Previous Projects
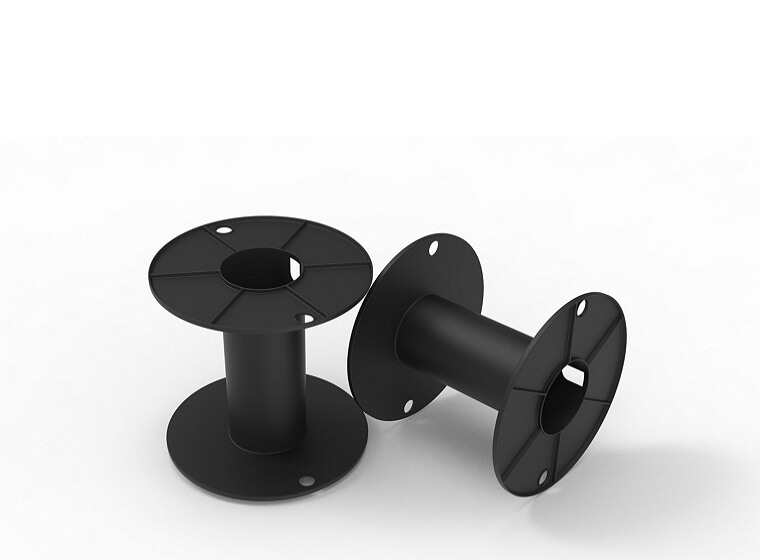

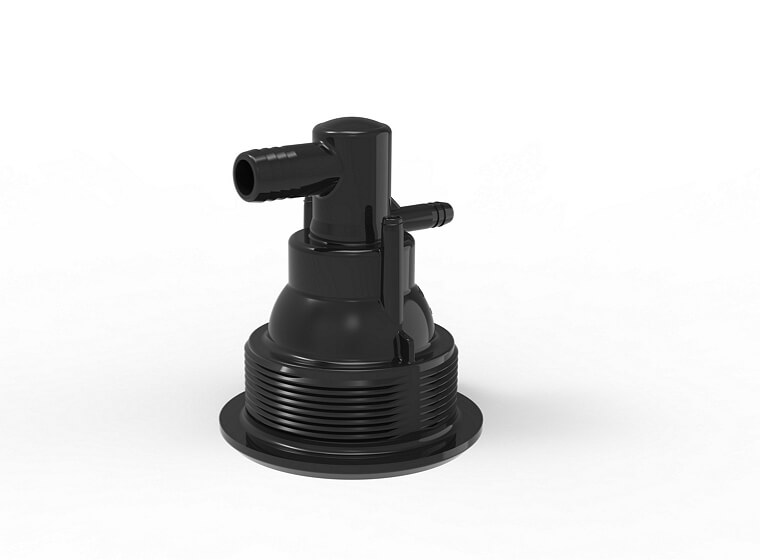
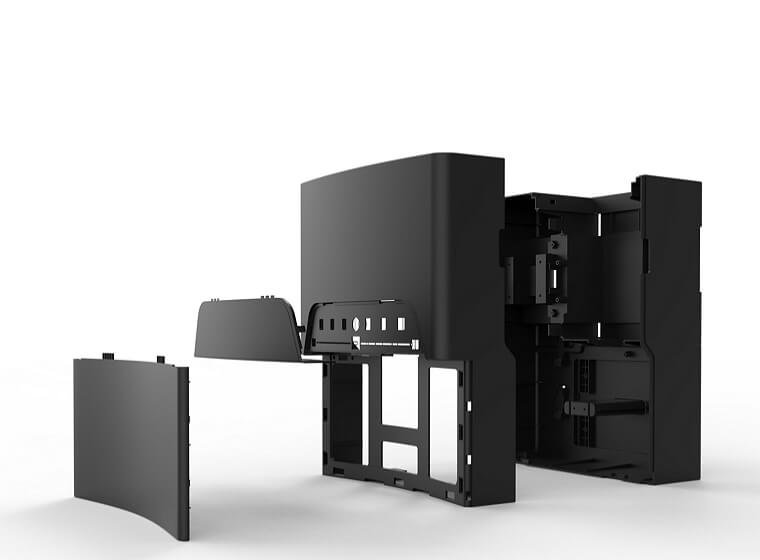
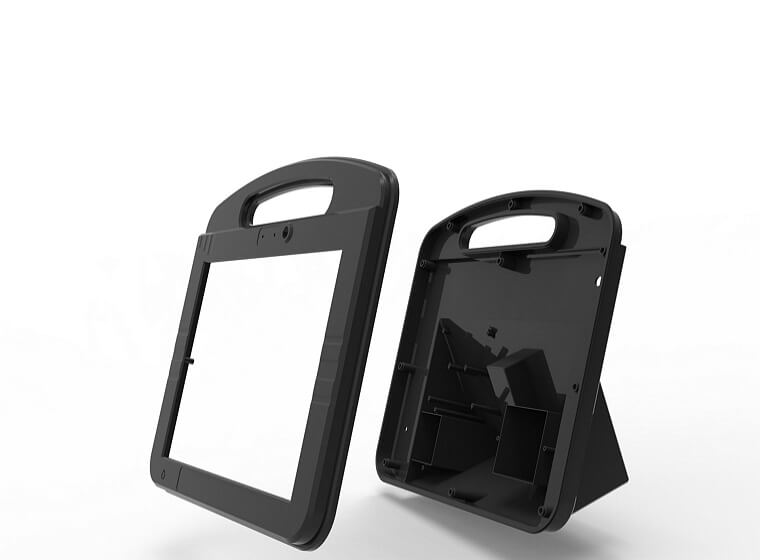
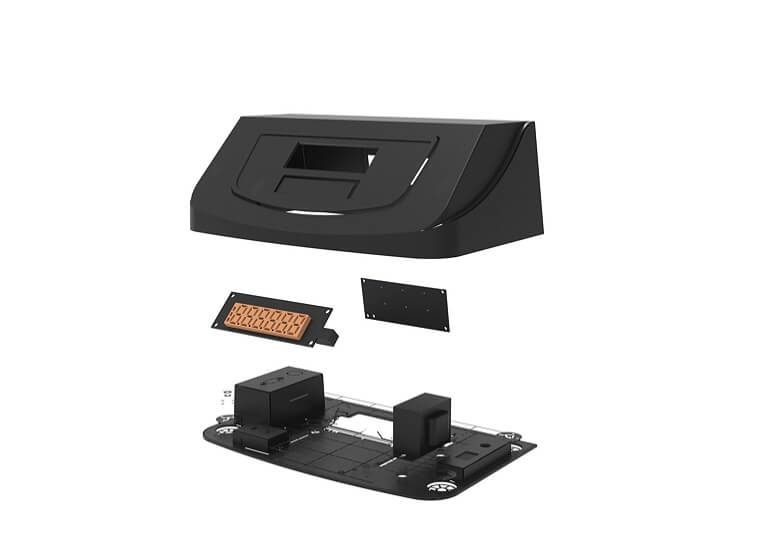
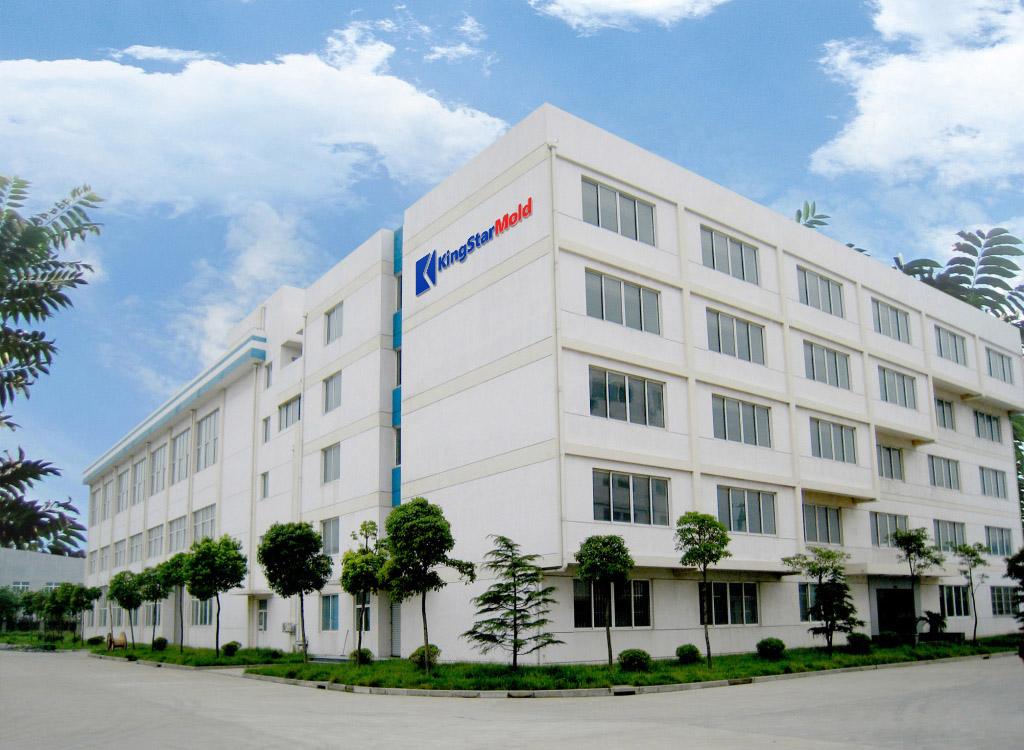
Our Factory In China
KingStar Mold is a leading manufacturer based in China, specializing in custom injection molds and the production of plastic and silicone components. With over ten years of experience, we offer comprehensive solutions from mold design to production, ensuring the highest standards of quality and precision.
Our factory is equipped with advanced machinery and staffed by skilled professionals, dedicated to delivering tailored, high-performance parts for a variety of industries. Whether it’s plastic, silicone, or a combination of materials, KingStar Mold provides reliable, cost-effective solutions for every project.
