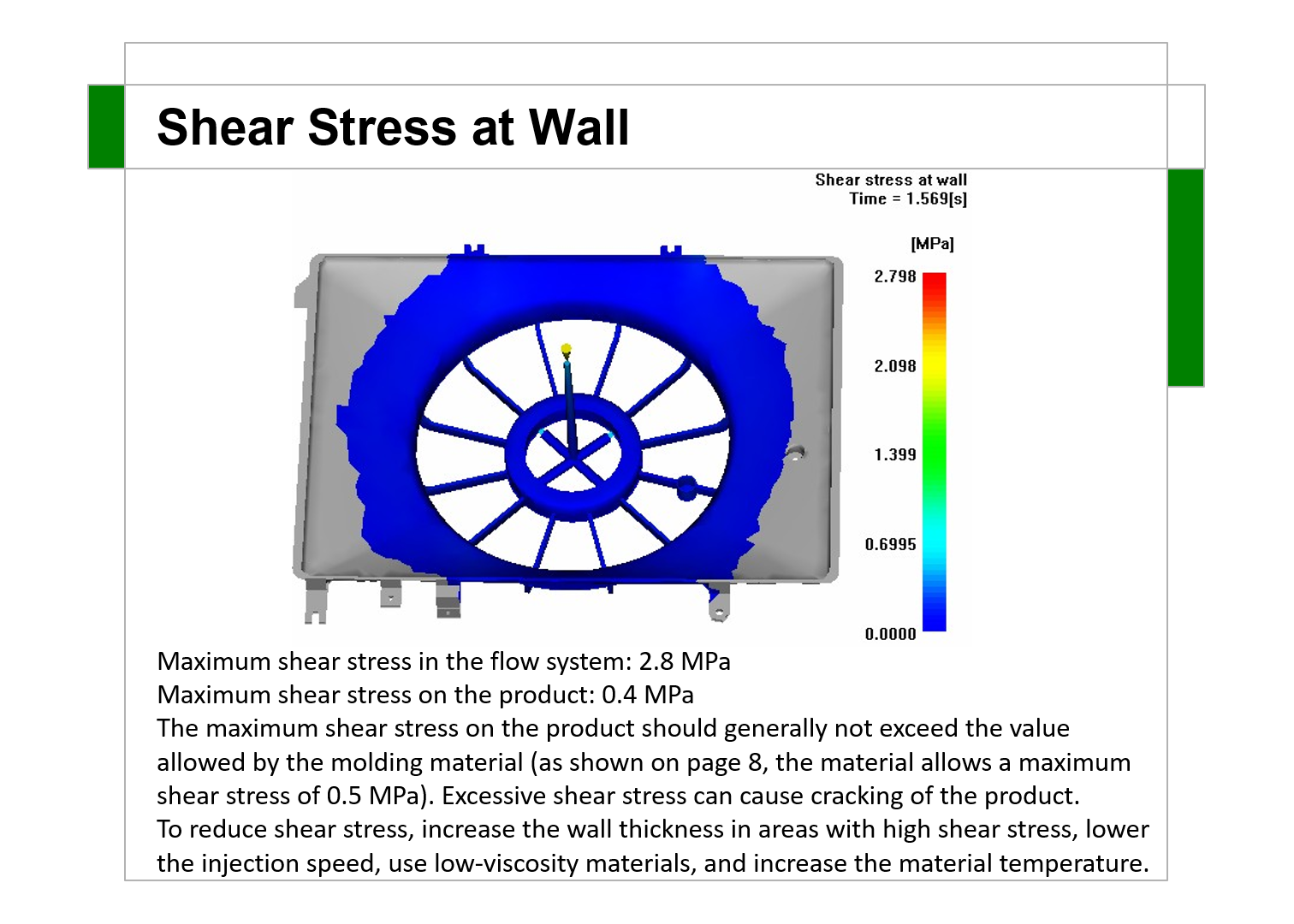
Monitoring both the maximum shear rate and shear stress at the wall is crucial to prevent material degradation and surface defects. Excessive shear rate can lead to overheating, causing material breakdown, while high shear stress can result in cracking or warping. Keeping these values within the material’s allowable limits ensures smoother flow, reduces surface imperfections, and maintains the strength and quality of the final product. Proper adjustments to injection speed, gate design, and mold temperature can help control these parameters.
6. Weld Lines Monitoring
Weld lines occur when two flow fronts meet during the injection molding process, leading to visible marks and potential weak spots in the finished part. These lines can impact the part’s aesthetics and mechanical properties, especially if they occur in high-stress areas. Monitoring and minimizing weld lines can be achieved by optimizing gate locations, improving mold design, and controlling the injection speed and pressure. Ensuring balanced flow and maintaining a consistent melt temperature also helps reduce the occurrence and severity of weld lines.
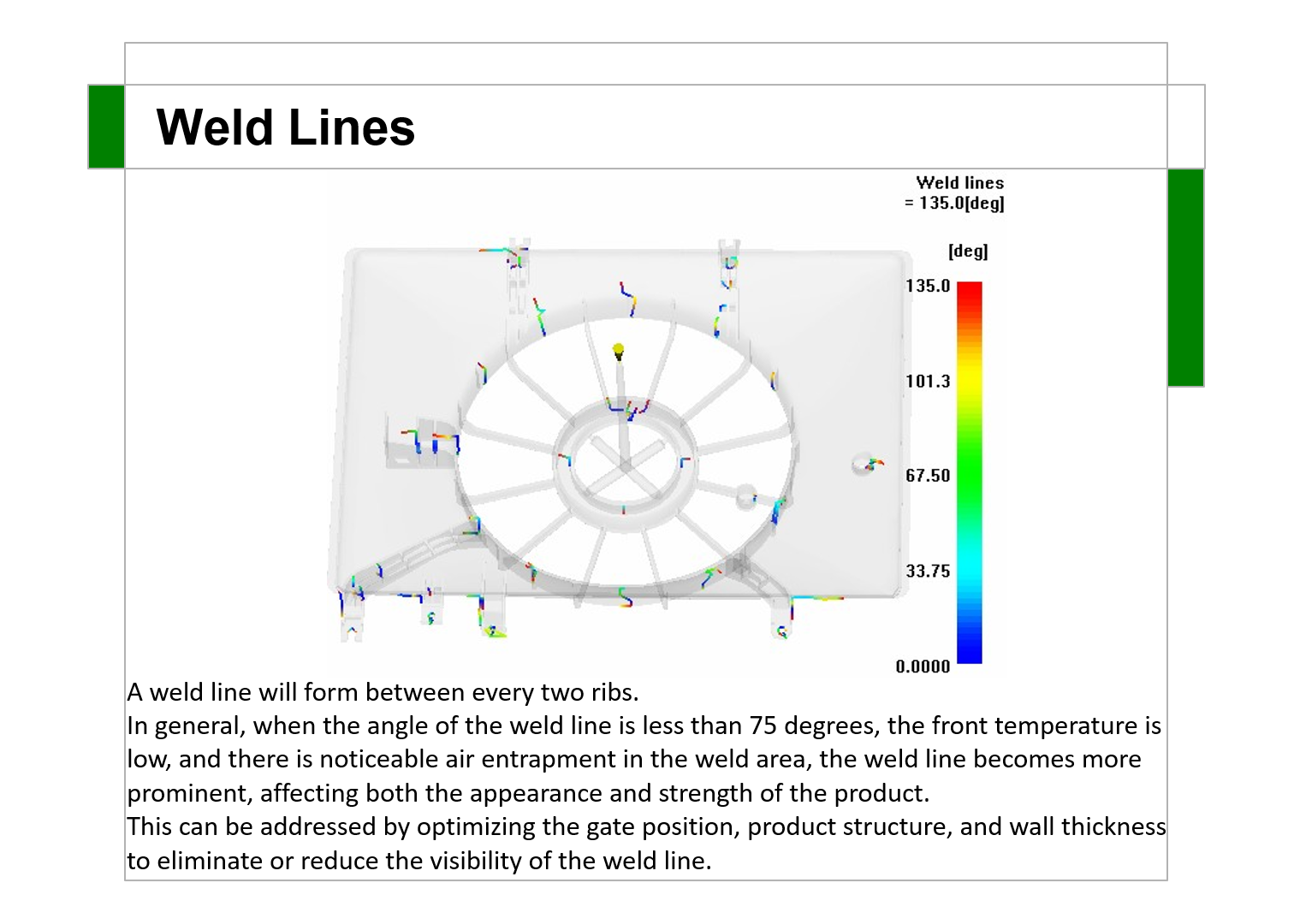
7. Ventilation and Air Trap Analysis
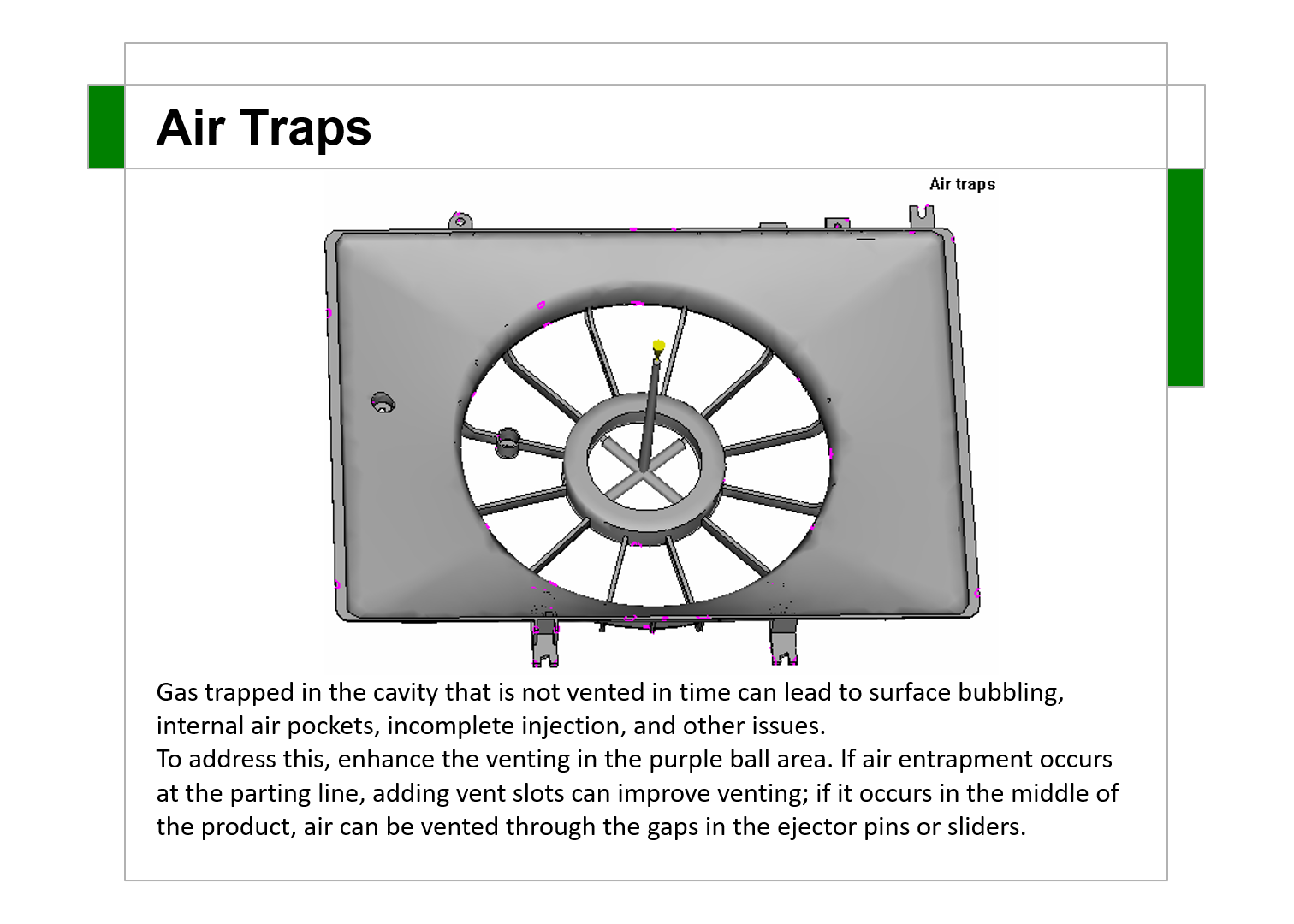
This step ensures that air and gases trapped in the mold cavity are effectively vented. Improper venting can lead to air traps, resulting in defects such as burns, weak spots, or poor surface quality. Effective venting design is crucial to allow for proper material flow and prevent trapped air from interfering with the injection process.
8. Shrinkage and Warpage Prediction
This step predicts material shrinkage during cooling and solidification, which can affect part dimensions and final quality. Shrinkage prediction is vital for adjusting part geometry and mold design to ensure that the final product remains within tolerances. Warpage prediction helps to identify areas where the part may deform and allows for design adjustments to minimize these effects.
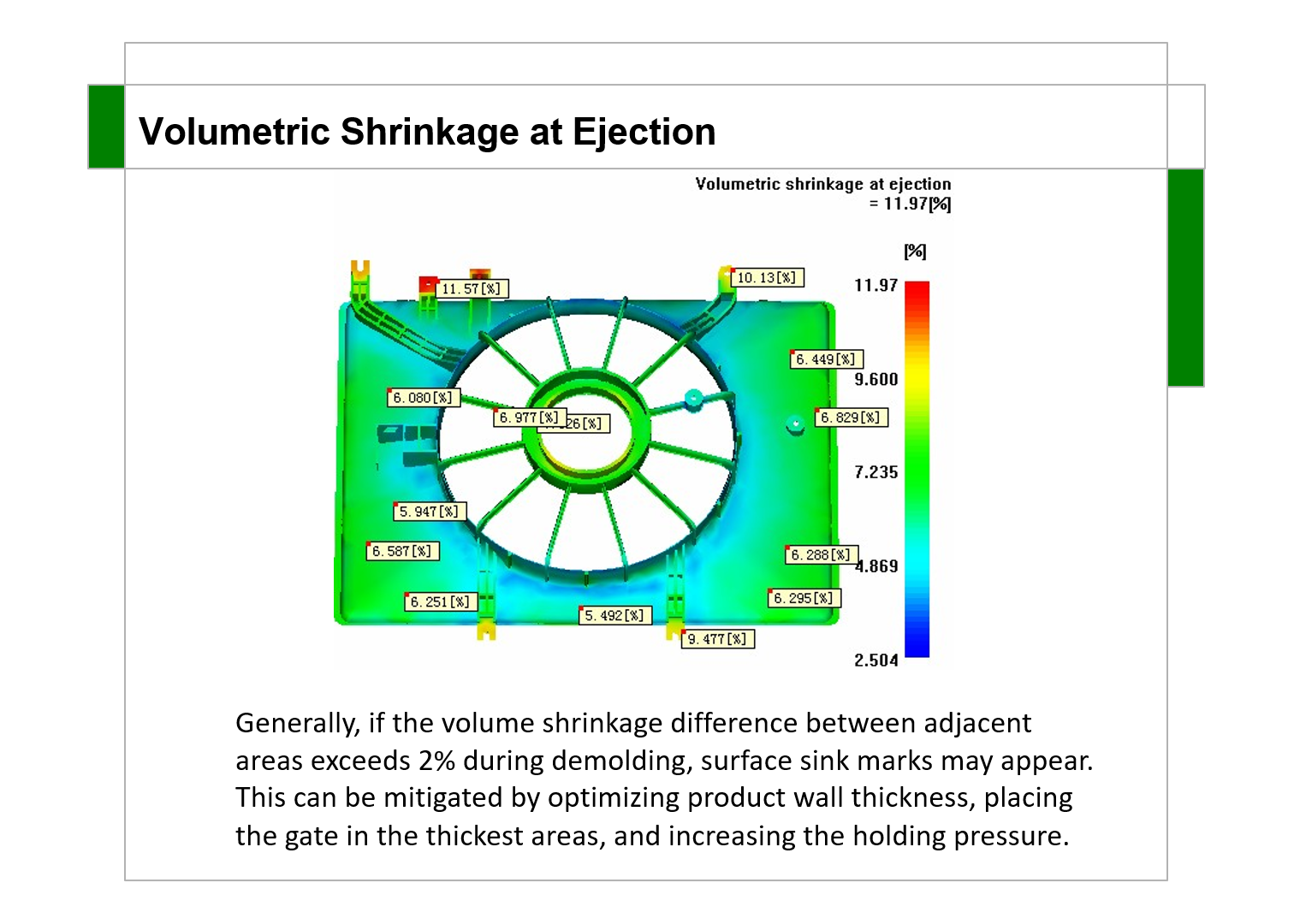
9. Frozen Layer Fraction Monitoring
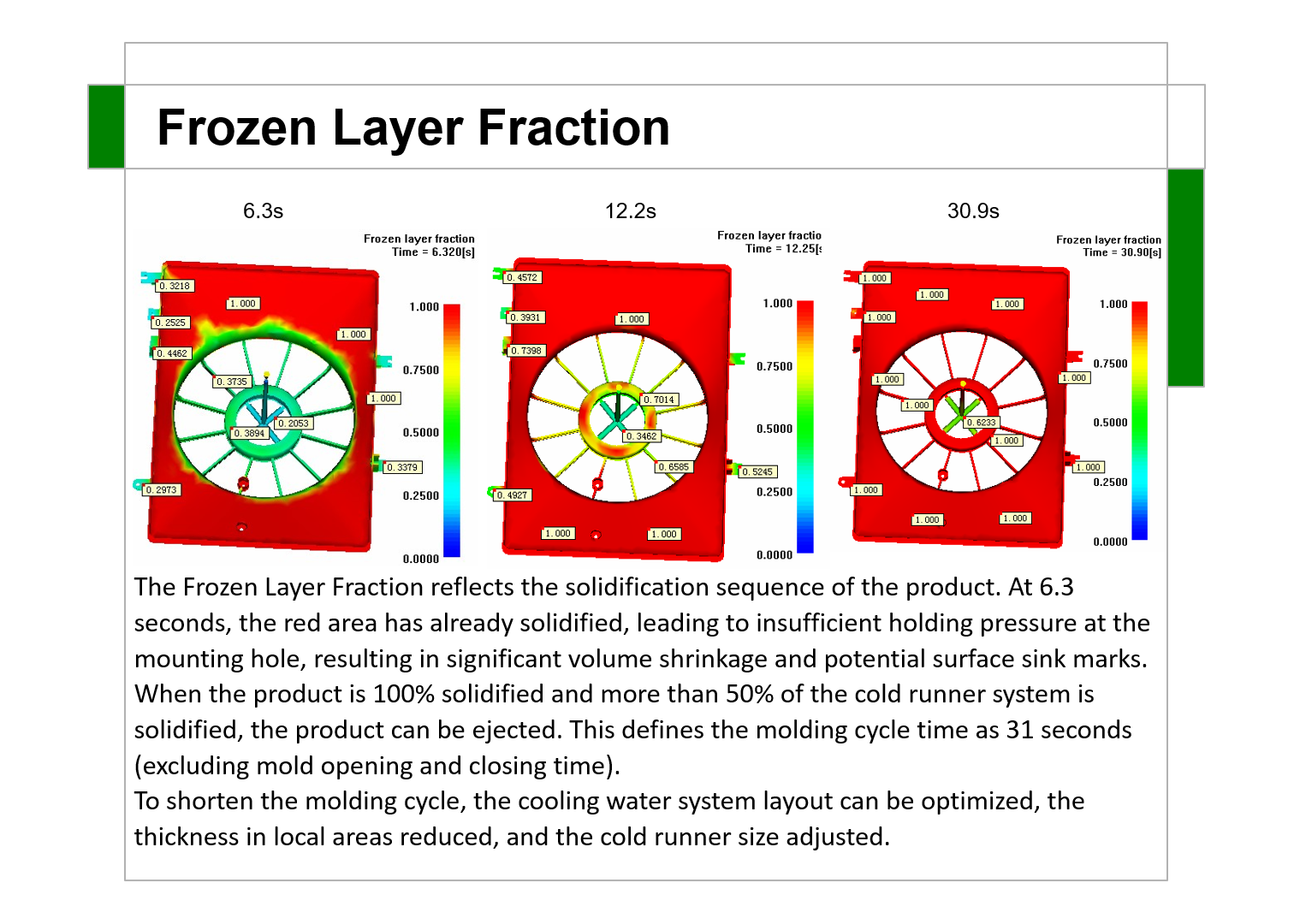
Frozen Layer Fraction refers to the percentage of the product that has solidified during the injection molding process. A higher fraction indicates that the material is cooling and solidifying faster, which can affect the flow and packing of the material within the mold. Monitoring the frozen layer helps optimize cooling time, prevent defects like sink marks or warping, and ensure uniform filling of the mold. Adjustments to cooling system design, material flow rate, and mold temperature can help achieve a more efficient solidification process and improve part quality.
10. Sink Mark Estimate