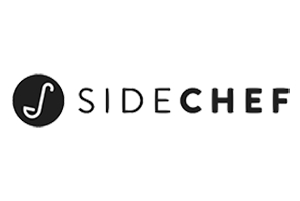
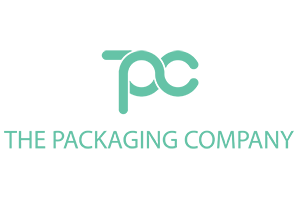
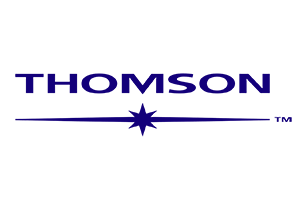
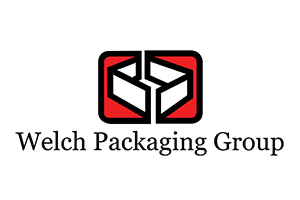
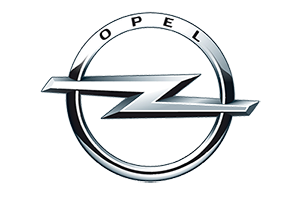
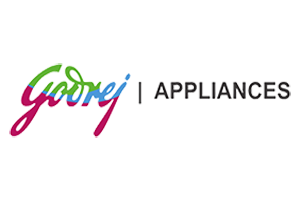
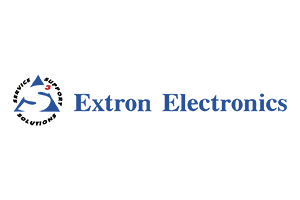
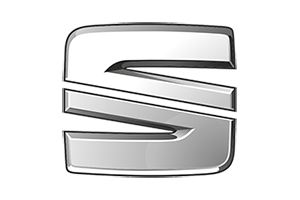
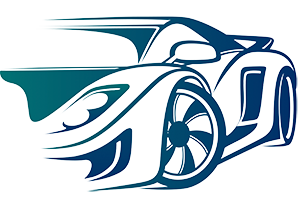
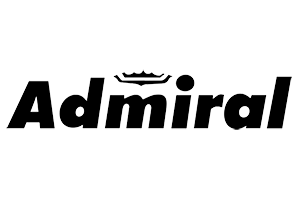
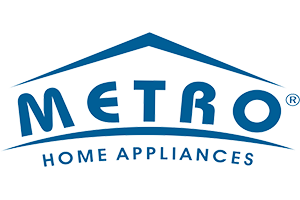
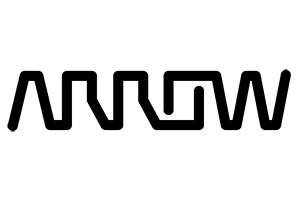
See Our Injection Molding Production
KingStar Mold’s Production Capacity
Production Capacity | Details | Production Capacity | Details |
---|---|---|---|
Machine Quantity | 20+ High-precision injection molding machines | Materials Handled | PE, PP, ABS, PC, POM, Nylon, TPU, and more |
Clamping Force | 50 to 800 tons | Molding Cycle Time | 10 to 60 seconds (depending on part complexity) |
Part Weight Range | 1g to 5000g | Lead Time for Production | 2 to 4 weeks (for standard molds) |
Production Volume | Up to 500,000 parts per month | Prototype Production Capability | Rapid prototyping with 3D printing and CNC |
Maximum Mold Size | 800 mm x 800 mm x 1000 mm | Post-Production Services | Assembly, painting, surface finishing, packaging |
Tolerance Accuracy | ±0.01 mm | Customization & Flexibility | Tailored solutions for low-volume & complex designs |
Orders Workflow
Initial Consultation & Design Review
We begin by discussing your project’s goals and reviewing the design to ensure it’s optimized for the specific manufacturing process. At this stage, we suggest improvements or adjustments to enhance efficiency, functionality, and manufacturability.
Material Selection
Our experts assist in selecting the right materials for your product based on performance requirements and compatibility with the manufacturing process. The correct material choice ensures durability, cost-effectiveness, and the desired product functionality.
Design & Engineering
Using advanced CAD and simulation tools, we develop a custom design for your project. This step ensures precise details and identifies potential challenges early in the process, optimizing the design for efficient manufacturing.
Prototyping & Sample Testing
A prototype or sample is created to verify design accuracy, functionality, and performance. Rigorous testing is conducted to ensure the product meets your specifications before moving into full-scale production.
Production Setup & Initial Production
We set up the required machines, molds, or tools for the manufacturing process. The initial production run is performed to confirm the setup, assess quality, and fine-tune settings for optimal results.
Final Production & Quality Control
After final approval, we proceed with full-scale production, ensuring continuous quality checks. Comprehensive inspections at each stage ensure that every part meets the highest standards before delivery.
Materials For Injection Molding
ABS
A strong, impact-resistant plastic commonly used in automotive and consumer goods applications.
PEEK
A thermoplastic with excellent chemical and thermal resistance, used in aerospace and medical applications.
PEI
A tough, high-heat resistant plastic used in automotive, aerospace, and electrical applications.
PA
Also known as nylon, it’s a durable, wear-resistant plastic ideal for automotive and industrial parts.
PBT
A strong, heat-resistant plastic used in automotive, electrical, and electronic components.
PC
A tough, high-impact plastic with excellent clarity, used in eyewear lenses and automotive parts.
PE
A versatile, lightweight plastic known for its chemical resistance and low friction properties.
PMMA
A transparent plastic often used as a glass substitute in lighting, signage, and optical lenses.
POM
A high-performance, low-friction plastic used in precision engineering applications like gears and bearings.
PP
A flexible, durable plastic with high resistance to chemicals and fatigue, often used for containers and packaging.
PPS
A high-temperature, chemically resistant plastic used in automotive and electrical applications.
PS
A rigid, inexpensive plastic often used in disposable products like packaging and cutlery.