Sink marks occur when the material inside the mold shrinks during cooling, leaving depressions or dimples on the surface of the part. This phenomenon is typically caused by excessive wall thickness or inadequate cooling. Monitoring sink mark estimates helps identify areas where material may not be packing properly, leading to surface defects. Adjustments such as optimizing wall thickness, improving cooling rates, or increasing packing pressure can reduce the occurrence of sink marks and improve the overall quality of the part.

11. Cooling Analysis
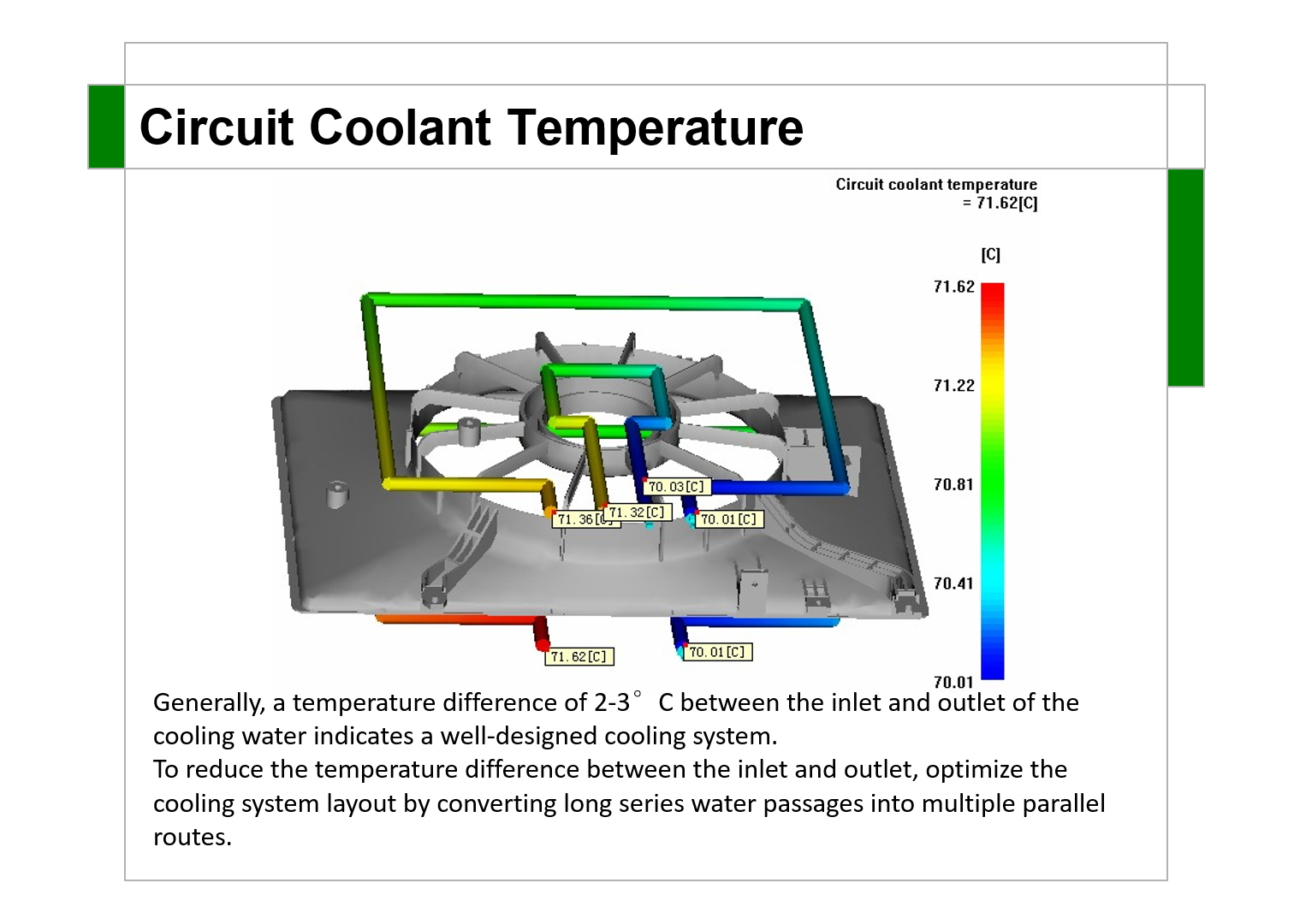
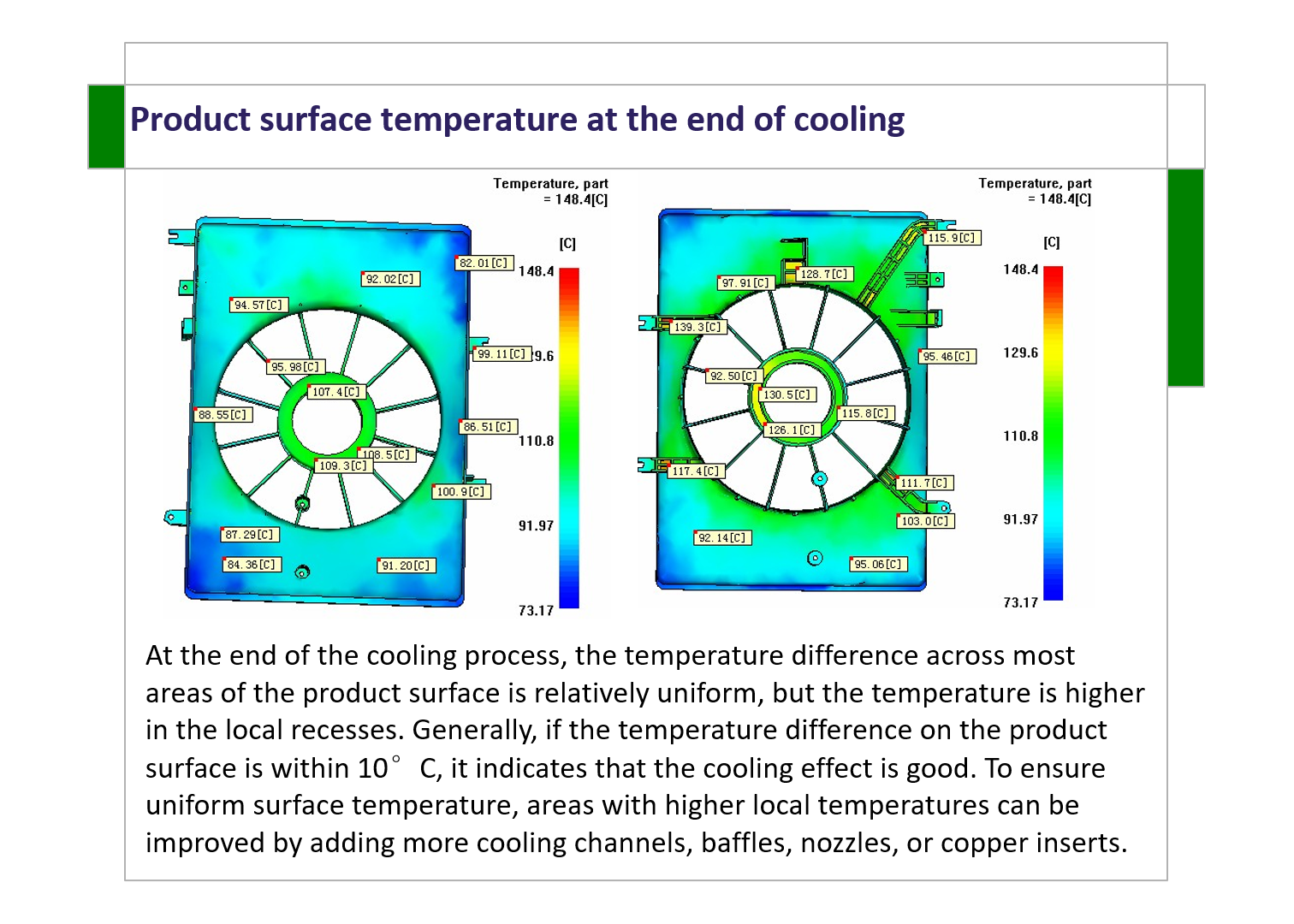
Cooling analysis helps to simulate and optimize the cooling process during injection molding, ensuring that the part cools evenly and efficiently. By evaluating the temperature distribution throughout the mold, this analysis identifies potential hot spots or uneven cooling that may cause warping or defects. Proper cooling system design, including the layout and size of cooling channels, can significantly reduce cycle times and improve part quality. Optimizing cooling parameters ensures consistent material properties, minimizes distortion, and enhances the overall manufacturing efficiency.
12. Deflection Analysis
Deflection analysis assesses the bending or deformation of a part due to internal stresses or external forces during the cooling phase. It is crucial for identifying areas where excessive warping may occur, which can affect the part’s fit, function, and overall quality. By evaluating the part’s geometry, material properties, and cooling conditions, this analysis helps predict how the part will behave after molding. Adjustments such as modifying wall thickness, gate locations, or cooling channel design can be made to minimize deflection and ensure the final part meets design specifications.
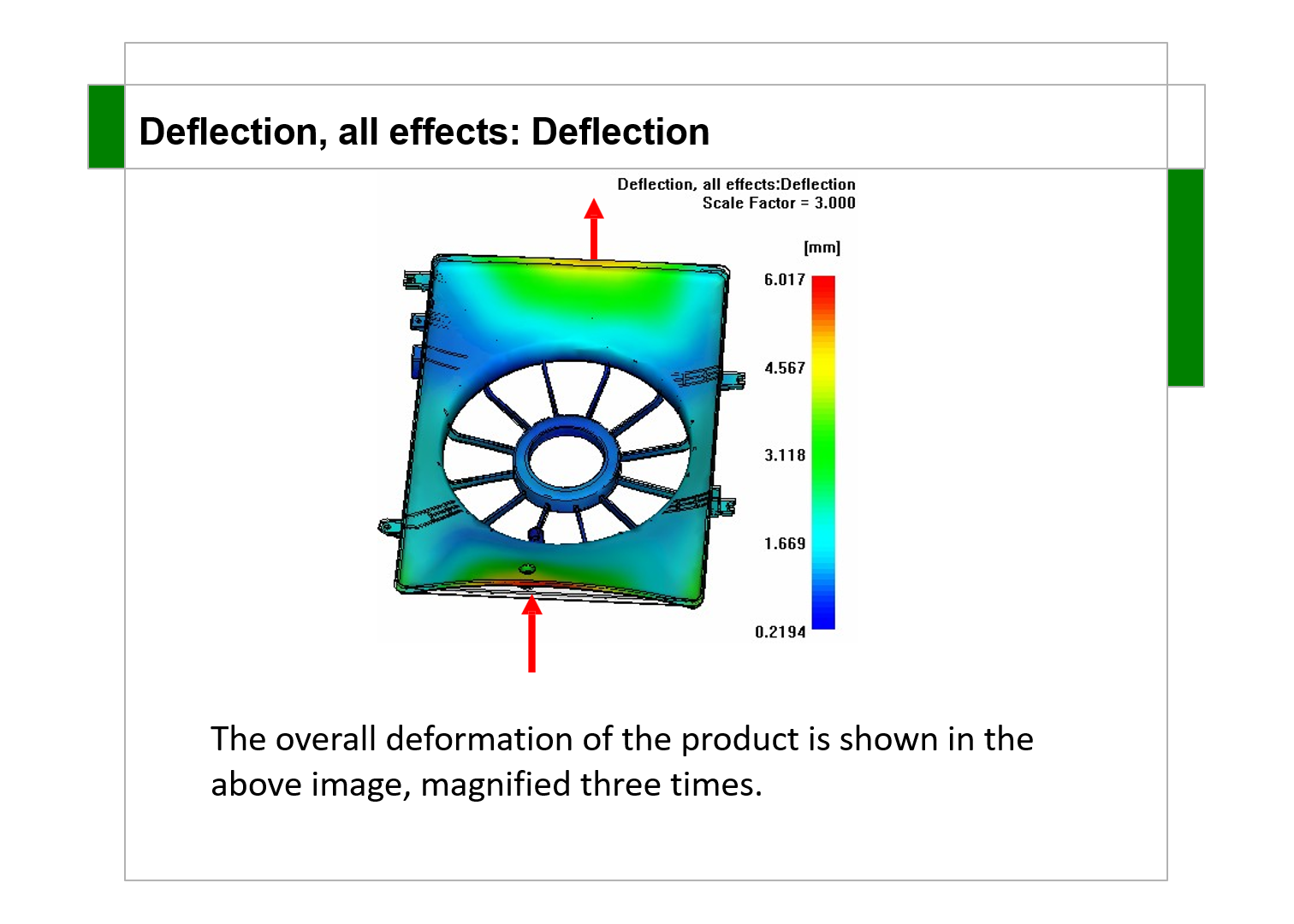
Key Factors Analyzed During Mold Flow Analysis
Key Factor | Description |
---|---|
Pressure | Pressure is one of the most critical factors in MFA. The software simulates how pressure affects the flow of molten material through the mold, ensuring it fills all cavities without causing issues like flash or incomplete filling (short shots). |
Temperature | Temperature distribution is carefully analyzed because it influences material viscosity and cooling rates. Uneven temperature distribution can lead to defects such as warping or uneven shrinkage. MFA helps predict these issues, allowing for better control over cooling time and temperature settings. |
Cooling Time | Cooling time is another crucial factor in the process. MFA calculates how long it takes for the material to cool and solidify within the mold. Optimizing this cooling time reduces cycle times and improves the consistency and dimensional accuracy of the final part. |
By analyzing these key factors, MFA enables engineers to make informed decisions about mold design and processing conditions, ensuring a smoother, more efficient manufacturing process with higher-quality products.