TPU
A flexible, durable plastic with excellent abrasion and impact resistance, used in footwear and automotive applications.
PTFE
Known as Teflon, it’s a non-stick, high-temperature resistant material used in seals, gaskets, and cookware.
PPSU
A durable, high-temperature plastic used in plumbing, medical, and aerospace industries.
PVC
A rigid or flexible plastic used in construction, plumbing, and electrical applications.
PLA
A biodegradable, plant-based plastic, ideal for eco-friendly applications and easy to mold.
Surface Finishing Service at KingStar Mold
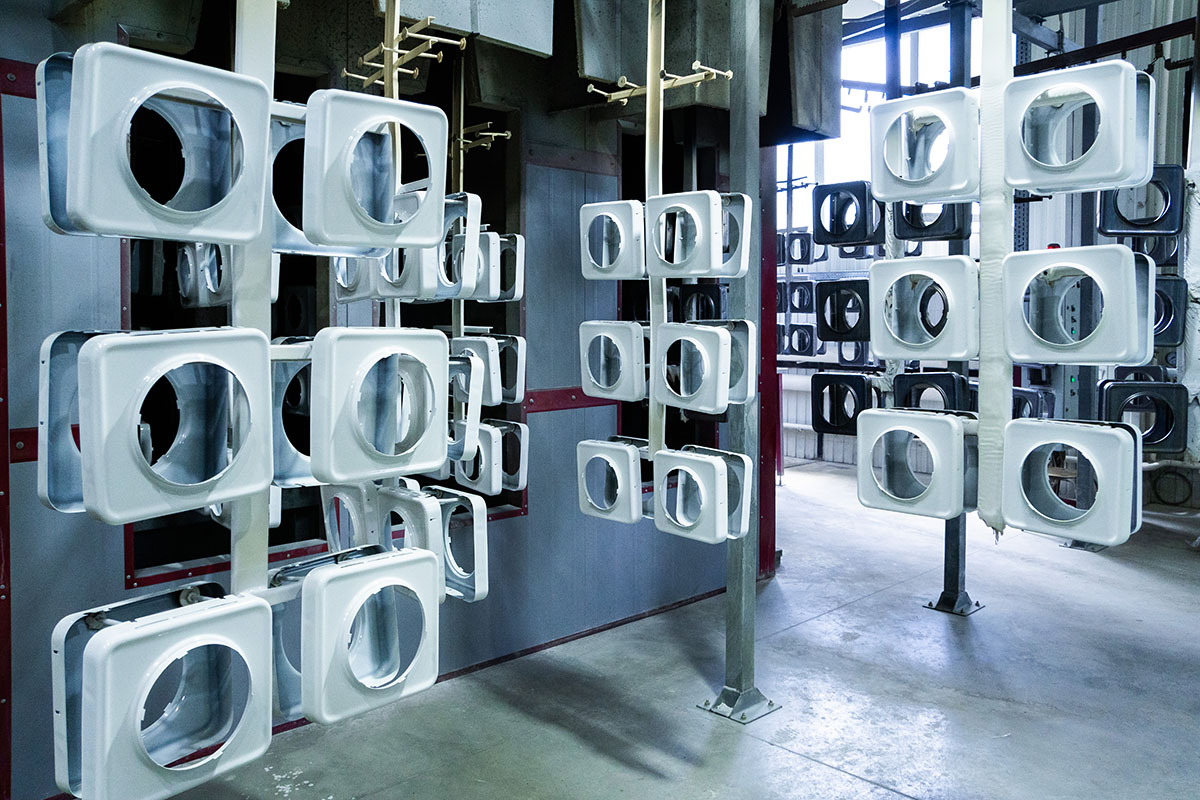
KingStar Mold offers a comprehensive range of surface treatment services to enhance the appearance, functionality, and durability of your injection-molded parts. Our services include options such as polishing, painting, anodizing, coating, and laser engraving, designed to improve surface finish, corrosion resistance, and wear resistance. By applying these treatments, we help ensure that your parts meet the highest quality standards, with the right finish for both aesthetic and performance requirements.