What Are the Key Benefits of Mold Flow Analysis?
1. Reduce Design Flaws and Manufacturing Issues:
Mold Flow Analysis helps identify potential design flaws and manufacturing issues early in the development process. By simulating the injection molding process before production begins, it allows engineers to detect problems such as warping, short shots, or air traps, and make necessary adjustments to the design, reducing the likelihood of defects in the final product.
2. Improve Material Usage and Reduce Production Costs:
MFA enables the optimization of material flow and mold design, which leads to more efficient use of materials. By preventing waste due to uneven filling or excessive scrap, MFA helps lower material costs and contributes to more cost-effective manufacturing, improving the overall profitability of production.
3. Shorten Time to Market:
By identifying potential issues before physical prototypes are made, Mold Flow Analysis can significantly shorten the product development timeline. Engineers can make data-driven decisions and implement design changes faster, reducing the time needed for physical testing and adjustments. This leads to quicker production cycles and faster time to market, allowing companies to respond to customer demands and market trends more swiftly.
What Features to Look for in Mold Flow Software?
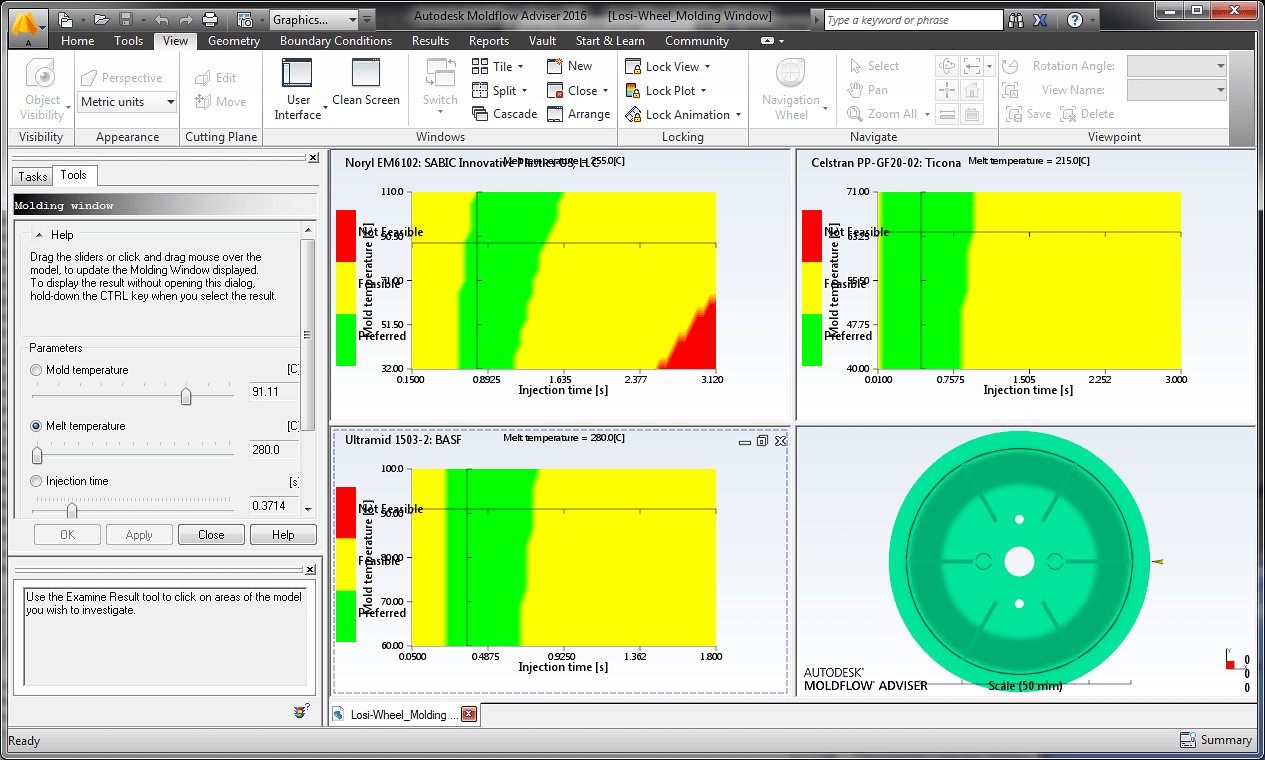
1. Simulation of Various Materials and Molding Conditions:
Advanced Mold Flow software allows simulation using a wide range of materials, including different types of plastics, composites, and elastomers. It also simulates various molding conditions, such as injection speed, pressure, and temperature. This feature helps optimize the design for specific materials and ensures that the injection molding process is tailored to the material’s behavior, improving overall quality and efficiency.
2. Visualization of Flow Patterns, Air Traps, and Cooling Efficiency:
The software provides detailed visual representations of the material flow within the mold, highlighting areas of uneven filling, air traps, or potential blockages. It also visualizes cooling efficiency, allowing engineers to pinpoint areas where cooling rates need adjustment. This insight helps prevent defects like warping, short shots, and weak spots in the final product.
3. Customization Options for Specific Project Needs:
Advanced Mold Flow software offers customization features to address the unique needs of different projects. Whether it’s adjusting for complex part geometries, specific mold designs, or specialized material properties, these options allow engineers to optimize every aspect of the simulation for the specific requirements of the product, ensuring an efficient and precise molding process.
How is Mold Flow Analysis Applied in Industry?
1. Automotive Industry:
In the automotive sector, Mold Flow Analysis is crucial for optimizing parts like bumpers, dashboards, and engine components. By simulating the injection molding process, manufacturers can reduce defects such as sink marks and warping that could affect the structural integrity or appearance of automotive parts. For example, MFA can help design parts with optimal thickness distribution to prevent deformation under high temperatures or pressure during use.
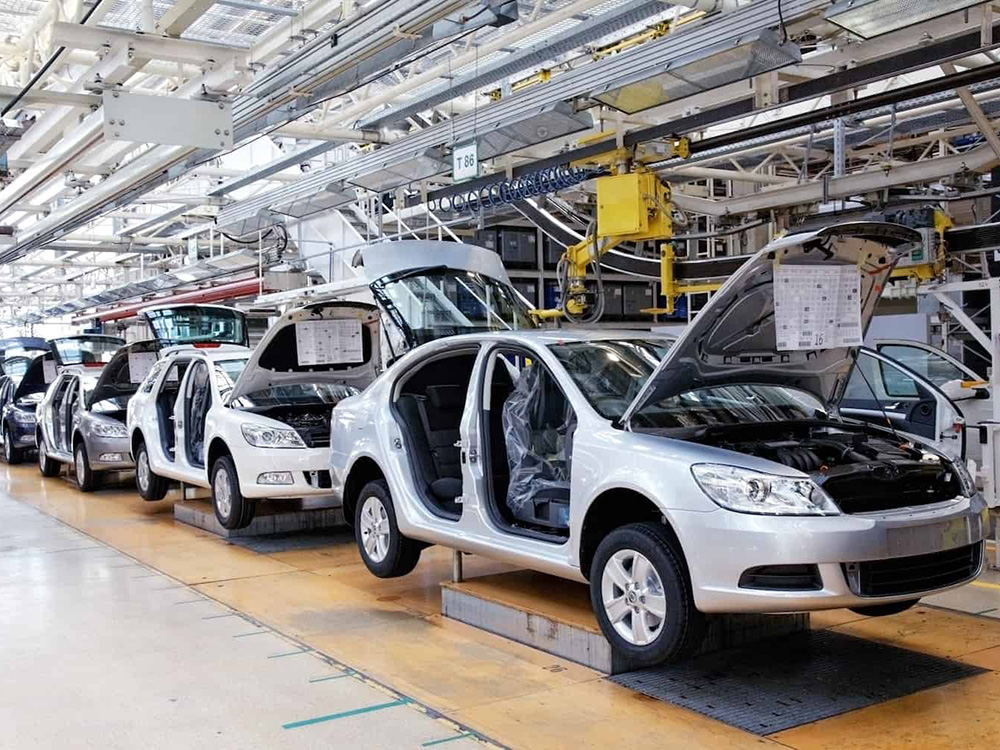
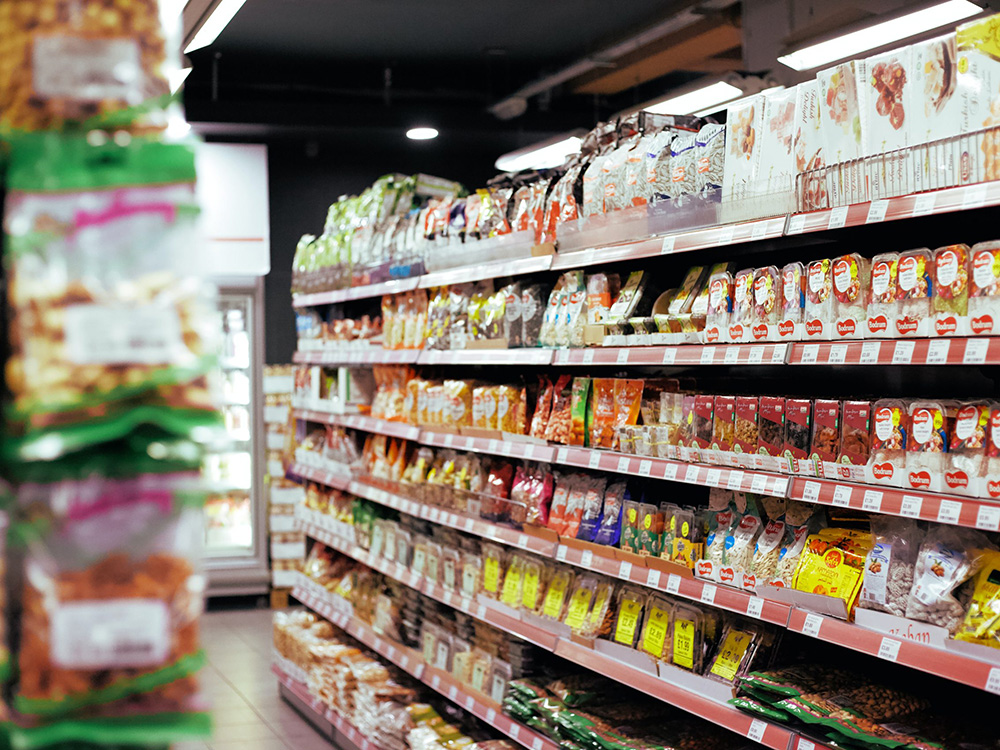
2. Consumer Products:
For consumer products like packaging, household goods, or toys, Mold Flow Analysis helps ensure high-quality, cost-effective production. By using MFA, companies can reduce material waste, improve part strength, and minimize cycle times. For example, in the production of plastic containers, MFA can optimize the mold design for uniform material distribution, ensuring consistent quality and minimizing defects such as flashing or voids.
3. Electronics Industry:
In electronics, precision and performance are critical. Mold Flow Analysis is used to ensure that components like casings, connectors, and internal parts are manufactured with high accuracy and minimal defects. For example, when designing phone housings, MFA can be applied to optimize cooling time and prevent warping, which could impact the final fit and function of the product.
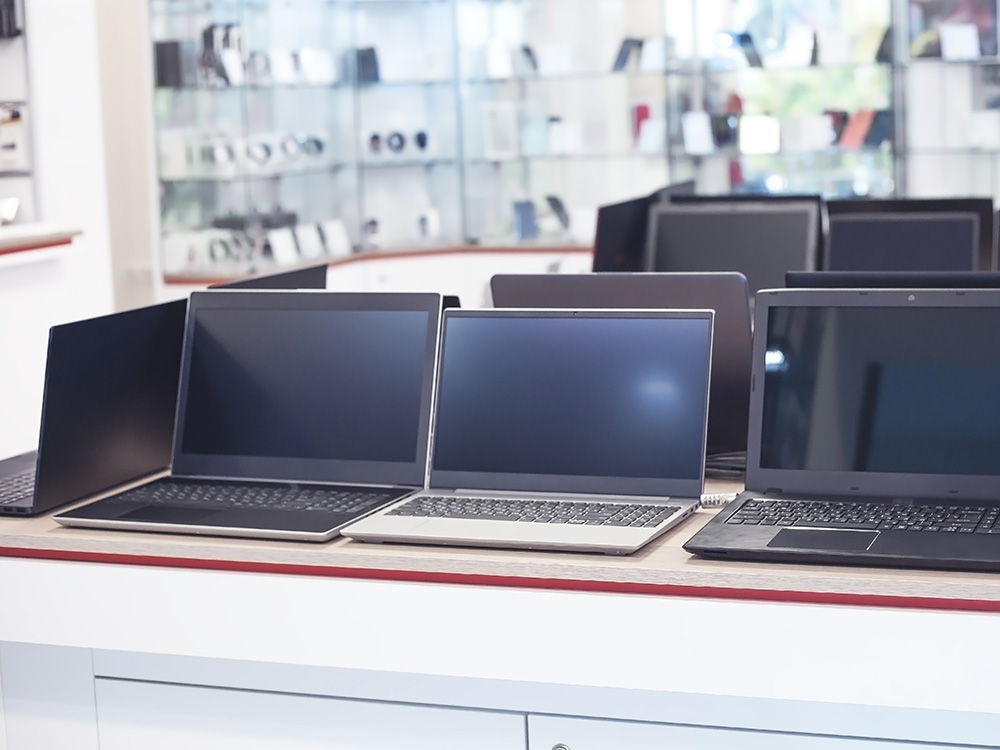
Examples of Specific Products or Case Studies
Automotive Case Study – Bumper Design Optimization
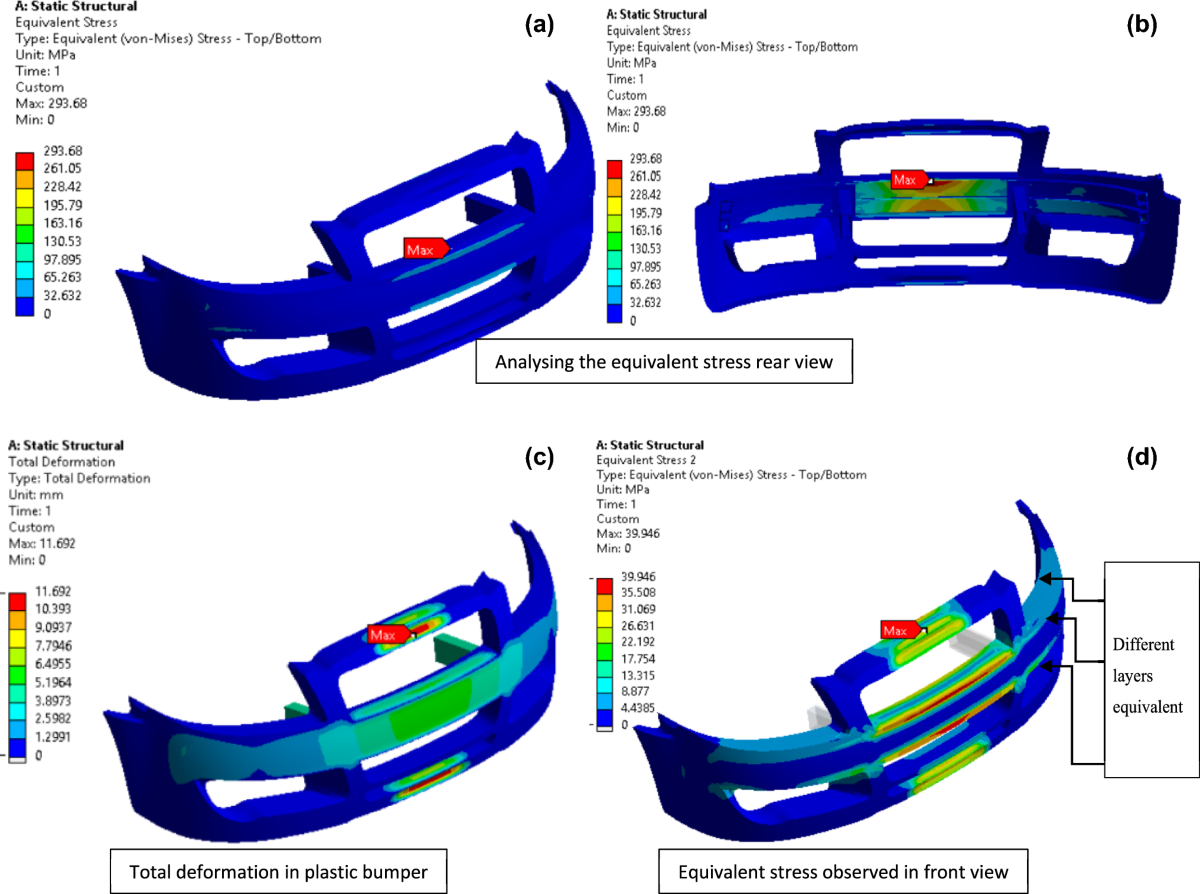
Using Mold Flow Analysis, an automotive manufacturer was able to optimize the design of a plastic bumper, ensuring even material flow during injection. The analysis revealed potential air trap zones and cooling inefficiencies, allowing for design changes that eliminated these issues. This resulted in a 15% reduction in material usage, a 20% faster production cycle, and a significant reduction in defects.