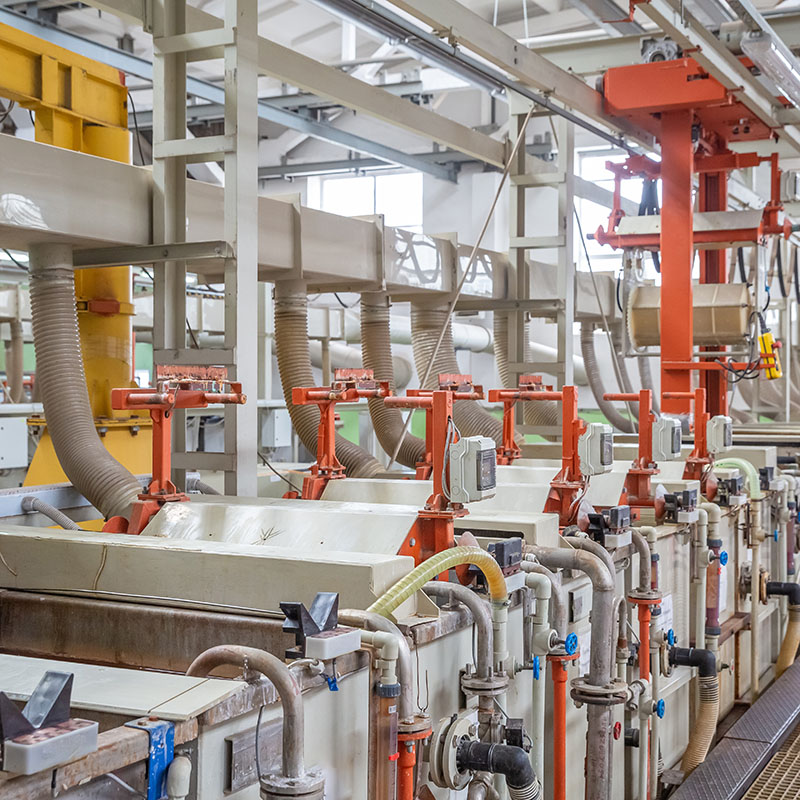
Anodizing
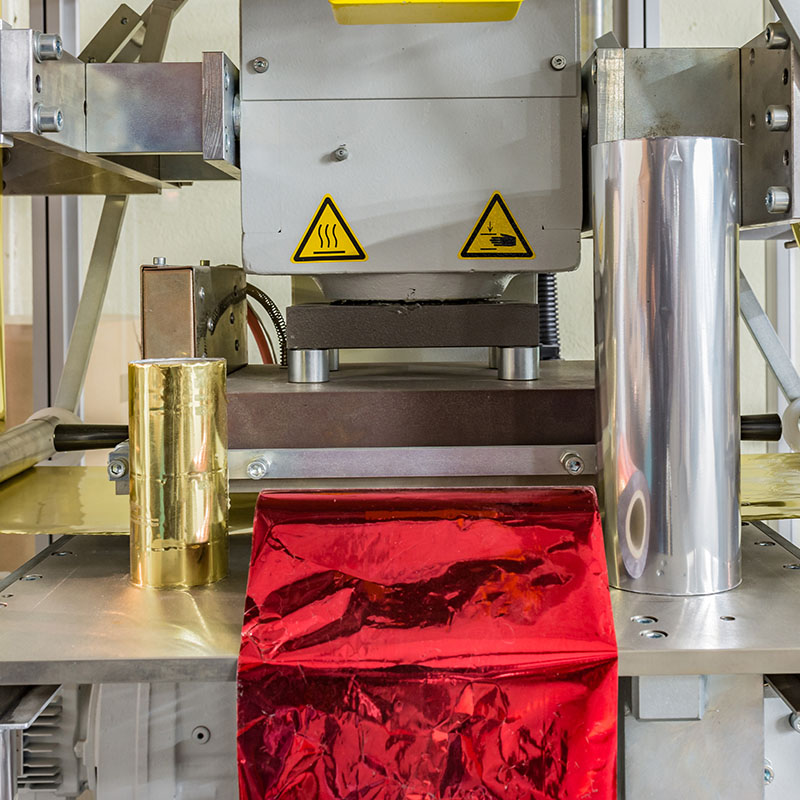
Hotstamping
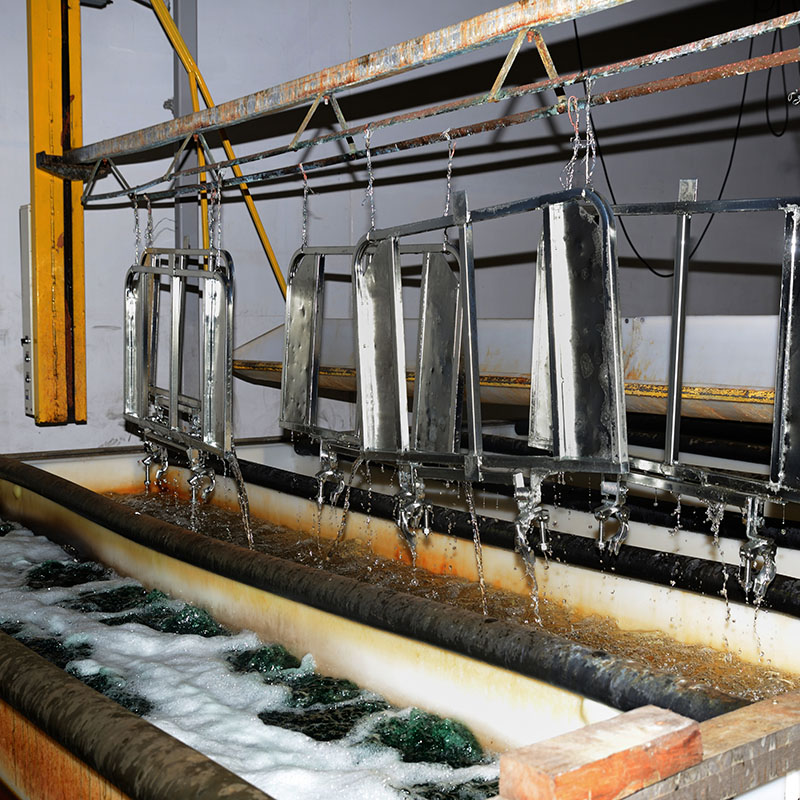
Electroplating
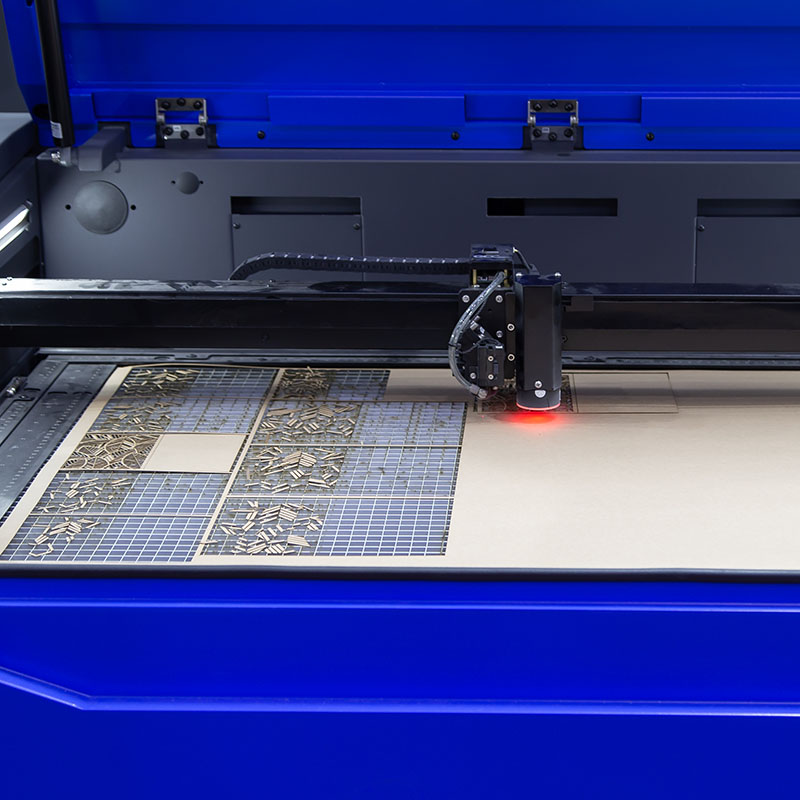
Laser Engraving
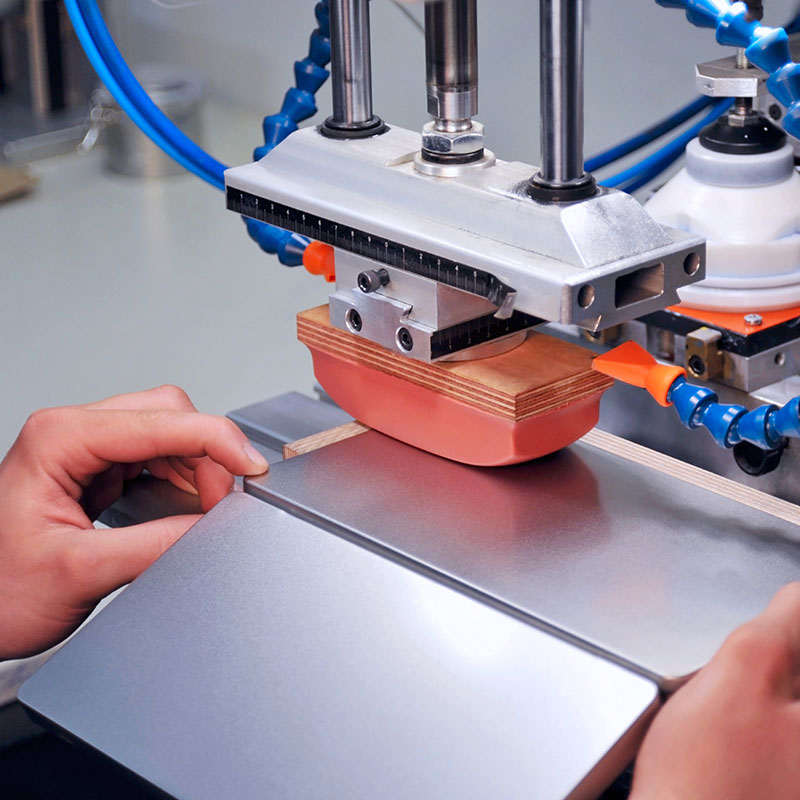
Pad Printing
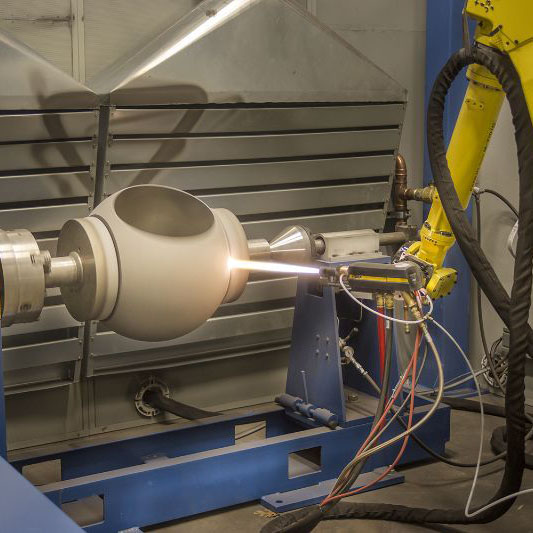
Spraying
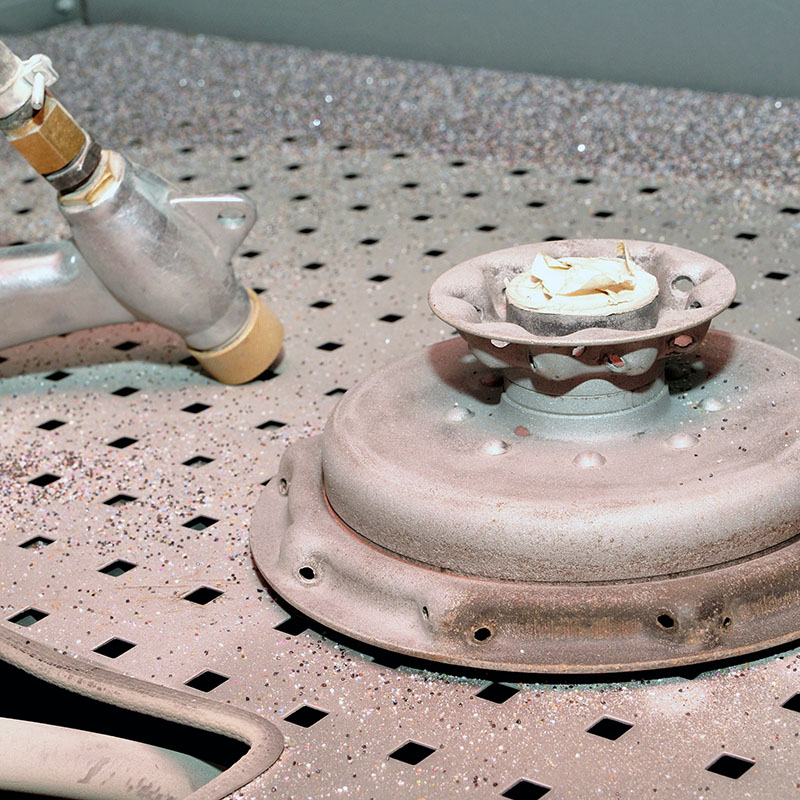
Sand Blasting
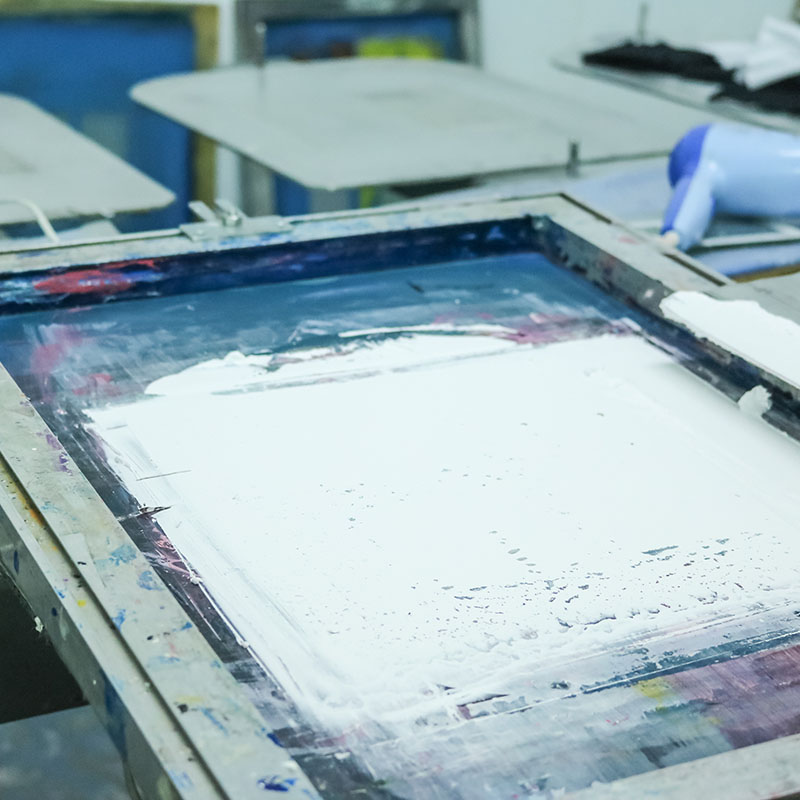
Silkscreen
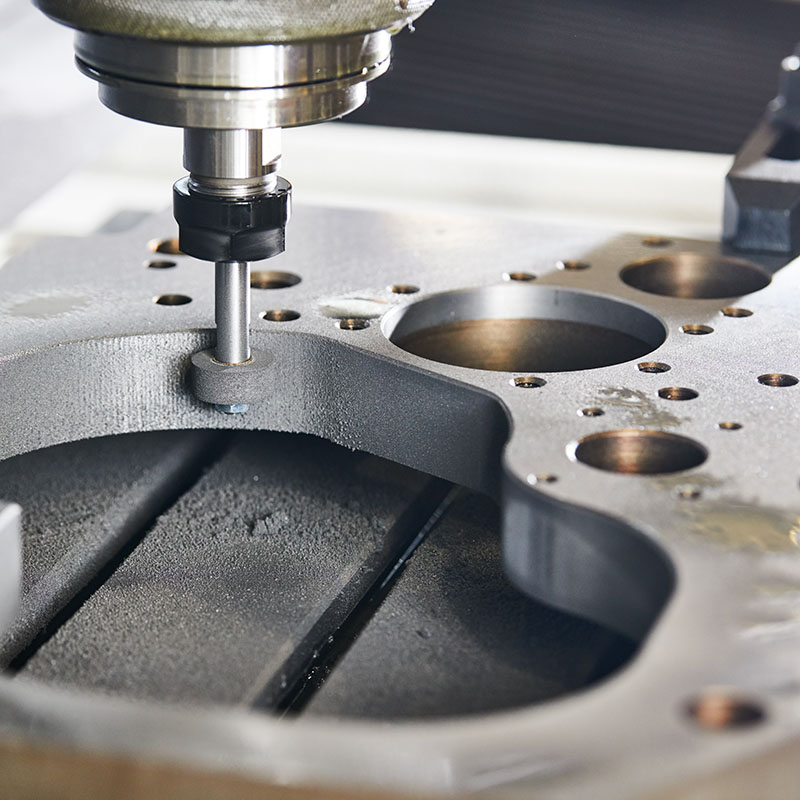
Grinding & Polishing
20+
Types Available
400M+
Capacity Monthly
20+
Partnerships