Consumer Product Case Study – Packaging Design
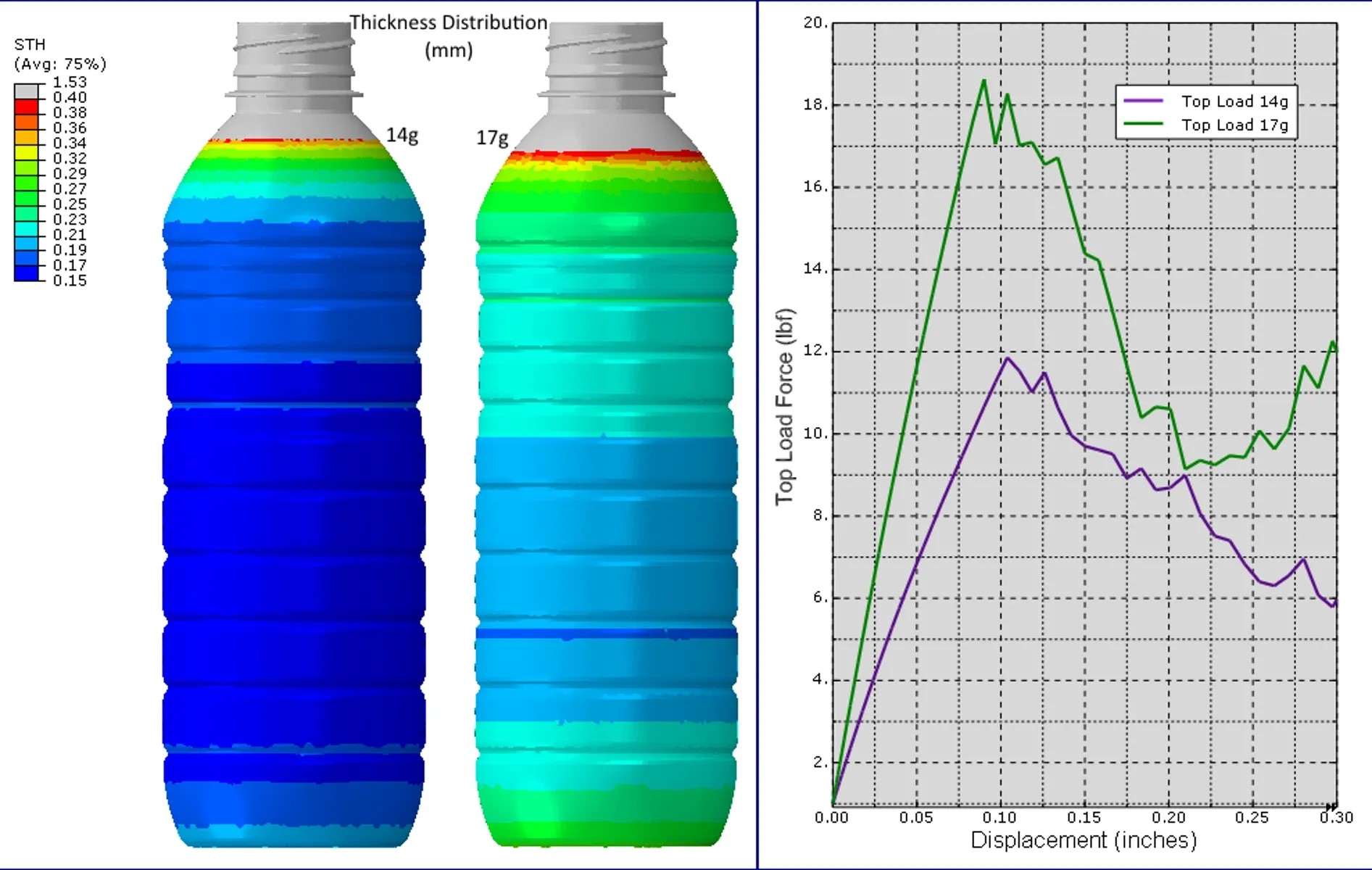
A company producing plastic packaging containers for food products used MFA to simulate various blow molding scenarios. The analysis showed how different design features impacted the material flow, helping to refine the mold design. The result was improved wall thickness consistency, faster cycle times, and a 10% reduction in material waste, leading to both cost savings and improved product quality.
Locomotive Case Study – Battery Housing
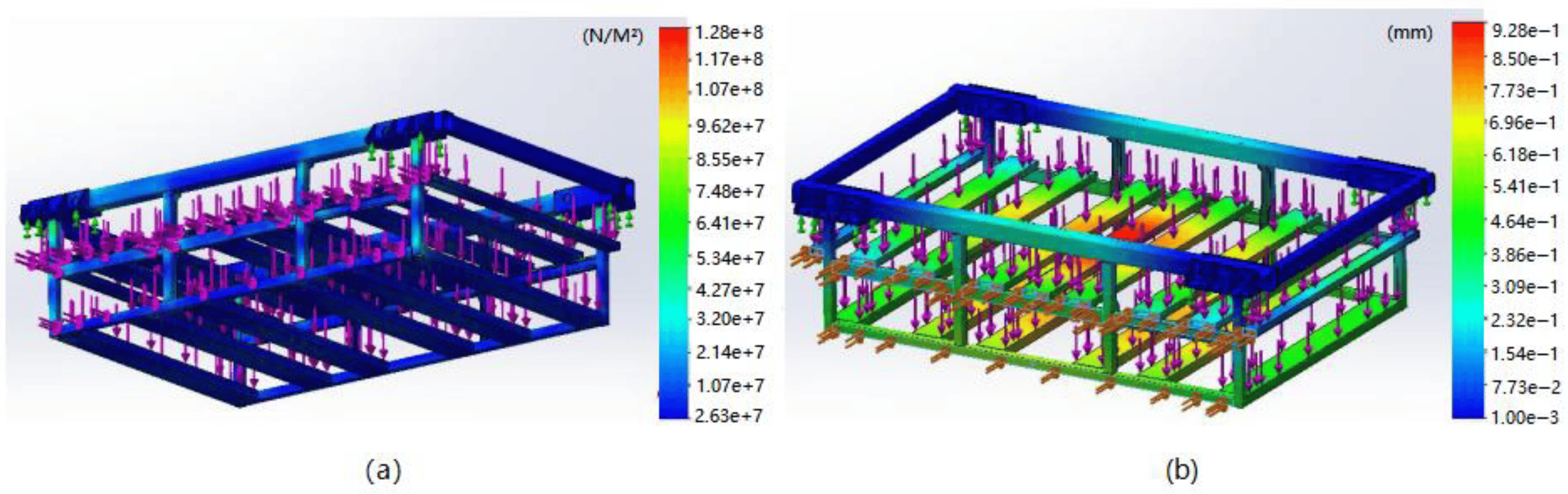
For a locomotive battery box, Mold Flow Analysis was applied to assess the material flow and stress distribution in the heavy-duty plastic design. By optimizing the injection points and adjusting wall thicknesses, the manufacturer enhanced the box’s structural integrity while maintaining lightweight characteristics. This led to improved durability under extreme conditions, reduced manufacturing time, and a 20% increase in production efficiency, ensuring the battery box met strict safety standards.