10Y+
Experience
99%+
Satisfactory Rate
Key Benefits of Choosing KingStar Mold
High Precision and Expertise
Fast Turnaround and Competitive Pricing
Comprehensive One-Stop Service
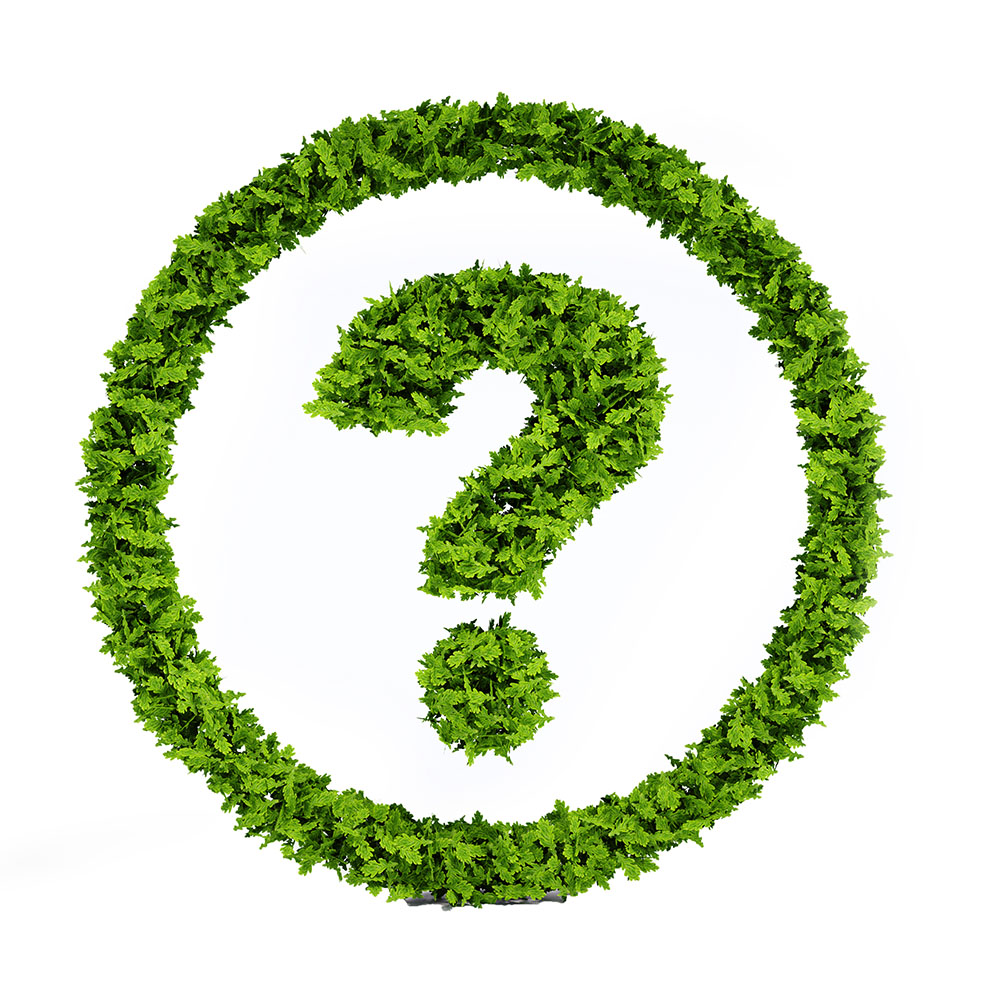
We offer several ways for you to contact us. Firstly, you can click here to access our contact page, and all you need to do is fill out a form to provide us with your information, requirements, and you can also upload some documents. Alternatively, you can send us an email to the address: sales@kingstarmold.com. Or you can call us directly to discuss your needs by calling +86 512 5799 9297. No matter which method you choose, we will reply to you within 24 hours and provide you with a detailed quotation after clarifying the details through communication.
We keep costs down firstly through early DFM to simplify designs and avoid mold reworks, using processes like two-shot or insert molding to skip extra steps, and picking the right materials (no overspending on high-performance plastics when basic ones could work just as well).
Plus, our lower labor costs help trim expenses without cutting quality.
For a deeper look at factors impacting cost and ways to lower it, you can check our post Injection Molding Cost: All Factors and How to Reduce It
We handle a range of post-production steps to get your molded parts ready for use or shipping. That includes surface finishing like painting, silk-screening, sand blasting, black oxide and so on; assembly work (fitting components together, adding fasteners); quality checks (dimensional testing, defect inspections…); and custom packaging (from bulk crates to retail-ready boxes).