How KingStar Mold Uses Mold Flow Analysis
At KingStar Mold, we integrate Mold Flow Analysis (MFA) into every stage of our design and production processes to ensure the highest quality and efficiency in our manufacturing operations. By leveraging advanced simulation software, we can accurately predict how molten material flows through the mold and optimize the design before physical production begins. This proactive approach allows us to identify and address potential issues such as material distribution, air traps, cooling inefficiencies, and part warping—ensuring that the final product meets both performance and aesthetic standards.
We work closely with our clients to incorporate MFA early in the design phase, helping them fine-tune their part designs and molds to reduce production risks and avoid costly delays. From the initial design concept through to the final production run, Mold Flow Analysis allows us to streamline the process, reduce material waste, and ensure optimal part quality, all while maintaining tight production timelines.
Our Expertise, Tools, and Software Used
At KingStar Mold, we utilize some of the most advanced Mold Flow Analysis software tools available in the industry, such as Moldex3D and Autodesk Moldflow. These powerful platforms allow us to simulate a wide variety of materials and molding conditions, providing in-depth insights into how different parameters affect the manufacturing process. Our team of experienced engineers is skilled in interpreting the results from these simulations, enabling us to make informed adjustments to the design and production process for optimal results.
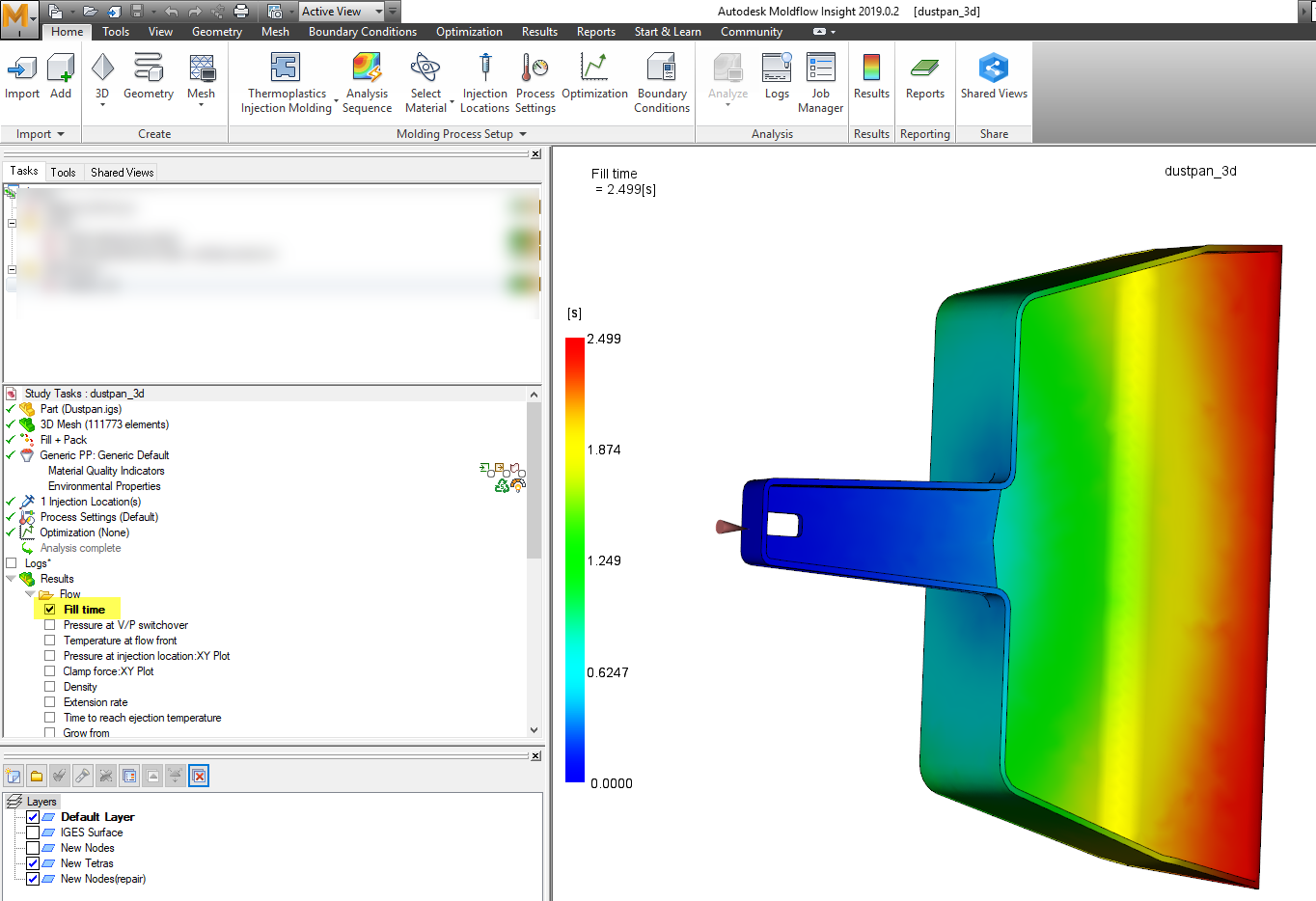
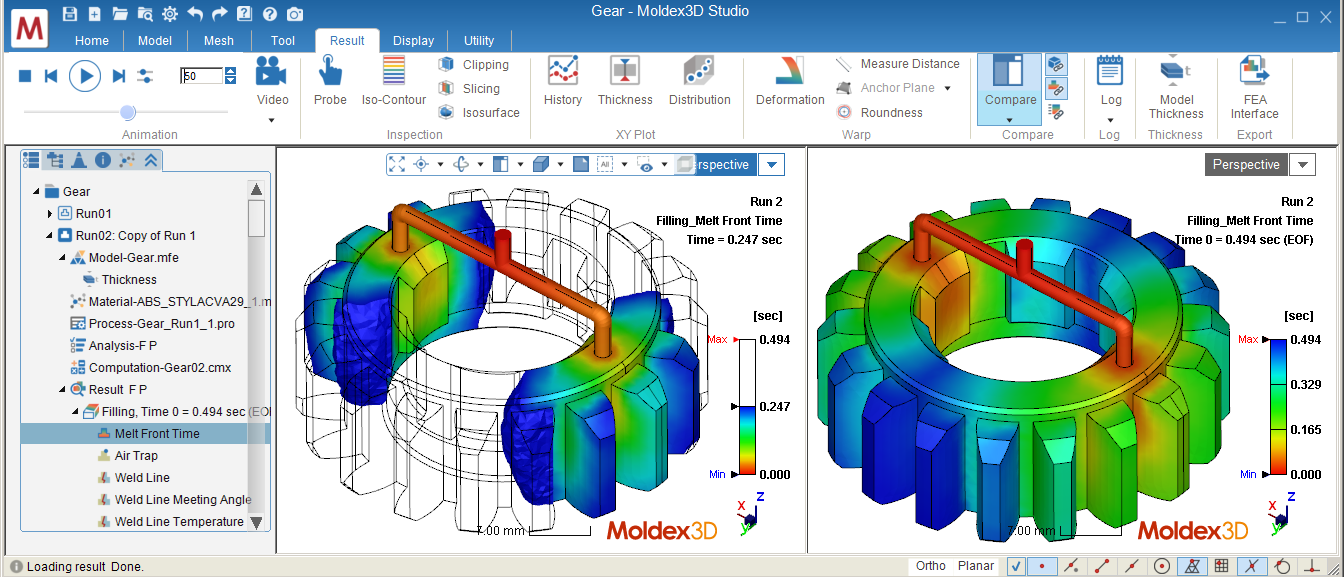
We also have expertise in customizing Mold Flow Analysis simulations to meet the specific needs of each project. Whether it’s adjusting for complex part geometries, specific material properties, or intricate cooling systems, we can fine-tune every aspect of the simulation to deliver accurate, actionable insights. By combining cutting-edge tools with our deep industry knowledge, KingStar Mold ensures the highest standards of quality, efficiency, and cost-effectiveness in every product we manufacture.
Conclusion
Mold Flow Analysis (MFA) is a vital tool in modern injection molding, offering significant benefits in terms of quality, efficiency, and cost-effectiveness. By accurately simulating the flow of molten material, MFA helps identify potential issues early in the design process, reducing defects, improving material usage, and optimizing production times. This leads to fewer errors, lower production costs, and faster time-to-market for your products.
As the leading on-demand manufacturer, KingStar Mold leverages the power of Mold Flow Analysis to ensure the highest quality standards in every project. Our expert team, equipped with advanced simulation tools, works closely with you to optimize your designs, minimize waste, and achieve optimal performance. Choose KingStar Mold for your next project, and experience the difference that cutting-edge Mold Flow Analysis can make in delivering superior products with exceptional efficiency and precision.